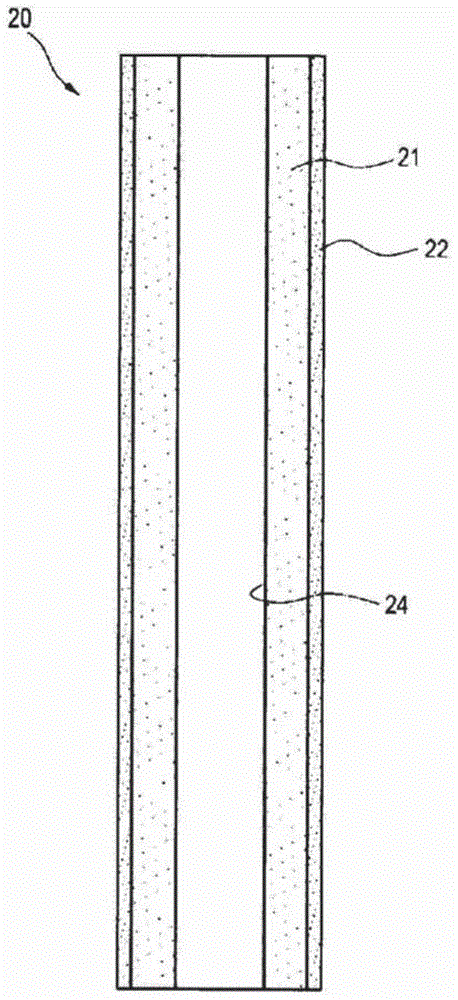
本发明涉及沸石膜和在无机氧化物多孔基材上形成了沸石膜的分离膜。本申请要求基于2017年1月18日申请的日本申请第2017-6851号的优先权,并援引上述日本申请中记载的全部记载内容。
背景技术:
:专利文献1公开了一种利用水蒸气对含有沸石晶种、有机结构导向剂和二氧化硅的膜状物进行处理而形成mfi型沸石膜,从而得到分离膜的方法。专利文献2公开了一种沸石膜,其中,在xrd测定中,所述沸石膜的来自020面的散射强度/来自101面的散射强度大于3.3,并且来自020面的散射强度/来自002面或102面的散射强度大于4.4。专利文献3公开了一种沸石膜,其中,在xrd测定中,所述沸石膜的来自002面散射强度/来自020面的散射强度为2以上,来自002面的散射强度/来自101面的散射强度为0.5~1.5,来自101面的散射强度/来自501面的散射强度为1.5以上,并且来自303面的散射强度/来自501面的散射强度为2以上。现有技术文献专利文献专利文献1:日本特开2001-31416号公报专利文献2:日本特开2004-2160号公报专利文献1:国际公开第2007/58388号技术实现要素:本发明的一个方式的沸石膜为在无机氧化物多孔基材上形成的mfi型沸石膜,其中,在所述沸石膜的通过以cukα射线作为射线源的x射线衍射测定得到的衍射图谱中,在以衍射角7.3°~8.4°处显示的、晶格面归属于011和/或101面的衍射峰的强度为基准时,在衍射角8.4°~9.0°处显示的、晶格面归属于200和/或020面的衍射峰的强度为0.3以上。另外,关于本发明的一个方式的分离膜,在包含含有90质量%以上的sio2的非晶质体的无机氧化物多孔基材上具有本发明的一个实施方式的沸石膜。附图说明图1为表示本发明的实施方式的分离膜的构成的图。图2为表示本发明的实施方式的制造方法的流程的图。图3a为表示例1中的通过不同的水添加量合成的膜的xrd图谱的图。图3b为表示例1中的通过不同的水添加量合成的膜的结晶度的图。图4为表示例1的通过不同的水添加量合成的膜的sem图像的图。图5a为表示例2的通过不同的合成时间合成的膜的xrd图谱的图。图5b为表示例2的通过不同的合成时间合成的膜的结晶度的图。图6为例2的通过不同的合成时间合成的膜的sem图像(其一)。图7为例2的通过不同的合成时间合成的膜的sem图像(其二)。图8为表示评价分离膜的透过性能的装置的一例的示意图。图9为表示例2的流速和分离系数α相对于合成时间的关系的图。图10为表示例3的通过不同的tpaoh浓度合成的膜的xrd图谱的图。图11为表示例4-1的分离膜的表面的结构的电子显微镜照片。图12为表示例4-1的分离膜的与长度方向正交的截面的结构的电子显微镜照片。图13为表示例5-4的分离膜的表面的结构的电子显微镜照片。图14为表示例5-4的分离膜的与长度方向正交的截面的结构的电子显微镜照片。图15为表示例8-1的分离膜的与长度方向正交的截面的结构的电子显微镜照片。图16为表示例4-1和例5-4的分离膜的表面的x射线衍射测定结果的图。图17为表示例8-1的分离膜的表面的x射线衍射测定结果的图。具体实施方式[发明所要解决的问题]在以往的水热合成法中,从溶液侧供给沸石成分,以晶种作为核,沸石晶体自其表面生长,因此取向晶体膜生长。在这样的具有高取向性的沸石分离膜中,由于粒子界面处的泄漏,分离系数降低,因此,为了提高分离系数,需要加厚膜厚。另一方面,加厚膜厚时,渗透通量降低。因此,要求渗透通量和分离比二者都提高的膜结构。本发明的目的在于提供一种即使膜厚薄分离能力也优异、渗透通量大的沸石膜和分离膜。[本公开的效果]根据本发明,能够提供一种即使膜厚薄分离能力也优异、渗透通量大的沸石膜和分离膜。[本发明的实施方式的说明]首先,列举并说明本申请发明的实施方式的内容。本申请发明的实施方式的沸石膜为,(1)在无机氧化物多孔基材上形成的mfi型沸石膜,其中,在所述沸石膜的通过以cukα射线作为射线源的x射线衍射测定得到的衍射图谱中,在以衍射角7.3°~8.4°处显示的、晶格面归属于011和/或101面的衍射峰的强度为基准时,在衍射角8.4°~9.0°处显示的、晶格面归属于200和/或020面的衍射峰的强度为0.3以上。