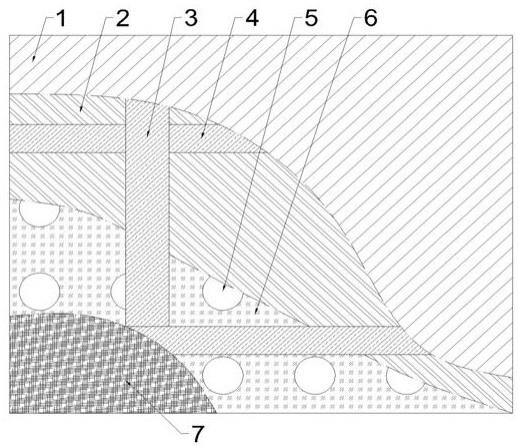
[0001]
本发明涉及建筑材料领域,更为具体的,涉及一种建筑用节能板材的制备方法。
背景技术:[0002]
在建筑材料领域,板材的广泛应用,建筑板材的种类也非常多,就其材质来分包括石膏板、铝塑复合板、发泡水泥板、硅酸钙板、玻璃钢板等。其中的发泡水泥复合的建筑用节能板是以钢边框或预应力混凝土边框、钢筋桁架作为框体支架,上、下用水泥面层复合,并在间隙空间中填充发泡水泥或者其他砂浆等其他填充料后成型,并经成型、蒸汽或高压蒸汽养护制成的板材,是集承重、保温、轻质、隔热、隔声、耐火等优良性能于一身的优质建筑材料。
[0003]
而随着建筑要求的提高,建筑对板材的要求也越来越高,除要求有较佳的强度和稳定性之外还要求有较佳的隔热保温性能以及隔音效果,通过综合使用承重材料以及保温砂浆、保温板材等为代表的保温材料,使得墙体能够在有效控制自身厚度的情况下具备较高的保温性能,在保温砂浆和保温板材在实现自身保温性能优化的同时,还需要解决包括节能、防火等在内的众多关键问题,以此有效实现保温砂浆和保温板材的可持续发展。
技术实现要素:[0004]
本发明所解决的技术问题在于提供一种建筑用节能板材的制备方法,以解决上述技术背景中的缺陷。
[0005]
本发明所解决的技术问题采用以下技术方案来实现:一种建筑用节能板材的制备方法,具体包括以下制备步骤:s1制备第一基板:将质量比为10:1~5:1的氯化镁、硫酸镁加水溶解,制成浓度为24~26波美度的混合溶液,将上述混合溶液加入水泥中调浆,控制水灰比为0.5,一并加入占水泥质量比1~5wt%的发泡剂、18~22wt%的粉煤灰,搅拌均匀后得到浆料,然后浇筑成型,养护得到第一基板;s2制备第二基板:以蒸压轻质加气混凝土隔墙板作为面板,在内侧衬装一层石膏板,控制蒸压轻质加气混凝土隔墙板与石膏板的厚度之比为1:1~1:2,在石膏板表面开点阵通槽至蒸压轻质加气混凝土隔墙板表面,得到第二基板;s3制备保温填充砂浆:以水泥为基材,加入占水泥质量比20~30wt%的填料、占水泥质量比3~5wt%的增强纤维、占水泥质量比1~3wt%的聚苯烯泡沫以及占水泥质量比0.3~1wt%的铁氧体粉末,加水调浆得到保温填充砂浆;s4将通过s1制得的第一基板作为外侧基板,通过将步骤s2制备制得的第二基板作为内侧基板,在第一基板与第二基板之间设置间隙空间,并在间隙空间位置设置支撑框体,在支撑框体之间预留注浆孔;s5在注浆孔位置进行压力注浆,注浆完成后养护成型,即得到成品节能板材。
[0006]
作为进一步限定,所述步骤s1以及所述步骤s3中采用的水泥优选为硫铝酸盐水
泥、普通硅酸盐水泥中的一种或两种的混合,且水泥等级为42.5以上,水泥过筛,并保证最大粒径不超过30μm。
[0007]
作为进一步限定,所述步骤s1中加入的发泡剂为十二烷基硫酸钠、脂肪醇聚氧乙烯醚硫酸钠、碳酸氢铵中的一种或者组合。
[0008]
作为进一步限定,所述步骤s1中进行的养护操作为常温洒水养护,养护至36~48h时脱模,然后继续养护时长为5~8d。
[0009]
作为进一步限定,所述石膏板表面点阵通槽优选为圆槽,其槽直径为6~8cm,槽间距为10~15cm。
