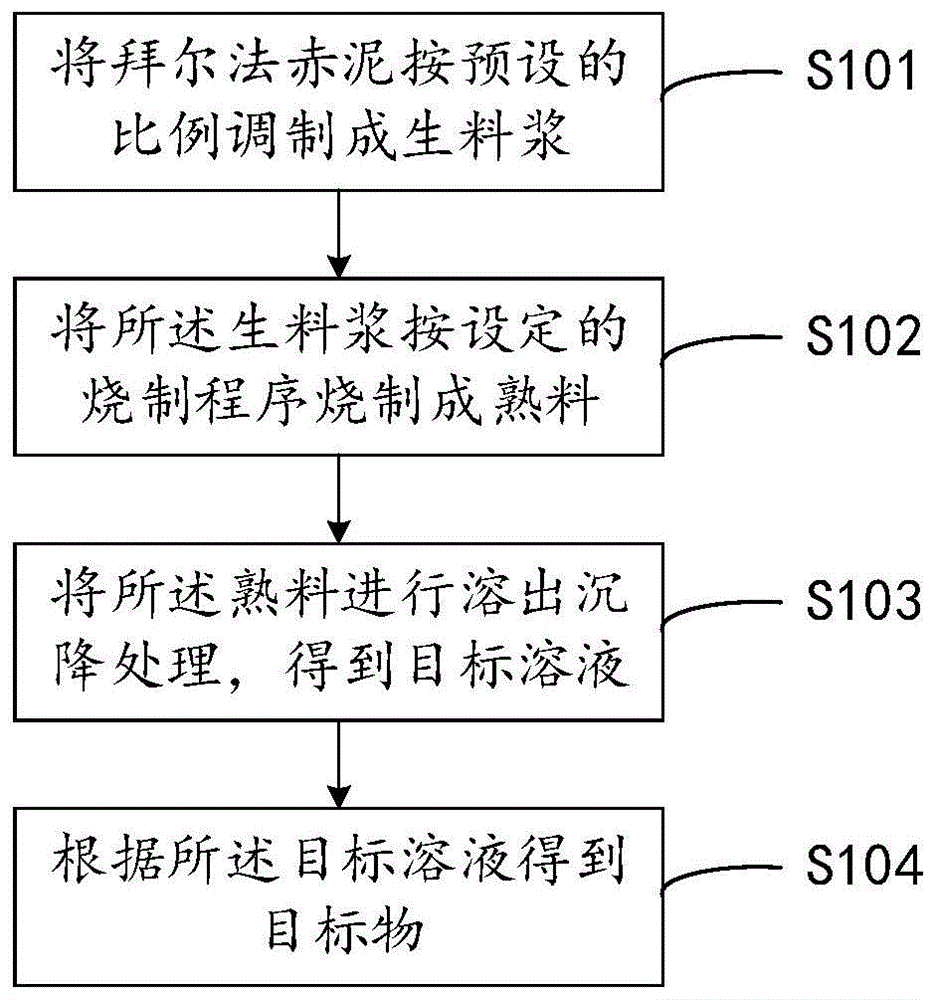
本发明涉及化学品制造技术领域,具体而言,涉及一种串联法烧结方法及系统。
背景技术:
铝土矿品位宜采用联合法生产氧化铝,目前主要氧化铝生产厂家均采用混联法。混联法是将拜尔法生产系统与烧结法生产系统进行并联,分别放入不同品位的矿石原料,拜耳系统消耗高品位矿石,烧结系统消耗中、低品位矿石,这样达到矿石资源的完全、有效利用。但混联法存在流程复杂、能耗高、投资大、成本高等诸多缺点。
技术实现要素:
为了克服上述现有技术中的不足,本发明提供一种串联法烧结方法及系统,以解决上述问题。
为了实现上述目的,本发明实施例所提供的技术方案如下所示:
第一方面,本发明实施例提供一种串联法烧结方法,包括:
将拜尔法赤泥按预设的比例调制成生料浆;
将所述生料浆按设定的烧制程序烧制成熟料;
将所述熟料进行溶出沉降处理,得到目标溶液;根据所述目标溶液得到目标物。
可选地,所述将拜尔法赤泥按预设的比例调制成生料浆的步骤,包括:在拜尔法赤泥中加入第一预设比例的碱粉配置成碱赤泥;将所述碱赤泥加入第二预设比例的预设材料配置成生料浆。
可选地,所述预设材料包括石灰石和无烟煤。
可选地,所述将所述生料浆按设定的烧制程序烧制成熟料的步骤,包括:采用喷入法将所述生料浆从窑尾喷入窑内;将煤粉从窑头喷入窑内;经过设定的烧制流程将所述生料浆烧制成熟料。
可选地,所述将所述生料浆按设定的烧制程序烧制成熟料的步骤,还包括:将喷入时产生的窑灰进行收集并返入窑内烧制。
可选地,所述将所述熟料进行溶出沉降处理,得到目标溶液的步骤,包括:将所述熟料进行第一段溶出磨处理;将所述第一段溶出磨处理后的溶出液进行分离沉降处理,得到目标溶液。
可选地,所述将所述熟料进行溶出沉降处理的步骤,还包括:将所述熟料进行第一段溶出磨处理;将所述第一段溶出磨处理后的返砂进行第二段溶出磨循环处理;将所述第二段溶出磨循环处理后的溶出液进行回收利用。
可选地,所述将所述熟料进行溶出沉降处理的步骤,还包括:将分离沉降后底流赤泥进行洗涤处理;将洗涤处理后的溢流进行碱的回收利用处理。
第二方面,本发明实施例提供一种串联法烧结系统,包括:
配碱槽,用于在拜尔法赤泥中加入第一预设比例的碱粉配置成碱赤泥。
管磨机,用于将所述碱赤泥加入第二预设比例的预设材料配置成生料浆。
烧成窑,用于根据设定的烧制流程将所述生料浆烧制成熟料。
第一段溶出磨,用于对所述熟料进行研磨并与调整液制成混合液体。
分离沉降槽,用于将所述混合液体进行沉降处理得到目标溶液。
拜尔法稀释后槽,用于将所述目标溶液进行脱硅处理得到目标物。
可选地,所述串联法烧结系统还包括:
第二段溶出磨,用于对所述第一溶出磨处理后的返砂进行多次研磨处理。
洗涤槽,用于对分离沉降槽处理后的底流赤泥进行多次洗涤以及对第二溶出磨处理后的返砂进行洗涤,并将洗涤后的溢流进行碱的回收利用处理。
本发明提供的串联法烧结方法及系统,直接以拜尔法生产系统的拜尔法赤泥为原料,拜尔法赤泥粒度细、温度高,这样既降低了料浆磨制的能耗和研磨体消耗,又提高料浆温度而降低熟料烧结煤耗,降低了能耗的基础上降低了投资和生产成本。
