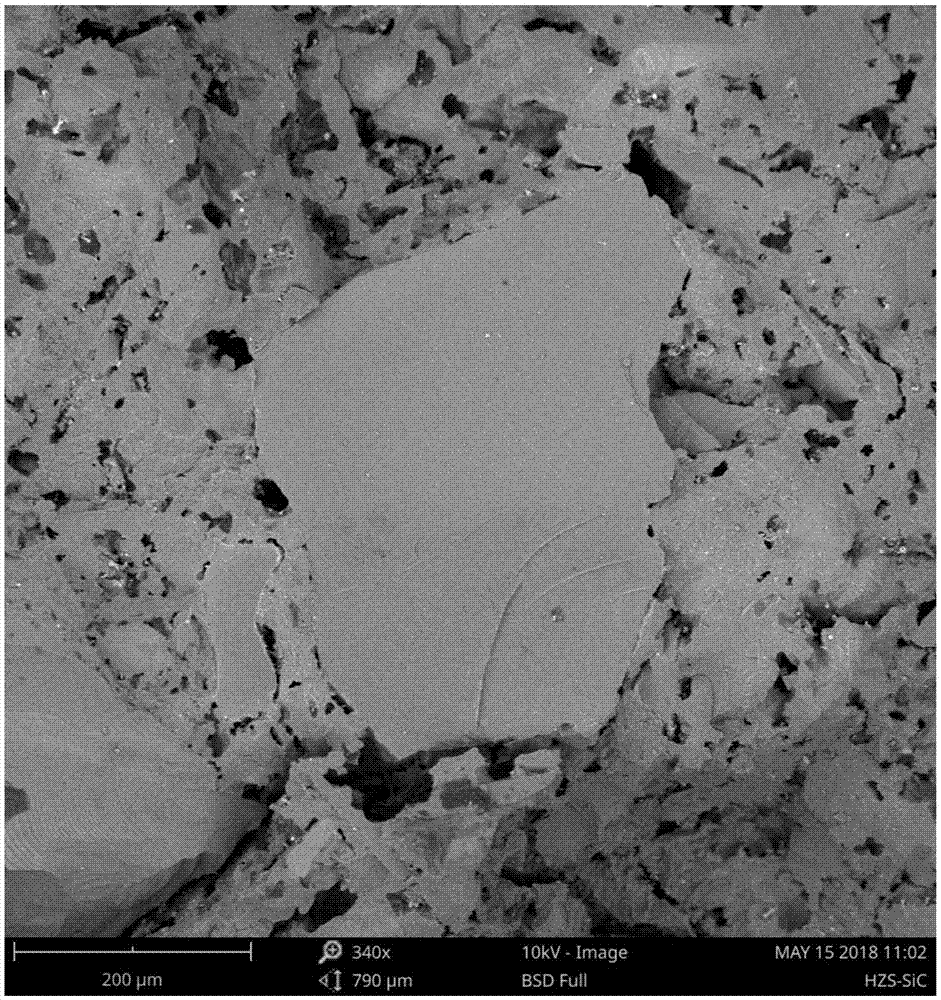
本发明涉及耐火材料生产
技术领域:
,具体涉及一种“红柱石‐碳化硼‐氮化硅‐碳化硅”四元耐火陶瓷的制备方法。
背景技术:
:特种船舶用增压锅炉内衬耐火材料作为高温结构材料,是船舶正常运行的关键基础材料,研究开发高效高抗热震长寿命内衬材料具有重要意义。增压锅炉作为船舶动力的心脏,工作时频繁的启、停及变负荷工作,导致炉膛温度和压力处于急速升降和不断变化的状态,炉体内衬不但要承受很高的温度,还要抵抗温度变化造成的热应力冲击、高温重油烟气的侵蚀、高温氧化变质等多重损毁作用。目前,增压锅炉内衬主要使用氮化硅结合碳化硅耐火陶瓷,应用于风口砖、观火孔砖和墙砖等炉膛热负荷、热冲击最强的部位,如申请号为201710729145.9,发明名称为氮化硅结合碳化硅耐火陶瓷的真空振动浇注成型方法的专利申请文件,该发明申请文件中的利用硅粉、碳化硅粉制得的氮化硅结合碳化硅耐火陶瓷,然而,氮化硅结合碳化硅耐火陶瓷的抗热震性能和耐氧化侵蚀性能差,使用寿命短,存在严重的安全隐患。因此,采用先进配方和工艺,制备具有高抗热震和耐氧化侵蚀性的新型耐火陶瓷对提高增压锅炉的服役寿命和运行安全性意义重大。技术实现要素:为解决以上问题,本发明的目的是提供一种具有较好的抗热震性能和耐氧化侵蚀性能的“红柱石‐碳化硼‐氮化硅‐碳化硅”四元耐火陶瓷的制备方法。为实现上述目的,本发明所设计的“红柱石‐碳化硼‐氮化硅‐碳化硅”四元耐火陶瓷的制备方法,包括以下步骤:1)浆料的制备:将硅粉、碳化硅粉、红柱石粉、碳化硼粉、结合剂、分散剂置于容器中干混搅拌,再加入水混合搅拌均匀,得到浆料;2)坯体的制备:将步骤1)所得的浆料放入真空振动浇注成型装置的漏斗内,在振动条件下,浆料由漏斗向下流入模具,待浆料完全流进模具后再振动处理,最后空气中养护干燥后得到成型的坯体;3)氮化处理:将步骤2)所得的坯体放入氮化炉中进行氮化处理,最后随炉冷却到室温,即可。其中,真空振动浇注成型装置的具体结构参见申请号为201710729144.4,发明名称为“用于碳化硅耐火陶瓷材料的真空振动浇注成型装置”中公开的真空振动浇注成型装置。与现有技术相比,本发明在传统的氮化硅结合碳化硅耐火陶瓷的基础上通过增加红柱石和碳化硼制得“红柱石‐碳化硼‐氮化硅‐碳化硅”四元耐火陶瓷,红柱石相在高温下煅烧会发生莫来石化,形成针状互穿的结构,为材料提供坚固的骨架,可起到原位自增强的作用,从而提高耐火陶瓷的抗热震性能;碳化硼相在高温氧化气氛中反应生成氧化硼,能够填充到连通的孔隙中,起到阻断氧继续侵入以及裂纹封填的作用,从而提高耐火陶瓷的耐氧化侵蚀性能。