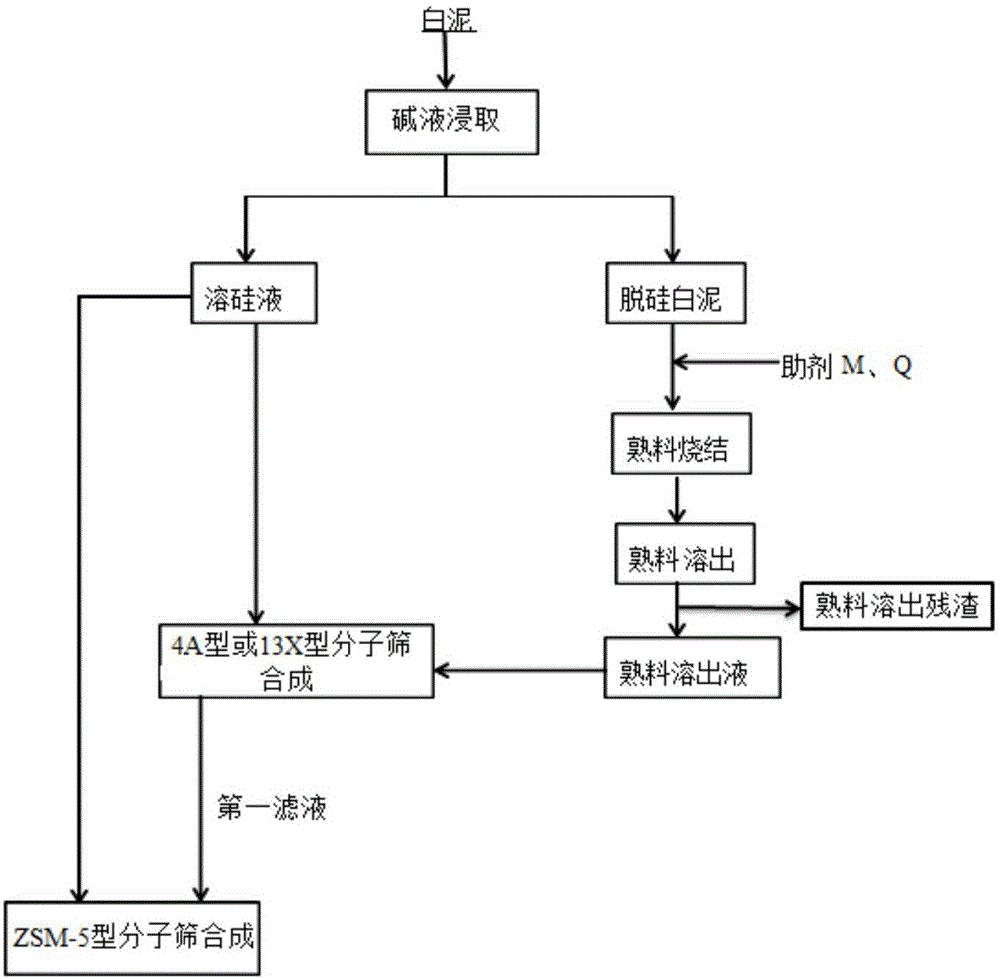
本发明涉及分子筛领域,具体涉及以白泥为原料制备分子筛的方法。
背景技术:
:粉煤灰是发电厂生产进程中的固体废弃物,排放量较大,污染严重。由于粉煤灰中含有氧化铝等有用矿物资源,因此对粉煤灰进行综合利用的研究较多。神华集团首创的“一步酸溶法”已经工业化试验验证技术可行,同时由于“一步酸溶法”具有工艺流程短等特点,拟大规模推广。但该法提铝后会产生大量的尾渣—俗称白泥,以准格尔地区粉煤灰酸法提取氧化铝工艺计算,每2.5吨粉煤灰生产1吨氧化铝,同时排出1.5吨的白泥,排放量大,污染环境。关于白泥的再利用已经有一些现有技术,cn103738977a公开了一种以白泥为原料制备4a型分子筛的方法,所述方法包括:向白泥中加入氢氧化钠溶液,反应,过滤,收集滤液;向所述滤液中加入偏铝酸钠,再通过水热合成工艺制备4a型分子筛。cn103663487a公开了一种利用白泥为原料合成y型分子筛的方法,所述方法包括以下步骤:配制偏铝酸钠结构导向剂;将白泥用氢氧化钠溶液浸取;向浸出滤液中加入水玻璃、偏铝酸钠、氢氧化钠和去离子水配制反应凝胶;晶化、洗涤后、干燥制得固体y型分子筛。但是上述两种方法都不同程度地存在不能充分地利用白泥原料,产生大量的残渣的问题,特别是白泥中15-20%左右的氧化铝作为废弃物丢弃,而在分子筛的制备过程中还需要另外加入铝源。《粉煤灰提取硫酸铝的残渣制备4a型分子筛》公开了采用粉煤灰提取硫酸铝产生的残渣为原料,以固相合成法合成4a型分子筛,通过将粉煤灰酸法提铝后的残渣与碱混合均匀、焙烧,晶化制得4a型分子筛。该方法虽然通过固相合成实现了充分利用白泥,但是仍然需要添加铝源—氢氧化铝,而且需要大量的烧碱,成本高,反应能耗大,对设备的要求高,在实际生产中不易实现。现有技术中还没有报道较独立、完善、条件温和的白泥再利用的方法。因此,亟需一种简便的、可以更有效地利用白泥而不需要额外添加硅源和铝源,并对设备要求不高,可以实现白泥全部消纳的制备分子筛的方法。技术实现要素:本发明的目的是为了克服现有技术存在的不能充分资源化利用白泥并需要额外添加硅源和铝源、对设备要求高等问题,提供一种以白泥为原料制备分子筛的方法。本发明的发明人在研究中发现,白泥的物质组成与粉煤灰相比有其特殊性:硅含量较普通粉煤灰更加富集,铝含量显著降低,fe、mg等酸溶性元素在酸法提铝过程中被大量去除,其中sio2与al2o3摩尔比(以下可以表示为硅铝比,或sio2/al2o3)约为10:1。白泥中硅铝摩尔比与高硅型分子筛、低硅型分子筛均不能完全匹配,如果粉煤灰酸法提铝残渣直接用于合成低硅分子筛(如4a型分子筛,硅铝比约为2-3;13x型分子筛,硅铝比约为2-3)时,si显著过量,需外加铝源;而用于合成高硅型分子筛(硅铝比约>30,如zsm-5型分子筛)时,al元素过量,又需外加硅源。另一方面,白泥中,莫来石、石英、锐钛矿等低活性组分较原粉煤灰进一步富集,制约白泥利用率的提高。因此如何合理且更好地利用白泥中的硅、铝资源,并在无需外加硅源和铝源的情况下制备分子筛,需要综合考虑上述因素。