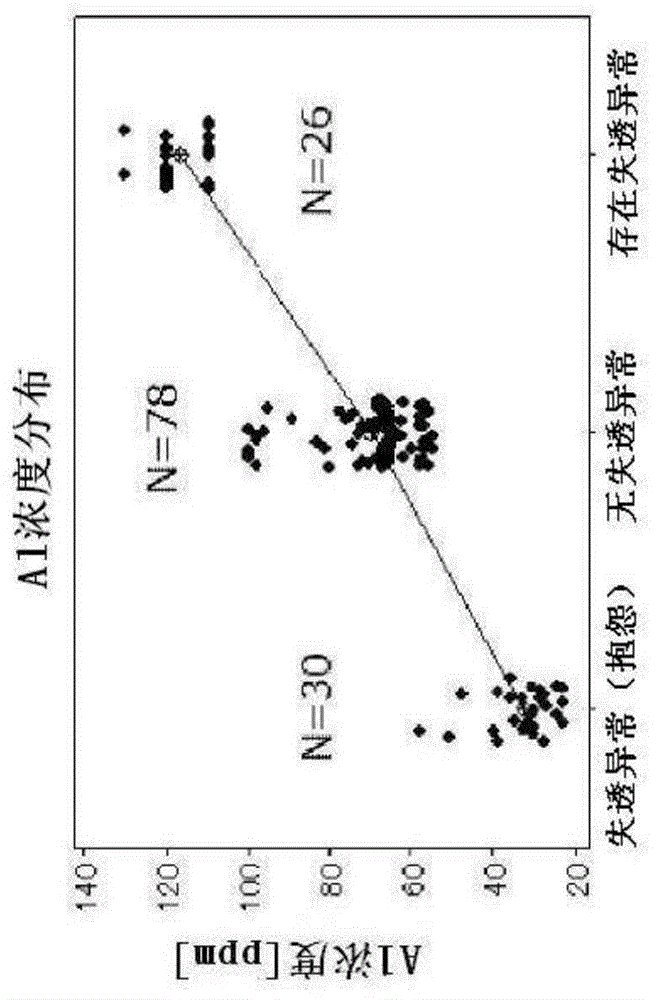
本发明涉及用于利用切克劳斯基法(czochralski)(以下,称为“cz法”)来提拉硅单晶的、或者用于光学玻璃熔融的石英玻璃坩埚以及石英玻璃坩埚的制造方法。
背景技术:
:在用于硅铸造、光学玻璃制造的熔融容器中,使用石英玻璃、碳制的坩埚。例如,太阳能电池所使用的多晶硅是以使放入在坩埚中的硅熔体从坩埚底面向一个方向凝固而形成柱状晶体的方法来制作的。与之相对,在单晶硅的制造中,一般使用切克劳斯基(cz)法,通过使硅熔体表面和籽晶之间利用熔体的表面张力相连,利用硅熔体内的强制对流使籽晶生长,一边使籽晶在硅熔体上向相反方向旋转一边提拉,从而在籽晶的下端生长晶锭单晶。另外,对于光学玻璃,例如从喷嘴的顶端滴下熔融玻璃来制作液滴状玻璃,并得到预成型玻璃,或者将熔融玻璃骤冷铸造,临时制作玻璃块,再研磨、抛光、清洗得到预成型玻璃,从而制造。例如,光学玻璃熔融用的石英玻璃坩埚使用天然二氧化硅原料。另一方面,硅单晶提拉用的石英玻璃坩埚中,有时将内层制作成高纯度的合成石英玻璃的透明层,将外层设为比内层纯度低但便宜的天然石英玻璃的不透明层。然而,石英玻璃坩埚逐年大型化,石英玻璃坩埚的大型化是为了提拉大口径硅单晶。这样,通过使石英玻璃坩埚大型化,从而能够使容纳在石英玻璃坩埚内并通过加热而成为硅熔融液的多晶硅的装填量增大,能够提拉的硅单晶变长,从而有生产量提高的优点。然而,其缺点是,由于将多晶硅加工成硅熔融液的熔融时间变长,且加热用的碳加热器的输出变大,所以石英玻璃坩埚必须在被暴露在比现有技术更高的高温中这样的苛刻环境下使用,给石英玻璃坩埚带来的恶劣影响也很大。具体地,近年来,随着硅单晶的大口径化,将已加热到1400℃的原料硅熔体长时间容纳在坩埚中,其内表面与硅熔体反应,在内表面的浅层发生结晶化,或者构成坩埚的石英玻璃的粘度下降,坩埚变得容易发生失透、变形。另外,由于硅单晶大口径化,所以原料硅熔体的量也增加,对坩埚的重量负载也变大,担心裂纹的产生、漏液之类的坩埚的脆化。而且,若随着原料硅熔体的量增加,坩埚自身也大型化,那么原料硅熔体的液面振动也变大。例如,现有的石英玻璃坩埚在高温区域的粘性值变低,在1400℃以上的热环境下难以长时间维持其形状。因此,在硅单晶提拉工序中产生了石英玻璃坩埚的变形导致的熔融硅的熔体面的变动以及单晶化率(提拉后的硅单晶重量与多晶硅填充重量之比)的下降等问题。因此,对于石英玻璃坩埚,特别是大型的石英玻璃坩埚,需求其强度达到即使在高温下也不变形并且能够抑制被容纳的原料硅熔体的液面振动。目前为止,为了抑制高温下坩埚的变形,使用在石英原料粉中添加铝(al),提高石英玻璃的粘度,促进结晶化的方法。另一方面,当石英玻璃中的al浓度变得过高时,坩埚的结晶化会快速进行,形成厚的结晶层,在冷却时坩埚有可能会产生裂纹,导致漏液。为了解决这种问题,例如专利文献1中公开了一种具备由如下石英玻璃原料构成的外层的石英玻璃坩埚,即al浓度8.8~15wtppm、钠(na)浓度低于0.1wtppm、钾(k)浓度低于0.2wtppm,且锂(li)浓度0.3~0.8wtppm,al相对于li的摩尔浓度比(al/li)7.5以下的石英玻璃原料。li由于具有抑制结晶化的作用,所以实现适当地抑制由于al而导致的结晶化促进作用的效果。在专利文献1中,用包含规定量的al和li在内的石英玻璃原料来形成外层,从而对坩埚赋予优异的强度特性。在专利文献2中公开有如下内容,在具有将天然二氧化硅粉熔融而形成的不透明的外层以及由合成石英玻璃构成的透明的内层的石英玻璃坩埚中,通过将从内表面到0.88mm深度的内层中的平均al浓度设为1~20ppm,平均oh基浓度设为150~300ppm,从而适度地生成方石英,其结果,即使长时间使用,玻璃熔析面的出现也少,提拉的硅单晶的成品率变高,而且能够抑制硅熔体表面的振动。将石英玻璃原料中的金属杂质(al、fe、na以及k等)的含有率从100中减去而得到的化学纯度通常能够在原材料交付时的验收检查时进行数值确认,但是对于石英玻璃的失透性,要在实际制造坩埚后,利用破坏检查才初次确认。也就是说,仅根据这些金属杂质的含量的测定结果来推测失透性是困难的,必须破坏坩埚,才能在使用前判断失透性。另外,为了解决上述坩埚的变形、破损的问题,在专利文献3中提出有一种三层结构的石英玻璃坩埚,其中,外层是添加al的石英层,中间层是天然石英层,内层是高纯度合成石英层。在硅单晶提拉工序的加热升温过程中,当该坩埚的外层在1200℃以上以一定温度加热时,会向方石英结晶化。而且,在方石英的生长过程中,粘度提升,进一步结晶化,从而能够得到高的耐久性,能够向前述那样解决坩埚的变形、破损之类的问题。另外,当添加有结晶化促进剂的外层粒子混入坩埚内表面时,会给坩埚的耐久性、单晶化率带来影响,所以本申请人在专利文献4中提出如下方案:在将使用前的坩埚开口部的包装取下时、利用吸盘吸附、放下坩埚开口部时,抑制添加有结晶化促进剂的外层粒子混入坩埚内表面。具体而言,在专利文献4中提出如下坩埚,该坩埚为了抑制添加了结晶化促进剂的外层粒子向坩埚内表面混入,而在从坩埚上端起30~50mm的区域内不形成添加有结晶化促进剂的外层。现有技术文献专利文献专利文献1:日本特开2014-5154号公报专利文献2:日本特开2005-231986号公报专利文献3:日本特开2000-247778号公报专利文献4:日本特开2010-275151号公报技术实现要素:发明欲解决的技术问题本发明是使用了含有规定量的al成分和ca成分的天然二氧化硅粉作为石英玻璃坩埚的原料的石英玻璃坩埚的制造方法,目的是提供一种能够使石英玻璃适度结晶化,能够抑制坩埚的变形以及裂纹的产生的低失透性的不透明石英玻璃坩埚的制造方法。另外,本发明的目的是提供含有规定量的al成分和ca成分的石英玻璃坩埚。