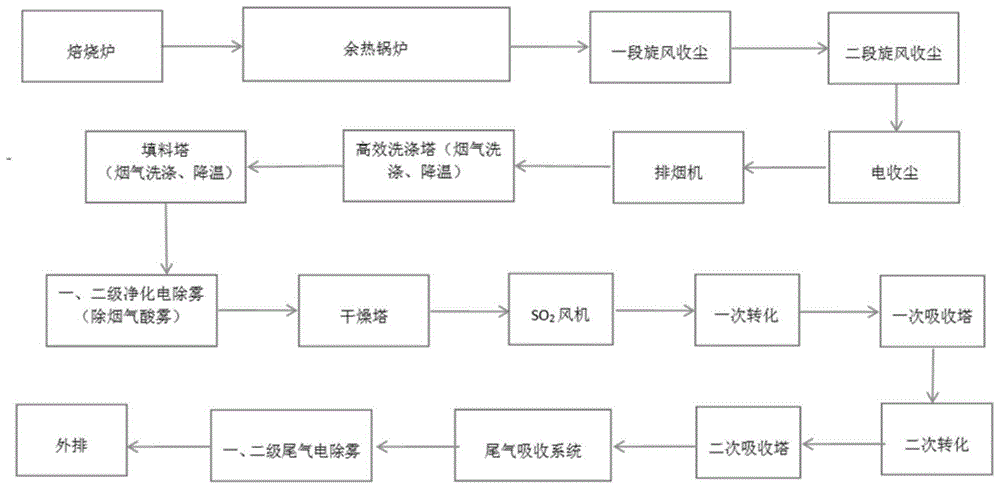
本发明属于冶炼烟气制酸技术领域,涉及冶炼烟气制酸技术领域的环保节能技术。具体涉及一种硫化锌精矿焙烧及其烟气制酸系统的开车方法。
背景技术:
目前,大型的锌冶炼企业大多采用成熟的湿法炼锌工艺进行炼锌,该工艺中首先将硫化锌精矿进行焙烧,焙烧产生的氧化锌焙砂经过稀硫酸浸出及电积等湿法炼锌工序产出电锌,焙烧产生的so2烟气经过余热锅炉降温、旋风收尘和电收尘设备除尘后送往制酸工序用于制造硫酸,如图1所示。在制酸工序中,来自焙烧工序的so2烟气经过净化、一次转化、一次吸收、二次转化、二次吸收制成硫酸,制酸尾气中残余的so2经尾气吸收系统处理后达标排放。
其中,烟气转化及吸收系统的工艺流程图如图2所示,烟气中的so2转化为so3的过程采用五段“3+2”双转化工艺、“iii.i一ⅴ.ⅳ.ⅱ”换热流程。该系统前期开车成功与否与烟气中so2处理是否达标具有密切的关系。现有技术中该系统在新建或大修后的系统开车过程中,因转化器催化剂层的温度过低,焙烧炉鼓风量、投料量、烟气so2浓度等指标与转化器催化剂层的温度不匹配,造成烟气中so2转化率低,制酸尾气中的so2含量超标,排放后对环境造成较大的危害,且其中so2的排放也造成资源浪费。
目前,主要通过对烟气so2转化系统的加热电炉进行项目改造、增大功率以提高催化剂层温度,从而实现so2转化率的提高,但是该方法在系统开车期间能源消耗量极大,大大提高了系统开车成本,在对尾气中so2降低的同时造成能源的极大消耗,经济效益差。
技术实现要素:
针对上述问题,本发明提供了一种硫化锌精矿焙烧及其烟气制酸系统的开车方法。该方法在不增加能源消耗的条件下使得系统开车能够保证制酸尾气的达标排放。既能够保证尾气的达标排放、避免对环境造成的影响、实现资源的回收利用,同时也没有增加任何的能源消耗,具有很好的经济效益。
本发明是通过以下技术方案实现的
一种硫化锌精矿焙烧及其烟气制酸系统的开车方法,该方法包括以下步骤:
(1)硫化锌精矿焙烧炉投料前3~10小时,检测烟气制酸系统处理烟气的尾气吸收液体,其中双氧水浓度≥1.50%,稀酸浓度≤10.0%时开始投料;
(2)烟气制酸系中转化器一段催化剂温度达到420℃及以上,转化器二段催化剂温度达到420℃及以上,转化器四段催化剂温度405℃及以上,转化器三段催化剂温度达到410℃时开车完成。
所述的硫化锌精矿焙烧及其烟气制酸系统的开车方法,该方法包括以下步骤:
(1)硫化锌精矿焙烧炉投料前3~10小时,检测烟气制酸系统处理烟气的尾气吸收液体,其中双氧水浓度≥1.50%,稀酸浓度≤10.0%时开始投料;
(2)当步骤(1)烟气制酸系统中尾气吸收系统的吸收液达到要求后,打开第一电炉对转化器一段进行加热,加热至催化剂420℃后,开始向焙烧炉内投料,投料时焙烧炉内鼓风量由20000m3/h逐渐上升至30000m3/h,同时逐渐增加焙烧炉内的投料量,且保持转化器一段(催化剂层)入口烟气中的so2体积浓度<4.0%;随着焙烧炉内硫化锌焙烧的进行,当转化器二段催化剂温度上升至420℃时,将焙烧炉内的鼓风量由30000m3/h上升至40000m3/h,同时逐渐增加焙烧炉内的投料量,且保持转化器一段(催化剂层)入口烟气中so2的体积浓度为4.0~6.0%;随着焙烧炉内硫化锌精矿焙烧的进行,当转化器四段催化剂温度达到405℃时,焙烧炉内鼓风量由40000m3/h逐渐上升至45000m3/h,同时逐渐增加焙烧炉内的投料量,且保持转化器一段(催化剂层)入口处烟气so2的体积浓度为6.0~7.0%;随着焙烧炉内硫化锌精矿焙烧的进行,当转化器三段催化剂层温度达到410℃时,开车成功。
