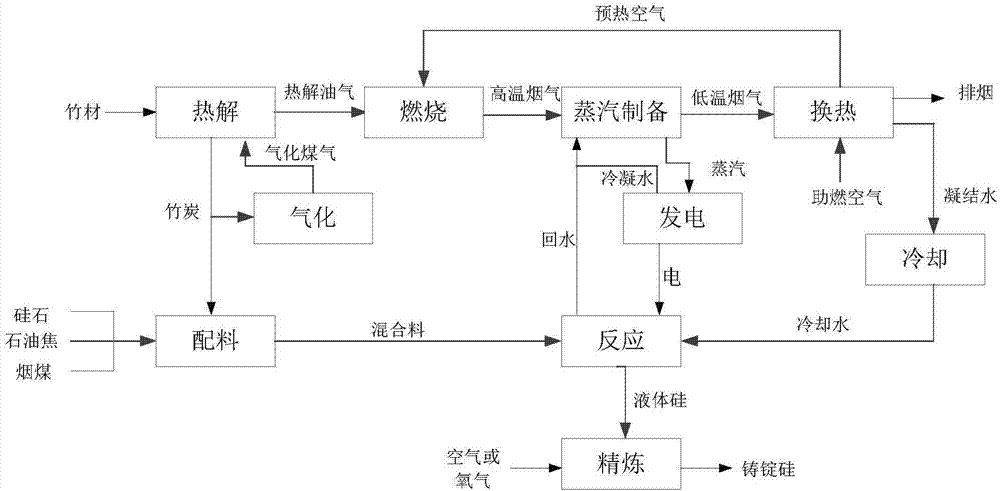
本发明属于硅单质的制备领域,具体地,涉及一种制备硅单质的系统及方法。
背景技术:
:传统制备硅单质的碳质还原剂为木炭、石油焦、烟煤,需要搭配使用才能达到最好的还原效果。木炭作为最重要的碳质还原剂之一,在硅石的冶炼中起着决定性的作用。但是,国内木炭基本都是土窑生产,规模小,干馏温度凭借经验判断,烧炭产生大量烟气,造成空气污染,因而生产受到严格限制,部分窑厂为缩短焖窑时间,后期注入大量的水降低炭温,造成木炭含水量极不稳定,木炭的化验结果显示,全水分含量极不稳定,平均值为44%,不但造成配料的大幅波动,影响了产品品质,同时增加了生产能耗。近年来,由于国家实施生态建设,控制林木砍伐,保护森林资源,已成大家的共识。目前一些地区明文规定,禁止伐林烧炭,有的地区还规定了停止使用木炭的具体时间,木炭的来源就更加有限。我国硅单质产量大省依次为新疆、云南、四川。除新疆外,云南和四川同时又是竹材(诸如毛竹)的产地,储量十分丰富。传统的大湖捕鱼和农作物大棚需要大量的毛竹,现在大湖捕鱼被限制,农作物大棚以钢结构代替毛竹支撑,其他轻工业制品如凉席、竹筷等需求量也降低,使得毛竹价格跌幅严重,并且毛竹加工废料、边角料、山间枯竹等难以利用,直接废弃。技术实现要素:针对现有技术的不足,本发明提供了一种制备硅单质的系统及方法。此工艺可解决竹材产能过剩的问题,同时将竹材进行充分的资源化利用,将其作为硅单质生产的碳质还原剂,可大大提高硅单质的产品品质,同时实现系统的用能平衡,无需外供能源,降低成本。本发明提供的制备硅单质的系统,包括:热解单元,包括热解装置和流化床气化装置,所述热解装置设有竹材入口、气化煤气入口、竹炭出口和热解油气出口;所述流化床气化装置设有竹炭入口和气化煤气出口,所述竹炭入口与所述热解装置的竹炭出口相连,所述气化煤气出口与所述热解装置的气化煤气入口相连;配料单元,设有硅石入口、石油焦入口、烟煤入口、竹炭入口和混合料出口,所述竹炭入口与所述热解装置的竹炭出口相连;硅单质生产单元,设有混合料入口和液体硅出口,所述混合料入口与所述配料单元的混合料出口相连;硅单质精炼单元,设有气体入口、液体硅入口和铸锭硅出口,所述液态硅入口与所述硅单质生产单元的液体硅出口相连;发电单元,包括燃烧装置、蒸汽产生装置和发电装置;所述燃烧装置设有热解油气入口、空气入口和高温烟气出口,所述热解油气出口与所述热解装置的热解油气出口相连;所述蒸汽产生装置设有高温烟气入口、水入口、蒸汽出口和低温烟气出口,所述高温烟气入口与所述燃烧装置的高温烟气出口相连;所述发电装置设有蒸汽入口、冷凝水出口和发电机组,所述蒸汽入口与所述蒸汽产生装置的蒸汽出口相连。在本发明的一些实施例中,所述硅单质生产单元还设有冷却水入口和回水出口,所述回水出口与所述蒸汽产生装置的水入口相连;所述系统还包括冷却水循环单元,所述冷却水循环单元包括换热装置和冷却装置;所述换热装置设有低温烟气入口、助燃空气入口、预热空气出口、烟气出口和凝结水出口,所述低温烟气入口与所述蒸汽产生装置的低温烟气出口相连;所述预热空气出口与所述燃烧装置的空气入口相连;所述冷却装置设有凝结水入口和冷却水出口,所述凝结水入口与所述换热装置的凝结水出口相连;所述冷却水出口与所述硅单质生产单元的冷却水入口相连。