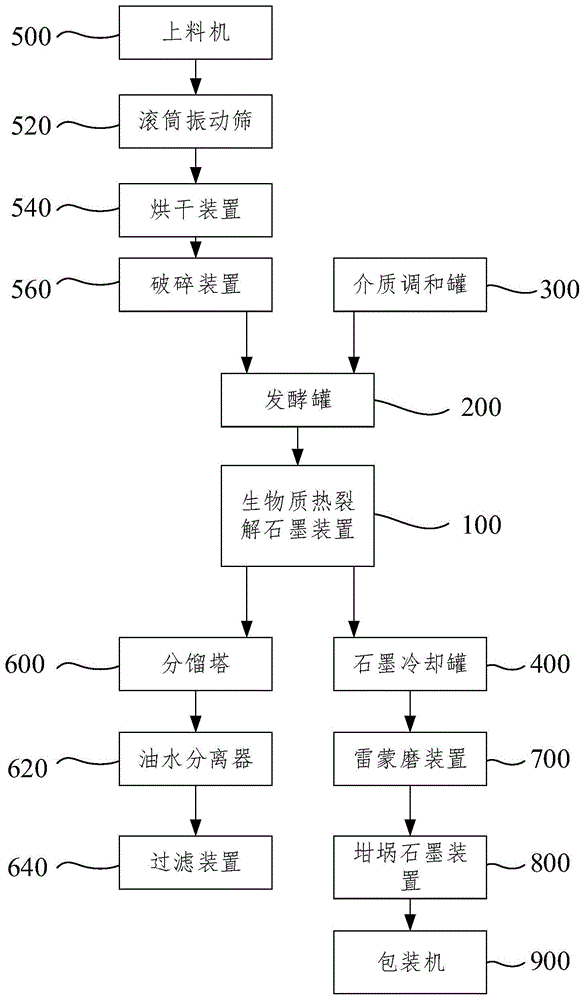
本发明涉及石墨
技术领域:
,具体涉及一种棕榈基人造石墨及其制备方法。
背景技术:
:石墨作为最主要的锂离子电池负极材料,按照种类大致分为天然石墨、人造石墨、中间相碳微球等。其中人造石墨具有许多优良的性质,因而在冶金、机械、电气、化工、纺织、国防等工业部门获得广泛应用。在冶金工业中,人造石墨可以作为炼钢电极,而天然石墨制成的电极就难以用于使用条件较苛刻的炼钢电炉;在机械工业中,石墨材料常用作润滑油的添加剂,输送腐蚀介质的设备,广泛采用人造石墨制成的活塞环、锂离子电池负极材料,密封圈和轴承,工作时无需加入润滑油;在化学工业中,人造石墨具有耐腐蚀、导热性好、渗透率低等特点,在化学工业中广泛用于制作热交换器、反应槽、吸收塔、过滤器等设备。现有人造石墨的制备方法一般是:以各项异性的针状焦为主要原料,在其中加沥青作为粘结剂,再加入少量其它辅料;各种原材料配合好以后,将其压制成型,然后在适当的温度下非氧化性气氛中处理,使之石墨化,得到人造石墨。然而,该方法的制备工艺繁琐、生产成本高、石墨化度不高。因此,现有人造石墨的制备方法有待进一步改进。技术实现要素:为此,本发明提供一种棕榈基人造石墨及其制备方法,以解决现有人造石墨的制备方法存在工艺繁琐、生产成本高、石墨化度不高等问题。为了实现上述目的,本发明提供如下技术方案:根据本发明的第一方面,一种棕榈基人造石墨的制备方法,所述制备方法包括如下步骤:步骤一,筛选棕榈壳,对筛选合格的棕榈壳依次经烘干和破碎处理后得到棕榈基驱体粉末;将沥青与轮胎油按比例混合搅拌得到沥青轮胎油混合液体;步骤二,将所述棕榈基驱体粉末与所述沥青轮胎油混合液体进行混合搅拌得到混合物料;步骤三,将所述混合物料与催化剂一起进行发酵处理得到发酵混合物料;步骤四,将所述发酵混合物料依次进行热裂解和石墨化处理得到棕榈基人造石墨。通过上述技术方案,本发明采用廉价的固态棕榈壳作为非针状焦前驱体,采用液态轮胎油作为针状焦前驱体,与粘结剂沥青一起制备人造石墨,使得制备的人造石墨生产成本低。本发明的制备方法将固态棕榈壳、液态轮胎油和粘结剂沥青先充分混合再催化能提升混合物料中各处针状焦前驱体与非针状焦前驱体的一致性,有利于提升所得人造石墨的振实密度和压实密度,从而提高所得人造石墨的品质,进而提升材料的能量密度。本发明的制备方法将固态棕榈壳、液态轮胎油和粘结剂沥青先充分混合再催化发酵然后热裂解最后石墨化处理得到人造石墨,制备过程简单易行,生产效率高,且产品石墨化度高。进一步地,步骤一中,对筛选合格的棕榈壳经烘干处理后含水量降至15%以下;对烘干后的棕榈壳经破碎处理后得到的棕榈基驱体粉末粒径为0.2-0.8mm。经棕榈壳破碎至规定粒径的粉末,方便与其他原料进行充分混合,有利于提升所得人造石墨的振实密度和压实密度,进而提升材料的能量密度。进一步地,步骤一中,所述沥青为石油沥青或者煤沥青中的一种。进一步地,步骤一中,所述沥青与轮胎油混合搅拌的重量比为1:(4.5-5.5);所述沥青与轮胎油混合搅拌的温度为80℃-150℃;所述沥青与轮胎油混合搅拌的时间为1h-1.5h。通过上述技术方案,沥青作为人造石墨的粘结剂,通过轮胎油进行加温稀释,进而更加方便与棕榈基驱体粉末进行有效混合。进一步地,步骤二中,所述棕榈基驱体粉末与所述沥青轮胎油混合液体混合搅拌的重量比为1:(1.4-1.6);所述棕榈基驱体粉末与所述沥青轮胎油混合液体混合搅拌的温度为80℃-150℃;所述棕榈基驱体粉末与所述沥青轮胎油混合液体混合搅拌的时间为1h-2h。通过上述技术方案,使每个棕榈基驱体粉末都充分包覆沥青轮胎油混合液体。进一步地,步骤三中,所述催化剂为过氧化氢,其用量为所述混合物料的0.25%-0.35%。通过上述技术方案,能够对混合物料进行有效的发酵。进一步地,步骤三中,所述发酵处理的温度为80℃-120℃;所述发酵处理的时间为2.5h-3.5h。