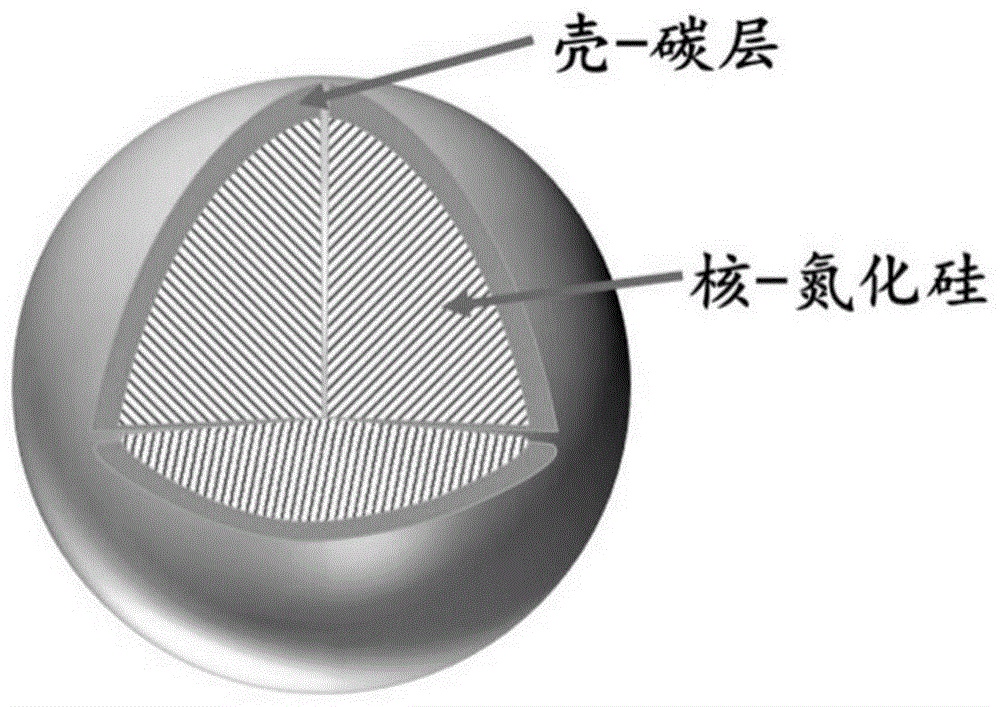
本发明属陶瓷
技术领域:
,更具体地,涉及一种用碳包覆制备低氧含量、高热导的氮化硅陶瓷的方法及其应用。
背景技术:
:随着科学技术的快速发展,电子元件设计趋于小型化、大功率、集成化等。尺寸缩小,功率增大则意味着电子元件内部将发热严重,需要及时依靠陶瓷基板向外部散热,才能有效维持电子元件的性能和寿命。性能优异的陶瓷基板材料除了拥有高热导率,还需具备良好的抗弯强度和断裂韧性等。氮化硅陶瓷具有高硬度、高强度、抗热振性能优异等特点,是综合性能最好的结构陶瓷材料。此外,研究发现氮化硅陶瓷材料理论热导率可达200~320w/(m·k)。因此氮化硅陶瓷是目前先进陶瓷基板的最优候选材料。目前市面上常见的陶瓷基板材料主要为氧化铍、三氧化铝和氮化铝。氧化铍陶瓷基板具备高热导,但氧化铍粉末有剧毒,难以推广应用;三氧化铝陶瓷基板机械强度高、化学稳定性高,但热导率低并且热膨胀系数高,在反复温度循环中易产生内应力,大大增加失效的概率,难以满足先进陶瓷基板材料的使用要求;氮化铝陶瓷基板具备高热导率,但是机械性能不佳,将严重影响陶瓷基板材料的可靠性。与其他陶瓷材料相比,作为综合性能最优的结构陶瓷材料,氮化硅具有明显优势,尤其是高温条件下氮化硅陶瓷材料表现出的耐高温性能、对金属的化学惰性、超高的硬度和断裂韧性等力学性能。研究表明,氮化硅陶瓷具有高的理论热导率,但由于缺陷、杂质、显微结构以及制备工艺等条件的影响,在实验制备氮化硅陶瓷过程中,氮化硅陶瓷热导率并不理想,远低于理论值。研究者对氮化硅陶瓷热导的前期理论研究发现,晶格氧是影响氮化硅陶瓷热导率最重要的因素。根据缺陷方程,sio2→sisi+2oc+vsi,氧原子溶于氮化硅晶格会产生硅空隙(vsi),硅空隙将作为声子散射中心,增加声子传导阻力,大幅降低氮化硅陶瓷热导率。氮化硅粉末表面常被氧化,生成二氧化硅,而二氧化硅中氧原子在氮化硅液相烧结过程中会不可避免融入氮化硅晶格,形成硅空隙,对声子产生散射作用。因此,设法降低氮化硅粉末氧含量,是提高氮化硅陶瓷热导率最有效的方法。技术实现要素:为了解决上述现有技术中存在的不足之处,本发明的目的在于提供一种用碳包覆制备低氧含量、高热导的氮化硅陶瓷的方法。该通过碳包覆氮化硅粉末,在烧结过程中控制温度使氮化硅表面包覆的碳层还原二氧化硅,降低氮化硅粉末整体氧含量,进而提高氮化硅陶瓷的热导率。本发明的另一目的在于提供一种方法上述方法制得的低氧含量、高热导的氮化硅陶瓷。本发明的目的通过下述技术方案来实现:一种用碳包覆制备低氧含量、高热导的氮化硅陶瓷的方法,包括如下具体步骤:s1.在去离子水中加入缓冲液tris-hcl,调节溶液ph值至8~11,将氮化硅粉末和盐酸多巴胺混合搅拌后,干燥过滤,得到聚多巴胺包覆的氮化硅粉末;s2.将聚多巴胺包覆的氮化硅粉末与烧结助剂混合,获得混合粉末;s3.将混合粉末置于石墨模具,在真空气氛下加热至600~800℃碳化,使聚多巴胺高温热解碳化,形成核壳结构的碳-氮化硅粉末;s4.然后加以20~30mpa轴向压力,在保护气氛下,加热至1200~1500℃,使碳-氮化硅粉末中的碳层与氮化硅表面的二氧化硅发生还原反应;将轴向压力升高至30~50mpa,再升温至1600~2000℃烧结,得到低氧含量、高热导的氮化硅陶瓷。