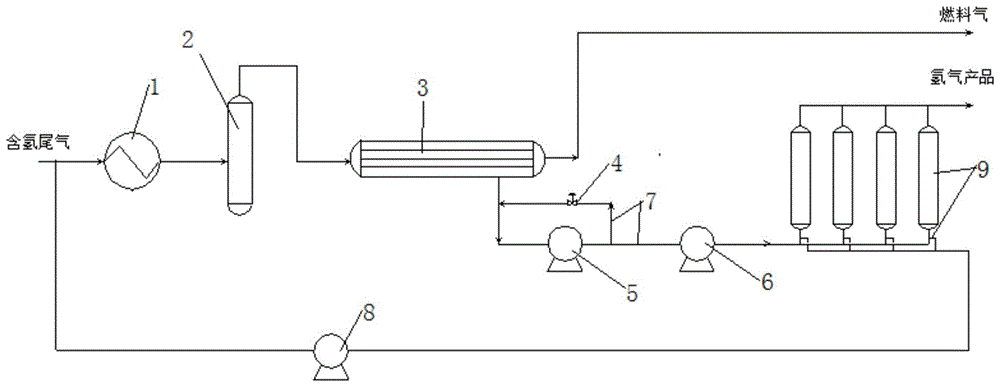
本发明属于化工氢气提取领域,尤其涉及一种从含氢燃料气中提纯回收氢气的装置及方法及应用。
背景技术:
:燃料气在工业上主要有天然气体燃料和人工气体燃料两大类,它们是清洁能源、优质能源,与人们的生活息息相关。所有气体燃料都是多种成分混合而成,其中可燃成分有氢、一氧化碳、甲烷、硫化氢以及各种碳氢化合物。不可燃气体主要有二氧化碳、氮气和水蒸气等。天然的有沼气、天然气、液化气等。经过加工而成的有由固体燃料经干馏或气化而成的焦炉气、水煤气、发生炉煤气等;石油加工而得的石油气,以及由炼铁过程中所产生的高炉气等。氢气是新型能源和石油化工中的一种重要资源,目前从含氢混合气、燃料气中分离回收氢气的技术主要有变压吸附法、膜分离法。在吸附平衡情况下,温度越低,压力越高,吸附量越大。反之,温度越高,压力越低,则吸附量越小。因此,气体的吸附分离方法,通常采用变温吸附或变压吸附两种循环过程。如果温度不变,在加压的情况下吸附,用减压(抽真空)或常压解吸的方法,称为变压吸附。变压吸附法的吸附分离是利用吸附剂对特定气体吸附和解吸能力上的差异进行分离。不同气体的吸附容量、吸附力、吸附速度随压力的不同而有差异,在吸附剂选择吸附的条件下,加压吸附混合物中的易吸附组分,当吸附床减压时,解吸这些吸附组分,从而使吸附剂再生。变压吸附法再生速度快、能耗低、操作简单、工艺成熟稳定。最大优点是可以得到产品纯度很高(99.99%)的氢气,氢气回收率在85%~90%左右,杂质含量少。但是对于氢气含量较低,压力较低的含氢燃料气,直接采用变压吸附装置分离,变压吸附吸附负荷高,投资高和占地面积大。气体膜分离技术是新一代气体分离技术,其原理是在压力驱动下,借助气体中各组分在高分子膜表面上的吸附能力以及在膜内溶解-扩散上的差异,即渗透速率差来进行分离,渗透推动力是膜两侧的分压差。膜分离技术具有工艺简单、操作弹性大、费用低等优点。但膜分离回收氢气的纯度不高,并且要求原料气有比较高的压力,对于原料气特别敏感,尤其是怕原料气带液。含氢燃料气体当压力为0.2mpa~1.0mpa,氢气含量20%~50%时,对这类气体进行提纯氢气,存在着由于氢气在膜表面的渗透推动力较小,从而膜分离效率较低、膜材料的用量大和投资成本高等技术问题。或者采用对含氢原料气进行压缩增压在1.0~3.0mpa下的方式来进行膜分离,获得高回收率的氢气,但又存在着压缩机贵,加压能耗高的技术问题。炼厂干气中轻烃和氢气有较高的利用价值,但其通常都被送入瓦斯管网用作燃料气,有些甚至放入火炬燃烧掉,造成了资源的极大浪费。炼厂干气主要来自原油的二次加工过程,如重油催化裂化、热裂化、延迟焦化等,其中催化裂化(fcc)产生的干气量较大,一般占原油加工量的4%~5%。fcc干气的主要成分是氢气(占25%~40%)和乙烯(占10%~20%),延迟焦化干气的主要成分是甲烷和乙烷。技术实现要素:为了解决以上技术问题,本发明提供一种从含氢燃料气中提纯回收氢气的装置及方法及应用,采用膜和变压吸附耦合氢燃料气中提纯回收氢气,克服了常规膜分离法在原料氢气含量较低的情况下需压缩增压在较高压力下操作和不能获得高纯度氢气的限制,能获得99.9%~99.999%纯氢或者高纯氢气产品。