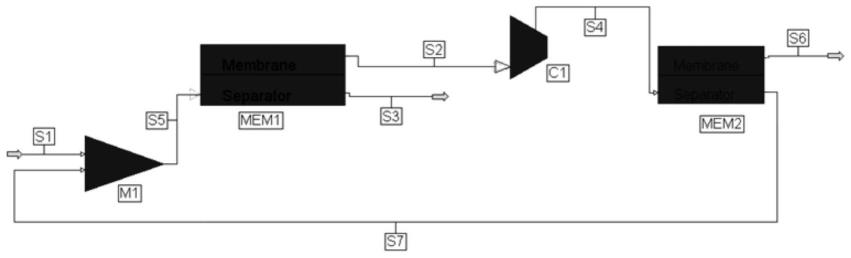
1.本发明涉及一种用于高纯氧制备的氧氩膜法分离工艺,属于功能膜和航海安全技术领域。
背景技术:2.作为基础性气体,氧气在舰船上的用途主要包括呼吸与燃烧、医疗保障用氧、应急维修焊接用氧等。随着我国舰船的现代化发展,其对氧气的需求量及品质要求进一步提高,采用高压气瓶作为氧气的保障来源已经越来越难以满足要求,因此开发可实现氧气自我保障能力的舰载高纯氧制备技术与装备具有极其重要的意义。
3.在以非深冷工艺制取船用气体的各种工艺中,以高纯氧制备最为困难。目前我国船舰上的氧制备技术采用以空气为原料气的变压吸附工艺,但受吸附平衡限制,只能从空气中制得~95%的普氧,其中尚含~5%的氩气及少量氮气,无法满足医用高纯氧含量不低于99.5%的国家标准。
4.中国专利cn201910415672.1公开了一种高纯氧气的制备装置及其制备方法,包括在船舶上设置的变压吸附法制氧装置和碳基分子筛制氧装置,在碳基分子筛制氧装置中的碳基分子筛吸附罐中的分子筛的微孔结构为2.8a-2.9a;在制备气输入管上设置有第二空气压缩泵,93%氧含量的制备好的氧气输出管通过第二空气压缩泵与制备气输入管连通,制备气输入管通过入气阀与碳基分子筛吸附罐连通,在碳基分子筛吸附罐上还分别设置有氩气排出管和高纯氧解吸输出管,高纯氧解吸输出管通过解吸输出阀与高纯氧贮存罐连接。此发明描述的工艺可以制备99.5%高纯氧,但是频繁的吸附解吸工艺复杂,且能耗高,占地大,对于舰船系统会造成了极大的能耗及空间负担。
5.此外中国专利cn201910621431.2公开了一种空气为原料的高纯氧生产装置及其生产装置,空气膨胀机通过管道经冷却器、主换热器与空气再沸器连接;空气再沸器通过管道与主换热器连接;带压力的天然气原料通过管道经主换热器与精馏塔底部的lng再沸器连接;以及精馏塔顶部通过管道与冷凝蒸发器底部连接;冷凝蒸发器顶部通过管道经粗氦过冷器与气液分离器连接。基于本发明装置的高纯氧生产方法,其以空气为原料,利用氮气的返流膨胀,实现高纯氧气的生产,并且高纯氧气以液体形式产出。该装置基于冷凝及精馏工艺制备高纯氧,在陆地上可为一种技术选择,但是在舰船上明显存在因能耗及占地所造成的现实困难。
6.此外中国专利cn105865148b提供一种高效生产高纯氧和高纯氮的方法,采用了高、中、低压精馏塔,且中、低压精馏塔的塔底分别设置再沸器和冷凝蒸发器,一部分空气在高压精馏塔内分离成高压氮气和富氧液空,另一部分空气进入中压精馏塔再沸器冷凝成液空;所述液空与所述富氧液空混合进入高压精馏塔冷凝蒸发器中蒸发成气态,再进入中压精馏塔;之后从中压精馏塔分离出高纯氮气产品和富氧液,该富氧液进入低压精馏塔,精馏后得高纯液氧产品。
7.如上所述,鉴于船上空间受限,空气湿度高盐度,航行振动冲击等问题的存在,为
基于多级吸附、低温精馏等技术的气体分离设备在舰船上的应用带来了极大的技术挑战。
8.为达到99.5%医用标准高纯氧的制备,变压吸附和膜分离耦合工艺是仅有的可靠选择。在膜的选择上基于致密陶瓷膜的富氧工艺技术上是可行的,但是其装备成本昂贵且需在极高温度下运行,无法在安全上较好地满足舰载要求;与之相比,有机聚合物分离膜可在室温下操作,过程简单稳定,可靠性强,能耗低,是舰载制氧系统的较好选择。
9.基于以上背景,本发明提供了一种用于高纯氧制备的氧氩膜法分离工艺。
技术实现要素:10.鉴于目前我国大吨位舰船对高纯氧制备技术的紧迫需求及高性能氧氩分离技术严重缺失的现实情况,本发明基于变压吸附-膜分离耦合技术,提供了一种以变压吸附制备的~95%普氧为原料气,依靠高性能聚合物分离膜的脱氩富氧分离技术,采用两级膜分离可制备满足国家医用高纯氧标准即99.5%浓度的高纯氧。本发明提供的膜法氧氩分离制备高纯氧技术可以在满足浓度要求的前提下尽可能提高系统的氧回收率,为我国舰船上高纯氧制备技术提供可靠选择。