根据该构成,能够提供一种即使膜厚薄渗透通量、分离能力也优异的沸石膜。(2)上述(1)的沸石膜,其中,在所述衍射图谱中,在以衍射角7.3°~8.4°处显示的、晶格面归属于011和/或101面的衍射峰的强度为基准时,在衍射角8.4°~9.0°处显示的、晶格面归属于200和/或020面的衍射峰的强度可以为0.4以上。(3)上述(1)的沸石膜,其中,在所述衍射图谱中,在以衍射角7.3°~8.4°处显示的、晶格面归属于011和/或101面的衍射峰的强度为基准时,在衍射角22.7°~23.5°处显示的、晶格面归属于501和/或051面的衍射峰的强度可以为0.5以上。(4)上述(3)的沸石膜,其中,在所述衍射图谱中,在以衍射角7.3°~8.4°处显示的、晶格面归属于011和/或101面的衍射峰的强度为基准时,在衍射角22.7°~23.5°处显示的、晶格面归属于501和/或051面的衍射峰的强度可以为0.6以上。(5)上述(1)或(3)的沸石膜,其中,在所述衍射图谱中,在以衍射角7.3°~8.4°处显示的、晶格面归属于011和/或101面的衍射峰的强度为基准时,在衍射角12.9°~13.5°处显示的、晶格面归属于002面的衍射峰的强度可以为0.25以下。(6)上述(1)、(3)和(5)中任一项的沸石膜,其中,在所述衍射图谱中,在以衍射角7.3°~8.4°处显示的、晶格面归属于011和/或101面的衍射峰的强度为基准时,在衍射角26.8°~27.2°处显示的、晶格面归属于104面的衍射峰的强度可以为0.2以下。另外,本申请发明的实施方式的分离膜,(7)在包含含有90质量%以上的sio2的非晶质体的无机氧化物多孔基材上具有上述(1)~(6)中任一项的沸石膜。根据该构成,由于基材为高二氧化硅基材,因此能够通过抑制氧化铝的溶出而维持膜的疏水性,发挥优异的分离能力。另外,由于将基材本身转变为沸石,因此膜与基材的亲和性良好,发挥优异的分离能力。(8)上述(7)的分离膜,其中,所述无机氧化物多孔基材也可以包含含有99质量%以上的sio2的非晶质体。根据该构成,由于基材为高二氧化硅基材,因此能够通过进一步抑制氧化铝的溶出而维持膜的疏水性,发挥优异的分离能力。另外,由于将基材本身转变为沸石,因此膜与基材的亲和性更好,发挥优异的分离能力。[具体实施方式]以下,对本发明的实施方式详细地进行说明。1.分离膜图1表示分离膜的一个实施方式。图1为分离膜的纵剖视图。分离膜20为近似圆柱形,具有带有中心孔24的无机氧化物多孔基材21。在多孔基材21的外周形成有沸石膜22。需要说明的是,分离膜的形状也可以设定为平面状等任意的形状,但从分离效率的观点考虑,为了进一步扩大与流体的接触面积,在本实施方式中设定为管状。分离膜20可以用于利用了分子筛效应、亲水/疏水性的气体分离膜、蒸发膜、膜分离反应器等中,特别适合用作乙醇/水分离用的分离膜。1-1.无机氧化物多孔基材作为本实施方式中使用的无机氧化物多孔基材21而言,只要根据本实施方式形成有沸石膜22的部分(基材的表面部分)的主要成分为非晶质sio2即可,例如,可以使用在氧化铝等基材表面形成了非晶质sio2的基材、基材整体由非晶质sio2形成的基材。另外,上述基材21优选包含含有90质量%以上的sio2的非晶质体、上述基材21进一步优选包含含有99质量%以上的sio2的非晶质体、上述基材21特别优选含有小于1质量%的al2o3。通过增加基材的sio2含有比例、并且降低al2o3和杂质的含有比例,能够抑制存在于基材中的al2o3、碱元素、硼等向沸石膜22中溶出,能够维持分离膜20的疏水性。另外,微量的氧化铝溶解能够提高二氧化硅基材的对碱的耐久性,因此在对沸石进行成膜处理时,能够通过抑制基材溶出而维持基材的强度。多孔基材21支撑该薄膜而几乎不干涉沸石膜22中的流体的透过,因此多孔基材21的孔隙率可以为35%~70%、平均孔径可以为250nm~600nm。需要说明的是,“孔隙率”可以以每单位体积的孔容所占的比例的形式来计算。此外,多孔基材21的厚度没有特别限制,从机械强度和气体透过性的平衡考虑,优选为0.2mm~5mm、更优选为0.5mm~3mm。