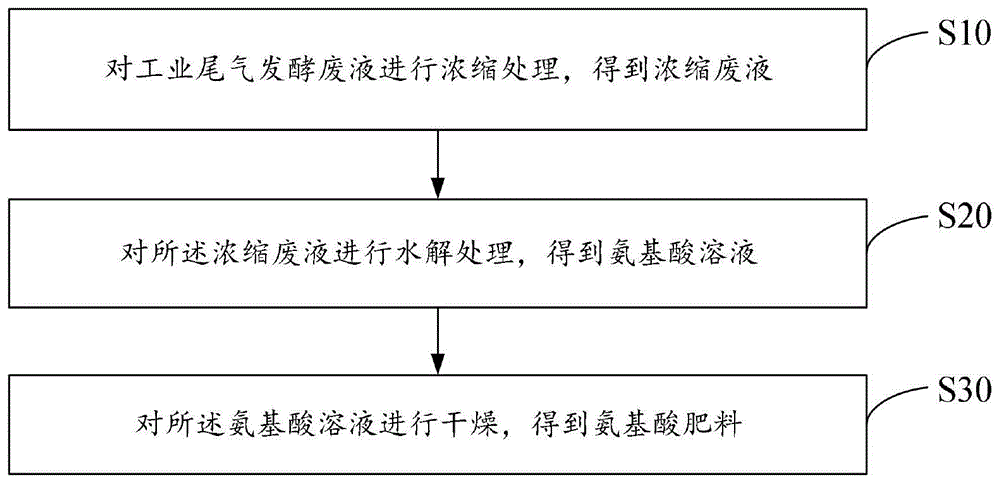
本发明涉及一种使用工业尾气发酵废液制备氨基酸肥料的方法及系统,属于氨基酸肥料制备
技术领域:
。
背景技术:
:我们已经发明了一种以含一氧化碳的工业尾气为原料通过发酵法生产乙醇的技术(申请号cn201710352273.6,一种工业尾气发酵法制乙醇的方法及系统),该技术公开了以工业尾气为原料发酵生产乙醇,相对于传统的粮食发酵生产乙醇的工艺具有“不与人争粮,不与粮争地”的优势,且成本远低于粮食发酵,同时可有效减少钢铁冶金、炼化产生的企业碳排放。然而,在利用工业尾气发酵生产乙醇的过程中,通过蒸馏提取乙醇后的醪液中固含物仅为菌体蛋白,应用价值较高,如直接排放,一方面会造成资源浪费,另一方面会造成污水处理负荷过大。因此需要开发一种新的利用途径,在实现高价值利用的同时,降低污水处理负荷。技术实现要素:针对上述现有技术的不足,本发明提供了一种使用工业尾气发酵废液制备氨基酸肥料的方法及系统,以解决现有技术中资源利用率低和污水处理负荷过大的技术问题。为实现上述目的,本发明实施例提供一种使用工业尾气发酵废液制备氨基酸肥料的方法,所述方法包括以下步骤:对工业尾气发酵废液进行浓缩处理,得到浓缩废液;对所述浓缩废液进行水解处理,得到氨基酸溶液;对所述氨基酸溶液进行干燥,得到氨基酸肥料。优选地,所述对工业尾气发酵废液进行浓缩处理,得到浓缩废液之前,所述方法还包括:通过工业尾气发酵制乙醇法对工业尾气进行发酵,得到工业尾气发酵废液。优选地,所述工业尾气发酵废液中含有菌体蛋白。优选地,所述对工业尾气发酵废液进行浓缩处理,得到浓缩废液,具体包括:对工业尾气发酵废液进行单效蒸发或多效蒸发,得到浓缩废液。优选地,所述对所述浓缩废液进行水解处理,得到氨基酸溶液,具体包括:通过酸解法、酶解法和酸酶联合水解法中的任一种对所述浓缩废液进行水解处理,得到氨基酸溶液。优选地,所述对所述氨基酸溶液进行干燥,得到氨基酸肥料,具体包括:对所述氨基酸溶液进行离心喷雾干燥或者压力喷雾干燥,得到氨基酸肥料。此外,为实现上述目的,本发明实施例还提供一种使用工业尾气发酵废液制备氨基酸肥料的系统,其特征在于,所述系统包括:蒸发浓缩装置,用于对工业尾气发酵废液进行浓缩处理,得到浓缩废液;水解装置,用于对所述浓缩废液进行水解处理,得到氨基酸溶液;喷雾干燥装置,用于对所述氨基酸溶液进行干燥,得到氨基酸肥料。优选地,所述系统还包括:第一进料泵,用于将所述工业尾气发酵废液送入至所述蒸发浓缩装置中;第二进料泵,用于将所述浓缩废液送入至所述水解装置中;第三进料泵,用于将所述氨基酸溶液送入至所述喷雾干燥装置中。优选地,所述水解装置为一个以上水解反应器。优选地,所述系统还包括:发酵装置,用于通过工业尾气发酵制乙醇法对工业尾气进行发酵,得到工业尾气发酵废液。相比于现有技术,本发明具有以下优点:本发明对工业尾气发酵废液进行浓缩处理,得到浓缩废液;对所述浓缩废液进行水解处理,得到氨基酸溶液;并对所述氨基酸溶液进行干燥,得到氨基酸肥料。能够将工业尾气发酵废液转化为氨基酸肥料,保留了工业尾气发酵废液中的氮、磷和钾等微量元素,从而提高了工业尾气发酵废液的资源利用率,并且降低了污水处理负荷。附图说明为了更清楚地说明本发明实施例中的技术方案,下面将对实施例描述中所需要使用的附图作简单地介绍,显而易见地,下面描述中的附图仅仅是本发明的一些实施例,对于本领域普通技术人员来讲,在不付出创造性劳动的前提下,还可以根据这些附图获得其他的附图。