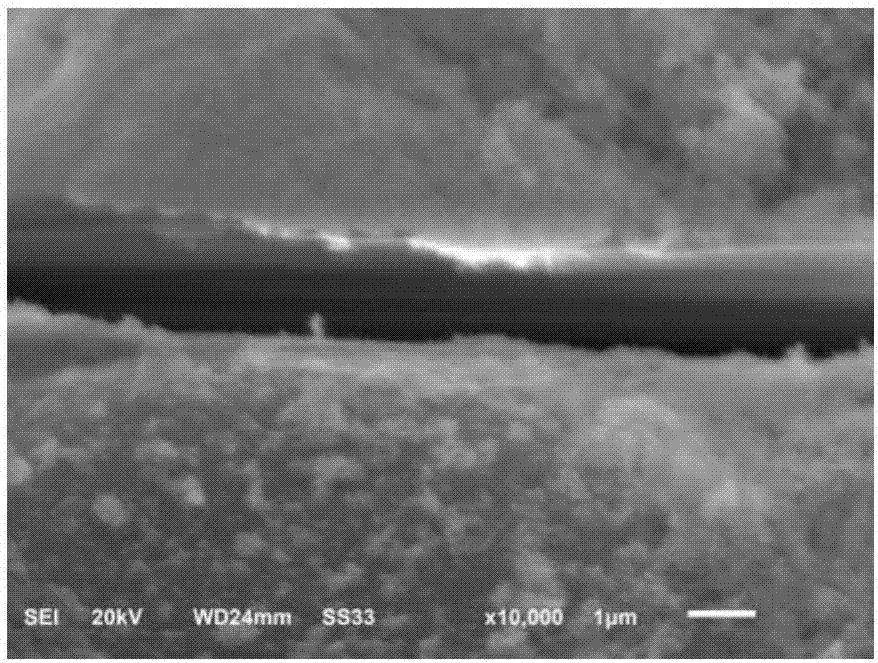
本发明涉及混凝土外加剂
技术领域:
,具体涉及一种增强型混凝土膨胀剂及其制备方法。
背景技术:
:近十几年来,随着“商品混凝土”的推广应用,高效减水剂、粉煤灰、磨细矿渣粉等有机、无机添加剂的使用日益广泛,混凝土技术不断发展,但混凝土裂缝问题一直困扰着技术人员。为获得高强甚至是超高强混凝土,其水灰比逐渐降低,必然导致混凝土发生收缩现象。人们对收缩给予了很大的关注,但引人关注的并不是收缩本身,而是由它带来的混凝土开裂现象。掺膨胀剂配制的补偿收缩混凝土是一种防止和减少混凝土开裂的有效方法,补偿收缩混凝土广泛用于地下防水、超长结构及大体积混凝土工程中,一定程度上解决了混凝土开裂的问题。随着膨胀剂需求量的日益提高,以硬石膏、铝矾土、地开石等为原料生成钙矾石膨胀源的原材料资源越来越少,随之而来的是各种原材料价格日益升高,同时各种天然矿物的开采,有悖于国家关于可持续发展的战略要求,新替代材料的研究和开发显得尤为紧迫。cn2017110832050一种持续稳定膨胀型膨胀剂的制备方法,利用偏高岭土、硫铝酸盐水泥熟料、钙矾石、钢渣等制备膨胀剂,以实现持续稳定膨胀的效果。cn2017101784772利用铝型材厂废渣合成无水硫铝酸钙膨胀剂的制备方法,称取铝型材厂废渣、高岭土、石灰石质材料或石灰石,经混合、研磨、过滤脱水、烘干等操作后制得膨胀剂。最大限度利用铝型材厂废渣。实现其循环利用。现有的柠檬酸渣的主要矿物组分为caso4,其含量高达75%,是石灰法制备柠檬酸时产生的工业废渣,渣量与产品量基本相当,排放量非常大,在未加利用前,占用了大量土地堆场,造成了极为恶劣的环境污染。微生物选矿是近几年发展起来的新工艺,生物浸矿残渣作为一种新的工业产物,其中含有一定量的重金属元素,随着排放量越来越高,如果不加以利用,必然会带来严重的生态危害。此外,市面上现有膨胀剂产品种类繁多,质量参差不齐,部分产品在补偿混凝土体积收缩的同时,劣化了混凝土的力学性能。因此,研究和开发一种解决资源浪费、补偿混凝土体积收缩、提高混凝土力学性能的膨胀剂具有重要意义。技术实现要素:为解决现有技术存在的问题,本发明提供一种增强型混凝土膨胀剂,该产品解决了柠檬酸渣及生物浸矿残渣工业利用率低、资源浪费、对生态环境造成污染等问题,同时有效改善硬化混凝土界面过渡区结构和性能,提高混凝土力学性能,并补偿混凝土服役过程中的体积收缩,具有较大的社会经济效益优势。本发明还提供了一种增强型混凝土膨胀剂的制备方法,制备方法简单,易于操作,便于大规模生产和推广。为实现上述目的,本发明采取如下的技术方案:一种增强型混凝土膨胀剂,包括以下重量百分比的组分:膨胀熟料40~65%、柠檬酸渣15~35%、金属硫化矿微生物选矿浸出渣5~15%、纳米二氧化硅10~15%、硅酸钠1~5%、硅烷偶联剂1~3%。优选地,包括以下重量百分比的组分:膨胀熟料42~60%、柠檬酸渣20~30%、金属硫化矿微生物选矿浸出渣8~12%、纳米二氧化硅10~15%、硅酸钠1~3%、硅烷偶联剂1~3%。