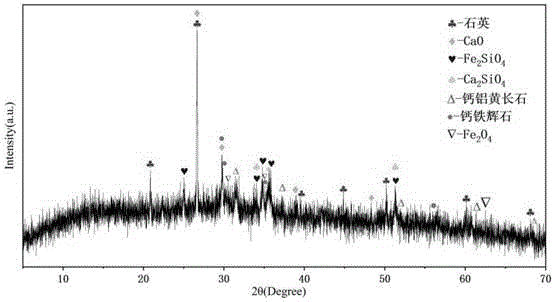
本发明涉及水泥建材领域,特别设计一种利用铜矿尾渣制备的水泥。
背景技术:
:铜渣是高温冶炼铜矿时产生的废渣,铜渣排放量大,占地多,能够造成很大的环境污染,已成为困扰企业的一大难题。目前,我国对铜尾矿的综合利用主要包括有用元素回收和铜尾矿回填采空区等方式,但是,铜尾矿的综合利用的利用率比较低。这是因为,由于铜尾矿中有价元素含量低,难于分离,回收试验时要经过特殊的工艺流程,有的甚至采用多次精选才能使最后得到的精矿达到品味要求,且回收有价元素后仍有大量二次尾渣产生,需进一步销纳处理。而采空区回填必须在不再生产以后才能进行回填,前期产生的铜尾矿仍需要修建尾矿库进行临时堆存,不仅占用土地,而且污染环境。如何加强对铜渣的综合利用,变废为宝,实现可持续性发展和固废资源化利用,减少铜渣对环境的影响,是目前亟待解决的问题。技术实现要素:为了解决上述问题,本发明人进行了锐意研究,利用铜渣复合材料作为活性混合材料,制备出一种水泥,该水泥的强度能够达到32.5标号水泥的强度标准。而且铜渣复合材料中绝大多数重金属在水中的浸出量均未超出国家标准,用铜渣复合材料制备的水泥不会对环境造成重金属污染,是一种环保水泥,从而完成了本发明。本发明一方面提供了一种铜渣复合材料,所述铜渣复合材料主要包括二氧化硅、氧化铁和氧化钙,其中,相对于铜渣复合材料总重量,二氧化硅中硅元素的含量为15-28wt%,氧化铁中铁元素的含量为12-20wt%,氧化钙中钙元素的含量为10-15wt%。本发明第二方面提供了一种水泥,所述水泥采用本发明第一方面所述的铜渣复合材料进行制备,所述水泥由包括如下重量份的原料制成:水泥熟料55-95份石膏5-20份铜渣复合材料6-50份。本发明第三方面提供了本发明第二方面所述的水泥的制备方法,所述方法包括以下步骤:步骤1,将铜渣复合材料进行研磨,得到铜渣粉体;步骤2,将水泥熟料和石膏进行研磨,得到混合粉体;步骤3,将铜渣粉体和混合粉体进行混合,得到水泥。附图说明图1示出铜渣复合材料的粒径分布图;图2示出铜渣复合材料的氮吸附等温线图;图3示出铜渣复合材料在显微镜下的物相形貌;图4示出铜渣复合材料在电子显微镜下的物相形貌;图5示出铜渣复合材料图3中e处的扫描电镜图;图6示出铜渣复合材料图3中e处的x射线能量色散谱图;图7示出铜渣复合材料图3中c处的扫描电镜图;图8示出铜渣复合材料图3中c处的x射线能量色散谱图;图9示出铜渣复合材料图3中d处的扫描电镜图;图10示出铜渣复合材料图3中d处的x射线能量色散谱图;图11示出铜渣复合材料图3中b处的扫描电镜图;图12示出铜渣复合材料图3中b处的x射线能量色散谱图;图13示出不同球磨时间处理后的铜渣粒度分布;图14示出铜渣复合材料的xrd图。具体实施方式下面通过附图和实施例对本发明进一步详细说明。通过这些说明,本发明的特点和优点将变得更为清楚明确。根据本发明一种优选的实施方式,所述铜渣复合材料的粒径为1-120μm,进一步优选为5-70μm,更优选为10-50μm。根据本发明一种优选的实施方式,所述铜渣复合材料的比表面积为5.710-8.560m2/g,进一步优选为6.905-7.287m2/g,更优选为7.143m2/g。