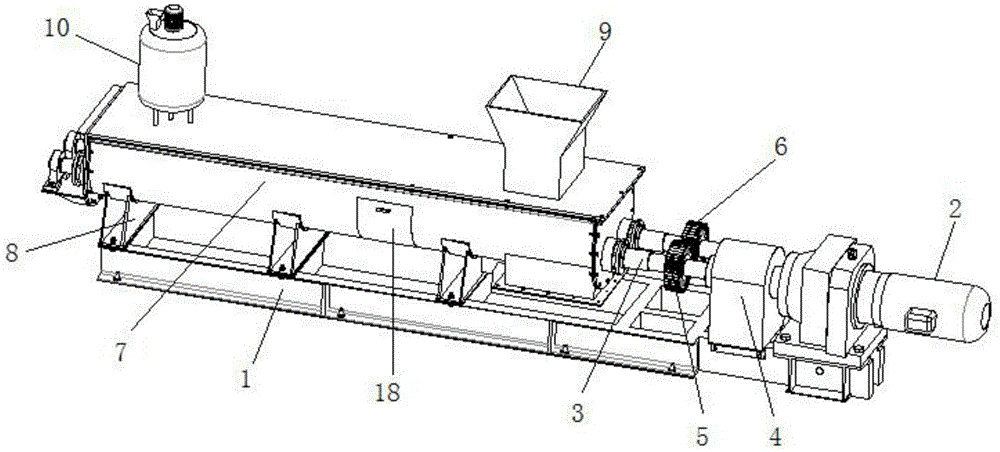
本发明涉及混凝土原料制备
技术领域:
,尤其涉及一种抗腐蚀混凝土结构的原料制备工艺及其专用搅拌装置。
背景技术:
:混凝土是指由胶凝材料将骨料胶结成整体的工程复合材料的统称,通常混凝土结构的制作是用水泥作胶凝材料,砂、石作骨料,与水、外加剂、掺合料按一定比例配合,经搅拌而得的水泥混凝土,也称普通混凝土,它广泛应用于土木工程。在混凝土中,砂、石起骨架作用,称为骨料;水泥与水形成水泥浆,普通混凝土浆包裹在骨料表面并填充其空隙。在硬化前,水泥浆起润滑作用,赋予拌合物一定和易性,便于施工,水泥浆硬化后,则将骨料胶结成一个坚实的整体;混凝土的技术性质在很大程度上是由原材料的性质及其相对含量决定的,同时也与施工工艺中的搅拌、成型和养护有关,因此,了解其原材料的性质、作用及其质量要求,合理选择原材料,这样才能保证混凝土的质量,在建筑物的梁、柱结构中采用高强度混凝土优越性非常明显,在同等条件下,混凝土强度越高,其结构构件的尺寸、体积就会相对减少,混凝土用量也将成比例地减少,同时由于结构断面的减少,不但使建筑物在观感上给人以舒适的感觉,而且增加了建筑物的实际使用面积,经济效益非常明显;目前的混凝土大多是普通的水泥混凝土,这种混凝土的抗腐蚀较差,很难适应一些酸碱的复杂环境,这些混凝土结构在遇到酸雨时就很容易被腐蚀,从而影响整个建筑的安全。技术实现要素:本发明的目的在于提供一种抗腐蚀混凝土结构的原料制备工艺及其专用搅拌装置,本发明通过混凝土结构原料的专用搅拌装置对原料进行添加和搅拌,通过在第一进料口向第一壳体内加入基础原料进行搅拌,通过第二进料口将具有粘合作用的混合溶液添加进入溶液搅拌装置并进行搅拌,通过第二导液管导出,并经由第一导液管在第一壳体内部均匀喷淋,使混合溶液和基础原料混合更加均匀,缩短了搅拌的时间,加快了混凝土结构的制备,提高了工作效率;通过在混凝土结构原料中添加铝粉,使铝粉混合在混凝土结构当中可以消耗掉混凝土结构内部残留的氧气,避免氧气与混凝土的其他组分发生氧化反应影响混凝土的质量,进而提高了混凝土结构的抗氧化性能,通过在混凝土结构原料中添加聚氨基甲酸酯,提高混凝土原料的抗酸碱性能,从而提高了制备而成的混凝土结构的防腐蚀能力。本发明的目的可以通过以下技术方案实现:一种抗腐蚀混凝土结构的原料制备工艺,包括聚氨基甲酸酯制备-混合溶液制备-基础原料制备-抗腐蚀混凝土结构原料制备,具体步骤如下:步骤一、聚氨基甲酸酯制备:向250mg的甲基苯中通入0.15m3的甲醛,同时缓慢滴加60ml9.5%稀盐酸,待反应5-10min后,加入45ml一氯代苯,搅拌反应3-5min,然后进行光气化反应15-20min,直到溶液的颜色完全变成黄色,停止反应,然后离心干燥,得到黄色粉末,即二苯基甲烷二异氰酸酯,向二苯基甲烷二异氰酸酯中加入75ml甲醇,并搅拌反应10-15min,得到聚氨基甲酸酯;步骤二、混合溶液制备:将苯丙乳液通过第二进料口加入,然后依次将热塑性丙烯酸树脂、羧甲基纤维素钠和聚二甲基硅氧烷加入第二壳体中,搅拌5-8min,得到混合溶液;步骤三、基础原料制备:将硅酸盐水泥、细骨料颗粒、粗骨料颗粒和水通过第一进料口加入并进行搅拌,搅拌过程中不断向第一壳体内添加聚丙纤维、减水剂、聚氨基甲酸酯和铝粉,得到基础原料;步骤四、抗腐蚀混凝土结构原料制备:打开控制阀,混合溶液通过第一导液管流入第一导液管,并由第一导液管底部的喷孔喷出,对第一壳体内的原料搅拌10min,打开出料门,取出制备完成的混凝土结构原料。