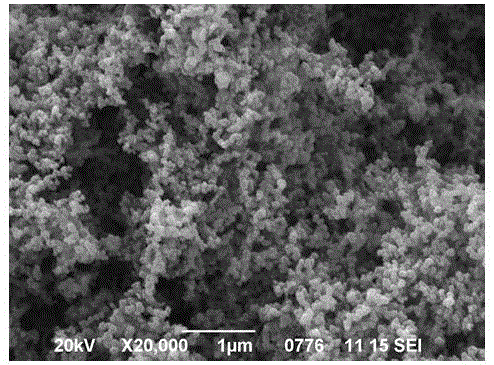
本发明涉及炭素石墨
技术领域:
,尤其涉及一种极细结构炭素石墨制品的制备方法。
背景技术:
:炭素石墨制品是以石油焦、沥青焦等焦炭为原料、煤沥青为粘接剂,经破碎、配料、混捏、成型、烧结、浸渍、石墨化、机械加工等工艺制造的一种耐高温抗氧化的导电材料,广泛应用于冶金、化工、航天、电子、机械、建材、核能等不同领域,如做耐磨用的轴承、密封环;电火花加工用电极、电解加工用电极;连续浇铸用结晶器;半导体生产用加热器、坩埚、炉衬;烧结模具及航空航天飞行器燃气舵及发动机保护套等。目前国内生产的炭素石墨制品多采用石油焦、沥青焦等为原材料,由于能源紧缺、环境污染等问题,石油焦、沥青焦等能源材料紧缺,伴随着国内治理环境污染等的停产、限产带来的成本增加、原料紧缺等严重限制了行业的发展。第二,石油焦等焦炭制品,由于其特殊的结构造成炭化、石墨化过程中挥发份的排除而引起开裂、破损等问题,严重影响了细结构石墨的性能。第三,石油焦等焦炭制品犹在粉碎过程中易造成形貌复杂,很难加工成≤3μm类球形的超微粉体材料,而造成细结构炭素石墨制品的各向异性,进一步影响了细结构炭素石墨制品的性能。第四,目前炭素石墨制品多采用混捏的方式混合母料和粘接剂以及其他添加成分,由于一次颗粒的粒径较大,导致石墨电极的各向同性较差,最终引起石墨电极性能的差异。其中,混捏属于干混的一种,而粘接剂有一定的粘性,混捏的方式极易导致材料组分分布的不均匀,而由于混合不均匀的各种组分在温度变化情况下的收缩比、收缩速度的不同,导致石墨电极容易在生产过程中产生内裂,最终引起石墨电极的报废,大大提高了石墨电极的生产成本。本发明人考虑,采用植物制品等为原料,解决能源材料带来的原料紧缺、成本上升、环境污染等一系列问题。并且,进一步提高极细结构炭素石墨制品的各项性能。技术实现要素:本发明解决的技术问题在于提供一种极细结构炭素石墨制品的制备方法,节能环保,且具有较高的密度和强度。有鉴于此,本发明提供了一种极细结构炭素石墨制品的制备方法,包括以下步骤:将农林废弃生物质炭化、制粉、形貌处理,得到≤3μm类球形的超微粉体;将所述超微粉体与粘接剂、添加剂、石墨化促进剂进行液相混合,然后干燥、成型、3-8次的反复浸渍与焙烧,石墨化处理,得到极细结构炭素石墨制品。优选的,所述农林废弃生物质为稻秆、麦秸、竹竿和椰壳中的一种或几种。优选的,所述炭化的温度为500-1100℃。优选的,制粉的粒度小于等于3μm。优选的,所述石墨化促进剂为硅、氧化硅、碳化硅、硼、氧化锰、稀土元素、氧化铁和碳酸钙中的一种或几种。优选的,所述添加剂为聚乙二醇、聚乙烯醇、聚丙烯醇、聚氧化乙烯、聚丙烯酸和羧甲基纤维素钠中的一种或几种。优选的,干燥后粉体的体密度为0.3-1.6g/cm3,粉体的粒度为0.1-50um,粉体的水分小于1%。优选的,所述成型控制比重为1.2-1.75g/cm3。优选的,所述一次焙烧的焙烧温度为300-1200℃,比重范围为1.1-1.75g/cm3,焙烧时间为50-360小时。优选的,所述石墨化处理的温度为2300-3500℃,石墨化处理的时间为1-30天。