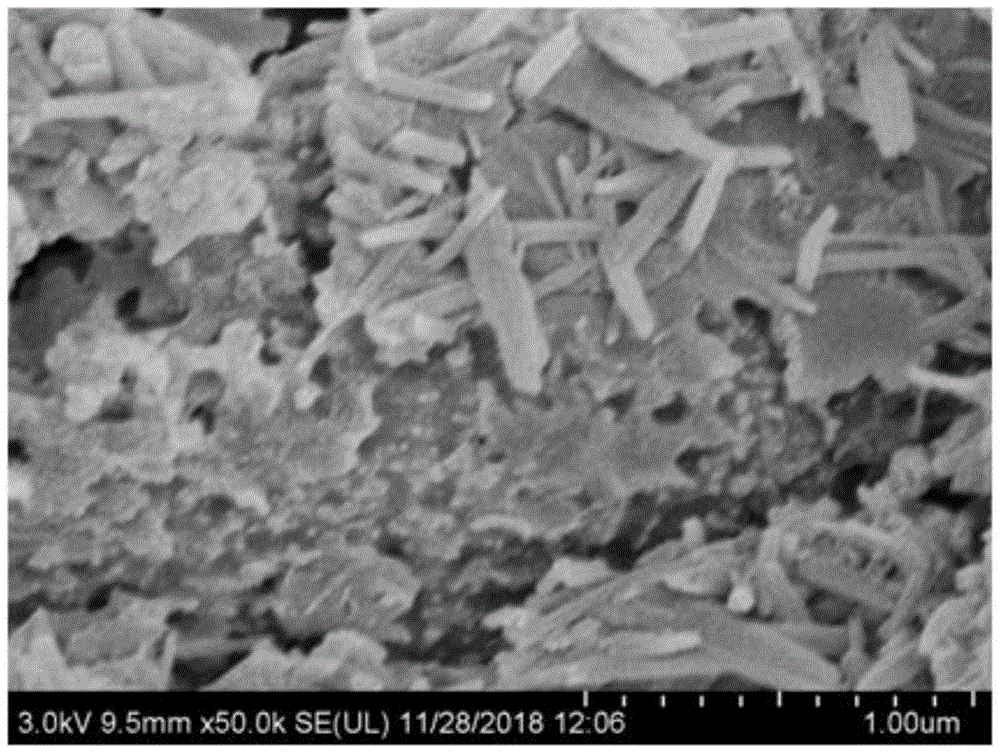
本发明属于混凝土制备
技术领域:
,特别是一种混凝土增强剂。
背景技术:
:混凝土是现代最主要的土木工程材料之一。它是一种由水泥、掺合料、颗粒状集料(粗/细骨料)、水、以及必要的外加剂,按一定比例配制、搅拌、成型、养护硬化而成的人工石材。其中水泥和掺合料的品质、混凝土的水灰比、集料的质量、养护条件(温度和湿度)、施工质量等因素都会对混凝土的强度性能产生影响,但归根结底影响最大的还是来源于胶凝材料的胶结作用。水泥是建筑材料的最大分支,每年要消耗大量的原、燃料。实践证明,以大量消耗资源,粗放经营的传统水泥工业发展模式已经难以适应时代的发展需求,行业迫切需求以资源节约、污染低、质量效率高、科技先导型的可持续发展的生态胶凝材料模式。加之现今水泥行业垄断地位,水泥价格不断飙升,缓解混凝土生产制备企业的成本压力也是迫在眉睫。据不完全统计,全国预拌混凝土生产企业每年需消耗近30亿吨胶凝材料,其中掺合料消耗量占一半左右。现代混凝土生产企业对于矿物掺合料的认知多数停留在追求经济效益而只固定掺用某一二种矿物掺合料的层次上。混凝土作为一种复杂多相体系,掺和料应用技术远远达不到客户的定向需求。另一方面,自改革开放以来,中国工业迅猛发展,导致各类工业废渣排放量剧增。目前,仍有多种工业固体废弃物未被有效利用,大量堆积在厂区附近,不仅污染、危害生态环境,还浪费资源,占用了大量土地。近年来,经国内外各方学者不懈努力,粉煤灰、矿渣等工业废渣已成功运用于水泥工业中,在某些地区已供不应求。但炉渣、钢渣、粒化电炉磷渣、磷石膏等工业废渣由于活性低、安定性不良、对水泥基材料缓凝等问题,未能在水泥工业中大量使用。因此,积极开展此类工业固体废弃物的基础应用研究,能够极大地拓展其利用领域和范畴,提高资源利用率。现有技术中,例如授权专利cn105060749b提供的“用隧道窑装备处理磷石膏制特种硬石膏胶凝材料的方法”中,采用将将按比例称重的磷石膏、石煤、废石渣经粉磨筛分、加水制粒后,在1180~1280℃下,煅烧30~50min,淬冷制得硬石膏熟渣。又例如论文《利用高掺量磷渣煅烧优质水泥特种熟料的研究》(陈丹等,硅酸盐通报,2010,(6))中公开了将按比例称重的石灰石、砂岩、磷渣、硫酸渣、粉煤灰、煤经过粉磨过筛,加水压制,先升温至950℃保温30min,再依次升温至1350℃、1400℃、1450℃保温30min,最后急速冷却破碎制成水泥特种熟料的方法。这些方法中都采用了煅烧法对原料进行熟化,制成的特种熟料提高了胶凝材料的胶凝性,混凝土的力学性能。但是,这些原料组成和方法对混凝土的替代程度有限,对粒化电炉磷渣、钢渣、固硫灰、磷石膏等工业固体废弃物的利用效率有限;混凝土的7d和28d抗压强度、抗渗性、28d收缩值、坍落度、坍落时间、凝结时间等性能的增强作用有限,不能满足客户的定向需求。技术实现要素:为了解决上述问题,本发明提供了一种混凝土增强剂,通过对磷石膏、炉渣、粒化电炉磷渣、石灰石等原料熟化,然后加入内养护持续激发剂,使制得的增强剂在保证优异的混凝土工作性能的前提下,能够替代一定量的水泥,增加混凝土强度,提升混凝土体积稳定性、抗渗性等长期性能及耐久性,同时大量使用现有的工业固体废弃物,变废为宝。具体通过以下技术实现。