11.选择适合的膜对本发明所涉及的高纯氧制备过程中氧氩分离至关重要。气体分子以“溶解扩散”机理渗透通过聚合物膜,其在膜内的渗透速率取决于两个因素:在膜内的溶解度系数及扩散系数。溶解度系数与气体分子与膜材料的亲和性相关,而扩散系数则取决于气体分子的大小。对本发明所分离的氧氩气体对而言,氧气的分子动力学直径为0.346nm,而氩气的分子动力学直径为0.34nm,两者非常接近且氩气小于氧气,使得两者的“扩散”选择性接近1,所以要提高氧氩分离系数,只能从调控“溶解”选择性角度出发,因此对氧氩分离膜的选择要从其对氧气与氩气的溶解选择性进行筛选。
12.膜材料是分离膜的核心,其本征渗透分离性能决定了分离膜所能实现功能的高度,聚酰亚胺作为膜材料具有优越的气体渗透分离性能,气体在聚合物膜中的渗透主要依赖聚合物链段和侧基的局部运动能力和自由体积。适用于膜分离的单体包括主要为芳香二酐和二胺,通过不同单体组合可以获得不同性能的聚酰亚胺。与柔性基团相比,刚性基团具有更紧密的分子堆积密度及更小的自由体积,更有望产生较高的氧氩“溶解”选择性能。因此尽管用于氧氩分离过程膜选择性很多,主要包括聚酰亚胺膜、聚醚酰亚胺膜、聚砜膜、醋酸纤维素、聚偏氟乙烯膜、聚苯砜膜、聚醚醚酮、聚四甲基异戊烯等;但从实际应用角度出发,聚酰亚胺膜是第一选择。
13.本发明的具体工艺采用图1所示的两级膜分离系统,原料气s1为变压吸附制备的普氧,直接进入一级膜组件mem1,一级渗余气s3所含氧浓度较低直接放空,一级渗透气s2经压缩机c1升压后进入二级膜组件mem2,二级渗透气s6即为满足医用氧国家标准的高纯氧产品气,二级渗余气s7因为氧含量仍较高故与原料气经混合器m1混合后循环进入一级膜组件;
14.本发明所提供的超纯氧制备技术采用的原料气为船载变压吸附系统所制备的普氧,其中含有氧浓度为93.0~96.0%,氩浓度为3.0~5.0%,氮浓度为1.0~2.0%;
15.本发明可采用的分离膜为聚酰亚胺膜、聚醚酰亚胺膜、聚砜膜、醋酸纤维素、聚偏氟乙烯膜、聚苯砜膜、聚醚醚酮、聚四甲基异戊烯等;膜材料是分离膜的核心,其本征渗透分离性能决定了分离膜所能实现功能的高度,聚酰亚胺作为膜材料具有优越的气体渗透分离
性能,气体在聚合物膜中的渗透主要依赖聚合物链段和侧基的局部运动能力和自由体积。适用于膜分离的单体包括主要为芳香二酐和二胺,通过不同单体组合可以获得不同性能的聚酰亚胺。与柔性基团相比,刚性基团具有更紧密的分子堆积密度及更小的自由体积,更有望产生较高的氧氩“溶解”选择性能。因此尽管用于氧氩分离过程膜选择性很多,但从实际应用角度出发,聚酰亚胺膜是第一选择。
16.本发明所采用的聚酰亚胺膜,其材料的本征氧氮分离系数一般应不低于6.5,氧氩分离系数不低于3.5。采用此材料制备的聚酰亚胺中空纤维膜,通过调控纺丝喷方及工艺参数,改膜的氧氩分离系数一般不低于3.7;氧氮分离系数一般不低于7.0;
17.基于本发明所采用分离膜的氧气优先透过性,在进行分离过程中,氧气优先于氩气及氮气渗透通过膜,使得在膜组件的渗透侧为富氧气体,渗余侧氧浓度低于原料气;在进行实际分离过程中,采用两级膜分离工艺,原料气中氧浓度经一级膜分离组件提浓后,需经过压缩增压后再进入二级膜分离组件进行进一步提浓,以使得二级渗透气的氧气含量满足国家医用高纯氧标准;
18.一般而言经过一级膜分离组件后,渗透气中氧浓度要增加到98.0~99.0%范围;经过二级膜分离组件后,渗余侧氧浓度为98.5%以上,渗透气中氧浓度不低于99.5%。考虑到二级渗余气的氧气浓度要高于经变压吸附制备的普氧原料气中的氧气浓度,这部分气体的循环回流进入一级膜组件会使得整个原料气的氧气浓度提升,有利于制备得到满足要求的医用高纯氧。
