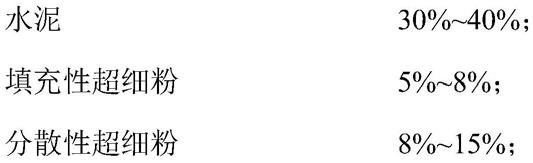
1.本发明属于水泥基材料技术领域,具体来讲,涉及一种海上风电导管架用水泥基灌浆料,以及该水泥基灌浆料的应用。
背景技术:2.随着我国海上风电建设的发展,风电场建设选址逐渐从潮间带走向海上,离岸距离越来越远、单机功率更高、矗立高度更大、水深持续增加、海况更趋复杂,设备基础承载、稳定要求的提高对灌浆连接技术提出更大的挑战。目前世界范围内采用的海上风电基础型式包括单桩基础、多角架基础、导管架基础、重力式基础、漂浮式基础等结构型式;而采用单桩基础、多角架基础、导管架基础及重力式基础,风机基础和钢管桩连接是通过灌浆方式进行,灌浆技术作为风机基础安装的重要关键技术,其灌浆质量将直接影响到桩基的整体稳定性能和安全性。灌浆连接段在结构上起到承上启下作用,施工上起到承前启后作用,通过灌浆连接,可降低风机安装误差、减少疲劳损伤。
3.由于灌浆连接段特殊的服役环境及施工工艺,要求灌浆料具有大流态性、超高强、高弹性模量、高早强、抗疲劳性等性能。大流态有利于灌浆料水下施工灌注,确保灌浆施工的连续通畅,而灌浆料的抗压强度与灌浆连接段轴压承载力密切相关,灌浆料抗压强度越高,相应灌浆连接段极限黏结强度越高,两者呈正相关。
4.灌浆料弹性模量反映的是材料受荷载时抵抗变形的能力,高的弹性模量意味着相同荷载作用下灌浆料较小的体积变形,进而保证灌浆连接段在外力荷载作用下处于安全可控的变形范围内。超高强灌浆料主要通过水泥、高强骨料以及超细粉体基于最紧密堆积原理配制而成,而细骨料的表观密度、硬度和弹性模量显著影响灌浆料的抗压强度及弹性模量。细骨料的表观密度越大、硬度越大、在灌浆料中的体积占比越高,相应灌浆料强度越高、弹性模量越大;但同时带来灌浆料浆液容重偏大,一方面在大流态下灌浆料体系容重较大导致骨料浆体密度差异较大,引起骨料沉降分离,另一方面较高的容重增加了灌浆料单方用量,成本增加。因此,在大流态情况下,兼顾实现灌浆料的低容重、高强高弹性模量等性能是当前应用中的迫切技术需求。
5.目前针对灌浆料的研究,主要是针对抗压强度进行的,但这些技术虽然达到了较大的28d抗压强度,却还存在其他方面的弊端。如一种水泥基超高强无收缩灌浆料,其常温下28d的抗压强度可达120mpa,但该灌浆料基体采用钢纤维增强,不适合于对灌浆料流动性及泵送性能要求较高的应用环境,且在海上风电场应用过程中钢纤维的加入可能带来氯离子侵蚀等耐久性问题;又如一种高强超流态膨胀水泥灌浆料,其标养28d抗压强度可以达到90mpa,但早期强度偏低,1d抗压强度只有20mpa,不利于施工的高效进行;再如一种超高强水泥材料的制作方法,其抗压强度可以达到150mpa,但材料流动性较差、无法实现自流平且泵送困难,且需要特殊的热压制作工艺,不具备现场应用的条件。在水泥基灌浆料的性能设计上,大流态是最基本的施工要求,在此基础上需满足超高强这一力学性能,继而对高弹性模量和低容重等方面提出进一步的需求。虽然目前存在海上风电导管架灌浆材料及其施工
方法的相关研究报道,但该技术无法实现灌浆料标养制度下兼顾超高强及高弹性模量的性能指标,也未对容重进行说明,且灌浆料的制备需要二次搅拌预混、搅拌时间较长,影响材料的使用效率。
6.然而,基于一般水泥基灌浆料的设计方法中弹性模量与容重的影响关系,难以兼顾高弹性模量与低容重的性能需求;因此,亟待开发一种用于海上风电灌浆连接、在满足流变的前提下,兼顾高弹性模量与低容重的超高强水泥基灌浆料。