为使本发明的上述目的、特征和优点能更明显易懂,下文特举本发明实施例,并配合所附附图,作详细说明如下。
附图说明
为了更清楚地说明本发明实施例的技术方案,下面将对实施例中所需要使用的附图作简单地介绍。应当理解,以下附图仅示出了本发明的某些实施例,因此不应被看作是对范围的限定,对于本领域普通技术人员来讲,在不付出创造性劳动的前提下,还可以根据这些附图获得其他相关的附图。
图1为本发明实施例提供的串联法烧结方法总流程图;
图2为本发明实施例提供的步骤s102的详细流程图;
图3为本发明实施例提供的步骤s103的第一处理过程流程图;
图4为本发明实施例提供的步骤s103的第二处理过程流程图;
图5为本发明实施例提供的碱的回收利用流程图;
图6为本发明实施例提供的串联法烧结系统使用总流程图。
图标:50-串联法烧结系统;501-配碱槽;502-管磨机;503-合格料浆槽;504-隔膜泵;505-烧成窑;506-熟料仓;507-第一段溶出磨;508-分离沉降槽;509-拜尔法稀释后槽;550-煤磨机;521-一次洗涤槽;522-二次洗涤槽;523-三次洗涤槽;524-四次洗涤槽;525-外排泵房;530-调整液槽;540-第二段溶出磨。
具体实施方式
下面将结合本发明实施例中的附图,对本发明实施例中的技术方案进行清楚、完整地描述。显然,所描述的实施例仅仅是本发明的一部分实施例,而不是全部的实施例。通常在此处附图中描述和示出的本发明实施例的组件可以以各种不同的配置来布置和设计。
因此,以下对在附图中提供的本发明的实施例的详细描述并非旨在限制要求保护的本发明的范围,而是仅仅表示本发明的选定实施例。基于本发明的实施例,本领域技术人员在没有做出创造性劳动的前提下所获得的所有其他实施例,都属于本发明保护的范围。
应注意到:相似的标号和字母在下面的附图中表示类似项,因此,一旦某一项在一个附图中被定义,则在随后的附图中不需要对其进行进一步定义和解释。
在本发明的描述中,需要说明的是,术语“中”、“上”、“下”、“水平”、“内”、“外”等指示的方位或位置关系为基于附图所示的方位或位置关系,或者是该发明产品使用时惯常摆放的方位或位置关系,仅是为了便于描述本发明和简化描述,而不是指示或暗示所指的装置或元件必须具有特定的方位、以特定的方位构造和操作,因此不能理解为对本发明的限制。此外,术语“第一”、“第二”等仅用于区分描述,而不能理解为指示或暗示相对重要性。
此外,术语“水平”、“竖直”等术语并不表示要求部件绝对水平或悬垂,而是可以稍微倾斜。如“水平”仅仅是指其方向相对“竖直”而言更加水平,并不是表示该结构一定要完全水平,而是可以稍微倾斜。
在本发明的描述中,需要说明的是,除非另有明确的规定和限定,术语“设置”、“相连”、“连接”应做广义理解,例如,可以是固定连接,也可以是可拆卸连接,或一体地连接。可以是机械连接,也可以是电性连接。可以是直接相连,也可以通过中间媒介间接相连,可以是两个元件内部的连通。对于本领域的普通技术人员而言,可以具体情况理解上述术语在本发明中的具体含义。