优选地,聚多巴胺包覆的氮化硅粉末的具体步骤如下:取1l去离子水,加入1~2g缓冲液(tris-hcl),使用naoh调节溶液ph值至8~11,依次加入10~20g氮化硅粉末,0.1~2g盐酸多巴胺(多巴胺无法直接获得,需通过盐酸多巴胺发生化学反应而获得),搅拌12~48h,使多巴胺发生聚合反应生成聚多巴胺,干燥过滤即可得到聚多巴胺包覆的氮化硅粉末。优选地,步骤s1中所述盐酸多巴胺的纯度为97%以上。优选地,步骤s1中所述的盐酸多巴胺与氮化硅粉末的质量比为(0.01~0.1):1。通过机械球磨工艺将预处理后的氮化硅粉末与烧结助剂混合均匀,优选地,球磨机为行星式球磨机或滚筒式球磨机。优选地,步骤s2中所述的烧结助剂为y2o3、sc2o3、sm2o3、lu2o3、er2o3、mgo、mg2si、mgsin2中的一种以上。优选地,步骤s2中所述的聚多巴胺包覆的氮化硅粉末和烧结助剂的质量比(89~97):(3~21);更为优选地,(94~97):(3~6)。优选地,步骤s1中所述的氮化硅粉末的粒径为0.5~3μm,纯度为99%以上,α-si3n4含量大于90%;步骤s2中所述烧结助剂的粒径为0.3~3μm,纯度为99%以上。优选地,步骤s3中所述碳化的时间为1~4h。优选地,步骤s4中所述的低氧含量、高热导的氮化硅陶瓷的相对密度为95~100%。优选地,步骤s4中所述保护气氛为氮气或氩气。优选地,步骤s4中所述升温速率均为1~30℃/min,所述还原反应的时间为4~7h;所述烧结的时间为4~6h。优选地,所述烧结为热压烧结、气压烧结、常压保护气氛烧结或微波加热烧结。一种低氧含量、高热导的氮化硅陶瓷,所述氮化硅陶瓷是由所述的方法制得。本发明以氮化硅粉末为原料,对氮化硅粉末进行预处理,实施碳包覆。碳包覆所使用的碳源为多巴胺,多巴胺可在任何物质表面聚合成聚多巴胺膜,并牢固黏附于该物质表面。基于上述原理,利用多巴胺作为碳源,在氮化硅表面聚合生成聚多巴胺,可以生成聚多巴胺包覆的氮化硅粉末,最后将聚多巴胺碳化得到碳包覆的氮化硅粉末。本发明的原理如下:通常氮化硅粉末表面有二氧化硅的氧化层,而二氧化硅中氧原子在氮化硅液相烧结过程中会不可避免融入氮化硅晶格,形成硅空隙,对声子产生散射作用,导致氮化硅具有低的热导率。本发明通过在氮化硅粉末表面包覆碳源,利用高温热解将碳源碳化,形成核壳结构碳-氮化硅粉末。然后通过控制温度,使碳层与氮化硅表面二氧化硅发生下列化学反应,有利于还原氮化硅表面的二氧化硅,降低粉末氧含量,从而降低氮化硅晶格氧含量,减小声子散射几率,提高氮化硅陶瓷的热导率。其原理如式(1)-(4)所示:3sio2(s)+2n2(g)+6c(s)=si3n4(s)+6co(g)式(1)sio2(s)+c(g)=sio(g)+co(g)式(2)sio2(s)+co(g)=sio(g)+co2(g)式(3)3sio(g)+2n2(g)+3co(g)=si3n4(s)+3co2(g)式(4)本发明人通过研究发现,在保证氮化硅陶瓷致密度的前提下,降低氮化硅粉末和烧结助剂中氧含量,是提高氮化硅陶瓷热导率的关键因素。因此,本发明人首次提出,通过碳包覆氮化硅粉末的方法,可精确控制碳层分布和精准调节碳层结构。在材料制备过程中辅以合适的温度,使碳层充分还原氮化硅表面二氧化硅,降低氮化硅粉末整体氧含量,从而减少氮化硅中晶格氧杂质,进一步降低硅空隙对声子的散射作用,最终实现提高氮化硅陶瓷热导率的目的。