作为优选方案,所述步骤1)中碳化硅粉、硅粉、红柱石粉、碳化硼粉、结合剂、分散剂的质量比为50~55:20~25:10~15:5~10:2~5:2~5。其中,碳化硅为增强相,在耐火陶瓷中起到承载的作用,较高的质量比有利于提高整体的强度。硅粉在氮化烧结后反应生成基体氮化硅相,将增强体结合起来,故需要一定的质量比满足结合强度要求,此外氮化硅本身具备高韧性和高热导率,有利于提高整体的抗热震性能。碳化硅和氮化硅两相是耐火陶瓷的主要相,但两者在高温氧化环境下会受到氧化腐蚀,需引入抗氧化组分。红柱石本身为氧化物,抗氧化性能优异,同时其在高温下的莫来石化可起到原位自增强的作用,有利于提高耐火陶瓷的抗热震性能。碳化硼为自愈合组分,在高温下生成玻璃相氧化硼能够封填裂纹,进一步阻断氧扩散,提高整体的抗氧化性能。红柱石和碳化硼在耐火陶瓷中均匀弥散分布,质量比相对较低。结合剂和分散剂为辅助材料,用量较少。作为优选方案,所述步骤1)中,碳化硅粉由黑碳化硅颗粒、碳化硅细粉、碳化硅微粉按照质量比10~14:1:1混合而成,其中,所述黑碳化硅颗粒的粒径为0.3~1.0mm,所述碳化硅细粉的粒径为200~240目,所述碳化硅微粉的粒径为1.0~3.0μm,纯度均大于98%;硅粉为纯度98%以上的金属硅粉,其粒径为200~240目。作为优选方案,所述步骤1)中,红柱石粉为纯度98%以上的红柱石粉,其粒径为0.3~1.0mm。作为优选方案,所述步骤1)中,碳化硼粉为纯度98%以上的碳化硼粉,其粒径为200~240目。作为优选方案,所述步骤1)中,结合剂为水合氧化铝、铝酸钙水泥、酚醛树脂中的一种或多种;分散剂为聚乙烯亚胺、聚乙烯醇、聚丙烯酸铵中的一种或多种。作为优选方案,所述步骤1)中,水的加入质量为原料总质量的6~10%,所述原料总质量为硅粉、碳化硅粉、红柱石粉、碳化硼粉、结合剂、分散剂的质量之和。作为优选方案,所述步骤1)中,干混搅拌的时间为5~30分钟,混合搅拌的时间为2~10分钟。作为优选方案,所述步骤2)中,振动频率为40~60hz;所述浆料完全流进模具后再振动处理的时间为1~2分钟;所述空气中养护的时间为12~36小时。作为优选方案,所述步骤3)中,氮化处理的升温程序为25℃~1000℃范围内升温速率为10℃/min;1000℃~1450℃升温速率为1℃/min,1450℃保温0.5h,最后随炉冷却到室温。作为优选方案,所述碳化硅粉、硅粉、红柱石粉、碳化硼粉、结合剂、分散剂的质量比为53~54:21~23:11~12:7~8:2~5:2,所述碳化硅粉由黑碳化硅颗粒、碳化硅细粉、碳化硅微粉按照质量比12~14:1:1混合而成,黑碳化硅颗粒的粒径为0.8~1.0mm,所述碳化硅细粉的粒径为210~230目,所述碳化硅微粉的粒径为2.5~3.0μm;所述硅粉粒径为210~230目;所述红柱石粉粒径为0.8mm;所述碳化硼粉粒径为210~230目;所述结合剂为水合氧化铝和铝酸钙水泥的混合物,所述分散剂为聚乙烯亚胺和聚乙烯醇的混合物。