就此发明人提出本发明所述方法以提高白泥的利用率,并通过4a型分子筛(或13x型分子筛)和zsm-5型分子筛的联产实现白泥的完全消纳。本发明的第一方面提供了一种以白泥为原料制备分子筛的方法,该方法包括:(1)将白泥用碱液进行浸取并分离,得到溶硅液和脱硅白泥;(2)将所述脱硅白泥与助剂m、助剂q混合制备生料浆,将所述生料浆烧结形成熟料,并将所述熟料进行溶出,得到熟料溶出液;(3)将所述熟料溶出液和至少一部分所述溶硅液进行混合并进行第一晶化,分离得到4a型分子筛或13x型分子筛,以及第一滤液;(4)将第一滤液、模板剂和可选的剩余的所述溶硅液进行第二晶化,分离得到zsm-5型分子筛和第二滤液。其中所述助剂m选自生石灰、石灰石、氧化镁和碳酸镁中的至少一种,所述助剂q为碳酸钠和/或碳酸钾。本发明所述方法可以充分资源化利用白泥,最大化地从白泥中提取硅元素和铝元素,使得熟料溶出残渣量较少,熟料溶出残渣中所含的铝元素、硅元素都较少;并且在不额外添加硅源和铝源的条件下制备低硅铝比分子筛、高硅铝比分子筛,并通过分子筛的串联制备工艺使提取所得的硅元素、铝元素全部消纳;同时本发明所述方法对设备要求不高,可以使用现有设备制备分子筛。附图说明图1是本发明所述方法一种实施方式的流程示意图。具体实施方式在本文中所披露的范围的端点和任何值都不限于该精确的范围或值,这些范围或值应当理解为包含接近这些范围或值的值。对于数值范围来说,各个范围的端点值之间、各个范围的端点值和单独的点值之间,以及单独的点值之间可以彼此组合而得到一个或多个新的数值范围,这些数值范围应被视为在本文中具体公开。本发明第一方面提供了一种以白泥为原料制备分子筛的方法,该方法包括:(1)将白泥用碱液进行浸取并分离,得到溶硅液和脱硅白泥;(2)将所述脱硅白泥与助剂m、助剂q混合制备生料浆,将所述生料浆烧结形成熟料,并将所述熟料进行溶出,得到熟料溶出液;(3)将所述熟料溶出液和至少一部分所述溶硅液进行混合并第一晶化,分离得到4a型分子筛或13x型分子筛,以及第一滤液;(4)将第一滤液、模板剂和可选的剩余的所述溶硅液进行第二晶化,分离得到zsm-5型分子筛和第二滤液;其中,所述助剂m选自生石灰、石灰石、氧化镁和碳酸镁中的至少一种,所述助剂q为碳酸钠和/或碳酸钾。在发明中,所述“白泥”为粉煤灰经“一步酸溶法”提铝后产生的尾渣。白泥主要含有:sio2、fe2o3、al2o3和tio2。例如在白泥中,sio2的含量可以约为70-80重量%,al2o3的含量可以约为10-15重量%,tio2的含量可以约为3-8重量%。在本发明所述方法中,步骤(1)中,将白泥用碱液进行浸取,所述浸取是为了实现从白泥中脱除硅得到溶硅液。使用的碱液为强碱的水溶液,所述强碱可以根据现有技术来选择,例如可以为碱金属和/或碱土金属的氢氧化物,优选地所述碱液为氢氧化钾和/或氢氧化钠的水溶液。所述碱液的浓度可以根据需要来调节,例如可以为60-300g/l。相对于1000kg的所述白泥,所述碱液的用量为2-6m3。在本发明所述方法中,在步骤(1)中,所述浸取的条件为:温度为50-150℃,优选为95-110℃;时间为0.5-5h。