解决以上技术问题的本发明中的一种从含氢燃料气中提纯回收氢气的装置,其特征在于:包括设有冷干机、过滤器、解气压缩机、膜分离器,真空泵,压力调节阀、富氢气压缩机、回流管线和变压吸附提纯氢气装置,冷干机与过滤器相连,过滤器与膜分离器相连,膜分离器与真空泵相连,真空泵与富氢气压缩机相连,压力调节阀一端设在膜分离器和真空泵之间,另一端设在真空泵与富氢气压缩机之间,膜分离器,真空泵和压力调节阀通过回流管线连接;富氢气压缩机与变压吸附提纯氢气装置相连,变压吸附提纯氢气装置与解气压缩机相连,解气压缩机另一端与冷干机连接;氢气产品通过变压吸附提纯氢气装置输出,剩余燃料气经过膜分离器输出;所有结构通过管线连接。所述膜分离器设有包括膜的膜组合件,所述膜设有渗余侧和渗透侧,渗透侧与真空泵相连,透过氢气;渗余侧一端与过滤器连接,另一端与燃料气装置连接,从而输出剩余燃料气。原料进气和出口相连的是渗余侧,渗透侧是透过氢气的另一侧。所述渗余侧压力0.2~1.0mpa。所述渗透侧压力为负压,为-0.04~-0.09mpa。优选方案中,所述渗透侧压力为-0.081~-0.085mpa。所述过滤器与冷干机之间设有加热器,加热器一端与过滤器连接,一端与冷干机连接。本发明中一种从含氢燃料气中提纯回收氢气的方法,其特征在于:包括以下步骤:(1)含氢燃料气进入冷干机脱除烃类组分、水等液态物质;(2)经过滤器脱除气体中的微量固体颗粒杂质;(3)进入膜分离器、真空泵、回流管线和压力调节阀提纯氢气,膜渗透侧的氢气经抽空后获得粗氢气产品,膜渗余侧的气体排出膜分离器,作为剩余燃料气输出;膜分离器中膜的渗透侧连接的将渗透侧压力降低并稳定至较低压力,剩余燃料气进入工厂燃料气管网作为燃料使用;(4)所述步骤(3)中粗氢气进入富氢气压缩机和变压吸附提纯氢气装置,再次提纯;一部份气体作为氢气产品输出;经抽空系统获得的氢气产品增压后再经变压吸附提纯氢气装置进一步提纯获得纯氢或者高纯氢气产品。(5)所述步骤(4)中另一部份少量气体经过解吸气压缩机,与含氢燃料气混合,循环使用。采用抽空系统对膜分离装置的渗透侧进行抽空时,采用将部分真空系统出口的氢气返流回膜装置的渗透侧,以保证渗透侧压力稳定。所述含氢燃料气压力为0.2mpa~1.0mpa,氢气含量20%~40%的炼油厂的含氢燃料气等其他含氢气体。所述步骤(1)步骤(2)之间还有加热步骤,加热后气体温度20℃~80℃,炼油厂含氢燃料气进入膜分离装置前先加热。所述步骤(2)中冷干温度2~10℃,压力值0.2mpa~1.0mpa。本发明一种从含氢燃料气中提纯回收氢气的装置,应用于对压力0.2mpa~1.0mpa,氢气含量20%~40%的燃料气中氢气的提纯。本发明所述装置应用于从炼厂干气中提纯氢气,压力0.2mpa~1.0mpa,氢气含量20%~40%的炼厂干气。本发明采用真空系统降低膜分离装置氢气渗透侧的压力,提高了氢气在膜两侧氢气的分压差,提高了氢气在膜表面的渗透推动力,与现有不对膜分离单元氢气渗透侧进行抽空降压的膜分离装置比较,氢气在膜表面的渗透效率可以提高15%~40%,可以明显降低膜分离装置的能耗和运行成本,采用膜装置的富氢渗透气加压后作为变压吸附装置的原料,优化了变压吸附的操作条件,显著降低变压吸附提氢气装置的投资和占地。经抽空后获得的氢气产品增压后再经变压吸附装置进一步提纯获得纯氢或者高纯氢气产品。又增加解吸气压缩机与变压吸附提纯氢气装置连接,使整体装置形成一个循环系统,增加回收分离效果,且又成本低操作简单。本发明氢气在膜表面的渗透效率可提高15%~40%,明显降低膜分离装置的能耗和运行成本,配合变压吸附提纯氢气装置能获得99.9%~99.999%的氢气产品。附图说明下面结合附图及具体实施方式对本发明做更进一步详细说明,所用设备仪器为常规设备和仪器,其中冷干机、过滤器、膜分离器、真空泵、压力调节阀、加热器、富氢气压缩机、解吸气压缩机、变压吸附提氢气装置等均为本