与现有技术相比,本发明具有以下有益效果:1.本发明通过碳包覆氮化硅粉末的方法,可精确控制碳层分布和精准调节碳层结构,可有效还原氮化硅表面二氧化硅,降低氮化硅粉末氧含量,缓和氮化硅晶格中声子散射作用,提高氮化硅陶瓷热导率。且所制备的氮化硅陶瓷致密度高于98.5%,例如可达99.6%,并具有高热导率,其热导率可达80w/(m·k)以上,例如85w/(m·k)。在材料制备过程中辅以合适的温度,使碳层充分还原氮化硅表面二氧化硅,降低氮化硅粉末整体氧含量,从而减少氮化硅中晶格氧杂质,进一步降低硅空隙对声子的散射作用,最终实现提高氮化硅陶瓷热导率的目的。2.本发明的方法可调节碳层形貌,而现有的其他技术主要通过机械球磨或其他混合方法将碳源混合进氮化硅粉末,碳源分布存在明显的随机性,且碳层形貌无法调控,导致最终的还原效果有限,氮化硅粉末氧含量降低效果不明显,热导率提升的不理想。附图说明图1为本发明的碳包覆氮化硅粉末核壳结构示意图。具体实施方式下面结合具体实施例进一步说明本发明的内容,但不应理解为对本发明的限制。若未特别指明,实施例中所用的技术手段为本领域技术人员所熟知的常规手段。除非特别说明,本发明采用的试剂、方法和设备为本
技术领域:
常规试剂、方法和设备。本发明实施例中所述的氮化硅粉末的粒径为0.5~3μm,纯度为99%以上,α-si3n4含量大于90%(商用氮化硅粉末常包含α-si3n4和β-si3n4两种结晶结构);步骤s2中所述烧结助剂的粒径范围为0.3~3μm,纯度为99%以上。实施例11.制备:(1)取1l去离子水,加入1g缓冲液(tris-hcl),使用naoh调节溶液ph值至9,依次加入20g氮化硅粉末,1g盐酸多巴胺,搅拌24h后,干燥过滤,得到聚多巴胺包覆的氮化硅粉末;(2)称量18g聚多巴胺包覆的氮化硅粉末,加入3wt.%y2o3作为烧结助剂,进行球磨混料,转速为200转/min,球磨时间2h;将过筛后的混合粉末16g置于石墨模具,在600℃,真空度为5pa条件下保温4h;在n2气氛下,轴向压力保持20mpa,升温至1400℃,保温4h;在n2气氛下,轴向压力升高至50mpa,升温至1750℃;保温5h;最后随炉冷却至室温,制得低氧含量、高热导的氮化硅陶瓷。2.性能测试:采用阿基米德排水法,测试试样密度。采用激光脉冲(lfa447,netzschinstrumentsco.ltd,selb,germany)测试,试样尺寸长宽高分别为10mm×10mm×2mm。氮化硅晶格氧含量:取1g烧结后的氮化硅陶瓷,加入50ml甲醇,用碳化钨球磨10min;500目过筛,置于60℃干燥12h;取干燥后的氮化硅粉末置于水浴加热60℃的hf(60%)中浸泡3h,然后再置于水浴加热120℃的h2so4(50%)中浸泡12h;酸处理后,用去离子水清洗3遍,置于110℃条件下,干燥12h,100目过筛;最后使用气体热萃取分析仪测试氮化硅晶格氧含量(modeltc-436,lecoco.,stjoseph,mi)。所得氮化硅的致密度可达99.4%,晶格氧含量为0.085wt.%,热导率可达76w/(m·k)。图1为本发明的碳包覆氮化硅粉末核壳结构示意图。从图1中可知碳包覆氮化硅粉末为核壳结构,内层是氮化硅粉末,外层为聚多巴胺碳化后形成的包覆碳层。