然而,在专利文献4中记载的坩埚中,由于在从坩埚上端起30~50mm的区域中,未形成添加有结晶化促进剂的外层,所以抑制了添加结晶化促进剂后的外层粒子混入坩埚内表面,实现了耐久性、单晶化率的提升,但是发现了坩埚的上端区域会向内侧变形(倾倒)的现象。在将硅单晶提拉的工序中,当坩埚的上端区域向内侧变形(倾倒)时,提拉装置内的气体的流动被阻碍,在被提拉的硅单晶中,有可能不能得到必要的结晶特性,另外在坩埚的上端区域极端地变形的情况下,坩埚的上端区域有可能与晶锭(硅单晶)接触,而无法继续坩埚的上端区域的提拉。另外,在专利文献3中记载的坩埚中,由于到坩埚开口部上端(口缘上端)为止形成有添加了结晶化促进剂的层,所以在结晶化时,有可能从坩埚开口部上端部的外周侧产生裂纹,由于裂纹向坩埚底部侧伸展而发生漏液。本发明人为了解决这些问题,进行了认真研究,通过确定不形成未添加结晶化促进剂的外层的区域,从而抑制从坩埚开口部(坩埚的上端)起产生的裂纹,并且抑制坩埚的上端区域向内侧的变形(倾倒),而完成本发明。本发明是在如前述的情况的基础上完成的,进一步目的是提供一种石英玻璃坩埚,其在具有添加了结晶化促进剂的外层的坩埚中,抑制从坩埚开口部(坩埚的上端)产生的裂纹,同时抑制了坩埚的上端区域向内部的变形(倾倒)。用于解决问题的技术手段即,本发明涉及以下(1)~(11)。(1)一种石英玻璃坩埚,含有al和ca。(2)如(1)所述的石英玻璃坩埚,其中,用化学纯度分析求出的铝浓度为55wtppm以上且100wtppm以下,钙浓度为1.2wtppm以上且9.5wtppm以下,根据铝浓度和钙浓度算出的al/ca摩尔浓度比为15以上。(3)如(2)所述的石英玻璃坩埚的制造方法,具有:工序1,将原料二氧化硅粉装填在旋转的成形模具中进行成形,所述原料二氧化硅粉中根据用化学纯度分析求出的铝浓度和钙浓度算出的al/ca摩尔浓度比为15以上;以及工序2,将电弧电极插入到所述成形模具中,对堆积在该成形模具内表面的原料二氧化硅粉层进行电弧熔融而玻璃化。(4)如(3)所述的石英玻璃坩埚的制造方法,其特征在于,在所述工序1中,原料二氧化硅粉的铝浓度为55wtppm以上且100wtppm以下,钙浓度为1.2wtppm以上且9.5wtppm以下。(5)如(1)所述的石英玻璃坩埚,其特征在于,所述石英玻璃坩埚具有:底部;底部拐角,所述底部拐角形成在所述底部的周围;以及侧部,所述侧部从所述底部拐角向上方延伸,所述石英玻璃坩埚具有坩埚上端区域,所述坩埚上端区域是从坩埚上端起向下方5mm以上且将上端的壁厚加上10mm而算出的长度以下的区域,所述坩埚上端区域包含由不透明外层和透明内层形成的两层结构,所述不透明外层包含天然原料石英玻璃,所述透明内层包含天然原料石英玻璃或者合成原料石英玻璃,从所述坩埚上端区域的下端起至少包含三层结构,所述三层结构由外层、不透明中间层以及所述透明内层形成,所述外层包含添加了结晶化促进剂的石英玻璃,所述不透明中间层从所述坩埚上端区域的不透明外层连续地形成。(6)如(5)所述的石英玻璃坩埚,其特征在于,所述添加了结晶化促进剂的石英玻璃含有al和ca,所述添加了结晶化促进剂的石英玻璃中的al浓度为9wtppm以上且20wtppm以下,ca浓度为0.1wtppm以上且0.6wtppm以下,al和ca的al/ca摩尔浓度比为15≤al/ca≤200。(7)如(5)或(6)所述的石英玻璃坩埚,其特征在于,所述石英玻璃坩埚在包含所述添加了结晶化促进剂的石英玻璃的外层的外侧进一步层叠包含天然原料石英玻璃的不透明外层,并且所述石英玻璃坩埚包含四层结构。(8)如(5)~(7)中任一项所述的石英玻璃坩埚,其特征在于,所述上端的壁厚为10mm以上且18mm以下。(9)一种石英玻璃坩埚,其特征在于,所述石英玻璃坩埚具有:底部;底部拐角,所述底部拐角形成在所述底部的周围;以及侧部,所述侧部从所述底部拐角向上方延伸,所述石英玻璃坩埚具有坩埚上端区域,所述坩埚上端区域是从坩埚上端起向下方5mm以上且将上端的壁厚加上10mm而算出的长度以下的区域,所述坩埚上端区域是由不透明外层和透明内层形成的两层结构,所述不透明外层包含天然原料石英玻璃,所述透明内层包含天然原料石英玻璃或者合成原料石英玻璃,从所述坩埚上端区域的下端起至少包含三层结构,所述三层结构由外层、不透明中间层以及所述透明内层形成,所述外层包含添加了结晶化促进剂的石英玻璃,所述不透明中间层从所述坩埚上端区域的不透明外层连续地形成。(10)如(9)所述的石英玻璃坩埚,其特征在于,所述石英玻璃坩埚在包含所述添加了结晶化促进剂的石英玻璃的外层的外侧进一步层叠包含天然原料石英玻璃的不透明外层,并且所述石英玻璃坩埚包含四层结构。(11)如(9)或(10)所述的石英玻璃坩埚,其特征在于,所述上端的壁厚为10mm以上且18mm以下。本发明的石英玻璃坩埚的制造方法的特征在于,具有:工序1,将原料二氧化硅粉装填在旋转的成形模具中进行成形,所述原料二氧化硅粉中根据用化学纯度分析求出的铝浓度和钙浓度算出的al/ca摩尔浓度比为15以上;以及工序2,将电弧电极插入到所述成形模具中,对堆积在所述成形模具内表面的原料二氧化硅粉层进行电弧熔融而玻璃化。在所述工序1中,优选地,原料二氧化硅粉中的铝浓度为55wtppm以上且100wtppm以下,所述钙浓度为1.2wtppm以上且9.5wtppm以下。具有这种组成的原料二氧化硅粉的粘性偏差小,通过用该原料二氧化硅粉形成石英玻璃坩埚,能够得到如下石英玻璃坩埚,该石英玻璃坩埚即使长时间在1400℃以上的高温下也不会变形,另外具有不会由于冷却时的体积变化而导致产生裂纹、漏液的优异强度。本发明的石英玻璃坩埚中,用化学纯度分析求得的铝浓度为55wtppm以上且100wtppm以下,钙浓度为1.2wtppm以上9.5wtppm以下,根据铝浓度和钙浓度算出的摩尔浓度比(al/ca)为15以上。