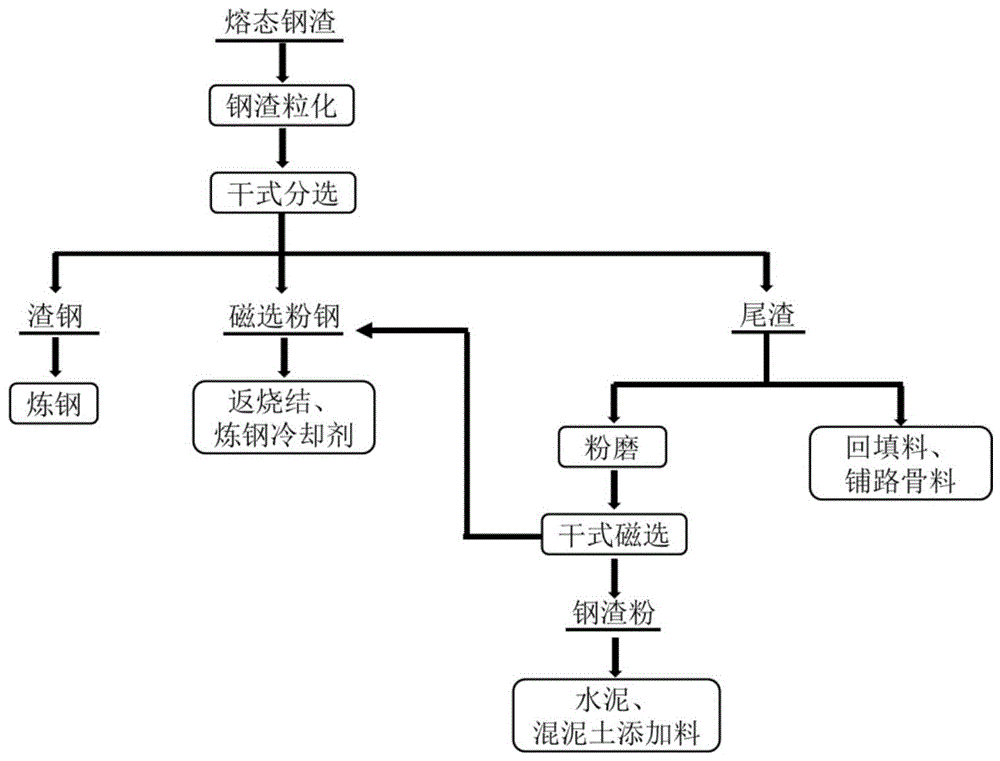
本发明涉及冶金固废处理
技术领域:
,尤其涉及一种钢渣全量利用方法。
背景技术:
:每生产一吨钢约产生150kg钢渣,目前我国的钢渣堆存量已超过10亿吨,利用率仅为10~20%。图1中给出了钢渣的处理利用流程,总的来说,钢渣需要进行粒化、磁选等处理后分级利用。钢渣的粒化方式包括热闷法、盘泼法、风淬法、水淬法、滚筒法、粒化轮法,本质上均以水作为冷却剂,除了风淬法能回收少部分热量外,其他方法中钢渣的热能都被浪费还消耗大量的水资源。其次,磁选粉钢的铁品位较低、磷含量较高,作为烧结配料会造成磷在铁水的富集,降低烧结矿的铁品位,提高铁水的处理成本。另外,钢渣碱度高,即使经过粒化消解处理,尾渣中仍含有一定含量的游离cao、mgo,且急冷后硅酸钙处于亚稳相,造成尾渣的组织稳定性差,直接作为回填料或铺路料时需堆放使其达到稳态化,耗时较长。如对尾渣进行研磨、磁选处理再利用,由于尾渣致密、坚硬,可磨性较差,制备钢渣微粉的磨矿成本高,降低了利用经济性,并且作为水泥或混凝土添加料时吸水性较强,会缩短硬化时间,铁含量高,添加量一般控制在30%以内,用量受到限制。因此,目前钢渣磁选之后的尾渣利用率极低,主要采取堆存处理,成为钢铁企业的顽疾。目前采用还原法处理钢渣受到关注。热态钢渣首先通过碳热还原,钢渣中的铁氧化物以及大部分磷还原进入铁水,高磷铁水再经碳酸钾脱磷得到磷酸钾,用于制备磷钾复合肥料,脱磷后的铁水返回炼钢。同时,还原后的低磷钢渣用作烧结熔剂或水泥原料。该工艺的优势在于回收了钢渣中的铁和磷,同时,还原后的尾渣不含铁,降低了钢渣的磨矿成本并增加了钢渣在水泥中的添加量,对钢渣的利用起到了较好的促进作用。但是,钢渣的产量没有实现源头减量,而末端利用价值受限于水泥的市场环境,尽管钢渣作为烧结熔剂可以烧结环节的熔剂消耗量,但钢渣的有效熔剂含量远低于石灰,降低了烧结矿的品位以及高炉熔炼过程的渣量。最理想的情况是,钢渣在回收磷和铁之后返回炼钢环境循环利用,可以大幅降低熔剂的添加量,同时缩短造渣时间。但是,钢渣的碳热还原过程中硫依然以cas的形态存在于钢渣中,循环利用富集后会降低钢渣的脱硫效果。另外,高磷铁水的脱磷需要消耗碳酸钾,碳酸钾的价格较高,并且在高温下易分解挥发,高温脱磷过程中的损耗较大,同时铁水中的碳含量较高,需返回炼钢过程重新吹炼。技术实现要素:鉴于上述的分析,本发明旨在提供一种钢渣全量利用方法,至少解决以下技术问题之一:(1)钢渣中的铁、硫、磷无法全量利用;(2)在炼钢过程中消耗大量的碱性熔剂;(3)大量尾渣堆存产生的环境污染问题。本发明提供一种钢渣全量利用方法,在钢渣处理过程中将钢渣中的硫、磷进行脱除回收,得到高纯氧化铁粉和低硫低磷熔分渣,全量利用不产生尾渣,包括以下步骤:步骤1.向钢渣通入空气或氧气,将钢渣中的硫转化为二氧化硫脱除,得到脱硫钢渣;步骤2.