另外,多孔基材21的沸石形成部分的比表面积可以为5m2/g以上且400m2/g以下。小于5m2/g时,由于表面积小,因此粒子表面能够负载的结构导向剂的量可能不足够,另外,由于由碱性成分导致的二氧化硅成分的溶出量不足,有可能变得无法完全转化为沸石。相反,比表面积大于400m2/g时,结构导向剂的负载量有可能过量,另外,由于碱性成分向基材渗透导致二氧化硅成分必要以上地溶出,有时会导致基材强度的降低。作为适当的比表面积而言,从前者的观点考虑,优选使得存在于多孔基材21的表面的粒子的直径为0.5μm以下的10m2/g以上。从后者的观点考虑,优选使得上述粒子的直径为50nm以上的100m2/g以下。1-2.沸石膜通过本实施方式得到的多孔基材21上形成的沸石膜22为mfi型沸石膜,与通过以往的水热合成法得到的沸石膜相比,是致密的膜。因此,本实施方式的沸石膜22的膜厚即使薄,分离能力也优异,能够提供渗透通量大的分离膜。在通过以cukα射线作为x射线源的x射线衍射测定得到的衍射图谱中,沸石膜22在以衍射角7.3°~8.4°处显示的、晶格面归属于011和/或101面的衍射峰的强度为基准时,在衍射角8.4°~9.0°处显示的、晶格面归属于200和/或020面的衍射峰的强度为0.3以上、优选为0.4以上。另外,在通过以cukα射线作为x射线源的x射线衍射测定得到的衍射图谱中,沸石膜22在以衍射角7.3°~8.4°处显示的、晶格面归属于011和/或101面的衍射峰的强度为基准时,在衍射角22.7°~23.5°处显示的、晶格面归属于501和/或051面的衍射峰的强度优选为0.5以上、更优选为0.6以上。另外,在通过以cukα射线作为x射线源的x射线衍射测定得到的衍射图谱中,沸石膜22在以衍射角7.3°~8.4°处显示的、晶格面归属于011和/或101面的衍射峰的强度为基准时,在衍射角12.9°~13.5°处显示的、晶格面归属于002面的衍射峰的强度优选为0.25以下。另外,在通过以cukα射线作为x射线源的x射线衍射测定得到的衍射图谱中,沸石膜22在以衍射角7.3°~8.4°处显示的、晶格面归属于011和/或101面的衍射峰的强度为基准时,在衍射角26.8°~27.2°处显示的、晶格面归属于104面的衍射峰的强度优选为0.2以下。x射线衍射测定例如可以使用bruker公司粉末x射线衍射装置d8advance,将加速电压设定为40kv、将电流设定为40ma、将光源设定为cukα、将测量角度设定为5°~80°从而进行测定。沸石膜22的厚度没有特别限制,优选为0.5μm~30μm。厚度小于0.5μm时,则沸石膜22中容易产生针孔,有可能无法得到充分的分离性能,另外,厚度大于30μm时,流体的透过速度变得过小,有时难以得到在实际使用上充分的透过性能。2.分离膜的制造方法如图2中示出的流程图所示,分离膜20通过以下方式制造:通过在无机氧化物多孔基材21的表面上通过涂布等方法形成沸石晶种以及含有结构导向剂的碱性成分从而得到形成体的第一工序、和在加热水蒸气气氛下对在该第一工序中得到的形成体进行处理的第二工序,在上述基材21的表面形成沸石膜22。2-1.第一工序在第一工序中,在无机氧化物多孔基材21的表面上通过涂布等方法形成沸石晶种以及含有结构导向剂的碱性成分。沸石的晶种是通过通常的沸石粒子的制造方法制作的沸石粒子。沸石晶种的粒径没有特别限制,例如为5μm以下、优选为3μm以下。结构导向剂是构建沸石的孔的有机化合物的模具(型剤),使用四乙基氢氧化铵、四丙基氢氧化铵、四丙基溴化铵、四丁基氢氧化铵等季铵盐、三甲基金刚烷铵盐等。碱性成分表示碱性的水溶液,优选为含有有机铵氢氧化物和/或有机铵卤盐和碱金属氢氧化物的水溶液。作为有机铵氢氧化物而言,例如可以列举四丙基氢氧化铵(tpaoh),作为有机铵卤盐而言,例如可以列举四丙基溴化铵(tpabr),作为碱金属氢氧化物而言,例如可以列举氢氧化钠或氢氧化钾。在使用含有有机铵氢氧化物的水溶液作为碱性成分的情况下,由于沸石膜由仅二氧化硅成分和有机铵形成,因此能够形成杂质成分极少的分离膜,能够抑制杂质从基材、膜中溶出。另外,在使用含有有机铵卤盐和碱金属氢氧化物的水溶液作为碱性成分的情况下,与有机铵氢氧化物相比,成分更稳定,并且能够根据碱金属氢氧化物的浓度调节碱浓度,因此能够构建不容易发生由过量的碱导致的基材的破坏等的工艺。