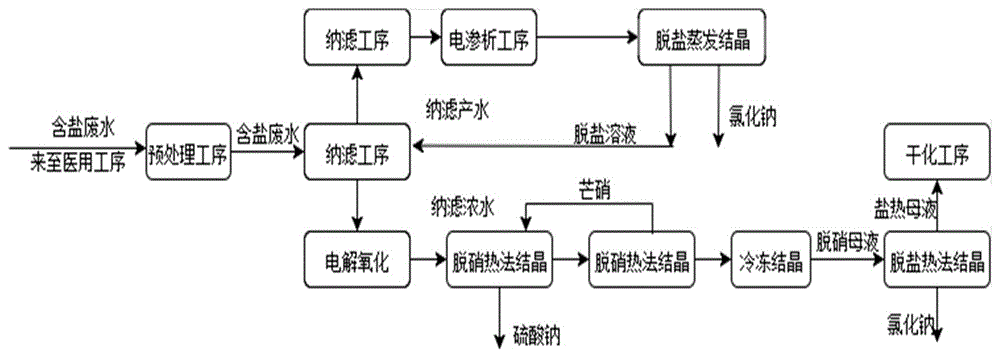
本发明涉及混盐碳化后分离
技术领域:
,特别涉及一种含有机物氯化钠、硫酸钠混盐碳化后分离方法。
背景技术:
:如图1所示,现有的浓盐废水中氯化钠和硫酸钠分离浓缩淘洗工艺及系统,主要包括氯化钠分离浓缩工艺段、硫酸钠淘洗分离浓缩工艺段和回用水收集系统;浓盐水除硬后进入一级分盐装置,一级分盐装置的产水浓缩后选择进行脱cod、脱硅、脱碳或降浊处理,再进入二级分盐装置,产水蒸发结晶制备氯化钠;二级分盐装置的浓水与部分回用水按比例混合后进入一级淘洗装置,产生的浓水与一级分盐装置的浓水混合后选择脱cod或降浊处理,再与回用水按比例。但浓盐废水中氯化钠和硫酸钠分离浓缩淘洗工艺及系统,缺陷如下:1、终点有还有少量混盐产生,无法彻底分离;2、有机物无法完全去除,收集盐的质量无法完全稳定;3、蒸发一次浓缩比例小(30~40%)成本高;4、热能利用率低等缺点。煤化工高盐废水中中分离提取硫酸钠、氯化钠,首先通过纳滤工序实现两种盐初步分离;然后通过电解氧化技术去除溶液中cod;在采用热法结晶和冷冻技术得到产品;具体如图1所示:但煤化工高盐废水中中分离提取硫酸钠、氯化钠,首先通过纳滤工序实现两种盐初步分离,电解氧化技术缺点:1、运行成本高电解用电能耗大;电解氧化过程安全要求等级高,操作风险大;3、投资成本高。另外mvr或多效蒸发器直接浓缩分离技术,主要是利用硫酸钠与氯化钠不同溶解度进行浓缩分盐。但直接浓缩技术缺点实:1、无法彻底进行分盐;2、有机物无法去除;3、产品盐为危废固体。技术实现要素:为了克服上述缺陷,本发明提供了一种含有机物氯化钠、硫酸钠混盐碳化后分离方法,使得碳化后污盐中硫酸钠与氯化钠一次处理达到符合国家标准工业盐且无新固废产生;废水零排放;解决能源费用高问题以及设备建设复杂问题。本发明为了解决其技术问题所采用的技术方案是:一种含有机物氯化钠、硫酸钠混盐碳化后分离方法,包括以下步骤:1)首先将碳化后的污盐加入溶解用水进行溶解,溶解后进行过滤得到混盐溶液;2)过滤后的混盐溶液采用冷冻结晶方式,在冷冻结晶器中冷冻,将硫酸钠结晶析出;析出硫酸钠结晶后的溶液采用离心过滤得到硫酸钠结晶,再用硫酸钠作为洗涤水进行二次提纯,对硫酸钠晶体进行洗涤,去除晶体夹带溶液中的氯化钠;3)经过离心过滤后的冷冻液一部分进入冷冻液收集池,一部分作为蒸发浓缩后冷冻结晶器的冷却水使用,使用后返回收集池;4)冷冻液收集池的冷却液经步骤3)中冷冻结晶器的返回的冷却液循环升温后,进入蒸发浓缩器中,浓缩过程产生冷凝水进入冷凝水收集槽,作为步骤1)中溶盐使用用水,当溶液体积浓缩至原体积的1/4时,开始进入氯化钠冷冻结晶器,进行冷却析出氯化钠晶体;5)氯化钠经离心甩干及洗涤后进入产品包装,结晶母液返回步骤1)循环处理。作为本发明的进一步改进,步骤1)中的溶解用水采用浓缩产生的冷凝水与氯化钠结晶母液。作为本发明的进一步改进,在步骤2)在冷冻结晶器中冷冻至-3~-5℃。