技术实现要素:7.为解决上述现有技术存在的问题,本发明提供了一种海上风电导管架用水泥基灌浆料,该水泥基灌浆料通过骨架设计、胶凝材料匹配以及界面改善的协同作用,实现了弹性模量与容重可调的目的,能够保证该水泥基灌浆料在静弹性模量介于50gpa~60gpa时,浆液容重在2400kg/m3~2900kg/m3之间变化。
8.为了达到上述发明目的,本发明采用了如下的技术方案:
9.一种海上风电导管架用水泥基灌浆料,其包括下述按质量百分数混合的各组分:
[0010][0011][0012]
其中,所述砂选自低密骨料、中密骨料和高密骨料中的至少两种,且在不超过1.18mm、1.18mm~2.36mm和2.36mm~4.75mm三级粒径范围内连续级配;所述低密骨料为黄砂和/或石英砂,所述中密骨料为石灰岩和/或玄武岩,所述高密骨料选自矾土、金刚砂、白刚玉、棕刚玉、碳化硅中的至少一种;所述砂的最大粒径小于4.75mm,体积密度为2.5g/cm3~3.9g/cm3,吸水率不超过4%。
[0013]
进一步地,所述填充性超细粉选自硅灰、沸石超细粉、超细稻壳灰中的任意一种或任意两种的混合物,且所述填充性超细粉的比表面积大于15000m2/kg。
[0014]
进一步地,所述分散性超细粉选自超细粉煤灰、超细石灰石粉、硅微粉、玻璃粉、超细矿粉、偏高岭土中的至少两种的混合物,且所述分散性超细粉的平均粒径为2μm~15μm。
[0015]
进一步地,所述纳米材料选自纳米二氧化硅、纳米碳酸钙、纳米碳纤维、碳纳米管、纳米金属氧化物中的任意一种或任意两种的混合物。
[0016]
进一步地,所述水泥基灌浆料的起初始流动度不低于280mm,在20℃水养28d后的抗压强度大于150mpa、抗折强度大于22mpa,静弹性模量为50gpa~60gpa,容重为2400kg/m3~2900kg/m3。
[0017]
进一步地,所述复合膨胀组分为质量比为1~1.8:100的塑性膨胀剂与多活性硬化阶段复合膨胀剂的混合物;其中,所述多活性硬化阶段复合膨胀剂由高活性mgo、中活性mgo、低活性mgo混合而成。
[0018]
进一步地,所述消泡剂为有机硅类消泡剂。
[0019]
进一步地,所述超塑化剂为聚羧酸高性能减水剂,减水率不低于35%。
[0020]
进一步地,所述分散剂为质量比为1:2的三聚磷酸钠与六偏磷酸钠的混合物。
[0021]
本发明的另一目的还在于提供一种如上任一所述的水泥基灌浆料的应用方法,将所述水泥基灌浆料与水直接拌合;其中,水料比为0.085:1~0.095:1。
[0022]
本发明通过骨架设计、胶凝材料匹配以及界面改善的协同作用,制备出容重及弹性模量可调的水泥基灌浆料,该水泥基灌浆料具有大流态及超高的力学性能,起初始流动度不低于280mm,20℃水养28d后抗压强度不低于150mpa、抗折强度大于22mpa,且其在静弹性模量介于50gpa~60gpa时,浆液容重在2400kg/m3~2900kg/m3之间变化,真正实现了水泥基灌浆料的容重及弹性模量可控可调的目的,解决了浆液容重及弹性模量不可兼顾的难题。本发明的水泥基灌浆料在应用时仅需与拌合用水直接拌合即可,无需进行二次搅拌预混,搅拌时间短。
具体实施方式
[0023]
以下,将来详细描述本发明的实施例。然而,可以以许多不同的形式来实施本发明,并且本发明不应该被解释为限制于这里阐述的具体实施例。相反,提供这些实施例是为了解释本发明的原理及其实际应用,从而使本领域的其他技术人员能够理解本发明的各种实施例和适合于特定预期应用的各种修改。
[0024]
