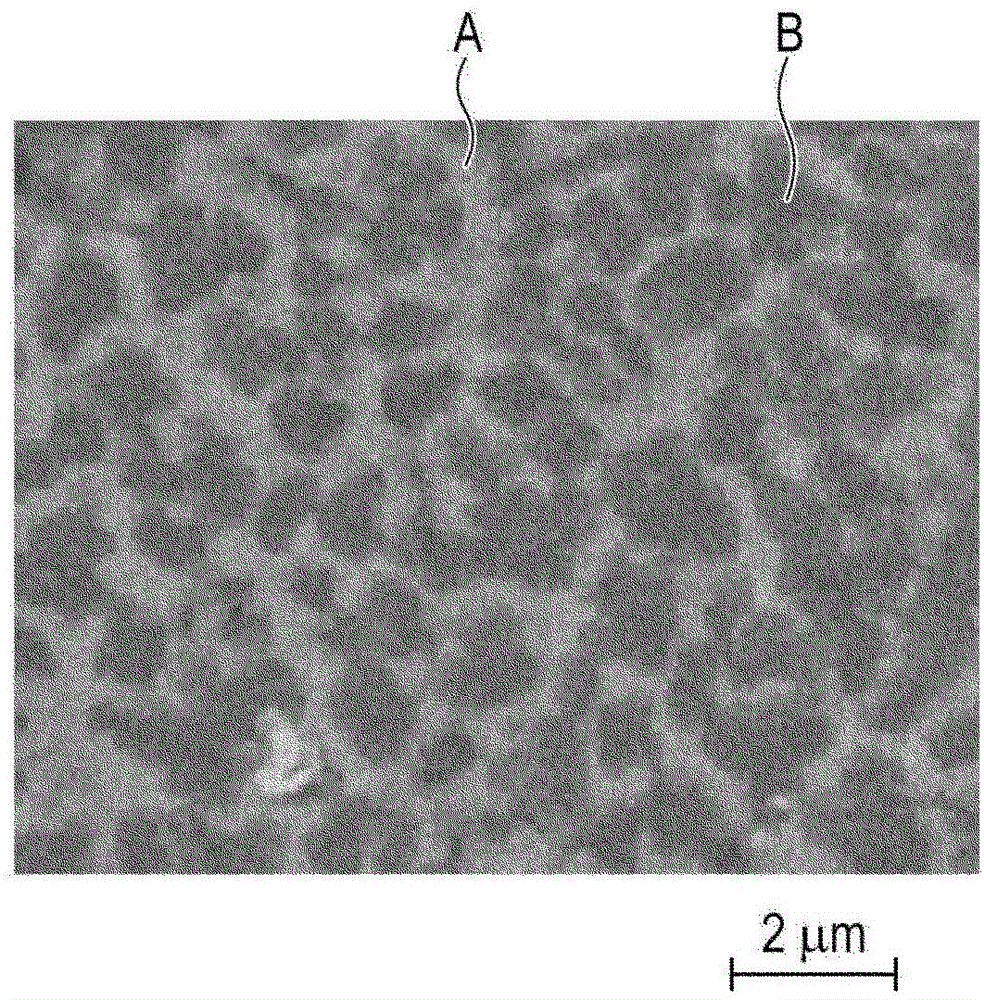
本公开涉及一种三维造型方法,该方法包括基于三维形状数据用能量束来照射粉末造型材料,以熔合和固化造型材料以进行造型。
背景技术:
:为了生产小批量的各种金属部件或具有复杂形状的金属部件,已经推进了使用粉末床熔合方法的三维造型技术的开发。该技术通过以下方法来形成三维物体:基于从造型对象物的三维形状数据生成的切片数据,来进行利用能量束的扫描粉末造型材料层的工艺,以局部熔合/固化多层造型材料。作为能量束,使用激光束、电子束等。近年来,已经检验了使用这种三维造型方法对难以加工的陶瓷材料(诸如碳化硅)进行造型。然而,诸如碳化物、硼化物和氮化物之类的陶瓷具有技术缺点,即当将能量快速投入其中时大多数陶瓷在没有熔合的情况下升华,或者在熔合和固化中没有结晶而变脆。轻质性、耐磨性、耐热冲击性、化学稳定性等优异并且被预期用于广泛领域的碳化硅是在常压下不具有熔点并且在2545℃(关于温度值,有各种观点,例如2700℃。)附近升华的材料。日本专利公开号2003-53847(专利文件1)提出了一种包括使用硅和碳化硅的混合粉末作为原料的方法,作为使用粉末床熔合方法来生产含有碳化硅的造型制品的方法。根据该方法,可以通过熔合和固化硅来生产包含硅和碳化硅的复合材料的造型制品。此外,pct日文翻译专利公开号2016-527161(专利文件2)公开了一种能够利用瞬时液相烧结来造型的混合材料的候选物,例如共晶或包晶。作为生产含有碳化硅的造型制品的造型材料的候选物,示例了碳化硅、氧化铝、稀土氧化物和二氧化硅的混合物,碳化硅、氮化铝和稀土氧化物的混合物,以及碳化硅和金属锗的混合物。然而,对于通过专利文件1的方法生产的造型制品,由于激光照射引起的快速加热使碳化硅升华、硅和碳化硅之间的边界部分中的接合弱的等原因,要获得的造型制品是脆性的。就专利文件2中描述的材料而言,二氧化硅在1900℃下分解成一氧化硅和氧气,氮化铝在2200℃下升华,金属锗在2400℃或更低的温度下沸腾。因此,推测即使当将材料和具有2545℃的升华点的碳化硅混合并一起加热时,与碳化硅混合的材料在碳化硅熔合之前挥发或沸腾,因此并未真正获得含有共晶或包晶的造型制品。可以认为,专利文件2中获得的造型制品也是脆性造型制品,在该造型制品中,如专利文件1,碳化硅和其它组成之间的边界部分中的接合是弱的。技术实现要素:为了解决上述缺点,一种造型方法包括:基于造型对象物的形状数据,利用能量束照射含有碳化硅和金属硼化物的粉末,以进行造型,其中金属硼化物具有低于碳化硅的升华点的熔点。参考附图,根据以下示例性实施方案的描述,其它特征将变得明显。附图的简要说明图1是实验中生产的样品1的抛光表面的电子显微照片。图2是实验中使用的碳化硅粉末的电子显微照片。图3是实验中使用的二硼化铬粉末的电子显微照片。图4是可以应用根据本公开的造型方法的三维造型装置的示意图。图5是示出在实验中产生的样品的形状的透视图。具体实施方式在下文中,参考附图详细描述本公开的实施方案。首先,参考图4描述可以应用根据本公开的造型方法的造型装置。造型装置100具有能够通过气体引入机构114和排气机构113控制内部气氛的腔室101。腔室101具有用于造型三维物体的造型容器120和粉末层形成机构106,该粉末层形成机构106用于通过在造型容器120内部散布作为造型材料的粉末(下文中有时简称为造型材料或粉末)来形成粉末层111。