向脱硫钢渣中加入碳质还原剂进行碳热还原,钢渣中的磷还原后部分以p2蒸汽的形态脱除,得到高磷高碳铁水和低硫低磷熔分渣,低硫低磷熔分渣返回炼钢环境循环利用;步骤3.对高磷高碳铁水进行雾化氧化,铁水中的碳、硫、磷杂质以气态氧化物形式脱除,得到高纯氧化铁粉;步骤4.步骤1、2、3得到的所有含碳、硫、磷气体混合氧化,冷却气体中的硫和磷分别制备硫酸和回收五氧化二磷。进一步地,所述步骤3中得到的高纯氧化铁粉还原制备高纯铁。进一步地,所述步骤4中混合氧化后的气体经余热锅炉回收余热降温至200℃以下,从气相中以固体形式沉积回收p2o5,沉积回收p2o5后的气体喷水处理,so3转化为工业硫酸。进一步地,所述步骤1中,通入的氧气与钢渣中金属铁的物质的量之比为0.45:1至0.9:1。进一步地,所述步骤1中,钢渣升温至1650℃-1750℃,保温1h至1.5h。进一步地,所述步骤1中,氧气的通入流量为1.8l/min至2l/min。进一步地,所述步骤1中,氧气的鼓吹时间为30min至60min。进一步地,所述步骤2中,高磷高碳铁水中,磷的含量为2.3%-2.4%,碳的含量为4.3%-4.6%。进一步地,所述步骤2中,低硫低磷熔分渣中,磷含量为0.041-0.047%,硫含量为0.008-0.013%。进一步地,所述步骤2中碳还原剂为低硫碳质还原剂,所述低硫碳质还原剂为兰炭或石墨粉,加入的碳质还原剂中碳与脱硫钢渣中铁氧化物中氧原子的物质的量之比为1.5-1.8:1。进一步地,所述步骤2在1700℃-1800℃下碳热还原40min至60min。进一步地,所述步骤3中,使用高压空气对高磷高碳铁水进行雾化氧化,氧化时间为30-50min。进一步地,所述步骤3中,高压空气气流对高磷高碳铁水进行雾化氧化,氧化温度为1500℃至1600℃。进一步地,所述步骤3中,空气的流量为2l/min至2.8l/min。进一步地,所述步骤3中气态氧化物为二氧化碳、三氧化硫、五氧化二磷。进一步地,所述步骤4中,氧化的温度为1000℃至1100℃。与现有技术相比,本发明至少可实现如下有益效果之一:(1)本发明通过首先对钢渣通入空气或氧气进行氧化,先将钢渣中杂质硫转化为二氧化硫脱除,氧化过程中硫化钙转化为氧化钙并与铁氧化后的三氧化二铁结合成铁酸钙,将钢渣中杂质硫实现率先脱除,避免了现有技术处理后钢渣中硫的留存,影响钢渣在炼钢环节循环利用时的脱硫效果。(2)脱硫后的钢渣通过碳热还原,与现有技术相比渣中的磷几乎全部被还原,一部分磷与金属铁结合进入铁水,得到高磷高碳铁水,另一部分磷以磷蒸气的形态脱除进入气相,得到的熔分渣几乎不含硫、磷,避免熔分渣在炼钢环节循环利用时影响脱磷效果。(3)高磷高碳铁水通过高压空气进行雾化冷却,铁水中的硫和磷几乎完全氧化脱除,得到高纯氧化铁粉末,可作为制备高纯铁的原料,提高产品的附加值。(4)钢渣脱硫氧化阶段、脱硫渣碳热还原阶段与高磷高碳铁水雾化氧化阶段产生的气体进行混合,钢渣脱硫氧化阶段产生的so2气体、脱硫渣碳热还原阶段产生的co气体和p2蒸气,被高磷高碳铁水雾化氧化阶段产生的气体中的残余o2氧化,最终混合氧化后的气体为so3、co2、p2o5,so3用于硫酸制备,p2o5直接回收。