进一步在于,所述的抗腐蚀混凝土结构原料,由如下重量份的主要原料制成:硅酸盐水泥120-150份、细骨料颗粒100-130份、粗骨料颗粒90-110份、水250-300份、聚丙纤维10-15份、减水剂3-5份、聚氨基甲酸酯12-16份、铝粉8-10份、苯丙乳液40-50份、热塑性丙烯酸树脂15-20份、羧甲基纤维素钠6-8份、聚二甲基硅氧烷1-3份。进一步在于,所述细骨料颗粒的直径为0.5-2cm,所述粗骨料颗粒的直径为2-3.5cm。一种抗腐蚀混凝土结构的原料制备专用搅拌装置,包括底座、第一壳体、第一电机、第一转轴和溶液搅拌装置,所述第一壳体的底面固定安装有固定托板,所述固定托板的底部与底座固定连接,所述第一电机通过螺栓固定安装于底座的上表面,所述溶液搅拌装置固定安装于第一壳体的上表面,所述第一壳体的上表面设置有第一进料口,所述第一进料口与第一壳体相连通,所述第一壳体的侧壁设置有出料门;所述底座上表面还固定安装有联轴器,所述联轴器位于第一电机和第一壳体之间,所述第一电机的输出轴安装在联轴器的内侧,所述第一转轴的个位为两个,两个所述第一转轴横向且平行设置,且两个所述第一转轴均安装于第一壳体上相对设置的两侧侧壁处,所述第一转轴的一端贯穿第一壳体的侧壁,且端部通过轴承安装于轴承座内,两个所述第一转轴的另一端均贯穿第一壳体的另一侧壁并延伸至第一壳体外部,其中一个所述第一转轴上固定安装有主动齿轮,且其端部与第一电机的输出轴固定连接,另一个所述第一转轴上固定安装有从动齿轮,两个所述第一转轴上均固定安装有相应的第一搅拌叶片,且分别位于两个所述第一转轴上的第一搅拌叶片呈对称分布;所述溶液搅拌装置包括第二壳体,所述第二壳体的底面通过支撑杆与第一壳体的上表面固定连接,所述第二壳体的上表面固定安装有第二电机,所述第二电机的输出轴贯穿第二壳体并延伸至第二壳体的内部,所述第二电机的输出轴端部固定连接有第二转轴,所述第二转轴上固定安装有第二搅拌叶片,所述第二壳体的上表面设置有第二进料口,且第二进料口与第二壳体内部相连通;所述第二壳体底面连接有第二导液管,所述第二导液管贯穿第一壳体并延伸至第一壳体的内侧,且第二导液管的下端固定连接有第一导液管,所述第一导液管的一端固定安装于第一壳体的侧壁处,所述第一导液管的另一端固定安装于安装板内,所述安装板固定安装于第一壳体的内侧上表面。进一步的,所述第一搅拌叶片为螺旋结构,两个所述第一转轴上均固定连接有若干个搅拌凸块,所述第一搅拌叶片和搅拌凸块呈交错设置。进一步的,所述第二搅拌叶片的表面开设有若干个圆形通孔。进一步的,所述第二壳体、第二导液管和第一导液管相连通,所述第二导液管上固定安装有控制阀。进一步的,所述第一导液管的底部开设有若干并排设置的用于喷洒混合溶液的喷孔。