通过上述技术方案,能够对混合物料进行更有效的发酵。进一步地,步骤四中,将所述发酵混合物料进行热裂解处理得到油蒸汽混合物和碳化料;油蒸汽混合物经油水分离器得到燃料油,碳化料经冷却系统冷却再通过颗粒整形后进入高温石墨化炉中进行石墨化处理。通过上述技术方案,采用本发明制备方法制备棕榈基人造石墨的过程中还能收获优质的燃料油,实用型强。进一步地,步骤四中,所述石墨化处理的具体步骤如下:将高温石墨化炉洗炉两-三次,抽至真空0.1mpa,再充氩气至大气压,抽真空至0.1mpa,然后充氩气至微正压;碳化料经冷却系统冷却再通过颗粒整形然后进入高温石墨化炉中;在氩气气氛下将高温石墨化炉升温至2800℃-3000℃保持4h-5h,然后自然降温至室温即得棕榈基人造石墨。进一步地,所述升温速度为10℃/min-15℃/min;所述氩气的通气流量为5l/min-15l/min。根据本发明的第二方面,一种棕榈基人造石墨,其特征在于,述一种棕榈基人造石墨采用上述的制备方法制备而成;所述棕榈基人造石墨的含碳量为99.4%以上,石墨化度为94.2%以上。本发明具有如下优点:本发明一种棕榈基人造石墨的制备方法通过采用固态棕榈壳作为非针状焦前驱体,采用液态轮胎油作为针状焦前驱体,与粘结剂沥青一起制备人造石墨,可使得制备的人造石墨同时具有能量密度高、寿命长和倍率好的特点。本发明一种棕榈基人造石墨的制备方法简单,操作过程安全可靠,生产效率高,且生产成本低,产品石墨化度高。采用本发明的制备方法制备的棕榈基人造石墨石墨化度达到94.2%以上,固定碳达到99.4%以上,远远超过现在市场的人造石墨产品;制备的棕榈基人造石墨电池可作为动力电池的负极材料,负极材料的成本低廉,原材料优质、丰富;制备的棕榈基人造石墨具有比表面积大、晶体结构稳定和电解液适应性强等特点。附图说明为了更清楚地说明本发明的实施方式或现有技术中的技术方案,下面将对实施方式或现有技术描述中所需要使用的附图作简单地介绍。显而易见地,下面描述中的附图仅仅是示例性的,对于本领域普通技术人员来讲,在不付出创造性劳动的前提下,还可以根据提供的附图引伸获得其它的实施附图。本说明书所绘示的结构、比例、大小等,均仅用以配合说明书所揭示的内容,以供熟悉此技术的人士了解与阅读,并非用以限定本发明可实施的限定条件,故不具技术上的实质意义,任何结构的修饰、比例关系的改变或大小的调整,在不影响本发明所能产生的功效及所能达成的目的下,均应仍落在本发明所揭示的技术内容能涵盖的范围内。图1为本发明一些实施例提供的一种棕榈基人造石墨的制备系统的结构图。图2为本发明一些实施例提供的一种棕榈基人造石墨的制备系统的详细结构图。图3为本发明一些实施例提供的一种棕榈基人造石墨的制备系统的发酵罐结构图。图4为本发明一些实施例提供的一种棕榈基人造石墨的制备系统的介质调和罐结构图。图5为本发明一些实施例提供的一种棕榈基人造石墨的制备系统的石墨冷却罐结构图。图6为本发明一些实施例提供的一种棕榈基人造石墨的制备系统的热裂解反应釜结构图。图7为本发明一些实施例提供的一种棕榈基人造石墨的制备系统的分馏塔结构图。图8为本发明一些实施例提供的一种棕榈基人造石墨的制备系统的上料机结构图。图9为实施例1得到的棕榈基人造石墨的x射线衍射图;图10为实施例1得到的棕榈基人造石墨的拉曼光谱图;图11为实施例1得到的棕榈基人造石墨的n2吸附-脱附等温曲线;图12为实施例1得到的棕榈基人造石墨的孔尺寸分布图。具体实施方式以下由特定的具体实施例说明本发明的实施方式,熟悉此技术的人士可由本说明书所揭露的内容轻易地了解本发明的其他优点及功效,显然,所描述的实施例是本发明一部分实施例,而不是全部的实施例。基于本发明中的实施例,本领域普通技术人员在没有做出创造性劳动前提下所获得的所有其他实施例,都属于本发明保护的范围。