排气机构113可以具有压力调节机构(诸如蝶形阀),以便调节压力,或者可以配置成能够由于气体供应和随气体供应(通常称为吹气更换)而带来的压力增加而调节腔室101中的气氛。造型容器120的底部包括能够通过升降机构108以在竖直方向上改变位置的平台107。升降机构108的移动方向和移动量由控制部115控制,且对应于要形成的粉末层111的层厚度来确定平台107的移动量。在平台107的造型表面侧,设置有用于设定基板109的结构(未示出)。基板109是包含可熔合材料(诸如不锈钢)的板。当熔合和固化第一粉末层时,表面与造型材料熔合,从而形成将造型制品固定到基板109的结构。因此,可以保持造型制品,使得在造型期间造型制品在基板109上的位置不会位移。在造型完成之后,基板109与造型制品机械分离。粉末层形成机构106具有存储粉末材料的粉末存储部和将粉末材料供应到造型容器120的供应机构。此外,可以在基板109上设置用于使粉末层平整到设定厚度的刮板或/和辊的任一或两者。造型装置100还具有用于使造型材料熔融(malting)的能量束源102、用于使能量束112双轴扫描的扫描镜103a和103b、以及用于将能量束会聚到照射部分的光学系统104。由于从腔室101的外部发射能量束112,因此在腔室101中设置用于将能量束112引入内部的引入窗口105。根据由控制部115获取的造型对象物的三维形状数据或造型材料的特征,通过控制部115来控制能量束112的功率密度和扫描位置。预先调整造型容器120和光学系统104的位置,使得束直径通过聚焦在粉末层111的表面上而为最小直径。表面上的束直径影响造型精度,因此其可以设定为30至100μm。接下来,描述造型方法。首先,将基板109设定在平台107上,然后用非活性气体(诸如氮气或氩气)置换腔室101的内部。当置换完成时,粉末层111通过粉末层形成机构106形成在基板109上。粉末层111形成有对应于从造型对象物的三维形状数据中生成的切片数据的切片间距(即层叠间距)的厚度。当粉末中含有的颗粒尺寸过小时,颗粒聚集,从而不能形成具有均匀厚度的粉末层。当颗粒的尺寸过大时,熔合需要高能量,因此造型变得困难。因此,粒径可以是约数微米至数十微米。粉末层的每层厚度影响造型精度,因此可以为约30至100μm。在此,描述用于测量本公开中的粉末的粒径的方法。粉末中含有的颗粒的粒径具有一定范围的分布,并且规定了中值粒径和最大粒径。根据jisr6001-2“bondedabrasives-determinationanddesignationofgrainsizedistribution”,根据工业中已经标准化的粒径评估方法,通过电阻法测量sic。根据jisz8832“particlesizedistributionmeasuringmethod-electricalsensingzonemethod”测量除sic之外的单硼化铬、二硼化铬等的粒径。接下来,使能量束112根据切片数据扫描,并且通过发射激光熔合预定区域的粉末。对于能量束源102,可以使用能够输出造型材料具有50%以上的高吸收率的波长的能量的能量束源。特别是在造型中,由于产生熔合金属硼化物包围碳化硅周边的状态,因此可以使用金属硼化物具有高吸收率的波长范围的能量束。当造型材料是二硼化铬时,具有1000至1120nm波长的半导体光纤激光器是合适的。能量束(激光束)112可以设定为如下水平的能量强度,在该水平的能量强度下,用光束照射的区域的粉末熔合并固化,使得颗粒彼此在数毫秒内粘结。