与现有技术相比,在钢渣处理利用过程,对钢渣中的各种物质进行充分利用,无处理后的尾渣生成,实现了钢渣的全量利用,解决了目前钢渣堆存的问题。(5)本发明提供的钢渣全量利用方法,在钢渣处理过程中将钢渣中的硫、磷进行脱除回收,得到高纯氧化铁粉和低硫低磷熔分渣,全量利用不产生尾渣。本发明中,上述各技术方案之间还可以相互组合,以实现更多的优选组合方案。本发明的其他特征和优点将在随后的说明书中阐述,并且,部分优点可从说明书中变得显而易见,或者通过实施本发明而了解。本发明的目的和其他优点可通过说明书以及附图中所特别指出的内容中来实现和获得。附图说明附图仅用于示出具体实施例的目的,而并不认为是对本发明的限制,在整个附图中,相同的参考符号表示相同的部件。图1为现有技术钢渣的处理和利用流程;图2为钢渣多级氧化-还原处理及全量利用流程图。具体实施方式钢渣中主要成分是铁、镁、钙、硅、铝,也含有一部分磷和硫杂质。其中,硫是制备硫酸的主要原料和核心元素,磷是制备各种磷酸类化合物、磷酸酯类化合物、红磷、白磷的主要原料和核心元素。因此,对于钢渣的全量利用,需要实现对钢渣中的硫、磷杂质提取出来,并将其转换为可以利用的相关化工原料;除此之外,还要实现钢渣中主要成分铁和渣的回收利用。由于钢渣中的硫、磷在炼钢环节循环利用过程中极易重新进入钢水造成对钢水的污染,因此必须脱除后才能返回炼钢环节循环利用。并且,还原过程中碳、硫、磷极易进入铁水,造成铁水硫、磷含量超标,必须对铁水进一步处理提升品质。基于此,在钢渣全量利用的方法中必须最先将硫元素从钢渣中分离。热态钢渣通过空气或纯氧,氧气与钢渣中的铁、氧化亚铁和硫化钙反应,形成铁酸钙以及二氧化硫,实现硫的脱除。经过研究,氧气的通入量与钢渣中金属铁的摩尔比控制在0.45~0.9之间,钢渣中的硫含量降至0.02%以下:3o2(g)+cas+2fe=so2(g)+cao·fe2o32o2(g)+cas+2feo=so2(g)+cao·fe2o33o2(g)+cao+4fe=2cao·fe2o3o2(g)+2cao+4feo=2cao·fe2o3在氧气作用下,硫被氧化成为二氧化硫气体脱离体系,而铁同时被氧化并与氧化钙结合为铁酸钙,在上述两种作用下,实现了硫的分离,同时避免了硫酸钙的生成。脱除硫的钢渣发现,各元素因被氧气均氧化为高氧化态无法进一步分离,因此加入还原剂,包括兰炭或石墨粉等低硫碳质还原剂。需要说明的是,可以使用的还原剂虽然较多,但使用其他还原剂会在钢渣中引入新的杂质元素,因此还原剂立足于目前体系中已有的元素,考虑到碳质还原剂还原能力强,价格便宜,钢铁生产中普遍使用,因此选择兰炭或石墨粉等低硫碳质还原剂。基于此,脱除硫的钢渣喷入兰炭或石墨粉等低硫碳质还原剂进行直接还原,磷大部分还原进入铁水,少部分以p2的形式进入气相,同时部分碳溶解进入铁水。