在本发明所述方法中,在步骤(1)中,白泥经浸取分离得到溶硅液和脱硅白泥。所述脱硅白泥主要含有al2o3、sio2和tio2,其中al2o3的含量约为40-70重量%,sio2的含量约为5-25重量%,主要物相为莫来石和锐钛矿。在本发明所述方法中,步骤(2)是为了将脱硅白泥中的铝元素活化以从脱硅白泥中提取铝元素。在制备生料浆的过程中,所述助剂m、助剂q的添加量可以根据脱硅白泥的成分来确定,调节助剂m、助剂q的量以使得所述生料浆的组成中以[a2o]/([al2o3]+[fe2o3])计的摩尔比为0.5-2.2,以[eo]/([sio2]+[tio2])计的摩尔比为0.5-2.5,含水率为35-50重量%,其中a2o和eo分别为助剂q和助剂m的氧化物形式。优选地,所述生料浆的组成中以[a2o]/([al2o3]+[fe2o3])计的摩尔比为1.5-2.2,以[eo]/([sio2]+[tio2])计的摩尔比为0.8-1.2,含水率为35-50重量%,在本发明所述方法中,在步骤(2)中,所述助剂m和助剂q可以以任何合适的形式添加以制备生料浆,例如以固体形式或水溶液形式添加。在本发明所述方法中,在步骤(2)中,所述烧结是为了实现脱硅白泥中铝元素的活化,将脱硅白泥中不可溶的以莫来石相存在的氧化铝烧结转化成可溶性盐如铝酸钠。在本发明中,设置助剂m、助剂q的量使得所述生料浆的组成中以[a2o]/([al2o3]+[fe2o3])计的摩尔比为0.5-2.2,以[eo]/([sio2]+[tio2])计的摩尔比为0.5-2.5,这样设置是为了在烧结过程中,使元素al尽可能多地与助剂q反应生成含al元素的可溶盐。由于烧结过程中元素fe的存在也会消耗掉一部分助剂q,因而也需要考虑存在的元素fe。同时设置以[eo]/([sio2]+[tio2])计的摩尔比为0.5-2.5,是为了使烧结时硅元素与助剂m反应生成硅酸盐,以释放元素al使其与助剂q反应。所述烧结的条件为:温度为1000-1300℃,优选地,温度为1000-1150℃;时间为0.5-2h。在本发明所述方法中,在步骤(2)中,烧结形成熟料之后,将所述熟料进行溶出,所述溶出包括将所述熟料置于水中或水溶液中。所述水溶液为以水作为溶质的溶液。水或水溶液用于溶解熟料中的铝可溶性盐。只要能达到溶解熟料中铝可溶性盐的目的,所述水溶液可以根据现有技术任意选择,优选地,所述水溶液选自氢氧化钠的稀溶液、氢氧化钾的稀溶液、碳酸钠的水溶液、碳酸钾的水溶液或它们任意组合的混合液,所述氢氧化钠或氢氧化钾的稀溶液的浓度可以根据需要调整,例如可以为10-30g/l。在本发明所述方法中,步骤(2)中,所述溶出的条件为:温度为60-90℃,时间为0.5-3h。所述溶出是为了将铝元素以可溶性铝盐的形式从熟料中提取出来。所述熟料经溶出后得到熟料溶出液和熟料溶出残渣。熟料溶出液主要成分为铝的可溶盐,如铝酸钠和/或铝酸钾,熟料溶出残渣的主要成分为硅酸钙和富钛矿,当熟料溶出残渣中钛元素含量超过30重量%时,可以该熟料溶出残渣为原料提取二氧化硅。