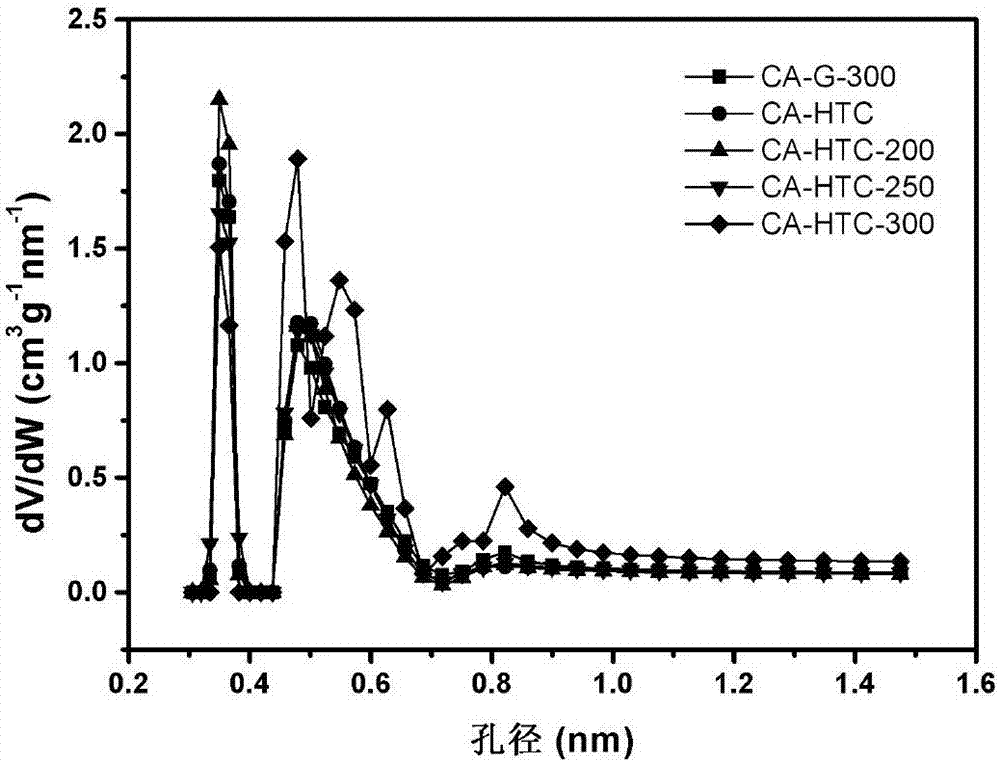
本发明涉及多孔碳材料制备
技术领域:
,特别涉及一种极微孔多孔碳材料及其制备方法。
背景技术:
:co2作为最主要的温室气体,如今在大气中的含量与日俱增,导致了全球变暖等一系列环境问题,严重威胁到了人类的生存发展,因此对co2的捕集与封存变得尤为重要。目前,co2捕集技术主要有吸收法、膜分离法和吸附法等。吸收法对设备腐蚀性大,再生能耗高,同时受温度的制约;膜分离法普遍成本较高,限制其应用;而吸附法表现出巨大的优势,备受研究者的青睐。吸附法技术的核心在于多孔固体吸附剂,目前应用于co2吸附的固体吸附剂主要有金属有机框架材料(mofs)、分子筛、多孔碳材料和高温碱金属或碱土金属复合氧化物。相比之下,多孔碳材料由于其出色的co2吸附性能,发达的孔隙结构、较低的经济成本、丰富的原料来源、良好的化学和热稳定性、较低的再生能耗以及结构可控性等优势,成为最具工业应用前景的co2固体吸附剂。通过水热碳化生物质资源的方式,可以在温和的反应条件下将生物质转化为碳材料以及高价值化学品,近年来引起业内研究人员的广泛关注。首先,原料来源广泛,各种各样的生物质、工业原料或者废物都可被用作碳前躯体合成微孔碳材料;其次,设备简单易操作,反应条件温和易控制,能耗低,易使生产扩大化与工业化;最后,使用水作反应介质,整个合成过程在密闭体系中进行,无污染物的生成,生产工艺绿色环保。然而,通过水热合成法得到的碳材料一般具有较低的比表面。如果应用到气体吸附领域,则需要进一步构建发达孔隙结构,特别是孔径尺寸小于0.7nm的极微孔分布对co2吸附捕集材料具有决定性因素。一般来说,工业上主要通过化学活化法制备高比表面积的碳材料,其中主要以koh为化学活化剂。该方法虽然能产生发达的孔隙结构,活化效果较好,但是传统的活化过程会消耗大量的koh,通常是以碳前驱物3~4倍的质量比进行物理研磨,使得制备成本增加,同时造成设备腐蚀,对环境产生较大的污染,且构建的微孔孔道主要集中在1~2nm,孔隙结构仍不够发达。技术实现要素:本发明的目的在于提供一种极微孔多孔碳材料及其制备方法。本发明提供的制备方法活化剂用量少,且制备得到的极微孔多孔碳材料富含孔径为0.7nm以下的极微孔。本发明提供了一种极微孔多孔碳材料的制备方法,包括以下步骤:(1)将单糖在空气中进行高温氧处理,得到氧处理碳材料;(2)将所述步骤(1)得到的氧处理碳材料与碱金属氢氧化物和水混合后进行置换反应,得到置换碳材料;(3)将所述步骤(2)得到的置换碳材料进行活化,得到极微孔多孔碳材料。优选的,所述步骤(1)替换为:将单糖的水溶液在密闭容器中进行水热反应,得到预碳化材料;将所述预碳化材料在空气中进行高温氧处理,得到氧处理碳材料。优选的,所述水热反应的温度为160~200℃,水热反应的时间为10~24h。优选的,所述单糖包括葡萄糖、果糖、半乳糖、核糖和脱氧核糖中的一种或多种。优选的,所述步骤(1)中高温氧处理的温度为200~400℃,高温氧处理的时间为2~12h。优选的,所述步骤(1)中的空气为静态空气或动态空气。优选的,所述步骤(2)中碱金属氢氧化物与氧处理碳材料的质量比优选为1.0~2.0。优选的,所述步骤(2)中置换反应的温度为60~80℃,置换反应的时间为8~12h。优选的,所述步骤(3)中活化的温度为600~800℃,活化的时间为2~8h。