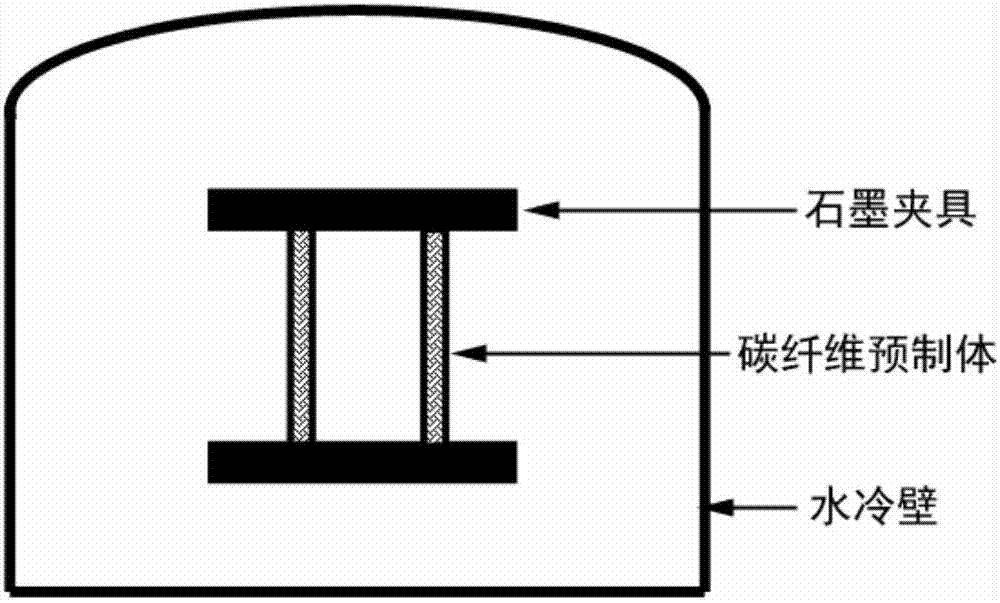
本发明涉及高温炉用发热体
技术领域:
,具体涉及一种表面具有热解碳涂层的碳/碳复合材料发热体及其制备方法,所制备的发热体既适用于高温真空熔炼炉也适用于其他高温工业炉。
背景技术:
:高温真空熔炼炉是熔炼高温合金等金属的主要设备,使用温度高达1600℃,圆筒形电阻发热体的壁较薄,以满足对电阻值的要求。石墨材料因本身力学性能低、机械强度差、易损坏、使用寿命短等缺点,不适合制备薄壁圆筒形发热体。碳/碳(c/c)复合材料具有高温强度大、密度低、抗热震、膨胀系数小、导热、导电性能好、可设计性等特点,是制备薄壁高温发热体的理想材料。cvi工艺是制备c/c复合材料的主要工艺,是碳氢气体在高温下裂解,在碳纤维表面沉积碳基体的一种工艺,其特点是基体结晶性好、强度高、耐高温、耐烧蚀、耐侵蚀、化学稳定性好,升温过程无挥发。但是采用cvi工艺沉积的工件表面易结壳,需几次加工去壳,该工艺同时具有周期长、制备成本高等缺点。e-cvi是在cvi的基础上通过引入电磁场来加快沉积效率,使得材料的制备周期大大缩短,所制c/c材料同样具有强度大、电阻稳定等特点。另外,高温真空熔炼炉在熔炼金属的过程中,物料会飞溅到发热体上,随着附着物料增多,会损伤发热体,降低使用寿命。技术实现要素::针对现在技术中存在的不足之处,本发明的目的在于提供一种表面具有热解碳涂层的碳/碳复合材料发热体及其制备方法,所制备的c/c复合材料发热体不易附着物料,制备工艺周期短,效率高。为实现上述目的,本发明所采用的技术方案如下:一种表面具有热解碳涂层的碳/碳发热体的制备方法,该方法首先对碳纤维预制体采用电耦合化学气相沉积工艺(e-cvi工艺)进行增密处理(致密化处理),制备成c/c复合材料发热体胚体;c/c复合材料发热体胚体经机械加工后获得c/c发热体,再采用化学气相沉积工艺(cvd)在c/c发热体表面沉积热解碳涂层,最后经高温纯化后获得所述表面具有热解碳涂层的c/c复合材料发热体。所述表面具有热解碳涂层的碳/碳复合材料发热体的制备方法,包括如下步骤:(1)界面层制备:采用等温cvi工艺(icvi工艺),将碳纤维预制体置于icvi炉中沉积热解碳,在碳纤维预制体上制备厚度为0.4~2μm的热解碳界面层;(2)利用电耦合化学气相沉积工艺(e-cvi),制备c/c复合材料发热体胚体,过程为:将步骤(1)制得的表面有界面层的碳纤维预制体置于带有水冷壁的e-cvi炉中沉积碳基体,获得c/c复合材料发热体胚体,整体密度控制在1.55~1.60g/cm3之间;(3)机械加工:将步骤(2)制备好的碳/碳(c/c)复合材料发热体胚体按照产品要求进行加工,制得所需形状和尺寸的碳/碳(c/c)发热体;(4)热解碳涂层制备:采用化学气相沉积(cvd)工艺,将步骤(3)加工成型后的碳/碳(c/c)发热体置于cvd炉中沉积热解碳涂层,以封闭碳/碳(c/c)发热体表面孔隙,得到所述表面具有热解碳涂层的碳/碳(c/c)发热体;通过控制沉积时间使发热体的终密度≥1.6g/cm3;(5)高温纯化:将步骤(4)制备的表面具有热解碳涂层的碳/碳(c/c)发热体置于高温纯化炉中进行纯化处理,得到表面具有热解碳涂层的碳/碳(c/c)复合材料发热体成品。