在本发明所述方法的一种优选的实施方式中,调节助剂m、助剂q的量以使得所述生料浆的组成中以[a2o]/([al2o3]+[fe2o3])计的摩尔比为2,以[eo]/([sio2]+[tio2])计的摩尔比为1,制备的生浆料可以在较低的温度下进行烧结,例如可以在1000-1150℃温度下进行烧结,得到的熟料进行溶出后产生的熟料溶出残渣较少。在本发明所述方法的另一种优选的实施方式中,调节助剂m、助剂q的量以使得所述生料浆的组成中以[a2o]/([al2o3]+[fe2o3])计的摩尔比为1,以[eo]/([sio2]+[tio2])计的摩尔比为2,制备的生浆料在1200-1300℃温度下进行烧结,得到的熟料进行溶出后产生熟料溶出残渣,所述熟料溶出残渣中al2o3的含量较少。在本发明中,所述方法还可以包括在溶出步骤之前,粉碎所述熟料,优选地将熟料粉碎至粒径为3-8mm。在本发明所述方法中,步骤(3)中,将熟料溶出液与至少一部分溶硅液混合,并进行第一晶化反应,过滤得到4a型分子筛或13x型分子筛,以及第一滤液。在此,通过调节熟料溶出液、溶硅液的用量以得到4a型分子筛或13x型分子筛。在本发明所述方法的一种优选的实施方式中,在步骤(3)中,将所述熟料溶出液和20-100重量%的溶硅液进行混合并第一晶化,分离得到4a型分子筛或13x型分子筛,以及第一滤液。在本发明所述方法,第一滤液中以al2o3计al的含量为1-5g/l。第一晶化的条件可以根据所需制备的分子筛、现有技术来选择。如本发明人所发现的,第一滤液、模板剂和可选的剩余的溶硅液混合之后,所得混合液中sio2/al2o3摩尔比为20-120,na2o/al2o3摩尔比=2-12,该混合液经晶化反应可以用于制备zsm-5型分子筛。所述模板剂可以根据现有技术来选择,例如可以选自四乙基氢氧化铵、四丙基溴化铵、异丙胺、四乙基氢氧化铵和二正丙胺中的至少一种。在本发明中,所述“可选的剩余的溶硅液”应理解为:1)如果步骤(3)中使用熟料溶出液与一部分溶硅液晶化以制备4a型分子筛或13x型分子筛,则“可选的剩余的溶硅液”应理解为步骤(3)进行之后剩余的溶硅液,工艺如图1所示;2)如果步骤(3)中使用熟料溶出液与全部溶硅液经晶化反应制备4a型分子筛或13x型分子筛,则“可选的剩余的溶硅液”应理解为不使用溶硅液。在本发明中,步骤(4)中,所述第二晶化的条件可以根据现有技术来调整。第二晶化后,分离所得第二滤液的主要成分为氢氧化钠溶液,以al2o3计的铝元素含量为0-1g/l。在一种优选的实施方式中,所述第二滤液可以返回至步骤(1)作为碱液以脱除白泥中的硅元素。本发明所述方法通过上述“碱液溶硅”和“烧结熟料溶铝”的步骤将白泥中的硅元素、铝元素全部或尽可能多地提取出来,使得所得熟料溶出残渣较少,并且熟料溶出残渣中残留的硅、铝元素较少,实现了充分资源化利用白泥;并且在不额外添加硅源和铝源的条件下通过低硅铝比分子筛、高硅铝比分子筛的串联制备工艺实现所提取的硅元素(溶硅液)、铝元素(熟料溶出液)的全部消纳;同时本发明所述方法对设备要求不高,可以使用现有的设备。