下面结合附图,对本发明的一些实施方式作详细说明。在不冲突的情况下,下述的实施例及实施例中的特征可以相互组合。
经申请人研究还发现目前现有的烧结法和混联法烧结窑处理的生料,其铝硅比一般在2.5-3.5,而对于低铝硅比(a/s≤2.0)拜尔法赤泥生料的烧结,因烧成窑难控制、沉降槽易跑浑等问题,工业生产一直尚无成熟成功的生产经验。
本申请提供以下几个实施例可以有效解决前面的各个技术问题,具体描述如下。
请参照图1,是本发明实施例提供的串联法烧结方法总流程图,串联法烧结方法包括以下步骤:
步骤s101,将拜尔法赤泥按预设的比例调制成生料浆。
在本发明提供的实施例中,拜尔法四洗底流赤泥加入第一预设比例的碱粉(例如:碳酸钠、碳酸氢钠)混合配制成碱赤泥,碱赤泥再与第二预设比例的石灰石和无烟煤磨制成含水分在40%左右的生料浆。
具体的,在进行生料浆配制时,入磨石灰石的粒度大小控制在40mm以下;入磨无烟煤的粒度大小控制在25mm以下;碱赤泥水分的比例控制在50%-52%范围内;生料浆的细度控制在120目筛子的通过率在14%以下;生料浆水分的比例控制在42%以下;碱比控制在1.04-1.12范围内,钙比控制在1.82-1.95范围内。
步骤s102,将所述生料浆按设定的烧制程序烧制成熟料。
在本发明提供的实施例中,在生料浆调配完成以后,采用喷入法将生料浆和煤粉喷入窑内,经过设定的烧制流程将生料浆烧制成熟料。
具体的,在进行熟料烧制时,煤粉灰所占比例小于12%;发热量控制在27.2-29.3兆焦/公斤;挥发的份额控制在25%-28%范围内,固定碳的比例控制在51%以上,含硫量控制在1%以下;烧制完成的熟料中氧化铝的标准溶出率ηa标大于85%;熟料氧化钠的标准溶出率ηa标大于95%;熟料破碎后的粒度控制在20mm以下;烧结时的温度控制在1120℃-1180℃范围内;窑尾的温度控制在420℃以下。
步骤s103,将所述熟料进行溶出沉降处理,得到目标溶液。
在本发明提供的实施例中,在熟料烧制完成后,就需要对熟料进行溶出沉降处理,以获得所需要的目标溶液用于进行氧化铝的生产。
具体的,在进行溶出沉降处理时,采用两段溶出,并在此基础进行优化改造后,大幅缩短溶出时间,提高二段磨溶出浓度及加大一段磨出料量,保证浓度的情况下降低了固含;溶出温度控制在85℃-90℃范围内;溶出液的苛性比值(ak)控制在1.10-1.20范围内;氧化铝的净溶出率大于85%;氧化钠净溶出率大于91%。分离沉降槽的温度控制在80℃-82℃范围内;洗涤槽温度控制在75℃-82℃范围内;洗涤洗水的温度控制在75℃-85℃范围内;分离粗液的悬浮物小于1g/l;末次底流的液体与固体的重量比(l/s)范围控制在1-1.5范围内;末次底流的附损控制在7.5g/l以下;弃赤泥附液中氧化钠的损失控制在5kg/t以内。
s104,根据所述目标溶液得到目标物。
在本发明提供的实施例中,将对最终获得的目标溶液进行脱硅处理进而得到所需的目标物。目标物为氧化铝。