本发明还提供了上述技术方案所述制备方法制备的极微孔多孔碳材料,所述极微孔多孔碳材料中的极微孔的孔径为0.7nm以下。本发明提供了一种极微孔多孔碳材料的制备方法,包括以下步骤:将单糖或单糖经水热反应得到的预碳化材料在空气中进行高温氧处理,得到氧处理碳材料;将所述氧处理碳材料与碱金属氢氧化物和水混合后进行置换反应,得到置换碳材料;将所述置换碳材料进行活化,得到极微孔多孔碳材料。本发明通过空气氧化法对单糖或水热碳材料进行处理,以实现对碳材料表面含氧官能团的调变,显著增加水热碳表面可进行离子交换的官能团(如羧基、酚羟基等)的含量,为后续离子型化学法活化过程提供离子交换位点,进而通过离子交换法实现碱金属离子的原子级分散,有效减少活化剂的用量,最终合成富含极微孔的多孔碳材料。实验结果表明,本发明提供的制备方法活化剂用量(折算成工业koh化学活化法用量)约为碳前驱体质量的0.1~0.3,制备得到的极微孔多孔碳材料富含中孔径为0.7nm以下的极微孔。附图说明图1为实施例1~4中得到的样品的n2吸脱附等温线;图2为实施例1~4中得到的样品的孔径分布图。具体实施方式本发明提供了一种极微孔多孔碳材料的制备方法,包括以下步骤:(1)将单糖在空气中进行高温氧处理,得到氧处理碳材料;(2)将所述步骤(1)得到的氧处理碳材料与碱金属氢氧化物和水混合后进行置换反应,得到置换碳材料;(3)将所述步骤(2)得到的置换碳材料进行活化,得到极微孔多孔碳材料。在本发明的一个技术方案中,本发明将单糖在空气中进行高温氧处理,得到氧处理碳材料。在本发明中,所述单糖优选包括葡萄糖、果糖、半乳糖、核糖和脱氧核糖中的一种或多种。本发明对所述单糖的来源没有特殊的限定,采用本领域技术人员熟知的市售产品即可。在本发明中,所述单糖优选为含有3~6个碳原子的多羟基醛或多羟基酮,能够作为碳源提供基体。在本发明中,所述空气优选为静态空气或动态空气。本发明对所述动态空气的流速没有特殊的限定,能够保证氧化反应的供氧量即可。在本发明中,所述高温氧处理的温度优选为200~400℃,更优选为250~350℃,最优选为300℃;所述高温氧处理的时间优选为2~12h,更优选为5~10h,最优选为6~8h。在本发明中,所述高温氧处理中,单糖与氧气进行部分氧化反应,从而在水热碳材料表面构筑含氧官能团,其中有一些含氧官能团具有与碱金属离子进行离子交换性能,为后续离子型化学法活化过程提供离子交换位点。在本发明的另一个技术方案中,本发明将单糖的水溶液在密闭容器中进行水热反应,得到预碳化材料;将所述预碳化材料在空气中进行高温氧处理,得到氧处理碳材料。本发明将单糖的水溶液在密闭容器中进行水热反应,得到预碳化材料。在本发明中,所述水热反应的温度优选为160~200℃,更优选为170~190℃,最优选为180℃;所述水热反应的时间优选为10~24h,更优选为12~20h,最优选为14~16h。在本发明中,所述水热反应无需额外的加压或减压,所述水热反应的压力优选为所述水热反应的温度下的自生压力。在本发明中,所述水热反应可以合成一定量的可进行离子交换的含氧官能团位点,进一步提高后续置换反应中的反应位点,使制备的多孔碳材料的比表面更高。本发明对所述水热反应的装置没有特殊的限定,采用本领域技术人员熟知的水热反应釜即可。水热反应完成后,本发明优选将所述水热反应的产物依次进行过滤、洗涤和干燥,得到预碳化材料。