针对现有技术中一般的水泥基灌浆料无法在保证流动性和超高强的前提下,进一步兼顾高弹性模量和低容重这一弊端,本发明通过骨架设计、胶凝材料匹配和界面改善的协同作用,配制出了具有大流态及超高力学性能、且兼顾容重和弹性模量的水泥基灌浆料,该灌浆料尤为适用于海上风电导管架连接使用。
[0025]
具体参阅下述表1,其示出了本发明的海上风电导管架用水泥基灌浆料的各组分及其含量。
[0026]
表1水泥基灌浆料的组分及含量wt%
[0027][0028]
要特别值得注意的是,在本发明的水泥基灌浆料的上述配比中,砂的具体配比最为关键。砂选自低密骨料、中密骨料和高密骨料中的至少两种,低密骨料选自黄砂、石英砂中的至少一种,中密骨料选自石灰岩、玄武岩中的至少一种,高密骨料选自矾土、金刚砂、白刚玉、棕刚玉、碳化硅中的至少一种;并且控制砂的最大粒径小于4.75mm,体积密度为2.5g/
cm3~3.9g/cm3,吸水率不超过4%。更为具体地,上述砂的粒径由不超过1.18mm、1.18mm~2.36mm和2.36mm~4.75mm三级连续级配形成。即该砂的组成一方面要遵循上述高、中、低密骨料中至少选择两种这一要求,又要符合该三级粒径进行连续级配的规则。
[0029]
在本发明的该水泥基灌浆料中,填充性超细粉选自硅灰、沸石超细粉、超细稻壳灰中的任意一种或任意两种的混合物,且该填充性超细粉的比表面积大于15000m2/kg;而分散性超细粉选自超细粉煤灰、超细石灰石粉、硅微粉、玻璃粉、超细矿粉、偏高岭土中的至少两种的混合物,且该分散性超细粉的平均粒径为2μm~15μm。
[0030]
上述表1中所示的纳米材料可以是纳米二氧化硅、纳米碳酸钙、纳米碳纤维、碳纳米管、纳米金属氧化物中的任意一种或任意两种的混合物。
[0031]
如此,即通过骨架设计、胶凝材料匹配以及界面改善的协同作用,制备出了容重及弹性模量可调的超高强水泥基灌浆料。该水泥基灌浆料的起初始流动度不低于280mm,在20℃水养28d后的抗压强度大于150mpa、抗折强度大于22mpa,且当其静弹性模量处于50gpa~60gpa的范围内时,容重可控制在2400kg/m3~2900kg/m3的范围内变化。
[0032]
具体来讲,本发明的该水泥基灌浆料,其通过下述原理及作用实现上述效果:
[0033]
首先,在骨架设计方面。根据骨料化学组成及体积密度的差异将骨料种类划分为低密骨料(黄砂、石英砂)、中密骨料(石灰岩、玄武岩)和高密骨料(矾土、金刚砂、白刚玉、棕刚玉、碳化硅)三类;骨料粒径包含不超过1.18mm、1.18mm~2.36mm以及2.36mm~4.75mm三档;高密骨料主要起骨架增强及提升基体刚度作用,低密骨料主要起调节浆液容重及改善流动性作用,中密骨料兼具两者作用。在骨料设计时,根据弹性模量与浆液容重技术要求,选择上述三类骨料中的两类及两类以上骨料,基于最紧密堆积原理,优选各种骨料的最佳比例及粒径,以获得最小堆积空隙率和最佳流动性,同时实现弹性模量及浆液容重的指标。
[0034]
然后,在超高强灌浆料制备方面。单单依靠骨料体系设计并不能实现大流态、超高强的性能指标要求,仍需要粉料体系协同作用进一步优化来实现流变及力学性能的兼顾。引入填充性超细粉,其水化反应活性较高,促进胶凝体系的二次水化反应进程,而较小的微纳米颗粒尺寸更易获得最优紧密堆积效果且可填充基体微结构缺陷,较大的比表面积使其具有吸水增稠作用,避免大流态可能带来的骨浆分离。此外,分散性超细粉主要起降粘分散、降低水化放热作用,其颗粒粒径介于填充性超细粉的硅灰与水泥之间,适当引入一方面有利于改善流动状态及优化胶凝材料体系颗粒级配进一步密实基体,另一方面其化学组成主要为二氧化硅和氧化铝,其掺量可起到调整浆液容重及基体弹性模量作用。