为了解决前述问题,本发明所涉及的石英玻璃坩埚所述石英玻璃坩埚具有:底部;底部拐角,所述底部拐角形成在所述底部的周围;以及侧部,所述侧部从所述底部拐角向上方延伸,所述石英玻璃坩埚具有坩埚上端区域,所述坩埚上端区域是从坩埚上端起向下方5mm以上且将上端的壁厚加上10mm而算出的长度以下的区域,所述坩埚上端区域包含由不透明外层和透明内层形成的两层结构,所述不透明外层包含天然原料石英玻璃,所述透明内层包含天然原料石英玻璃或者合成原料石英玻璃,从所述坩埚上端区域的下端起至少包含三层结构,所述三层结构由外层、不透明中间层以及所述透明内层形成,所述外层包含添加了结晶化促进剂的石英玻璃,所述不透明中间层从所述坩埚上端区域的不透明外层连续地形成。如此,在从坩埚上端起向下方5mm以上且将上端的壁厚加上10mm而算出的长度以下的坩埚上端区域中未形成外层,所述外层包含添加了结晶化促进剂的石英玻璃。因此,能够在抑制从坩埚开口部(坩埚的上端部)产生的裂纹的同时,抑制坩埚的上端部区域向内部的变形(倾倒)。而且,能够实现坩埚的耐久性的提升、单晶化率的提升,而且,能够解决由于坩埚的上端区域向内部变形(倾倒)而产生的硅单晶的结晶品质异常。此外,在所述坩埚上端区域从坩埚上端起向下方不到5mm的情况下,会从坩埚上端附近的外周侧产生裂纹,所以不优选。另外,在坩埚上端区域超过将坩埚上端的壁厚加上10mm而算出的长度的情况下,坩埚的上端区域会向会向坩埚内侧变形(倾倒),所以不优选。向所述外层添加的结晶化促进剂具体优选为al和ca。优选地,所述添加了结晶化促进剂的石英玻璃中的al浓度为9wtppm以上且20wtppm以下,ca浓度为0.1wtppm以上且0.6wtppm以下,且优选地,al和ca的摩尔浓度比(al/ca)为15≤al/ca≤200的范围。此处,优选地,在包含所述添加了结晶化促进剂的石英玻璃的外层的外侧进一步层叠包含天然原料石英玻璃的不透明外层,并且包含四层结构。另外,优选地,所述上端的壁厚为10mm以上且18mm以下。在坩埚上端的壁厚不到10mm的情况下,坩埚有破损的可能,另外耐久性不好,所以不优选。另外,在上端的壁厚超过18mm的情况下,坩埚的重量增大到必要量以上,所以不优选。在所述上端的壁厚为10mm以上且18mm以下的情况下,所述坩埚上端区域成为从坩埚上端起向下方去5mm以上且从上端起20mm~28mm以下。该情况下,由于在专利文献4记载的从坩埚的上端起30~50mm的区域内形成有添加了结晶化促进剂的外层,所以在使用前将坩埚开口部的包装取下时或者在用吸盘吸附、解吸坩埚开口部时,使添加了结晶化促进剂的外层粒子不混入坩埚内表面即可。发明效果根据本发明,通过将根据al浓度和ca浓度算出的摩尔浓度比(al/ca)为15以上的二氧化硅粉用作石英玻璃坩埚的原料,从而原料的粘性的偏差变小,石英玻璃适度地结晶化,能够制造低失透且维持了强度的石英玻璃坩埚。这样的石英玻璃坩埚能够抑制由于加热时间的变长而导致的坩埚的变形、裂纹的产生,而且即使坩埚变大,也能够抑制原料硅熔体的液面振动。具体而言,当作为原料的天然二氧化硅粉的化学纯度分析中的al/ca摩尔比为15以上,且优选为al浓度为55wtppm以上100wtppm以下,ca浓度为1.2wtppm以上9.5wtppm以下时,能够制造抑制了异常失透的石英玻璃坩埚。即,可以说即使不破坏石英玻璃坩埚来进行失透评价,也能够在原料阶段判断石英玻璃的失透性。根据本发明,通过判断原料能否使用,从而能够制造减少了与破损相关的异常失透的产生的石英玻璃坩埚。另外,根据本发明,在具有添加了结晶化促进剂的外层的石英玻璃坩埚中,能够得到在抑制从坩埚开口部(坩埚的上端)产生的裂纹的同时,抑制坩埚的上端区域向内侧的变形(倾倒)的石英玻璃坩埚。附图说明图1a~图1d是表示在例b的原料二氧化硅粉(图像中,表示失透异常(抱怨))、例a的原料二氧化硅粉(图像中,表示无失透异常)以及例c的原料二氧化硅粉(图像中,表示存在失透异常)中的al浓度(wtppm)分布(图1a),ca浓度(wtppm)分布(图1b)、na浓度(wtppm)分布(图1c)以及k浓度(wtppm)分布(图1d)的图表。图2a~图2c是表示基于图1a~图1d的结果的al/na摩尔浓度比分布(图2a)、al/k摩尔浓度比分布(图2b)以及al/ca摩尔浓度比分布(图2c)的图表。图3a~图3c是表示基于图1a和图2c的al浓度(wtppm)与al/ca摩尔浓度比的相关性的图表(图3a),以及表示基于图1b和图2c的ca浓度(wtppm)与al/ca摩尔浓度比的相关性的图表(图3b)及其放大图表(图3c)的图表。图4是表示将例b的石英玻璃坩埚在1500℃的条件下热处理100小时后将其破坏而制作的试验片(al/ca摩尔浓度比:7.43)的失透状态的照片。图5是表示将例c的石英玻璃坩埚在1500℃的条件下热处理100小时后将其破坏而制作的试验片(al/ca摩尔浓度比:2.44)的失透状态的照片。图6是表示将例a的石英玻璃坩埚在1500℃的条件下热处理100小时后将其破坏而制作的试验片(al/ca摩尔浓度比:42.34)的失透状态的照片。图7是本发明所涉及的石英玻璃坩埚的剖视图。图8是图7的石英玻璃坩埚的局部放大剖视图。图9是用于对图7的石英玻璃坩埚的各层的厚度尺寸进行说明的局部放大剖视图。图10是用于制造图7的石英玻璃坩埚的石英玻璃坩埚制造装置的剖视图。符号说明1石英玻璃坩埚2由添加有结晶化促进剂的石英玻璃构成的外层3不透明中间层4透明内层5a不透明外层5b不透明外层6坩埚上端7侧部8底部拐角9底部10坩埚上端区域30石英玻璃坩埚制造装置t坩埚上端的壁厚h从坩埚上端起的长度尺寸具体实施方式以下,对本发明的实施方式的一例进行说明。