一种混凝土增强剂,按重量份数包含:特种熟料10份、工业固体废弃物20~30份、石膏30份、天然矿物材料30~40份,还包含内养护持续激发剂,所述内养护持续激发剂的含量占所述混凝土增强剂的总重量的5%;其中,所述特种熟料是将磷石膏、炉渣、粒化电炉磷渣、石灰石通过粉磨、混合、加水造粒、烘干、煅烧、降温、急速冷却粉碎的方法制得;所述工业固体废料是由比表面积≥400m2/kg的钢渣和比表面积≥390m2/kg的粒化电炉磷渣按重量比1:9混合而成;所述内养护持续激发剂是将固硫灰充分浸泡于丙烯酰胺溶液中,经负压吸滤后处理至饱和面干状态即得;所述天然矿物材料为明矾石粉。当需要使用时,提前1天将上述混凝土增强剂的各种原料按比例混匀即可直接使用,在混凝土中搅拌过程中与混凝土的其他原料一同掺入即可。上述增强剂所用的特种熟料,由磷石膏、炉渣、粒化电炉磷渣及少量石灰石混合、高温煅烧所得。其中,水泥特种熟料中含有较多的硫铝酸钙,水化初期迅速反应生成钙矾石,为混凝土提供优异的早期强度,补偿水泥混凝土体积収缩。上述增强剂所用的内养护持续激发剂,由浸泡丙烯酰胺的固硫灰负压吸滤并处理至饱和面干状态制得。固硫灰是循环流化床工艺燃煤过程中产生的工业废渣,是一种内部多孔的粉状物,能够有效的吸附各类有机物。丙烯酰胺是一类含有酰胺基团的有机物,在水泥基碱性环境中能够聚合反应生成聚丙烯酰胺,并进一步水解与水泥中的c3s、c2s等矿物反应生成相应的水化产物,改变水泥石结构,提升混凝土性能。通过预先将固硫灰在丙烯酰胺水溶液中浸泡,能够使丙烯酰胺分子和水分子进入固硫灰的孔洞中,在混凝土硬化过程中,丙烯酰胺分子以及水分子缓慢释放,促进胶凝材料水化,从而起到补强促进作用。上述增强剂所用的工业固体尾渣,包括粒化电炉磷渣和钢渣,粒化电炉磷渣是电炉法制备黄磷时产生的工业副产品。用电炉法制取黄磷时,形成熔融炉渣,经水淬急冷,即为粒化电炉磷渣。粒化电炉磷渣的主要成分为sio2和cao,此外还含有少量al2o3、fe2o3及可溶性p和f,其中玻璃体含量>90%,具有潜在水硬性。钢渣是炼钢过程中的一种副产品,主要矿物组成中有c3s、c3a、f-cao等物质,能够水化反应生成相应水化产物。这2类物质经各自粉磨再以一定比例掺入混凝土中后,水化初期钢渣反应生成氢氧化钙,与水泥水化反应一同作用,在液相中形成碱性环境,使得磷渣表面开始溶解并水化,生成水化硅酸钙凝胶等初期水化产物。磷渣的水化过程又能反过来加速水泥及钢渣的持续水化。因此,所述的工业固体尾渣虽初期反应较慢,但能够互相激发,最终生成更多的水化硅酸钙凝胶等水化产物,使水泥石结构更加致密,为混凝土后期强度稳定发展提供保障。上述增强剂所用的石膏作为一种易得且成本较低的硫酸盐类物质,能够调节硅酸盐水泥凝结时间,激发剂,充分激发矿粉、粉煤灰等矿物掺和料的潜在活性,更早、更多的参与胶凝材料的水化反应,提高混凝土早期强度。此外,硫酸根离子与掺和料中的活性al2o3的反应产物为钙矾石,此反应固相体积增大,使混凝土产生一定的微膨胀,补偿混凝土的体积収缩。上述增强剂所用的天然矿物材料明矾石粉,可优选产地为浙江苍南的;其主要作用是在混凝土中起到填充作用。明矾石粉主要矿物成分为较难参与水化反应的明矾石及石英,能够填充骨料及浆体之间的孔隙,增加水泥石的密实程度,进而增加混凝土强度。