本发明的有益效果:本发明通过混凝土结构原料的专用搅拌装置对原料进行添加和搅拌,通过在第一进料口向第一壳体内加入基础原料进行搅拌,通过第二进料口将具有粘合作用的混合溶液添加进入溶液搅拌装置并进行搅拌,通过第二导液管导出,并经由第一导液管在第一壳体内部均匀喷淋,使混合溶液和基础原料混合更加均匀,缩短了搅拌的时间,加快了混凝土结构的制备,从而提高了工作效率;通过在混凝土结构原料中添加铝粉,使铝粉混合在混凝土结构当中可以消耗掉混凝土结构内部残留的氧气,避免氧气与混凝土的其他组分发生氧化反应影响混凝土的质量,进而提高了混凝土结构的抗氧化性能,通过在混凝土结构原料中添加聚氨基甲酸酯,提高混凝土原料的抗酸碱性能,从而提高了制备而成的混凝土结构的防腐蚀能力。附图说明为了便于本领域技术人员理解,下面结合附图对本发明作进一步的说明。图1为本发明一种抗腐蚀混凝土结构的原料制备专用搅拌装置的立体结构图;图2为本发明一种抗腐蚀混凝土结构的原料制备专用搅拌装置正视剖面图;图3为本发明一种抗腐蚀混凝土结构的原料制备专用搅拌装置中溶液搅拌装置的正视剖面图。图中:1、底座;2、第一电机;3、第一转轴;4、联轴器;5、主动齿轮;6、从动齿轮;7、第一壳体;8、固定托板;9、第一进料口;10、溶液搅拌装置;101、第二壳体;102、第二电机;103、第二转轴;104、第二搅拌叶片;105、第二进料口;106、支撑杆;107、圆形通孔;11、第一搅拌叶片;12、搅拌凸块;13、轴承座;14、第一导液管;15、第二导液管;16控制阀;17、安装板;18、出料门。具体实施方式下面将结合实施例对本发明的技术方案进行清楚、完整地描述,显然,所描述的实施例仅仅是本发明一部分实施例,而不是全部的实施例。基于本发明中的实施例,本领域普通技术人员在没有作出创造性劳动前提下所获得的所有其它实施例,都属于本发明保护的范围。一种抗腐蚀混凝土结构的原料制备工艺,包括聚氨基甲酸酯制备-混合溶液制备-基础原料制备-抗腐蚀混凝土结构原料制备,具体步骤如下:步骤一、聚氨基甲酸酯制备:向250mg的甲基苯中通入0.15m3的甲醛,同时缓慢滴加60ml9.5%稀盐酸,待反应5-10min后,加入45ml一氯代苯,搅拌反应3-5min,然后进行光气化反应15-20min,直到溶液的颜色完全变成黄色,停止反应,然后离心干燥,得到黄色粉末,即二苯基甲烷二异氰酸酯,向二苯基甲烷二异氰酸酯中加入75ml甲醇,并搅拌反应10-15min,得到聚氨基甲酸酯;步骤二、混合溶液制备:将苯丙乳液通过第二进料口105加入,然后依次将热塑性丙烯酸树脂、羧甲基纤维素钠和聚二甲基硅氧烷加入第二壳体101中,搅拌5-8min,得到混合溶液;步骤三、基础原料制备:将硅酸盐水泥、细骨料颗粒、粗骨料颗粒和水通过第一进料口9加入并进行搅拌,搅拌过程中不断向第一壳体7内添加聚丙纤维、减水剂、聚氨基甲酸酯和铝粉,得到基础原料;步骤四、抗腐蚀混凝土结构原料制备:打开控制阀16,混合溶液通过第一导液管15流入第一导液管14,并由第一导液管14底部的喷孔喷出,对第一壳体7内的原料搅拌10min,打开出料门18,取出制备完成的混凝土结构原料。