作为本发明的进一步改进,所述步骤2)中硫酸钠的浓度为1%。作为本发明的进一步改进,在步骤1)中加入naoh调节溶液ph在8.5~9.0之间,保证在蒸发结晶过程易结垢物质生成沉淀,进入溶解过滤分离后固定碳中,碱性溶液无论在冷冻结晶还是蒸发结晶过程中对设备的腐蚀性对酸性好很多,实现对设备的保护。本发明的有益效果是:相比现有的分离技术,本发明具有以下优点:1、针对食品厂、农药厂生产过程产生的含有机物的硫酸钠、氯化钠污盐碳化后分盐技术;2、在氯化钠、硫酸钠溶解度范围内,配制不同浓度的溶液混盐,应用范围广;3、加入naoh调整ph值,实现易结垢物质的去除,延长蒸发器腔体生产周期,降低生产成本;4、不产生任何废水,实现废水零排放;5、不产生二次固废,完全实现此类污盐无害化处理;6、能源合理利用,可降低生产成本约30%左右(主要指冷冻离心硫酸钠后冷冻液作为冷却水使用及氯化钠离心母液返回溶盐处理,实现热源利用。)附图说明图1为现有技术示意图;图2为本发明流程示意图;具体实施方式为了加深对本发明的理解,下面将结合实施例和附图对本发明作进一步详述,该实施例仅用于解释本发明,并不构成对本发明保护范围的限定。图2出示了本发明一种含有机物氯化钠的一种实施方式,硫酸钠混盐碳化后分离方法,其特征在于:包括以下步骤:1)首先将碳化后的污盐加入溶解用水进行溶解,溶解后进行过滤得到混盐溶液;2)过滤后的混盐溶液采用冷冻结晶方式,在冷冻结晶器中冷冻,将硫酸钠结晶析出;析出硫酸钠结晶后的溶液采用离心过滤得到硫酸钠结晶,再用硫酸钠作为洗涤水进行二次提纯,对硫酸钠晶体进行洗涤,去除晶体夹带溶液中的氯化钠;3)经过离心过滤后的冷冻液一部分进入冷冻液收集池,一部分作为蒸发浓缩后冷冻结晶器的冷却水使用,使用后返回收集池;4)冷冻液收集池的冷却液经步骤3)中冷冻结晶器的返回的冷却液循环升温后,进入蒸发浓缩器中,浓缩过程产生冷凝水进入冷凝水收集槽,作为步骤1)中溶盐使用用水,当溶液体积浓缩至原体积的1/4时,开始进入氯化钠冷冻结晶器,进行冷却析出氯化钠晶体;5)氯化钠经离心甩干及洗涤后进入产品包装,结晶母液返回步骤1)循环处理。步骤1)中的溶解用水采用浓缩产生的冷凝水与氯化钠结晶母液。在步骤2)在冷冻结晶器中冷冻至-3~-5℃。所述步骤2)中硫酸钠的浓度为1%。在步骤1)中加入naoh调节溶液ph在8.5~9.0之间。实施例一:某食品厂产生的废盐经碳化后,氯化钠含量:94.15%、硫酸钠:2.85%、碳化物:2.94%、其余物质:0.06%。首先配制氯化钠浓度150g/l,硫酸钠溶度4.54g/l,5m³,耗碱2.3kg搅拌20分钟后过滤分离后在1.5m³反应釜内冷冻至-4.5℃,未见有晶体析出,冷却液经二次过滤后进入3m³冷冻液收集池待用。将冷冻液转入1.5m³蒸发浓缩釜采用蒸汽加热(负压),浓缩至剩余体积约为400l时开始有晶体出现,浓缩过程产生的冷凝水转入5m³贮槽进行收集。当釜内剩余250l左右时,转入1m³冷却反应釜中用后续冷冻液进行冷却降温,当温度将至38℃时,进行离心甩干分离氯化钠盐。