另外,碱性成分中的结构导向剂的浓度优选为0.05m以上,因为由此使晶体生长进行。此外,碱性成分中的结构导向剂的浓度优选为0.3m以下,因为由此能够有效抑制基材的消耗。在无机氧化物多孔基材21的表面上的沸石晶种的形成例如可以通过在沸石晶种的水分散液中浸渍、提起无机氧化物多孔基材21的方法进行。此时,通过向沸石晶种的水分散液中添加碱性成分,也可以与晶种同时在无机多孔基材21的表面涂布形成碱性成分。另外,沸石晶种的形成也可以通过以下方式进行:制备分散有沸石的聚合物膜,将沸石分散膜卷绕在支撑体外表面上,然后煅烧除去聚合物部分。在这种情况下,将干燥后的沸石粉末分散在氯仿或丙酮溶剂中,然后添加聚甲基丙烯酸甲酯并进行搅拌,然后通过流延法制备分散有沸石晶种的聚合物膜。将该膜卷绕胶粘在无机氧化物多孔基材21上,然后在550℃下在大气中进行煅烧,由此能够在无机氧化物多孔基材21的表面上形成晶种层。在本实施方式中,也可以通过电泳法在无机氧化物多孔基材21上形成沸石晶种。根据该方法,能够控制晶种的位置和密度,能够提高最终得到的沸石膜22的致密性。电泳法通过如下方式进行:在上下密封的多孔基材21内部填充有机溶剂、例如丙酮,在外部充满分散有沸石晶种的有机溶剂,并对多孔基材21内部电极和容器侧电极施加电压,由此使晶种附着在基材21表面。电泳法例如通过施加50v的电压5分钟来进行。在晶种附着后,从溶液中提起基材21并干燥,然后例如在300℃下进行6小时加热处理,由此完成在基材21上的晶种的形成。通过电泳法使晶种附着,然后对晶种附着的多孔基材上下进行密封,浸渍在tpaoh水溶液中,然后提起,由此在表面涂布形成碱性成分。tpaoh水溶液优选0.05m以上且0.5m以下,例如可以使用0.1m的tpaoh水溶液。另外,在干燥基材21上的碱性成分时,能够抑制基材21上的碱性成分的厚度和浓度不均,因此优选。3-2.第二工序将在第一工序中得到的形成体设置在每容器容积含有0.5体积%~5体积%的水的水热处理容器中,在140℃~180℃下进行规定时间、例如24小时的热处理,由此能够在晶种周边形成沸石膜。另外,优选用于放入水热处理容器中从而得到加热水蒸气气氛的水量为饱和水蒸气量的2倍以上,因为由此能够充分进行向成膜区域的水蒸气供给。然而,当放入水热处理容器中的水量大于饱和水蒸气量的20倍时,可能容易在膜结构上产生缺陷。饱和水蒸气量(wh2o-s)是单位体积(1m3)的加热处理温度(t)下的饱和水蒸气压(ps)下的水蒸气质量,单位为g/m3。在设定为容器容积(v)内的质量的情况下为wh2o-s×v(g)。饱和水蒸气量通过如下方式得到:利用近似式求出规定温度下的饱和水蒸气压(p(t)),根据气体的状态方程式换算为水蒸气量。作为饱和水蒸气压的近似式而言,有如下所述的wagner式。p(t)=pc·exp[(ax+bx1.5+cx3+dx6)/(1-x)]在此,pc=221200[hpa]:临界压力、tc=647.3[k]:临界温度、x=1-(t+273.15)/tc、a=-7.76451、b=1.45838、c=-2.7758、d=-1.23303(a~d:系数)。利用气体的状态方程式:p/rt=n/v由所得到的饱和水蒸气压p(t)求出每单位体积的水蒸气摩尔数,由水的分子量得到饱和水蒸气量。另外,从晶体生长的观点考虑,第二工序中的加热水蒸气气氛下的处理优选为4小时以上。进一步更优选为8小时以上,因为由此沸石晶体结构稳定。然而,处理时间比36小时长时,由于晶体成分的溶出等原因导致结晶性有可能变差,以及制造时间有可能增加。对于通过第一工序和第二工序得到的形成体而言,在清洗后进行干燥,然后在350℃~600℃下煅烧规定时间、例如12小时,由此燃烧除去结构导向剂,从而形成分离膜20。根据本实施方式的制造方法,与以往的水热合成法相比,通过使用少量的结构导向剂,能够得到分离能力优异、渗透通量大的分离膜,从制造成本的观点考虑是有利的。实施例以下示出使用了本发明的实施例的评价试验的结果,进一步详细地说明本发明。需要说明的是,本发明不限于这些实施例。