本发明提供一种极细结构炭素石墨制品的制备方法,包括:将农林废弃生物质炭化、制粉、形貌处理,得到≤3μm类球形的超微粉体;将所述超微粉体与粘接剂、添加剂、石墨化促进剂进行液相混合,然后干燥、成型、3-8次的反复浸渍与焙烧,石墨化处理,得到极细结构炭素石墨制品。与现有技术相比,本发明以农林废弃生物质为原料,避免了能源材料的使用,且该材料炭化后易制成类球形的超微粉体,为降低细结构石墨的各向异性奠定了基础;本发明采用极细的农林废弃生物质为原料,并采用液相法混合主材和粘接剂、添加剂等材料,保证了细结构炭素石墨制品的整体一致性,进一步提高了各向同性,避免内裂等问题,降低了极细结构炭素石墨制品的生产成本及过程控制成本,节能环保,提高了极细结构炭素石墨制品的密度和强度,综合性能良好。附图说明图1为本发明实施例1原料炭化、形貌处理后的sem图;图2为本发明实施例1制备的细结构石墨的外观图。具体实施方式为了进一步理解本发明,下面结合实施例对本发明优选实施方案进行描述,但是应当理解,这些描述只是为进一步说明本发明的特征和优点,而不是对本发明权利要求的限制。本发明实施例公开了一种极细结构炭素石墨制品的制备方法,包括以下步骤:将农林废弃生物质炭化、制粉、形貌处理,得到≤3μm类球形的超微粉体;将所述超微粉体与粘接剂、添加剂、石墨化促进剂进行液相混合,然后干燥、成型、3-8次反复浸渍与焙烧,石墨化处理,得到极细结构炭素石墨制品。作为优选方案,所述农林废弃生物质为稻秆、麦秸、竹竿和椰壳中的一种或几种。所述炭化的温度优选为500-1100℃,更优选为500-900℃。本发明优选根据不同的原料调整不同的炭化温度,保证杂质、挥发份的充分排出。作为优选方案,将炭化后的材料进行制粉,制粉的粒度优选小于3μm。对制粉后的材料进行形貌处理,保证材料的类球形,从而保证原材料各向同性。在液相混合的步骤中,将溶剂、粘结剂、石墨化促进剂、添加剂混合均匀,最后加入形貌处理后的主料进行混合,通过间隔时间测试不同部位的固含量及粘度,待不同部位的固含量和粘度差异性小于±2%,即能保证混合的均匀度。所述粘接剂优选为低温沥青、焦油、树脂、高温改性沥青。所述添加剂为聚乙二醇、聚乙烯醇、聚丙烯醇、聚氧化乙烯、聚丙烯酸、羧甲基纤维素钠中的一种或几种,添加量为所述超微粉体的0.1wt%~5wt%。所述石墨化促进剂为硅、氧化硅、碳化硅、硼、氧化锰、稀土元素、氧化铁和碳酸钙中的一种或几种,添加量为所述超微粉体的2wt%~8wt%。所述液相混合采用的溶剂为水或酒精。添加剂的主要作用是保证液相混合时能够分散均匀,只有各种成分分散均匀了,才能保证最终产品的各向同性和综合性能的提升。本发明在干燥步骤后,形成组分分布均匀的混合粉体。干燥后粉体的体密度优选为0.3-1.6g/cm3,粉体的粒度优选为0.1-50um,粉体的水分优选小于1%。作为优选方案,所述成型利用等静压机或模压机进行压制成型。所述成型控制比重优选为1.2-1.75g/cm3。作为优选方案,所述一次焙烧的焙烧温度为300-1200℃,比重范围为1.1-1.75g/cm3,焙烧时间为50-360小时。所述二次焙烧的焙烧温度在850℃以下。本发明的焙烧和浸渍的重复次数根据选择的原料和所需产品进行选择,优选为3-8次。作为优选方案,本发明的焙烧和石墨化过程必须在埋伏情况或保护性气体气氛下进行,所述保护性气体优选为氩气、氦气或氖气。