本发明的石英玻璃坩埚的制造方法具有:工序1,在旋转的成形模具中,装填al/ca摩尔浓度比为15以上的原料二氧化硅粉并成形,该摩尔浓度比根据利用化学纯度分析求出的铝(al)浓度(wtppm)和钙(ca)浓度(wtppm)算出;以及工序2,将电弧电极插入所述成形模具中,使堆积在所述成形模具内表面的原料二氧化硅粉层电弧熔融而玻璃化。也就是说,本发明的特征在于将作为形成石英玻璃的原料的天然二氧化硅粉中的al浓度和ca浓度调整为规定量。在石英玻璃坩埚由构成外层的天然二氧化硅粉和构成内层的合成二氧化硅粉形成的情况下,将构成外层的天然二氧化硅粉的al浓度和ca浓度调整为规定量。在工序1中,选择al/ca摩尔浓度比为15以上的原料二氧化硅粉,该摩尔浓度比根据用化学纯度分析求得的al浓度和ca浓度算出。对于原料二氧化硅粉,除al/ca为15以上之外,还优选al浓度为55wtppm以上且100wtppm以下、ca浓度为1.2wtppm以上且9.5wtppm以下。化学纯度分析具体是指icp发射光谱分析。al有促进石英玻璃结晶化的作用,通过在石英玻璃中以所述范围内的浓度含有al,从而al与ca以恰当的平衡相互作用,不会使石英玻璃过度结晶化,而是维持适度的结晶化的进行,从而能够提升坩埚的强度。ca有抑制结晶化的作用,在石英玻璃中,起到适度地抑制因al而造成的结晶化促进作用的效果。在原料二氧化硅粉中,在al和ca以外,作为不可避免的成分,还包含钠(na)、钾(k)以及锂(li)等。这些不可避免的成分是在原料二氧化硅粉的制造工序中,在使金属硅(si)与水在包含碱性催化剂和分散剂的水溶液中反应得到胶体二氧化硅的工序中混入。通过将原料二氧化硅中的al和ca的摩尔浓度比(al/ca)设为15以上,从而能够抑制胶体二氧化硅的粘性偏差。碱性催化剂是包含na、k或li的金属一价氢氧化物等,分散剂是无机酸、有机酸或者它们的盐(na盐、k盐、li盐以及铵盐等)。优选为硅单晶提拉用石英玻璃坩埚中使用的原料二氧化硅粉中的na浓度不到0.1wtppm,k浓度不到0.2wtppm,li浓度不到0.1wtppm。优选为光学玻璃熔融用石英玻璃坩埚所使用的原料二氧化硅粉中的na的浓度不到15wtppm,k浓度不到15wtppm,li浓度不到10wtppm。需要说明的是,na、k以及li都有对石英玻璃的结晶化促进作用,但是都是成为一价阳离子的碱金属,与成为三价阳离子的al相比与si的亲和性高,结晶化促进作用显著,所以难以通过调整它们的浓度来控制结晶化的程度。另外,碱金属会成为所提拉的硅单晶的重大的污染源。因此,优选为在坩埚的构成材料中不含有碱金属,可以利用纯化处理等方法将碱金属精制除去。al在结晶结构中在si的位置进行了同晶置换时,成为正电荷不足的状态。当ca被嵌入该部分时,al的电荷被约束。该电荷被约束的原子对不会成为结晶化的起点。当al/ca摩尔浓度比过大时,具体而言,当超过70时,ca浓度相对小,与si4+同晶置换后的al3+被电荷约束的比例下降,该部分容易成为结晶化的起点。并且,随着al/ca摩尔浓度比变大,结晶化的起点成为失透核,其个数增加,结晶化被促进。特别是,当al/ca摩尔浓度比超过100时,在坩埚尤其是底部的弯曲部,由于冷却时的体积变化,有时会在坩埚产生裂纹,进而有时会发生漏液。因此,优选为将al/ca摩尔浓度比设为70以下,从而将电荷不被约束而存在的al量抑制在微少的量,能够抑制失透核的产生,维持适度的结晶化的进行。这种al浓度例如可以通过向原料二氧化硅粉中添加硝酸铝九水合物(al(no3)3·9h2o)的水溶液等,调节至相对于原料二氧化硅粉中包含的ca浓度而成为规定量。在工序1中,将天然二氧化硅粉装填在旋转的成形模具中,并利用旋转成型法来成形。在石英玻璃坩埚包括外层和内层的情况下,以规定的层厚来装填外层形成用的天然二氧化硅粉,接着,在其内侧以规定厚度装填内层形成用的合成二氧化硅粉,并成形。也可以在外层形成后,利用火焰熔融法使内层直接堆积而形成。接着,在工序2中,将电弧电极插入到旋转的成形模具中,进行电弧熔融而玻璃化。电弧熔融在减压条件下进行,具体地优选为在真空条件下进行,且优选为以约2000℃和小于1小时的条件进行。通过所述工序1和2,得到例如厚度10~30mm、外径22~36英寸、高400~900mm的石英玻璃坩埚。得到的石英玻璃坩埚中,用化学纯度分析求得的al浓度为55wtppm以上且100wtppm以下,ca浓度为1.2wtppm以上且9.5wtppm以下,al/ca摩尔浓度比为15以上。需要说明的是,石英玻璃坩埚中的al浓度、ca浓度、na浓度和k浓度以及al/na摩尔浓度比、al/k摩尔浓度比和al/ca摩尔浓度比与原料二氧化硅粉中的这些数值相同。本发明的石英玻璃坩埚的制造方法中,除使用含有规定量的al和ca的天然二氧化硅粉作为原料之外,其他并不限制,一般通过旋转模具法和电弧熔融法来制造,但是也可以通过其他公知的方法来制造。本发明所涉及的石英玻璃坩埚由于使用了前述的原料二氧化硅粉,所以低失透、且适度地结晶化,维持了强度。这种石英玻璃坩埚用于硅单晶提拉、光学玻璃熔融,即使长时间在高温条件下使用,也能够抑制变形,特别是适合用于大口径的硅单晶提拉。以下,基于附图说明本发明所涉及的石英玻璃坩埚的另一个实施方式的一例。图7是本发明所涉及的石英玻璃坩埚1的剖视图。图8是图7的石英玻璃坩埚的局部放大剖视图。该石英玻璃坩埚1例如在单晶提拉装置(未图示)中使用,且以在装置中被碳基座(未图示)抱持的状态被使用。即,在单晶提拉装置中,被容纳在石英玻璃坩埚1内的多晶硅被熔融,并从硅熔融液提拉硅单晶。石英玻璃坩埚1例如被形成为直径810mm(32英寸),如图7所示,从坩埚上端6起向下方到规定距离为止的部分(以下,称为坩埚上端区域10)被构成为两层结构。