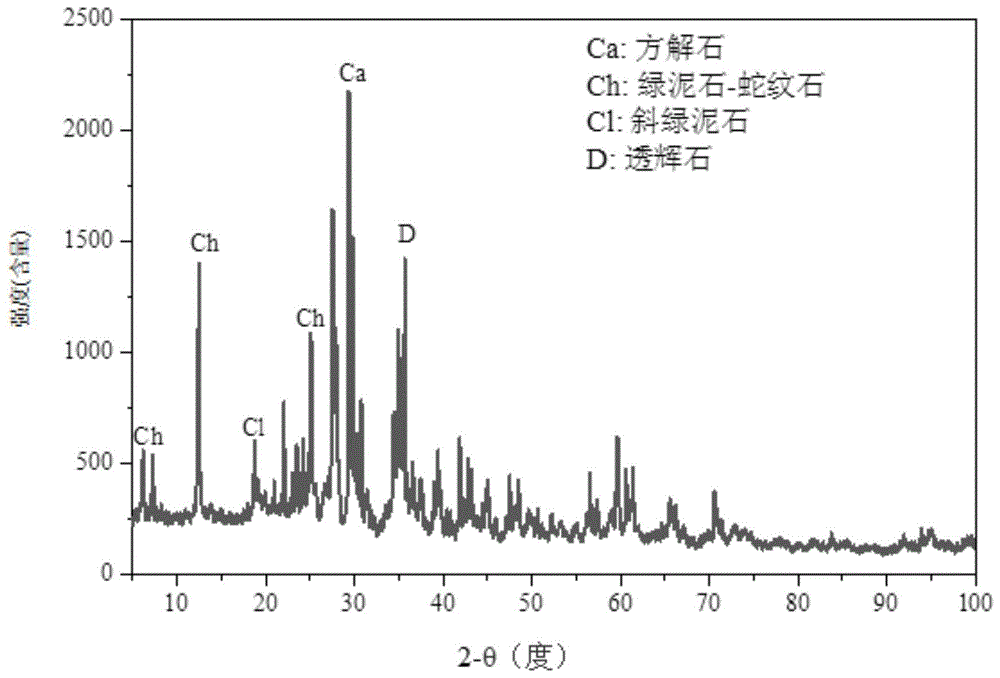
本发明涉及建筑材料领域,具体地,涉及非烧结玄武岩尾矿砖及其制备方法。
背景技术:
:目前传统建筑行业所用实心/空心砖多以粘土和页岩为原料经高温(900~1000℃)烧结所得,其不足之处在于:一是以自然资源为原料,破坏耕地资源,二是制备温度较高,能耗较大,三是烧结过程中产生有害气体,污染环境。随着我国城市、公路、铁路建设的不断推进,为满足建设用碎石、砂子市场的需求,有效的促进了石料开采加工企业蓬勃发展。在我国富有大量玄武岩矿石的一些地区,利用玄武岩矿石生产建设所用的碎石和机制砂,而在生产加工过程中会产生大量的玄武岩尾矿,该尾矿颗粒粒径一般为0~90μm,难以堆放,很容易造成粉尘污染,且约束了企业可持续发展的要求。因此,为了解决玄武岩尾矿处理、环境污染等问题。如何将玄武岩尾矿有效利用,使之变废为宝成为了一个亟待解决的重要课题。技术实现要素:本发明一方面所要解决的技术问题是提供一种非烧结玄武岩尾矿砖,该非烧结玄武岩尾矿砖以玄武岩尾矿为基体,实现了尾矿资源以及固体废弃物资源的有效利用。本发明另一方面所要解决的技术问题是提供一种非烧结玄武岩尾矿砖的制备方法,该方法免蒸免烧,简化了尾矿砖的制备工艺,而且制得的玄武岩尾矿砖具有较好地抗压强度。为了实现上述目的,本发明一方面提供一种非烧结玄武岩尾矿砖,按质量份计,该非烧结玄武岩尾矿砖由以下组分制得:玄武岩尾矿50-60份、粉煤灰40-50份、碱性激发剂13-18份。优选地,按质量份计,由以下组分制得:玄武岩尾矿53-57份、粉煤灰43-48份、碱性激发剂15-16份。优选地,所述玄武岩尾矿中粒度小于165.5μm的颗粒含量为90-93%。优选地,所述粉煤灰为一级粉煤灰。优选地,所述碱性激发剂由氢氧化钠和水玻璃按质量(0.8-1.2):(1.8-2.3)配制得到。本发明另一方面提供一种非烧结玄武岩尾矿砖的制备方法,该方法包括如下步骤:将玄武岩尾矿、粉煤灰干混,然后加入碱性激发剂和水混合均匀,得到混合料;将所述混合料压制成型后通风或洒水养护,得到所述玄武岩尾矿砖;其中,按质量份计,所述玄武岩尾矿取50-60份,所述粉煤灰取40-50份,所述碱性激发剂取13-18份。优选地,按质量份计,所述玄武岩尾矿取53-57份,所述粉煤灰取43-48份,所述碱性激发剂取15-16份。优选地,所述玄武岩尾矿中粒度小于165.5μm的颗粒含量为90-93%;所述粉煤灰为一级粉煤灰。优选地,所述碱性激发剂的制备方法为:氢氧化钠固体加入去离子水配成10m-15m的氢氧化钠溶液,所述氢氧化钠溶液与水玻璃混合均匀即得;其中,所述氢氧化钠固体与所述水玻璃的质量比为(0.8-1.2):(1.8-2.3)。优选地,所述干混的时间为1-5min;加入所述碱性激发剂和所述水后的搅拌时间为8-12min;所述压制的压强为3-8mpa,时间为2-5min;所述通风或洒水养护的时间为25-30天。通过上述技术方案,本发明实现了以下有益效果:本发明采用碱性激发剂对玄武岩尾矿进行激发,通过不同的配比可以制成不同强度的非烧结尾矿砖,实现了尾矿资源以及固体废弃物资源的合理大量利用。