实施例1一种棕榈基人造石墨的制备方法包括如下步骤:步骤一,棕榈基驱体通过滚筒振动筛筛选,去除粉末及灰尘取得高品质的棕榈壳原料,对筛选合格的棕榈基驱体通过输送进入烘干系统进行烘干,棕榈基驱体所含水分40%-50%,烘干后使水分降至15%以下,对烘干后的棕榈基驱体采用破碎机经破碎处理后得到粒径为0.2-0.8mm的棕榈基驱体粉末。将沥青与轮胎油按重量比为1:5混合,在80℃-150℃下搅拌1h得到沥青轮胎油混合液体。步骤二,将所述棕榈基驱体粉末与所述沥青轮胎油混合液体按重量比为1:1.5在温度为80℃-150℃下进行混合搅拌1h-2h得到混合物料。步骤三,将所述混合物料与所述混合物料0.3%量的过氧化氢一起在温度为80℃-120℃下进行发酵处理3h得到发酵混合物料;步骤四,将所述发酵混合物料进行热裂解处理,热裂解温度达到450℃-480℃停止出油,混合物达到干点,得到油蒸汽混合物和碳化料;油蒸汽混合物经油水分离器得到燃料油,碳化料经冷却系统冷却再通过颗粒整形后进入高温石墨化炉中进行石墨化处理;所述石墨化处理的具体步骤如下:将高温石墨化炉洗炉两次,抽至真空0.1mpa,再充氩气至大气压,抽真空至0.1mpa,然后充氩气至微正压;将100kg碳化料经冷却系统冷却再通过颗粒整形然后进入高温石墨化炉中;在通气流量为5l/min-15l/min的氩气气氛下,将高温石墨化炉以15℃/min的升温速度升温至2950℃保持5h,然后自然降温至室温即得82.7kg棕榈基人造石墨。石墨化处理过程中材料的损耗率为17.3%。实施例2一种棕榈基人造石墨的制备方法,该制备方法与实施例1存在如下区别,其他同实施例1:所述石墨化处理的具体步骤如下:将高温石墨化炉洗炉两次,抽至真空0.1mpa,再充氩气至大气压,抽真空至0.1mpa,然后充氩气至微正压;将100kg碳化料经冷却系统冷却再通过颗粒整形然后进入高温石墨化炉中;在通气流量为5l/min-15l/min的氩气气氛下,将高温石墨化炉以10℃/min的升温速度升温至3000℃保持4h,然后自然降温至室温即得81.5kg棕榈基人造石墨。石墨化处理过程中材料的损耗率为18.5%。实施例3一种棕榈基人造石墨的制备方法,该制备方法与实施例1存在如下区别,其他同实施例1:所述石墨化处理的具体步骤如下:将高温石墨化炉洗炉两次,抽至真空0.1mpa,再充氩气至大气压,抽真空至0.1mpa,然后充氩气至微正压;将100kg碳化料经冷却系统冷却再通过颗粒整形然后进入高温石墨化炉中;在通气流量为5l/min-15l/min的氩气气氛下,将高温石墨化炉以15℃/min的升温速度升温至3000℃保持5h,然后自然降温至室温即得85.2kg棕榈基人造石墨。石墨化处理过程中材料的损耗率为14.8%。实施例4本实施例中的一种棕榈基人造石墨的制备方法,包括实施例1或2或3中的全部技术特征,另外,本实施例的制备方法采用以下一种棕榈基人造石墨的制备系统实现:如图1至图8所示,本实施例中的一种棕榈基人造石墨的制备系统,包括上料机500、滚筒振动筛520、烘干装置540、破碎装置560、介质调和罐300、发酵罐200、生物质裂解石墨装置100、石墨冷却罐400、雷蒙磨装置700、坩埚石墨装置800和包装机900;上料机500的出料口与滚筒振动筛520的进料口连通,滚筒振动筛520的出料口与烘干装置540的进料口连通,烘干装置540的出料口与破碎装置560的出料口连通,破碎装置560以及介质调和罐300的出料口均与发酵罐200连通,发酵罐200的出料口与生物质裂解石墨装置100的进料口连通,生物质裂解石墨装置100的石墨物料出口与石墨冷却罐400连通,石墨冷却罐400依次连接有雷蒙磨装置700、坩埚石墨装置800和包装机900。