上述步骤(1)中,所述碳纤维预制体按照发热体形状和性能要求制成,碳纤维预制体一般采用2d针刺结构,轴向采用一层12k(或3k、6k)无纬布与一层12kpancf网胎铺层,环向采用一层12k(或3k、6k)无纬布与一层12kpancf网胎铺层,交替叠加连续逐层针刺而成整体针刺织物;碳纤维预制体的体积密度一般要求在0.4~0.6g/cm3之间。上述步骤(1)中,所述等温cvi(icvi)工艺制备界面层过程中:以丙烷为气态前驱体,氩气为稀释气体,沉积温度850~980℃,氩气流量为0.05~0.4m3/h,丙烷流量为0.05~0.4m3/h,沉积时间5-10h。上述步骤(2)中,所述电耦合化学气相沉积工艺(e-cvi)中,将表面有界面层的碳纤维预制体置于带有水冷壁的e-cvi炉内直接通电加热,纤维周围产生电磁场,由于预制体的隔热及外部气流和水冷壁的作用,预制体内形成温度梯度,反应气体在电磁场、温度场和流体场的相互作用下实现快速沉积。上述步骤(2)中,所述电耦合化学气相沉积工艺(e-cvi)中,以丙烷为气态前驱体,氩气为稀释气体,沉积温度(温度梯度范围)700~1100℃,氩气流量为0.03~0.5m3/h,丙烷流量为0.03~0.5m3/h,沉积时间10-40h。上述步骤(4)中,所述化学气相沉积(cvd)工艺中:以丙烷为气态前驱体,氩气为稀释气体,沉积温度1000~1200℃,氩气流量为0.04~0.6m3/h,丙烷流量为0.04~0.6m3h,沉积时间20-40h。上述步骤(5)中,所述高温纯化工艺中:纯化温度1700~2400℃,纯化时间5-10h。所制备的表面具有热解碳涂层的碳/碳复合材料发热体的密度≥1.6g/cm3,室温条件下电阻为20~35μω·m。所述发热体应用于高温真空熔炼炉或其他高温工业炉。本发明的优点及有益效果如下:1、本发明中,采用icvi、e-cvi、cvd和纯化工艺制备发热体,制备周期可大大缩短,成本大幅降低,制备周期在40-90小时,成本仅为传统工艺的1/2。在c/c发热体表面均匀沉积一层热解碳涂层,从而填充了发热体表面的细孔,进一步增加了表层的致密性,使得飞溅的物料不易附着和损伤发热体,使发热体的使用寿命提高一倍。2、本发明方法制备的发热体密度≥1.6g/cm3,电阻率(20-35μω·m)。该发热体在高温真空熔炼炉中使用时升温速率高,保温段阻值稳定。附图说明:图1为e-cvi炉中发热体沉积示意图。图2为圆筒形发热体示意图。具体实施方式:下面结合实施例对本发明作进一步说明。本发明为表面具有热解碳涂层的碳/碳复合材料发热体,其制备方法包括如下步骤:(1)界面层制备:采用icvi工艺将碳纤维预制体置于icvi炉中沉积热解碳,在碳纤维预制体上制备厚度为0.4~2μm的热解碳界面层;碳纤维预制体按照发热体形状和性能要求制成筒状,以下实施例中碳纤维预制体采用2d针刺结构,轴向采用一层12k(或3k、6k)无纬布与一层12kpancf网胎铺层,环向采用一层12k(或3k、6k)无纬布与一层12kpancf网胎铺层,交替叠加连续逐层针刺而成整体针刺织物;碳纤维预制体的体积密度在0.4~0.6g/cm3之间。