即,所述坩埚上端区域10由不透明外层5a和透明内层4形成,该不透明外层5a由天然原料石英玻璃层构成,该透明内层4与该不透明外层5a的内侧邻接,并其包含在硅单晶提拉时与熔融硅接触的合成原料石英玻璃(或者天然原料石英玻璃)。此外,此处不透明是指在石英玻璃中,内部存在有很多气泡,在外观上为白色浑浊状态。另外,天然原料石英玻璃是指将水晶等天然材质原料熔融而制造的石英玻璃,合成原料石英玻璃例如是指将利用硅醇盐的水解所合成的合成原料熔融而制造的石英玻璃。另外,在比坩埚上端区域10更靠下方处,在侧部7以及以底部9与底部拐角8之间的曲率变化点为基准的规定范围中,设置有外层2,该外层2包含添加了结晶化促进剂的石英玻璃。在设置有该外层2的部分,构成由不透明中间层3以及所述透明内层4形成的三层结构,该不透明中间层3由从所述不透明外层5a连续形成的天然原料石英玻璃构成。而且坩埚底部9成为由不透明外层5b和透明内层4形成的两层结构,该不透明外层5b包含从所述不透明中间层3连续形成的天然原料石英玻璃,该透明内层4包含与不透明外层5b邻接的合成原料石英玻璃(或天然原料石英玻璃)。更详细地说明,如图8的剖视图所示,从坩埚上端6起向下方距离h为止的区域被形成为两层结构的坩埚上端区域10,所述距离h为5mm以上并且为将上端的壁厚t加上10mm而算出的长度以下。此处,所述上端的壁厚t一般是10mm以上且18mm以下,所述坩埚上端区域h一般被设置成从坩埚上端起向下方5mm以上且从上端起20mm以上且28mm以下。这是由于方石英的热膨胀远比石英玻璃的热膨胀大,所以拉伸应力作用在外表面,在所述两层结构的坩埚上端区域10为从坩埚上端6起向下方不到5mm的情况下,会从坩埚上端附近的外周侧产生裂纹,所以不优选。另外,在坩埚上端区域超过将坩埚上端的壁厚加上10mm而算出的长度的情况下,坩埚的上端区域会向会向坩埚内部变形(倾倒),所以不优选。该坩埚的上端区域向坩埚内部的变形是由于透明内层4的粘性低,对坩埚上端的口缘作用向内侧拉伸的力,另外不透明外层5a中含有气泡,所以不透明外层5a的膨胀比透明内层4的膨胀大,使坩埚的上端向坩埚内侧变形的力发生作用(向内侧倾倒的力发生作用)。另外,如图8所示,在坩埚内,底部9具有半径r的曲率(第一曲率),底部拐角8具有半径r的曲率(第二曲率)。另外,坩埚侧部7沿铅垂方向形成为直线状。此处,外层2从坩埚上端区域10的下端起向下方形成,并且外层2的下端被形成到以曲率变化点p为基准的规定范围内,该曲率变化点p为底部9(曲率半径r)和底部拐角8(曲率半径r)之间的曲率变化点。更具体地,外层2的下端被形成在以将半径r的曲率中心c与曲率变化点p连接的直线l上设为0°而使该直线l绕曲率中心c旋转±5°的范围内为止。这是由于,在将下方(底部方向)作为正方向的情况下,当将外层2的下端形成到比+5°大的范围时,结晶化(方石英化)会快速进行,难以得到期望的坩埚与碳基座的紧密贴合性,碳基座对坩埚的支撑变得不稳定,存在硅单晶化率下降的倾向。另一方面,当将外层2的下端形成在比-5°小的范围内时,外层2在坩埚整体所占的比例变小,存在耐热变形性降低的倾向。另外,如图9所示,外层2被形成为坩埚侧部7处的厚度尺寸et1和坩埚底部拐角8处的厚度尺寸et2都在0.5~5mm(优选为1~3mm)。这是由于当厚度比5mm大时,由于坩埚壁部层间的热膨胀差所引起的大的应力的产生,从而存在产生裂纹的可能,当厚度比0.5mm小时,存在耐热变形性低的倾向。另外,外层2的结晶化促进剂浓度例如设为35~100ppm(优选为50~80ppm)。这是由于,当结晶化促进剂浓度比100ppm高时,结晶化容易快速进行,在坩埚与碳基座的紧密贴合稳定前结晶化可能就会结束。另一方面,当结晶化促进剂浓度比35ppm低时,结晶化速度慢,难以得到期望的耐热变形性。另外,包含天然原料石英玻璃的不透明中间层3例如被形成为在坩埚侧部7处的厚度尺寸mt1为3mm以上,在坩埚底部拐角8处的厚度尺寸mt2为6mm以上。另外,坩埚上端区域10的不透明外层5a处的厚度尺寸mt4例如被形成为10mm以上且18mm以下,坩埚底部9的不透明外层5b处的厚度尺寸mt3例如被形成为6mm以上。这是由于,当三层部分处的不透明中间层3的厚度小于3mm时,容易减弱由于石英玻璃粉熔融中的电弧火焰的不规则流动而造成不透明中间层3的结晶化促进剂化合物飞散的防止效果,外层2的结晶化促进剂化合物会通过不透明中间层3混入透明内层4,透明内层4的结晶化促进剂浓度可能会变大。另外,坩埚上端区域10中的不透明外层5a的厚度尺寸mt4为10mm以上且18mm以下,以抑制从坩埚上端放热。另外,由于当坩埚底部拐角8处的不透明中间层3的厚度尺寸mt2以及坩埚底部9处的不透明外层5b的厚度尺寸mt3小于6mm时,难以得到充分的耐热变形性,所以不优选。另外,透明内层4是将na、k、al的金属杂质含量分别为1ppm以下的合成原料石英玻璃(或天然原料石英玻璃)熔融而形成的基本上不存在气泡的透明层。在透明内层4中,坩埚上端区域10以及坩埚侧部7处的厚度尺寸it1、坩埚底部拐角8处的厚度尺寸it2以及坩埚底部9处的厚度尺寸it3都被形成为3mm以上的厚度。这是由于,当透明内层4的厚度小于3mm时,难以将与硅熔体接触的透明内层4内表面的结晶化促进剂浓度抑制得足够低,例如成为1ppm以下。需要说明的是,在上述实施方式中,以包含添加有结晶化促进剂的石英玻璃的外层2以及不透明中间层3、透明内层4的三层结构的坩埚为例进行说明。但是,本发明并不限定于此,例如也可以是如下四层结构的坩埚,即从坩埚内侧起层叠透明内层4、不透明中间层3、由未添加结晶化促进剂的石英玻璃构成的第一外层,并在包含石英玻璃的第一外层的外侧层叠包含添加了结晶化促进剂的石英玻璃的第二外层。