(多孔二氧化硅基材)通过外接cvd法,制作外径10mm、内径8.4mm、长度300mm、孔隙率64%、平均孔径500nm的多孔二氧化硅管,将其切割成长度30mm的管并作为多孔二氧化硅基材使用。(晶种附着多孔二氧化硅基材)使用胶体二氧化硅、tpabr、氢氧化钠、蒸馏水作为原料,以使得sio2:tpabr:naoh:h2o的摩尔比为1:0.2:0.1:40的方式进行混合,在室温下搅拌60分钟,由此得到了晶种生成用溶胶。使该溶胶在聚丙烯制容器内在100℃、144小时的搅拌条件下进行反应,合成了mfi型沸石晶体(silicalite-1)。通过抽滤回收该沸石晶体,利用热水清洗,然后在60℃下进行10小时干燥处理,从而得到了粒径约1μm的高硅沸石晶种。需要说明的是,胶体二氧化硅使用了触媒化成工业株式会社制造的cataloidsi-30(注册商标)(sio2:30.17%、na2o:0.4%、h2o:69.43%)。在100ml丙酮溶剂中加入0.5g高硅沸石晶种,并利用超声波将其分散30分钟。在上下密封后的多孔二氧化硅基材内部填充仅丙酮溶剂,在外部充满分散有高硅沸石晶种的丙酮溶剂,在基材内部电极和容器侧电极间施加50v的电压5分钟,由此使晶种附着在基材表面。将其从溶液中提起,在大气中干燥30分钟,然后在300℃下进行6小时加热处理,从而制作了晶种附着多孔二氧化硅基材。<例1(水量的影响)>将晶种附着多孔二氧化硅基材的上下密封,在0.1m的tpaoh水溶液中浸渍基材整体,然后提起,在60℃下干燥了1小时。之后,以使得基材不接触水的方式将基材设置在水在1g~12g范围内的水热处理容器(容器内容积120cc)中,在160℃下进行24小时热处理,在基材表面形成了沸石膜。热处理后,清洗形成体,在60℃下干燥10小时,然后在375℃下煅烧40小时,由此除去结构导向剂,得到了例1-1~例1-5的分离膜。需要说明的是,例1-1~例1-5的分离膜分别表示放入水热处理容器中的水量为1g、3g、6g、9g、12g的分离膜。使用bruker公司粉末x射线衍射(xrd)装置d8advance对所得到的分离膜的表面结构进行了分析。在将加速电压设定为40kv、将电流设定为40ma、将光源设定为cukα、将测量角度设定为5°~80°的条件下进行了测定。另外,利用扫描电子显微镜(sem)观察了所得到的分离膜的表面和截面的形态。图3a、图3b示出在改变了水添加量的情况下的xrd图谱、和由在2θ=20°-40°范围内的前15个峰强度之和得到的结晶度。在任一个样品中,均能够确认:与处理前相比,水热处理后基于mfi的结晶性增加,没有其它杂质相的形成。另外,水添加量为3g时,成功合成了结晶性最高的膜。将利用sem观察分离膜的表面和截面的形态而得到的照片示于图4。与处理前相比,晶体形态发生变化,水添加量为3g时,成功合成了最致密且连续的膜。而且,在致密的沸石层和支撑体之间确认到mfi特有的柱状晶体的形成。在160℃下水热容器容积为120ml的情况下,饱和水蒸气量达到0.37g。由上述结果可知,水添加量优选为显著大于饱和水蒸气量的3g以上。另外,在为3g以上时,晶体的形态显著变化,确认到晶体间的空隙,由此可以设想,优选相对于饱和水蒸气量为3倍以上且10倍以下的水量。当然,该值可以根据容器容积、成膜基材面积等而变化,因此该值只是作为参考值,是在本成膜条件下能够应用的值。<例2(热处理时间的影响)>为了研究热处理时间的影响,进行了以下所示的一系列实验。将晶种附着多孔二氧化硅基材的上下密封,在0.1m的tpaoh水溶液中浸渍基材整体,然后提起,在60℃下干燥1小时。之后,以使得基材不接触水的方式将基材设置在放入了3g水的水热处理容器(容器内容积120cc)中,在160℃下进行2小时~48小时热处理,在基材表面形成了沸石膜。热处理后,清洗形成体,在60℃下干燥10小时,然后在375℃下煅烧40小时,由此除去结构导向剂,得到了例2-1~例2-8的分离膜。需要说明的是,例2-1~例2-8的分离膜分别表示热处理时间为2小时、4小时、8小时、12小时、16小时、24小时、36小时、48小时的分离膜。通过与例1同样的条件的xrd分析和利用sem进行的膜结构观察对所得到的分离膜的表面的结构进行了评价。