顶层的粉末层被分成用光束照射以被熔合和固化的区域和未用光束照射且仍含有粉末的区域。在用光束照射的区域中,造型所需的条件是不仅使表面层熔合和固化,而且在一定程度上使紧接在表面层下面的层熔合和固化。当紧接在表面层下面的层的熔合不充分时,造型可能导致各层的剥离,从而获得具有低强度的造型制品。在直接放置在基板109上的第一粉末层的熔合和固化中,需要同时熔合基板109的表面,因此能量束的照射条件是考虑到基板的热容量、导热性等而设定的。随后,通过升降机构108使造型平台107对应于层叠间距降低,将粉末铺展在已用能量束112扫描的层上以形成新的粉末层,然后用能量束112进行扫描和照射。如上所述,在用能量束112照射的区域中,先前用能量束112扫描的层的表面也再次熔合和固化。当紧接在新粉末层中用能量束112照射的区域下方的区域是已经熔合并固化的区域时,在新粉末层的光束照射区域中,在新粉末层的光束照射区域和先前熔合和固化的区域之间的边界部分中,材料被混合并固化,以彼此结合。当重复这些操作时,可以形成造型制品110。实施例将与碳化硅混合的粉末材料随后,基于实验描述适于生产包含碳化硅的三维物体的与碳化硅混合的粉末材料。本公开通过将碳化硅粉末与和碳化硅产生共晶或亚共晶的金属硼化物粉末混合以形成造型粉末,然后生产含有碳化硅和金属硼化物的共晶或亚共晶的造型制品,来实现具有接近碳化硅单一物质强度的强度的造型制品。在此,描述了共晶/亚共晶。材料x和材料y的混合物,诸如金属,具有熔点低于每种材料的熔点的材料比。在这种情况下,熔点最低的材料比被称为共晶组成,且该熔点被称为共晶温度。温度从等于或高于共晶组成下的共晶温度的温度降低的状态是在熔点以上为液相,并且是材料x和材料y在低于熔点时同时沉积的状态。因此,材料x和材料y形成包含精细沉积相并具有被称为薄片结构等的层状结构和高强度的共晶体。接下来,考虑在材料x和材料y的混合物中包含比共晶组成更大量的材料x的情况。在这种情况下,该状态在熔点以上时是液相。当温度从熔点降低时,材料x首先固化并且材料x沉积(称为初晶)至共晶温度。当温度降低至共晶温度时,除沉积材料x的晶体之外的液相部分具有共晶组成。当温度从该状态降低到共晶温度以下时,材料x和材料y同时沉积。更具体地,与从一开始就从共晶组成开始的情况相比,形成如下的结构,在该结构中,与早先开始的材料x沉积的程度相对应地混合了大量生长的晶体。当材料y的量大于共晶组成的量时,材料y的晶体大量生长。这些状态被称为亚共晶。这个实验检验了诸如粉末的组成或粒径的条件,在该条件下可以获得共晶态或大碳化硅晶体的亚共晶态,以获得接近于碳化硅的物理性质的物理性质。粉末1作为碳化硅,准备了具有14.7μm的中值粒径的碳化硅粉末(由pacificrundumco.,ltd.制造,商品名nc#800)。图2是其电子显微照片。作为将被混合的硼化铬,准备了具有2200℃的熔点的二硼化铬粉末(由japannewmetalsco.,ltd.制造,商品名crb2-o,约5μm的中值粒径)。图3是其电子显微照片。将粉末以碳化硅:二硼化铬=3:1的摩尔比共混,以形成产生共晶或亚共晶的组合物粉末,然后在球磨机中混合以形成粉末1。将用于确定摩尔比的方法和混合方法同样地应用于其他粉末。本文使用的中值粒径与中值粒度同义,是指具有50%的粉末频度累积的粒径。