所述石墨化处理的温度优选为2300-3000℃,更优选为2300-2900℃;石墨化处理的时间优选为1-30天,更优选为15-30天。从以上方案可以看出,本发明采用稻秆、麦秸、竹竿、椰壳等农林废弃生物质为原料,解决了能源材料带来的原料紧缺、成本上升、环境污染等一系列问题,同时该材料炭化后的材料较容易制粉,粒径<3μm,经过形貌处理可以得到≤3μm类球形的超微粉体材料,为降低后续细结构石墨的各向异性奠定了基础。本发明采用极细的原材料,并采用液相法混合主材和粘接剂、添加剂等材料,保证了细结构炭素石墨制品的整体一致性,进一步提高了各向同性,并避免了由于温度变化造成的弹性形变而引起的内裂等问题,降低了极细结构炭素石墨制品的生产成本及过程控制成本,提高了极细结构炭素石墨制品的各项性能。本发明具有如下优点:1、原材料绿色、环保:采用植物制品为原料,原料来源绿色、环保,来源广泛,同时解决了能源材料带来的原料紧缺、成本较高等问题。2、各向同性好:植物制品炭化后的材料较易粉碎,经过形貌处理后可加工成≤3μm类球形的超微粉体材料,类球形的结构和极细(<3μm)的粒径,保证了最后极细结构炭素石墨制品的各向同性,提高了制品的性能。3、高性能:各向同性优异的原材料及特殊的加工工艺,保证了极细结构炭素石墨制品优异的性能。为了进一步理解本发明,下面结合实施例对本发明提供的技术方案进行详细说明,本发明的保护范围不受以下实施例的限制。本发明实施例采用的原料均为市购。实施例1称取椰壳1000kg,利用回转炉进行炭化,炭化温度900℃,保温30小时;炭化后材料用磨粉机进行磨粉,磨粉粒度≤1μm;磨粉后进行球形化处理形成主料,要求形貌为类球形,如图1所示;称取400kg的酒精,加入2kg的pva搅拌30min,然后加入软化点在280℃的沥青40kg、氧化铁10kg进行搅拌,分散均匀后加入已经形貌处理过的主料200kg,边研磨边搅拌,待不同部位的固含量和粘度差异性小于±2%,停止搅拌;将液体进行干燥,保证粒度范围控制在0.1-50um,保证粉体的体密度范围控制为0.3-1.6g/cm3,保证粉体的粒度范围分布为0.1-50um,保证粉体的水分控制在小于1%,形貌为球形;利用等静压机进行等静压成型,控制比重范围控制在:1.2-1.75g/cm3;采用低温沥青(软化点小于70)进行浸渍;在800摄氏度进行焙烧,焙烧时间为:300小时;焙烧完后再次进行浸渍、焙烧,反复进行三次,保证极细结构炭素石墨制品半成品的密度>1.9g/cm3;对焙烧完成的极细结构炭素石墨制品半成品在2900℃进行石墨化,石墨化时间为10天;石墨化完成后,随炉温冷却,得到极细结构炭素石墨制品。本发明的焙烧和石墨化是在埋伏隔绝空气的情况下进行。图1为本发明实施例1原料炭化、形貌处理后的sem图。从sem图可以看出,大部分颗粒属于纳米级别,此次制粉的最大颗粒小于1μm,保证了一次颗粒的小粒径,从而更加提高了产品的各向同性。图2为本发明实施例制备的极细结构炭素石墨制品的外观图,即采用生物制炭最终制成的细结构炭素石墨制品,由于一次颗粒度≤3μm,因此与常规产品相比表面更细腻、更光滑。对比例1称取石油焦1000kg进行磨粉,磨粉粒度d50=18-22μm;称取500kg石油焦粉,与125kg软化点在92℃的沥青、10kg的氧化铁进行混捏。