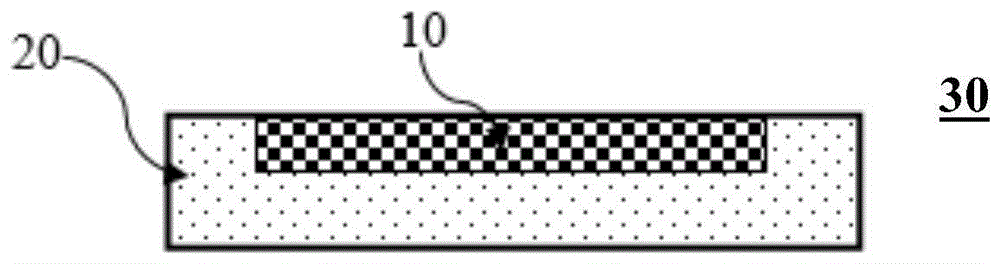
本发明涉及连铸用材料
技术领域:
,具体尤其涉及一种新型耐冲刷耐热震式冲击砖,用于制作中间包的冲击区或稳流器。
背景技术:
:连铸作为炼钢生产的重要环节,是整个炼钢系统实现高效低成本生产的基础和保障。而中间包浇注,是将液态钢水转变为固态的过程,它是连铸过程中的关键性工艺程序。中间包在连铸过程中承接钢水、钢水分流、促进钢水中夹杂物上浮等作用的重要功能性容器。中间包的长使用寿命、安全稳定性是保证连铸生产效率的关键因素,而中间包底部的冲击区是决定中间包使用寿命的关键部位。冲击砖是用于制作中间包的冲击区的重要耐火材料。现有冲击砖主要使用在中间包内钢水浇注冲击区部位,该部位长期被高压钢水冲击,因此需要较高的抗钢水侵蚀性和热态强度。现有的冲击砖大多采用镁碳砖和铝镁碳砖,镁碳砖中因为镁砂的热膨胀较大容易导致剥落断裂,铝镁碳砖存在总体强度不高等问题,另外上述产品在浇注钢水时均会对钢水造成一定污染,由于其中碳含量较高尤其不适合冶炼优质特种钢等品种。为满足连续浇钢的要求,在钢水液面过低时冲击砖存在多次开浇问题,普通冲击砖容易发生穿孔、漏钢等事故。因此,提高冲击砖的耐冲刷性是这类材料的最重要的技术要求。技术实现要素:(一)要解决的技术问题鉴于现有技术的上述缺点,本发明提供一种新型耐冲刷耐热震式冲击砖,该冲击砖以冲压成型和浇注成型相结合,并优化材料组合,不仅实现了废旧耐火材料的循环使用,同时提高冲击砖的耐冲刷性能,使冲击砖的耐连续冲刷时间达到现有镁碳砖或铝镁碳砖的3-5倍以上。(二)技术方案为了达到上述目的,本发明采用的主要技术方案包括:第一方面,本发明提供一种新型耐冲刷耐热震式冲击砖,其包括:冲压成型板和浇注成型体;所述冲压成型板的原料组成包括:金属硅粉、金属铝粉、碳化硅、致密刚玉、铝镁尖晶石和粘合剂;所述冲压成型板是采用压力机一体冲压成型;所述浇注成型体为采用浇注料经模具浇注、振动成型、养护、脱模、烘烤制得;所述浇注成型体的原料组成包括:废旧钢玉颗粒、白钢玉细粉、铝钙水泥微粉、活性铝粉、微硅粉、减水剂和水;所述冲压成型板预先固定在模具内的预定位置,使浇注料填充在所述冲压成型板的周围,所述浇注成型体与所述冲压成型板一体浇注成型。根据本发明的较佳实施例,其中,所述冲压成型板的原料中,所述粘合剂为酚醛树脂,其用量为原料总质量的4-6%。根据本发明的较佳实施例,其中,所述冲压成型板的原料组成为:所述金属硅粉用量为5-8质量份、金属铝粉1-5质量份、碳化硅10-15质量份、致密刚玉30-60质量份、铝镁尖晶石15-25质量份。致密刚玉是采用高纯氧化铝和还原剂按一定配比在电弧炉内经高温熔融后冷却而成的一种新型高纯耐火原料。致密刚玉是一种高档耐火材料,主晶相为α-al2o3,颜色为灰白色。产品有熔点高、体积密度大以及气孔率低的特点,在高温下具有优良的耐磨性、抗渣性、体积稳定性和抗热震性能,被认为是刚玉系列中最优秀的耐火原材料。进一步优选地,冲压成型板的原料组成为:金属硅粉用量为5-6质量份,金属铝粉2-3质量份、碳化硅8-10质量份、致密刚玉50-60质量份和铝镁尖晶石20-25质量份。其中,上述各材料可为市售规格。例如,金属硅粉的颗粒粒径为20~50μm,金属铝粉粒径为20-40目或60-100目或100-150目;碳化硅细粉的粒径<0.074mm;尖晶石为150-250目;致密刚玉粒径为0-1mm。根据本发明的较佳实施例,其中,所述冲压成型板镶嵌在所述浇注成型体的表面、内层或底面。根据本发明的较佳实施例,其中,所述冲压成型板是在1200吨以上压力下一体冲压成型,经烘烤至300-350℃冷却后备用。