经过研究,还原后的熔分渣铁含量低于2%、磷含量低于0.05%,可以返回炼钢环节循环利用:ca3(po4)2+5c=3cao+5co+p23c+cao·fe2o3=3cao+5co+fe铁的氧化物被碳还原为铁水,未反应完全的碳和被碳还原的磷溶解在铁水中,构成了高磷高碳的铁水。高磷、高碳铁水通过空气高压喷头将铁水雾化成为小铁珠,并同时铁被氧化为不同形态的氧化铁。研究发现,其中的碳、硫、磷全部氧化为气体进入气相,氧化铁粉末中碳、硫、磷含量之和低于0.01%:fes+2o2=2feo+so2c+o2=co24fe3p+11o2=12feo+2p2o52fe+o2=2feo6feo+o2=2fe3o44fe3o4+o2=6fe2o3铁水经过空气雾化氧化后,铁被氧化为氧化铁粉末,磷被氧化为五氧化二磷气体,碳被氧化为二氧化碳气体,因此可以顺利的将氧化铁粉末与五氧化二磷气体和二氧化碳气体分离。需要补充说明的是,此步骤中少量的杂质硫也被空气氧化为二氧化硫,随五氧化二磷和二氧化碳一起在气相中与氧化铁粉末实现分离。与此同时,钢渣氧化阶段与脱硫钢渣碳热还原阶段产生的气体与铁水雾化氧化阶段产生的气体混合,由于铁水雾化氧化阶段以过量空气为氧化剂,气体中有残余的氧气存在,钢渣氧化阶段产生的so2和脱硫钢渣碳热还原阶段产生的co、p2被完全氧化。2so2+o2=2so32co+o2=2co22p2+5o2=2p2o5混合氧化后的气体包括p2o5、co2、so3、o2和n2五种主要成分,将混合气体通过余热锅炉回收余热,温度降至200℃以下,p2o5以固体粉末从气相沉积分离回收,脱除磷之后的气体通过喷水吸收so3制备硫酸,实现硫的脱除,剩余气体达标排放。so3+h2o=h2so4以此实现了钢渣中的全量利用。下面结合附图来具体描述本发明的优选实施例,其中,附图构成本申请一部分,并与本发明的实施例一起用于阐释本发明的原理,并非用于限定本发明的范围。实施例一本发明的一个具体实施例,公开了一种钢渣全量利用方法,如图2所示。转炉钢渣成分如表1所示,tfe含量为17.3%,s含量为0.09%,p2o5含量为1.42%。表1转炉钢渣主要化学成分成分sio2mfeal2o3feomgosp2o5cao质量分数%7.86.31.3714.14.640.091.4251.02将1kg钢渣放置在感应电炉内,感应电炉以石墨坩埚为发热体,石墨坩埚内部以镁砂为耐材,防止渗碳。温度升高至1650℃后保温1h,保证钢渣充分熔化,将压缩空气通过一根刚玉管以2l/min的流量鼓入熔渣中,鼓吹时间为30min,此时通入的o2与钢渣中金属铁的摩尔比为0.45。渣样冷却后破碎、研磨至粒度小于0.074mm(200目)的粉末,通过碳硫分析仪测定钢渣中的硫含量为0.018%。将脱硫之后的钢渣经化学滴定分析确定三氧化二铁、四氧化三铁和氧化亚铁含量,根据钢渣的铁氧化物含量配入石墨粉,控制c/o为1.2,混合均匀的试样分别在电阻炉内1700℃保温40min进行还原。