本发明的优点在于:与传统的氮化硅结合碳化硅耐火陶瓷的制备方法相比,本发明添加碳化硅粉、硅粉、红柱石和碳化硼原料并结合真空振动浇注成型的生产工艺得到的“红柱石‐碳化硼‐氮化硅‐碳化硅”四元耐火陶瓷的抗热震性能和耐氧化侵蚀性能明显优于传统的氮化硅结合碳化硅耐火陶瓷。附图说明图1为实施例1所制备的“红柱石-碳化硼-氮化硅-碳化硅”四元耐火陶瓷a的扫描电镜微观形貌图。图2为实施例1所制备的“红柱石-碳化硼-氮化硅-碳化硅”四元耐火陶瓷a在热震实验后的断口微观形貌,具体实施方式为更好地理解本发明,以下将结合附图和具体实例对发明进行详细的说明。为解决现有氮化硅结合碳化硅耐火陶瓷中存在抗热震性能和耐氧化侵蚀性能差的问题,本发明提供一种“红柱石‐碳化硼‐氮化硅‐碳化硅”四元耐火陶瓷的制备方法,其通过添加红柱石和碳化硼提高耐火陶瓷的抗热震性能和耐氧化侵蚀性能。以下将通过具体的实施例来对本发明“红柱石‐碳化硼‐氮化硅‐碳化硅”四元耐火陶瓷的制备方法的优选方式进行详细地说明。实施例1“红柱石-碳化硼-氮化硅-碳化硅”四元耐火陶瓷的制备方法包括步骤:1)浆料的制备:称取质量百分比为50%的碳化硅粉(由黑碳化硅颗粒、碳化硅细粉、碳化硅微粉按照质量比10:1:1混合而成,黑碳化硅颗粒的粒径为1.0mm,碳化硅细粉的粒径为240目,碳化硅微粉的粒径为3.0μm),质量百分比为25%的硅粉(粒径为240目)、质量百分比为15%的红柱石粉(粒径为1.0mm)、质量百分比为5%的碳化硼粉(粒径为240目)、质量百分比为3%的水合氧化铝、质量百分比为2%的聚乙烯亚胺,以上原料的纯度均大于98%,将上述原料放入搅拌式混料机,干混10分钟,然后以均匀的速度加入原料总质量8%的水,搅拌2分钟出料,得到浆料。2)坯体的制备:将步骤1)所得的浆料放入真空振动浇注成型装置的漏斗内,在振动频率为60hz的振动条件下,浆料由漏斗向下流入模具,待浆料完全流进模具后再振动1分钟,最后空气中养护12小时干燥后得到成型的坯体。3)氮化处理:将步骤2)所得的坯体放入氮化炉中进行氮化处理,25℃~1000℃范围内升温速率为10℃/min;1000℃~1450℃升温速率为1℃/min,1450℃保温0.5h最后随炉冷却到室温,即可获得“红柱石‐碳化硼-氮化硅-碳化硅”四元耐火陶瓷a。图1为“红柱石-碳化硼-氮化硅-碳化硅”四元耐火陶瓷a的断口的微观形貌,可以看出,增强体碳化硅颗粒与基体结合紧密,样品呈现穿晶断裂模式,说明碳化硅颗粒的增强作用得到了充分发挥。