本发明对所述过滤、洗涤和干燥的操作没有特殊的限定,采用本领域技术人员熟知的过滤、洗涤和干燥的技术方案即可。在本发明中,所述干燥的温度优选为70~90℃,更优选为80℃;所述干燥的时间优选为8~12h,更优选为10h。得到预碳化材料后,本发明将所述预碳化材料在空气中进行高温氧处理,得到氧处理碳材料。在本发明中,所述预碳化材料的高温氧处理的操作优选与上述技术方案所述高温氧化处理的技术方案相同,在此不再赘述。在本发明中,所述高温氧处理过程中,预碳化材料与氧气进行部分氧化反应,从而在水热碳材料表面构筑含氧官能团,其中有一些含氧官能团具有与碱金属离子进行离子交换性能,为后续离子型化学法活化过程提供离子交换位点。得到氧处理碳材料后,本发明将所述氧处理碳材料与碱金属氢氧化物和水混合后进行置换反应,得到置换碳材料。在本发明中,所述碱金属氢氧化物优选包括氢氧化钾和/或氢氧化钠。在本发明中,所述碱金属氢氧化物与氧处理碳材料的质量比优选为1.0~2.0,更优选为1.1~1.5。本发明对所述氧处理碳材料与碱金属氢氧化物和水混合的操作没有特殊的限定,采用本领域技术人员熟知的混合反应原料的技术方案即可。本发明优选将所述氧处理碳材料与碱金属氢氧化物的水溶液混合。本发明对所述碱金属氢氧化物的水溶液的浓度没有特殊的限定,任意浓度均可。在本发明中,所述碱金属氢氧化物的水溶液的浓度优选为0.01~1mol/l,更优选为0.03~0.3mol/l。在本发明中,所述置换反应的温度优选为60~80℃,更优选为65~75℃,最优选为70℃;所述置换反应的时间优选为8~12h,更优选为9~11h,最优选为10h。在本发明中,所述置换反应过程中,碱金属氢氧化物中的碱金属离子与氧处理碳材料表面的官能团(如羧基或酚羟基等)发生置换,使碱金属离子实现原子级分散,在最终产物中形成分布均匀的极微孔。本发明对所述置换反应的温度控制方式没有特殊的限定,采用本领域技术人员熟知的水浴加热法即可。在本发明中,所述置换反应优选在搅拌条件下进行。本发明对所述搅拌的速率没有特殊的限定,采用本领域常规的搅拌的速率即可。置换反应完成后,本发明优选将所述置换反应的产物依次进行离心、洗涤和干燥。本发明对所述离心、洗涤和干燥的操作没有特殊的限定,采用本领域技术人员熟知的离心、洗涤和干燥的技术方案即可。在本发明中,所述洗涤优选为水洗;所述洗涤的次数以洗涤剂呈中性为止。得到置换碳材料后,本发明将所述置换碳材料进行活化,得到极微孔多孔碳材料。在本发明中,所述活化的温度优选为600~800℃,更优选为620~680℃,最优选为640~660℃;所述活化的时间优选为2~8h,更优选为4~6h,最优选为5h。在本发明中,所述活化优选在真空或惰性气体保护下进行;所述惰性气体优选为氮气。在本发明中,原子级分散的碱金属离子在活化过程中与水热碳材料表面的含氧官能团在高温下发生分解反应进而形成孔径为0.7nm以下的极微孔。本发明对所述活化的装置没有特殊的限定,采用本领域技术人员熟知的管式加热炉即可。活化完成后,本发明优选将所述活化的产物依次进行酸洗和干燥,得到极微孔多孔碳材料。本发明对所述酸洗和干燥的操作没有特殊的限定,采用本领域技术人员熟知的酸洗和干燥的技术方案即可。在本发明中,所述酸洗的洗涤剂优选为稀盐酸;所述稀盐酸的质量浓度优选为5~15%,更优选为10%。