根据本发明的较佳实施例,其中,所述冲压成型板的尺寸为20~80cm*20~80cm*5~20cm。根据本发明的较佳实施例,其中,浇注成型体的原料组成为:5-8mm的废旧刚玉30-45质量份、3-5mm的废旧刚玉10-18质量份、1-3mm的废旧刚玉10-18质量份、0-1mm的废旧刚玉8-20质量份;白刚玉细粉为20-30质量份,铝钙水泥微粉为3-8质量份,活性铝粉3-8质量份,微硅粉2-5质量份,减水剂0.2-1质量份;所述白刚玉细粉、铝钙水泥微粉、活性铝粉、微硅粉的粒径均为过200目筛;用水量为前述各项质量总和的5-8%。上述各种不同规格的废旧刚玉的用量配比,主要是将废旧刚玉的粒径进行分级,然后根据废旧刚玉尽可能获得最大的堆积密度的配比进行级配,如此有利于获得抗冲击性能最优的浇注成型体。根据本发明的较佳实施例,其中,在所述冲击砖中,所述冲压成型板的数量为2块或2块以上,叠合设置。通过叠合预埋在浇注成型体的模具中,使浇注成型体将冲压成型板一体浇注成型在其内部。另一方面,本发明还提供一种新型耐冲刷耐热震式冲击砖的制备方法,其包括如下步骤:s1:将金属硅粉5-8质量份、金属铝粉1-5质量份、碳化硅10-15质量份、致密刚玉30-60质量份和铝镁尖晶石15-25质量份混合,再加入4-6%的酚醛树脂,球磨均匀,在1200吨以上压力机上一体冲压成型,得到尺寸为20~80cm*20~80cm*5~20cm的冲压成型板;经烘烤至300-350℃冷却后备用;s2:将规格5-8mm的废旧刚玉30-45质量份、规格3-5mm的废旧刚玉10-18质量份、规格1-3mm的废旧刚玉10-18质量份、规格0-1mm的废旧刚玉8-20质量份、减水剂0.2-1质量份、过200目筛的白刚玉细粉为20-30质量份、过200目筛的铝钙水泥微粉为3-8质量份、过200目筛的活性铝粉3-8质量份,过200目筛的微硅粉2-5质量份混合,得到干混料;s3:加入占干混料质量5-8%的水,拌和均匀,得到浇注料;s5:将模具固定在振动机的振动平台上,模具内表面刷脱模剂,在模具中预定位置安装步骤s1得到的冲压成型板,将所述浇注料浇注到模具中振动成型,养护、脱模、烘烤制得所述冲击砖。其中,s3的拌和时间为8-12min。其中,s4的振动成型时间为30-40min,以确保浇注料的流动性。浇注料在加入到模具中时至成型结束,振动平台始终处于振动状态,以保证浇注料的密实和气体的充分排出。养护的环境温度优选为≥40℃,更优选为40-60℃;养护的环境湿度优选为≤50%,更优选为20-50%。养护包括脱模前养护和脱模后养护,脱模前养护20-30h,脱模后养护10-16h。烘烤的时间为24-32h,能够确保材料内部的水分充分排出至干燥。烘烤温度可为多阶段温度烘烤,第一阶段由25℃升至60℃,升温速率为12-15℃/h,第一阶段保温在60℃下2-3h;第二阶段60℃升至140℃,升温速率为10-12℃/h,第二阶段保温在140℃下2-3h;第三阶段140℃升至180℃,升温速率为10℃/h,第三阶段保温在180℃下2h;第三阶段180℃升至220℃,升温速率为12-15℃/h,第三阶段保温在220℃下6-7h。通过上述细化的多阶段温度烘烤,可保证冲击砖在水分的充分排出同时避免材料内部、材料与所述冲压成型板之间产生裂纹。再一方面,本发明提供一种稳流器,其用于连铸中间包,用以平稳中间包钢水液面,所述稳流器包括本体和设于本体内底面或冲击侧面上的冲击砖;所述冲击砖为上述人以实施例所述的冲击砖。通过设置本发明的冲击砖,可大幅延长稳流器的耐冲刷寿命,降低浇注成本和提高浇注效率。