所述的抗腐蚀混凝土结构原料,由如下重量份的主要原料制成:硅酸盐水泥120-150份、细骨料颗粒100-130份、粗骨料颗粒90-110份、水250-300份、聚丙纤维10-15份、减水剂3-5份、聚氨基甲酸酯12-16份、铝粉8-10份、苯丙乳液40-50份、热塑性丙烯酸树脂15-20份、羧甲基纤维素钠6-8份、聚二甲基硅氧烷1-3份。所述细骨料颗粒的直径为0.5-2cm,所述粗骨料颗粒的直径为2-3.5cm。如图1-3所示,一种抗腐蚀混凝土结构的原料制备专用搅拌装置,包括底座1、第一壳体7、第一电机2、第一转轴3和溶液搅拌装置10,所述第一壳体7的底面固定安装有固定托板8,所述固定托板8的底部与底座1固定连接,所述第一电机2通过螺栓固定安装于底座1的上表面,所述溶液搅拌装置10固定安装于第一壳体7的上表面,所述第一壳体7的上表面设置有第一进料口9,所述第一进料口9与第一壳体7相连通,所述第一壳体7的侧壁设置有出料门18;所述底座1上表面还固定安装有联轴器4,所述联轴器4位于第一电机2和第一壳体7之间,所述第一电机2的输出轴安装在联轴器4的内侧,所述第一转轴3的个位为两个,两个所述第一转轴3横向且平行设置,且两个所述第一转轴3均安装于第一壳体7上相对设置的两侧侧壁处,所述第一转轴3的一端贯穿第一壳体7的侧壁,且端部通过轴承安装于轴承座13内,两个所述第一转轴3的另一端均贯穿第一壳体7的另一侧壁并延伸至第一壳体7外部,其中一个所述第一转轴3上固定安装有主动齿轮5,且其端部与第一电机2的输出轴固定连接,另一个所述第一转轴3上固定安装有从动齿轮6,两个所述第一转轴3上均固定安装有相应的第一搅拌叶片11,且分别位于两个所述第一转轴3上的第一搅拌叶片11呈对称分布;所述溶液搅拌装置10包括第二壳体101,所述第二壳体101的底面通过支撑杆106与第一壳体7的上表面固定连接,所述第二壳体101的上表面固定安装有第二电机102,所述第二电机102的输出轴贯穿第二壳体101并延伸至第二壳体101的内部,所述第二电机102的输出轴端部固定连接有第二转轴103,所述第二转轴103上固定安装有第二搅拌叶片104,所述第二壳体101的上表面设置有第二进料口105,且第二进料口105与第二壳体101内部相连通;所述第二壳体101底面连接有第二导液管15,所述第二导液管15贯穿第一壳体7并延伸至第一壳体7的内侧,且第二导液管15的下端固定连接有第一导液管14,所述第一导液管14的一端固定安装于第一壳体7的侧壁处,所述第一导液管14的另一端固定安装于安装板17内,所述安装板17固定安装于第一壳体7的内侧上表面。其中,所述第一搅拌叶片11为螺旋结构,两个所述第一转轴3上均固定连接有若干个搅拌凸块12,所述第一搅拌叶片11和搅拌凸块12呈交错设置,使原料搅拌更加充分,所述第二搅拌叶片104的表面开设有若干个圆形通孔107,搅拌时溶液通过圆形通孔107得到进一步细化,从而使溶液搅拌更加细致均匀,所述第二壳体101、第二导液管15和第一导液管14相连通,所述第二导液管15上固定安装有控制阀16,所述第一导液管14的底部开设有若干并排设置的用于喷洒混合溶液的喷孔,混合溶液经由第一导液管14在第一壳体7内部均匀喷淋,使混合溶液和基础原料混合更加均匀,缩短了搅拌的时间,加快了混凝土结构的制备,从而提高了工作效率。