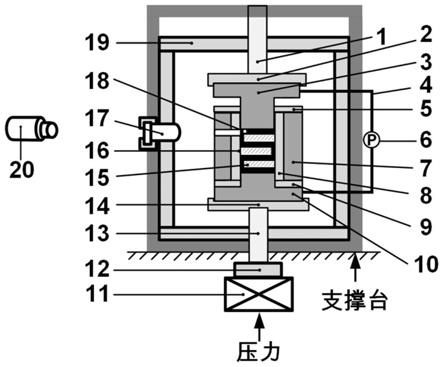
[0001]
本发明涉及陶瓷材料加工技术领域,具体涉及一种快速烧结陶瓷装置及方法。
背景技术:[0002]
陶瓷材料以其高熔点、高强度、高硬度及高温热稳定性等优异性能而被广泛应用于结构和功能领域。目前,陶瓷材料的制备技术主要包括传统高温烧结、反应烧结、热等静压烧结等,这些技术通常依靠热对流或热辐射方式对陶瓷生坯进行加热,而且加热速率较低、烧结周期较长、能源利用率低。对于高温易挥发陶瓷(如锂离子电池材料),较长的烧结时间导致组分挥发,从而削弱了材料的性能。
[0003]
为了降低烧结能耗,缩短周期,人们提出了放电等离子烧结(spark plasma sintering,sps,或称为电火花烧结)。中国专利申请号为201110287859.1,发明人为刘桂武等人提出“高压烧结组合模具及其制备纳米陶瓷的高压快速烧结方法”。他们将装有纳米陶瓷粉末的高压烧结组合模具置于等离子烧结炉中进行烧结。在加热速率100~300℃/min,烧结压力100~1000mpa,烧结温度500~800℃,烧结保温时间3-10min条件下对陶瓷进行烧结。该技术在烧结导电样品时,电流直接流经样品,依靠样品产生焦耳热实现陶瓷烧结。而通常导电样品电阻较小,这就需要较大(几百到上千安培)的直流脉冲电流。当烧结非导电样品时,电流流经石墨模具,较大的石墨模具通过产生焦耳热再对样品进行加热,这无疑极大降低了热量利用效率。中国专利申请号为201910233609.6,发明人为何湘衡等人提出“一种金属氧化物陶瓷材料快速烧结炉及其烧结工艺”。炉膛从上到下依次设置有相互连通的高温腔室、中温腔室、低温腔室。烧结时通过将坯体依次送入低温,中温和高温腔室实现快速烧结。但是该技术依然需要对腔室进行预加热。这种需要依靠炉膛加热来实现样品受热的方式其效率都较低,因为炉膛的加热速率慢,而能实现的最高温度相对较低(高温腔室最高温度为1700℃)。为提高热效率,2010年,科罗拉多大学raj等人发明了一种新技术,在120v/cm场强、850℃温度下,5s内即可将初始致密度为50%的陶瓷生坯烧结致密,由于烧结时会发生闪光现象因而将其称为闪烧(flash sintering of nanograin zirconia in<5s at 850℃,journal of the american ceramic society,2010年93卷11期,p3556-p3559)。中国专利申请号201910058819.6,发明人为蒲永平等人提出的“一种低温快速烧结nbt压电陶瓷的方法”,即属闪烧技术。闪烧过程中样品与电源两端通过电极相连,利用电流流经样品时产生的焦耳热来实现烧结。这就需要样品具有一定导电性。但是通常陶瓷材料多数不导电或室温下导电性弱,需要加热到较高温度部分陶瓷才具有一定的离子或电子导电能力。所以,在闪烧中,通常需要先将炉体加热到一定温度(一般为几百度)以使样品具有一定的导电性。此外,闪烧技术最大的不足在于样品烧结不均匀,且闪烧发生的临界条件在很大程度上取决于电源能力(比如需要极高的电压以驱动陶瓷材料内的离子或电子运动),这导致它的普适性和经济性大打折扣。并且闪烧技术仅适合于单件生产,对样品有着特殊的需求,同时传统电窑炉在对陶瓷材料进行制备时存在着烧结周期长、能耗高、能源利用率低、成本高的缺点,适应性不佳,需要进行改善。
技术实现要素:[0004]
为实现上述目的,本发明提供如下技术方案:
[0005]
一种快速烧结陶瓷装置,包括炉体、开设在炉体一侧的观察窗以及设置在炉体内的加压组件和测温组件,还包括通电组件与绝缘组件,炉体内腔中心处设有石墨模具,石墨模具内设有呈s形设置并放置有样品的石墨软毡;
[0006]