[0010]
作为进一步限定,所述步骤s3中采用的填料为经过破碎和研磨处理过的粒径不超过3mm的炉渣、回收陶瓷渣、回收玻璃渣中的一种或者组合。
[0011]
作为进一步限定,所述增强纤维为尼龙纤维、聚丙烯纤维、无碱玻璃纤维、钢纤维中的一种或者组合。
[0012]
作为进一步限定,所述支撑框体的截面为方管、工字形截面轻钢梁或者u形截面轻钢梁。
[0013]
作为进一步限定,所述步骤s5中进行养护成型时采用热养护,养护温度为养护温度为50~80℃,养护时长为5~6d 。
[0014]
有益效果:本发明的建筑用节能板材的制备方法对传统发泡水泥复合板体结构中的保温砂浆以及水泥保温面层进行工艺技术优化,使之具有隔音、保温、高强度的特点,可作为建筑用节能板材用于楼板组装、墙面和屋面建设,有利于减少集成房屋施工时的能源消耗,既有助于提高建筑的节能保温性能,与其他板材相比在节能方面确实有着不可比拟的优势,同时易于施工操作,性能稳定,能有效降低建筑施工成本。
附图说明
[0015]
图1为本发明的较佳实施例的结构示意图。
[0016]
其中:1、第一基板;2、保温填充砂浆;3、竖梁;4、横梁;5、点阵通槽;6、石膏板;7、蒸压轻质加气混凝土隔墙板。
具体实施方式
[0017]
为了使本发明实现的技术手段、创作特征、达成目的与功效易于明白了解,下面结合具体图示,进一步阐述本发明。
[0018]
在实施例一中,建筑用节能板材按照以下方式制备:首先制备第一基板以及第二基板:制备第一基板时将质量比为10:1的氯化镁、硫酸镁加水溶解,制成浓度为26波美度的混合溶液,将上述混合溶液加入硫铝酸盐水泥中调浆,该硫铝酸盐水泥的水泥等级为42.5,并进行筛分,控制筛分后的水泥粉末的最大粒径不超过30μm,并控制水灰比为0.5,一并加入占水泥质量比5wt%的十二烷基硫酸钠作为发泡剂、18wt%的粉煤灰,搅拌均匀后得到浆料,然后浇筑成型,常温洒水养护,养护至45h时脱模,然后继续养护时长为7d后得到第一基板1,备用。
[0019]
制备第二基板时,选用厚度为8mm的蒸压轻质加气混凝土隔墙板7作为面板,在蒸
压轻质加气混凝土隔墙板的一侧表面施胶,并粘连一块尺寸与蒸压轻质加气混凝土隔墙板7一致的厚度为10mm的石膏板6,该石膏板6上预留有直径为8cm、槽间距为15cm的点阵通槽5,成型时,在石膏板6表面施加30mpa的压力,压制15min后稳定成型得到第二基板。
[0020]
然后制备保温填充砂浆,以等级为42.5的硫铝酸盐水泥为基材,将基材水泥进行筛分,控制水泥过筛后最大粒径不超过30μm,加入占水泥质量比30wt%的填料、占水泥质量比5wt%的增强纤维、占水泥质量比1wt%的聚苯烯泡沫以及占水泥质量比1wt%的铁氧体粉末,加水调浆得到保温填充砂浆2。其中,填料为经过破碎和研磨处理的粒径不超过3mm的回收陶瓷渣与回收玻璃渣的质量比1:1的混合物粉末;增强纤维为尼龙纤维。
[0021]
将第一基板1作为外侧基板,石膏板6和蒸压轻质加气混凝土隔墙板7压合制成的第二基板作为内侧基板,在第一基板1与第二基板之间设置间隙空间,并在间隙空间位置横向间隔设置横梁4、竖向间隔设置竖梁3,横梁4和竖梁3的截面均为方管,建筑用节能板材利用横梁4与竖梁3组成的横竖框体结构作为支撑框体,在支撑框体上预留注浆孔,并在注浆孔位置进行压力注浆,使得保温填充砂浆填充满第一基板1与第二基板之间的间隙空间,注浆完成后封闭注浆孔,热养护6d,控制养护温度为80℃,养护成型后即得到成品节能板材。