技术领域:
中常规通用设备,从市场上可以购买:图1和图2为本发明中装置结构示意图图3为本发明中部份工艺流程图其中,图中标识具体为:1.冷干机,2.过滤器,3.膜分离器(3-1.渗余侧,3-2.渗透侧),4.压力调节阀,5.真空泵,6.富氢气压缩机,7.回流管线,8.解吸气压缩机,9.变压吸附提氢气装置,10.加热器具体实施方式实施例1一种从含氢燃料气中提纯回收氢气的装置,设有冷干机、过滤器、解气压缩机、膜分离器,真空泵,压力调节阀、富氢气压缩机、回流管线和变压吸附提纯氢气装置,冷干机与过滤器相连,过滤器与膜分离器相连,膜分离器与真空泵相连,真空泵与富氢气压缩机相连,压力调节阀一端设在膜分离器和真空泵之间,另一端设在真空泵与富氢气压缩机之间,膜分离器,真空泵和压力调节阀通过回流管线连接;富氢气压缩机与变压吸附提纯氢气装置相连,变压吸附提纯氢气装置与解气压缩机相连,解气压缩机另一端与冷干机连接;氢气产品通过变压吸附提纯氢气装置输出,剩余燃料气经过膜分离器输出;所有结构通过管线连接。膜分离器设有包括膜的膜组合件,所述膜设有渗余侧和渗透侧,渗透侧与真空泵相连,透过氢气;渗余侧一端与过滤器连接,另一端与燃料气装置连接,从而输出剩余燃料气。原料进气和出口相连的是渗余侧,渗透侧是透过氢气的另一侧。真空泵的连接位点是在富氢气的渗透侧。渗余侧压力0.5mpa,渗透侧压力为负压,为-0.06mpa。膜分离器设有膜组合件,其形状为圆筒状,中又设有分离膜,为中空纤维膜。中空纤维膜外形像纤维状,具有自支撑作用的膜,是以聚砜、二甲基乙酰胺为原料加工成中空内腔的纤维丝,再除以高渗透性聚合物,具有选择性渗透特性。由于水蒸气、氢、氨和二氧化碳渗透较快,而甲烷、氮、氩、氧和一氧化碳等渗透较慢,这样就使渗透快的与渗透慢的分离。与高分子膜更容易透过相对分子质量小的不可冷凝气体如氢气有着区别。利用两侧之气体压力差和混合气体中燃料气和氢气透过速度之差,选择性的透过氢气,从而达到分离之效果。氢气由真空泵输送。使氢气从燃料气中有选择性的分离出来,使氢气回收提高。实施例2一种从含氢燃料气中提纯回收氢气的装置,设有冷干机、过滤器、加热器、解气压缩机、膜分离器,真空泵,压力调节阀、富氢气压缩机、回流管线和变压吸附提纯氢气装置,冷干机与过滤器相连,过滤器与膜分离器相连,加热器一端与过滤器连接,一端与冷干机连接,膜分离器与真空泵相连,真空泵与富氢气压缩机相连,压力调节阀一端设在膜分离器和真空泵之间,另一端设在真空泵与富氢气压缩机之间,膜分离器,真空泵和压力调节阀通过回流管线连接;富氢气压缩机与变压吸附提纯氢气装置相连,变压吸附提纯氢气装置与解气压缩机相连,解气压缩机另一端与冷干机连接;氢气产品通过变压吸附提纯氢气装置输出,剩余燃料气经过膜分离器输出;所有结构通过管线连接。膜分离器设有包括膜的膜组合件,所述膜设有渗余侧和渗透侧,渗透侧与真空泵相连,透过氢气;渗余侧一端与过滤器连接,另一端与燃料气装置连接,从而输出剩余燃料气。原料进气和出口相连的是渗余侧,渗透侧是透过氢气的另一侧。真空泵的连接位点是在富氢气的渗透侧。渗余侧压力0.2或1.0mpa,渗透侧压力为负压,为-0.04或-0.09mpa。