图5a、图5b表示在水添加量为3g的条件下改变热处理时间的情况下的xrd图谱(a)和由在2θ=20°-40°范围内的前15个峰强度之和得到的结晶度(b)。直到热处理时间达到24小时为止,随着热处理时间的增加,结晶度提高,超过24小时时,结晶度降低。认为:直到24小时为止,由于晶种的生长、支撑体自身的沸石化,峰值强度变高,但在24小时以后,晶体生长停止,由于处于碱性气氛下,因此结晶度由于再溶解而降低。根据该结果,认为合成时间为24小时在本条件下是最佳的。将利用sem观察分离膜的表面和截面的形态而得到的照片示于图6、7。随着热处理时间的增加,分离膜的形态发生了显著变化。根据截面sem图像,直到热处理时间达到8小时为止,基材成分在晶种层的膜化和生长中被消耗,确认到致密的沸石层的生长。热处理时间大于8小时时,在致密的沸石层和支撑体之间确认到来自支撑体的coffin型晶体的形成。随着热处理时间从12小时增加到24小时,coffin型晶体的尺寸增大。24小时以后,膜形态没有显著差异。直到24小时为止的截面观察的结果和图5b的结晶度曲线的倾向是一致的。(渗透汽化实验(pv:pervaporation))通过渗透汽化试验对例2中得到的分离膜的性能进行了评价。渗透汽化试验是利用图8的示意图所示的装置进行的。将10%的乙醇水溶液在水浴中加热至50℃,在其中放入一端密封、另一端与真空泵连接的分离膜,对内部进行减压,并每隔规定时间利用采样冷阱采集透过液体。通过液相色谱法测定所得到的减压侧的液体组成,评价了乙醇的分离浓缩的状态。将渗透汽化试验的结果示于表1和图9。表1.改变热处理时间而制作的分离膜的etoh/h2o渗透汽化特性分离膜2-12-22-32-42-52-62-72-8热处理时间(小时)2481216243648jtotal[kg/(m2·小时)]25.96.715.024.894.494.474.95.24etohconc.[重量%]1461808586888779αetoh1.41437.149.955.866.159.933.7psi1187181239249291288171表中,jtotal表示渗透通量、etohconc.表示透过液体的乙醇浓度、αetoh表示分离系数、psi表示渗透汽化分离指数。jtotal、αetoh和psi通过下述式计算出。分离系数αetoh随热处理时间而变化,在24小时时取得最大值,之后降低。该倾向也与根据xrd图谱计算出的结晶度曲线的图(图5b)一致,明确了分离系数依赖于膜的结晶性。另外,已知表示膜性能的psi值最大达到290。<例3(结构导向剂的浓度的影响)>为了研究结构导向剂的浓度的影响,进行了以下所示的一系列实验。将晶种附着多孔二氧化硅基材的上下密封,在0.01m~0.5m的tpaoh水溶液中浸渍基材整体,然后提起,在60℃下干燥了1小时。之后,以使得基材不接触水的方式将基材设置在放入了3g水的水热处理容器(容器内容积120cc)中,在160℃下进行24小时热处理,在基材表面形成了沸石膜。热处理后,清洗形成体,在60℃下干燥10小时,然后在375℃下煅烧40小时,由此除去结构导向剂,得到了例3-1~例3-7的分离膜。需要说明的是,例3-1~例3-7的分离膜分别表示tpaoh水溶液中的tpaoh浓度为0.01m、0.05m、0.075m、0.1m、0.125m、0.3m、0.5m的分离膜。通过与例1相同的条件的xrd分析对所得到的分离膜的表面的结构进行了评价。图10示出在将水添加量固定为3g、将合成时间固定为24小时而改变结构导向剂(tpaoh)浓度的情况下的xrd图谱。当tpaoh浓度为0.01m时,通过xrd图谱能够确认在处理后晶种几乎没有生长。在直到tpaoh浓度为0.1m为止的范围内,膜的结晶度增加,之后逐渐降低,由此可知存在适当的tpaoh浓度。而且,关于tpaoh浓度为0.3m、0.5m的分离膜,与tpaoh浓度为0.1m的分离膜相比,膜的机械强度弱、对支撑体的损害变大。由以上结果确认到,在本条件下,0.1m为优选的结构导向剂(tpaoh)的浓度。<例4(通过改变晶种附着量而使膜厚变化时的影响)>除了通过改变晶种附着量来调节沸石膜的膜厚以外,通过与例2-6相同的方法制作了例4-1~例4-3的分离膜。