离心母液此时返回溶盐工序配制。当配制液循环三周期后,在冷冻结晶环节产生并收集硫酸钠固体,且离心甩干硫酸钠晶体后液用于冷却液过程中无晶体产生,无堵塞管道现象。产品十水硫酸钠(则无酸硫酸钠)检测结果如下:项目指标硫酸钠(naso4)质量分数%97.5%钙镁(以mg计)含量质量分数%0.3氯化钠(以cl计)0.8水分(%)1.4%产品氯化钠检测结果:项目指标氯化钠(%)97.9水分(%)0.6水不溶物(%)0.1钙镁离子总量(%)0.6硫酸根离子(%)0.8案例二某食品厂产生的废盐经碳化后,氯化钠含量:35.5%、硫酸钠:57.01%、碳化物:2.44%、其余物质:0.05%。首先配制氯化钠浓度143g/l,硫酸钠溶度230g/l,4m³,耗碱1.8kg搅拌30分钟后过滤分离后在1.5m³反应釜内冷冻至-5℃,硫酸钠晶体析出,冷却液经二次过滤后进入3m³冷冻液收集池待用。将冷冻液转入1.5m³蒸发浓缩釜采用蒸汽加热(负压),浓缩至剩余体积约为350l时开始有晶体出现,浓缩过程产生的冷凝水转入5m³贮槽进行收集。当釜内剩余260l左右时,转入1m³冷却反应釜中用后续冷冻液进行冷却降温,当温度将至40℃时,进行离心甩干分离氯化钠盐。离心母液此时返回溶盐工序配制。离心甩干硫酸钠晶体后液用于冷却液过程中无晶体产生,无堵塞管道现象。产品十水硫酸钠(则无酸硫酸钠)检测结果如下:项目指标硫酸钠(naso4)质量分数%97.3%钙镁(以mg计)含量质量分数%0.35氯化钠(以cl计)0.85水分(%)1.5%产品氯化钠检测结果:项目指标氯化钠(%)98.5水分(%)0.5水不溶物(%)0.1钙镁离子总量(%)0.1硫酸根离子(%)0.8案例三某食品厂产生的废盐经碳化后,氯化钠含量:15.5%、硫酸钠:82.01%、碳化物:2.44%、其余物质:0.05%。首先配制氯化钠浓度49.14g/l,硫酸钠溶度260.3g/l,4m³,耗碱2.05kg搅拌25分钟后过滤分离后在1.5m³反应釜内冷冻至-3.5℃,硫酸钠晶体析出,冷却液经二次过滤后进入3m³冷冻液收集池待用,前三批冷冻液直接返回配制溶解液。将冷冻液转入1.5m³蒸发浓缩釜采用蒸汽加热(负压),浓缩至剩余体积约为380l时开始有晶体出现,浓缩过程产生的冷凝水转入5m³贮槽进行收集。当釜内剩余230l左右时,转入1m³冷却反应釜中用后续冷冻液进行冷却降温,当温度将至40℃时,进行离心甩干分离氯化钠盐。离心母液此时返回溶盐工序配制。离心甩干硫酸钠晶体后液用于冷却液过程中无晶体产生,无堵塞管道现象。产品十水硫酸钠(则无酸硫酸钠)检测结果如下:项目指标硫酸钠(naso4)质量分数%97.8%钙镁(以mg计)含量质量分数%0.4氯化钠(以cl计)0.8水分(%)1.0%产品氯化钠检测结果:项目指标氯化钠(%)98.2水分(%)0.8水不溶物(%)0.12钙镁离子总量(%)0.4硫酸根离子(%)0.48当前第1页12