[0035]
再次,采用纳米材料,利用其超细纳米尺寸、超高反应活性及微成核效应,进一步填充微结构空隙、促进胶凝材料的水化进程及水化产物的成核结晶。此外,超细粉体分散剂提高了纳米材料及超细粉体在基体中的分散性,减少因超细颗粒团聚引起的内部缺陷。
[0036]
最后,在界面改善方面。中、高密骨料吸水且为多孔结构,在基体水化过程中起内养护作用,而骨料较高的表面粗糙度亦增加界面黏结强度。填充性超细粉的微观形貌均为多孔微纳米材料,一方面其超细颗粒尺寸填充基体缺陷,另一方面其多孔结构在水化早期吸收部分自由水,降低骨料表面水膜层厚度、缩小骨料表面区域水胶比梯度差异,减少界面多孔通道,且随着水化的不断进行,释放自由水促进水化产物进一步水化形成高密度产物,从而改善薄弱界面过渡区域提高基体密实度。
[0037]
进一步地,上述表1中水泥可以是强度等级为52.5及以上的硅酸盐水泥或普通硅
酸盐水泥;复合膨胀组分为质量比为1~1.8:100的塑性膨胀剂与多活性硬化阶段复合膨胀剂的混合物;其中,多活性硬化阶段复合膨胀剂由高活性mgo(反应时间≤120s)、中活性mgo(反应时间为120s~180s)、低活性mgo(反应时间为180s~220s)混合而成;消泡剂为有机硅类消泡剂,如可以是德国明凌化学p803粉末消泡剂;超塑化剂为聚羧酸高性能减水剂,减水率不低于35%,如可以是江苏苏博特新材料股份有限公司生产的-300p粉体聚羧酸高性能减水剂;分散剂为质量比为1:2的三聚磷酸钠与六偏磷酸钠的混合物。
[0038]
本发明还提供了上述水泥基灌浆料的应用方法,即将水泥基灌浆料中各粉体成分于搅拌机内混合均匀,继而与水直接拌合即可;一般来讲,控制水料比为0.085:1~0.095:1。
[0039]
以下将通过具体的实施例来体现本发明的上述水泥基灌浆料的组成,实施例1-5中各水泥基灌浆料的组分及其含量如表2所示。
[0040]
表2实施例1-5中水泥基灌浆料的组分及含量wt%
[0041][0042]
上述实施例1-5中的水泥均采用p
·ⅱ52.5硅酸盐水泥;复合膨胀组分均为质量比为1.5:100的塑性膨胀剂与多活性硬化阶段复合膨胀剂的混合物,其中,多活性硬化阶段复合膨胀剂均由质量比为1:1:1的高活性mgo、中活性mgo、低活性mgo混合而成;消泡剂均为德国明凌化学p803粉末消泡剂;超塑化剂均为江苏苏博特新材料股份有限公司生产的-300p粉体聚羧酸高性能减水剂;分散剂均为质量比为1:2的三聚磷酸钠和六偏磷酸钠的混合物。
[0043]
上述实施例1-5中的填充性超细粉、分散性超细粉、纳米材料、砂分别如表3-6所示。
[0044]
表3实施例1-5中填充性超细粉的组成
[0045][0046]
表4实施例1-5中分散性超细粉的组成
[0047][0048][0049]
表5实施例1-5中纳米材料的组成
[0050][0051]
表6实施例1-5中砂的组成
[0052][0053]
注:表6中一级表示粒径不超过1.18mm的骨料,二级表示粒径为1.18mm~2.36mm的骨料,三级表示粒径为2.36mm~4.75mm的骨料。
[0054]
为了验证本发明的上述水泥基灌浆料的优异性能,进行了下述对比实验。该对比实验以上述实施例3中水泥基灌浆料的组分为基准,分别改变了砂的组成,及缺少填充性超细粉、分散性超细粉、纳米材料即分散剂,并将缺少的质量补充至水泥的含量处。对应获得的对比例1-5的组成及含量如表7所示。