(三)有益效果(1)本发明的主要技术特点在于,将冲压成型和浇注成型相结合,得到一体浇注成型包覆冲压成型板的复合式冲击砖,该冲压成型板作为冲击砖的基本骨架,而可解决普通浇注砖不耐钢水冲蚀、容易发生开裂、穿孔、漏钢事故等问题,相较于普通的镁碳砖和铝镁碳砖,本发明的冲击砖具有更优的耐冲刷性和安全性。(2)本发明进一步通过材料的优化组合,使冲压成型板和浇注成型体都具有较高的抗钢水侵蚀性和热态强度(耐热震性)。此外,本发明所选用的材料为不含碳或含碳量极低的组分,不会污染钢液,尤其适于冶炼优质特种钢等品种。经实际生产可知,使用本发明的冲击砖相较于普通的镁碳砖和铝镁碳砖,能满足3次以上开浇,使用寿命(连续冲刷时间)提高了3-5倍以上。(3)将本发明的冲击砖安装在中间包的冲击区,可以抵挡多次连浇、串浇,保证中间包的安全运行,减少事故的发生;此外,本发明回收使用了废旧刚玉颗粒,可在满足多次串浇及连浇的基础上,使冲击砖成本降低,且由于耐冲蚀性提高,可防止多次开浇造成冲击砖穿孔、发生漏钢,有利于保障安全生产,且使中间包和连铸工艺的整体成本降低。附图说明图1为本发明冲击砖的结构示意图一。图2为本发明冲击砖的结构示意图二。图3为本发明冲击砖的结构示意图三。图4为本发明冲击砖的结构示意图四。图5为本发明较佳实施例1的稳流器的结构示意。图6为本发明较佳实施例2的稳流器的结构示意。图7为本发明较佳实施例3的稳流器的结构示意。图8为本发明较佳实施例4的稳流器的结构示意。图9为本发明较佳实施例5的稳流器的结构示意。具体实施方式为了更好的解释本发明,以便于理解,下面结合附图,通过具体实施方式,对本发明作详细描述。本发明的主要技术方案在于,将冲压成型和浇注成型相结合,得到一体浇注成型包覆冲压成型板的复合式冲击砖,该冲压成型板可解决普通浇注砖不耐冲蚀、容易发生穿孔、漏钢事故等问题。此外,本发明进一步通过优选冲压成型板和浇注成型体的原料及配合比例,进一步提高冲击砖的抗钢水侵蚀性和耐热震性。具体地,先将冲压成型原料拌合均匀,并装填到压力成型模具中,振实,设定冲压机压力大小,采用压力机采用超过1200吨压力冲压得到预定尺寸的一体冲压成型板10,如尺寸为20~80cm*20~80cm*5~20cm,优选为35cm*35cm*7cm。然后,按照浇注成型的干原料组成混合,最后加水拌和成浇注料,将该冲压成型板预设在浇注成型模具的预定位置,浇注后强烈振动以振实密度,成型后养护、脱模、再养护,最后烘烤得到冲击砖30。该冲击砖的浇注成型体20将预埋件冲压成型板10一体浇注包覆在其内部,冲压成型板10被镶嵌在浇注成型体20的表面、底面或中间。如图1-3所示。再如4所示,在冲击砖30中,冲压成型板10的数量可为2块或2块以上,叠合设置,以进一步增强冲击砖30整体的抗钢水冲蚀和耐热震性能。具体地,可通过叠合预埋在浇注成型体20的模具中,使浇注成型体20将冲压成型板10一体浇注成型在其内部。本发明中,冲压成型板的原料组成包括:金属硅粉、金属铝粉、碳化硅、致密刚玉、铝镁尖晶石和粘合剂,粘合剂可为酚醛树脂。具体地,冲压成型板的原料组成为:金属硅粉的用量5-8质量份、金属铝粉1-5质量份、碳化硅10-15质量份、致密刚玉30-60质量份、铝镁尖晶石15-25质量份。粘合剂的用量为原料总质量的4-6%,优选为5%。酚醛树脂在烘烤至300-350℃时大量分解,350℃几乎可完全分解。优选地,冲压成型板的原料组成为:金属硅粉用量为5-6质量份,金属铝粉2-3质量份、碳化硅8-10质量份、致密刚玉50-60质量份和铝镁尖晶石20-25质量份;进一步优选地,金属硅粉用量为5质量份,金属铝粉3质量份、碳化硅10质量份、致密刚玉60质量份和铝镁尖晶石25质量份。