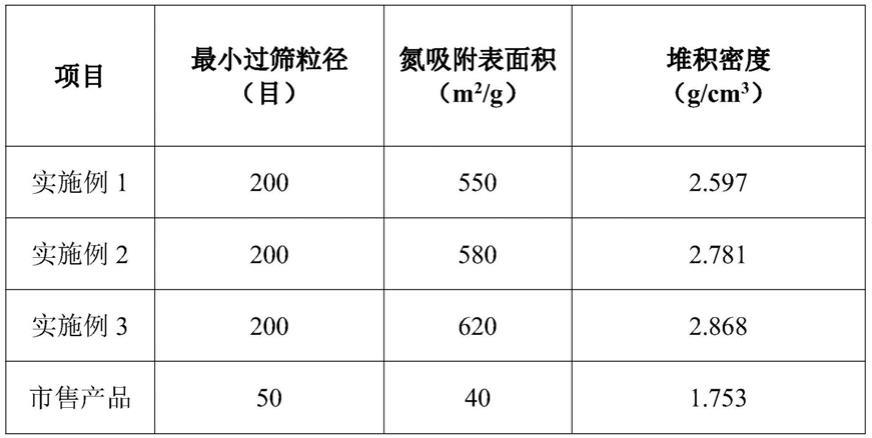
[0001]
本发明涉及氟化锂制备方法领域,尤其涉及一种超纯高活性电池级氟化锂的制备方法。
背景技术:[0002]
随着高纯氟化锂传统应用领域需求的日益增长及一些新的应用领域的不断出现(如将其应用于合成六氟磷酸锂的原料、远距离通信光纤材料等),高纯氟化锂的制备越来越为人们所重视,上世纪八十年代末,在国际上开始出现高纯氟化锂的制备技术的报道,先后介绍的方法有直接制备法、离子交换制备法、萃取制备法等。
[0003]
直接制备法是早期制备高纯lif的主要方法,原料一般为固体li2co3与氢氟酸溶液。这种方法原理简单,但对固体li2co3的质量要求很高,且所生成lif颗粒粒度分布极不均匀。后来,又有人提出用固体licl与brf3反应来制备高纯lif,但由于反应中使用了强氧化剂brf3,并生成了有害气体cl2及brcl,从而使这种方法的应用也受到了极大限制。另外,也有人尝试用li2so4溶液与氢氟酸或氢氟酸的盐反应来制备高纯lif。上述方法工艺流程比较简单,并且制得的lif产品也基本满足当时对高纯lif的要求,但随着对高纯lif质量要求的日益提高,特别是对一些过渡金属元素杂质含量要求的日益严格,这些方法已有被淘汰的趋势。
[0004]
离子交换制备法是将原料用离子交换法除杂后再来制备高纯lif的方法。1961年公布的美国专利中,robert等人详细介绍了用离子交换法来纯化可溶性锂盐的方法(us2980499),后来,robert又在制备高纯lif时首次使用了这种方法(us3179495),其制备高纯lif的过程可用方程式表示如下:
[0005]
na2sif6+4naoh=6naf+sio2+2h2o
[0006]
naf+lioh=lif+naoh
[0007]
式中lioh溶液已经过离子交换预处理除杂。
[0008]
次年公布的美国专利中,robert对上述工艺进行了改进。他直接用经离子交换法制得的lioh溶液与na2sif6反应同样制得了高纯lif(us3241914),其反应方程式可表示为:
[0009]
6lioh+na2sif6=6lif+na2sio3+3h2o
[0010]
离子交换制备法,充分利用了磷肥厂副产物na2sif6,有效降低了lif的生产成本,其主要缺点是所制得的高纯lif中的硅及一些过渡金属杂质元素的含量仍较高,其原因可能是对na2sif6的预处理不够,从而使这种方法制得的高纯lif不适用于对这些杂质离子敏感的领域。目前离子交换法仍广泛应用于制备高纯lif及其他一些高纯锂盐产品。日本电信电话株式会社的小林健二等人在1989~1993年间,连续取得了三个专利。这三个专利介绍了用复分解法制备高纯氟化锂,即用经离子交换法除去过渡金属杂质后的醋酸锂溶液与氢氟酸溶液反应,制得了酸含量低于10-4%,fe、co、ni、cu、cr等过渡金属杂质含量均低于10-7%的高纯lif。
[0011]
近年来,lipf6的合成技术也在不断进步,高纯度的lif的制备技术也有很多研究
者在深入探讨。氟化锂工业化生产多采用高纯碳酸锂和hf反应制得。在专利cn101723413a中,采用的是高纯碳酸锂料浆采用co2进行碳化,得到碳酸氢锂溶液,再经过精密过滤器过滤。然后向过滤后的溶液中加入hf水溶液,控制ph0.3-5,反应得到氟化锂料浆,料浆经过滤,真空干燥得到高纯氟化锂。传统工艺的高纯氟化锂材料的制备过程仍然存在很多的不确定性,制备的材料纯度不够高,特备是以hf为原料的制备方法,还存在lif
·
hf复合物的影响,影响了制备lipf6材料的纯度。另外制备出的氟化锂活性上也存在着不稳定性,从而在后续的六氟磷酸锂合成中,会形成部分包覆,直接影响到六氟磷酸锂的指标。