利用等静压机进行等静压成型,控制比重范围控制在:1.2-1.75g/cm3;采用低温沥青(软化点小于70)进行浸渍;在800摄氏度进行焙烧,焙烧时间为:300小时;焙烧完后再次进行浸渍、焙烧,反复进行三次,保证细结构炭素石墨制品半成品的密度>1.9g/cm3;对焙烧完成的细结构炭素石墨制品半成品在2900℃进行石墨化,石墨化时间为10天;石墨化完成后,随炉温冷却,得到常规细结构炭素石墨制品。分别对本实施例制备的极细结构炭素石墨制品和对比例1制备的细结构炭素石墨制品的性能进行检测,结果如表1所示。表1本发明实施例1和对比例1制备的细结构炭素石墨制品的性能结果检验参数纯度一次颗粒度体积密度抗压强度抗折强度单位%μmg/cm3mpampa实施例1极细结构炭素石墨制品99≤1μm1.984225对比例1制备的常规细结构石墨制品99201.954125实施例2称取稻杆1000kg,利用回转炉进行炭化,炭化温度900℃,保温30小时;炭化后材料用磨粉机进行磨粉,磨粉粒度≤1μm;磨粉后进行球形化处理,要求形貌为类球形;称取400kg的酒精,加入2kg的pva搅拌30min,然后加入软化点在280℃的沥青40kg、氧化铁10kg进行搅拌,分散均匀后加入已经形貌处理过的主料200kg,边研磨边搅拌,待不同部位的固含量和粘度差异性小于±2%,停止搅拌;将液体进行干燥,保证粒度范围控制在0.1-50μm,保证粉体的体密度范围控制为0.3-1.6g/cm3,保证粉体的粒度范围分布为0.1-50um,保证粉体的水分控制在小于1%,形貌为球形;利用等静压机进行等静压成型,控制比重范围控制在:1.2-1.75g/cm3;采用低温沥青(软化点小于70)进行浸渍;在900摄氏度进行焙烧,焙烧时间为:400小时;焙烧完后再次进行浸渍、焙烧,反复进行三次,保证极细结构炭素石墨制品半成品的密度>1.9g/cm3;对焙烧完成的极细结构炭素石墨制品半成品在2900℃进行石墨化,石墨化时间为15天;石墨化完成后,随炉温冷却,得到极细结构炭素石墨制品。本发明的焙烧和石墨化是在埋伏隔绝空气的情况下进行。分别对本实施例制备的极细结构炭素石墨制品和对比例1制备的常规细结构炭素石墨制品的性能进行检测,结果如表2所示。表2本发明实施例2和对比例1制备的细结构炭素石墨制品的性能结果检验参数纯度一次颗粒度体积密度抗压强度抗折强度单位%μmg/cm3mpampa实施例2极细结构炭素石墨制品99≤11.964225对比例1制备的常规细结构石墨制品99201.954125以上实施例的说明只是用于帮助理解本发明的方法及其核心思想。应当指出,对于本
技术领域:
的普通技术人员来说,在不脱离本发明原理的前提下,还可以对本发明进行若干改进和修饰,这些改进和修饰也落入本发明权利要求的保护范围内。对所公开的实施例的上述说明,使本领域专业技术人员能够实现或使用本发明。对这些实施例的多种修改对本领域的专业技术人员来说将是显而易见的,本文中所定义的一般原理可以在不脱离本发明的精神或范围的情况下,在其它实施例中实现。因此,本发明将不会被限制于本文所示的这些实施例,而是要符合与本文所公开的原理和新颖特点相一致的最宽的范围。当前第1页1 2 3