通过上述步骤,解决了熟料中氧化铝含量太低,为了提高溶出液氧化铝浓度造成的固含高二次损失大的问题。避免了因高温导致的硅含量剧增问题,也避免了低温导致的溶液粘稠和赤泥结块问题。有效的解决了串联法中分离沉降槽处理液量小经常跑浑的难点问题。
请参照图2,是本发明实施例提供的步骤s102的详细流程图,在采用串联法烧结时,因为烧成窑烧结范围过窄,非常难控制,所以本发明实施例采用以下步骤来解决,其具体内容如下:
步骤s201,采用喷入法将所述生料浆从窑尾喷入窑内。
在本发明提供的实施例中,采用喷入法将生料浆成雾状从窑尾喷入窑内,生料浆的喷入量按照设定值进行。
步骤s202,采用喷入法将煤粉从窑头喷入窑内。
在本发明提供的实施例中,采用喷入法将煤粉从窑头喷入窑内,煤粉的喷入量按照设定值进行。通过这种方式,在煤粉充分燃烧的同时能够实现对烧制温度的控制,更好地实现对拜耳法赤泥的烧制。
步骤s203,将喷入时产生的窑灰进行收集并返入窑内烧制。
在本发明提供的实施例中,喷入法产生的窑灰可以进行收集,然后返回窑内继续进行烧制。
具体的,因为喷入法会产生大量的窑灰,所以综合使用竖直烟道、旋风收尘、电收尘等方法来对窑灰进行收集,再把收集到的窑灰返回窑内继续进行烧制。
步骤s204,经过设定的烧制流程将所述生料浆烧制成熟料。
在本发明提供的实施例中,在对生料浆烧制时,设定的烧制流程可以是:将配置好的生料浆在窑内经过烘干带的烘干后依次经过预热带、分解带、烧成带完成熟料的烧制,最后通过冷却带进行冷却处理。
通过上述步骤,充分解决了铝硅比小于2.0的物料烧结范围窄,温度低的问题,对窑灰进行回收再利用,也节约了成本,提高了产量。
请参照图3、图4,图3是本发明实施例提供的步骤s103的第一处理过程流程图。图4是本发明实施例提供的步骤s103的第二处理过程流程图。
在熟料烧制完成后进行溶出沉降处理时,其具体步骤如下:
步骤s301,将所述熟料进行第一段溶出磨处理。
在本发明提供的实施例中,为了获得适用于氧化铝生产的目标溶液,需要先对熟料进行溶出磨处理,获得溶出液。
步骤s302,将所述第一段溶出磨处理后的溶出液进行分离沉降处理,得到目标溶液。
在本发明提供的实施例中,在进行溶出磨处理得到溶出液后,需对其进行分离沉降处理,得到用于生产氧化铝的目标溶液。
步骤s303,将所述第一段溶出磨处理后的返砂进行第二段溶出磨循环处理。
在本发明提供的实施例中,熟料在进行第一段溶出磨处理后,返砂将进行第二段溶出磨循环处理,直到返砂粒度大小达到设置的范围。
步骤s304,将所述第二段溶出磨循环处理后的溶出液进行回收利用。
在本发明提供的实施例中,为了更好地节约成本,对第二段溶出磨循环处理后的溶出液进行回收利用,降低了泥砂固含量高造成的二次损失。
具体的,对进行第二段溶出磨处理后的溶出液进行第一次洗涤后的溢流进行回收利用。
经过上述步骤,实现了对氧化铝的高效生产,提高了生产量,也节约了生产成本。
请参照图5,是本发明实施例提供的碱的回收利用流程图;为了更好地实现碱的回收利用,降低生产成本,采用以下步骤实现碱的回收利用,其具体内容如下:
步骤s401,将分离沉降后底流赤泥进行洗涤处理。