实施例2与实施例1不同之处在于:制备多巴胺溶液中盐酸多巴胺含量由1g升高至2g。1.取1l去离子水,加入1g缓冲液(tris-hcl),使用naoh调节溶液ph值至9,依次加入20g氮化硅粉末,2g盐酸多巴胺,搅拌24h后,干燥过滤即可得到聚多巴胺包覆的氮化硅粉末;2.称量18g聚多巴胺包覆的氮化硅粉末,加入3wt.%y2o3作为烧结助剂,进行球磨混料,转速为200转/min,球磨2h;将过筛后的混合粉末16g置于石墨模具,在600℃,真空度为5pa条件下保温4h;在n2气氛条件下,轴向压力保持20mpa,升温至1400℃,保温4h;在n2气氛条件下,轴向压力升高至50mpa,升温至1750℃;保温5h;最后随炉冷却至室温,制得低氧含量、高热导的氮化硅。由以上制备的氮化硅致密度可达99.6%,晶格氧含量为0.064wt.%,热导率可达85w/(m·k)。与实施例1相比,随着盐酸多巴胺含量升高,所包覆聚多巴胺层厚增加,最终碳化后形成的碳层厚度也随之增加。对比例1与实施例1不同之处在于:将碳源(淀粉)与氮化硅粉末、烧结助剂球磨混料,未进行包覆。取20g氮化硅粉末加入3wt.%y2o3作为烧结助剂,1wt.%淀粉,进行球磨混料,转速为200转/min,球磨2h;将过筛后的混合粉末16g置于石墨模具,在600℃,真空度为5pa条件下保温4h;在n2气氛条件下,轴向压力保持20mpa,升高温度至1400℃,保温4h;在n2气氛条件下,轴向压力升高至50mpa,温度升高至1750℃;保温5h;最后随炉冷却至室温,制得氮化硅。所得氮化硅的致密度可达99.9%,晶格氧含量为0.187wt.%,热导率可达64w/(m·k)。对比例2与实施例1不同之处在于:未加入碳源。取20g氮化硅粉末加入3wt.%y2o3作为烧结助剂,进行球磨混料,转速为200转/min,球磨时间2h;将过筛后的混合粉末16g置于石墨模具,在n2气氛条件下,轴向压力升高至50mpa,升温至1750℃;保温5h;最后随炉冷却至室温,制得氮化硅。所得氮化硅的致密度可达99.2%,晶格氧含量为0.406wt.%,热导率可达53w/(m·k)。表1为实施例与对比例所制备的氮化硅陶瓷的性能参数碳引入形式氮化硅晶格氧含量致密度热导率实施例1碳包覆0.085wt.%99.4%76w/(m·k)实施例2碳包覆0.064wt.%99.6%85w/(m·k)对比例1球磨混入0.187wt.%99.9%64w/(m·k)对比例2未引入碳层0.406wt.%99.2%53w/(m·k)表1为实施例1-2与对比例1-2所制备的氮化硅陶瓷的性能参数。从表1中可知:(1)引入碳源(例如:球磨混入和碳包覆),通过碳还原氮化硅表面二氧化硅层,可降低氮化硅晶格氧含量,提高氮化硅陶瓷热导率;(2)与球磨混入碳源的方法相比,碳包覆方法可精确控制碳源分布,具有更好的还原效果,氮化硅晶格氧含量降低更明显,制备的氮化硅陶瓷热导率更高;(3)通过调控碳层包覆厚度,可精确控制还原效果,进一步降低氮化硅晶格氧含量,提高氮化硅陶瓷热导率。上述实施例为本发明较佳的实施方式,但本发明的实施方式并不受上述实施例的限制,其他的任何未背离本发明的精神实质与原理下所作的改变、修饰、替代、组合和简化,均应为等效的置换方式,都包含在本发明的保护范围之内。当前第1页12