通电组件设置在石墨软毡上下方并与bn侧板相配合,用于对石墨软毡内放置的样品通电加热;
[0007]
加压组件,设置在炉体的上下端,用于对样品压制成型;
[0008]
绝缘组件,分别设置在石墨软毡与石墨模具,加压组件不锈钢上压头和石墨上压头,加压组件不锈钢下压头和石墨下压头,石墨上压头与石墨模具,石墨下压头和石墨模具之间,用于电绝缘,以确保电流只流经石墨软毡,而不流经石墨模具和不锈钢上压头及不锈钢下压头,也不会引起炉体内电流短路,从而保证只对石墨软毡通电加热。
[0009]
作为本发明进一步的方案,通电组件包括石墨上压头、铜电极、电源和石墨下压头,石墨上压头和石墨下压头分别设置在石墨软毡上下方并与石墨软毡相接触,电源设置在炉体外,其两端分别连接有铜电极,两个铜电极另一端分别穿过炉体与石墨上压头和石墨下压头电性连接,铜电极与炉体之间用聚四氟乙烯绝缘并密封。
[0010]
作为本发明进一步的方案,加压组件包括液压控制元件、压力传感器、不锈钢上压头和不锈钢下压头,不锈钢上压头设置在炉体上端部,其底端与石墨上压头上端面相连接,不锈钢下压头设置在炉体下端部,其顶端与石墨上压头固定连接,不锈钢下压头底端与设置在炉体外的液压控制元件输出端固定连接,压力传感器设置在液压控制元件与不锈钢下压头的连接处,用于对液压控制元件施加的压力进行检测。
[0011]
作为本发明再进一步的方案,绝缘组件包括bn侧板、bn上板、bn下板和设置在石墨上压头与石墨下压头上的bn上绝缘套和bn下绝缘套,bn侧板设置在石墨模具内壁与石墨软毡的连接处,bn上板和bn下板分别铺设在石墨模具上下端面,bn上板和bn下板上开设有与石墨上压头和石墨下压头相配合的中心孔。
[0012]
作为本发明再进一步的方案,bn上绝缘套和bn下绝缘套端部分别开设有与不锈钢上压头、不锈钢下压头相配合的螺纹槽。
[0013]
作为本发明再进一步的方案,测温组件包括红外测温仪和设置在bn侧板内壁上的热电偶,bn侧板和石墨模具等高位置处开设有一个通孔,通孔与设置在观察窗外的红外测温仪感应端相对应,红外测温仪另一端与计算机电性连接,用以实时获得石墨软毡的温度与时间曲线。
[0014]
作为本发明再进一步的方案,bn侧板由四瓣拼接而成,围成一个方形孔槽,用于对石墨软毡和样品进行放置。
[0015]
作为本发明再进一步的方案,样品由陶瓷粉末制成,陶瓷粉末为氧化物或碳化物、氮化物、硼化物以及陶瓷金属复合材料中的一种或多种复合。
[0016]
一种快速烧结陶瓷装置的烧结方法,包括以下几个步骤:
[0017]
1)陶瓷粉末在200~500mpa的压力下压制成具有一定形状的样品生坯,然后将样品生坯放置于石墨软毡上,石墨软毡包裹着样品围成s形放置在石墨模具内;
[0018]
2)将石墨上压头和石墨下压头分别与石墨软毡接触,并通过铜电极与电源相连;
[0019]
3)炉子抽真空至10pa以下,然后打开电源开关给石墨软毡通电,调节电流使石墨软毡温度迅速达到预定值,电源电压范围为10-30v,电流范围为20-50a;
[0020]
4)温度恒定后,保持通电5~30s;
[0021]
5)在保温过程中,施加0~50mpa压力,随后断开电源,按一定速率进行降温。
[0022]
作为本发明进一步的方案,样品被包裹在s形叠放的石墨软毡之间,当待烧结样品导电或者高温下会与石墨反应时,且烧结温度≤1200℃时,样品与石墨软毡之间采用0.5mm氧化铝纤维纸使其绝缘,样品、纤维纸与石墨软毡叠成s形放置到石墨模具内;当待烧结样品导电或者高温下会与石墨反应时,且烧结温度>1200℃,样品表面喷涂bn粉体,使其与石墨软毡绝缘。
[0023]
与现有技术相比,本发明的有益效果是:
[0024]
1.与传统烧结方法相比,该方法无需对炉体进行加热,加热速度快,烧结温度高,周期短,极大提高了生产效率,降低了能耗;