图2为“红柱石-碳化硼-氮化硅-碳化硅”四元耐火陶瓷a在热震实验后的断口微观形貌,可以看出,耐火陶瓷经高温氧化后材料内部玻璃相增多,断口粗糙度下降,大量孔隙被填充,局部可以观察到裂纹被锚固的迹象。说明高温下红柱石和碳化硼发生相变,生成的玻璃相具有适中的粘度,且对主要相氮化硅和碳化硅有良好的润湿性。氧化膜覆盖材料孔隙和裂纹,使得氧气由通过孔隙向材料内部的快速扩散转变为通过氧化膜向材料内部的扩散过程,扩散速率大大降低,材料从而获得良好的自愈合功能,抗氧化性也明显提高。实施例2“红柱石-碳化硼-氮化硅-碳化硅”四元耐火陶瓷的制备方法包括步骤:1)浆料的制备:称取质量百分比为55%的碳化硅粉(由黑碳化硅颗粒、碳化硅细粉、碳化硅微粉按照质量比14:1:1混合而成,黑碳化硅颗粒的粒径为0.3mm,碳化硅细粉的粒径为200目,碳化硅微粉的粒径为1.0μm),质量百分比为20%的硅粉(粒径为200目)、质量百分比为10%的红柱石粉(粒径为0.3mm)、质量百分比为10%的碳化硼粉(粒径为200目)、质量百分比为2%的铝酸钙水泥、质量百分比为3%的聚乙烯醇,以上原料的纯度均大于98%,将上述原料放入搅拌式混料机,干混5分钟,然后以均匀的速度加入原料总质量6%的水,搅拌10分钟出料,得到浆料。2)坯体的制备:将步骤1)所得的浆料放入真空振动浇注成型装置的漏斗内,在振动频率为40hz的振动条件下,浆料由漏斗向下流入模具,待浆料完全流进模具后再振动2分钟,最后空气中养护36小时干燥后得到成型的坯体;3)氮化处理:将步骤2)所得的坯体放入氮化炉中进行氮化处理,25℃~1000℃范围内升温速率为10℃/min;1000℃~1450℃升温速率为1℃/min,1450℃保温0.5h最后随炉冷却到室温,即可获得“红柱石‐碳化硼-氮化硅-碳化硅”四元耐火陶瓷b。实施例3“红柱石-碳化硼-氮化硅-碳化硅”四元耐火陶瓷的制备方法包括步骤:1)浆料的制备:称取质量百分比为51%的碳化硅粉(由黑碳化硅颗粒、碳化硅细粉、碳化硅微粉按照质量比12:1:1混合而成,黑碳化硅颗粒的粒径为0.5mm,碳化硅细粉的粒径为220目,碳化硅微粉的粒径为2.0μm),质量百分比为22%的硅粉(粒径为220目)、质量百分比为11%的红柱石粉(粒径为0.5mm)、质量百分比为6%的碳化硼粉(粒径为220目)、质量百分比为5%的酚醛树脂、质量百分比为5%的聚丙烯酸铵,以上原料的纯度均大于98%,将上述原料放入搅拌式混料机,干混30分钟,然后以均匀的速度加入原料总质量10%的水,搅拌10分钟出料,得到浆料。