所述的硫化锌精矿焙烧及其烟气制酸系统的开车方法,步骤(1)对烟气制酸系统处理烟气的尾气吸收系统的液体进行检测时每小时检测一次。
所述的硫化锌精矿焙烧及其烟气制酸系统的开车方法,步骤(2)中焙烧炉内的鼓风量为20000m3/h时,向焙烧炉内的投料量为7.0±0.5t/h;焙烧炉内的鼓风量为30000m3/h时,向焙烧炉内的投料量为15.0±0.5t/h;焙烧炉内的鼓风量为40000m3/h时,向焙烧炉内的投料量为23.0±0.5t/h;焙烧炉内的鼓风量为45000m3/h时,向焙烧炉内的投料量为27.0±0.5t/h。
所述的硫化锌精矿焙烧及其烟气制酸系统的开车方法,所述的烟气制酸系统包与焙烧炉烟气出口相连通的烟气净化装置(湿式除尘器),与烟气净化装置相连通的干燥塔,与干燥塔相连通的so2风机,与so2风机相连通的ⅲ换热器(的壳程),与ⅲ换热器(的壳程)相连通的ⅰ换热器(的壳程),与ⅰ换热器(的壳程)相连通的第一电炉,与第一电炉相连通的转化器一段,与转化器一段相连通的ⅰ换热器(的管程),与ⅰ换热器(的管程)相连通的转化器二段,与转化器二段相连通的ⅱ换热器(的管程),与ⅱ换热器(的管程)相连通的转化器三段,与转化器三段相连通的ⅲ换热器(的管程),与ⅲ换热器(的管程)相连通的第一吸收塔;第一吸收塔同时与相并联的ⅴ换热器(的壳程)及ⅳ换热器(的壳程)相连通,ⅴ换热器(的壳程)及ⅳ换热器(的壳程)同时与ⅱ换热器(的壳程)相连通,ⅱ换热器(的壳程)与第二电炉相连通,第二电炉与转化器四段相连通,转化器四段与ⅳ换热器(的管程)相连通,ⅳ换热器(的管程)与转化器五段相连通,转化器五段与ⅴ换热器(的管程)相连通,ⅴ换热器(的管程)与第二吸收塔相连通,第二吸收塔与尾气吸收系统相连通,尾气吸收系统与尾气一级电除雾器相连通,尾气一级电除雾器(除去尾气中的硫酸雾滴)与尾气二级电除雾器(除去尾气中的硫酸雾滴)相连通,尾气二级电除雾器与尾气烟囱相连通,由尾气烟囱外排;
所述干燥塔还与93%成品酸库相连通(93%的浓硫酸通过在干燥塔内与烟气的逆向接触,除去其中的水分。);
所述第一吸收塔及第二吸收塔均还与98%成品酸库相连通(98%的浓硫酸通过在吸收塔内与烟气的逆向接触,吸收其中的so3,转化为硫酸。)。
所述的烟气制酸系统为本领域技术人员熟知的系统,其中的换热器为本领域技术人员熟知的换热器。换热器包括换热器壳程与换热器管程,热气进入换热器管程中对经过换热器壳程中的气体进行加热,同时换热器管程中的热气得到降温。
与现有技术相比,本发明具有以下积极有益效果
现有技术中对于硫化锌精矿焙烧及对其产生的尾气进行处理的制酸系统开车时,对于尾气的处理结果不理想,排放的尾气难以达标,对环境造成污染同时也造成其中资源的浪费。而为了提高处理效果耗费大量能源,提高了尾气处理成本,回收资源的同时造成能源高消耗。而本申请则在不增加投资、电耗、能源消耗的条件下,确保了尾气制酸系统在新建或大修后的开车过程中能够较好的处理尾气,使其排放的尾气完全达标,既保证了尾气可以达标排放、又对其中的资源进行了高效回收,环境友好且在该领域具有很好的经济效益。