本发明制备成的玄武岩尾矿砖无侧限抗压强度最高可达20.63mpa,且在吸水率等等方面均满足《非烧结垃圾尾矿砖》国家标准的要求,为有效利用玄武岩尾矿提供一种合适的思路,为尾矿和固体废弃物的合理二次利用带来借鉴,减少了能源损耗和温室效应,能够产生很好的社会效益、经济效益和环境效益。附图说明图1是本发明实施例中玄武岩的xrd图;图2是本发明实施例中玄武岩尾矿的化学成分和粒度分析;图3是本发明实施例中粉煤灰的xrd图;图4是本发明实施例中粉煤灰的化学成分和粒度分析。具体实施方式在本文中所披露的范围的端点和任何值都不限于该精确的范围或值,这些范围或值应当理解为包含接近这些范围或值的值。对于数值范围来说,各个范围的端点值之间、各个范围的端点值和单独的点值之间,以及单独的点值之间可以彼此组合而得到一个或多个新的数值范围,这些数值范围应被视为在本文中具体公开。本发明提供的非烧结玄武岩尾矿砖,按质量份计,由以下组分制得:玄武岩尾矿50-60份、粉煤灰40-50份、碱性激发剂13-18份。其中,玄武岩尾矿的主要成分是sio2、cao、fe2o3、al2o3等,粉煤灰中的主要成分为sio2和al2o3,玄武岩尾矿、粉煤灰原料中的铝硅酸盐在碱性激发剂溶解,并发生聚合作用。为了进一步增强玄武岩尾矿砖的抗压强度,按质量份计,该玄武岩尾矿砖由以下组分制得:玄武岩尾矿53-57份、粉煤灰43-48份、碱性激发剂15-16份。所述玄武岩尾矿中粒度小于165.5μm的颗粒含量为90-93%,粒度小可以使得玄武岩和粉煤灰混合更为均匀,进一步增强玄武岩尾矿砖的抗压强度。本发明的该优选方案,尾矿中剩余粒度较大的部分可以在砖块成型过程中起到骨架的作用,最终也可以提高试件强度。所述粉煤灰为一级粉煤灰。优选地,所述碱性激发剂由氢氧化钠和水玻璃按质量(0.8-1.2):(1.8-2.3)配制得到。本发明另一方面提供一种非烧结玄武岩尾矿砖的制备方法,该方法包括如下步骤:将玄武岩尾矿、粉煤灰干混,然后加入碱性激发剂和水混合均匀,得到混合料;将混合料压制成型后通风或洒水养护,得到所述玄武岩尾矿砖;其中,按质量份计,所述玄武岩尾矿取50-60份,所述粉煤灰取40-50份,所述碱性激发剂取13-18份。优选地,按质量份计,所述玄武岩尾矿取53-57份,所述粉煤灰取43-48份,所述碱性激发剂取15-16份。优选地,所述玄武岩尾矿中粒度小于165.5μm的含量不低于90%;所述粉煤灰为一级粉煤灰。优选地,所述碱性激发剂的制备方法为:氢氧化钠固体加入去离子水配成10m-15m的氢氧化钠溶液,所述氢氧化钠溶液与水玻璃混合均匀即得;其中,所述氢氧化钠固体与所述水玻璃的质量比为(0.8-1.2):(1.8-2.3)。所述干混的时间、加入碱性激发剂和水后的搅拌时间以及压制压强和时间可以是本领域的技术人员根据实际情况进行调整。优选地,所述干混的时间为1-5min;加入所述碱性激发剂和所述水后的搅拌时间为8-12min;所述压制的压强为3-8mpa,时间为2-5min;所述通风或洒水养护的时间为25-30天。以下将通过实施例对本发明进行详细描述。以下实施例中,粒度分布、无侧限抗压强度通过使用万能材料试验机,在仅有轴向压力的实验条件下,对试样进行无侧限压缩试验测得;密度、吸水率、饱和系数、抗冻性能、抗软化性能、耐碱性能分别通过《混凝土砌块和砖试验方法》gb/t4111-2013和《非烧结垃圾尾矿砖》jc/t422-2007方法测得。