根据本发明一种优选的实施方式,所述铜渣复合材料主要包括二氧化硅、氧化铁和氧化钙,其中,相对于铜渣复合材料总重量,二氧化硅中硅元素的含量为15-28wt%,优选为15-21wt%,氧化铁中铁元素的含量为12-20wt%,优选为12-17.3wt%,氧化钙中钙元素的含量为10-15wt%,优选为10-13.6wt%。在进一步优选的实施方式中,所述硅元素的含量为18-20.8wt%,铁元素的含量14-17.0wt%,钙元素的含量为10-13.2wt%。在更进一步优选的实施方式中,所述硅的元素含量为20.31wt%,铁元素的含量为16.39wt%,钙元素的含量为12.69wt%。其中,硅酸盐水泥的主要成分是硅酸三钙,硅酸二钙,铝酸三钙和铁铝酸四钙,其主要成分是氧化钙,二氧化硅,氧化铝和氧化铁。本发明中铜渣复合材料内含有大量的二氧化硅、氧化铁和氧化钙,可用做生产水泥的活性混合材料,用来生产水泥。其中,水泥的活性混合材料指的是常温下能与石灰、石膏或硅酸盐水泥熟料一起,加水拌合后能发生水化反应,生成水硬性的水化产物的混合材料。根据本发明一种优选的实施方式,所述铜渣复合材料还含有少量的氧化铝,氧化镁和二氧化钛,其中,相对于铜渣复合材料总重量,氧化铝中铝元素的含量为3.0-4.1wt%,优选为3.0-3.65wt%;氧化镁中镁元素的含量为1.5-2.4wt%,优选为1.5-2.15wt%;氧化钛中钛元素的含量为0.11-0.20wt%,优选为0.11-0.165wt%。在进一步优选的实施方式中,所述铝元素的含量为3.2-3.6wt%,镁元素的含量为1.7-2.1wt%,钛元素的含量为0.13-0.16wt%。在更进一步优选的实施方式中,所述铝元素的含量为3.57wt%,镁元素的含量为1.94wt%,钛元素的含量为0.15wt%。在铜渣复合材料中,铝元素的主要存在形式是氧化铝,镁元素的主要存在形式是氧化镁,钛元素的主要存在形式是二氧化钛。用铜渣复合材料生产水泥时,铜渣复合材料中含有的少量的二氧化钛对水泥的硬化过程能够起到强化作用,但是氧化镁会影响水泥的安定性,在生产水泥时,需要对其含量进行严格的控制。根据本发明一种优选的实施方式,所述铜渣复合材料还含有铜、铬、锰、铅和锌等重金属元素。发明人按国家标准《固体废物浸出毒性浸出方法》(gb5086.1~2-1997)规定的方法,将铜渣复合材料进行了水中毒性浸出试验,结果如表1:表1铜渣复合材料在水中的浸出毒性试验数据由表1可知,铜渣复合材料中绝大多数的重金属在水中的浸出量远远低于国家标准,不到国家标准的千分之一。虽然国家标准中没有给出锰元素的标准数值,但是,本发明中锰的浸出量只有31.9μg/l,属于微克级别,几乎不会对环境产生影响。用铜渣复合材料制备的水泥,不会对环境造成重金属污染,对环境十分友好。根据本发明一种优选的实施方式,所述铜渣复合材料物相由玻璃相和结晶相组成,所述结晶相包括石英、氧化钙、硅酸铁、硅酸二钙、钙铝黄长石、钙铁辉石及四氧化三铁等物质;所述玻璃相包括铁和钙的硫化物以及含钙铝铁的硅酸盐。本发明第二个方面提供了一种水泥,所述水泥利用本发明第一方面所述的铜渣复合材料进行制备。根据本发明一种优选的实施方式,所述水泥由包括如下重量份的原料制成:水泥熟料55-95份石膏5-20份铜渣复合材料6-50份。其中,水泥熟料指的是硅酸盐水泥熟料,硅酸盐水泥熟料即为国际上的波特兰水泥熟料,是一种由主要含有氧化钙、二氧化硅、氧化铝和三氧化二铁的原料按照适当配比磨成细粉烧至部分熔融,所得的一硅酸钙为主要矿物成分的水硬性凝胶物质。