2)坯体的制备:将步骤1)所得的浆料放入真空振动浇注成型装置的漏斗内,在振动频率为50hz的振动条件下,浆料由漏斗向下流入模具,待浆料完全流进模具后再振动2分钟,最后空气中养护24小时干燥后得到成型的坯体;3)氮化处理:将步骤2)所得的坯体放入氮化炉中进行氮化处理,25℃~1000℃范围内升温速率为10℃/min;1000℃~1450℃升温速率为1℃/min,1450℃保温0.5h最后随炉冷却到室温,即可获得“红柱石‐碳化硼-氮化硅-碳化硅”四元耐火陶瓷c。实施例4“红柱石-碳化硼-氮化硅-碳化硅”四元耐火陶瓷的制备方法包括步骤:1)浆料的制备:称取质量百分比为53%的碳化硅粉(由黑碳化硅颗粒、碳化硅细粉、碳化硅微粉按照质量比12:1:1混合而成,黑碳化硅颗粒的粒径为0.8mm,碳化硅细粉的粒径为230目,碳化硅微粉的粒径为2.5μm),质量百分比为23%的硅粉(粒径为230目)、质量百分比为12%的红柱石粉(粒径为0.8mm)、质量百分比为8%的碳化硼粉(粒径为230目)、质量百分比为1%的水合氧化铝和1%的铝酸钙水泥、质量百分比为1%的聚乙烯亚胺和1%的聚乙烯醇,以上原料的纯度均大于98%,将上述原料放入搅拌式混料机,干混20分钟,然后以均匀的速度加入原料总质量7%的水,搅拌8分钟出料,得到浆料。2)坯体的制备:将步骤1)所得的浆料放入真空振动浇注成型装置的漏斗内,在振动频率为60hz的振动条件下,浆料由漏斗向下流入模具,待浆料完全流进模具后再振动2分钟,最后空气中养护30小时干燥后得到成型的坯体;3)氮化处理:将步骤2)所得的坯体放入氮化炉中进行氮化处理,25℃~1000℃范围内升温速率为10℃/min;1000℃~1450℃升温速率为1℃/min,1450℃保温0.5h最后随炉冷却到室温,即可获得“红柱石‐碳化硼-氮化硅-碳化硅”四元耐火陶瓷d。实施例5“红柱石-碳化硼-氮化硅-碳化硅”四元耐火陶瓷的制备方法包括步骤:1)浆料的制备:称取质量百分比为54%的碳化硅粉(由黑碳化硅颗粒、碳化硅细粉、碳化硅微粉按照质量比14:1:1混合而成,黑碳化硅颗粒的粒径为1.0mm,碳化硅细粉的粒径为210目,碳化硅微粉的粒径为3.0μm),质量百分比为21%的硅粉(粒径为210目)、质量百分比为11%的红柱石粉(粒径为0.8mm)、质量百分比为7%的碳化硼粉(粒径为210目)、质量百分比为3%的水合氧化铝和2%的铝酸钙水泥、质量百分比为1%的聚乙烯亚胺和1%的聚乙烯醇,以上原料的纯度均大于98%,将上述原料放入搅拌式混料机,干混10分钟,然后以均匀的速度加入原料总质量8%的水,搅拌2分钟出料,得到浆料。