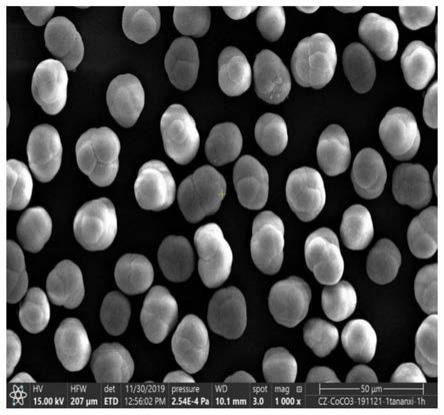
[0001]
本发明属于锂离子电池技术领域,具体涉及一种电池用掺铝大粒度碳酸钴的制备方法。
背景技术:[0002]
钴酸锂电极材料具有较高的比容量和良好的循环稳定性能,是目前广泛应用于3c领域的正极材料,作为钴酸锂的前驱体(碳酸钴)的品质,决定了电池材料的性能。
[0003]
传统的碳酸钴生产方法大多采用钴盐溶液、铝盐溶液与沉淀剂(如碳酸氢铵或碳酸氢钠溶液)并流沉淀,合成掺铝碳酸钴产品,由于在反应体系内碳酸氢铵或碳酸氢钠溶液既充当沉淀剂同时也充当络合剂,当温度大于35℃时,碳酸氢铵就会分解,导致反应体系内沉淀剂、络合剂缓存量不稳定,碳酸钴结晶的晶型多次发生变化,铝元素不能均匀掺杂,生产出的掺铝碳酸钴产品性能较差,影响电池的电化学性能。
技术实现要素:[0004]
针对现有技术中的问题,本发明采取氨水或者乙二胺作为络合剂,在合成过程中,单独加入络合剂,控制反应体系中游离氨的浓度,达到稳定体系内沉淀剂和络合剂缓存量的目的,进而防止碳酸钴晶型的转变。
[0005]
本发明采用以下技术方案:
[0006]
一种电池用掺铝大粒度碳酸钴的制备方法,其特征在于,所述方法包括以下步骤:
[0007]
(1)向反应釜中加入碳酸氢铵溶液作为底液,将带有底液的反应釜升温至40℃-53℃、搅拌转速调节为100-180转/分钟,将反应釜内的ph调节为6~8;
[0008]
(2)向带有底液的反应釜中以并流的方式加入物料碳酸氢铵溶液、钴铝溶液、络合剂溶液,得到浆料;向反应釜内加入物料的过程中保持反应釜内的ph为6~8、游离氨为6g/l-7g/l,反应釜内浆料密度维持在1.2g/ml-1.5g/ml;当浆料中的产品平均粒度达到9μm-10μm时,将反应釜的搅拌转速调节为60-80转/分钟;当浆料中的产品平均粒度达到19μm-20μm时,停止向反应釜中加入物料;
[0009]
(3)将产品粒度为19μm-20μm的浆料在反应釜内保温陈化、过滤、烘干,得到电池用掺铝大粒度碳酸钴。
[0010]
根据上述的电池用掺铝大粒度碳酸钴的制备方法,其特征在于,步骤(2)络合剂溶液中的络合剂为氨水、乙二胺中的一种或两种,络合剂溶液的浓度为80g/l~120g/l。
[0011]
根据上述的电池用掺铝大粒度碳酸钴的制备方法,其特征在于,步骤(1)中用纯水或者碳酸氢铵将反应釜内的ph调节为6~8;步骤(1)中底液的浓度为140g/l-150g/l,步骤(1)中底液的加入量为10l-30l。
[0012]
根据上述的电池用掺铝大粒度碳酸钴的制备方法,其特征在于,步骤(2)中碳酸氢铵溶液的浓度为220g/l~250g/l,钴铝溶液中钴离子的浓度为100g/l~120g/l、铝离子的浓度为0.40g/l~0.80g/l;碳酸氢铵溶液、钴铝溶液、络合剂溶液的体积比为1:(0.3~
0.8):(0.002~0.008)。
[0013]
本发明的有益技术效果:与现有技术相比,本发明采取氨水或者乙二胺作为络合剂,在合成过程中,利用络合剂并流加入反应体系,控制反应体系中游离氨的浓度,达到稳定体系内沉淀剂和络合剂缓存量的目的,进而防止碳酸钴晶型的转变。本发明控制合成体系浆料密度,使得反应体系更加稳定,提升产品的致密度。本发明工艺简单、能耗较低,易于产业化、制备出的掺铝大粒度碳酸钴产品品质高、振实高、比表面积大。
附图说明
[0014]
图1为实施例1制备的电池用掺铝大粒度碳酸钴的扫描电子显微镜照片;
[0015]
图2为实施例1制备的电池用掺铝大粒度碳酸钴不同倍数的扫描电子显微镜照片。
具体实施方式
[0016]
本发明的一种电池用掺铝大粒度碳酸钴的制备方法,包括以下步骤:
[0017]
(1)向反应釜中加入碳酸氢铵溶液作为底液,将反应釜内的ph调节为6~8,优选的,用纯水或者碳酸氢铵将反应釜内的ph调节为6~8。打开搅拌,并将搅拌转速调至100-180转/分钟,迅速加热并将反应体系温度稳定在40℃-53℃。底液碳酸氢铵溶液的浓度为140g/l-150g/l,底液的加入量为10l-30l。
[0018]