[0025]
2.与sps技术相比,本发明方法无需昂贵的直流脉冲电源,所加电流仅为几十安培,远远小于sps用的几百到几千安排的大电流。同时,本发明方法无需对模具进行加热,热量通过热传导直接作用到样品上,加热速度快,能源利用率高,且可以同时烧结多个样品,实现高通量制备,而且,能耗低,装置简单。
[0026]
3.与闪烧技术相比,该方法对材料无特殊选择性要求,且无需通过炉子将样品预热到一定温度,烧结周期短,能实现多样品同时制备。
[0027]
总之,本发明操作简单,高效易行,普适性强,丰富了陶瓷烧结技术,而且获得的陶瓷致密化程度更高。
附图说明
[0028]
图1是本发明采用的一种快速烧结陶瓷装置的原理示意图。
[0029]
图2是本发明中的温度与时间关系的曲线示意图。
[0030]
图3为本发明实施例1所获得的al2o3微观结构形貌图。
[0031]
图4为本发明实施例4所获得的la2zr2o7微观结构形貌图。
[0032]
图5为本发明实施例5所获得的高熵氧化物陶瓷(la
0.2
nd
0.2
sm
0.2
eu
0.2
gd
0.2
)2zr2o7微观结构形貌图。
[0033]
图6为本发明实施例6所获得的tic微观结构形貌图。
[0034]
图中,1、不锈钢上压头;2、bn上绝缘套;3、石墨上压头;4、铜电极;5、bn上板;6、电源;7、石墨模具;8、bn侧板;9、bn下板;10、石墨下压头;11、液压控制元件;12、压力传感器;13、不锈钢下压头;14、bn下绝缘套;15、样品;16、热电偶;17、观察窗;18、石墨软毡;19、炉体;20、红外测温仪。
具体实施方式
[0035]
下面将结合本发明实施例中的附图,对本发明实施例中的技术方案进行清楚、完整地描述,显然,所描述的实施例仅仅是本发明一部分实施例,而不是全部的实施例。基于本发明中的实施例,本领域普通技术人员在没有做出创造性劳动前提下所获得的所有其他实施例,都属于本发明保护的范围。
[0036]
如图1所示,本发明提供了一种快速烧结陶瓷装置,包括炉体19、开设在炉体19一侧的观察窗17以及设置在炉体19内的加压组件和测温组件,还包括通电组件与绝缘组件,炉体19内腔中心处设有石墨模具7,石墨模具7内设有呈s形设置并放置有样品15的石墨软毡18;
[0037]
通电组件设置在石墨软毡18上下方并与bn侧板8相配合,用于对石墨软毡18内放置的样品15通电加热;
[0038]
加压组件,设置在炉体19的上下端,用于对样品15压制成型;
[0039]
绝缘组件,分别设置在石墨软毡18与石墨模具7,加压组件不锈钢上压头1和石墨上压头3,加压组件不锈钢下压头13和石墨下压头10,石墨上压头3与石墨模具7,石墨下压头10和石墨模具7之间,用于电绝缘,以确保电流只流经石墨软毡18,而不流经石墨模具7和不锈钢上压头1及不锈钢下压头13,也不会引起炉体内电流短路,从而保证只对石墨软毡18通电加热;
[0040]
通电组件包括石墨上压头3、铜电极4、电源6和石墨下压头10,石墨上压头3和石墨下压头10分别设置在石墨软毡18上下方并与石墨软毡18相接触,电源6设置在炉体19外,其两端分别连接有铜电极4,两个铜电极4另一端分别穿过炉体19与石墨上压头3和石墨下压头10电性连接,铜电极与炉体之间用聚四氟乙烯绝缘并密封。
[0041]
加压组件包括液压控制元件11、压力传感器12、不锈钢上压头1和不锈钢下压头13,不锈钢上压头1设置在炉体19上端部,其底端与石墨上压头3上端面相连接,不锈钢下压头13设置在炉体19下端部,其顶端与石墨上压头3固定连接,不锈钢下压头13底端与设置在炉体19外的液压控制元件11输出端固定连接,压力传感器12设置在液压控制元件11与不锈钢下压头13的连接处,用于对液压控制元件11施加的压力进行检测;