本发明实施例中使用的玄武岩尾矿取自陕西省岚皋县城关镇平溪河某玄武岩矿场,经烘干粉粹后得到实验所需的尾矿,备用;粉煤灰取自河南某燃煤火电厂,从煤燃烧后的烟气中收捕下来的细灰,为一级粉煤灰;氢氧化钠为分析纯试剂naoh片状固体;水玻璃为质量含量为40-45%的市售硅酸钠溶液,如产自无锡市亚泰联合化工有限公司的硅酸钠质量含量为42%的水玻璃。取少量玄武岩尾矿,经x射线衍射分析后,其主要矿物组成见图1。由图1可知,此玄武岩尾矿的矿物组成主要成分为方解石、绿泥石-蛇纹石、斜绿泥石和透辉石。而此玄武岩尾矿的化学成分和粒度分析分别见表1和图2。表1玄武岩尾矿的化学组成氧化物sio2caofe2o3al2o3mgo含量(%)37.2917.0018.2411.707.87此玄武岩尾矿中以sio2居多,其次为cao、fe2o3、al2o3,这些成分易于被碱性激发剂激发发生地聚反应,进而提高产品的强度。玄武岩尾矿的粒度集中分布在0μm~165.5μm之间,达到了90%以上。粉煤灰烘干后取样进行x射线衍射分析,结果如图3。由图3可知,此粉煤灰的矿物组成主要为莫来石。此粉煤灰的化学成分和粒度分析见表2和图4。表2粉煤灰的化学组成氧化物sio2al2o3fe2o3caok2o含量(%)51.9530.596.534.771.80此粉煤灰中sio2和al2o3含量最高,分别为51.95%和30.59%。本发明中的玄武岩矿、粉煤灰与碱性激发剂混合后,初始强度阶段,在高压成型等条件下,借助压制过程原材料颗粒之间的空气被充分排出,原料颗粒之间紧密接触,增加了砖坯的密实度,使砖坯产生了自然粘结。在免烧砖制备过程中,砖坯的初始强度不仅体现砖坯的密实程度,而且决定砖块后期强度的增长。在强度形成阶段,玄武岩尾矿、粉煤灰原料中的铝硅酸盐在新型碱性激发剂溶解,溶解的铝硅配合物由固体颗粒表面向颗粒间隙的扩散,凝胶相逐渐排除剩余的水分,缩聚硬化成矿物聚合材料砖体,聚合物材料的凝胶相m+n{-(sio2)z-alo2-}n·wh2o的形成,导致在碱硅酸盐溶液和铝硅配合物之间发生聚合作用。之后的硬化过程,是在碱性催化剂作用下的硅氧键和铝氧键的断裂-重组的反应过程。铝硅酸盐聚合反应是一个放热脱水的过程。反应以水为介质,聚合后又将大部分水排除,少量水则以结构水的形式取代【sio4】中的一个o的位置,最终形成alo4和sio4四面体结构单元组成三维立体网状结构的无机聚合物,发生缓慢的化学反应,缓慢促进砖的强度提高。实施例1(1)将80kg氢氧化钠固体加入去离子水配成10m的氢氧化钠溶液,将180kg水玻璃加入到氢氧化钠溶液中并混合均匀制得碱性激发剂;(2)将500kg玄武岩尾矿(粒度在165.5μm以下的颗粒的质量含量为90%)和500kg一级粉煤灰在搅拌机中进行干混3min,然后加入130kg碱性激发剂和50kg水,混匀搅拌10min得到混合料,将混合料倒进制砖机中在5mpa下压制3min成型。成型后的砖坯移入室内通风养护28天,制得尾矿砖。所得成品无侧限抗压强度达到15.3mpa,密度1.70kg/m3,吸水率、饱和系数、抗冻性能、抗软化性能、耐碱性能都达到国标《非烧结垃圾尾矿砖》mu15级别。