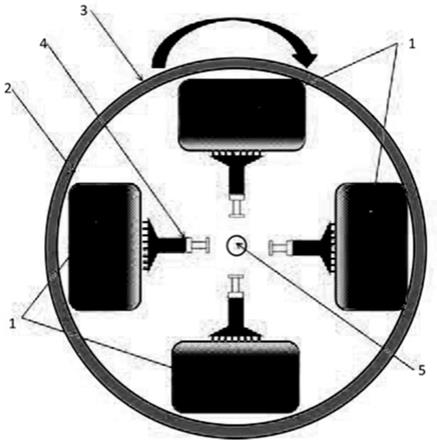
[0001]
本发明涉及一种低成本耐高温碳陶复合材料及制备方法,属于碳陶复合材料技术领域。
背景技术:[0002]
碳陶复合材料是继碳碳复合材料发展而来的新型耐高温耐氧化陶瓷基复合材料,其设计目标是比碳碳复合材料具有更优异的耐高温氧化性能、耐高温水汽腐蚀性能和摩擦性能。因此,在新一代高性能飞机摩擦材料和高温耐烧蚀材料方面有着巨大的应用价值,也是欧美等发达国家竞相开展研究的新型陶瓷基复合材料。
[0003]
陶复合材料传统的制备方法主要有两大类:一是采用多次浸渍裂解路线通过碳纤维或碳化硅纤维增强体浸渍含碳、硅、氧等元素的有机先驱体熔体或溶体,然后通过高温无氧或惰性气体保护裂解制备出碳纤维增强碳化硅复合材料。由于一次浸渍、裂解获得的碳陶复合材料孔隙率较高,因此为提高致密度,需要多次浸渍裂解。同时,含碳、硅、氧等元素的有机先驱体本身由于合成技术难度大,成本高。因此,该工艺能耗高、制备周期长,导致碳陶复合材料成本极高。另一种方法是采用含有碳、硅等元素的气态先驱体在碳纤维或碳化硅纤维增强体中进行化学气相渗透路线,在高温下裂解含有碳、硅等元素的气态先驱体,获得致密度高的碳陶复合材料。该方法由于采用气体渗透,因此可以获得高致密度的陶瓷基复合材料,但由于气相渗透沉积效率较低,因此导致该常用的工业化方法极高的能耗成本和时间成本。
[0004]
因此,为拓展碳陶复合材料的应用领域、降低制备成本,迫切需要开发一种低成本先驱体和制备工艺方法。
技术实现要素:[0005]
本发明针对现有技术存在的不足,提供一种低成本耐高温碳陶复合材料及制备方法,所述的碳陶复合材料致密度高,耐高温,而且制备成本低,适合工业化生产。
[0006]
本发明解决上述技术问题的技术方案如下:一种低成本耐高温碳陶复合材料,所述的碳陶复合材料为对碳陶复合材料增强体使用先驱体进行增密处理得到,所述的先驱体原料包括正硅酸乙酯、铝粉、无水乙醇、三甲基二氯硅烷和碱性硅溶胶,所述先驱体的合成过程如下:
[0007]
1)将正硅酸乙酯、无水乙醇和去离子水在室温下混合均匀,制备出含硅、氧源的溶液;
[0008]
2)在隔绝空气的条件下,将三甲基二氯硅烷缓慢滴加到铝粉中,并缓慢搅拌;
[0009]
3)在步骤2)的铝粉与甲基二氯硅烷混合物中缓慢滴加碱性硅溶胶,并用氨水调节ph值至9-10.5,在60-95℃下至铝粉形成胶体状,得到胶体状铝粉;
[0010]
4)将步骤1)的含硅、氧源的溶液与步骤3)的胶体状铝粉进行均匀混合,并搅拌,加去离子水调整粘度至100-800cps,得到先驱体。
[0011]
优选的,步骤1)中,所述正硅酸乙酯、无水乙醇和去离子水的摩尔比为1:0.65-2.5:1.2-2.8。
[0012]
优选的,步骤2)中,所述铝粉与所述三甲基二氯硅烷的摩尔比为1:0.05-0.08,所述的铝粉为80-120目的球形铝粉。
[0013]
优选的,步骤4)中,所述含硅、氧源的溶液与所述胶体状铝粉的质量比为1:0.7~1.5。
[0014]
本发明还公开了低成本耐高温碳陶复合材料的制备方法,所述碳陶复合材料的制备方法包括如下步骤:
[0015]
(a)将商用碳纤维或碳化硅纤维预成型体裁切成规则块体,作为碳陶复合材料增强体;
[0016]
(b)将先驱体置于多针头注射器中,用于对碳陶复合材料增强体注射增密处理;
[0017]
(c)将碳陶复合材料增强体对称置于高速旋转的离心筒中,离心筒内壁和离心筒外壁中间通入导热油或蒸汽,用于对商用碳纤维或碳化硅纤维预成型体加热,蒸发先驱体中的水分,离心筒的中心轴镶嵌高速轴承;
[0018]
(d)将装满先驱体的多针头注射器均匀插到碳陶复合材料增强体表面,多针头注射器和碳陶复合材料增强体对称布置到离心筒四周,并装卡固定;
[0019]
(e)启动离心筒,并开启离心筒内壁和离心筒外壁中间的导热油或蒸汽的加热功能,多针头注射器中的先驱体在离心力作用下均匀从碳陶复合材料增强体上表面渗入下表面,在离心筒内壁梯度加热作用下,多驱体挥发水分,将固含量留在碳陶复合材料增强体内,形成致密化并干燥处理后的碳陶复合材料生坯基体;
[0020]
(f)将步骤(e)中得到的碳陶复合材料生坯基体置于气氛保护炉或真空炉中烧结,得到所述的碳陶复合材料。
[0021]
进一步的,所述的离心筒内壁涂覆有高发射率的发热体,所述离心筒内壁涂覆有炭黑或者石墨涂层;所述离心筒外壁的外部设有保温材质。
[0022]
进一步的,步骤(e)中,所述离心筒的转速为500-8000rpm,加热温度为90-200℃,离心时间为2-30h。
[0023]
进一步的,步骤(f)中,烧结温度为1400-1850℃。
[0024]
本发明的有益效果是:所述的碳陶复合材料表面平整,无明显气孔或变形,整体结构致密,致密度为95%以上,所述碳陶复合材料的弯曲强度最高可达220mpa,最低为98mpa。所述碳陶复合材料耐高温,而且制备成本低,适合工业化生产。
附图说明
[0025]
图1为带加热功能的离心筒示意图;
[0026]
图2为实施例中制备的碳陶复合材料光学照片;
[0027]
图3为实施例中制备的碳陶复合材料表面sem微观形貌照(a)低倍(b)高倍片;
[0028]
图中,1碳陶复合材料增强体;2.离心筒内壁;3离心筒外壁;4多针头注射器;5.中心轴。
具体实施方式
[0029]
为使本发明的上述目的、特征和优点能够更加明显易懂,下面对本发明的具体实施方式做详细的说明。在下面的描述中阐述了很多具体细节以便于充分理解本发明。但是本发明能够以很多不同于在此描述的其它方式来实施,本领域技术人员可以在不违背本发明内涵的情况下做类似改进,因此本发明不受下面公开的具体实施例的限制。
[0030]
除非另有定义,本文所使用的所有的技术和科学术语与属于本发明的技术领域的技术人员通常理解的含义相同。本文中在本发明的说明书中所使用的术语只是为了描述具体的实施方式的目的,不是旨在于限制本发明。
[0031]
一种低成本耐高温碳陶复合材料,所述的碳陶复合材料为对碳陶复合材料增强体1使用先驱体进行增密处理得到,所述的先驱体原料包括正硅酸乙酯、铝粉、无水乙醇、三甲基二氯硅烷和碱性硅溶胶,所述先驱体的合成过程如下:
[0032]
1)将正硅酸乙酯、无水乙醇和去离子水按照摩尔比为1:0.65-2.5:1.2-2.8,在室温下混合均匀,制备出含硅、氧源的溶液;