图1为本发明所述使用工业尾气发酵废液制备氨基酸肥料的方法的流程示意图;图2为本发明所述使用工业尾气发酵废液制备氨基酸肥料的系统的结构示意图。附图标号说明:标号名称标号名称1第一进料泵4水解装置2蒸发浓缩装置5第三进料泵3第二进料泵6喷雾干燥装置具体实施方式下文将结合具体实施方式和实施例,具体阐述本发明,本发明的优点和各种效果将由此更加清楚地呈现。本领域技术人员应理解,这些具体实施方式和实施例是用于说明本发明,而非限制本发明。在整个说明书中,除非另有特别说明,本文使用的术语应理解为如本领域中通常所使用的含义。因此,除非另有定义,本文使用的所有技术和科学术语具有与本发明所属领域技术人员的一般理解相同的含义。若存在矛盾,本说明书优先。除非另有特别说明,本发明中用到的各种原材料、试剂、仪器和设备等,均可通过市场购买得到或者可通过现有方法制备得到。参照图1,本发明实施例提供一种使用工业尾气发酵废液制备氨基酸肥料的方法,具体包括以下步骤:步骤s10:对工业尾气发酵废液进行浓缩处理,得到浓缩废液;所述工业尾气发酵废液中含有较低浓度的菌体蛋白,将菌体蛋白从所述工业尾气发酵废液中提取出来的难度较大,为了降低提取难度、提高提取效率,将预先对所述工业尾气发酵废液进行蒸发浓缩,得到浓缩废液。进一步地,浓缩处理所产生的蒸汽冷凝水直接回用于生产。进一步地,对工业尾气发酵废液进行单效蒸发或多效蒸发,得到浓缩废液。单效蒸发的操作费用高于多效蒸发,而单效蒸发的设备费用低于多效蒸发,在具体实现中,可根据实际生产强度和设备量对所述工业尾气发酵废液进行单效蒸发或者多效蒸发,例如,在蒸发设备数量较少时对所述工业尾气发酵废液进行单效蒸发,在蒸发设备数量较多时对所述工业尾气发酵废液进行多效蒸发,以得到浓缩废液。进一步地,通过工业尾气发酵制乙醇法对工业尾气进行发酵,得到工业尾气发酵废液。所述工业尾气发酵制乙醇法的具体实施过程为:将工业尾气进行预处理,所述预处理包括:脱除工业尾气中的有毒物质,得到净化的尾气;将所述净化的尾气用于发酵,得到发酵成熟醪以及余气;将所述发酵成熟醪蒸馏,得到乙醇以及含菌余馏水;将所述含菌余馏水分离浓缩,得到浓液及清液;将所述清液净化处理;将所述余气进行尾气处理,去除残留的一氧化碳。其中,所述浓液即为所述工业尾气发酵废液。步骤s20:对所述浓缩废液进行水解处理,得到氨基酸溶液;所述浓缩废液中含有较高浓度的菌体蛋白,所述菌体蛋白包括不溶性蛋白和可溶性蛋白,其中可溶性蛋白易溶于水,若直接对所述浓缩废液进行干燥处理,则将会从所述浓缩废液中的不溶性蛋白得到固体蛋白物质,而所述浓缩废液中的可溶性蛋白由于溶于水被干燥,无法得到固态蛋白物质,而造成了资源浪费。因此,为了提高所述浓缩废液中菌体蛋白的提取率,将对所述浓缩废液进行水解处理,将所述浓缩废液中的不溶性蛋白和可溶性蛋白均水解为可溶性氨基酸,得到氨基酸溶液,避免了资源浪费。进一步地,通过酸解法、酶解法和酸酶联合水解法中的任一种对所述浓缩废液进行水解处理,得到氨基酸溶液。酸解法是利用酸分解矿物原料制取无机产品的一种湿法过程,酶解法是利用活性酶来水解特定物质的方法,酸酶联合水解法则是酸解法和酶解法共同使用的方法。