[0012]
因此,需要设计一种超纯高活性电池级氟化锂的制备方法。
技术实现要素:[0013]
本发明的目的在于克服现有技术中的缺陷,提供一种超纯高活性电池级氟化锂的制备方法。
[0014]
本发明通过下述方案实现:
[0015]
一种超纯高活性电池级氟化锂的制备方法,该方法包括以下步骤:
[0016]
步骤一、用超纯水将无水氟化氢调配为有水氢氟酸,将所述有水氢氟酸与粗品氟化锂调配成氟化锂料浆;
[0017]
步骤二、在持续搅拌下,将所述氟化锂料浆连续送入球磨机进行球磨,球磨机内的悬浊液温度为50-100摄氏度,待球磨机内的物料完成溶出后,将溶出液进行过滤、洗涤,得到精品氟化氢微晶体;
[0018]
步骤三、将所述精品氟化氢微晶体投加到无水氟化氢中,在10-15摄氏度下溶解10-30分钟,过滤得到澄清的氟化氢锂溶液;
[0019]
步骤四、将所述氟化氢锂溶液在低温冷冻浴内降温结晶,降温速率为3-8℃/h,在终点温度-50℃下维持0.5-0.8h,得到晶浆;
[0020]
步骤五、将所述晶浆进行固液分离,分离后得到透明的氟化锂晶体,将所述透明的氟化锂晶体在氮气保护下进行气流干燥,气流干燥温度为在150摄氏度;经过一次气流干燥完成后的物料再进行真空干燥,在1h内升温至300摄氏度,保持温度12h,得到超纯高活性电池级氟化锂晶体。
[0021]
在步骤一中,所述有水氢氟酸的质量百分比浓度为5%-25%,调配时环境温度为0-20摄氏度。
[0022]
在步骤二中,通过调整进入球磨机中有水氢氟酸的温度来控制球磨机内部悬浊液的温度。
[0023]
在步骤二中,所述球磨机溶出液的质量浓度为80-120mg/l。
[0024]
在步骤三中,所述精品氟化氢与无水氟化氢的质量比为1:5-6。
[0025]
在步骤三中,所述过滤采用过滤精度为0.5微米的四氟滤袋进行过滤。
[0026]
在步骤四中,所述的低温冷冻浴内使用的冷媒介质为工业乙醇水溶液;乙醇水溶液中,乙醇的质量百分比为70%。
[0027]
本发明的有益效果为:
[0028]
1.本发明一种超纯高活性电池级氟化锂的制备方法用一定质量分数的水氢氟酸作悬浮剂,对悬浮物料进行湿法球磨,过滤去除杂质。原料结晶间夹杂的微量杂质会在球磨
作用下进入悬浮液体系中,发生反应溶解于氢氟酸中。通过球磨增大氟化锂晶体的表面活化能,进一步释放结晶包覆的轻组分杂质。
[0029]
2.氟化锂的制备对提高六氟磷酸锂和其他关键锂电材料具有重要的作用,目前市售的氟化锂纯度均不能满足电池级氟化锂的要求,本发明在球磨、过滤、洗涤的基础上,继续利用无水氟化氢溶解氟化锂特性和降温重结晶提纯原理,提纯得到精品氟化锂,同时利用无水氟化氢沸点低的性质,提供了一个低能耗、短流程的提纯工艺,最终得到氟化锂产品符合电池的应用。
具体实施方式
[0030]
下面结合具体实施例对本发明进一步说明:
[0031]
一种超纯高活性电池级氟化锂的制备方法,该方法包括以下步骤:
[0032]
步骤一、用超纯水将无水氟化氢调配为有水氢氟酸,将所述有水氢氟酸与粗品氟化锂调配成氟化锂料浆;
[0033]
步骤二、在持续搅拌下,将所述氟化锂料浆连续送入球磨机进行球磨,球磨机内的悬浊液温度为50-100摄氏度,待球磨机内的物料完成溶出后,将溶出液进行过滤、洗涤,得到精品氟化氢微晶体;
[0034]
步骤三、将所述精品氟化氢微晶体投加到无水氟化氢中,在10-15摄氏度下溶解10-30分钟,过滤得到澄清的氟化氢锂溶液;
[0035]
步骤四、将所述氟化氢锂溶液在低温冷冻浴内降温结晶,降温速率为3-8℃/h,在终点温度-50℃下维持0.5-0.8h,得到晶浆;
[0036]