在本发明的一些实施例中,所述发电装置与所述硅单质生产单元相连,所述硅单质生产单元所需的电能来自所述发电装置。在本发明的一些实施例中,所述发电装置的冷凝水出口与所述蒸汽产生装置的水入口相连。本发明提供的利用上述系统制备硅单质的方法,包括如下步骤:将竹材送入所述热解装置进行热解,获得竹炭和热解油气;将所述竹炭分别送入流化床气化装置和所述配料单元;所述竹炭在流化床气化装置进行气化,获得气化煤气;将所述气化煤气送入所述热解装置,作为燃料用于热解所述竹材;将硅石、石油焦、烟煤送入所述配料单元,与所述竹炭进行配料,获得混合料;将所述混合料送入所述硅单质生产单元进行反应,获得液体硅;将所述液体硅送入所述硅单质精炼单元,并通入空气或氧气,进行氧化精炼除去所述液体硅中的铝和钙,获得铸锭硅;将所述热解油气送入所述燃烧装置中进行燃烧,获得高温烟气;将所述高温烟气送入所述蒸汽产生装置中与水换热,获得蒸汽和低温烟气;将所述蒸汽送入所述发电装置进行发电,获得电能和冷凝水。在本发明的一些实施例中,还包括如下步骤:将所述低温烟气与助燃空气换热,获得预热空气和凝结水;将所述预热空气送入所述燃烧装置中,与所述热解油气进行燃烧;将所述凝结水冷却后送入所述硅单质生产单元,用于冷却所述硅单质生产单元,获得回水;将所述回水送入所述蒸汽产生装置中,与所述高温烟气进行换热,制备所述蒸汽。在本发明的一些实施例中,将所述发电装置产生的电能用于为所述硅单质生产单元供电。在本发明的一些实施例中,将所述冷凝水送入所述蒸汽产生装置中制备所述蒸汽。在本发明的一些实施例中,所述石油焦、所述烟煤、所述竹炭的重量比为(60-70):(5-10):(20-40)。在本发明的一些实施例中,所述竹材的热解温度为500℃-800℃。本发明实现了竹材的资源化利用,实现了硅单质生产的用能自足,降低了硅单质的生产成本。本发明采用油气直燃工艺,提高了系统的热效率,解决了成分复杂的热解油的使用,杜绝了污水的产生。此外,本发明将一部分竹炭气化,制得的气化煤气作为燃料用于热解竹材,充分利用竹炭,解决了热解装置自用能。本发明的附加方面和优点将在下面的描述中部分给出,部分将从下面的描述中变得明显,或通过本发明的实践了解到。附图说明图1为本发明实施例中的一种制备硅单质的系统的结构示意图。图2为本发明实施例中的一种制备硅单质的工艺流程图。具体实施方式以下结合附图和实施例,对本发明的具体实施方式进行更加详细的说明,以便能够更好地理解本发明的方案以及其各个方面的优点。然而,以下描述的具体实施方式和实施例仅是说明的目的,而不是对本发明的限制。本发明采用廉价的竹材为原料,竹材热解后,得到的竹炭一部分与石油焦、烟煤一起作为碳质还原剂用以与硅石反应制备硅单质,另一部分气化制气化煤气,制得的气化煤气作为燃料用于热解竹材;得到的热解油气经过燃烧、换热后变为蒸汽,将蒸汽用于发电。