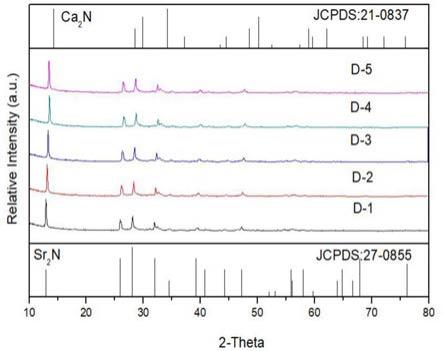
1.本发明涉及化工技术领域,尤其涉及一种高纯锶钙铕氮化物固溶体粉末及其制备方法。
背景技术:2.目前,随着新材料技术的发展,具有可控性的高纯锶钙铕氮化物固溶体粉体逐渐在行业内兴盛起来,展现出了良好的市场前景,锶钙铕氮化物固溶体可使用在led荧光粉、陶瓷颜料等领域的原材料。
3.氮化钙、氮化锶等的制备方法一般都是由碱土金属与氮气或氨气在高温下直接作用来获得。最早开发这种技术的典型方法是将碱土金属氮化物置于镍坩埚中,在纯净的氮气气流中加热得到,这项工作是由henri de moissan研究的(comptes rendus a 1’academie des sciences,18981,vol.127,pages497-503)。同样专利cn03815383.1中佛朗科伊斯
·
拉科斯特提供氮化钙的合成工艺是利用钙锌合金,在反应容器中将预热的氮气通入,利用钙与氮气反应放出的热量使锌蒸发掉而得到氮化钙,这种工艺的到的氮化钙纯度不够高。
4.金属钙、锶与氮气反应在200℃的温度下就开始了,但重量的增加是小幅度的,等到后期反应就会停止,这是因为反应生成一层n-ca或n-sr膜使得反应难以进行,即便是在650℃保温50小时以上,反应也难以进行,并且要通入大量的氮气气流。这时如果氮气中夹带少量的杂质气体如:水分、二氧化碳、氧气等都会被高温下的金属全部吸收,最后得到的产物氧含量也会很高,并且要使得反应完全反应时间需要持续100小时以上。
5.以上方法获得的产品纯度不高,还比较费氮气。
技术实现要素:6.本发明的目的是针对上述问题,提供一种高纯锶钙铕氮化物固溶体粉末及其制备方法。无需添加任何添加剂,操作简便,保证了产品的纯度;合成效率更高,氢气、氮气用量少,生产效率更高;工艺容易控制,氢化、氮化时间短,能耗少,生产周期短。
7.为了实现上述目的,本发明的技术方案是:
8.一种高纯锶钙铕氮化物固溶体粉末,其通式为(sr1-x-ycaxeuy)2n(0≤x≤0.45,0.008≤y≤0.025)。
9.作为对上述技术方案的改进,本发明提供了上述高纯锶钙铕氮化物固溶体粉末的制备方法,该制备方法的步骤是:
10.s1、称取纯度≧99.99%的金属钙ca、纯度≧99.99%的金属锶sr、纯度≧99.99%的金属铕eu,将其置于氧化铝坩埚的真空熔炼炉内,抽真空洗炉三次通入氩气作为保护气体,并在700~880℃熔融浇筑于铸锭模具中,获得合金铸锭;
11.s2、将步骤s1获得的铸锭清理表面后,置于氢破碎炉中,用氩气洗炉三次,通入纯度≧99.99%的氢气并加热至200~400℃,使合金铸锭破碎为粗颗粒,然后抽真空,加热至
600℃脱氢,获得合金粗粉末;
12.s3、将氢破碎炉的温度降低至150℃以下,开始通入由纯度≧99.99%的液氮汽化获得的氮气并逐步升温至580℃,压力保持在0.5mpa~0.8mpa,保温5小时,获得高纯锶钙铕氮化物固溶体粗粉末;
13.s4、将步骤s3获得的粗粉末装入不锈钢罐中,移入水、氧含量均小于1ppm的手套箱内,在涂有碳化钨涂层的粉碎机内粉碎获得不同目数的粉末。
14.作为对上述技术方案的改进,在步骤s2中,所述铸锭清理表面是指把铸锭的金属表面的氧化层和杂质造渣去除,然后抛光铸锭的金属表面使其表面残留的氧化层彻底去除。
15.作为对上述技术方案的改进,在步骤s3中,所述压力最佳为0.6~0.7mpa。
16.与现有技术相比,本发明具有的优点和积极效果是:
17.本发明合成的高纯锶钙铕氮化物是固溶体纯净物,不是氮化钙、氮化锶、氮化铕的三种机械混合物,这可从实施例的xrd图谱中看到,本发明固溶体的衍射峰与标准卡片纯氮化锶是相似的,并随着ca量的增加会向大角度移动,这是由于ca2+的离子半径较小的缘故。
18.本发明高纯锶钙铕氮化物固溶体粉末的高纯主要基于以下几点:
19.第一:原料纯度高,使用的原料是金属钙纯度为99.99%、金属锶纯度为99.99%、金属铕纯度为99.99%、,氩气用液氩汽化做保护气纯度达到99.999%以上,氮气用液氮汽化纯度为99.999%以上,氢气纯度达到99.99%,等原辅材料的严格要求。
20.第二:过程控制较好,本发明首先将进出熔融铸锭形成锶钙铕的合金,在熔炼过程中把铸锭的金属表面的氧化层和杂质造渣去除,第二步在进入氢破炉前继续抛光金属表面使其表面残留的氧化层彻底去除。
21.第三:引入氢气破碎工艺,可以避免大块生成物在后期过程中接触氧气水分等有害气体,并且氢气可以将部分未完全氧化的金属还原,进一步降低氧含量。
22.第四:粗粉的后期处理过程中是在水、氧含量均小于1ppm的手套箱中处理,并且是使用涂有高硬度耐磨碳化钨涂层的粉碎机粉碎完成,过程中进一步避免机械杂质的引入。
23.本发明固溶体粉末还有一个特点,由于各种金属经过熔炼工序各种原料是在熔融状态下得到均匀的分布,即从原子层面混合,然后在经过氢破,氮化等工序,所以整个过程获得的产品均一性和一致性较高。
24.本发明的另外还有个一个优点是使用静态高压法制备氮化物固溶体粉末,无需大量的氮气气流,可以避免由于氮气中夹杂的少量杂质气体累积导致产品的杂质不可控。
25.本发明最后一步是合成温度较低,最高温度只需要580℃相比于其他方法温度低,但压力较大,当压力低于0.5mpa时产品会出现反应不彻底,当压力高于0.8mpa时由于反应速度过快,局部温度过高产生熔融,导致反应无法进行,因此本发明的最优选是0.6~0.7mpa。
26.由于本发的固溶体粉末经过了氢破碎环节,金属的表面和内部都存有大大小小或多或少的裂纹,这些裂纹之间的作用是构成了后期在合成氮化物固溶体的时候,氮气进入金属的通道,从而使反应更加容易进行,另外这些细小的裂纹也为后期机械破碎获得不同目数的粉末提拱了助力。
附图说明
27.为了更清楚地说明本发明实施例或现有技术中的技术方案,下面将对实施例或现有技术描述中所需要使用的附图作简单地介绍,显而易见地,下面描述中的附图仅仅是本发明的一些实施例,对于本领域普通技术人员来讲,在不付出创造性劳动性的前提下,还可以根据这些附图获得其他的附图。
28.图1为实施例1-5制得的锶钙铕氮化物粉体的xrd图;
29.图2为对比例1-3中三种荧光粉样品在460nm激发下的发射光谱图。
具体实施方式
30.下面将结合本发明实施例中的附图,对本发明实施例中的技术方案进行清楚、完整地描述,显然,所描述的实施例仅仅是本发明一部分实施例,而不是全部的实施例。基于本发明中的实施例,本领域普通技术人员在没有做出创造性劳动前提下所获得的所有其他实施例,所作的任何修改、等同替换、改进等,均应包含在本发明的保护范围之内。
31.本发明实施例与对比例所用金属钙为99.99%纯度,金属锶为99.99%纯度,金属铕为99.999%纯度,氮化硅为ube,e10产品,氮化铝、氮化钙、氮化锶均为西格玛原料,氮气为99.999%的液氮汽化、氩气用99.999%的液氩汽化,氢气为99.99%纯度氢气。
32.实施例1:(sr