优选地,包括以下重量百分比的组分:膨胀熟料50%、柠檬酸渣25%、金属硫化矿微生物选矿浸出渣10.4%、纳米二氧化硅10.6%、硅酸钠1.5%、硅烷偶联剂2.5%。利用膨胀组分在水化过程中产生体积膨胀来补偿水泥基材料的收缩。所述金属硫化矿微生物选矿浸出渣,主要是铜矿、金矿、铀矿等的生物浸矿残渣。利用柠檬酸渣和生物浸矿残渣,充分利用其蕴含的so3、sio2、石灰石、金属氧化物资源,在生成硫铝膨胀源体系的同时形成硅酸盐水泥石结构,能补偿混凝土收缩并增强混凝土强度,不但解决了天然原材料的消耗,而且保护了环境,具有较好的社会意义。优选地,所述膨胀熟料包括以下重量百分比的组分:77.2~78.5%的cao、7.0~8.3%的so3、3.6~6.2%的sio2、3.3~4.4%的al2o3、0.8~1.3%的fe2o3、0.12~0.96%的mgo、0.1~0.35%的b2o3、余量的杂质;其中,所述膨胀熟料中f-cao的含量为59.5~65.5%,基于所述膨胀熟料的总重量。更优选地,所述膨胀熟料包括以下重量百分比的组分:77.8%的cao、7.6%的so3、4.9%的sio2、3.8%的al2o3、1.0%的fe2o3、0.54%的mgo、0.22%的b2o3、余量的杂质;其中,所述膨胀熟料中f-cao的含量为62.5%,基于所述膨胀熟料的总重量。优选地,所述柠檬酸渣中so3含量≥50%,含水率≤0.5%,比表面积≥350m2/kg。优选地,所述金属硫化矿微生物选矿浸出渣的含水率≤0.5%,比表面积≥300m2/kg。优选地,所述硅烷偶联剂为si69和/或si75。优选地,所述膨胀熟料中碱含量为0.1~0.2%,烧失量≤1.5%,基于所述膨胀熟料的总重量。优选地,所述膨胀熟料水中7d的限制膨胀率为0.140~0.240%。依据国家标准《混凝土膨胀剂》(gb/t23439-2017)实验方法,所述膨胀熟料水中7d的限制膨胀率为0.140~0.240%。一种增强型混凝土膨胀剂的制备方法,包括以下步骤:s1.按重量百分比称取各组分,将所述膨胀熟料破碎后,粉磨至比表面积≥320m2/kg,制得重量为m的膨胀熟料粉末;s2.称取重量为2%m的步骤s1制得的膨胀熟料粉末后,与所述硅烷偶联剂混合后研磨制成料1;s3.将步骤s2制得的料1与所述柠檬酸渣、金属硫化矿微生物选矿浸出渣、纳米二氧化硅、硅酸钠,余量的步骤s1制得的膨胀熟料粉末,一起投入混合机中,关闭投料口后开始计时,搅拌5~6分钟即制得本发明所述的增强型混凝土膨胀剂。与现有技术相比,本发明的有益效果是:1、本发明提供的增强型混凝土膨胀剂在补偿混凝土服役过程中体积收缩的同时,能有效改善硬化混凝土界面过渡区结构和性能,提高混凝土抗压强度、抗折强度、抗拉强度等力学性能;2、本发明解决了柠檬酸渣及生物浸矿残渣工业利用率低、资源浪费、对生态环境造成污染等问题,具有较大的社会经济效益优势;3、本发明提供的增强型混凝土膨胀剂制备方法,具有原料易于获取、制备工艺简单的特点,提高了产品的匀质性,保障了使用效果。