以下将通过实施例对本发明进行详细描述。实施例中使用的白泥为由内蒙古准格尔地区电厂的粉煤灰进行“一步酸溶法”提取氧化铝产生的废渣。白泥中氧化硅含量为78.7%,氧化铝含量为13.4%,氧化钛含量为5.2%;主要物相成分为非晶态二氧化硅、莫来石和锐钛矿,其主要成分如表1所示。实施例1(1)取上述组成的白泥1000g,在氢氧化钠溶液浓度170g/l,白泥与氢氧化钠溶液比例为1000kg:4m3,在90℃下搅拌反应2小时,过滤洗涤,得到溶硅液(主要成分为硅酸钠溶液,包含少量铝酸钠溶液)和脱硅白泥,脱硅白泥主要成分见表1,其中氧化硅含量为23.2%,氧化铝含量为56.7%,氧化钛含量为11.7%,主要物相为莫来石和锐钛矿。(2)将脱硅白泥与石灰石、碳酸钠溶液进行混合制备生料浆,使得所述生料浆的组成中以[na2o]/([al2o3]+[fe2o3])计的摩尔比为2,以[cao]/([sio2]+[tio2])计的摩尔比为1,含水率为40%,将生料浆喷入回转窑在1000℃下进行烧结1.5h,将烧结产生的熟料粉碎至粒径为3-8mm,在水中75℃下将熟料进行溶出1h,产生的熟料溶出液主要成分为铝酸钠,溶出后产生熟料溶出残渣185g,主要成分见表1。(3)将50重量%的所述溶硅液和熟料溶出液混合搅拌(混合液中以[na2o]/[sio2]计的摩尔比为1.3,以[sio2]/[al2o3]计的摩尔比为2.2),并进行第一晶化,然后洗涤、过滤干燥得到分子筛和第一滤液,所述分子筛经xrd测试显示即为4a型分子筛。(4)将剩余的所述溶硅液、所述第一滤液和模板剂四丙基溴化铵混合进行第二晶化,然后洗涤、过滤得到分子筛和第二滤液(第二滤液中以al2o3计的铝元素含量为0.1g/l),所得分子筛经xrd测试显示即为zsm-5型分子筛。所述第二滤液返回至步骤(1)的溶硅工艺。实施例2参照实施例1所述方法制备分子筛,不同的是:(3)将70重量的%溶硅液和熟料溶出液混合搅拌(混合液中以[na2o]/[sio2]计的摩尔比为1.4、以[sio2]/[al2o3]计的摩尔比为4),并进行第一晶化,然后洗涤、过滤得到分子筛和第一滤液,所述分子筛经xrd测试显示即为13x型分子筛。(4)将剩余的溶硅液、所述第一滤液与模板剂四丙基溴化铵混合晶化,然后洗涤、过滤得到分子筛和第二滤液(其中以al2o3计的铝源含量为0.5g/l)。所得分子筛经xrd测试显示为zsm-5型分子筛。所述第二滤液返回至步骤(1)的溶硅步骤。实施例3参照实施例1所述方法制备分子筛,不同的是:(3)将全部溶硅液和熟料溶出液混合搅拌(混合液中以[na2o]/[sio2]计的摩尔比为1.8、以[sio2]/[al2o3]计的摩尔比为5),并进行第一晶化,然后洗涤、过滤得到分子筛和第一滤液,所述分子筛经xrd测试显示即为13x型分子筛。(4)将剩余的溶硅液、所述第一滤液与模板剂四丙基溴化铵混合晶化,然后洗涤、过滤得到分子筛和第二滤液(其中以al2o3计的铝源含量为0.5g/l)。所得分子筛经xrd测试显示为zsm-5型分子筛。所述第二滤液返回至步骤(1)的溶硅步骤。