在方法该开车过程中,通过焙烧炉鼓风量、投料量、催化剂温度及so2浓度的精准对应,保证了烟气制酸系统中尾气的达标排放,且没有任何的能源消耗的增加,解决了该领域中高能耗处理尾气达标的技术缺陷,具有较高的应用前景。
附图说明
图1为硫化锌精矿焙烧及其烟气制酸系统的工艺流程图,
图2为烟气制酸(烟气转化及吸收)系统的工艺流程图。
具体实施方式
下面通过具体实施方式对本发明进行更加详细的说明,以对本发明技术方案进行解释,但并不用于对本发明保护范围的限制。
本发明提供了一种硫化锌精矿焙烧及其烟气制酸系统的开车方法,该方法包括以下步骤:
s1,在焙烧炉内投料前3小时(一般为投料前3~10小时),对烟气制酸系统中的尾气吸收系统的吸收液进行检测,每小时检测一次,保证其中双氧水质量浓度≥1.50%,稀硫酸质量浓度≤10.0%。且整个开车期间保持此状态,直到系统达到正常生产的工艺条件;
s2,当烟气制酸系统中尾气吸收系统的吸收液达到要求后,打开第一电炉对转化器一段催化剂进行加热,加热至420℃后,开始向焙烧炉内投料,投料时焙烧炉内鼓风量由20000m3/h逐渐上升至30000m3/h,并逐渐增加焙烧炉内的投料量,且保持转化器一段(催化剂层)入口烟气中的so2体积浓度<4.0%。
其中该过程中,焙烧炉内部的投料量及鼓风量对应如表1所示
表1转化器一段温度与焙烧炉内部的投料量及鼓风量控制
随着焙烧炉内硫化锌焙烧的进行,当转化器二段催化剂温度上升至420℃时,将焙烧炉内的鼓风量由30000m3/h上升至40000m3/h,并逐渐增加焙烧炉内的投料量,且保持转化器一段催化剂层入口烟气中so2的体积浓度为4.0~6.0%,
该过程中,焙烧炉内鼓风量及投料量对应如表2所示:
表2转化器二段温度与焙烧炉内部的投料量及鼓风量控制
随着焙烧炉内硫化锌精矿焙烧的进行,当转化器四段催化剂温度达到405℃时,焙烧炉内鼓风量由40000m3/h逐渐上升至45000m3/h,并逐渐增加焙烧炉内的投料量,且保持转化器一段催化剂入口处烟气so2的体积浓度为6.0~7.0%,
该过程中,焙烧炉内鼓风量及投料量对应如表3所示:
表3转化器三段温度与焙烧炉内部的投料量及鼓风量控制
随着焙烧炉内硫化锌精矿焙烧的进行,当转化器三段催化剂层温度达到410℃时,开车成功。
如图2所示,上述的烟气制酸系统为本领域技术人员熟知的烟气制酸系统,其中由焙烧炉烟气出口出来的烟气进入烟气净化装置(湿式除尘器),由烟气净化装置净化后进入干燥塔(烟气进入干燥塔中,与塔内93%的硫酸逆向接触,除去其中的水分。)内进行干燥(干燥至水分含量为0.05g/m3以下),经过干燥塔干燥后的烟气经过so2风机进入到ⅲ换热器的壳程中进行换热升温,由ⅲ换热器的壳程进入到ⅰ换热器的壳程中进行换热升温,然后经过第一电炉进入转化器一段进行催化氧化(将烟气中的so2催化氧化为so3),经过转化器一段催化氧化后的气体进入到ⅰ换热器的管程中进行降温(在降温的同时也对ⅰ换热器的壳程中的烟气进行了加热),降温后进入到转化器二段进行催化氧化,经过转化器二段催化氧化后的烟气进入到ⅱ换热器的管程中进行降温,降温后进入到转化器三段进行催化氧化,经过转化器三段催化氧化后的烟气进入到ⅲ换热器的管程中进行降温(经过转化器三段催化氧化后,烟气中约95%的so2转化为了so3),降温后进入到第一吸收塔中,在第一吸收塔中与98%浓硫酸逆向接触,so3被浓硫酸吸收,其中含有剩余so2的烟气从第一吸收塔塔顶出来同时进入到ⅴ换热器的壳程及ⅳ换热器的壳程中进行换热升温,然后再进入ⅱ换热器的壳程中并经过第二电炉升温,然后