通过本实施例的一种棕榈基人造石墨的制备系统,结构简化、加工方便、生产效率提高、产品收率提高、环境污染减少;提供有可选性自动进料和自动出碳装置,使进料和出碳更加方便快捷,提高工作效率;整个运行过程环保无污染,全程电子系统监控,操作简单,运行稳定,安全可靠;利用棕榈基原料进行热裂解碳化,制备棕榈基石墨在技术上先进可行,投资少,原料多,收效快。本实施例中的一种棕榈基人造石墨的制备系统还包括分馏塔600、油水分离器620和过滤装置640;生物质裂解石墨装置100的热裂解反应釜上方安装有分馏塔600,分馏塔600的液体出口与油水分离器620的入口连通,油水分离器620的油出口与过滤装置640连通;还包括引风机和烟气净化装置,生物质裂解石墨装置100的炉体产生的热气经引风机引入发酵罐200和介质调和罐300进行加温使用,发酵罐200和介质调和罐300的出风口经烟气净化装置处理后排放;还包括燃烧机和气体回收装置,燃烧机和气体回收装置均与生物质裂解石墨装置100连通。具体的,生物质裂解石墨装置100通过发酵后的混合物进入进料漏斗,通过进料口绞龙将混合物料输入至图6所示的热裂解反应釜中,进料漏斗下方的蝴蝶阀开气,当所需物料进料完毕,电动蝴蝶阀关合,使热裂解反应釜内得以密闭;热裂解反应釜内下方为出碳绞龙,出口处有电磁阀开关控制,热裂解过程完成后将开关打开,将裂解后的石墨原料进入石墨冷却罐400中;热裂解反应釜上方装图7所示的分馏塔600,分馏塔600装有温度传感器,自动泄压阀,当热裂解反应釜釜内压力达到0.2千帕的时候泄压阀自动打开泄压,保证生产的安全,泄压的气体进入气体暂存罐;分馏塔600将裂解过程中的温度所产生的油水气混合物通过冷凝水循环系统进入油水分离器620中的油水分离罐体内,经分级分离后完成油水分离,水在分离后有少量油得不到充分分离,经油水分离器620进行分离,经过水净化系统完成环保排放标准;分离出来的油返回油品过滤装置;油水气经过水冷却系统后有一部分不可冷凝的气体,进入气体暂存罐,气体暂存罐的罐体设有气体进口与出口、检查口、压力表和防回火装置;气体暂存罐内的气体供给燃烧系统;采用耐火砖将热裂解反应釜砌筑在炉体内,使燃烧系统进行加温;热裂解反应釜内装有温度传感器,将热裂解反应釜内温度传到温控系统,以达到时时监测;炉体加温的过程中产生的热气经引风机引入介质调和罐300和发酵罐200加温的使用,发酵罐200与介质调和罐300的出风口经烟气净化系统处理,达到环保标准排放;冷却后的石墨原料通过整形颗粒机进行颗粒整形,达到石墨化炉所需要求,在生产过程中会产生一些颗粒粉末经除尘系统以达到环保要求。高温石墨化炉对整形的颗粒加以石墨化处理,温度在2800℃-3000℃对棕榈基碳化料煅烧,得到高品质的人造石墨。在本实施例中,其裂解工艺可直接把棕榈基发酵后的混合物装入到生物质热裂解石墨装置100中,可馏出油蒸汽混合物,通过油水分离器620、经冷却系统使油气冷凝得到品质较好的燃料油和棕榈基人造石墨的原料,从裂解处理器出来的废气烟尘,一部分通过特制管道利用余热作用于介质调和罐300和发酵罐200使用,而后进入逆流湿式烟尘处理装置,达标后排放;另一部分低碳链不凝气通过安全水封进入可燃气回收系统,作为裂解炉的燃料燃烧掉,棕榈基人造石墨在生产运行中能够有效地防止气体的外泄。本实施例中的一种棕榈基人造石墨的制备系统中,发酵罐200包括发酵外罐体207、发酵内罐体208、发酵搅拌装置、发酵输送装置和发酵上料装置,发酵外罐体207和发酵内罐体208均为中空结构,发酵外罐体207套设在发酵内罐体208的外周侧,发酵内罐体208和发酵外罐体207之间形成有环形中空且密封的加热腔室,发酵内罐体208和发酵外罐体207的共同端面上设置有发酵进风口216和发酵出风口215,发酵内罐体208的内部空腔内设置有发酵搅拌装置和发酵输送装置,发酵内罐体208的下侧壁设置有贯穿发酵外罐体207的发酵下料口217,发酵下料口217的下方设置有发酵上料装置,发酵内罐体208的上侧壁还设置有贯穿发酵外罐体207的发酵进料口201、介质调和油入口202、催化剂入口203和发酵排气口204,料口、介质调和油入口202、催化剂入口203以及发酵排气口204均与发酵内罐体208的内部空腔连通;本实施例的发酵外罐体207和发酵内罐体208均为圆筒形结构,发酵外罐体207和发酵内罐体208连接处的端面以及发酵内罐体208的端面均设置有封闭的圆板;发酵搅拌装置实现对发酵内罐体208内的物料的搅拌,发酵输送装置实现对发酵内罐体208内的物料的一侧向另一侧输送;发酵上料装置实现将发酵下料口217的物料输送至生物质热解石墨装置中。