按照硅酸盐水泥熟料的主要特性与用途,可以分为通用水泥熟料、低碱水泥熟料、中抗硫酸盐水泥熟料、高抗硫酸盐水泥熟料、中热水泥熟料和低热水泥熟料等类型。在本分发明中,对于水泥熟料没有特别限定,不过优选通用水泥熟料。在进一步优选的实施方式中,所述水泥由包括如下重量份的原料制成:水泥熟料80-89份石膏5-15份铜渣复合材料10-30份。在更进一步优选的实施方式中,所述水泥由包括如下重量份的原料制成:水泥熟料80份石膏5份铜渣复合材料15份。根据本发明一种优选的实施方式,所述水泥原料中的铜渣复合材料是铜陵有色股份铜山矿业有限公司对安徽铜陵铜山的铜矿经过选铜选铁处理后剩余的矿渣,主要包括二氧化硅,二氧化硅中硅元素的含量相对于铜渣复合材料总重量为15-28wt%,优选为15-21wt%。在进一步优选的实施方式中,二氧化硅中硅元素的含量相对于铜渣复合材料总重量为18-20.8wt%。在更进一步优选的实施方式中,二氧化硅中硅元素的含量相对于铜渣复合材料总重量为20.31wt%。根据本发明一种优选的实施方式,所述水泥原料中的铜渣复合材料还主要包括氧化铁,氧化铁中铁元素的含量相对于铜渣复合材料总重量为12-20wt%,优选为12-17.3wt%。在进一步优选的实施方式中,氧化铁中铁元素的含量相对于铜渣复合材料总重量为14-17.0wt%。在更进一步优选的实施方式中,氧化铁中铁元素的含量相对于铜渣复合材料总重量为16.39wt%。根据本发明一种优选的实施方式,所述水泥原料中的铜渣复合材料还主要包括氧化钙,氧化钙中钙元素的含量相对于铜渣复合材料总重量为10-15wt%,优选为10-13.6wt%。在进一步优选的实施方式中,氧化钙中钙元素的含量相对于铜渣复合材料总重量为10-13.2wt%。在更进一步优选的实施方式中,氧化钙中钙元素的含量相对于铜渣复合材料总重量为12.69wt%。根据本发明一种优选的实施方式,所述水泥原料中的铜渣复合材料还包括少量的氧化铝,氧化铝中铝元素的含量相对于铜渣复合材料总重量为3.0-4.1wt%,优选为3.0-3.65wt%,进一步优选为3.2-3.6wt%,更优选为3.57wt%。根据本发明一种优选的实施方式,所述水泥原料中的铜渣复合材料还包括少量的氧化镁,氧化镁中镁元素的含量相对于铜渣复合材料总重量为1.5-2.4wt%,优选为1.5-2.15wt%,进一步优选为1.7-2.1wt%,更优选为1.94wt%。根据本发明一种优选的实施方式,所述水泥原料中的铜渣复合材料还包括少量的二氧化钛,二氧化钛中钛元素的含量相对于铜渣复合材料总重量为0.11-0.20wt%,优选为0.11-0.165wt%,进一步优选为0.13-0.16wt%,更优选为0.15wt%。根据本发明一种优选的实施方式,所述铜渣复合材料的粒径为1-120μm,进一步优选为5-70μm,更优选为10-50μm。根据本发明一种优选的实施方式,所述铜渣复合材料的比表面积为5.710-8.560m2/g,进一步优选为6.905-7.287m2/g,更优选为7.143m2/g。本发明第三个方面提供了一种水泥的制备方法,所述方法包括以下步骤:步骤1,将铜渣复合材料进行研磨,得到铜渣粉体;铜渣复合材料内虽然含有水泥活性体,具有胶凝活性,但是活性较低,采用研磨可以对铜渣复合材料的活性进行激发。通过研磨能够增加铜渣复合材料的细度,提高其比表面积,破坏铜渣复合材料重的玻璃体,将包裹在里面的硅酸盐和铝酸盐等活性矿物暴露出来,能够增加与水的接触面积,加快水泥的凝结。