附图说明图1是从空白实验组中提取标准养护28d龄期的普通混凝土中砂浆组份的放大10000倍的sem图;图2是实验中提取标准养护28d龄期的掺增强型混凝土膨胀剂的混凝土中砂浆组份放大10000的sem图,所述的增强型混凝土膨胀剂来源于实施例3;图3是从空白实验组中提取的标准养护28d龄期的普通混凝土中砂浆组份的放大2000倍的sem图;图4是实验中提取标准养护28d龄期的掺增强型混凝土膨胀剂的混凝土中砂浆组份的放大2000倍的sem图,所述增强型混凝土膨胀剂来源于实施例3。具体实施方式下面将结合本发明中的附图,对本发明的技术方案进行清楚、完整地描述,显然,所描述的实施例仅仅是本发明一部分实施例,而不是全部的实施例。基于本发明中的实施例,本领域普通技术人员在没有做出创造性劳动条件下所获得的所有其它实施例,都属于本发明保护的范围。实施例1一种增强型混凝土膨胀剂,包括以下重量百分比的组分:膨胀熟料40%,柠檬酸渣30%,辉铜矿(cu2s)微生物选矿浸出渣14.5%,纳米二氧化硅10%,硅酸钠3%,硅烷偶联剂si752.5%。膨胀熟料包括如下重量百分比的组分:78.15%的cao、7.02%的so3、4.66%的sio2、3.85%的al2o3、0.99%的fe2o3、0.42%的mgo、0.21%的b2o3;膨胀熟料中f-cao的含量为63.29%。膨胀熟料中碱含量为0.16%,烧失量为0.17%,基于所述膨胀熟料的总重量;且膨胀熟料水中7d的限制膨胀率为0.187%。柠檬酸渣中so3含量为51.32%,含水率为0.21%,比表面积368m2/kg;辉铜矿(cu2s)微生物选矿浸出渣的含水率0.43%,比表面积327m2/kg。一种增强型混凝土膨胀剂的制备方法,包括以下步骤:s1.按重量百分比称取各组分,将所述膨胀熟料破碎后,粉磨至比表面积≥320m2/kg,制得重量为m的膨胀熟料粉末;s2.称取重量为2%m的步骤s1制得的膨胀熟料粉末后,与硅烷偶联剂si75混合后研磨制成料1;s3.将步骤s2制得的料1与柠檬酸渣、辉铜矿(cu2s)微生物选矿浸出渣、纳米二氧化硅、硅酸钠,余量的步骤s1制得的膨胀熟料粉末,一起投入混合机中,关闭投料口后开始计时,搅拌6分钟即制得本发明所述的增强型混凝土膨胀剂。实施例2本实施例与实施例1基本相同,不同之处在于:一种增强型混凝土膨胀剂,包括以下重量百分比的组分:膨胀熟料48%、柠檬酸渣18.5%、辉铜矿(cu2s)微生物选矿浸出渣14.7%、纳米二氧化硅14.6%,硅酸钠3%,硅烷偶联剂si751.2%。实施例3本实施例与实施例1基本相同,不同之处在于:一种增强型混凝土膨胀剂,包括以下重量百分比的组分:膨胀熟料50%,柠檬酸渣25%,辉铜矿(cu2s)微生物选矿浸出渣10.4%,纳米二氧化硅10.6%,硅酸钠1.5%,硅烷偶联剂si692.5%。膨胀熟料包括如下重量百分比的组分:77.23%的cao、7.57%的so3、5.93%的sio2、3.42%的al2o3、1.24%的fe2o3、0.23%的mgo、0.15%的b2o3;膨胀熟料中f-cao的含量为59.85%。膨胀熟料中碱含量为0.11%,烧失量为0.47%,基于所述膨胀熟料的总重量;且膨胀熟料水中7d的限制膨胀率0.234%。