此时,第一外层形成到坩埚上端6为止,第二外层形成到从坩埚上端6起向下方5mm以上且将上端的壁厚加上10mm而算出的长度以下的区域为止。下面,对具有所述结构的石英玻璃坩埚1的制造方法进行说明。使用如图10所示的石英玻璃坩埚制造装置30来制作石英玻璃坩埚1。石英玻璃坩埚制造装置30的坩埚成形用模具11由内侧部件12和保持体14构成,该内侧部件12例如由穿设有多个贯通孔的模具或者进行高纯化处理后的多孔质碳模具等气体透过型部件构成,该保持体14在其外周设置有通气部13,并保持所述内侧部件12。另外,保持体14的下部固定有与未图示的旋转装置连结的旋转轴15,旋转轴15将坩埚成形用模具11支承为能够旋转。通气部13经由在保持体14的下部设置的开口部16与在旋转轴15的中央设置的排气路径17连结,该排气路径17与减压机构18连结。在与内侧部件12对置的上部设置有:电弧放电用的电弧电极19、添加了结晶化促进剂的石英玻璃的供给喷嘴20、天然原料石英玻璃供给喷嘴21以及合成原料石英玻璃供给喷嘴22。外层2所使用的添加了结晶化促进剂的石英玻璃粉以如下方式得到。例如在结晶化促进剂是al的情况下,将使石英玻璃粉的al浓度成为35~100ppm的量的al硝酸盐(al(no3)3)溶解在水中而制作al(no3)3水溶液,并将该水溶液添加到天然原料石英玻璃粉中并搅拌。被浸在al(no3)3水溶液中的石英玻璃粉以800~1100℃的条件被加热处理以脱水、除去酸性成分。在将mg、ca等作为结晶化促进剂的情况下,也同样将溶解有硝酸盐的水溶液添加到天然原料石英玻璃粉中,并搅拌、加热处理,从而得到。在添加al以及ca作为结晶化促进剂的情况下,优选添加了结晶化促进剂的石英玻璃中的al浓度为9wtppm以上且20wtppm以下,ca浓度为0.1wtppm以上且0.6wtppm以下,al与ca的摩尔浓度比(al/ca)为15≤al/ca≤200。通过添加所述结晶化促进剂,从而石英玻璃粉的粘性偏差变小,在得到的硅坩埚中,抑制了从坩埚的上端产生的裂纹、上端区域向内部的变形(倾倒)。在使用上述的石英玻璃坩埚制造装置30将这样得到的添加al的石英玻璃粉制作石英玻璃坩埚1的情况下,运行未图示的旋转驱动源,使旋转轴15向箭头的方向旋转,由此使坩埚成形用模具11高速地旋转。接着,从添加有结晶化促进剂的石英玻璃的供给喷嘴20向坩埚成形用模具11内供给以如上方式得到的添加al的石英玻璃粉。被供给的添加al的石英玻璃粉由于离心力而按压在内侧部件12的内表面侧,形成为外层2。此处,外层2如用图8说明的那样,确定上端和下端的位置,并除去多余的上部以及底部。接着,从天然原料石英玻璃供给喷嘴21供给天然原料石英玻璃粉,以形成不透明中间层3和不透明外层5a、5b,该不透明中间层3和不透明外层5a、5b在包含添加al的石英玻璃层的外层2的内表面侧处的厚度为3mm以上,在坩埚上端区域处的厚度为3mm以上,在底部拐角以及底部处的厚度为6mm以上。被供给的天然原料石英玻璃粉由于离心力而向外层2的内表面侧以及内侧部件12按压,成形为不透明中间层3和不透明外层5a、5b的成形体。接着,从合成原料石英玻璃供给喷嘴22供给na、k、al的金属杂质含量分别为1ppm以下的合成原料石英玻璃粉(或者天然原料石英玻璃粉),以在不透明中间层3和不透明外层5a、5b的内表面侧形成具有3mm以上厚度的透明层。被供给的合成原料石英玻璃粉由于离心力而向不透明中间层3以及不透明外层5a、5b的内表面侧按压,成形为透明内层4的成形体。如此,得到存在al浓度阶梯性减少的有浓度差的外层2、不透明中间层3、不透明外层5a、5b以及透明内层4的坩埚成形体。并且,利用减压机构18的工作,使内侧部件12内减压,将电弧电极19通电而从坩埚成形体的内侧加热,使坩埚成形体的透明内层4、不透明中间层3、不透明外层5a、5b以及外层2熔融,制造石英玻璃坩埚1。如以上,根据本实施方式,石英玻璃坩埚1的坩埚上端区域10是从坩埚上端起向下方5mm以上且将上端的壁厚加上10mm而算出的长度以下的区域,坩埚上端区域10被形成为由不透明外层5和透明内层4形成的两层结构,该不透明外层5包含天然原料石英玻璃,该透明内层4包含天然原料石英玻璃或合成原料石英玻璃。因此,能够在抑制从坩埚开口部(坩埚的上端部)产生的裂纹的同时,抑制坩埚的上端部区域向内侧的变形(倾倒)。而且,能够实现坩埚的耐久性的提升、单晶化率的提升,进一步,能够解决由于坩埚的上端区域向内侧变形(倾倒)而产生的硅单晶的结晶品质异常。此外,根据该石英玻璃坩埚1,在硅单晶提拉的开始初期阶段,不存在外层2的规定范围的底部9(不透明外层5b)会软化而与支撑石英玻璃坩埚1的碳基座紧密贴合,该外层2包含添加了结晶化促进剂的石英玻璃。之后,从提拉开始直到结束为止期间,由于高温加热,规定范围的底部拐角8以及侧部7等的外层进行结晶化(方石英化),石英玻璃坩埚1整体与支撑其的碳基座的紧密贴合稳定性提升。另外,由于结晶化而耐热变形性提升。因此,能够确保石英玻璃坩埚1的耐热变形性,同时得到基于碳基座的支撑的紧密贴合稳定性,能够使硅单晶的单晶化率提升。[实施例]以下,基于本发明的实施例进行具体说明,但是本发明并不被下述实施例限制。[例a]使用利用icp分析法分析的无机成分的含量如下的原料二氧化硅粉78批次(n=78):al浓度55~100wtppm、ca浓度1.2~9.5wtppm、na浓度6.9~18wtppm、k浓度2.1~13wtppm(图1a~图1d)。图2a~图2c表示基于图1a~图1d的结果的al/na摩尔浓度比分布(图2a)、al/k摩尔浓度比分布(图2b)以及al/ca摩尔浓度比分布(图2c)。图3a~图3c是基于图2c的结果的al浓度与al/ca的摩尔浓度比相关性(图3a),以及ca浓度与al/ca的摩尔浓度比相关性(图3b)和其放大图表(图3c)。