然后,通过与对例2中得到的分离膜的评价相同的方法,实施了渗透汽化试验。将其结果示于表2。表2.沸石膜的膜厚不同的分离膜的etoh/h2o渗透汽化试验结果分离膜4-14-24-3膜厚(μm)689jtotal[kg/(m2·小时)]4.885.025.19etohconc.[重量%]75.776.975.6αetoh28.13028psi137151145(以往的方法)以下示出的例5~例8是涉及作为相对于本发明的比较例的现有技术的水热合成法的例子。例5~例7是在二氧化硅基材上通过水热合成法形成沸石膜的例子,例8是在氧化铝基材上通过水热合成法形成沸石膜的例子。<例5(水热合成法的研究1:水热合成时间的影响)>使用胶体二氧化硅、tpabr、氢氧化钠、蒸馏水作为原料,以使得sio2:tpabr:naoh:h2o的摩尔比为1:0.05:0.05:75的方式进行混合,在22℃下搅拌60分钟,由此得到了膜形成用溶胶。将上述的晶种附着多孔二氧化硅基材浸渍在该膜形成用溶胶中,在水热处理容器(容器内容积120cc)内在160℃下处理4小时~24小时,以基材上的晶种作为核进行了沸石的合成。热处理后,清洗形成体,在60℃下干燥10小时,然后在375℃下煅烧60小时,由此除去结构导向剂,得到了例5-1~例5-4的分离膜。需要说明的是,例5-1~例5-4的分离膜分别表示热处理时间为4小时、8小时、6小时、24小时的分离膜。然后,通过与对例2中得到的分离膜的评价相同的方法,实施了渗透汽化试验。将其结果示于表3。表3.例5中得到的分离膜的etoh/h2o渗透汽化试验结果分离膜5-15-25-35-4水热处理时间(小时)481624jtotal[kg/(m2·小时)]3.7132.512.16etohconc.[重量%]86.491.191.391.6αetoh57929598psi208273236210由例5的结果可知,在水热合成法中也可以通过适当的水热处理时间得到高分离系数α,但渗透通量jtotal停留在3[kg/m2·小时]附近。<例6(水热合成法的研究2:tpabr对sio2的摩尔比的影响)>使用胶体二氧化硅、tpabr、氢氧化钠、蒸馏水作为原料,以使得sio2:tpabr:naoh:h2o的摩尔比为1:0.005~0.1:0.05:75的方式进行混合,在22℃下搅拌60分钟,由此得到了膜形成用溶胶。将上述的晶种附着多孔二氧化硅基材浸渍在该膜形成用溶胶中,在水热处理容器(容器内容积120cc)内在160℃下处理12小时,以基材上的晶种作为核进行了沸石的合成。热处理后,清洗形成体,在60℃下干燥10小时,然后在375℃下煅烧60小时,由此除去结构导向剂,从而得到了例6-1~例6-4的分离膜。需要说明的是,例6-1~例6-4的分离膜分别表示tpabr对sio2的摩尔比为0.005、0.001、0.05、0.1的分离膜。然后,通过与对例2中得到的分离膜的评价相同的方法,实施了渗透汽化试验。将其结果示于表4。表4.例6中得到的分离膜的etoh/h2o渗透汽化试验结果分离膜6-16-26-36-4tpabr对sio2的摩尔比0.0050.010.050.1jtotal[kg/(m2·小时)]3.902.932.792.64etohconc.[重量%]83.688.389.289.6αetoh45.867.974.177.4psi174.4195.9204.2201.5<例7(水热合成法的研究3:凝胶老化温度的影响)>在水热合成法中,根据初始凝胶的状态,所得到的膜的特性容易变化。在此,不将凝胶的老化温度固定在22℃,评价了在不进行控制的室温下的老化状态下的成膜结果。使用胶体二氧化硅、tpabr、氢氧化钠、蒸馏水作为原料,以使得sio2:tpabr:naoh:h2o的摩尔比为1:0.005~0.1:0.05:75的方式进行混合,设定为室温(22℃~25℃)并搅拌60分钟,由此得到了膜形成用溶胶。将上述的晶种附着多孔二氧化硅基材浸渍在该膜形成用溶胶中,在水热处理容器(容器内容积120cc)内在160℃下处理12小时,以基材上的晶种作为核进行了沸石的合成。热处理后,清洗形成体,在60℃下干燥10小时,然后在375℃下煅烧60小时,由此除去结构导向剂,得到了例7-1~例7-4的分离膜。