0.992
eu
0.008
)2n
33.称取金属钙819.7g,金属铕1.25g,在真空熔炼炉中用氩气洗炉三次,冲氩气至80kpa加热至800℃熔融成浆液状态,浇注冷却得到合金铸锭。清理干净合金铸锭表面后装入氢破炉中,抽真空三次加热至220℃活化通入氢气然后在加热至400℃保温4h后,加热至600℃抽真空脱去氢气,真空度小于40pa(仪表显示)后,冷却至150℃以下,开始通入氮气至0.4mpa,然后逐步升温至580℃维持气体压力0.5mpa保温4小时,5min内压力表显示不在下将,反应结束。然后冷却至室温状态,用不锈钢罐装料后移入水、氧含量均小于1ppm的手套箱内,用涂有碳化钨涂层的粉碎机内粉碎、过筛得到~150目的粉末样品,编号s-01做xrd检测。
34.实施例2:(sr
0.8
ca
0.185
eu
0.015
)2n
35.称取金属钙83.2g,金属锶786.5g,金属铕25.57g,在真空熔炼炉中用氩气洗炉三次,冲氩气至80kpa加热至830℃熔融成浆液状态,浇注冷却得到合金铸锭。清理合金铸锭表面装入氢破炉中,抽真空三次加热至220℃活化通入氢气然后在加热至400℃保温4h后,加热至600℃抽真空脱去氢气,真空度小于40pa(仪表显示)后,冷却至150℃以下,开始通入氮气至0.4mpa,然后逐步升温至580℃维持气体压力0.5mpa保温4小时,5min内压力表显示不在下将,反应结束。然后冷却至室温状态,用不锈钢罐装料,移入水、氧含量均小于1ppm的手套箱内,用涂有碳化钨涂层的粉碎机内粉碎、过筛得到~150目的粉末样品,编号s-02做xrd检测。
36.实施例3:(sr
0.75
ca
0.235
eu
0.015
)2n
37.称取金属钙295.7g,金属锶543.9g,金属铕31.44g,在真空熔炼炉中用氩气洗炉三次,冲氩气至80kpa加热至850℃熔融成浆液状态,浇注冷却得到合金铸锭。清理合金铸锭表面装入氢破炉中,抽真空三次加热至220℃活化通入氢气然后在加热至400℃保温4h后,加热至600℃抽真空脱去氢气,真空度小于40pa(仪表显示)后,冷却至150℃以下,开始通入氮
气至0.4mpa,然后逐步升温至580℃维持气体压力0.5mpa保温4小时,5min内压力表显示不在下将,反应结束。然后冷却至室温状态,用不锈钢罐装料,移入水、氧含量均小于1ppm的手套箱内,用涂有碳化钨涂层的粉碎机内粉碎、过筛得到~150目的粉末样品,编号s-03做xrd检测。
38.实施例4:(sr
0.535
ca
0.45
eu
0.02
)2n
39.称取金属钙295.7g,金属锶543.9g,金属铕31.44g,在真空熔炼炉中用氩气洗炉三次,冲氩气至80kpa加热至830℃熔融成浆液状态,浇注冷却得到合金铸锭。清理合金铸锭表面装入氢破炉中,抽真空三次加热至220℃活化通入氢气然后在加热至400℃保温4h后,加热至600℃抽真空脱去氢气,真空度小于40pa(仪表显示)后,冷却至150℃以下,开始通入氮气至0.4mpa,然后逐步升温至580℃维持气体压力0.5mpa保温4小时,5min内压力表显示不在下将,反应结束。然后冷却至室温状态,用不锈钢罐装料,移入水、氧含量均小于1ppm的手套箱内,用涂有碳化钨涂层的粉碎机内粉碎、过筛得到~150目的粉末样品,编号s-04做xrd检测。
40.实施例5:(sr
0.55
ca
0.425
eu
0.025
)2n