例a的试料符合图1a~图1d、图2a~图2c、图3a~图3c的图表中的“无失透异常”。如图3a所示,点集中在al浓度55wtppm以上且100wtppm以下,al/ca摩尔浓度比在15以上的范围内。由该结果启示,当选择al浓度以及al/ca摩尔浓度比在所述范围内的原料二氧化硅粉时,能够制造低失透的石英玻璃坩埚。接着,选择所述原料二氧化硅粉中al/ca摩尔浓度比为42.34的原料二氧化硅粉,将该原料二氧化硅粉(al/ca摩尔浓度比=42.34)以规定的厚度装填在旋转的坩埚成形用模具内,并利用旋转成型法成形。接着,将电弧电极插入到坩埚成形用模具内,利用减压电弧熔融以约2000℃和不到一小时的条件玻璃化,从而制作厚度30mm、外径28英寸、高度665mm的石英玻璃坩埚。从石英玻璃坩埚切下45mm×30mm×20mm厚的试验片,在大气中以1500℃的温度进行100小时热处理,通过目视观察发生的点失透,来评价结晶化。如图6所示,虽然识别到几个点失透,但是整体是低失透的。需要说明的是,石英玻璃坩埚中的无机成分的含量是al浓度55~100wtppm、ca浓度1.2~9.5wtppm、na浓度6.9~18wtppm、k浓度2.1~13wtppm,与原料二氧化硅粉中的无机成分的含量相同。[例b]使用利用icp分析法分析的无机成分的含量如下的原料二氧化硅粉30批次(n=30):al浓度23~58wtppm、ca浓度3.9~38wtppm、na浓度7.5~39wtppm、k浓度5.2~22wtppm(图1a~图1d)。也就是说,在例b中,使用al/ca摩尔浓度比不到15的原料二氧化硅粉。图2a~图2c表示基于图1a~图1d的结果的al/na摩尔浓度比分布(图2a)、al/k摩尔浓度比(图2b)以及al/ca摩尔浓度比(图2c)。图3a~图3c表示基于图2c的结果的al浓度与al/ca的摩尔浓度比相关性(图3a),以及ca浓度与al/ca的摩尔浓度比相关性(图3b)和其放大图(图3c)。例b的试料符合图1a~图1d、图2a~图2c、图3a~图3c的图表中的“失透异常(抱怨)”。选择所述原料二氧化硅粉中的al/ca摩尔浓度比为7.43的原料二氧化硅粉,并与例a同样,制作石英玻璃坩埚。得到的石英玻璃坩埚中产生裂纹等导致的异常失透。接着,从所述石英玻璃坩埚切下45mm×30mm×20mm厚的试验片,在大气中以1500℃的温度进行100小时热处理,通过目视观察发生的点失透,来评价结晶化。按照图4所示,整体白色浑浊,可知产生了异常失透。[例c]使用利用icp分析法分析的无机成分的含量如下的原料二氧化硅粉26批次(n=26):al浓度110~130wtppm、ca浓度18~240wtppm、na浓度11~19wtppm、k浓度10~31wtppm(图1a~图1d)。即,在例c中使用ca浓度与al浓度相比异常高的原料二氧化硅粉。图2a~图2c表示基于图1a~图1d的结果的al/na摩尔浓度比分布(图2a)、al/k摩尔浓度比(图2b)以及al/ca摩尔浓度比(图2c)。图3a~图3c表示基于图2c的结果的al浓度与al/ca的摩尔浓度比相关性(图3a),以及ca浓度与al/ca的摩尔浓度比相关性(图3b)和其放大图表(图3c)。例c的试料符合图1a~图1d、图2a~图2c、图3a~图3c的图表中的“有失透异常”。选择所述原料二氧化硅粉中的al/ca摩尔浓度比为2.44的原料二氧化硅粉,并与例a同样,制作石英玻璃坩埚。得到的石英玻璃坩埚中产生裂纹等导致的异常失透。从所述石英玻璃坩埚切下45mm×30mm×20mm厚的试验片,在大气中以1500℃进行100小时热处理,通过目视观察发生的点失透,来评价结晶化。按照图5所示,整体白色浑浊,可知产生了异常失透。如图4和图5所示,对于发生了异常失透的石英玻璃坩埚中使用的原料中的al浓度、ca浓度或其他无机成分的化学分析值,虽然未确认共通的倾向,但是在al与碱金属元素(k、na、ca)的摩尔浓度比(图2a~图2c)方面,如图2c所示,确认了异常失透的原料的al/ca摩尔浓度比存在都不到15的倾向。因此,可以认为若选择al/ca摩尔浓度比在15以上的原料二氧化硅粉,则能够抑制二氧化硅坩埚的异常失透。而且,对al浓度或ca浓度与al/ca摩尔浓度比的相关性进行确认的结果,如图3a~图3c所示,可知只要使用al浓度为55~100wtppm(图3a)、ca浓度为1.2~9.5wtppm(图3b)的原料二氧化硅粉即可。接着,对本发明所涉及的石英玻璃坩埚,基于与上述实施方式不同的实施例进行进一步说明。在本实施例中,使用含有前述实施方式所示的结构的石英玻璃坩埚来进行硅单晶的提拉,并对得到的硅单晶的结晶化率(成品率)与使用的石英玻璃坩埚的开口部上端的变形量进行检验。(实验1)在实验1中,将所述实施方式中的坩埚上端区域10的形成区域作为条件,使用32英寸坩埚,并且制造石英玻璃坩埚,对制造的各石英玻璃坩埚进行单晶提拉。作为具体的条件,将成为两层结构的所述坩埚上端区域设定为从坩埚上端向下方到50mm为止的区域(例1-1)、到45mm为止的区域(例1-2)、到40mm为止的区域(例1-3)、到35mm为止的区域(例1-4)、到30mm为止的区域(例1-5)、到25mm为止的区域(例1-6)、到20mm为止的区域(例1-7)、到15mm为止的区域(例1-8)、到10mm为止的区域(例1-9)、到5mm为止的区域(例1-10)、到0mm为止的区域(例1-11)。此时所使用的石英玻璃坩埚的各层的厚度尺寸如下。参考图9进行表示,将透明内层4的厚度尺寸it1设为3mm,将厚度尺寸it2设为7mm,将厚度尺寸it3设为3mm。另外,不透明外层5a的厚度尺寸mt4为12mm,厚度尺寸mt2为17mm,厚度尺寸mt3为12mm。另外,外层2的厚度尺寸et1和厚度尺寸et2为1mm。