采用上述混凝土增强剂,能够等质量替代10%~20%水泥作为混凝土的原料,显著降低了成本;使混凝土7d抗压强度比最高可达126%,28d抗压强度比最高可达122%;降低了混凝土28d干缩率,提升了混凝土抗渗等级;促进粒化电炉磷渣、钢渣、固硫灰、磷石膏等工业固体废弃物的高效率利用,节约了资源能源,保护了环境,是一种兼顾实用性、经济型与环保型,适应现代混凝土的发展的新型绿色混凝土掺和料。优选地,上述混凝土增强剂,按重量份数包含:特种熟料10份、工业固体废弃物25份、石膏30份、天然矿物材料35份,还包含内养护持续激发剂,所述内养护持续激发剂的含量占所述混凝土增强剂的总重量的5%。更优选地,上述混凝土增强剂中,所述特种熟料的制备方法具体为:s1、将磷石膏、炉渣、粒化电炉磷渣、石灰石各自粉磨,并按重量比15:30:15:40混合,然后按照水料比0.3加水造粒备用;s2、将步骤s1所得物料烘干后升温至1350℃保温30min,然后再降温至1200℃保温30min,立即取出急速冷却至室温,粉磨至比表面积≥350m2/kg,即得成品。上述特种熟料在制备时,将物料加水造粒的目的在于使物料混合均匀密实,煅烧过程中能够充分发生固相反应。通过将物料烘干后升温至1350℃保温煅烧,再降至1200℃的方式,一方面有利于降低熟料颗粒黏度,一方面能够保证炉体在煅烧结束开炉时炉体不因温差过大而受损。上述特种熟料在制备时,步骤s2可采用硅碳棒箱式电阻炉作为煅烧设备。更优选地,上述混凝土增强剂中,所述内养护持续激发剂的具体制备方法为:所述内养护持续激发剂的具体制备方法为:取比表面积≥350m2/kg,需水量比≥115%的固硫灰,加至纯度≥95%的丙烯酰胺溶液中浸泡时间2~6h,然后负压吸滤即得。负压参数为-0.020~-0.010mpa更优选地,上述混凝土增强剂中,所述钢渣是经磁选、静置后所得,且其化学成分中feo含量≤2.0%,且f-cao含量≥3%。更优选地,上述混凝土增强剂中,所述石膏是将硬石膏和磷石膏按重量比1:1混合粉磨而成。进一步优选地,所述石膏的原料硬石膏的化学成分中:cao含量≥38.0%,so3含量≥50.0%;所述石膏中的磷石膏化学成分cao含量≥34.0%,so3含量≥48.0%,且预先经水洗,105℃烘干,500℃煅烧3h后制得。所述的磷石膏作为一种工业废渣,对硅酸盐水泥的超缓凝作用是制约其应用于水泥工业的一大阻碍。依据本发明所述的预处理方法,能够最大限度的减弱磷石膏对硅酸盐水泥的缓凝作用,其原因在于,磷石膏超缓凝作用是由于含有较多的可溶性p和f,及部分有晶体缺陷的共晶p和f,使得其在水中溶解速度过快,使得其对硅酸盐水泥的缓凝作用加剧。而经水洗、烘干和煅烧之后,大部分可溶性p和f被消除,共晶p和f得到有效释放,变成难溶体。因此,磷石膏超缓凝作用得到有效解决。更优选地,上述混凝土增强剂中,所述明矾石粉的粒径≤0.08mm,筛余≤10%。采用此规格的明矾石粉,能为水泥水化提供晶核,使得反应初期水化硅酸钙凝胶等水化产物以此为中心迅速富集,进而加速水化反应的进程。与现有技术相比,本发明的有益之处在于:1、能够等质量替代10%~15%水泥作为混凝土的原料,显著降低了成本;2、使混凝土7d抗压强度比最高可达126%,28d抗压强度比最高可达122%;降低了混凝土28d干缩率,提升了混凝土抗渗等级;3、促进粒化电炉磷渣、钢渣、固硫灰、磷石膏等工业固体废弃物的高效率利用,节约了资源能源,保护了环境,是一种兼顾实用性、经济型与环保型,适应现代混凝土的发展的新型绿色混凝土掺和料。