实施例4参照实施例1所述方法制备分子筛,不同的是:(3)将20重量的%溶硅液和熟料溶出液混合搅拌(混合液中以[na2o]/[sio2]计的摩尔比为1.1、以[sio2]/[al2o3]计的摩尔比为2),并进行第一晶化,然后洗涤、过滤得到分子筛和第一滤液,所述分子筛经xrd测试显示即为4a型分子筛。(4)将剩余的溶硅液、所述第一滤液与模板剂四丙基溴化铵混合晶化,然后洗涤、过滤得到分子筛和第二滤液(其中以al2o3计的铝源含量为0.8g/l)。所得分子筛经xrd测试显示为zsm-5型分子筛。所述第二滤液返回至步骤(1)的溶硅步骤。实施例5参照实施例1所述方法制备分子筛,不同的是,在步骤(2)中,将脱硅白泥与生石灰、碳酸钠溶液进行混合制备生料浆,使得所述生料浆的组成中以[na2o]/([al2o3]+[fe2o3])计的摩尔比为1,以[cao]/([sio2]+[tio2])计的摩尔比为2,含水率为42%,将生料浆喷入回转窑在1250℃下进行烧结1h,得到熟料溶出后产生的熟料溶出残渣再经水热脱碱为240g,熟料溶出残渣的主要成分见表1。所得第二滤液中以al2o3计的铝元素含量为1g/l。实施例6参照实施例1所述方法制备分子筛,不同的是,在步骤(2)中将脱硅白泥与碳酸镁、碳酸钾溶液进行混合制备生料浆,使得所述生料浆的组成中以[k2o]/([al2o3]+[fe2o3])计的摩尔比为2,以[mgo]/([sio2]+[tio2])计的摩尔比为1,含水率为42%,将生料浆喷入回转窑在1150℃下进行烧结1.5h,将烧结产生的熟料粉碎至粒径为3-8mm,在氢氧化钾稀溶液(浓度为15g/l)中75℃下将熟料进行溶出1h,产生的熟料溶出液主要成分为铝酸钾,溶出后产生的熟料溶出残渣为215g,其主要成分见表1。结果所得第二滤液中以al2o3计的铝源含量为0.5g/l。实施例7参照实施例1所述方法制备分子筛,不同的是,在步骤(2)中将按照实施例1制备的生料浆喷入回转窑在1300℃下进行烧结2h最后产生的熟料溶出残渣为198g,其主要成分见表1。结果所得第二滤液中以al2o3计的铝源含量为0.6g/l。表1熟料溶出残渣成分实施例1实施例5实施例6实施例7总重量/g185240215198al2o3/重量%1.351.21.251.38sio2/重量%35.225.325.935.5tio2/重量%27.621.721.926.7fe2o3/重量%2.71.82.22.6na2o/重量%1.51.21.41.7通过表1的结果可以看出,本发明所述方法可以最大化地资源化利用白泥,最大化地从白泥中提取硅和铝,同时在制备分子筛时不需要额外添加硅源和铝源。本发明所述方法可将白泥中的al2o3含量降低至2%以下,并且通过本发明所述工艺流程制备分子筛,可以实现溶硅液和熟料溶出液的全部消纳。以上详细描述了本发明的优选实施方式,但是,本发明并不限于此。在本发明的技术构思范围内,可以对本发明的技术方案进行多种简单变型,包括各个技术特征以任何其它的合适方式进行组合,这些简单变型和组合同样应当视为本发明所公开的内容,均属于本发明的保护范围。当前第1页12