另外,坩埚开口部上端的厚度尺寸it1和mt4之和t为15mm。另外,参考图8进行表示,底部9的曲率半径r(第一曲率)为813mm,底部拐角8的曲率半径r(第二曲率)为160mm。另外,外层2的下端形成在以将半径r的曲率中心c与曲率变化点p连接的直线l上作为0°而使该直线l绕曲率中心c旋转±5°的范围内。而且,外层2的结晶化促进剂浓度设定为50ppm。硅单晶的提拉条件如下。关于硅单晶的提拉,将原料的多晶硅块放入石英玻璃坩埚,并保持在非活性气体氛围、10torr~200torr的氩气氛围,用5小时~25小时从室温升温至提拉温度的1400℃~1550℃,并保持在该温度10小时将多晶硅块熔融,形成硅熔体。将籽晶(硅单晶)浸入该硅熔体(缩颈工序),一边使坩埚旋转一边缓缓提拉籽晶,以籽晶为核使硅单晶生长。对于实验1,表1示出例1-1~1-11中每个例的条件以及实验结果。此外,在表1中,变形量表示坩埚上端向内侧的倾倒量。另外,成品率表示单晶化率。而且,在备注中,将不能继续进行硅单晶提拉的情况表示为“不可”,将能够继续硅单晶提拉的情况表示为“容许”,将产生裂纹且不能继续进行硅单晶提拉的情况表示为“裂纹”。【表1】最外层上端位置(mm)变形量(mm)备注成品率(%)5034不可04525不可304019不可573515不可73308不可82254容许100202容许100150容许100100容许10050容许10000裂纹0由上述表1的结果能够确认,最外层的上端位置在5mm到25mm的范围,也就是说在从坩埚上端向下方5mm以上且将上端部的壁厚15mm加上10mm而算出的长度(25mm)以下的区域,能够抑制从坩埚开口部(坩埚的上端部)产生的裂纹,同时能够抑制坩埚的上端部向内部的变形(倾倒)。而且,能够实现坩埚的耐久性的提升、单晶化率的提升,进一步,能够解决由于坩埚的上端区域向内部变形(倾倒)而产生的硅单晶的结晶品质异常。(实验2)与实验1同样,使用22英寸坩埚,并制作石英玻璃坩埚,对制成的各坩埚进行单晶提拉。作为具体的条件,将成为两层结构的所述坩埚上端区域设定为从坩埚上端向下方到50mm为止的区域(例2-1)、到45mm为止的区域(例2-2)、到40mm为止的区域(例2-3)、到35mm为止的区域(例2-4)、到30mm为止的区域(例2-5)、到25mm为止的区域(例2-6)、到20mm为止的区域(例2-7)、到15mm为止的区域(例2-8)、到10mm为止的区域(例2-9)、到5mm为止的区域(例2-10)、到0mm为止的区域(例2-11)。此时所使用的石英玻璃坩埚的各层的厚度尺寸如下。参考图9进行表示,透明内层4的厚度尺寸it1为3mm,厚度尺寸it2为7mm,厚度尺寸it3为3mm。另外,不透明外层5a的厚度尺寸mt4为10mm,厚度尺寸mt2为16mm,厚度尺寸mt3为9mm。另外,外层2的厚度尺寸et1和厚度尺寸et2为1mm。另外,坩埚开口部上端的厚度尺寸it1和mt4之和t为13mm。另外,参考图8进行表示,底部9的曲率半径r(第一曲率)为813mm,底部拐角8的曲率半径r(第二曲率)为160mm。另外,外层2的下端形成在以将半径r的曲率中心c与曲率变化点p连接的直线l上作为0°而使该直线l绕曲率中心c°旋转±5的范围内。而且,外层2的结晶化促进剂浓度设定为50ppm。需要说明的是,硅单晶的提拉条件与实验1是相同条件。对于实验2,表2示出例2-1~2-11的每个例的条件以及实验结果。此外,在表2中,变形量表示坩埚上端向内部的倾倒量。另外,成品率表示单晶化率。而且,在备注中,将不能继续进行硅单晶提拉的情况表示为“不可”,将能够继续硅单晶提拉的情况表示为“容许”,将产生裂纹且不能继续进行硅单晶提拉的情况表示为“裂纹”。【表2】最外层上端位置(mm)变形量(mm)备注成品率(%)5023不可04518不可284015不可493512不可68309不可79257不可86204容许100152容许100100容许10050容许10000裂纹0由上述表2的结果能够确认,最外层的上端位置在5mm到20mm的范围,也就是说在从坩埚上端向下方5mm以上且将上端部的壁厚13mm加上10mm而算出的长度(23mm)以下的范围,能够抑制从坩埚开口部(坩埚的上端部)产生的裂纹,同时能够抑制坩埚的上端部向内部的变形(倾倒)。而且,能够实现坩埚的耐久性的提升、单晶化率的提升,进一步,能够解决由于坩埚的上端区域向内部变形(倾倒)而产生的结晶品质异常。由以上的实施例的实验结果能够确认,从坩埚上端向下方5mm以上且将上端部的壁厚加上10mm而算出的长度以下的区域,能够抑制从坩埚开口部(坩埚的上端部)产生的裂纹,同时能够抑制坩埚的上端部向内部的变形(倾倒)。(实验3)在将成为两层结构的坩埚上端区域设定为从坩埚上端向下方到10mm为止的区域的例1-9中,将外层2的结晶化促进剂浓度以及浓度比设定为表3所示的数值。表3示出实验3的结果。需要说明的是,在表3中,变形量表示坩埚上端向内部的倾倒量,成品率表示单晶化率。而且,在备注中,将能够继续硅单晶提拉的情况表示为“容许”,将产生裂纹且不能继续进行硅单晶提拉的情况表示为“不可”。【表3】1)不可的理由是过度失透所导致的裂纹2)不可的理由是结晶不充分所导致的变形。虽然详细且参照特定实施方式对本发明进行了说明,但本领域技术人员可以明了在不脱离本发明的精神和范围的情况下可以施加各种变更或修正。本申请基于2018年12月13日提出的日本专利申请2018-233607号、2018年12月27日提出的日本专利申请2018-244033号、2019年10月1日提出的日本专利申请2019-181105号以及2019年10月1日提出的日本专利申请2019-181106号,并将其内容作为参照而取入。当前第1页12