附图说明图1为在混凝土中掺和实施例3制备的混凝土增强剂后的砂浆微观sem电镜照片,掺和量为20%。具体实施方式下面将对本发明的技术方案进行清楚、完整地描述,显然,所描述的实施例仅仅是本发明一部分实施例,而不是全部的实施例。基于本发明中的实施例,本领域普通技术人员在没有做出创造性劳动条件下所获得的所有其它实施例,都属于本发明保护的范围。以下实施例和比较例的混凝土增强剂的制备方法均为:将所有的原料按各实施例和比较例所述的重量份数称取后,混匀即可。以下实施例1~3和比较例1~2的混凝土增强剂中,所述特种熟料的制备方法为:s1、将磷石膏、炉渣、粒化电炉磷渣、石灰石各自粉磨,并以特定重量比例混合,加入一定量的水造粒备用;s2、将步骤s1所得物料烘干后升温至1350℃保温30min,然后再降温至1200℃保温30min,立即取出急速冷却,粉磨至比表面积约350m2/kg,即得成品。所述内养护持续激发剂的具体制备方法为:取比表面积约400m2/kg且不低于350m2/kg,需水量比约115%的固硫灰,加至纯度95%的丙烯酰胺溶液中浸泡时间4h,然后在-0.020~-0.010mpa的负压下吸滤即得。所述工业固体废料是由比表面积约400m2/kg的钢渣和比表面积约390m2/kg粒化电炉磷渣按重量比1:9混合而成;所述钢渣是经磁选、静置后所得,且其化学成分中feo含量为2.0%,且f-cao含量为3%。所述石膏是将硬石膏和磷石膏按重量比1:1混合粉磨而成,所述硬石膏的化学成分中:cao含量为38.0%,so3含量为50.0%;所述石膏中的磷石膏化学成分cao含量为34.0%,so3含量为48.0%,且预先经水洗,105℃烘干,500℃煅烧3h后制得。所述天然矿物材料为明矾石粉,产地为浙江苍南,且粒径约0.08mm,筛余10%。实施例1~3和比较例1~2实施例1~3和比较例1~2所制备的混凝土增强剂,包含特种熟料、工业固体废弃物、石膏、天然矿物材料,其重量份数如下表1所示;此外,均还包含占所述混凝土增强剂的总重量的5%的内养护持续激发剂。表1实施例1~3和比较例1~2的原料的重量份数,单位:份比较例3本比较例提供的混凝土增强剂,其原料及重量份数与制备方法与实施例3基本相同,不同之处在于:所述内养护持续激发剂的具体制备方法为:取比表面积约300m2/kg且不大于350m2/kg,需水量比约115%的固硫灰,加至纯度95%的丙烯酰胺溶液中浸泡4h,烘干即得。比较例4本比较例提供的混凝土增强剂,其原料及重量份数与制备方法与实施例3基本相同,不同之处在于:所述内养护持续激发剂的具体制备方法为:取比表面积约400m2/kg且不低于350m2/kg,需水量比约115%的固硫灰,以及纯度≥95%的丙烯酰胺颗粒,直接混匀即得。比较例5本比较例提供的混凝土增强剂,其原料中所用的内养护持续激发剂为比表面积约400m2/kg且不低于350m2/kg,需水量比约115%的固硫灰(即未经丙烯酰胺溶液浸泡),其他原料与重量份数以及制备方法与实施例3基本相同。比较例6本比较例提供的混凝土增强剂,其原料中不含内养护持续激发剂,其他原料及重量份数与实施例3基本相同。