粉末2将与粉末1中相同的碳化硅粉末和具有约2100℃的熔点的单硼化铬粉末(由japannewmetalsco.,ltd.制造,商品名crb-o,约9μm的中值粒径)以碳化硅:单硼化铬=3:1的摩尔比共混,然后混合以形成粉末2。粉末3将与粉末1中相同的碳化硅粉末和具有约2400℃的熔点的二硼化钒粉末(约4μm的中值粒径,由japannewmetalsco.,ltd.制造,商品名vb2-o)以碳化硅:二硼化钒=1:1的摩尔比共混,然后混合以形成粉末3。粉末4将与粉末1中相同的碳化硅粉末和具有约2920℃的熔点的二硼化钛粉末(由japannewmetalsco.,ltd.制造,商品名tib2-n,约4μm的中值粒径)以碳化硅:二硼化钛=1:1的摩尔比共混,然后混合以形成粉末4。粉末5将与粉末1中相同的碳化硅粉末和具有约3200℃的熔点的二硼化锆(由japannewmetalsco.,ltd.制造,商品名zrb2-o,约5μm的中值粒径)以碳化硅:二硼化锆=1:1的摩尔比共混,然后混合以形成粉末5。表1共同显示了每种粉末的组成。表1造型制品的生产使用所准备的粉末和图4中所示的造型装置来进行造型。具体地,对于每种粉末,在含有不锈钢的基板109上生产八个具有10mm×10mm底面积的长方体形状的造型制品。图5示出了在完成造型之后的八个造型制品121至128和基板109的透视图。使用具有1090nm波长的半导体光纤激光器作为能量束源102,以100w的激光功率和40μm的照射间距进行照射。适合于造型的照射能量根据不同粉末材料类型而变化,因此在改变用于每个造型制品121至128的扫描速率的同时进行造型,这也用作条件的设定。扫描速率设定为以下八种扫描速率:100毫米/秒、250毫米/秒、500毫米/秒、667毫米/秒、1000毫米/秒、1333毫米/秒、1667毫米/秒和2000毫米/秒。以50μm的层叠间距造型20层,从而获得具有约1mm高度的长方体。使用设置在以固定速率旋转的台上的砂纸#400至#4000,以与基板109一体的形状将造型制品的表面逐步抛光。然后,评估是否保持造型制品的形状。此外,从粉末的造型制品中可以用砂纸#4000抛光的造型制品中选择具有最少缺陷的造型制品作为粉末形成的样品,然后通过电子显微镜进行表面观察以确认共晶/亚共晶的存在。表2显示了结果。每个项目的评估标准如下:造型适当性:能够完成20层造型的情况:a在造型中途无法进行造型的情况:b抛光适当性:能使用所有砂纸#400至#4000进行抛光的情况:a使用任何一种砂纸在抛光过程中形状坍塌的情况:b总体判断:将造型适当性和抛光适当性均评估为a的情况:a将造型适当性和抛光适当性中的至少任一个评估为b的情况:b表2材料粉末造型适当性抛光适当性共晶/亚共晶总体判断样品1粉末1aa存在a样品2粉末2aa存在a样品3粉末3aa存在a样品4粉末4ab不清楚b样品5粉末5ab不清楚b所有粉末都能够造型。然而,在使用粉末4和5的造型制品中,空缺在外观上是显著的,并且在使用砂纸#400的抛光中造型制品从顶层塌陷。图1是使用粉末1的造型制品的抛光表面的电子显微照片。发现存在浅色区域a和深色区域b。当使用edx(能量色散x射线光谱)识别构成每个区域的元素时,从区域a中主要检测出铬,并且从区域b中主要检测出硅。另外,当通过xrd(x射线衍射)分析时,其表明了在区域a中检测到的铬包含在二硼化铬中,并且在区域b中检测到的硅包含在碳化硅中。