实施例3一种从含氢燃料气中提纯回收氢气的装置,设有冷干机、过滤器、加热器、解气压缩机、膜分离器,真空泵,压力调节阀、富氢气压缩机、回流管线和变压吸附提纯氢气装置,冷干机与过滤器相连,过滤器与膜分离器相连,加热器一端与膜分离器连接,一端与冷干机连接,膜分离器与真空泵相连,真空泵与富氢气压缩机相连,压力调节阀一端设在膜分离器和真空泵之间,另一端设在真空泵与富氢气压缩机之间,膜分离器,真空泵和压力调节阀通过回流管线连接;富氢气压缩机与变压吸附提纯氢气装置相连,变压吸附提纯氢气装置与解气压缩机相连,解气压缩机另一端与冷干机连接;氢气产品通过变压吸附提纯氢气装置输出,剩余燃料气经过膜分离器输出;所有结构通过管线连接。膜分离器设有包括膜的膜组合件,所述膜设有渗余侧和渗透侧,渗透侧与真空泵相连,透过氢气;渗余侧一端与过滤器连接,另一端与燃料气装置连接,从而输出剩余燃料气。原料进气和出口相连的是渗余侧,渗透侧是透过氢气的另一侧。真空泵的连接位点是在富氢气的渗透侧。渗余侧压力0.8mpa,渗透侧压力为负压,-0.081或-0.085mpa,或-0.083mpa。实施例4原料气组成组成h2ch4c2h6c3h8c4c5+v%501712.59.542将组成含量如上表的炼油厂重整变压吸附提氢解吸气在0.5mpa、~40℃条件下进入冷干机脱除如烃类组分、水等液态物质,进入过滤器脱除其中的微量固体颗粒杂质后,进入有膜分离器、真空泵、回流管线和压力调节阀组成的小循环结构提纯氢气,膜的渗透侧连接的真空泵、回流管线和压力调节阀将渗透侧压力降低并稳定到-0.085mpa,富氢渗透气经真空泵抽出(除少部分返回膜单元稳定压力外)获得富氢气(粗氢气产品)经压缩机加压至2.6mpa进入变压吸附提纯氢气装置获得99.999%的高纯氢气,变压吸附提纯氢气装置的含氢解吸气经压缩机增压到0.55mpa返回于重整变压吸附提氢解吸气混合作为膜分离装置的原料,未通过膜的渗余气排出装置进入工厂燃料气管网作为燃料气,见图1。冷干机中冷干温度2~10℃,压力值0.2mpa~1.0mpa。粗氢气产品进入富氢气压缩机和变压吸附提纯氢气装置,再次提纯;一部份气体作为氢气产品输出;经抽空系统获得的氢气产品增压后再经变压吸附提纯氢气装置进一步提纯获得纯氢或者高纯氢气产品。一部份气体从变压吸附提纯氢气装置出来后经过解吸气压缩机,与含氢燃料气混合,循环使用。本实施例中,氢气的纯度为99.999%、氢气收率为95%。实施例5原料气组成组成h2n2ch4c2h4c2h6c3h8c4c5+v%26.314.227.315.612.70.820.62.48将组成含量如上表的炼油厂催化裂化干气在0.7mpa、~40℃条件下进入冷干机脱除如烃类组分、水等液态物质,进入过滤器脱除其中的微量固体颗粒杂质后,进入有膜件、真空泵、回流管线和压力调节阀组成的真空膜分离装置提纯氢气,膜的渗透侧连接的真空泵、回流管线和压力调节阀将渗透侧压力降低并稳定到-0.081mpa,富氢渗透气经真空泵抽出(除少部分返回膜单元稳定压力外)获得的富氢气经压缩机加压至2.0mpa进入变压吸附提纯氢气装置,获得99.9%的氢气产品输出装置,未通过膜的渗余气和变压吸附提纯氢气的解吸气排出装置进入工厂燃料气管网作为燃料气。本实施例中,氢气的纯度为99.9%、氢气收率为82%。