本发明提供的制备硅单质的系统,包括:热解单元,包括热解装置和流化床气化装置,热解装置设有竹材入口、气化煤气入口、竹炭出口和热解油气出口;流化床气化装置设有竹炭入口和气化煤气出口,竹炭入口与热解装置的竹炭出口相连,气化煤气出口与热解装置的气化煤气入口相连;配料单元,设有硅石入口、石油焦入口、烟煤入口、竹炭入口和混合料出口,竹炭入口与热解装置的竹炭出口相连;硅单质生产单元,设有混合料入口和液体硅出口,混合料入口与配料单元的混合料出口相连;硅单质精炼单元,设有气体入口、液体硅入口和铸锭硅出口,液态硅入口与硅单质生产单元的液体硅出口相连;发电单元,包括燃烧装置、蒸汽产生装置和发电装置;燃烧装置设有热解油气入口、空气入口和高温烟气出口,热解油气出口与热解装置的热解油气出口相连;蒸汽产生装置设有高温烟气入口、水入口、蒸汽出口和低温烟气出口,高温烟气入口与燃烧装置的高温烟气出口相连;发电装置设有蒸汽入口、冷凝水出口和发电机组,蒸汽入口与蒸汽产生装置的蒸汽出口相连。本发明实现了竹材的资源化利用,实现了硅单质生产的用能自足,降低了硅单质的生产成本。本发明采用油气直燃工艺,提高了系统的热效率,解决了成分复杂的热解油的使用,杜绝了污水的产生。此外,本发明将一部分竹炭气化,制得的气化煤气作为燃料用于热解竹材,充分利用竹炭,解决了热解装置自用能。在本发明的一些实施例中,上述硅单质生产单元还设有冷却水入口和回水出口,回水出口与蒸汽产生装置的水入口相连;上述系统还包括冷却水循环单元,冷却水循环单元包括换热装置和冷却装置。换热装置设有低温烟气入口、助燃空气入口、预热空气出口、烟气出口和凝结水出口,低温烟气入口与蒸汽产生装置的低温烟气出口相连;预热空气出口与燃烧装置的空气入口相连。冷却装置设有凝结水入口和冷却水出口,凝结水入口与换热装置的凝结水出口相连;冷却水出口与硅单质生产单元的冷却水入口相连。在本发明的另一些实施例中,发电装置与硅单质生产单元相连,硅单质生产单元所需的电能来自发电装置。将产生的电能用于供给硅单质生产单元,降低了整个工艺的成本。发电装置的冷凝水也可用于制备蒸汽,在本发明的一些实施例中,发电装置的冷凝水出口与蒸汽产生装置的水入口相连。图1所示为本发明制备硅单质的系统的优选实施例,其中,热解装置为旋转床1,配料单元为配料仓2,硅单质生产单元为埋弧电炉3,硅单质精炼单元为硅包4,燃烧装置为燃烧室5,蒸汽产生装置为余热锅炉6,发电装置为蒸汽轮机7,换热装置为换热器8,冷却装置为冷却塔9,流化床气化装置为流化床10。此外,图1所示的系统还包括用于往硅包4中吹气的空压机11。整个系统实现电能自足、燃料自足,并产出高品质的硅单质,具有较高的经济效益。旋转床1设有竹材入口101、竹炭出口102、热解油气出口103和气化煤气入口104。配料仓2设有硅石入口201、石油焦入口202、烟煤入口203、竹炭入口204和混合料出口205。其中,竹炭入口204与旋转床1的竹炭出口102相连。埋弧电炉3设有混合料入口301、液体硅出口302、冷却水入口303、回水出口304和电能入口305。其中,混合料入口301与配料仓2的混合料出口205相连。