当使用由mathworks(商品名:matlab)制造的图像处理软件通过图像处理分析图1,然后计算包含硅的区域b的晶粒尺寸时,晶粒尺寸在0.2至1.32μm的范围内。具有区域b的最大频度(具有最高丰度比的晶粒尺寸)的晶粒尺寸为0.5至0.6μm。这表明区域b小至14.7μm的1/10以下,14.7μm是作为原料的图2的碳化硅粉末的中值粒径。当将碳化硅粉末与二硼化铬粉末的混合比由摩尔比=3:1转换成体积比时,碳化硅的体积为二硼化铬体积的约2.8倍。图1的图像分析结果显示,造型后含有硅的区域b的积分面积是含有铬的区域a的积分面积的1.34倍。发现碳化硅的比例减少至混合粉末的大约一半。如果减少量仅由碳化硅的挥发所导致,则体积应为造型前体积的1/1000以下,且造型制品中碳化硅的含量应为其1/1000以下,因为晶粒尺寸是造型前晶粒尺寸的1/10以下。然而,造型后碳化硅比例的减少仍然是混合粉末的大约一半。因此,很难理解被认为等同于图1中的碳化硅的区域b的尺寸仅由图2的碳化硅的颗粒表面的挥发所导致。于是,推测被认为等于图1中的碳化硅的区域b是沉积的结果。当理解为样品1的造型制品含有碳化硅和二硼化铬的共晶或亚共晶时,不会产生矛盾。基于这样的概念,在本公开中,基于xrd(x射线衍射)、电子显微照片,和edx(能量色散x射线光谱)的结果确定存在或不存在碳化硅和金属硼化物的共晶或亚共晶的生成。基于上述评估标准的评估结果表明,在使用粉末1至3造型的样品1至3中生成了共晶或亚共晶。更具体地,发现当使用碳化硅与二硼化铬、一硼化铬和二硼化钒中的任一种的混合粉末进行造型时,得到造型制品,在该造型制品中,生成了与碳化硅的共晶或亚共晶,并且该造型制品具有使得表面可以抛光的强度。另一方面,使用粉末4和5造型的样品4和5的强度过低,使得即使改变光束照射条件时样品4和5也不能承受用砂纸#400进行抛光。上述结果表明,当使用碳化硅和具有低于碳化硅升华点的熔点的金属硼化物的混合物时,可以生产具有承受抛光处理的强度的造型制品。换句话说,使用碳化硅和具有高于碳化硅升华点的熔点的金属硼化物的混合物,不能生产具有承受抛光处理的强度的造型制品。可以认为以下假设是其原因。首先,以具有低于碳化硅升华点(2545℃)的熔点的二硼化铬(熔点2200℃)为例。当向碳化硅和二硼化铬的混合粉末发射激光束以提高温度时,二硼化铬首先达到熔点并熔合。然后,可以容易地想象,碳化硅颗粒表面被熔合的二硼化铬覆盖。认为碳化硅单独升华,但在两种物质之间的界面中熔合。因此,碳化硅的熔合从碳化硅和二硼化铬的熔融物质之间的界面发展。据推测,即使当温度升高到达碳化硅的升华点时,挥发的碳化硅也熔进熔合的二硼化铬,从而限制了挥发。因此,认为即使当通过激光束照射温度超过碳化硅的升华点至高温时,碳化硅和二硼化铬熔合的状态也得以保持。此后,推测当激光束的照射时间结束,使得照射区域的温度开始降低时,碳化硅和二硼化铬各自开始沉积,以形成图1中的两种物质没有间隙地混合的状态。接着,以作为具有高于碳化硅升华点(2545℃)的熔点的金属硼化物的二硼化钛(熔点2920℃)为例。当通过用激光束照射碳化硅和二硼化钛的混合物来升高温度时,温度在达到二硼化钛的熔点之前达到碳化硅的升华点。因此,首先开始碳化硅的升华,然后二硼化钛开始熔合。由于表面蒸发,碳化硅的颗粒进入压力增加的状态,因此熔合的二硼化钛和碳化硅粉末的接触非常有限,并且碳化硅在二硼化钛熔合期间也继续升华,因此两种物质的接触面积不会增加。