2)坯体的制备:将步骤1)所得的浆料放入真空振动浇注成型装置的漏斗内,在振动频率为40hz的振动条件下,浆料由漏斗向下流入模具,待浆料完全流进模具后再振动2分钟,最后空气中养护12小时干燥后得到成型的坯体;3)氮化处理:将步骤2)所得的坯体放入氮化炉中进行氮化处理,25℃~1000℃范围内升温速率为10℃/min;1000℃~1450℃升温速率为1℃/min,1450℃保温0.5h最后随炉冷却到室温,即可获得“红柱石‐碳化硼-氮化硅-碳化硅”四元耐火陶瓷e。实施例6“红柱石-碳化硼-氮化硅-碳化硅”四元耐火陶瓷的制备方法包括步骤:1)浆料的制备:称取质量百分比为55%的碳化硅粉(由黑碳化硅颗粒、碳化硅细粉、碳化硅微粉按照质量比10:1:1混合而成,黑碳化硅颗粒的粒径为0.3mm,碳化硅细粉的粒径为200目,碳化硅微粉的粒径为1.0μm),质量百分比为20%的硅粉(粒径为200目)、质量百分比为10%的红柱石粉(粒径为0.3mm)、质量百分比为10%的碳化硼粉(粒径为200目)、质量百分比为2%的酚醛树脂、质量百分比为2%的聚乙烯亚胺和1%的聚丙烯酸铵,以上原料的纯度均大于98%,将上述原料放入搅拌式混料机,干混30分钟,然后以均匀的速度加入原料总质量6%的水,搅拌10分钟出料,得到浆料。2)坯体的制备:将步骤1)所得的浆料放入真空振动浇注成型装置的漏斗内,在振动频率为60hz的振动条件下,浆料由漏斗向下流入模具,待浆料完全流进模具后再振动1分钟,最后空气中养护20小时干燥后得到成型的坯体;3)氮化处理:将步骤2)所得的坯体放入氮化炉中进行氮化处理,25℃~1000℃范围内升温速率为10℃/min;1000℃~1450℃升温速率为1℃/min,1450℃保温0.5h最后随炉冷却到室温,即可获得“红柱石‐碳化硼-氮化硅-碳化硅”四元耐火陶瓷f。实施例1~6得到的“红柱石-碳化硼-氮化硅-碳化硅”四元耐火陶瓷a~f的性能如表1。表1检测项目抗热震性能抗氧化性能单位次%(质量增加率)测试方法1100℃水冷1000℃,500小时干燥空气样品a>501.0%样品b>501.1%样品c>501.2%样品d>500.9%样品e>500.8%样品f>501.1%sicatec75252.7%表1中样品a~f分别为实施例1~6得到的“红柱石-碳化硼-氮化硅-碳化硅”四元耐火陶瓷a~f;对比例sicatec75为市售氮化硅结合碳化硅耐火陶瓷。从表1中可以看出,本发明制得的“红柱石-碳化硼-氮化硅-碳化硅”四元耐火陶瓷与传统的氮化硅结合碳化硅耐火陶瓷相比,抗热震性能和抗氧化性能均明显改善。以上所述实施例仅表达了本发明的几种实施方式,其描述较为具体和详细,但并不能因此而理解为对本发明专利范围的限制。应当指出的是,对于本领域的普通技术人员来说,在不脱离本发明构思的前提下,还可以做出若干变形和改进,这些都属于本发明的保护范围。因此,本发明专利的保护范围应以所附权利要求为准。当前第1页12