在本发明提供的实施例中,在进行分离沉降处理后,底流赤泥中仍然含有大量的碱,若对其直接进行排放,不但会污染环境,还造成了碱的浪费,所以在进行排放之前,进行多次洗涤,回收其中的碱是非常有必要的。
本实施例对底流赤泥进行了四次洗涤处理,最后进行洗水处理后才将泥砂进行排放。
步骤s402,将洗涤处理后的溢流进行碱的回收利用处理。
在本发明提供的实施例中,对底流赤泥进行四次洗涤后获得的溢流进行回收利用处理,获得其中的碱。
具体的,将分离沉降处理后的底流赤泥经过第一次洗涤后的溢流进行碱的回收利用处理,对第一次洗涤后的底流赤泥进行第二次洗涤并把洗涤后的溢流进行碱的回收利用处理。对第二次洗涤后的底流赤泥进行第三次洗涤处理。对第三次洗涤后的底流赤泥进行第四次洗涤处理,在进行第四次洗涤时加入洗水进行反向洗涤。
更为具体的,进行反向洗涤时,第四次洗涤后的溢流采用第三次洗涤的方式进行洗涤并再次把第三次洗涤后的溢流采用第二次洗涤的方式进行洗涤,最后再将第二次洗涤后的溢流进行碱的回收利用处理。
经过上述步骤,实现了底流赤泥中碱的回收利用,也减少了对环境的污染、减少了生产成本。
请参照图6,是本发明实施例提供的串联法烧结系统使用总流程图。串联法烧结系统50包括:配碱槽501;与配碱槽501连接的管磨机502,与管磨机502连接的合格料浆槽503;与合格料浆槽503连接的隔膜泵504;与隔膜泵504连接的烧成窑505;与烧成窑505连接的熟料仓506;与熟料仓506连接的第一段溶出磨507;与第一段溶出磨507连接的分离沉降槽508;与分离沉降槽508连接的拜尔法稀释后槽509。
串联法烧结系统还包括:与烧成窑505连接的煤磨机550;与第一段溶出磨507连接的调整液槽530;与第一段溶出磨507连接的第二段溶出磨540;与分离沉降槽508连接的一次洗涤槽521;与一次洗涤槽521连接的二次洗涤槽522;与二次洗涤槽522连接的三次洗涤槽523;与三次洗涤槽523连接的四次洗涤槽524;与四次洗涤槽524连接的外排泵房525。
具体的,配碱槽501用于将第一预设比例(如图1所述)的纯碱和拜尔法四洗底流赤泥配制成碱赤泥,碱赤泥经过泵送往碱赤泥储槽储存,碱赤泥储槽内的碱赤泥通过泵送至管磨机502,管磨机502再将第二预设比例(如图1所述)的石灰石和无烟煤配制成生料浆,在生料浆配制完成后,再经泵将磨制后的生料浆送至料浆调配槽储存,各料浆调配槽经取样分析按要求的碱比、钙比等指标进行调配至合格,在经泵送至合格料浆槽503储存。
合格料浆经隔膜泵504、喷枪使料浆成雾状从窑尾喷入烧成窑505内,煤粉通过燃烧器从窑头喷入进行燃烧,含水40%左右的生料浆在窑内烘干带基本干燥,成为含水8%以下的干料面,并顺次经过预热带、分解带、烧成带烧成熟料,然后经过冷却带进入篦冷机,篦冷机降低熟料温度并将熟料破碎至粒度≤20mm后,由链斗输送机、槽式输送机等输送设备将熟料贮存在熟料仓506中。
原煤由皮带输送到原煤仓内,经耐压式称重给煤机均匀定量地加入煤磨机550内,磨内干燥介质来自篦冷机热风,磨制合格的煤粉经过布袋收尘器收集进入煤粉计量仓,过滤后的气体经煤粉离心通风机排入大气。使用烧成窑505时煤粉经锁风定量给煤机输送到煤风混合管,经煤粉罗茨风机、燃烧器喷入烧成窑505内燃烧。