根据本发明一种优选的实施方式,所述研磨为球磨。其中,球磨在球磨机内进行,一方面球磨机的粉碎比大,易于调整产品的出料细度。另一方面球磨机的生产能力大,能够长时间连续运转,可满足较大规模生产的需要。根据本发明一种优选的实施方式,所述研磨中,球料比为4-8:1,进一步优选为5-7:1,更优选为6:1。其中,球料比过小,球磨机的粉磨效率低,球料比过大,会增加球磨机筒体的负荷,容易损坏设备。发明人经过大量的实验发现,当球料比为6:1时,球磨效果最好。根据本发明一种优选的实施方式,所述研磨的转速为10-60rpm,进一步优选为20-40rpm,更优选为25rpm。根据本发明一种优选的实施方式,所述研磨时间为30min-6h。本发明中,球磨时间对铜渣复合材料的粒径具有较大影响,见图13和表2,表2球磨不同时间后铜渣粉体粒径参数未经处理的铜渣复合材料的粒径主要分布在1-120μm之间,粒径呈正态分布,对其进行筛分,可以得到d10,d50,d90粉体。其中,d10、d50、d90的粒径参数,代表的含义分别是铜渣复合材料的累计粒径分布数达到10%、50%和90%时所对应的粒径。它们的物理意义分别是粒径小于(或大于)它的颗粒占铜渣复合材料的10%、50%和90%。从图13和表2中可以看出,d50铜渣复合材料的粒径随着研磨时间的延长而降低,而且粒径降低趋势逐渐减小。d10铜渣复合材料和d90铜渣复合材料的粒径随着研磨时间的延长先降低后增加,粉体粒径增加的原因是因为粉体的团聚。因此,需要严格控制球磨时间。在进一步优选的实施方式中,所述研磨时间为1-4h。在更进一步优选的实施方式中,所述研磨时间为2h。根据本发明一种优选的实施方式,在研磨之前,对铜渣复合材料进行筛分,经过筛分后的铜渣复合材料的粒径为10-50μm,优选为15-45μm,更优选为20-30μm。由表2可知,铜渣复合材料的粒径主要集中分布在20μm左右,经过筛分后的铜渣复合材料的粒度更加均匀,有助于控制球磨条件。步骤2,将水泥熟料和石膏进行研磨,得到混合粉体;现有技术中,在水泥的生产过程中,往往将水泥熟料、石膏和活性混合材料一起进行研磨,但是,不同原料的易磨性指数并不相同,同时研磨会导致水泥熟料、石膏和活性混合材料的粒径存在差异,进而影响到水泥的强度。本发明中,熟料的易磨性指数要比铜渣复合材料的易磨性指数小很多,将二者分别进行研磨,能够使得原料的研磨更充分,得到的粉体更均匀。根据本发明一种优选的实施方式,步骤2中,所述研磨与步骤1中的研磨相同。根据本发明一种优选的实施方式,步骤2中,水泥熟料的重量份为55-95份,石膏的重量份为5-20份。在进一步优选的实施方式中,步骤2中,水泥熟料的重量份为80-89份,石膏的重量份为5-15份。在更进一步优选的实施方式中,步骤2中,水泥熟料的重量份为80份,石膏的重量份为5份。步骤3,将铜渣粉体和混合粉体进行混合,得到水泥;根据本发明一种优选的实施方式,步骤3中,铜渣粉体的重量份为6-50份。在进一步优选的实施方式中,步骤3中,铜渣粉体的重量份为10-30份。在进一步优选的实施方式中,步骤3中,铜渣粉体的重量份为15份。本发明中,通过控制铜渣复合材料的重量份来调整水泥中的二氧化硅,氧化钙和氧化铁的含量,使得所制备的水泥能够达到国家标准。