由此,碳化硅的熔合非常有限,并且即使在冷却时碳化硅也几乎不沉积。因此,不能获得在没有间隙的情况下存在共晶或亚共晶的状态的造型制品,并且认为获得了脆性造型制品,在该脆性造型制品中在碳化硅和二硼化钛之间的边界部分中的结合是弱的。从上述假设和实验结果可以认为,当用含有碳化硅粉末和具有低于碳化硅升华点的熔点的金属硼化物粉末的粉末材料进行造型时,获得了如下造型制品,在该造型制品中,生成了共晶或亚共晶,且边界部分中的结合是强的,并且该造型制品可以承受抛光处理。碳化硅粉末与金属硼化物粉末的混合比接下来,使用混合有碳化硅粉末和二硼化铬粉末的粉末来研究适合于造型制品的碳化硅和二硼化铬的混合比。对于碳化硅粉末和二硼化铬粉末,使用与粉末1同样的粉末。当碳化硅和二硼化铬的总混合粉末为100%时,使用以摩尔比计以7.0%、10%、30%、50%、65%和70%的比例含有二硼化铬粉末的粉末作为粉末6至11。以与使用粉末1至5的造型相同的方式,使用粉末6至11来生产和评估造型制品。表3显示了结果。在摩尔比的列中,显示了(碳化硅的摩尔%)/(二硼化铬的摩尔%)的值。表3对于样品6,能够进行造型,但是当用砂纸#400抛光时顶层坍塌。对于样品11,在造型期间在表面上形成球状突起,并且在粉末层形成中发生麻烦,因此不可能继续造型。当分析球状异物时,发现异物是二硼化铬。这被认为是熔合二硼化铬的纯度增加,因此表面上形成的液滴的表面张力增加,使得具有增大直径的那些固化。在样品7至10中,令人满意地进行造型和抛光。以上结果表明,当总混合粉末为100%时,以摩尔比计以10%以上且65%以下的比例含有二硼化铬的粉末适用于造型制品。更具体地,发现其中碳化硅与二硼化铬的摩尔比在0.54≤碳化硅/二硼化铬≤9.00的范围内的混合粉末适用于造型制品。碳化硅的粒径接下来,在使用碳化硅和二硼化铬的混合粉末的造型中,研究了可以进行造型的碳化硅粉末的粒径范围。对于碳化硅粉末,使用五种粉末:由pacificrundumco.,ltd.制造的商品名nc#280、nc#320和nc#4000,以及由fujimiincorporated.制造的商品名gc#6000和gc#8000。对于二硼化铬粉末,使用与粉末1同样的粉末。将每种碳化硅粉末与二硼化铬粉末共混以具有碳化硅:二硼化铬=3:1的摩尔比,然后在球磨机中混合30分钟,以生产粉末12至16。在与样品1至5相同的条件下,使用粉末12至16来生产样品12至16,其为约1mm厚的造型制品。此时,由于层叠间距需要大于粒径,所以对应于所使用的粉末的粒径来恰当地设置层叠间距。用砂纸#400至#4000依次抛光所获得的样品12至16,然后以与样品1至5中相同的方式评估关注是否存在能够在上述激光照射条件下保持造型制品形状的样品。表4显示结果。这里,将粉末铺设和造型质量均判断为a的情况判断为a,并将粉末铺设和造型质量中任何一个判断为b的情况判断为b.表4在使用粉末13的造型中,当层叠间距为50μm时发生厚度不均匀,并且发生不良粉末铺设,使得不能覆盖下层。然而,当层叠间距为70μm时,能够进行粉末铺设,并且在上述激光照射条件下获得能够抛光的造型制品。另一方面,在使用粉末12的造型中,当层叠间距为70μm时发生不良的粉末铺设。当层叠间距为90μm时,可以进行粉末铺设,但是不能获得具有使得可以抛光造型制品的强度的造型制品。在使用粉末15的造型中,当层叠间距为30μm时,可以进行粉末铺设,并且能够生产能够被抛光的造型制品。