步骤五、将所述晶浆进行固液分离,分离后得到透明的氟化锂晶体,将所述透明的氟化锂晶体在氮气保护下进行气流干燥,气流干燥温度为在150摄氏度;经过一次气流干燥完成后的物料再进行真空干燥,在1h内升温至300摄氏度,保持温度12h,得到超纯高活性电池级氟化锂晶体。
[0037]
在步骤一中,所述有水氢氟酸的质量百分比浓度为5%-25%,调配时环境温度为0-20摄氏度。
[0038]
在步骤二中,通过调整进入球磨机中有水氢氟酸的温度来控制球磨机内部悬浊液的温度。
[0039]
在步骤二中,所述球磨机溶出液的质量浓度为80-120mg/l。
[0040]
在步骤三中,所述精品氟化氢与无水氟化氢的质量比为1:5-6。
[0041]
在步骤三中,所述过滤采用过滤精度为0.5微米的四氟滤袋进行过滤。
[0042]
在步骤四中,所述的低温冷冻浴内使用的冷媒介质为工业乙醇水溶液;乙醇水溶液中,乙醇的质量百分比为70%。
[0043]
本申请用一定质量分数的水氢氟酸作悬浮剂,对悬浮物料进行湿法球磨,过滤去除杂质。原料结晶间夹杂的微量杂质会在球磨作用下进入悬浮液体系中,发生反应溶解于氢氟酸中。通过球磨增大氟化锂晶体的表面活化能,进一步释放结晶包覆的轻组分杂质。
[0044]
氟化锂的制备对提高六氟磷酸锂和其他关键锂电材料具有重要的作用,目前市售的氟化锂纯度均不能满足电池级氟化锂的要求,本发明在球磨、过滤、洗涤的基础上,继续利用无水氟化氢溶解氟化锂特性和降温重结晶提纯原理,提纯得到精品氟化锂,同时利用
无水氟化氢沸点低的性质,提供了一个低能耗、短流程的提纯工艺,最终得到氟化锂产品符合电池的应用。
[0045]
下面结合具体实施例对本申请做进一步阐述:
[0046]
实施例1
[0047]
一种超纯高活性电池级氟化锂的制备方法,该方法包括以下步骤:
[0048]
步骤一、用超纯水将无水氟化氢调配为有水氢氟酸,将所述有水氢氟酸与粗品氟化锂调配成氟化锂料浆;所述有水氢氟酸的质量百分比浓度为25%,调配时环境温度为0摄氏度。
[0049]
步骤二、在持续搅拌下,将所述氟化锂料浆连续送入球磨机进行球磨,球磨机内的悬浊液温度为80摄氏度,待球磨机内的物料完成溶出后,将溶出液进行过滤、洗涤,得到精品氟化氢微晶体;所述球磨机溶出液的质量浓度为120mg/l。
[0050]
步骤三、将所述精品氟化氢微晶体投加到无水氟化氢中,在10摄氏度下溶解20分钟,过滤得到澄清的氟化氢锂溶液;所述精品氟化氢与无水氟化氢的质量比为1:6。
[0051]
步骤四、将所述氟化氢锂溶液在低温冷冻浴内降温结晶,降温速率为3℃/h,在终点温度-50℃下维持0.6h,得到晶浆;
[0052]
步骤五、将所述晶浆进行固液分离,分离后得到透明的氟化锂晶体,将所述透明的氟化锂晶体在氮气保护下进行气流干燥,气流干燥温度为在150摄氏度;经过一次气流干燥完成后的物料再进行真空干燥,在1h内升温至300摄氏度,保持温度12h,得到超纯高活性电池级氟化锂晶体。
[0053]
实施例2
[0054]
一种超纯高活性电池级氟化锂的制备方法,该方法包括以下步骤:
[0055]
步骤一、用超纯水将无水氟化氢调配为有水氢氟酸,将所述有水氢氟酸与粗品氟化锂调配成氟化锂料浆;所述有水氢氟酸的质量百分比浓度为5%,调配时环境温度为10摄氏度。
[0056]
步骤二、在持续搅拌下,将所述氟化锂料浆连续送入球磨机进行球磨,球磨机内的悬浊液温度为100摄氏度,待球磨机内的物料完成溶出后,将溶出液进行过滤、洗涤,得到精品氟化氢微晶体;所述球磨机溶出液的质量浓度为80mg/l。
[0057]
步骤三、将所述精品氟化氢微晶体投加到无水氟化氢中,在12摄氏度下溶解30分钟,过滤得到澄清的氟化氢锂溶液;所述精品氟化氢与无水氟化氢的质量比为1:5。
[0058]
步骤四、将所述氟化氢锂溶液在低温冷冻浴内降温结晶,降温速率为6℃/h,在终点温度-50℃下维持0.8h,得到晶浆;