比较例7本比较例提供的混凝土增强剂,其他原料及重量份数与实施例3基本相同,不同之处在于:所述特种熟料的制备方法具体为:s1、将磷石膏、炉渣、粒化电炉磷渣、石灰石各自粉磨,并以特定重量比例混合,加入一定量的水造粒备用;s2、将步骤s1所得物料烘干后升温至1350℃保温煅烧30min,立即取出急速冷却,粉磨至比表面积>350m2/kg即得成品。应用例:对实施例1~3和比较例1~7的混凝土增强剂的性能检测(1)试验方法本试验设试验空白对照组为普通c35等级混凝土,实施例1~3和比较例1~7的混凝土增强剂用于取代水泥,且掺量设定为胶凝材料总质量的10%和15%,其他材料用量保持不变,分别进行混凝土的工作性(坍落度、粘度采用倒塌落时间表示)、凝结时间差、力学性能(7d、28d抗压强度)、28d收缩值、抗渗性能试验测试。本试验所用到的水泥为po42.5普通硅酸盐水泥,粉煤灰为ⅱ级粉煤灰,矿粉为s95级矿粉,其中所用混凝土原材料的化学组份如表2所示。表2混凝土原材料成份分析本试验所用混凝土强度等级为c35,减水剂为聚羧酸减水剂,塌落度控制为200±10mm。其中混凝土详细配合比如表3所示。表3试验所用混凝土的原料及配合比试验类别水泥粉煤灰矿粉砂石减水剂水增强剂空白对照200808080010603.91700试验组(15%掺量)170808080010603.917030试验组(20%掺量)160808080010603.917040(2)试验结果对实施例1~3和比较例1~7的混凝土的性能检测,检测结果如下表4、表5。表4中混凝土增强剂的掺和量为10%,表5中混凝土增强剂的掺和量为15%。表4实施例1~3和比较例1~7制备的混凝土的性能检测结果(增强剂掺和量10%)表5实施例1~3和比较例1~7制备的混凝土的性能检测结果(增强剂掺和量15%)当使用混凝土增强剂掺和量为10%和15%时,通过对比实施例1~3,比较例1、2和空白对照可知,采用实施例1~3制备的混凝土增强剂,其取代相应水泥用量后,对混凝土的坍落度影响不大,混凝土的粘度(倒坍落时间)得以一定改善;制备的增强剂,在保持原有混凝土配合比设计不变的前提下,对混凝土的塌落度基本没影响,混凝土粘度(倒坍落时间表示)得以改善。通过对比实施例3和比较例3~6可知,在增强剂中是否加入内养护持续激发剂,内养护持续激发剂是采用丙烯酰胺溶液浸泡的固硫灰,还是将丙烯酰胺和固硫灰简单混合,又或是只包括普通固硫灰,对增强剂的有益效果具有显著影响,尤其是对制备的混凝土的坍落度、抗压强度和抗渗性。采用丙烯酰胺溶液浸泡的方式,相比于其他3种方式,相应制备的增强剂在替代相应量的水泥后制备的混凝土,力学性能明显更好,抗渗性能更佳,说明采用丙烯酰胺溶液浸泡的方式的效果最好,简单的原料混合,虽然有一定效果,但远没有本专利的技术优秀。通过对比实施例3和比较例7可知,改变特种熟料的煅烧方法,对用增强剂替代相应量的水泥后制备混凝土,其力学性能也有一定影响。采用直接升温煅烧和急速冷却的方式,替代相应量的水泥后制备的混凝土,力学性能有些许增强,但效果不明显。由此可见,采用丙烯酰胺对固硫灰的预处理方式,对于制备的增强剂替代水泥,掺和到混凝土中,其对坍落性、混凝土粘度以及力学性能都有明显影响。从附图1中可以看出,在水泥水化产物界面,催生了很多的棒状钙矾石产物生成,填充水泥石孔隙,提高水泥石密实性,从而提高了混凝土的强度。当前第1页12