一种增强型混凝土膨胀剂的制备方法,与实施例1基本相同,不同之处在于:s2.称取重量为2%m的步骤s1制得的膨胀熟料粉末后,与硅烷偶联剂si69混合后研磨制成料1。实施例4本实施例与实施例1基本相同,不同之处在于:一种增强型混凝土膨胀剂,包括以下重量百分比的组分:膨胀熟料63%,柠檬酸渣15.5%,生物浸矿残渣6%,纳米二氧化硅10.1%,硅酸钠3.5%,硅烷偶联剂si691.9%。膨胀熟料包括如下重量百分比的组分:77.23%的cao、7.57%的so3、5.93%的sio2、3.42%的al2o3、1.24%的fe2o3、0.23%的mgo、0.15%的b2o3;膨胀熟料中f-cao的含量为59.85%。膨胀熟料中碱含量为0.11%,烧失量为0.47%,基于所述膨胀熟料的总重量;且膨胀熟料水中7d的限制膨胀率0.234%。一种增强型混凝土膨胀剂的制备方法,与实施例1基本相同,不同之处在于:s2.称取重量为2%m的步骤s1制得的膨胀熟料粉末后,与硅烷偶联剂si69混合后研磨制成料1。对比例1本对比例与实施例3基本相同,不同之处在于:膨胀熟料中碱含量为0.17%,烧失量为1.14%,基于所述膨胀熟料的总重量;且膨胀熟料水中7d的限制膨胀率为0.152%。对比例2本对比例与实施例3基本相同,不同之处在于:一种增强型混凝土膨胀剂,包括以下重量百分比的组分:膨胀熟料50%,柠檬酸渣25%,辉铜矿(cu2s)微生物选矿浸出渣10.4%,二氧化硅10.6%,硅酸钠1.5%,硅烷偶联剂si692.5%。一种增强型混凝土膨胀剂的制备方法,与实施例3基本相同,不同之处在于:s3.将步骤s2制得的料1与柠檬酸渣、辉铜矿(cu2s)微生物选矿浸出渣、二氧化硅、硅酸钠,余量的步骤s1制得的膨胀熟料粉末,一起投入混合机中,关闭投料口后开始计时,搅拌6分钟即制得本发明所述的增强型混凝土膨胀剂。对比例3本对比例与实施例3基本相同,不同之处在于:一种增强型混凝土膨胀剂,包括以下重量百分比的组分:膨胀熟料50%,硬石膏25%,辉铜矿(cu2s)微生物选矿浸出渣10.4%,纳米二氧化硅10.6%,硅酸钠1.5%,硅烷偶联剂si692.5%。一种增强型混凝土膨胀剂的制备方法,与实施例3基本相同,不同之处在于:s3.将步骤s2制得的料1与硬石膏、辉铜矿(cu2s)微生物选矿浸出渣、纳米二氧化硅、硅酸钠,余量的步骤s1制得的膨胀熟料粉末,一起投入混合机中,关闭投料口后开始计时,搅拌6分钟即制得本发明所述的增强型混凝土膨胀剂。对比例4本对比例与实施例3基本相同,不同之处在于:一种增强型混凝土膨胀剂,包括以下重量百分比的组分:膨胀熟料50%,柠檬酸渣25%,硅灰10.4%,纳米二氧化硅10.6%,硅酸钠1.5%,硅烷偶联剂si692.5%。一种增强型混凝土膨胀剂的制备方法,与实施例3基本相同,不同之处在于:s3.将步骤s2制得的料1与柠檬酸渣、硅灰、纳米二氧化硅、硅酸钠,余量的步骤s1制得的膨胀熟料粉末,一起投入混合机中,关闭投料口后开始计时,搅拌6分钟即制得本发明所述的增强型混凝土膨胀剂。