41.称取金属钙304.4g,金属锶514.2g,金属铕52.46g,在真空熔炼炉中用氩气洗炉三次,冲氩气至80kpa加热至830℃熔融成浆液状态,浇注冷却得到合金铸锭。清理合金铸锭表面装入氢破炉中,抽真空三次加热至220℃活化通入氢气然后在加热至400℃保温4h后,加热至600℃抽真空脱去氢气,真空度小于40pa(仪表显示)后,冷却至150℃以下,开始通入氮气至0.4mpa,然后逐步升温至580℃维持气体压力0.5mpa保温4小时,5min内压力表显示不在下将,反应结束。然后冷却至室温状态,用不锈钢罐装料,移入水、氧含量均小于1ppm的手套箱内,用涂有碳化钨涂层的粉碎机内粉碎、过筛得到~150目的粉末样品,编号s-05做xrd检测。
42.对比例1:
43.称取实施例2的高纯锶钙铕氮化物固溶体粉末100g,加入52.46gsi3n4,45.99galn,混合均匀后装入钼坩埚中在碳管炉内氮气气氛下,1850℃温度下1mpa的压力下保温4小时,获得荧光粉样品,编号d-01。
44.对比例2:
45.称取实施例3的高纯锶钙铕氮化物固溶体粉末100g,加入53.91gsi3n4,447.24galn,混合均匀后在碳管炉内氮气气氛下,1850℃温度下1mpa的压力下保温4小时,获得荧光粉样品,编号d-02。
46.对比例3:
47.称取氮化锶87.03g、氮化钙10.26g、氮化铕2.79g,加入52.46gsi3n4,45.99galn,混合均匀后在碳管炉内氮气气氛下,1850℃温度下1mpa的压力下保温4小时,获得荧光粉样品,编号d-03。
48.结论:
49.从图1可以明显看出随着ca浓度的增大,逐渐向大角度偏移,这时由于ca的半径比sr小的缘故,并没有形成新的ca2n相,说明ca完全进入了锶的位置形成了固溶体。从图2可以看出对比例1、2和3的仅仅只是因为原料不同,导致发光强度3低于1和2。另外1和2的区别是eu含量相同,ca和sr的含量不同,随着钙含量的增加发射峰的位置红移。
50.从图1和2可以看出,用本发明固溶体粉末制备的(ca/sr)alsin3:eu红色荧光粉,其发射强度比直接用氮化钙、氮化锶、氮化铕、氮化硅、氮化铝获得的荧光粉强度更高。原因来自三个方面。1、合成荧光粉的原料锶钙铕已经在原子层面均匀分布,因为在(ca/sr)alsin3荧光粉中eu是占据ca/sr的位置。相比于用氮化钙、氮化锶、氮化铕的制备方案只是在分子层面混合,使ca/sr和eu从小颗粒分子层面的混合改进到原子层面的混合,大大缩短了烧结时eu替代ca/sr原子的扩散距离,并且能够均匀的分布于整个晶体中,可以减少反应时间,产物亮度更高。2、氮化铕无法用机械的方法粉碎到非常细小的尺寸,这样会造成eu离子在荧光粉单个颗粒的不同部位,或不同颗粒上或多或少存在偏析现象,导致发光亮度不能发挥到最佳强度。3、在本发明的固溶体中eu离子首先是以二价形式固溶在sr/ca的位置上,(ca/sr)alsin3荧光粉的发光是eu2+的发光,这还可以消除由于荧光粉制备过程中还原不彻底,eu3+的存在导致发光减弱的情况。
51.另外本身金属锶和钙形成的氮化物为二价离子化合物,以sr2+和ca2+的价态存在,而氮化铕形成的是三价离子化合物,以eu3+存在,但由于eu离子进入了ca的位置,就变成了以钙为基质的固溶体,稳定存在。
52.从对比例附图中可以看到利用锶钙铕固溶体粉末作为原料,比直接用三种单原料合成的荧光粉发射强度高,充分说明了原料混合的均一度,另外对比例1、2说明随着钙锶比例的变化并未对荧光粉强度产生影响只对峰的位置产生影响。