基于100重量份的原料,当石膏重量份为5份,铜渣复合材料作为活性混合材料重量份在15份以内时,制备的水泥可以达到42.5标号水泥的强度等级;基于100重量份的原料,当石膏重量份为5份,铜渣复合材料作为活性混合材料重量份为30份时,制备的水泥可以达到32.5标号水泥的强度等级。本发明所具有的有益效果包括:1)本发明制备的水泥成本低、抗折强度和抗压强度高;2)本发明制备的水泥,充分利用工业废料,变废为宝,提高了铜渣的经济价值;3)本发明的经济效益显著,社会环保效益突出。实施例实施例和实验例中所采用的铜渣复合材料为铜陵有色股份铜山矿业有限公司对安徽铜陵铜山的铜矿经过选铜选铁处理后剩余的矿渣。实施例1:称取27g铜渣复合材料放入球磨机中,在25rpm转速下研磨2h,得到铜渣粉体;称取22.5g石膏和400.5g水泥熟料放入球磨机中,在25rpm转速下研磨2h,得到混合粉体;将铜渣粉体和混合粉体进行混合,搅拌均匀,得到水泥;将制备的水泥与1350g标准砂和225g水进行混合,制备水泥胶砂,并测试其抗折强度和抗压强度,测试结果见表3。实施例2:重复实施例1,其区别在于铜渣复合材料的质量为40.5g,水泥熟料的质量为387g。实施例3:重复实施例1,其区别在于铜渣复合材料的质量为54g,水泥熟料的质量为373.5g。实施例4:重复实施例1,其区别在于铜渣复合材料的质量为67.5g,水泥熟料的质量为360g。实施例5:重复实施例1,其区别在于铜渣复合材料的质量为90g,水泥熟料的质量为337.5g。实施例6重复实施例1,其区别在于铜渣复合材料的质量为135g,水泥熟料的质量为292.5g。实施例7重复实施例1,其区别在于铜渣复合材料的质量为180g,水泥熟料的质量为247.5g。对比例对比例1重复实施例1的制备过程,区别在于:不添加铜渣复合材料,水泥熟料的质量为427.5g。其中,实施例1-7以及对比例1中水泥胶砂的强度测试结果如表3所示:表3铜渣复合材料不同添加量对水泥胶砂强度的影响其中,表3中,铜渣材料重量百分含量指的是铜渣材料的重量占铜渣材料、水泥熟料和石膏的总重量的百分比。42.5标号水泥3天抗折强度大于等于3.5mpa,28天抗折强度大于等于6.5mpa,3天抗压强度大于等于17.0mpa,28天抗压强度大于等于42.5mpa。32.5标号水泥3天抗折强度大于等于2.5mpa,28天抗折强度大于等于5.5mpa,3天抗压强度大于等于10.0mpa,28天抗压强度大于等于32.5mpa。由表3可知,当石膏重量百分比为5%时,随着铜渣复合材料重量百分比的增加,制备的水泥胶砂的抗折强度和抗压强度呈现先增加后减小的趋势。当铜渣复合材料重量百分比在15%以内时,制备的水泥可以达到42.5标号水泥的强度等级;当石膏重量百分比为5%,铜渣复合材料重量百分比为30%时,制备的水泥可以达到32.5标号水泥的强度等级。当铜渣复合材料重量百分比超过15%时,水泥胶砂的早期强度衰减,可能是因为铜渣复合材料的加入影响了硅酸三钙和硅酸二钙的水化反应。实验例实验例1采用英国马尔文公司生产的激光粒度分析仪对铜渣复合材料进行粒径分析,结果如图1所示:由图1可知,铜渣复合材料的粒径呈正态分布,说明铜渣复合材料的粒径分布均匀,其粒径主要分布范围为1-120μm。铜渣复合材料的平均粒径d50为21μm。实验例2采用美国康塔公司生产的比表面积仪对铜渣复合材料进行五点氮吸附等温线的测定,结果如图2所示:依据吸附等温线计算得到铜渣的比表面积为7.143m2/g。从颗粒粒径按等径球体模型计算的面积远小于该值,表明铜渣粉体中含有多孔性结构。