[0055]
表7对比例1-5中对比水泥基灌浆料的组分及含量wt%
[0056][0057][0058]
上述对比例1中的砂与实施例3中的砂的组成的不同之处在于:本对比例中的砂全部为普通黄砂,而并非如实施例3中的不同密度骨料及粒径级配。
[0059]
将上述实施例1-5获得的水泥基灌浆料及对比例1-5获得的对比水泥基灌浆料,按照水料比为0.092:1经水拌合,分别测试浆液容重、流动度、抗折强度、抗压强度以及静弹性模量。其中流动度、抗折强度及抗压强度测试方法参照gb/t 50448《水泥基灌浆材料应用技术规范》,浆液容重测试方法参照gb/t 50080-2016《普通混凝土拌合物性能试验方法标准》,静弹性模量测试方法参照gb/t 50081-2002《普通混凝土力学性能试验方法标准》。
[0060]
上述实施例1-5中水泥基灌浆料及对比例1-5中对比水泥基灌浆料的各性能测试结果如表8所示。
[0061]
表8实施例1-5中水泥基灌浆料及对比例1-5中对比水泥基灌浆料的测试结果
[0062][0063]
根据表8中实施例1-5的数据可以看出,本发明所提供的水泥基灌浆料在无纤维增强标准养护28d时可实现大流态、超高强以及容重和弹性模量兼顾的性能指标。
[0064]
将表8中对比例1-5的数据分别与实施例3的数据进行对比,可以看出,对比例1中虽然对比水泥灌浆料的流动度较好、浆液容重小,但其力学性能均明显低于实施例3中的水泥基灌浆料;可见砂的具体配制规则对最终获得的水泥基灌浆料的力学性能影响很大。对比例2中缺少填充性超细粉,填充性超细粉其水化反应活性较高,促进胶凝体系的二次水化反应进程,且较小的微纳米颗粒尺寸更易获得最优紧密堆积效果且可填充基体微结构缺陷,较大的比表面积使其具有吸水增稠作用,避免大流态可能带来的骨浆分离;因此缺少填充性超细粉后获得的对比吐尼基灌浆料的流动性显著增大,即增加了骨浆分离的风险,且抗压强度、抗折强度和弹性模量也均存在不同程度的降低。对比例3中缺少分散性超细粉,分散性超细粉主要起降粘分散、降低水化放热作用,不仅有利于改善流动状态及优化胶凝材料体系颗粒级配进一步密实基体,而且起到调整浆液容重及基体弹性模量作用;缺少分散性超细粉后获得的对比水泥基灌浆料的流动性劣化、粘度增大,不利于泵送施工,且其弹性模量亦下降。对比例4中缺少纳米材料,其抗压强度和抗折强度远低于实施例3;纳米材料由于其超小纳米尺寸、超高反应活性及微成核效应,进一步填充微结构空隙、促进胶凝材料的水化进程及水化产物的成核结晶,缺少纳米材料后获得的对比水泥基灌浆料的力学性能即降低。对比例5中缺少分散剂,分散剂提高了纳米材料及两类超细粉体(填充性超细粉和分散性超细粉)在基体中的分散性,减少因超细颗粒团聚引起的内部缺陷,性能数据显示缺少分散剂后获得的对比水泥基灌浆料的流动性及力学性能全面下降,基体内超细粉易团聚而形成内部缺陷,超细粉的团聚亦带来自由水无法释放,浆体粘度增大、含气量增大,力学性能进一步降低。
[0065]
可见,本发明的该水泥基灌浆料通过骨架设计、胶凝材料匹配以及界面改善的协同作用,从而达到了在保证流动性和超高强的前提下,进一步兼顾容重及弹性模量可调的效果,这些成分在搭配上相互影响,而并非是单独存在的。
[0066]
虽然已经参照特定实施例示出并描述了本发明,但是本领域的技术人员将理解:在不脱离由权利要求及其等同物限定的本发明的精神和范围的情况下,可在此进行形式和细节上的各种变化。