通过本实施例的一种发酵罐200,通过热风加温装置对发酵内罐体和发酵外罐体之间的加热空腔进行加热以及热风循环,热风不断的输入与输出对罐体进行加热,达到所需温度;通过设置发酵搅拌装置,有效的实现了对混合物料的均匀搅拌;通过设置发酵输送装置,有效的实现了发酵后的混合物的输送;通过设置发酵上料装置,有效的将发酵好的物料输送至生物质热解石墨装置中。发酵罐200还包括发酵温度传感器222,发酵温度传感器222设置在发酵内罐体208的内部空腔内;还包括发酵保温层206,发酵保温层206套设在发酵外罐体207的外周侧;还包括发酵压力表221,发酵压力表221设置在发酵内罐体208的端面上,发酵压力表221用于显示发酵内罐体208的内部空腔的压力;通过设置发酵温度传感器222,实现了对发酵内罐体208内的温度的监测和控制;通过设置发酵压力表221,实现了对发酵内罐体208内部的压力的监测。发酵罐200还包括发酵检查口205,发酵检查口205设置在发酵内罐体208的上侧壁且贯穿发酵外罐体207,发酵检查口205与发酵内罐体208的内部空腔连通;本实施例的一种发酵罐200还包括催化剂喷淋装置209,催化剂喷淋装置209设置在发酵内罐体208的内部空腔内,催化剂喷淋装置209与催化剂入口203位于发酵内罐体208内部空腔的一端连接;通过设置发酵检查口205,实现了对发酵内罐体208内的发酵情况的及时查看;通过设置催化剂喷淋装置209,实现了将催化剂均匀的喷洒在发酵内罐体208中的物料上,提高了发酵的均匀度,提高了发酵效率。发酵罐200还包括发酵电动阀门227和发酵固定地脚218,发酵进料口201与发酵内罐体208内部空腔连通的管道上设置有发酵电动阀门227,发酵外罐体207的下侧壁设置有发酵固定地脚218;通过设置发酵电动阀门227,实现了对发酵进料口201内喂入物料的流量和体积控制。发酵罐200的发酵搅拌装置包括发酵搅拌减速电机223、发酵搅拌轴210、第一固定法兰212、第二固定法兰225和多个发酵搅拌叶片211,发酵搅拌轴210横向设置在发酵内罐体208的内部空腔内,发酵搅拌轴210的两端分别通过第一固定法兰212和第二固定法兰225转动连接在发酵内罐体208的端面上,发酵搅拌轴210的外侧壁设置有多个发酵搅拌叶片211,发酵搅拌轴210位于第二固定法兰225外侧的一端与发酵搅拌减速电机223的输出轴传动连接。本实施例中的一种发酵罐200,发酵输送装置包括发酵绞龙减速电机224、发酵出料绞龙213、第三固定法兰214和第四固定法兰226,发酵出料绞龙213横向设置在发酵内罐体208的内部空腔内,发酵出料绞龙213设置在发酵搅拌轴210的下方,发酵出料绞龙213的两端通过第三固定法兰214和第四固定法兰226转动连接在发酵内罐体208的端面上,发酵出料绞龙213位于第四固定法兰226外侧的一端与发酵绞龙减速电机224的输出轴传动连接。本实施例中的一种发酵罐200,发酵上料装置包括发酵上料减速电机220和发酵上料绞龙219,发酵上料绞龙219倾斜设置在发酵下料口217的下方,发酵下料口217与发酵上料绞龙219的壳体下端侧壁连通,发酵上料绞龙219的下端与发酵上料减速电机220的输出轴传动连接,例如发酵上料绞龙219的倾斜45°设置;通过多个发酵搅拌叶片211和发酵搅拌轴210为核心部件构成的发酵搅拌装置,提高了发酵效率,有利于将物料进行搅拌发酵;通过发酵出料绞龙213的设置,实现了发酵内罐体208内部的物料的快速输送;通过倾斜设置的发酵上料绞龙219,实现了物料自下而上的稳定输送。