实施例1所述的抗腐蚀混凝土结构原料,由如下重量份的主要原料制成:硅酸盐水泥120份、细骨料颗粒100份、粗骨料颗粒90份、水250份、聚丙纤维10份、减水剂3份、聚氨基甲酸酯12份、铝粉8份、苯丙乳液40份、热塑性丙烯酸树脂15份、羧甲基纤维素钠6份、聚二甲基硅氧烷1份;实施例2所述的抗腐蚀混凝土结构原料,由如下重量份的主要原料制成:硅酸盐水泥135份、细骨料颗粒120份、粗骨料颗粒100份、水275份、聚丙纤维12份、减水剂4份、聚氨基甲酸酯14份、铝粉9份、苯丙乳液45份、热塑性丙烯酸树脂17、羧甲基纤维素钠7、聚二甲基硅氧烷2份;实施例3所述的抗腐蚀混凝土结构原料,由如下重量份的主要原料制成:硅酸盐水泥150份、细骨料颗粒130份、粗骨料颗粒110份、水300份、聚丙纤维15份、减水剂5份、聚氨基甲酸酯16份、铝粉10份、苯丙乳液50份、热塑性丙烯酸树脂20份、羧甲基纤维素钠8份、聚二甲基硅氧烷3份;对比例1所述的抗腐蚀混凝土结构原料,由如下重量份的主要原料制成:硅酸盐水泥135份、细骨料颗粒120份、粗骨料颗粒100份、水275份、聚丙纤维12份、减水剂4份、聚氨基甲酸酯14份、苯丙乳液45份、热塑性丙烯酸树脂17、羧甲基纤维素钠7、聚二甲基硅氧烷2份;对比例2所述的抗腐蚀混凝土结构原料,由如下重量份的主要原料制成:硅酸盐水泥135份、细骨料颗粒120份、粗骨料颗粒100份、水275份、聚丙纤维12份、减水剂4份、铝粉9份、苯丙乳液45份、热塑性丙烯酸树脂17、羧甲基纤维素钠7、聚二甲基硅氧烷2份;实施例4将实施例1-3和对比例1中制备抗腐蚀混凝土结构的原料进行抗氧化性能测试,具体测试步骤如下:将实施例1-3和对比例1中制备的原料分别放入样板制作模具中,制得对应的30cm*30cm*2cm的混凝土样板,将其取出至通风环境中干燥5h,混凝土样板凝固后将其放置于温度26℃的密闭环境中,并向其中通入氧气,将混凝土样板放置10d,取出混凝土样板,并将其放置于冲击试验机中,进行冲击强度测试,结果如下:表1实施例1-3和对比例1中混凝土样板通氧后的冲击强度(单位:j/m2)实施例1实施例2实施例3对比例1冲击强度2792.32811.72815.62074.4由表1可知,本实施例1-3中混凝土样板测得的冲击强度为2792.3-2815.6j/m2,对比例1中混凝土样板测得的冲击强度为2074.4j/m2,因此,在混凝土结构的原料添加铝粉可以提高混凝土的抗氧化性能,铝粉混合在混凝土结构当中,可以消耗掉混凝土结构内部残留的氧气,避免氧气与混凝土的其他组分发生氧化反应影响混凝土的质量,进而提高了混凝土结构的抗氧化性能;实施例5将实施例1-3和对比例2中制备抗腐蚀混凝土结构的原料进行抗酸碱性能测试,具体测试步骤如下:将实施例1-3和对比例2中制备的原料分别放入样板制作模具中,制成对应的10cm*10cm*2cm的混凝土样板,将