按照这个比例制备的冲压成型板,在相同厚度相同中间包中的抗钢水侵蚀能力最强、侵蚀最缓慢。本发明中,浇注成型体的原料组成包括:废旧钢玉颗粒、白钢玉细粉、铝钙水泥微粉、活性铝粉、微硅粉、减水剂和水。具体地,浇注成型体的原料组成为:5-8mm的废旧刚玉30-45质量份、3-5mm的废旧刚玉10-18质量份、1-3mm的废旧刚玉10-18质量份、0-1mm的废旧刚玉8-20质量份;白刚玉细粉为20-30质量份,铝钙水泥微粉为3-8质量份,活性铝粉3-8质量份,微硅粉2-5质量份,减水剂0.2-1质量份;所述白刚玉细粉、铝钙水泥微粉、活性铝粉、微硅粉的粒径均为过200目筛;用水量为前述各项质量总和的5-8%。其中,上述各材料可为市售规格。例如,金属硅粉的颗粒粒径为20~50μm,金属铝粉粒径为20-40目或60-100目或100-150目;碳化硅细粉的粒径<0.074mm;尖晶石为150-250目;致密刚玉粒径为0-1mm。减水剂可采用木质素磺酸盐、萘磺酸盐甲醛聚合物、六偏磷酸钠等。减水剂能减少拌合用水量,对水泥颗粒有分散作用,能改善其工作性能,减少单位用水量,改善混凝土拌合物的流动性;或减少单位水泥用量,节约水泥。本发明新型耐冲刷耐热震式冲击砖30可直接安装在中间包底部的冲击区,以提高冲击区的耐热钢水冲蚀性能,增加中间包的使用次数。此外,如图5-图9所示的,本发明的新型耐冲刷耐热震式冲击砖30还可用于制作稳流器。稳流器安装在中间包的预定位置(钢液从大包注入的位置),其作用主要是将钢液注流引起的强烈涡流限制在中间包的冲击区局部位置,减少钢水飞溅、湍流和卷渣的几率,促进钢水内夹杂物的上升,从而减少夹杂物。如图5所示,为本发明实施例1的稳流器100。其包括铝镁质稳流器本体101和稳流器底部102。该本体101的截面为圆形,内部为空腔,上方设有口部103,本体101四周设有稳流器壁105,稳流器壁105概呈横向的u字形,口部103的直径小于稳流器底部102的直径。稳流器壁105包括依次连接的倾斜段1051,平直段1052,凸弧段1053,外扩段1054。其中倾斜段1051和稳流器底部102连接,凸弧段1053使本体101的口腔在该处形成一个收缩部位。钢液从大包注入到稳流器100时,首先冲击稳流器底部102,然后向四周分散蔓延,随着稳流器壁105顺势流动,最后从口部103溢出。该过程可消耗钢液注入过程中的动能,使钢液快速挥发平静,减少其湍流和卷渣的几率,同时也让温度场分布更为均匀。而凸弧段1053对钢水具有挡渣作用。因此,稳流器底部102首当其冲地收到钢液的冲击。在该部位安装了本发明的耐冲刷耐热震式冲击砖30,该冲击砖30下沉一小段距离,该冲击砖30与稳流器底部102之间的缝隙用耐火泥抹平。如图6所示,为本发明实施例2的稳流器200,包括稳流器本体201,内部设有稳流腔203,稳流腔203的底部镶嵌设有冲击砖30,稳流腔203内还设有导流墙202,可以对钢水进行导流和缓冲。导流柱202上部为凸弧形,稳流腔203截面为圆形,稳流腔203一侧设有溢流口204。导流墙202的一侧面镶嵌有冲击砖30。导流墙202的两端不与稳流器本体201内壁相接,间距形成流道。钢水从大包注入稳流腔203内,通过导流墙202进行导流,防止钢水飞溅,配合圆形稳流腔203优化钢水流场,促进钢液成分和温度的均匀。稳流器本体201本体采用铝镁质材料浇注成型,预留镶嵌沉槽,镶嵌冲击砖30后,缝隙用耐火泥抹平。如图7所示,为本发明实施例3的稳流器300,包括稳流器本体301,内部设有截面为正四边形的稳流腔302,该稳流腔302包括冲击底部303和缩小的开口304,开口304的内径小于稳流腔302的内径,该冲击底部303设为顶角为圆弧过渡的等腰三角形。