(2)采用同时进料的方式,向带有底液的反应釜反应体系中以并流的方式加入物料碳酸氢铵溶液、钴铝溶液、络合剂溶液,得到浆料;碳酸氢铵溶液的浓度为220g/l~250g/l,钴铝溶液中钴离子的浓度为100g/l~120g/l、铝离子的浓度为0.40g/l~0.80g/l,络合剂溶液中的络合剂为氨水、乙二胺中的一种或两种,络合剂溶液的浓度为80g/l~120g/l。碳酸氢铵溶液、钴铝溶液、络合剂溶液的体积比为1:(0.3~0.8):(0.002~0.008)。向反应釜内加入物料的过程中保持反应釜内的ph为6~8、游离氨为6g/l-7g/l;同时开启提浓系统,保持反应釜内浆料比重维持在1.2g/ml-1.5g/ml;当浆料中的产品平均粒度达到9μm-10μm时,将反应釜的搅拌转速调节为60-80转/分钟;当浆料中的产品平均粒度(d50)达到19μm-20μm时,停止向反应釜中加入物料。
[0019]
(3)将产品粒度为19μm-20μm的浆料在反应釜内保温陈化、过滤、烘干,得到电池用掺铝大粒度碳酸钴。
[0020]
实施例1
[0021]
向反应釜中加入10l碳酸氢铵溶液作为底液,用纯水或者碳酸氢铵将反应釜内的ph调节为7~8。打开搅拌,并将搅拌转速调至160转/分钟,迅速加热并将反应体系温度稳定在53℃。底液的浓度为140-150g/l。
[0022]
采用同时进料的方式,向带有底液的反应釜反应体系中以并流的方式加入物料碳酸氢铵溶液、钴铝溶液、氨水,得到浆料;碳酸氢铵溶液的浓度为240g/l,钴铝溶液中钴离子的浓度为110g/l、铝离子的浓度为0.60g/l,氨水的浓度为90g/l。碳酸氢铵溶液、钴铝溶液、络合剂溶液的体积比为1:(0.3~0.8):0.002。向反应釜内加入物料的过程中保持反应釜内的ph为7.1-7.2、游离氨为6.5g/l-7g/l;同时开启提浓系统,保持反应釜内浆料比重维持在1.4g/ml-1.5g/ml;当浆料中的产品平均粒度达到9μm-10μm时,将反应釜的搅拌转速调节为60-80转/分钟;当浆料中的产品平均粒度(d50)达到19μm-20μm时,停止向反应釜中加入物
料。
[0023]
将产品粒度为19μm-20μm的浆料在反应釜内保温陈化、过滤、烘干,得到电池用掺铝大粒度碳酸钴。
[0024]
实施例2
[0025]
向反应釜中加入10l碳酸氢铵溶液作为底液,用纯水或者碳酸氢铵将反应釜内的ph调节为7~8。打开搅拌,并将搅拌转速调至160转/分钟,迅速加热并将反应体系温度稳定在48℃。底液的浓度为140-150g/l。
[0026]
采用同时进料的方式,向带有底液的反应釜反应体系中以并流的方式加入物料碳酸氢铵溶液、钴铝溶液、氨水,得到浆料;碳酸氢铵溶液的浓度为240g/l,钴铝溶液中钴离子的浓度为110g/l、铝离子的浓度为0.60g/l,氨水的浓度为90g/l。碳酸氢铵溶液、钴铝溶液、络合剂溶液的体积比为1:(0.3~0.8):0.005。向反应釜内加入物料的过程中保持反应釜内的ph为7.3-7.4、游离氨为6g/l-6.5g/l;同时开启提浓系统,保持反应釜内浆料比重维持在1.3g/ml-1.4g/ml;当浆料中的产品平均粒度达到9μm-10μm时,将反应釜的搅拌转速调节为60-80转/分钟;当浆料中的产品平均粒度(d50)达到19μm-20μm时,停止向反应釜中加入物料。
[0027]
将产品粒度为19μm-20μm的浆料在反应釜内保温陈化、过滤、烘干,得到电池用掺铝大粒度碳酸钴。
[0028]
实施例3
[0029]
向反应釜中加入30l碳酸氢铵溶液作为底液,用纯水或者碳酸氢铵将反应釜内的ph调节为7~8。打开搅拌,并将搅拌转速调至160转/分钟,迅速加热并将反应体系温度稳定在50℃。步骤(1)中底液的浓度为140-150g/l。
[0030]
采用同时进料的方式,向带有底液的反应釜反应体系中以并流的方式加入物料碳酸氢铵溶液、钴铝溶液、氨水,得到浆料;碳酸氢铵溶液的浓度为240g/l,钴铝溶液中钴离子的浓度为110g/l、铝离子的浓度为0.60g/l,氨水的浓度为90g/l。碳酸氢铵溶液、钴铝溶液、络合剂溶液的体积比为1:(0.3~0.8):0.008。向反应釜内加入物料的过程中保持反应釜内的ph为6.9-7.1、游离氨为6g/l-6.5g/l;同时开启提浓系统,保持反应釜内浆料比重维持在1.2g/ml-1.3g/ml;当浆料中的产品平均粒度达到9μm-10μm时,将反应釜的搅拌转速调节为60-80转/分钟;当浆料中的产品平均粒度(d50)达到19μm-20μm时,停止向反应釜中加入物料。
[0031]
将产品粒度为19μm-20μm的浆料在反应釜内保温陈化、过滤、烘干,得到电池用掺铝大粒度碳酸钴。