[0033]
2)在隔绝空气的条件下,将三甲基二氯硅烷缓慢滴加到铝粉中,并缓慢搅拌,所述铝粉与所述三甲基二氯硅烷的摩尔比为1:0.05-0.08,所述的铝粉为80-120目的球形铝粉;
[0034]
3)在步骤2)的铝粉与甲基二氯硅烷混合物中缓慢滴加碱性硅溶胶,并用氨水调节ph值至9-10.5,在60-95℃下至铝粉形成胶体状,得到胶体状铝粉;
[0035]
4)将步骤1)的含硅、氧源的溶液与步骤3)的胶体状铝粉按照质量比为1:0.7~1.5进行均匀混合,并搅拌,加去离子水调整粘度至100-800cps,得到先驱体。
[0036]
所述低成本耐高温碳陶复合材料的制备方法,包括如下步骤:
[0037]
(a)将商用碳纤维或碳化硅纤维预成型体裁切成规则块体,作为碳陶复合材料增强体1;
[0038]
(b)将先驱体置于多针头注射器4中,用于对碳陶复合材料增强体1注射增密处理;
[0039]
(c)将碳陶复合材料增强体1对称置于高速旋转的离心筒中,离心筒内壁2和离心筒外壁3中间通入导热油或蒸汽,离心筒的中心轴5镶嵌高速轴承,所述的离心筒内壁2涂覆有高发射率的发热体,所述离心筒内壁2涂覆有炭黑或者石墨涂层,所述离心筒外壁3的外部设有保温材质。;
[0040]
(d)将装满先驱体的多针头注射器4均匀插到碳陶复合材料增强体1表面,多针头注射器4和碳陶复合材料增强体1对称布置到离心筒四周,并装卡固定;
[0041]
(e)启动离心筒,所述离心筒的转速为500-8000rpm,并开启离心筒内壁2和离心筒外壁3中间的导热油或蒸汽的加热功能,加热温度为90-200℃,多针头注射器4中的先驱体在离心力作用下均匀从碳陶复合材料增强体1上表面渗入下表面,在离心筒内壁2梯度加热作用下,多驱体挥发水分,将固含量留在碳陶复合材料增强体1内,形成致密化并干燥处理后的碳陶复合材料生坯基体,离心时间为2-30h;
[0042]
(f)将步骤(e)中得到的碳陶复合材料生坯基体置于气氛保护炉或真空炉中烧结,烧结温度为1400-1850℃,得到所述的碳陶复合材料。
[0043]
所述的碳陶复合材料光学照片,可以看到,烧结后表面比较平整,无明显气孔或变形。
[0044]
从碳陶复合材料表面sem微观形貌照片可以看到,整体结构比较致密,微观仍有随
机分布的微孔,根据扫描照片结果微孔直径约为100-400nm。根据排水法测得致密度为95%以上。根据三点弯曲试验,制备的碳陶复合材料弯曲强度最高可达220mpa,最低为98mpa。
[0045]
以上所述实施例的各技术特征可以进行任意的组合,为使描述简洁,未对上述实施例中的各个技术特征所有可能的组合都进行描述,然而,只要这些技术特征的组合不存在矛盾,都应当认为是本说明书记载的范围。
[0046]
以上所述实施例仅表达了本发明的几种实施方式,其描述较为具体和详细,但并不能因此而理解为对发明专利范围的限制。应当指出的是,对于本领域的普通技术人员来说,在不脱离本发明构思的前提下,还可以做出若干变形和改进,这些都属于本发明的保护范围。因此,本发明专利的保护范围应以所附权利要求为准。