本发明通过空气氧化法对单糖或水热碳材料进行处理,以实现对碳材料表面含氧官能团的调变,显著增加水热碳表面可进行离子交换的官能团(如羧基、酚羟基等)的含量,为后续离子型化学法活化过程提供离子交换位点,进而通过离子交换法实现碱金属离子的原子级分散,有效减少活化剂的用量,最终合成富含极微孔的多孔碳材料。实验结果表明,本发明提供的制备方法活化剂用量(折算成工业koh化学活化法用量)约为碳前驱体质量的0.1~0.3,制备得到的极微孔多孔碳材料富含中孔径为0.7nm以下的极微孔。本发明还提供了上述技术方案所述制备方法制备的极微孔多孔碳材料,所述极微孔多孔碳材料中的极微孔的孔径为0.7nm以下。为了进一步说明本发明,下面结合实施例对本发明提供的极微孔多孔碳材料的制备方法进行详细地描述,但不能将它们理解为对本发明保护范围的限定。实施例1:将8g葡萄糖直接置于静态空气气氛的马弗炉中于300℃下处理5h得到氧处理碳材料。将氧处理碳材料质量1.1倍的koh配制成浓度为30ml的水溶液,加入上述氧处理碳材料,然后于70℃水浴锅内搅拌10h,离心分离至洗涤液呈中性,之后将固体在80℃烘箱内烘干得到碱金属置换碳材料。将上述的碱金属置换碳材料置于管式电阻炉中活化,在氮气气氛下升温至800℃,恒温2h,最后得到样品置于10%稀盐酸中搅拌1h,干燥,即可得样品ca-g-300。实施例2:将8g葡萄糖添加到60ml水溶液中,搅拌至澄清液,放入聚四氟乙烯于反应釜中,于160℃水热处理12h,最后将得到的固体混合物进行过滤、洗涤,然后在80℃下干燥10h,得到水热预碳化材料。将上述预碳化材料置于空气气氛马弗炉中于200℃下处理20h得到氧处理碳材料。将氧处理碳材料质量1.5倍的koh配制成30ml水溶液,加入上述氧处理碳材料,然后于70℃水浴锅内搅拌10h,离心分离至洗涤液呈中性,之后将固体在80℃烘箱内烘干得到碱金属置换碳材料。将上述的碱金属置换碳材料置于管式电阻炉中活化,在氮气气氛下升温至600℃,恒温8h,最后得到样品置于10%稀盐酸中搅拌1h,干燥,即可得样品ca-htc-200。实施例3:将8g葡萄糖添加到60ml水溶液中,搅拌至澄清液,放入聚四氟乙烯于反应釜中,于180℃水热处理12h,最后将得到的固体混合物进行过滤、洗涤,然后在80℃下干燥10h,得到水热预碳化材料。将上述预碳化材料置于空气气氛马弗炉中于250℃下处理10h得到氧处理碳材料。将氧处理碳材料质量1.5倍的koh配制成30ml水溶液,加入上述氧处理碳材料,然后于70℃水浴锅内搅拌10h,离心分离至洗涤液呈中性,之后将固体在80℃烘箱内烘干得到碱金属置换碳材料。将上述的碱金属置换碳材料置于管式电阻炉中活化,在氮气气氛下升温至700℃,恒温4h,最后得到样品置于10%稀盐酸中搅拌1h,干燥,即可得样品ca-htc-250。实施例4:将8g葡萄糖添加到60ml水溶液中,搅拌至澄清液,放入聚四氟乙烯于反应釜中,于200℃水热处理12h,最后将得到的固体混合物进行过滤、洗涤,然后在80℃下干燥10h,得到水热预碳化材料。将上述预碳化材料置于空气气氛马弗炉中于300℃下处理5h得到氧处理碳材料。将氧处理碳材料质量1.5倍的koh配制成30ml水溶液,加入上述氧处理碳材料,然后于70℃水浴锅内搅拌10h,离心分离至洗涤液呈中性,之后将固体在80℃烘箱内烘干得到碱金属置换碳材料。