对比例5本对比例与实施例3基本相同,不同之处在于:一种增强型混凝土膨胀剂,包括以下重量百分比的组分:膨胀熟料50%,柠檬酸渣25%,辉铜矿(cu2s)微生物选矿浸出渣10.4%,纳米二氧化硅10.6%,硅酸钠1.5%,硅烷偶联剂kh-5502.5%。一种增强型混凝土膨胀剂的制备方法,与实施例3基本相同,不同之处在于:s2.称取重量为2%m的步骤s1制得的膨胀熟料粉末后,与硅烷偶联剂kh-550混合后研磨制成料1s3.将步骤s2制得的料1与柠檬酸渣、辉铜矿(cu2s)微生物选矿浸出渣、纳米二氧化硅、硅酸钠,余量的步骤s1制得的膨胀熟料粉末,一起投入混合机中,关闭投料口后开始计时,搅拌6分钟即制得本发明所述的增强型混凝土膨胀剂。试验例1将实施例1~实施例4,对比例1~对比例5制得的膨胀剂,以及市售膨胀剂按如下表1所示的配合比(kg/m3)进行混凝土试验:表1混凝土试验其中,水泥为42.5级普通硅酸盐水泥,粉煤灰为ⅱ级粉煤灰,矿渣粉为s95级粒化高炉矿渣粉,砂的细度模数为2.7,石子为5~31.5mm连续级配碎石,减水剂为胶凝材料重量百分比的掺量。各胶凝材料主要化学组成如下表2所示(wt,%):表2各胶凝材料的主要化学组分样品名称loisio2al2o3fe2o3caomgoso3水泥3.7825.755.783.9854.292.014.15粉煤灰2.7149.8925.244.025.181.18/矿粉7.9728.7110.080.5943.765.88/对使用实施例1~实施例4、对比例1~对比例5制得的膨胀剂,以及市售膨胀剂配制的混凝土进行水中14d和空气中28d限制膨胀率、28d抗压强度、抗折强度及轴心抗拉强度测试,测试结果如下表3所示:表3混凝土特性测试从上表3中数据可以看到,实施例1~实施例4中的膨胀剂制备的混凝土,水中养护14d和空气中养护28d的限制膨胀率、以及混凝土28d抗压强度、抗折强度和轴心抗拉强度均高于空白实验组、高于对比例1~对比例5中的膨胀剂制备的混凝土;而市售膨胀剂虽能从一定程度上补偿混凝土体积收缩,但劣化了混凝土的力学性能。对使用市售膨胀剂制备得到的混凝土,及使用实施例3所得的增强型膨胀剂制得得到的混凝土进行扫描电镜分析;结合图1~图4,可以看到掺入该种增强型混凝土膨胀剂后,混凝土更致密,且骨料与胶凝材料界面过渡区有填充物,界面更密实。综合以上试验数据及其对比结果可知,本发明所述的增强型混凝土膨胀剂不但能很好地补偿混凝土的体积收缩,且能显著改善混凝土力学性能。试验例2依据国家标准《混凝土膨胀剂》(gb/t23439-2017)实验方法,对实施例1~实施例4以及市售膨胀率胶砂检测,测试结果如下表4:表4膨胀剂性能测试从上表4中测试数据可以看到,实施例1~实施例4制得的膨胀剂的技术参数均高于国家标准中ⅱ型膨胀剂的技术要求,表明其能产生体积膨胀,抑制水泥基材料的自身体积收缩。以上实施例仅示例性说明本发明的原理及其功效,以及部分技术方案的实施例,而非对其的限制,本行业的技术人员应该了解,本发明不受上述实施例的限制,在不脱离本发明精神和范围的前提下,可以对其中部分或全部技术特征进行各种变化和改进,但这些修改或变化都将落入要求保护的本发明范围内。当前第1页12