在使用粉末16的造型中,粉末在粉末铺设中聚集,从而发生厚度不均匀,因此不能实现三层或更多层的层叠。根据以上结果,考虑了适合于造型的粒径。首先,从最大粒径和层叠间距与粉末铺设结果之间的关系可以发现,层厚度小于最大粒径的粉末铺设是可能的。当推定该现象时,在形成粉末层中,对应于一层的造型(层叠间距)降低造型平台107,然后铺设粉末材料。彼时形成的粉末层的厚度大于层叠间距,因为对应于当通过先前的激光照射使下层熔合和固化时粉末被熔合以被熔融在一起的程度,粉末之间的空间被关闭,并且块体小。因此,认为能够以70μm的层叠间距没有问题地进行由pacificrundumco.,ltd.制造的具有98μm的最大粒径的nc#320的粉末铺设,因为通过实际粉末铺设形成的粉末层的厚度接近最大粒径。为了增加造型制品层叠方向上的强度,不仅需要熔合将被激光束(能量束)照射其表面的层,而且需要再次熔合已用激光束辐照的紧接着该层下面的层的表面,以加强层之间的结合。由于从表面侧发射激光束用于加热,因此在粉末表面和内部之间产生温差。当再熔合紧接着粉末层下面的已经熔合并固化部分时,在粉末层的厚度变大时,需要进一步提高粉末层表面的温度。认为当提高粉末层表面的温度以再熔合紧接着粉末层下面的层时,粉末层的表面过热,而碳化硅进一步升华,由此挥发成分增加,且因此不能形成共晶或亚共晶。另一方面,通常已知的是,当粒径减小时,更可能发生聚集。表4中所示的实验结果表明,在碳化硅和二硼化铬的情况下,当碳化硅的中值粒径小于2μm时,难以均匀地铺设粉末。从上面的描述得出结论,当碳化硅的中值粒径在2μm以上且41.1μm以下的范围内时,可以由碳化硅和二硼化铬来生产含有共晶或亚共晶的造型制品。粉末材料的改性除非粉末材料中包含的两种粉末均匀混合,否则在要生产的造型制品中可能发生组成不均匀,从而在物理性质中发生不均匀。因而,材料粉末可以不是碳化硅粉末和金属硼化物粉末的混合粉末,并且可以包含含有碳化硅和金属硼化物的颗粒群。具体地,可以使用通过金属硼化物镀碳化硅颗粒获得的那些。这次,关注于碳化硅和二硼化铬,用碳化硅和单硼化铬以及碳化硅和硼化钒的双组分体系进行检验。但是,适当地添加各种含硼物质,(诸如硼化钛、硼化镧、碳化硼和锆石硼化物)不偏离本申请。这些含硼物质在某些情况下根据材料具有例如降低比重和提高强度的效果,并且可以适当添加。另外,不排除粉末材料中含有杂质水平的除碳化硅和含硼物质以外的物质的情况。在该申请中,具有5μm的中值粒径的粉末用于二硼化铬,具有9μm的中值粒径的粉末用于单硼化铬。这是因为仅使用市售粉末,并且其使用不是技术限制。它被认为是可以通过检验来适当选择的要素。作为造型中使用的粉末材料,描述了碳化硅粉末和金属硼化物粉末的混合粉末,但是可以使用含有包含碳化硅和金属硼化物的颗粒的粉末。此外,尽管这次基于使用能量束的粉末床熔合方法给出了说明,但是可以使用经由相同热经历的造型方法而不限于该技术。例如,包括同时喷射气体和粉末材料然后用激光进行熔合的定向能量沉积方法也是可用的。实现了生产迄今为止难以处理和造型的具有接近碳化硅的物理性质的造型制品。例如,碳化硅和金属硼化物的共晶体或亚共晶体可用于要求具有高耐热温度和高导热率的热交换器、发动机喷嘴等。虽然已经参考示例性实施方案描述了本公开,但是应该理解,本发明不限于所公开的示例性实施方案。以下权利要求的范围应被赋予最广泛的解释,以包含所有这些修改和等同的结构和功能。当前第1页12