本实施例中的一种棕榈基人造石墨的制备系统中,介质调和罐300包括介质调和内罐体301、介质调和外罐体302、介质调和搅拌装置、介质调和上料斗308、介质调和上料装置、渣浆泵317和介质油泵318,介质调和内罐体301和介质调和外罐体302均为中空壳体结构,介质调和外罐体302套设在介质调和内罐体301的外周侧,介质调和外罐体302和介质调和内罐体301之间设置有用于热风循环的加热腔,介质调和内罐体301内部设置有介质调和搅拌装置,介质调和外罐体302上设置有与加热腔连通的介质调和进风口305和介质调和出风口306,介质调和内罐体301的上端面上设置有介质调和入料口313和介质油入口312,介质调和内罐体301的下端面上设置有介质调和出渣口321,介质调和上料斗308设置在介质调和外罐体302外侧下端,介质调和上料装置的下端伸入至介质调和上料斗308内,介质调和上料装置的上端与介质调和入料口313连通,渣浆泵317的入口通过管道与介质调和出渣口321连通,介质油泵318的出口通过管道与介质油入口312连通。本实施例中的配置中有轮胎油输入计量装置和沥青上料计量装置,通过计量装置输入所需物料,还包括加温装置和混合物输出装置;将轮胎油与沥青加热搅拌,使轮胎油沥青充分溶解稀释,加温温度80-150°,罐体有温度传感器显示所需温度,还包括玻璃管视镜;通过此装置得到轮胎油沥青混合物,输送泵输送,进入发酵罐;通过本实施例的一种介质调和罐300,实现了在轮胎油和沥青混合物输送至发酵罐前的均匀搅拌,混合物的溶解更加充分,具有较好的调和效率和调和质量。介质调和罐300的介质调和搅拌装置包括介质调和搅拌减速电机311、介质调和搅拌轴3和介质调和搅拌叶片304,介质调和搅拌减速电机311设置在介质调和内罐体301顶部外侧,介质调和搅拌轴303竖直设置在介质调和内罐体301内,介质调和搅拌减速电机311的输出轴与介质调和搅拌轴303传动连接,介质调和搅拌轴303的外侧壁上设置有多个介质调和搅拌叶片304;介质调和上料装置包括介质调和上料绞龙307和介质调和上料减速电机310,介质调和上料绞龙307的进口向下伸入至介质调和上料斗308内,介质调和上料绞龙307的转轴上端与介质调和上料减速电机310的输出轴传动连接,介质调和上料绞龙307的上端出口与介质调和入料口313连通,介质调和上料绞龙307为螺旋输送器;在本实施例中,介质调和搅拌减速电机311指的是在电机端部设置有减速器的电机结构;通过设置介质调和搅拌减速电机311、介质调和搅拌轴303和介质调和搅拌叶片304构成的介质调和搅拌装置,实现了对介质调和内罐体301内混合物料的搅拌,提高了调和的均匀度,提高了调和效率;通过设置介质调和上料绞龙307和介质调和上料减速电机310构成的介质调和上料装置,实现了对混合前物料的输送。介质调和罐300还包括视镜309,视镜309贯穿设置在介质调和内罐体301及介质调和外罐体302的侧壁上;还包括介质调和检查口314,介质调和检查口314设置在介质调和内罐体301的上端面上;还包括介质调和排气口315,介质调和排气口315设置在介质调和内罐体301的上端面上,介质调和排气口315位于介质调和检查口314的旁侧,例如视镜309为透明材质;通过设置视镜309,实现了对介质调和内罐体301内部的搅拌工作状态的观察;通过设置介质调和检查口314,实现了对介质调和内罐体301内部的检查维护;通过设置介质调和排气口315,实现了介质调和内罐体301内气体的排出,避免压力过大。