(2)将步骤(1)制得的表面有界面层的碳纤维预制体置于带有水冷壁的e-cvi炉中沉积c基体,获得碳/碳(c/c)复合材料发热体胚体,整体密度控制在1.55~1.60g/cm3之间;该步骤采用e-cvi工艺的过程为:将表面有界面层的碳纤维预制体置于带有水冷壁的e-cvi炉内直接通电加热,碳纤维预制体采用石墨夹具固定;通电后纤维周围产生电磁场,由于预制体的隔热及外部气流和水冷壁的作用,预制体内形成温度梯度(700~1100℃),反应气体在电磁场、温度场和流体场的相互作用下实现快速沉积(图1)。(3)机械加工:将步骤(2)制备好的碳/碳(c/c)复合材料发热体胚体按照产品要求加工成所需形状和尺寸的碳/碳(c/c)发热体;(4)热解碳涂层制备:采用化学气相沉积(cvd)工艺,将步骤(3)加工成型后的碳/碳(c/c)发热体置于cvd炉中沉积热解碳涂层,以封闭碳/碳(c/c)发热体表面孔隙,得到所述表面具有热解碳涂层的碳/碳(c/c)发热体;通过控制沉积时间使发热体的终密度≥1.6g/cm3;(5)高温纯化:将步骤(4)制备的表面具有热解碳涂层的碳/碳(c/c)发热体置于高温纯化炉中进行纯化处理,得到表面具有热解碳涂层的碳/碳(c/c)发热体成品。实施例1发热体尺寸为内径300mm,高120mm,壁厚2.5mm。2d针刺毡留有加工余量,密度为0.5g/cm3;采用icvi工艺制备热解碳界面层,氩气流量0.16m3/h,丙烷流量0.16m3/h,沉积温度950℃,沉积时间5小时;采用e-cvi工艺沉积碳基体,氩气流量0.1m3/h,丙烷流量0.1m3/h,沉积时间20h;采取机械加工成型后,采用cvd工艺制备热解碳涂层,氩气流量0.2m3/h,丙烷流量0.2m3/h,沉积温度1200℃,沉积时间10小时;采用纯化工艺进行纯化处理,温度1800℃,时间5小时;发热体最终密度1.61g/cm3,制备周期40小时。制备的圆筒状发热体成品如图2所示。发热体的主要性能:项目实测结果密度1.61g/cm3室温电阻0.095μω·m实施例2发热体尺寸为内径300mm,高240mm,壁厚3mm。2d针刺毡留有加工余量,密度为0.52g/cm3;采用icvi工艺制备热解碳界面层,氩气流量0.16m3/h,丙烷流量0.16m3/h,沉积温度950℃,沉积时间5小时;采用e-cvi工艺沉积碳基体,氩气流量0.1m3/h,丙烷流量0.13/h,沉积时间25h;采取机械加工成型后,采用cvd工艺制备热解碳涂层,氩气流量0.2m3/h,丙烷流量0.2m3/h,沉积温度1200℃,沉积时间10小时;采用纯化工艺进行纯化处理,温度1800℃,时间6小时;发热体最终密度1.62g/cm3,制备周期46小时。发热体的主要性能:当前第1页12