还原试样冷却后,通过荧光分析分别测定熔分渣、铁水的磷含量,通过碳硫分析仪测定铁水的碳、硫含量和熔分渣的硫含量。此时,熔分渣磷、硫含量为0.047%、0.013%,铁水的磷、硫、碳含量分别为2.33%、0.04%、4.34%。还原得到的铁水冷却后破碎为细小的金属铁粒,称量40g装入刚玉皿内在管式电阻炉内加热至1600℃,以2l/min的流量通入空气进行氧化,氧化时间为30min。冷却后的氧化试样通过碳硫分析仪测定碳、硫含量,荧光分析测定磷含量。此时,碳含量为0.005%,硫含量为0.001%,磷含量为0.003%。将白磷固体放置在刚玉皿内,刚玉皿放置在两端设有通气口的管式电阻炉内,从管的一端通入co2、so2和空气,电阻炉从室温升温至1000℃,模拟混合氧化过程。从管式炉出口端排出的气体进入一个外部喷水冷却的密闭钢质圆筒降温,分离出颗粒状的p2o5,从圆筒排出的气体进入装水的密闭塑料桶吸收so3,剩余气体通过红外气体分析仪分析表明so3被完全吸收转化成硫酸。实施例二本发明的一个具体实施例,公开了一种钢渣全量处理利用方法。选取与实施例一相同的钢渣1kg放置在感应电炉内,温度升高至1750℃后保温1.5h,保证钢渣充分熔化,将压缩空气通过一根刚玉管以1.8l/min的流量鼓入熔渣中,鼓吹时间为60min,此时通入的o2与钢渣中金属铁的摩尔比为0.9。渣样冷却后破碎、研磨至粒度小于0.074mm(200目)的粉末,通过碳硫分析仪测定钢渣中的硫含量为0.004%。将脱硫之后的钢渣经化学滴定分析确定三氧化二铁、四氧化三铁和氧化亚铁含量,根据钢渣的铁氧化物含量配入石墨粉,控制c/o为1.5,混合均匀的试样分别在电阻炉内1800℃保温60min进行还原。还原试样冷却后,通过荧光分析分别测定熔分渣、铁水的磷含量,通过碳硫分析仪测定铁水的碳、硫含量和熔分渣的硫含量。此时,熔分渣磷、硫含量为0.041%、0.008%,铁水的磷、硫、碳含量分别为2.38%、0.043%、4.51%。还原得到的铁水冷却后破碎为细小的金属铁粒,称量40g装入刚玉皿内在管式电阻炉内加热至1500℃,以2.8l/min的流量通入空气进行氧化,氧化时间为50min。冷却后的氧化试样通过碳硫分析仪测定碳、硫含量,荧光分析测定磷含量。此时,碳含量为0.002%,硫含量为0.001%,磷含量为0.001%。将白磷固体放置在刚玉皿内,刚玉皿放置在两端设有通气口的管式电阻炉内,从管的一端通入co2、so2和空气,电阻炉从室温升温至1100℃,模拟混合氧化过程。从管式炉出口端排出的气体进入一个外部喷水冷却的密闭钢质圆筒降温,分离出颗粒状的p2o5,从圆筒排出的气体进入装水的密闭塑料桶吸收so3转化成硫酸。以上所述,仅为本发明较佳的具体实施方式,但本发明的保护范围并不局限于此,任何熟悉本
技术领域:
的技术人员在本发明揭露的技术范围内,可轻易想到的变化或替换,都应涵盖在本发明的保护范围之内。当前第1页12