介质调和罐300还包括内罐温度传感器319和外罐温度传感器320,内罐温度传感器319设置在介质调和内罐体301的内部,外罐温度传感器320设置在介质调和外罐体302的外侧壁上;还包括介质调和压力表316,介质调和压力表316设置在介质调和内罐体301的上端面上,介质调和压力表316用于测量介质调和内罐体301内的压力;通过设置内罐温度传感器319,实现了对介质调和内罐体301内部温度的监测;通过设置外罐温度传感器320,实现了对介质调和外罐体302的温度的监测;通过设置介质调和压力表316,实现了对介质调和内罐体内部压力的观测。介质调和罐300的介质调和内罐体301的下端设置有锥形筒,介质调和出渣口321设置在锥形筒的下部尖端处,渣浆泵317的进料口通过管道与介质调和出渣口321的上方连通;介质调和进风口305和介质调和出风口306位于同一平面内,介质调和进风口305和介质调和出风口306对称设置在介质调和外罐体302的外侧壁上;通过设置在介质调和内罐体301下端的锥形筒,提高了渣料排出的速度。本实施例中的一种棕榈基人造石墨的制备系统中,石墨冷却罐400包括冷却外罐体422、冷却内罐体423、冷却入料管419、冷却出料管409、冷却上料绞龙装置和冷却搅拌输送装置,冷却外罐体422和冷却内罐体423均为竖直设置的中空的壳体结构,冷却外罐体422套设在冷却内罐体423的外周侧,冷却外罐体422和冷却内罐体423之间形成有第一循环水腔415,冷却外罐体422的侧壁上设置有与第一循环水腔415连通的冷却罐体上水口410和冷却罐体出水口406,冷却内罐体423的上端设置有冷却入料管419,冷却入料管419与冷却上料绞龙装置的出料口连接,冷却上料绞龙装置倾斜设置在冷却外罐体422的旁侧,冷却内罐体423的下部设置有冷却出料管409,冷却内罐体423内部竖直设置有冷却搅拌输送装置;在本实施例中,优选的,冷却罐体上水口410设置冷却罐体出水口406的下方,二者斜向对称设置,在本实施例中反应釜碳化后的石墨原料通过绞龙输送方式进入本实施例的一种棕榈基石墨冷却罐内,罐体由冷却外罐体422包裹冷却内罐体423组成,通过内外罐423体之间的第一循环水腔415空间通过水不断的循环由下进上出方式循环;通过本实施例的一种石墨冷却罐400,通过设置第一循环水腔,增强了冷却效果;通过设置冷却搅拌输送装置,既能起到搅拌作用,还能同时起到物料输送作用,本装置冷却效率高且显著提高了冷却效果。石墨冷却罐400的冷却上料绞龙装置包括冷却上料绞龙减速电机418和上料绞龙,上料绞龙的壳体与冷却入料管419固定连接,冷却上料绞龙减速电机418的输出轴与上料绞龙的转轴传动连接,上料绞龙为螺旋输送器;冷却上料绞龙装置还包括第二循环水腔414、绞龙进水口412和绞龙出水口413,第二循环水腔414套设在上料绞龙的外周侧,第二循环水腔414的侧壁下端设置有绞龙进水口412,第二循环水腔414的侧壁上端设置有绞龙出水口413;通过设置冷却上料绞龙减速电机418,实现了物料的自动向上输送;通过设置第二循环水腔414,实现了对上料绞龙输送过程中物料的冷却。石墨冷却罐400的冷却搅拌输送装置包括冷却搅拌减速电机401、冷却搅拌轴402、冷却搅拌叶片407和冷却出料绞龙408,冷却搅拌轴402的上端转动连接在冷却内罐体423的上端面上,冷却搅拌轴402的下端与冷却出料绞龙408的上端固定连接,冷却出料绞龙408的下端转动连接在冷却内罐体423的下端面上,冷却搅拌轴402的外周侧间隔设置有多个冷却搅拌叶片407,冷却出料绞龙408为螺旋输送器,冷却搅拌减速电机401设置在冷却内罐体423的上端面上,冷却搅拌减速电机401的输出轴与冷却搅拌轴402传动连接;还包括冷却固定法兰416,冷却内罐体423的下端设置有锥形筒,冷却固定法兰416固定在锥形筒的下方尖端,冷却出料绞龙408的下端转动连接在冷却固定法兰416中,冷却出料管409设置在锥形筒的锥面上;还包括蝴蝶阀417,蝴蝶阀417设置在冷却出料管409中;通过设置相互连接的冷却搅拌轴402与冷却出料绞龙408,精简了结构,实现了上部搅拌下部输送的双重技术效果,相比于分别设置的搅拌和输送装置而言,显著提高了输送效率;通过设置在冷却内罐体423下部的锥形筒,提高了物料的出料速度;通过设置在冷却出料管409中的蝴蝶阀417,实现了出料的速度的控制。