硅包4设有气体入口401、液体硅入口402和铸锭硅出口403。其中,液体硅入口402与埋弧电炉3的液体硅出口302相连。燃烧室5设有热解油气入口501、空气入口502和高温烟气出口503。其中,热解油气入口501与旋转床1的热解油气出口103相连。余热锅炉6设有高温烟气入口601、水入口602、蒸汽出口603和低温烟气出口604。其中,高温烟气入口601与燃烧室5的高温烟气出口503相连。蒸汽轮机7设有蒸汽入口701、冷凝水出口702和电能出口703。其中,蒸汽入口701与余热锅炉6的蒸汽出口603相连,冷凝水出口702与余热锅炉6的水入口602相连,电能出口703与埋弧电炉3的电能入口305相连(即将蒸汽轮机7产生的电能输送至埋弧电炉3)。换热器8设有低温烟气入口801、助燃空气入口802、预热空气出口803、烟气出口804和凝结水出口805。其中,低温烟气入口801与余热锅炉6的低温烟气出口604相连,预热空气出口803与燃烧室5的空气入口502相连。冷却塔9设有凝结水入口901和冷却水出口902。其中,凝结水入口901与换热器8的凝结水出口805相连。流化床10设有竹炭入口1001和气化煤气出口1002。其中,竹炭入口1001与旋转床1的竹炭出口102相连,气化煤气出口1002与旋转床1的气化煤气入口104相连。空压机11设有气体入口1101和气体出口1102。其中,气体出口1102与硅包4的气体入口401相连。图2所示为本发明提供的一种制备硅单质的方法,包括如下步骤:将竹材送入热解装置进行热解,获得竹炭和热解油气;将竹炭分别送入流化床气化装置和配料单元;竹炭在流化床气化装置进行气化,获得气化煤气;将气化煤气送入热解装置,作为燃料用于热解竹材;将硅石、石油焦、烟煤送入配料单元,与竹炭进行配料,获得混合料;将混合料送入硅单质生产单元进行反应,获得液体硅;将液体硅送入硅单质精炼单元,并通入空气或氧气,进行氧化精炼除去液体硅中的铝和钙,获得铸锭硅(即硅单质);将热解油气送入燃烧装置中进行燃烧,获得高温烟气;将高温烟气送入蒸汽产生装置中与水换热,获得蒸汽和低温烟气;将蒸汽送入发电装置进行发电,获得电能和冷凝水。竹材的含水率和大小影响热解的效率,在本发明优选的实施例中,竹材的含水率在10wt%(重量百分含量)-15wt%左右,并且,在热解前先将竹材破碎至10mm-100mm的块状。热解温度影响竹材的热解效果,在本发明优选的实施例中,竹材的热解温度为500℃-800℃,在此温度下,能降低热解单元的能耗。当使用旋转床1进行热解时,当热解的温度低于600℃,比电阻≥2000ω·cm,当热解温度大于700℃,比电阻≤10ω·cm,因此,为保证竹炭具有较高的比电阻,最佳的热解温度为600℃-700℃。旋转床1在热解时为无氧环境,热解产生的热解油气中甲烷含量>10v/v%(体积百分含量),一氧化碳含量>30v/v%,其他烃类>10v/v%,热值达5000kcal/m3以上,可见,竹材热解产生的热解油气具有较高的利用价值。在热解装置顶端排出的热解油气温度约为550℃,不经冷却,直接热送至燃烧装置中进行燃烧,大大提高了系统的热利用率。