其取出至通风环境中干燥5h,混凝土样板凝固后将其分别放置于13%h2so4和9%naoh中,持续15d,取出混凝土样板,并将其放置于冲击试验机中,进行冲击强度测试,结果如下:表2实施例1-3和对比例2中混凝土样板在h2so4和naoh中浸泡后的冲击强度(单位:j/m2)由表2可知,实施例1-3中的混凝土样板在13%h2so4中浸泡后的冲击强度为2433.4-2542.7j/m2,对比例2中的混凝土样板在13%h2so4中浸泡后的冲击强度为1817.6j/m2,实施例1-3中的混凝土样板在9%naoh中浸泡后的冲击强度2586.5-2637.1j/m2,对比例2的混凝土样板在9%naoh中浸泡后的冲击强度为1953.8j/m2,因此,实施例1-3中的混凝土样板在13%h2so4和9%naoh中浸泡后的冲击强度均大于对比例2的混凝土样板的冲击强度,添加了聚氨基甲酸酯的混凝土原料的抗酸碱性能得到明显提升。本发明中的抗腐蚀混凝土结构的原料制备专用搅拌装置的工作原理为:启动第一电机2,第一电机2的输出轴转动并通过联轴器4带动第一转轴3转动,第一转轴3带动主动齿轮5转动,主动齿轮5带动与其啮合的从动齿轮6转动,从动齿轮6带动与其固定的第一转轴3转动,从而使两个第一转轴3反向转动,两个第一转轴3转动的同时分别带动对称设置的两个第一搅拌叶片11和搅拌凸块12转动,从而对第一壳体7内的基础原料进行搅拌;启动第二电机102,第二电机102的输出轴转动并带动与其端部固定的第二转轴103转动,第二转轴103带动第二搅拌叶片104转动并对第二壳体101内的混合溶液进行搅拌,搅拌的同时,溶液通过圆形通孔107进而更加细化,使溶液搅拌更加细致均匀;打开控制阀16,混合溶液通过第二导液管15进入第一导液管14,并由第一导液管14底部的喷孔喷出,第一搅拌叶片11和搅拌凸块12对原料再次搅拌,最后通过打开出料门18取出所制备的混凝土结构的原料。本发明通过混凝土结构原料的专用搅拌装置对原料进行添加和搅拌,通过在第一进料口9向第一壳体7内加入基础原料进行搅拌,通过第二进料口105将具有粘合作用的混合溶液添加进入溶液搅拌装置并进行搅拌,通过第二导液管15导出,并经由第一导液管14在第一壳体7内部均匀喷淋,使混合溶液和基础原料混合更加均匀,缩短了搅拌的时间,加快了混凝土结构的制备,从而提高了工作效率;通过在混凝土结构原料中添加铝粉,使铝粉混合在混凝土结构当中可以消耗掉混凝土结构内部残留的氧气,避免氧气与混凝土的其他组分发生氧化反应影响混凝土的质量,进而提高了混凝土结构的抗氧化性能,通过在混凝土结构原料中添加聚氨基甲酸酯,提高混凝土原料的抗酸碱性能,从而提高了制备而成的混凝土结构的防腐蚀能力。以上公开的本发明优选实施例只是用于帮助阐述本发明。优选实施例并没有详尽叙述所有的细节,也不限制该发明仅为所述的具体实施方式。显然,根据本说明书的内容,可作很多的修改和变化。本说明书选取并具体描述这些实施例,是为了更好地解释本发明的原理和实际应用,从而使所属
技术领域:
技术人员能很好地理解和利用本发明。本发明仅受权利要求书及其全部范围和等效物的限制。当前第1页12