19.本发明提供了一种可用于大型船舶上符合国家医用标准的高纯氧膜法制备方法,目前船舶上制氧系统以变压吸附为主,受吸附平衡限制,只能制备出~95%的普氧,其中尚含~5%的氩气。鉴于船上空间受限,空气湿度高盐度,航行振动冲击等问题的存在,为基于多级吸附、低温精馏等技术的气体分离设备在舰船上的应用带来了极大的技术挑战。为满足氧含量不低于99.5%的国家医用高纯氧标准,本发明提供了一种经济适用、安全可靠的基于高性能聚合物分离膜的脱氩富氧分离技术,采用两级膜分离,可以在满足浓度要求的前提下尽可能提高系统的氧回收率。与传统变压吸附过程比较,膜分离具有过程简单,占地少,能耗低、易放大等优点,应用于舰船体系高纯氧制备过程具有明显的技术优势。
20.与常用的基于多级吸附、低温精馏等技术的气体分离装置及过程相比,本发明具有以下技术优势:
21.(1)采用膜法对制备医用高纯氧过程简单且稳定可靠、能耗低;
22.(2)中空纤维膜尺寸小,比表面高,中空纤维膜组件体积小,不会对船舰体系造成过大的空间负担;
23.(3)膜组件规格可变,可依据具体高纯氧制备要求选择合适的膜组件,适应性强。
24.基于以上总结,本发明所提供的一种一种可用于大型船舶上符合国家医用标准的高纯氧膜法制备方法,对实现我国舰船高纯氧制备工艺过程具有重要价值。
附图说明
25.图1两级膜法氧氩分离系统
26.图2聚酰亚胺中空纤维膜显微镜照片(膜丝外径~0.3mm)
具体实施方式
27.本发明采用的膜组件的结构和操作方式如下:
28.一级膜组件和二级膜组件的结构都为常用的集束式膜组件,分别由500根中空纤维膜装在中空密闭组件壳内,两端通过环氧树脂密封的形式使中空纤维膜靠近二开口端的外壁面四周边缘分别与组件壳内壁面密闭连接,将中空纤维膜的管内与管外流道分开于二个环氧树脂密封处之间的组件壳侧壁上设有原料气进口和出口,于中空纤维膜两侧开口端设有富集气出口;在实际分离过程中,原料气通入膜管外,氧气选择性渗透到膜管内,在管内的出口端得到氧气富集气。
29.本发明的具体工艺采用图1所示的两级膜分离系统,原料气s1为变压吸附制备的普氧,由一级膜组件mem1的原料气进口直接进入一级膜组件mem1,由一级膜组件mem1的原料气出口流出的一级渗余气s3所含氧浓度较低直接放空,由一级膜组件mem1的富集气出口流出的一级渗透气s2经压缩机c1升压后由二级膜组件mem2的原料气进口进入二级膜组件mem2,由二级膜组件mem2的富集气出口流出的二级渗透气s6即为满足医用氧国家标准的高纯氧产品气,由二级膜组件mem2的原料气出口流出的二级渗余气s7因为氧含量仍较高故与原料气经混合器m1混合后循环由一级膜组件mem1的原料气进口进入一级膜组件;
30.实施例1
31.采用的中空纤维膜是基于6fda单体的刚性聚酰亚胺膜材料,把100g聚酰亚胺溶解于300gnmp(n-甲基吡咯烷酮)与50g四氢呋喃组成的混合溶剂中,充分搅拌后移入纺丝料罐,静置得到均匀透明的纺丝液,然后进行干湿纺丝。纺丝温度70℃,芯液为质量浓度50wt%nmp的水溶液,流量1.2ml/min,凝胶浴为水,水浴温度为室温。所纺的中空纤维膜在流动去离子水中清洗24小时后采用溶剂置换法进行干燥,制备出了非对称内压型中空纤维膜(如图2所示)。
32.实施例2
33.在室温下对实施例1中所描述的聚酰亚胺膜气体渗透性能进行测试,其氧气渗透速率为8.0gpu,氧氩分离系数为3.5,氧氮分离系数为6.8。
34.实施例3
35.采用氧气含量分别为96.5%(二级渗余气循环混合后使得这部分气体浓度高于原料气95.0%的氧浓度)及98.5%的标准混合气(平衡气为氩气),对实施例1所描述聚酰亚胺膜的氧氩分离性能进行评价。以96.5%氧含量气体作为第一级膜分离组件的模拟原料气,而98.5%氧含量气体作为第二级膜分离组件的模拟原料气,在室温18.0℃下进行。实验结果证明对氧氩分离体系而言,原料气的压力越高,在渗透侧所制备的富氧气中氧含量越高;加大高压侧放空量,制备的富氧气浓度表现出明显的升高趋势。一般第一级膜分离组件原料侧压力保持在8~10atm,第二级膜组件原料侧压力与第一级相当,两级膜组件的渗透侧都保持常压。就富集效果而言,以96.5%氧含量混合气作为原料气,经一级膜分离后,渗透侧的氧浓度可以达到98.5%的水平,而二级膜分离后所得的渗透气浓度则可以满足99.5%的医用高纯氧标准。