使钢水冲击该底部303后随即向四周散开,在稳流腔302内钢液变得更加均匀,钢液从开口304溢出。受冲击最为厉害的部位为稳流腔302的内侧壁,在该部位镶嵌有冲击砖30。稳流器本体301本体采用铝镁质材料浇注成型,预留镶嵌沉槽,镶嵌冲击砖30后,缝隙用耐火泥抹平。如图8所示,为本发明实施例4的稳流器400,包括稳流器本体401,内部设有截面圆形的稳流腔402,该稳流腔402为圆台型,底部较大,而上部渐变缩小,稳流腔402包括一个开口4021,开口4021处形成缩径部,开口4021与稳流腔402的内壁之间形成一个斜坡过渡。稳流腔402的底部403上镶嵌有冲击砖30。稳流腔402一侧为溢流挡墙404,其低于周围其他挡墙的高度,挡墙404的上部为溢流口403。稳流器本体401本体采用铝镁质材料浇注成型,预留镶嵌沉槽,镶嵌冲击砖30后,缝隙用耐火泥抹平。稳流器400可降低大包主流对中间包冲击区的冲蚀程度,增加中间包使用寿命,有效改善中间包冲击区钢水流动形态,防止钢水稳流卷渣,提高钢水洁净度。如图9所示,为本发明实施例5的稳流器500,包括稳流器本体501,内部设有稳流腔502,稳流腔502包括一个开口5021,开口5021处形成向稳流腔502中心线凸起的挡块a。开口5021为钢液溢流口。稳流腔502的内侧壁和底部均设有本发明的新型耐冲刷耐热震性冲击砖30。稳流器本体501本体采用铝镁质材料浇注成型,预留镶嵌沉槽,镶嵌冲击砖30后,缝隙用耐火泥抹平。稳流器500可降低大包主流对中间包冲击区的冲蚀程度,增加中间包使用寿命,有效改善中间包冲击区钢水流动形态,防止钢水稳流卷渣,提高钢水洁净度。冲击砖30的外部浇注成型体20能够与浇注成型的稳流器本体501实现紧密粘接,冲击砖30内的冲压成型板10则具有很强的抗钢液侵蚀性能,延长该该稳流器500的使用寿命。以下将本发明部分具体实施例的耐冲刷耐热震式冲击砖30制备方法部分具体实施例。制备实施例一冲击砖30的制备方法包括如下步骤:s1:将金属硅粉6质量份,金属铝粉2质量份,碳化硅8质量份,致密刚玉50质量份,铝镁尖晶石20质量份混合,再加入5%的酚醛树脂,500rpm球磨20min均匀,在1200吨压力机上一体冲压成型,得到尺寸为50cm*50cm*7cm的冲压成型板;经烘烤至350℃冷却后备用。其中,金属硅粉的中值粒径为30μm,金属铝粉粒径为60-100目;碳化硅细粉的粒径<0.074mm;尖晶石为150-250目;致密刚玉粒径为0-1mm。s2:将规格5-8mm的废旧刚玉40质量份、规格3-5mm的废旧刚玉10质量份、规格1-3mm的废旧刚玉10质量份、规格0-1mm的废旧刚玉10质量份、减水剂六偏磷酸钠0.4质量份、过200目筛的白刚玉细粉为25质量份、过200目筛的铝钙水泥微粉6质量份、过200目筛的活性铝粉6质量份,过200目筛的微硅粉4质量份混合,得到干混料;s3:将干混料加入占干混料质量6%的水,拌和均匀,得到浇注料;s5:将模具固定在振动机的振动平台上,模具内表面刷脱模剂,在模具的中间部位的表面处固定冲压成型板,将浇注料浇注到模具中振动40min成型,40-60℃湿度40%条件下养护30h、脱模、脱模后按照前述条件养护12h,烘烤制得冲击砖,冲击砖厚度为40cm。烘烤温度可为多阶段温度烘烤,第一阶段由25℃升至60℃,升温速率为12-15℃/h,第一阶段保温在60℃下2h;第二阶段60℃升至140℃,升温速率为10-12℃/h,第二阶段保温在140℃下2h;第三阶段140℃升至180℃,升温速率为10℃/h,第三阶段保温在180℃下2h;第三阶段180℃升至220℃,升温速率为12-15℃/h,第三阶段保温在220℃下6h。