需要说明的是,例7-1~例7-4的分离膜分别表示tpabr对sio2的摩尔比为0.005、0.001、0.05、0.1的分离膜。然后,通过与对例2中得到的分离膜的评价相同的方法,实施了渗透汽化试验。将其结果示于表5。表5.例7中得到的分离膜的etoh/h2o渗透汽化试验结果分离膜7-17-27-37-4tpabr对sio2的摩尔比0.0050.010.050.1jtotal[kg/(m2·小时)]4.352.562.32.66etohconc.[重量%]66858984αetoh17.550.970.446.5psi72128160123由以上的例6和例7的结果可知,水热合成法对所得到的膜的初始凝胶的制造条件敏感,对凝胶的老化温度的精密控制是有必要的。<例8(在水热合成中的基材的影响:氧化铝基材)>在nikkato制造的外径12mm、内径9mm、长度80mm、孔隙率38%、平均孔径1400nm的多孔氧化铝管上,通过电泳法使高硅沸石晶种附着,从而制作了晶种附着的多孔氧化铝基材。使用胶体二氧化硅、tpabr、氢氧化钠、蒸馏水作为原料,以使得sio2:tpabr:naoh:h2o的摩尔比为1:0.005:0.05:50~150的方式进行混合,在室温下搅拌60分钟,由此得到了膜形成用溶胶。将该基材浸渍在上述的膜形成用溶胶中,在水热处理容器(容器内容积120cc)内在160℃下处理24小时,以基材上的晶种作为核进行了沸石的合成。热处理后,清洗形成体,在60℃下干燥10小时,然后在375℃下煅烧60小时,由此除去结构导向剂,得到了例8-1~例8-5的分离膜。需要说明的是,例8-1~例8-5的分离膜分别表示h2o对sio2的摩尔比为150、125、100、75、50的分离膜。然后,通过与对例2中得到的分离膜的评价相同的方法,实施了渗透汽化试验。其结果示于表6。表6.例8中得到的分离膜的etoh/h2o渗透汽化试验结果分离膜8-18-28-38-48-5sio2/h2o1/1501/1251/1001/751/50膜厚[μm]468912jtotal[kg/(m2·小时)]0.690.380.820.470.71etohconc.[重量%]52.058.084.091.086.0αetoh10.813.642.588.066.0psi75344046由例8的结果可以确认,与使用了二氧化硅基材的水热合成法、使用了二氧化硅基材的例1~例4所涉及的无凝胶法相比,在使用氧化铝基材的情况下,渗透通量、αetoh均较低。即,确认到由使用二氧化硅基材导致的分离特性的提高。(合成方法和基材对分离膜的表面结构的影响)图11和图12分别示出例4-1的分离膜的表面和与长度方向正交的截面的利用电子显微镜观察的照片。另外,图13和图14分别示出例5-4的分离膜的表面和与长度方向正交的截面的利用电子显微镜观察的照片。确认到:与例5-4的分离膜相比,例4-1的分离膜具有包含细小晶体的沸石膜,并且具有致密性。此外,图15示出例8-1的分离膜的与长度方向正交的截面的利用电子显微镜观察的照片。在支撑体为氧化铝基材的情况下,没有确认到致密的膜的形成。另外,使用bruker公司粉末x射线衍射装置d8advance对例4-1、例5-4和例8-1的分离膜的表面的结构进行了分析。在将加速电压设定为40kv、将电流设定为40ma、将光源设定为cukα、将测量角度设定为5°~80°的条件下进行了测定。将所得到的光谱示于图16和图17。以在衍射角7.3°~8.4°处显示的、晶格面归属于011和/或101面的衍射峰的强度为基准,将峰强度归一化,并将所得到的结果示于表7。表7由表7确认到,与通过使用氧化铝基材或二氧化硅基材的水热合成法得到的沸石膜相比,通过本申请的实施方式的制造方法形成的沸石膜的以在衍射角7.3°~8.4°处显示的、以晶格面归属于011和/或101面的衍射峰的强度为基准归一化后的峰强度显著不同。参考特定的方式详细地说明了本发明,但对于本领域技术人员而言显而易见的是,可以在不脱离本发明的精神和范围的情况下进行各种变更以及修正。附图标记20:分离膜21:无机氧化物多孔基材22:沸石膜24:中心孔当前第1页12