实施例2(1)将120kg氢氧化钠固体加入去离子水配成15m的氢氧化钠溶液,将230kg水玻璃加入到氢氧化钠溶液中并混合均匀制得碱性激发剂;(2)将600kg玄武岩尾矿(粒度在165.5μm以下的颗粒的质量含量为91%)和400kg一级粉煤灰在搅拌机中进行干混2min,然后加入180kg碱性激发剂和50kg水,混匀搅拌9min得到混合料,将混合料倒进制砖机中在4mpa下压制2min成型。成型后的砖坯移入养护室进行洒水养护25天,得到尾矿砖。所得成品无侧限抗压强度达到19.8mpa,密度1.89kg/m3,吸水率、饱和系数、抗冻性能、抗软化性能、耐碱性能都达到国标《非烧结垃圾尾矿砖》mu15级别。实施例3(1)将100kg氢氧化钠固体加入去离子水配成11m的氢氧化钠溶液,将200kg水玻璃加入到氢氧化钠溶液中并混合均匀制得碱性激发剂;(2)将530kg玄武岩尾矿(粒度在165.5μm以下的颗粒的质量含量为92.58%)和430kg一级粉煤灰在搅拌机中进行干混1min,然后加入150kg碱性激发剂和50kg水混匀搅拌8min得到混合料,将混合料倒进制砖机中在3mpa下压制5min成型。成型后的砖坯移入养护室进行通风养护30天,制得尾矿砖。所得成品无侧限抗压强度达到17.68mpa,密度1.79kg/m3,吸水率、饱和系数、抗冻性能、抗软化性能、耐碱性能都达到国标《非烧结垃圾尾矿砖》mu15级别。实施例4(1)将90kg氢氧化钠固体加入去离子水配成12m的氢氧化钠溶液,将190kg水玻璃加入到氢氧化钠溶液中并混合均匀制得碱性激发剂;(2)将570kg玄武岩尾矿(粒度在165.5μm以下的颗粒的质量含量为93%)和480kg一级粉煤灰在搅拌机中进行干混4min,然后加入140kg碱性激发剂和50kg水混匀搅拌11min得到混合料,将混合料倒进制砖机中在6mpa下压制4min成型。成型后的砖坯移入养护室进行洒水养护29天,制得尾矿砖。所得成品无侧限抗压强度达到16.97mpa,密度1.75kg/m3,吸水率、饱和系数、抗冻性能、抗软化性能、耐碱性能都达到国标《非烧结垃圾尾矿砖》mu15级别。实施例5(1)将110kg氢氧化钠固体加入去离子水配成14m的氢氧化钠溶液,将210kg水玻璃加入到氢氧化钠溶液中并混合均匀制得碱性激发剂;(2)将550kg玄武岩尾矿(粒度在165.5μm以下的颗粒的质量含量为93%)和450kg一级粉煤灰在搅拌机中进行干混5min,然后加入160kg碱性激发剂和50kg水混匀搅拌12min得到混合料,将混合料倒进制砖机中在8mpa下压制3min成型。成型后的砖坯移入养护室进行洒水养护26天,制得尾矿砖。所得成品无侧限抗压强度达到20.63mpa,密度1.93kg/m3,吸水率、饱和系数、抗冻性能、抗软化性能、耐碱性能都达到国标《非烧结垃圾尾矿砖》mu15级别。对比例1(1)将80kg氢氧化钠固体加入去离子水配成10m的氢氧化钠溶液,将180kg水玻璃加入到氢氧化钠溶液中并混合均匀制得碱性激发剂;(2)将500kg玄武岩尾矿(粒度在165.5μm以下的颗粒的质量含量为90%)和550kg一级粉煤灰在搅拌机中进行干混3min,然后加入130kg碱性激发剂和50kg水,混匀搅拌10min得到混合料,将混合料倒进制砖机中在5mpa下压制3min成型。