[0042]
绝缘组件包括bn侧板8、bn上板5、bn下板9和设置在石墨上压头3与石墨下压头10上的bn上绝缘套2和bn下绝缘套14,bn侧板8设置在石墨模具7内壁与石墨软毡18的连接处,bn上板5和bn下板9分别铺设在石墨模具7上下端面,bn上板5和bn下板9上开设有与石墨上压头3和石墨下压头10相配合的中心孔;工作时,绝缘组件用于确保电流只流经石墨软毡18,而不流经石墨模具7和不锈钢上压头1和不锈钢下压头13,也不会引起炉体19内电流短路,从而保证通电组件只对石墨软毡18通电加热;
[0043]
bn上绝缘套2和bn下绝缘套14端部分别开设有与不锈钢上压头1、不锈钢下压头13相配合的螺纹槽;
[0044]
测温组件包括红外测温仪20和设置在bn侧板8内壁上的热电偶16,bn侧板8和石墨模具7等高位置处开设有一个通孔,通孔与设置在观察窗17外的红外测温仪20感应端相对应,红外测温仪20另一端与计算机电性连接,用以实时获得石墨软毡18的温度与时间曲线;炉体19内温度采用红外测温仪20和热电偶16同时测量,也可单独使用,在本实验中所用的红外测温仪20其测温范围为1000~3200℃,样品15的温度通过热电偶16记录,热电偶16连接温控表并将数据传送到计算机;
[0045]
bn侧板8由四瓣拼接而成,围成一个方形孔槽,用于对石墨软毡18和样品15进行放置;
[0046]
样品15由陶瓷粉末制成;陶瓷粉末为氧化物或碳化物、氮化物、硼化物以及陶瓷金属复合材料中的一种或多种复合。
[0047]
实施例1:
[0048]
本实施例所述的一种快速高温烧结al2o3的新方法是按照以下步骤进行的:
[0049]
a、首先将30nm的al2o3粉末与3wt.%pva水溶液混合并研磨均匀,然后在400mpa的压力下压制成20
×
20
×
4mm3的al2o3生坯,初始致密度为50%;
[0050]
b、将a中制备的生坯在空气中600℃预烧1h去除有机物pva;
[0051]
c、将b获得的5个坯体放置在长度为150mm,宽度为20mm,厚度为3mm的s形叠放的石墨软毡18之间,并围成s形放置入在石墨模具7内的bn侧板8方形孔槽中;然后将炉子抽真空至10pa以下;
[0052]
d、通电,使电流迅速达到35a,试样以1000℃/min加热速率达到1800℃,不施加压力,在该温度保温20s后再以该速率降至室温,即完成al2o3快速高温烧结。
[0053]
e、将所得的坯体采用阿基米德法测量其密度,并计算其致密度可得到92%。
[0054]
本发明实施例1中记录的温度随时间的变化曲线如图2所示;其微观结构如图3所示。
[0055]
实施例2:
[0056]
本实施例与实施例1不同的是:所述的初始氧化铝颗粒尺寸为500nm,电流大小为40a,烧结温度为2000℃,其他参数和步骤与实施例1相同,测得的致密度高达95%。
[0057]
实施例3:
[0058]
本实施例与实施例1不同的是:样品15尺寸为φ12
×
4mm2,石墨软毡18尺寸为150mm
×
20mm
×
5mm,电流大小为35a,烧结温度为1800℃,其他参数和步骤与实施例1相同,测得的致密度高达95%。
[0059]
实施例4:
[0060]
本实施例选用的陶瓷粉末为30nm的复合氧化物陶瓷la2zr2o7,样品尺寸为φ6
×
4mm2,样品数量为10个,石墨软毡尺寸为100
×
15
×
4mm3,施加电流大小为40a,温度为1900℃,保温时间为22s,加热和降温速率为750℃/min。其他参数和步骤与实施例1相同,陶瓷致密度高达97%,其微观结构如图4所示。
[0061]
实施例5:
[0062]
本实施例选用的陶瓷粉末为30nm的高熵氧化物陶瓷(la
0.2
nd
0.2
sm
0.2
eu
0.2