[0022]
在实施例一的工艺条件下,其制得的建筑用节能板材的导热系数为0.062w/m
·
k,压强度为51mpa、折强度为28mpa,对外表面出较佳的导热性能以及物理性能。
[0023]
实施例二中建筑用节能板材按照以下方式制备:首先制备第一基板以及第二基板:制备第一基板时将质量比为6:1的氯化镁、硫酸镁加水溶解,制成浓度为25波美度的混合溶液,将上述混合溶液加入普通硅酸盐水泥中调浆,该硫铝酸盐水泥的水泥等级为42.5,并进行筛分,控制筛分后的水泥粉末的最大粒径不超过30μm,并控制水灰比为0.5,一并加入占水泥质量比4wt%的十二烷基硫酸钠作为发泡剂、20wt%的粉煤灰,搅拌均匀后得到浆料,然后浇筑成型,常温洒水养护,养护至40h时脱模,然后继续养护时长为7d后得到第一基板1,备用。
[0024]
制备第二基板时,选用厚度为10mm的蒸压轻质加气混凝土隔墙板7作为面板,在蒸压轻质加气混凝土隔墙板的一侧表面施胶,并粘连一块尺寸与蒸压轻质加气混凝土隔墙板7一致的厚度为20mm的石膏板6,该石膏板6上预留有直径为7cm、槽间距为12cm的点阵通槽5,成型时,在石膏板6表面施加30mpa的压力,压制15min后稳定成型得到第二基板。
[0025]
然后制备保温填充砂浆,以等级为42.5的硫铝酸盐水泥为基材,将基材水泥进行筛分,控制水泥过筛后最大粒径不超过30μm,加入占水泥质量比25wt%的填料、占水泥质量比4wt%的增强纤维、占水泥质量比2wt%的聚苯烯泡沫以及占水泥质量比0.8wt%的铁氧体粉末,加水调浆得到保温填充砂浆2。其中,填料为经过破碎和研磨处理的粒径不超过3mm的炉渣、回收陶瓷渣、回收玻璃渣的质量比2:1:1的混合物粉末;增强纤维为无碱玻璃纤维与钢纤维的质量比5:1的混合物纤维。
[0026]
将第一基板1作为外侧基板,石膏板6和蒸压轻质加气混凝土隔墙板7压合制成的第二基板作为内侧基板,在第一基板1与第二基板之间设置间隙空间,并在间隙空间位置横向间隔设置横梁4、竖向间隔设置竖梁3,横梁4和竖梁3的截面均为工字形截面轻钢梁,建筑用节能板材利用横梁4与竖梁3组成的横竖框体结构作为支撑框体,在支撑框体上预留注浆孔,并在注浆孔位置进行压力注浆,使得保温填充砂浆填充满第一基板1与第二基板之间的
间隙空间,注浆完成后封闭注浆孔,热养护6d,控制养护温度为70℃,养护成型后即得到成品节能板材。
[0027]
在实施例二的工艺条件下,其制得的建筑用节能板材的导热系数为0.064w/m
·
k,压强度为47mpa、折强度为32mpa,对外表面出较佳的导热性能以及物理性能。
[0028]
以上各实施例仅用以说明本发明的技术方案,而非对其限制;尽管参照前述各实施例对本发明进行了详细的说明,本领域的普通技术人员应当理解:其依然可以对前述各实施例所记载的技术方案进行修改,或者对其中部分或者全部技术特征进行等同替换;而这些修改或者替换,并不使相应技术方案的本质脱离本发明各实施例技术方案的范围。