在具体实现中,根据所述浓缩废液中的菌体蛋白的类型选取适宜的水解法进行水解,例如所述浓缩废液中的菌体蛋白能够被某种活性酶催化分解,则使用酶解法或者酸酶联合水解法进行水解,若所述浓缩废液中的菌体蛋白能够被某种酸分解则使用酸解法或者酸酶联合水解法进行水解。步骤s30:对所述氨基酸溶液进行干燥,得到氨基酸肥料。所述工业尾气发酵废液中的蛋白质几乎都转化至所述氨基酸溶液中,此时,对所述氨基酸溶液进行干燥,得到的氨基酸肥料中含有大量氮、磷和钾等各种作物所需的微量元素,且该氨基酸肥料符合ny1429-2010含氨基酸水溶肥料标准各项指标要求。进一步地,对所述氨基酸溶液进行离心喷雾干燥或者压力喷雾干燥,得到氨基酸肥料。离心喷雾干燥是利用水平方向作高速旋转的圆盘给予氨基酸溶液以离心力,使其以高速甩出,形成薄膜、细丝或液滴,由于空气的摩擦、阻碍、撕裂的作用,随圆盘旋转产生的切向加速度与离心力产生的径向加速度,结果以一合速度在圆盘上运动,其轨迹为一螺旋形,液体沿着此螺旋线自圆盘上抛出后,就分散成很微小的液滴以平均速度沿着圆盘切径方向运动,同时液滴又受到地心吸力而下落,由于喷洒出的微粒大小不同,因而它们飞行距离也就不同,因此在不同的距离落下的微粒形成一个以转轴中心对称的圆柱体,即为氨基酸肥料。压力喷雾干燥是利用高压泵,以70~200大气压的压力,将所述氨基酸溶液通过雾化器(喷枪),聚化成10~200的雾状微粒与热空气直接接触,进行热交换,短时间完成干燥。在实际操作中,可根据具体的操作设备选取离心喷雾干燥或者压力喷雾干燥进行干燥。在本实施例中,通过对工业尾气发酵废液进行浓缩处理,得到浓缩废液;对所述浓缩废液进行水解处理,得到氨基酸溶液;并对所述氨基酸溶液进行干燥,得到氨基酸肥料。实现了将工业尾气发酵废液转化为氨基酸肥料,保留了工业尾气发酵废液中的氮、磷和钾等微量元素,从而提高了工业尾气发酵废液的资源利用率,并且降低了污水处理负荷。参照图2,本发明实施例提供一种使用工业尾气发酵废液制备氨基酸肥料的系统,所述系统包括:蒸发浓缩装置2,用于对工业尾气发酵废液进行浓缩处理,得到浓缩废液;所述工业尾气发酵废液中含有较低浓度的菌体蛋白,将菌体蛋白从所述工业尾气发酵废液中提取出来的难度较大,为了降低提取难度、提高提取效率,将预先对所述工业尾气发酵废液进行蒸发浓缩,得到浓缩废液。进一步地,所述蒸发浓缩装置2顶部产生的蒸汽冷凝水直接回用于生产。水解装置4,用于对所述浓缩废液进行水解处理,得到氨基酸溶液;所述浓缩废液中含有较高浓度的菌体蛋白,所述菌体蛋白包括不溶性蛋白和可溶性蛋白,其中可溶性蛋白易溶于水,若直接对所述浓缩废液进行干燥处理,则将会从所述浓缩废液中的不溶性蛋白得到固体蛋白物质,而所述浓缩废液中的可溶性蛋白由于溶于水被干燥,无法得到固态蛋白物质,而造成了资源浪费。因此,为了提高所述浓缩废液中菌体蛋白的提取率,将对所述浓缩废液进行水解处理,将所述浓缩废液中的不溶性蛋白和可溶性蛋白均水解为可溶性氨基酸,得到氨基酸溶液,避免了资源浪费。进一步地,所述水解装置4为一个以上水解反应器。喷雾干燥装置6,用于对所述氨基酸溶液进行干燥,得到氨基酸肥料。所述工业尾气发酵废液中的蛋白质几乎都转化至所述氨基酸溶液中,此时,对所述氨基酸溶液进行干燥,得到的氨基酸肥料中含有大量氮、磷和钾等各种作物所需的微量元素,且该氨基酸肥料符合ny1429-2010含氨基酸水溶肥料标准各项指标要求,所述氨基酸肥料从所述喷雾干燥装置6底部移出。进一步地,所述系统还包括:发酵装置,用于通过工业尾气发酵制乙醇法对工业尾气进行发酵,得到工业尾气发酵废液。