gd
0.2
)2zr2o7,样品尺寸为φ6
×
4mm2,石墨软毡尺寸为120
×
15
×
4mm3,样品数量为6个,施加电流大小为35a,温度为1800℃,加热和降温速率为400℃/min。其他参数和步骤与实施例1相同,陶瓷致密度高达98%,其微观结构如图5所示。
[0063]
实施例6:
[0064]
本实施例选用的陶瓷粉末为1μm的tic,与实施例1不同的是陶瓷粉勿需与pva水溶液混合也不需在600℃预烧去除有机物。tic坯体表面喷涂bn绝缘以确保石墨软毡产生足够的焦耳热。样品尺寸为φ12
×
4mm2,石墨软毡尺寸为150
×
20
×
3mm3,数量5个,施加电流大小为48a,温度为2300℃,加热和降温速率为1500℃/min,施加压力大小为27mpa。陶瓷致密度高达94%,其微观结构如图6所示。
[0065]
实施例7:
[0066]
本实施例选用的陶瓷粉末为1μm的si3n4,不同的是陶瓷粉勿需与pva水溶液混合也不需在600℃预烧去除有机物。样品尺寸为20mm
×
20mm
×
3mm,数量4个,石墨软毡尺寸为150
×
20
×
3mm3,施加电流大小为35a,温度为1800℃,加热和降温速率为1000℃/min,施加压力大小为30mpa,陶瓷致密度高达95%。
[0067]
实施例8:
[0068]
本实施例选用的陶瓷粉末为1μm的tib2,与实施例1不同的是陶瓷粉勿需与pva水溶液混合也不需在600℃预烧去除有机物。tib2坯体表面喷涂bn绝缘以确保石墨软毡产生足够的焦耳热。石墨软毡尺寸为160
×
20
×
3mm3,样品尺寸为10mm
×
10mm
×
3mm,数量5个,施加电流大小为45a,温度为2200℃,加热和降温速率为1500℃/min,施加压力大小为28mpa,陶瓷致密度高达94%。
[0069]
实施例9:
[0070]
本实施例选用的陶瓷粉末为1μm的li
1.5
al
0.5
ge
1.5
(po4)3(lagp),与实施例1不同的是lagp坯体与石墨软毡之间通过氧化铝纤维纸隔绝。纤维纸与石墨软毡之间紧密接触并成s形叠层放置。石墨软毡尺寸为150
×
20
×
2mm3,施加电流大小为20a,温度为1000℃,加热和降温速率为2000℃/min,无需施加压力,陶瓷致密度高达94%。
[0071]
本发明的工作原理是:装置在工作时,将陶瓷粉末在一定的压力下压制成一定尺寸的样品15生坯,将样品15置于炉体19内s形叠放的石墨软毡18之间,电源6启动,通过铜电极4给石墨软毡18施加直流电,温度稳定后,加压组件施加压力,样品15在焦耳热传导和压力的作用下在数秒内快速烧结,断电后样品15迅速降至室温;陶瓷采用电流热效应和热传导实现了较快的加热速率,同时避免了大量热量散失;样品15在超快的加热速率下绕过了低温缓慢加热阶段,从而减少了颗粒长大并保持了较高的烧结驱动力,提高了致密化速率;本发明操作简单,高效易行,普适性强,丰富了陶瓷烧结技术,而且获得的陶瓷致密化程度更高,适用性更宽泛。对于本领域技术人员而言,显然本发明不限于上述示范性实施例的细节,而且在不背离本发明的精神或基本特征的情况下,能够以其他的具体形式实现本发明。因此,无论从哪一点来看,均应将实施例看作是示范性的,而且是非限制性的,本发明的范围由所附权利要求而不是上述说明限定,因此旨在将落在权利要求的等同要件的含义和范围内的所有变化囊括在本发明内。不应将权利要求中的任何附图标记视为限制所涉及的权利要求。
[0072]
此外,应当理解,虽然本说明书按照实施方式加以描述,但并非每个实施方式仅包含一个独立的技术方案,说明书的这种叙述方式仅仅是为清楚起见,本领域技术人员应当将说明书作为一个整体,各实施例中的技术方案也可以经适当组合,形成本领域技术人员可以理解的其他实施方式。