实验例3对铜渣复合材料进行x射线荧光法分析,结果如表4所示:表4.铜渣中化学元素含量表元素含量/%al3.57ca12.69cr0.0054cu0.015fe16.39k0.53mg1.94mn0.311na0.31pb0.0068s0.555si20.31ti0.150zn0.23p0.024由表4可知,铜渣复合材料的主要化学成分为cao、sio2、fe2o3,mgo、al2o3、tio2含量较少。除此以外,还含有金属硫化物及其它金属氧化物以及铅、锰、铜、铬等重金属元素。实验例4按《固体废物浸出毒性浸出方法》(gb5086.1~2-1997)规定的方法,将铜渣复合材料进行水中毒性浸出试验,结果如表1所示:表1铜渣复合材料在水中的浸出毒性试验数据由表1可知,铜渣复合材料中的绝大多数的重金属毒性浸出量远远低于国家标准,不到国家标准的千分之一。虽然国家标准中没有给出锰元素的标准数值,但是,本发明中锰的浸出量只有31.9μg/l,属于微克级别,几乎不会对环境产生影响。用铜渣复合材料制备的水泥,不会对环境造成重金属污染,对环境十分友好。实验例5将铜渣复合材料按照中华人民共和国地质矿产行业标准dz/t0275.3-2015(矿石光片制样)制成的光片分别在光学显微镜和电子显微镜下进行形貌及亮度(灰度)的观察,结果如图3和图4所示:由图3和图4可知,图中高亮白色、边界弯曲、无一定形状的为单质铁,标记为a;图中浅灰色为铁的氧化物,铁的氧化物多以串珠状、粒状、似圆形形态存在,标记为b;图中大量分布的深灰色条状物为钙铁硅酸盐类,标记为c;图中连续分布的黑色玻璃态物质为钙铝铁的硅酸盐类,标记为d;除此以外,铜渣中还有一种亮度与铁的氧化物很相近、但亮度不均匀的物质,多以粒状或圆形颗粒单独存在,此应为金属硫化物或铁与其它金属的固溶体物,标记为e。实验例6对实验例5中标注的b、c、d和e处进行x射线能量散失谱分析,结果如图5-12所示:图5和图6对应图3和图4中的e物质,其能谱中硫、铁含量较高,两者摩尔比为0.78,故此处铁部分可能以单质形式存在,部分以硫化物形式存在。图7和图8对应图3和图4中的c物质,其能谱中硅钙铁含量较高,为钙铁硅酸盐;图9和图10对应图3和图4中的d物质,其能谱中除铝硅钙铁含量较高外,还含有一定量的钾、钠,故可能为钙铝铁的硅酸盐玻璃;图11和图12对应图3和图4中的b物质,其能谱中只有铁,几乎无其它金属元素,推测可能为氧化亚铁。结合光学显微镜物相分析和x射线色散谱元素分析,可进一步确定铜渣复合材料中的物相组成及物相分布。其中,铜渣复合材料中含有的钙铝铁的硅酸盐类能增加水泥中铁铝酸四钙的含量,有利于提高水泥早期强度、粘结力、耐动压、耐磨和增大应变能力。铜渣复合材料中含有的钙铁硅酸盐能够提高水泥中铁的含量,增强水泥的抗压强度。实验例7对铜渣复合材料进行x射线衍射分析,结果如图14所示:由图14可以看出,铜渣物相由玻璃相和结晶相组成,结晶相有石英、氧化钙、硅酸铁、硅酸二钙、钙铝黄长石、钙铁辉石及四氧化三铁等物质。结晶相中硅酸盐类矿物均具有一定的水化活性,可为制备的水泥提供一定的强度,尤其是硅酸二钙可为水泥提供后期强度;玻璃相物质经球磨活化后可为水泥提供水硬活性。以上结合了优选的实施方式对本发明进行了说明,不过这些实施方式仅是范例性的,仅起到说明性的作用。在此基础上,可以对本发明进行多种替换和改进,这些均落入本发明的保护范围内。当前第1页12