实施例6原料气组成组成h2c1c2c3c4c5c6c7+v%25.712.1352.10.771.912.621.802.97将组成含量如上表的焦化干气在0.3mpa、~30℃条件下进入冷干机脱除如烃类组分、水等液态物质,进入过滤器脱除其中的微量固体颗粒杂质后,进入有膜件、真空泵、回流管线和压力调节阀组成的真空膜分离装置浓缩氢气,膜的渗透侧连接的真空泵、回流管线和压力调节阀将渗透侧压力降低并稳定到-0.09mpa,富氢渗透气经真空泵抽出(除少部分返回膜单元稳定压力外)获得富氢气经压缩机加压至2.5mpa进入变压吸附提纯氢气装置获得99.9%氢气产品,变压吸附提纯氢气装置的解吸气和未通过膜的渗余气排出装置进入工厂燃料气管网作为燃料气。本实施例中,氢气的纯度为99.9%、氢气收率为70%。本发明中将压力0.2mpa~1.0mpa的炼油厂含氢燃料气引入真空膜分离装置,采用抽空系统对膜分离装置的渗透侧进行抽空,并保持渗透侧压力为负压,从抽空系统的出口获得粗氢气,分离氢后的渗余气作为燃料气体排出膜分离装置。实施例7一种从含氢燃料气中提纯回收氢气的方法,包括以下步骤:(1)含氢燃料气进入冷干机脱除烃类组分、水等液态物质;冷干温度2~10℃,含氢燃料气压力为0.2mpa~1.0mpa,氢气含量20%~40%的炼油厂的含氢燃料气等其他含氢气体。(2)进入加热器中加热,加热后气体温度20℃或80℃或60℃,炼油厂含氢燃料气进入过滤和膜分离装置前先加热。(3)经过滤器脱除气体中的微量固体颗粒杂质;(4)进入膜分离器、真空泵、回流管线和压力调节阀提纯氢气,膜渗透侧的氢气经抽空后获得粗氢气产品,膜渗余侧的气体排出膜分离器,作为剩余燃料气输出;膜分离器中膜的渗透侧连接的将渗透侧压力降低并稳定至较低压力,剩余燃料气进入工厂燃料气管网作为燃料使用;(5)所述步骤(3)中粗氢气产品进入富氢气压缩机和变压吸附提纯氢气装置,再次提纯;一部份气体作为氢气产品输出;经抽空系统获得的氢气产品增压后再经变压吸附提纯氢气装置进一步提纯获得纯氢或者高纯氢气产品。(6)所述步骤(4)中另一部份少量气体经过解吸气压缩机,与含氢燃料气混合,循环使用。采用抽空系统对膜分离装置的渗透侧进行抽空时,采用将部分真空系统出口的氢气返流回膜装置的渗透侧,以保证渗透侧压力稳定。本发明中含氢燃料气进入冷干机脱除烃类组分、水等液态物质,再经过滤器脱除气体中的微量固体颗粒杂质后,又经膜分离器、真空泵、回流管线和压力调节阀分离氢气,膜的渗透侧连接的真空泵、回流管线和压力调节阀将渗透侧压力降低并稳定至较低压力,由于真空系统降低了渗透侧的压力,明显提高了作为氢气渗透推动力的膜两侧的分压差,提高了膜装置中氢气的渗透效率,与未在渗透侧进行抽空降压的现有膜分离回收氢气装置比较,可以减少膜的用量降低成本,增加氢气的产量提高经济效益。渗透侧的富氢气经抽空系统获得,富氢气经压缩机加压后进入变压吸附装置进一步提纯获得99.9%~99.999%纯氢或者高纯氢气产品,渗余侧的气体进入工厂燃料气管网作为燃料使用;部份气体又经过解吸气压缩机后,与含氢燃料气混合,一起再进入冷干机中进行下一次氢气分离回收。整体结构形成循环回收分离系统,结构设计简单,回收分离效果好,成本低。以上显示和描述了本发明的基本原理和主要特征以及本发明的优点,上述实施例和说明书所描述的只是说明本发明的原理,在不脱离本发明精神和范围的前提下,本发明还会有各种变化和改进,这些变化和改进都将落入要求保护的本发明范围内。本发明要求保护的范围由所附的权利要求书及其等效物界定。当前第1页12