在硅单质生产过程中,需将硅石和碳质还原剂进行配比,为了保证熔炼过程中不会出现sic和sio2剩余、含碳过少导致sio2反应不完全和含碳过多导致sic大量生成等情况出现,需严格控制碳质还原剂中的c和硅石中的sio2分子比为2。选择碳质还原剂除了考察固定碳和灰分的含量外,还要求具有反应活性好、比电阻高、高温下不易发生石墨化、粒度适宜、具有一定的机械强度,本发明使用的碳质还原剂包括石油焦、烟煤和竹炭,三种碳质还原剂的性能见表1。表1硅单质生产中碳质还原剂特性对比为了保证最终制得的硅单质的质量,在本发明优选实施例中,石油焦、烟煤、竹炭的重量比为(60-70):(5-10):(20-40)。进一步地,为了得到质量较好的硅单质,石油焦、烟煤和竹炭的粒径的成分及粒度要求如表2所示。表2碳质还原剂成分及粒度要求名称挥发分/wt%灰分/wt%固定碳/wt%粒度/mm竹炭25-30<5>8510-80石油焦12-16<0.582-921-15烟煤<30<8--1-13硅石中sio2含量越高,制得的硅单质越好,sio2含量应大于98%,在本发明更优选实施例中,所用的硅石中sio2含量≥99wt%、fe2o3≤0.015wt%、al2o3≤0.03wt%、cao≤0.20wt%、p2o5≤0.02wt%、mgo≤0.20wt%,其余≤0.535wt%。此外,硅石的粒径也不宜过大或过小,在本发明优选的实施例中,硅石的粒径为8mm-80mm。高温烟气与水换热后,获得蒸汽和低温烟气,低温烟气的温度在300℃左右,在本发明优选的实施例中,将低温烟气与助燃空气换热,获得预热空气和凝结水;将预热空气送入燃烧装置中,与热解油气进行燃烧;将凝结水冷却后送入硅单质生产单元,用于冷却硅单质生产单元,获得回水;将回水送入蒸汽产生装置中,与高温烟气进行换热,制备蒸汽。低温烟气能将助燃空气预热到200℃左右,最终排放的烟气的温度低于100℃,充分回收了烟气的显热。凝结水经高温灼烧其有机成分已被分解,cod含量几乎为零。凝结水的温度约为70℃,经冷却后,将其用于冷却硅单质生产单元,不仅杜绝了污水的产生,而且减少了系统的需水量,降低了硅单质的生产成本。优选地,可将凝结水降温至约12℃。从硅单质生产单元出来的回水温度大于80℃,与高温烟气换热后即可制备蒸汽。整个工艺没有污水产生。图2所示的工艺中,发电装置产生的电能用于为硅单质生产单元供电。多余的电量可用于工业园区生活用电或按照生物质发电并入电网。当采用埋弧电炉3生产硅单质时,其能耗约为10080千瓦时/吨,比利用木炭生产硅单质的装置节能约16%。硅单质在埋弧电炉3内呈液态排出,利用空压机11将空气或氧气通入液体硅中,氧化精炼能有效地除去硅单质中的主要杂质铝和钙,且工艺过程简单。蒸汽发电之后变为冷凝水,图2所示的工艺中,冷凝水与回水一起被送入蒸汽产生装置中,用于制备蒸汽。本发明制得的硅单质质量好,而且制备工艺过程简单,硅烧损率低。下面参考具体实施例,对本发明进行说明。下述实施例中所取工艺条件数值均为示例性的,其可取数值范围如前述