[0059]
步骤五、将所述晶浆进行固液分离,分离后得到透明的氟化锂晶体,将所述透明的氟化锂晶体在氮气保护下进行气流干燥,气流干燥温度为在150摄氏度;经过一次气流干燥完成后的物料再进行真空干燥,在1h内升温至300摄氏度,保持温度12h,得到超纯高活性电池级氟化锂晶体。
[0060]
实施例3
[0061]
一种超纯高活性电池级氟化锂的制备方法,该方法包括以下步骤:
[0062]
步骤一、用超纯水将无水氟化氢调配为有水氢氟酸,将所述有水氢氟酸与粗品氟化锂调配成氟化锂料浆;所述有水氢氟酸的质量百分比浓度为5%-25%,调配时环境温度
为0-20摄氏度。
[0063]
步骤二、在持续搅拌下,将所述氟化锂料浆连续送入球磨机进行球磨,球磨机内的悬浊液温度为50-100摄氏度,待球磨机内的物料完成溶出后,将溶出液进行过滤、洗涤,得到精品氟化氢微晶体;所述球磨机溶出液的质量浓度为80-120mg/l。
[0064]
步骤三、将所述精品氟化氢微晶体投加到无水氟化氢中,在10-15摄氏度下溶解10-30分钟,过滤得到澄清的氟化氢锂溶液;所述精品氟化氢与无水氟化氢的质量比为1:5-6。
[0065]
步骤四、将所述氟化氢锂溶液在低温冷冻浴内降温结晶,降温速率为3-8℃/h,在终点温度-50℃下维持0.5-0.8h,得到晶浆;
[0066]
步骤五、将所述晶浆进行固液分离,分离后得到透明的氟化锂晶体,将所述透明的氟化锂晶体在氮气保护下进行气流干燥,气流干燥温度为在150摄氏度;经过一次气流干燥完成后的物料再进行真空干燥,在1h内升温至300摄氏度,保持温度12h,得到超纯高活性电池级氟化锂晶体。
[0067]
本申请粗品氟化锂的纯度为99wt%,无水氟化氢为99.95-99.97wt%的工业品无水氟化氢,精品氟化氢微晶体的纯度为99.91wt%。
[0068]
将上述3个实施例及市售的超纯高活性电池级氟化锂进行取样分析,分析结果如表1所示,具体取样过程和分析过程参照相关规范进行,在此不再赘述。从表1中可以看出,本申请三个实施例制备得到的超纯高活性电池级氟化锂的最小过筛粒径、氮吸附表面积、堆积密度等指标均远远优于现有的市售产品。
[0069]
表1超纯高活性电池级氟化锂分析结果
[0070][0071]
分别称取上述3个实施例超纯高活性电池级氟化锂晶体3克,混合均匀后进行用电感耦合原子发射光谱仪进行元素定量分析,结果表明其中的氟化锂质量分数大于99.99%,本申请制备的样品已超过电池级氟化锂理化指标,能满足市场对电池级氟化锂的需求。
[0072]
本申请采用有水氢氟酸作为悬浮剂,对市售低纯度、低活性的粗品氟化锂进行纯化。通过球磨除去氟化锂结晶表面的枝状晶,使杂质溶解于氢氟酸中过滤去除,得到了精品氟化氢微晶体。
[0073]
为了进一步提高精品氟化氢微晶体的纯度和活性,将精品氟化氢微晶体溶于无水
氟化氢得到氟化氢锂溶液,使得固态锂资源转变为液态锂,然后利用重结晶析出晶浆(氟化锂固体),固液分离后进行气流干燥和真空,上述整个过程中氟化锂得到除杂和微观结构的改变,在高低比表面积相互转换间达到微观结构的改变,最终得到得到的氟化锂纯度控制在99.99%以上,颗粒较传统方法细小而均匀,堆积密度显著上升,比表面积约为400~900m/g,活性更高,该指标能满足市场对电池级氟化锂的需求,也符合hg/t4507-2013《高纯工业品氟化锂》中合格品验收要求。
[0074]
尽管已经对本发明的技术方案做了较为详细的阐述和列举,应当理解,对于本领域技术人员来说,对上述实施例做出修改或者采用等同的替代方案,这对本领域的技术人员而言是显而易见,在不偏离本发明精神的基础上所做的这些修改或改进,均属于本发明要求保护的范围。