将上述的碱金属置换碳材料置于管式电阻炉中活化,在氮气气氛下升温至800℃,恒温2h,最后得到样品置于10%稀盐酸中搅拌1h,干燥,即可得样品ca-htc-300。实施例5:采用热重分析(tga)测定碱金属置换碳材料中k+的含量,具体测试方法如下:将一定量的碱金属置换碳材料置于热重分析样品池,以5℃/分钟的升温速率升温至900℃后恒温2小时,测定样品池内样品的重量变化情况。根据失重后残留的重量,以k2o为例计算k+含量,以此为基础计算折合koh量,计算koh/水热碳质量比,其结果列于表1:表1实施例1~4中合成样品的孔结构数据实施例残留含量(%)折合k+(mmol)koh/水热碳实施例1111.170.14实施例2161.700.22实施例3192.020.27实施例4212.230.30通过表1可以看到:对于实施例1,仅采用空气氧化法也可以合成富含离子交换位点,然而量相对较少。对于实施例2~4,利用温和的水热条件联合空气氧化法对水热碳材料进行处理可以成功实现对碳材料表面的官能团的调变,为后续离子型化学活化法提供离子交换位点,最终实现k+置换,置换k+的量折合koh后与水热碳材料的质量比介于0.1~0.3,活化剂用量远小于常规koh物理混合化学活化法。实施例6:采用低温n2吸附-脱附法对实施例3中合成的代表性样品进行孔结构分析。n2吸附-脱附曲线以液氮为冷阱,高纯氮作为吸附质,通过静态容量法测定孔结构和比表面积。样品测试前,在300℃的温度下,真空脱气3h,从而脱出样品中吸附的水分子以及其他通过物理吸附的杂质。据n2于77k下在材料表面的吸附量随压力变化的特性做出样品的吸附-脱附等温线。通过brunauer-emmett-teller法(bet法)计算材料的比表面积,根据t-plot法计算微孔表面积、微孔孔容。材料的微孔分布采用低相对压力下的氮气吸附数据,通过dft的方法计算得到。表2是实施例1~4中合成样品的孔结构数据。图1是实施例1~4样品的n2吸脱附等温线。图2是实施例1~4样品的孔径分布图。通过表2孔结构数据和图1n2吸脱附数据可以看到,本发明提供的空气氧化法合成的生物质基多孔碳材料具有发达的微孔结构。而图2的孔径分布可以看到,本发明合成的多孔碳材料的孔径更多的集中在小于0.7nm的极微孔范围。表2实施例1~4中合成样品的孔结构数据实施例7:利用静态吸附法对制备好的样品aca1、aca2、aca5、aca10进行co2的吸附性能测试。吸附测试前,将吸附剂在300℃条件下脱气4h,真空度达到1μmmhg,除去水分和杂质。脱气后测试吸附剂在0℃和25℃的co2吸附性能。测试结果如表3:通过表3co2的吸附性能测试结果可以看到:实施例1中对生物质材料直接进行空气氧化法处理得到的多孔碳材料同样可以具有相当量的co2吸附容量。实施例2~4中对水热碳材料进行空气氧化处理得到的碳材料可以显著提高co2的吸附容量。表30℃和25℃条件下co2的吸附性能结果从以上实施例可以看出,本发明提供的制备方法活化剂用量少,制备得到的极微孔多孔碳材料的富含孔径为0.7nm以下的极微孔,比表面积大,对co2的吸附性能好。以上所述仅是本发明的优选实施方式,并非对本发明作任何形式上的限制。应当指出,对于本
技术领域:
的普通技术人员来说,在不脱离本发明原理的前提下,还可以做出若干改进和润饰,这些改进和润饰也应视为本发明的保护范围。当前第1页12