制备实施例二冲击砖30的制备方法包括如下步骤:s1:将金属硅粉5质量份,金属铝粉3质量份,碳化硅10质量份,致密刚玉60质量份,铝镁尖晶石25质量份混合,再加入6%的酚醛树脂,500rpm球磨25min均匀,在1200吨压力机上一体冲压成型,得到尺寸为50cm*50cm*7cm的冲压成型板;经烘烤至350℃冷却后备用。其中,金属硅粉的中值粒径为40μm,金属铝粉粒径为60-100目;碳化硅细粉的粒径<0.074mm;尖晶石为150-250目;致密刚玉粒径为0-1mm。s2:将规格5-8mm的废旧刚玉45质量份、规格3-5mm的废旧刚玉12质量份、规格1-3mm的废旧刚玉12质量份、规格0-1mm的废旧刚玉8质量份、减水剂六偏磷酸钠0.5质量份、过200目筛的白刚玉细粉为20质量份、过200目筛的铝钙水泥微粉8质量份、过200目筛的活性铝粉8质量份,过200目筛的微硅粉8质量份混合,得到干混料;s3:将干混料加入占干混料质量6%的水,拌和均匀,得到浇注料;s5:将模具固定在振动机的振动平台上,模具内表面刷脱模剂,在模具的中间部位的表面处固定冲压成型板,将浇注料浇注到模具中振动40min成型,40-60℃湿度40%条件下养护24h、脱模、脱模后按照前述条件养护12h,烘烤制得冲击砖30,烘烤参见制备实施例一。冲击砖厚度为40cm。制备实施例三冲击砖30的制备方法包括如下步骤:s1:将金属硅粉5质量份,金属铝粉1.5质量份,碳化硅10质量份,致密刚玉47质量份,铝镁尖晶石25质量份混合,再加入5%的酚醛树脂,500rpm球磨25min均匀,在1200吨压力机上一体冲压成型,得到尺寸为50cm*50cm*7cm的冲压成型板;经烘烤至350℃冷却后备用。步骤s2-s5与制备实施二处理条件均相同。制备对比例一在实施例二的基础上,s1中完全去掉碳化硅。将金属硅粉5质量份,金属铝粉15质量份,致密刚玉55质量份,铝镁尖晶石23质量份混合,再加入6%的酚醛树脂,在1200吨压力机上一体冲压成型,得到尺寸为50cm*50cm*7cm的冲压成型板;经烘烤至350℃冷却后备用。步骤s2-s5与制备实施二处理条件均相同。制备对比例二在实施例二的基础上,s1中完全去掉金属铝粉。将金属硅粉5质量份,碳化硅10质量份,致密刚玉60质量份,铝镁尖晶石23质量份混合,再加入6%的酚醛树脂,500rpm球磨25min均匀,在1200吨压力机上一体冲压成型,得到尺寸为50cm*50cm*7cm的冲压成型板;经烘烤至350℃冷却后备用。步骤s2-s5与制备实施二处理条件均相同。制备对比例三在实施例二的基础上,s2中去掉活性铝粉。其他步骤和条件与制备实施二处理条件均相同。将以上实施例、对比例和市购同厚度的镁碳砖和铝镁碳砖安装在某钢铁厂中间包底部冲击区进行实际生产和性能测试,结果如下:冲击砖使用寿命冲击砖钢液侵蚀情况制备实施例一62h侵蚀12mm制备实施例二67h侵蚀11mm制备实施例三58h侵蚀16mm对比例一45h侵蚀27mm对比例二48h侵蚀24mm对比例三50h侵蚀21mm镁碳砖18h侵蚀40mm铝镁碳砖22h侵蚀40mm由以上表可知,使用本发明的冲击砖,可延缓冲击区的冲蚀速度,延长中间包的使用寿命。最后应说明的是:以上各实施例仅用以说明本发明的技术方案,而非对其限制;尽管参照前述各实施例对本发明进行了详细的说明,本领域的普通技术人员应当理解:其依然可以对前述各实施例所记载的技术方案进行修改,或者对其中部分或者全部技术特征进行等同替换;而这些修改或者替换,并不使相应技术方案的本质脱离本发明各实施例技术方案的范围。当前第1页12