所述工业尾气发酵制乙醇法的具体实施过程为:将工业尾气进行预处理,所述预处理包括:脱除工业尾气中的有毒物质,得到净化的尾气;将所述净化的尾气用于发酵,得到发酵成熟醪以及余气;将所述发酵成熟醪蒸馏,得到乙醇以及含菌余馏水;将所述含菌余馏水分离浓缩,得到浓液及清液;将所述清液净化处理;将所述余气进行尾气处理,去除残留的一氧化碳。其中,所述浓液即为所述工业尾气发酵废液。进一步地,所述系统还包括:第一进料泵1,用于将所述工业尾气发酵废液送入至所述蒸发浓缩装置2中;第二进料泵3,用于将所述浓缩废液送入至所述水解装置4中;第三进料泵5,用于将所述氨基酸溶液送入至所述喷雾干燥装置6中。在本实施例中,通过蒸发浓缩装置2对工业尾气发酵废液进行浓缩处理,得到浓缩废液;通过水解装置4对所述浓缩废液进行水解处理,得到氨基酸溶液;并通过喷雾干燥装置6对所述氨基酸溶液进行干燥,得到氨基酸肥料。实现了将工业尾气发酵废液转化为氨基酸肥料,保留了工业尾气发酵废液中的氮、磷和钾等微量元素,从而提高了工业尾气发酵废液的资源利用率,并且降低了污水处理负荷。为了更加清晰地理解本发明的目的、技术方案及优点,以下结合实施例,对本发明进行进一步详细说明。此处所描述的具体例子所涉及的具体数据仅用以解释本发明,并不用于限定本发明。实施例1工业尾气发酵废液中菌体蛋白固含量为30g/l,流量为25m3/h,经第一进料泵送入蒸发浓缩装置。蒸发浓缩装置为三效蒸发器,浓缩5倍得到浓缩废液,浓缩废液中的菌体蛋白含量为150g/l,浓缩废液流量为5m3/h。浓缩废液经第二进料泵进入酸法水解反应器,采用盐酸(6n)水解,水解温度115℃,时间20h,之后降温至80℃,加碳酸钠中和至ph为4.5,得到氨基酸溶液。氨基酸溶液经第三进料泵送入离心式喷雾干燥塔进行干燥,进风温度200℃,出风温度75℃,固体氨基酸肥料含水率6%,游离氨基酸含量>45%。实施例2工业尾气发酵废液中菌体蛋白固含量为28g/l,流量为30m3/h,经第一进料泵送入蒸发浓缩装置。蒸发浓缩装置为三效蒸发器,浓缩5倍得到浓缩废液,浓缩废液中的菌体蛋白含量140g/l,浓缩废液流量为6m3/h。浓缩废液先经第二进料泵进入酸法水解反应器,采用盐酸(6n)水解,水解温度115℃,时间20h,之后降温至50℃,加碳酸钠中和至ph为7。之后送入酶法水解反应器,采用枯草杆菌中性蛋白酶,反应时间15h,得到氨基酸溶液。通过酸酶法水解后的氨基酸溶液经第三进料泵送入离心式喷雾干燥塔进行干燥,进风温度220℃,出风温度80℃,固体氨基酸肥料含水率5%,游离氨基酸含量>52%。最后,还需要说明的是,术语“包括”、“包含”或者其任何其他变体意在涵盖非排他性的包含,从而使得包括一系列要素的过程、方法、物品或者设备不仅包括那些要素,而且还包括没有明确列出的其他要素,或者是还包括为这种过程、方法、物品或者设备所固有的要素。尽管已描述了本发明的优选实施例,但本领域内的技术人员一旦得知了基本创造性概念,则可对这些实施例作出另外的变更和修改。所以,所附权利要求意欲解释为包括优选实施例以及落入本发明范围的所有变更和修改。显然,本领域的技术人员可以对本发明进行各种改动和变型而不脱离本发明的精神和范围。这样,倘若本发明的这些修改和变型属于本发明权利要求及其等同技术的范围之内,则本发明也意图包含这些改动和变型在内。当前第1页1 2 3