石墨冷却罐400还包括冷却电控阀门420,冷却电控阀门420设置在冷却入料管419中;还包括冷却检查口403和冷却排气口404,冷却检查口403和冷却排气口404设置在冷却内罐体423的上端面上;还包括冷却罐体支撑地脚421,冷却罐体支撑地脚421的上端固定在冷却外罐体422的下端,冷却罐体支撑地脚421的下端固定在地面上;通过设置在冷却入料管419中的冷却电控阀门420,实现了对冷却罐中的物料输入的速度控制;通过设置冷却检查口403,实现了对冷却内罐体423内部的检测;通过设置冷却排气口404,实现了搅拌过输送过程中废气的输出;通过设置冷却罐体支撑地脚421,提高了冷却外罐体422的固定支撑效果。石墨冷却罐400还包括冷却压力表405和冷却温度传感器411,冷却压力表405设置在冷却内罐体423的上端面上,冷却压力表405用于监测冷却内罐体423内的压力,冷却温度传感器411设置在冷却内罐体423内,冷却温度传感器411用于监测冷却内罐体423内的温度;通过设置冷却压力表405,实现了对冷却罐内的压力的控制,提高了安全性;通过设置冷却温度传感器411,实现了对冷却罐内温度的控制。实验例1、将实施例1经冷却系统冷却和通过颗粒整形后的碳化料与最终得到的棕榈基人造石墨分别进行sgs检测,检测报告分别如表1和表2所示。表1经冷却系统冷却和通过颗粒整形后的碳化料的检测报告表检测项目基态单位检测结果检测依据灰分干基%3.9gb/t17664-1999全硫干基%0.05参照gb/t214-2007碳干基%83.94参照gb/t30733-2014表2最终得到的棕榈基人造石墨的检测报告表检测项目基态单位检测结果检测依据挥发分干基%0.9gb/t17664-1999碘吸附值/mg/g<600gb/t12496.8-2015碳干基%99.43参照gb/t30733-2014由表1和表2的对比结果可以看出,采用本发明的制备方法得到碳化料石墨化度高,最终得到的棕榈基人造石墨的含碳量高。2、将实施例1得到的棕榈基人造石墨依据qj2507-1993碳素材料微观结构参数测试方法检测其石墨化度,检测的x射线衍射图谱如图9所示,根据x射线衍射图谱得到实施例1得到的棕榈基人造石墨的石墨化度为94.2%,石墨化度高。3、将实施例1得到的棕榈基人造石墨取六个点分别进行拉曼光谱仪分析检测,其中四个点的检测图谱如图10所示,从拉曼光谱图可以初步分析实施例1得到的棕榈基人造石墨具有多层石墨烯结构。4、将实施例1得到的棕榈基人造石墨进行bet比表面积和孔体积测试,n2吸附-脱附等温曲线和孔尺寸分布状况分别如图11和图12所示,结果显示,实施例1得到的棕榈基人造石墨具有很大的比表面积,达到1850m2/g,孔体积为0.96cm3/g,孔尺寸分布在4nm以下,孔丰富,其比表面积和孔体积性能明显高于目前市场上售卖的活性碳,将其制作成活性炭用在吸附,超级电容器,催化剂载体等应用方向是可行。5、采用实施例1得到的棕榈基人造石墨作为动力电池的负极材料使用时,得到的充放电曲线斜率大,即使在大电流下,金属锂也较难沉积,提高了电池的安全性能;充电深度可以调整,因此可以控制电压变化;棕榈基人造石墨的容量可以达到300~350mah〃g-1,循环性能可以提升至1500次以上。虽然,上文中已经用一般性说明及具体实施例对本发明作了详尽的描述,但在本发明基础上,可以对之作一些修改或改进,这对本领域技术人员而言是显而易见的。因此,在不偏离本发明精神的基础上所做的这些修改或改进,均属于本发明要求保护的范围。当前第1页12