发明内容中所示,对于未特别注明的工艺参数,可参照常规技术进行。下述实施例所用的检测方法均为本行业常规的检测方法。实施例本实施例采用图1所示的系统与图2所示的工艺流程制备硅单质,具体如下:热解:将竹材送入旋转床1进行热解,获得竹炭和热解油气。其中,所用的竹材为毛竹,首先破碎成10mm-100mm的块状物料,在空气中自然风干20天左右,含水率降至10wt%以下。旋转床1内为绝氧环境,炉膛的温度为700℃,物料热解温度为600℃。制得的竹炭的工业分析及元素分析如表3,碘值:400mg/g-500mg/g,600℃热解温度下,比电阻为2155ω·cm-2356ω·cm。表3竹炭的元素分析与工业分析表气化:将一部分竹炭送入流化床10进行气化,获得气化煤气,所得气化煤气热值大于2000kcal/m3。将气化煤气作为燃料送入旋转床1。配料:将硅石、石油焦、烟煤和一部分竹炭送入配料仓2进行配料,获得混合料。硅石的sio2含量为98.7wt%,粒径为8mm-80mm。石油焦:竹炭:烟煤=7:5:5;碳质还原剂中的c和硅石中的sio2分子比为2;石油、竹炭和烟煤的成分及粒度要求如表2所示。制备硅单质:将混合料送入埋弧电炉3进行反应,获得液体硅;将液体硅送入硅包4,并由空压机11通入空气或氧气,进行氧化精炼除去液体硅中的铝和钙,获得铸锭硅。竹炭定价3000元/t,固定碳含量85wt%,木炭定价2800元/t,固定碳含量为70wt%。生产1吨铸锭硅消耗0.5t木炭,在满足固定碳需求的情况下,生产1吨铸锭硅仅消耗0.4t竹炭,则每生产1吨铸锭硅可节省200元。本实施例生产的铸锭硅纯度为99.99%,达到了化学级硅单质的水平,可用于有机硅产品的原料。发电:将热解油气送入燃烧室5进行燃烧,获得高温烟气;将高温烟气送入余热锅炉6中与水换热,获得蒸汽和低温烟气;将蒸汽送入蒸汽轮机7进行发电,获得电能和冷凝水。获得的电能用于为埋弧电炉3供电。冷凝水送入余热锅炉6中,与高温烟气进行换热,制备蒸汽。蒸汽轮机7的发电效率大于25%。冷却水循环:将低温烟气送入换热器8与助燃空气换热,获得预热空气和凝结水;将预热空气送入燃烧室5中,与热解油气进行燃烧;将凝结水送入冷却塔9中冷却后送入埋弧电炉3,用于冷却埋弧电炉3,获得回水;将回水送入余热锅炉6中,与高温烟气进行换热,制备蒸汽。凝结水在冷却塔9中冷却至7℃,回水为85℃。生产1吨硅单质,埋弧电炉的能耗为10080kwh,每天按产50吨硅单质,竹材处理量为1000吨/天,每吨竹材可发电500kwh左右,竹材热解产炭率为35%,其中每生产1吨硅单质,有0.5吨竹炭作为碳质还原剂,另有6.5吨竹炭送至流化床气化装置进行气化。整个系统实现电能自足、燃料自足,并产出高品质的硅单质,具有较高的经济效益。显然,上述实施例仅仅是为清楚地说明本发明所作的举例,而并非对实施方式的限定。对于所属领域的普通技术人员来说,在上述说明的基础上还可以做出其它不同形式的变化或变动。这里无需也无法对所有的实施方式予以穷举。而由此所引申出的显而易见的变化或变动仍处于本发明的保护范围之中。当前第1页12