成型后的砖坯移入室内通风养护28天,制得尾矿砖。所得成品无侧限抗压强度达到14.7mpa,密度1.69kg/m3,吸水率、饱和系数、抗冻性能、抗软化性能、耐碱性能不能达到国标《非烧结垃圾尾矿砖》mu15级别。对比例2(1)将80kg氢氧化钠固体加入去离子水配成10m的氢氧化钠溶液,将180kg水玻璃加入到氢氧化钠溶液中并混合均匀制得碱性激发剂;(2)将500kg玄武岩尾矿(粒度在165.5μm以下的颗粒的质量含量为90%)和450kg一级粉煤灰在搅拌机中进行干混3min,然后加入100kg碱性激发剂和50kg水,混匀搅拌10min得到混合料,将混合料倒进制砖机中在5mpa下压制3min成型。成型后的砖坯移入室内通风养护28天,制得尾矿砖。所得成品无侧限抗压强度达到10.72mpa,密度1.73kg/m3,吸水率、饱和系数、抗冻性能、抗软化性能、耐碱性不能达到国标《非烧结垃圾尾矿砖》mu15、级别。对比例3(1)将70kg氢氧化钠固体加入去离子水配成10m的氢氧化钠溶液,将240kg水玻璃加入到氢氧化钠溶液中并混合均匀制得碱性激发剂;(2)将500kg玄武岩尾矿(粒度在165.5μm以下的颗粒的质量含量为90%)和500kg一级粉煤灰在搅拌机中进行干混3min,然后加入130kg碱性激发剂和50kg水,混匀搅拌10min得到混合料,将混合料倒进制砖机中在5mpa下压制3min成型。成型后的砖坯移入室内通风养护28天,制得尾矿砖。所得成品无侧限抗压强度达到14.2mpa,密度1.66kg/m3,吸水率、饱和系数、抗冻性能、抗软化性能、耐碱性不能达到国标《非烧结垃圾尾矿砖》mu15级别。对比例4(1)将80kg氢氧化钠固体加入去离子水配成10m的氢氧化钠溶液,将180kg水玻璃加入到氢氧化钠溶液中并混合均匀制得碱性激发剂;(2)将500kg玄武岩尾矿(粒度在165.5μm以下的颗粒的质量含量为85%)和500kg一级粉煤灰在搅拌机中进行干混3min,然后加入130kg碱性激发剂和50kg水,混匀搅拌10min得到混合料,将混合料倒进制砖机中在5mpa下压制3min成型。成型后的砖坯移入室内通风养护28天,制得尾矿砖。所得成品无侧限抗压强度达到13.9mpa,密度1.70kg/m3,吸水率、饱和系数、抗冻性能、抗软化性能、耐碱性不能达到国标《非烧结垃圾尾矿砖》mu15级别。从上述试验结果可以看出,当本发明的各组分的用量不在本发明的提出的范围内,以及粒度在165.5μm以下的玄武岩尾矿颗粒的质量含量低于90%时,所制得的尾矿砖的性能将明显变劣。以上结合实施例详细描述了本发明的优选实施方式,但是,本发明并不限于上述实施方式中的具体细节,在本发明的技术构思范围内,可以对本发明的技术方案进行多种简单变型,这些简单变型均属于本发明的保护范围。另外需要说明的是,在上述具体实施方式中所描述的各个具体技术特征,在不矛盾的情况下,可以通过任何合适的方式进行组合,为了避免不必要的重复,本发明对各种可能的组合方式不再另行说明。此外,本发明的各种不同的实施方式之间也可以进行任意组合,只要其不违背本发明的思想,其同样应当视为本发明所公开的内容。当前第1页12