进入到转化器四段进行二次转化,总转化率达到99.5%以上,然后进入到ⅳ换热器的管程中进行换热降温,降温后进入到转化器五段进行催化氧化,经过转化器五段催化氧化后进入ⅴ换热器的管程进行降温,降温后进入到第二吸收塔,在第二吸收塔中与98%浓硫酸逆向接触,so3被吸收,剩余烟气进入尾气吸收系统中进行再次吸收(吸收其中剩余的微量未被前期处理的so2气体),然后经过尾气一级电除雾器及尾气二级电除雾器除去尾气中的硫酸雾滴,然后由尾气烟囱外排,此时排出的烟气完全达标,对于环境没有影响,且其中的so2被回收为再利用资源,具有双重效果。
该过程中,其中的换热器壳程中热源均来自于对应的转化器中的热气,使得热源进行循环利用,达到节能降耗的效果;转化器一段反应产生的热气进入到ⅰ换热器管程中对经过其壳程中的烟气进行加热(同时本身得到降温),转化器二段中反应产生的的热气进入到ⅱ换热器管程中用于对经过其壳程中的烟气进行加热,转化器三段中反应产生的热气进入到ⅲ换热器管程中用于对经过其壳程中的烟气进行加热,转化器四段中反应产生的热气进入到ⅳ换热器管程中用于对经过其壳程中的烟气进行加热,转化器五段中反应产生的热气进入到ⅴ换热器管程中对经过其壳程中的烟气进行加热。
本发明所述焙烧炉精炼硫化锌精矿为本领域熟知的焙烧炉。
下面通过具体实施例对本发明进行说明。
实施例1
(1)在焙烧炉内投料前3小时,对烟气制酸系统中的尾气吸收系统的吸收液进行检测,每小时检测一次,保证其中双氧水质量浓度≥1.50%,稀硫酸质量浓度≤10.0%。且整个开车期间保持此状态,直到系统达到正常生产的工艺条件;
(2)当烟气制酸系统中尾气吸收系统的吸收液达到要求后,打开第一电炉对转化器一段催化剂进行加热,加热至420℃后,开始向焙烧炉内投料,投料时焙烧炉内鼓风量由20000m3/h逐渐上升至30000m3/h,并逐渐增加焙烧炉内的投料量,且保持转化器一段(催化剂层)入口烟气中的so2体积浓度<4.0%。其中焙烧炉内部的投料量、鼓风量、转化器一段催化剂温度及转化器一段(催化剂层)入口so2浓度对应如表4所示,
表4焙烧炉投料量、鼓风量、转化器一段温度及对应so2浓度
(3)随着焙烧炉内硫化锌焙烧的进行,当转化器二段催化剂温度上升至420℃后,将焙烧炉内的鼓风量由30000m3/h上升至40000m3/h,并逐渐增加焙烧炉内的投料量,且保持转化器一段催化剂层入口烟气中so2的体积浓度为4.0~6.0%。其中焙烧炉内部的投料量、鼓风量、转化器二段催化剂温度及转化器一段(催化剂层)入口so2浓度对应如表5所示,
表5焙烧炉投料量、鼓风量、转化器二段温度及对应so2浓度
(4)随着焙烧炉内硫化锌精矿焙烧的进行,当转化器四段催化剂温度达到405℃时,焙烧炉内鼓风量由40000m3/h逐渐上升至45000m3/h,并逐渐增加焙烧炉内的投料量,且保持转化器一段(催化剂层)入口处烟气so2的体积浓度为6.0~7.0%。其中焙烧炉内部的投料量、鼓风量、转化器四段催化剂温度及转化器一段(催化剂层)入口so2浓度对应如表6所示,
表6焙烧炉投料量、鼓风量、转化器四段温度及对应so2浓度
(5)随着焙烧炉内硫化锌精矿焙烧的进行,当转化器三段催化剂层温度达到410℃后开车成功,转入正常生产。
该开车法在整个开车过程中控制制酸尾气的so2含量﹤20mg/m3,远优于国家排放标准,并且该过程中没有额外能源、电耗等的消耗。在没有增加额外消耗的条件下达到了硫化锌精矿焙烧烟气的达标排放。