具体的,煤磨机550可以是辊盘式磨煤机,但不限于,也可以是立式磨粉机、高压悬辊磨机、中速微粉磨机等。输送机、篦冷机的种类也不对其进行限定,能满足实际应用需求即可。
熟料仓506的熟料经定量给料机,链斗输送机送往第一段溶出磨507,按照每吨熟料约加入2.4-2.7m3的比例加入调整液或一次洗涤槽521的溢流(调整液或一次洗涤槽521的溢流存储在调整液槽530中,成分包括铝酸钠),再在第一段溶出磨507进行铝酸钠的溶出反应,溶出后得到的混合液体经溜槽进入一段分级机,一段分级机溢流经泵送往分离沉降槽508。一段磨分级机返砂由二次洗液冲进二段溶出磨540闭路系统,二段分级机溢流经泵送往一次洗涤槽521,二段分级机返砂返回第二段溶出磨540循环磨细。
分离沉降槽508进行沉降处理后获得的目标溶液(即粗液)送拜尔法稀释后槽509进行脱硅处理后生产氧化铝,底流赤泥进入一次洗涤槽521,并依次经过二次洗涤槽522、三次洗涤槽523的洗涤、四次洗涤槽524的洗涤后,四次洗涤槽524的底流(即:弃赤泥)经外排泵房525排入赤泥库。
在四次洗涤槽524进行洗涤时还会加入洗水,进行反向洗涤。具体的,四次洗涤槽524的溢流先进入三次洗涤槽523进行洗涤。洗涤完以后的溢流再进入二次洗涤槽522进行洗涤,二次洗涤槽522的溢流最后送往调整液槽530,实现碱的回收利用。
需要说明的是,上述洗涤过程只是本发明实施例众多实施例中的一部分,洗涤槽的数目并不局限于上述的数目,可以根据实际应用需求进行增加或者减少。
综上所述,本发明提供一种串联法烧结方法及系统,本发明提供的串联法烧结方法及系统,在进行氧化铝的生产时与目前的广泛使用的混联法相比具有诸多优势。首先,目前广泛使用的混联法生产氧化铝是将拜尔法生产系统与烧结法生产系统进行并联,分别利用不同品位的矿石原料进行氧化铝的生产,虽然一定程度上达到了矿石资源有效利用,但是拜尔法所占比例低、能耗高,也就造成了需要投入更高的成本,增加更多的投资;而本发明采用串联法烧结方法,将拜尔法生产系统与烧结法生产系统进行串联,烧结法生产系统以拜尔法生产系统产出的赤泥作为原料,因为拜尔法赤泥本身温度就很高,在烧结时也就减少了能耗,从而降低了成本和投资。其次,目前现有的烧结法和混联法烧结窑处理的生料,铝硅比一般在2.5-3.5,对于低铝硅比(2.0以下)的拜尔法赤泥生料的烧结并无成熟且成功的经验,而本发明提供的串联法在利用拜尔法对高铝硅比的矿石进行氧化铝的生产的基础上,也能利用低铝硅比的拜尔法赤泥实现氧化铝的生产。最后,本发明还进行了碱的回收利用处理,降低了碱耗;在生料浆制作工程中加入石灰石,解决了铁使赤泥沉降性能变差的问题,也为含铁量高的赤泥的进一步利用奠定了基础。
以上所述仅为本发明的部分实施例而已,并不用于限制本发明,对于本领域的技术人员来说,本发明可以有各种更改和变化。凡在本发明的精神和原则之内,所作的任何修改、等同替换、改进等,均应包含在本发明的保护范围之内。