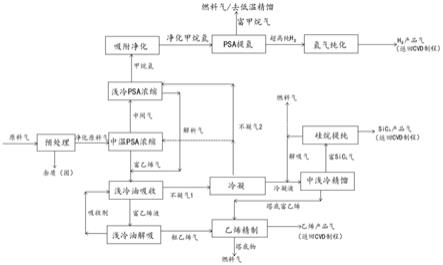
乙烯与硅烷反应的sic
‑
cvd无氯外延制程尾气ftrpsa回收与循环再利用方法
技术领域
1.乙烯与硅烷反应的sic
‑
cvd无氯外延制程尾气ftrpsa回收与循环再利用方法,本发明属于半导体材料与半导体制程环保技术领域,具体涉及sic
‑
cvd外延制程尾气处理技术领域。
背景技术:2.碳化硅(sic)作为第三代半导体材料,因其具有宽禁带、耐高温与高压、高频大功率,及耐辐射等优异特性,已广泛应用于it及电子消费品、汽车、光伏光电、核反应堆,以及系统工作条件苛刻的航空航天与军事等领域的功率开关、变频变压、ups等电力电子元器件,其中,外延是sic材料得以广泛应用的关键生产步骤。
3.sic外延制程有高温升华(pvt)、化学气相沉积(cvd)、液相生长外延(lpe)、分子束外延生长(mbe)、电子回旋共振等离子化学气相沉积(ecr
‑
mpcvd)等,而工业上普遍采用的是具有外延生长温度低、生产批量大、外延薄膜均匀性好,以及操作易控制特点的cvd制程,其中,按参与反应的硅(si)源和碳(c)源(称为“反应前驱物”)不同而又可分为无氯、含氯及同时含c/si源的有机硅化合物的sic
‑
cvd外延制程,进而,不同的外延制程所产生的尾气组成也不尽相同,处理方法随之也不同。
4.常规的sic
‑
cvd无氯外延制程中,有一种工艺目前较为普遍使用,是以硅烷(sih4)为si源、乙烯(c2h4)为c源,在氢气(h2)或氩气(ar)为载气的携带下进入cvd反应腔(炉),在一定温度及压力下进行化学气相沉积反应,所产生的外延薄膜在适合的衬底或基片(通常是si或sic材料)上形成一层薄膜,即外延层,经处理后得到合格的sic外延片,而在气相中含有,参与反应的生成物h2、ch4、含乙烷高烃等的碳二以上轻烷烃类(c
2+
)及少量的si粉或si团簇或c粉等固体微小颗粒,未反应完的sih4、c2h4,不参与反应的载气h2或ar,以及微量或痕量的其它杂质,如一氧化碳(co)、二氧化碳(co2)等。商业上常用h2作为载气,可以有效提升外延效率。由于尾气中含有有毒有害且易燃易爆的硅烷、氢气、甲烷、乙烯及轻烃类(c
2+
)组分,因而,对尾气处理的方法也比较特殊,尤其是安全性问题至关重要。
5.现有对常规的基于乙烯与硅烷反应的sic
‑
cvd无氯外延制程尾气进行处理的方法主要有三种,干法吸附、燃烧法与直接冷凝法。
6.第一,干法吸附可采用一次性吸附,吸附质为硅烷、硅团簇、乙烯及c
2+
等,非吸附质主要是h2、ch4及少量的硅烷、c
2+
组分,经过测试后达标直接排放,其中,吸附饱和后的吸附剂定期更换;或采用吸附剂可在线再生的变温吸附(tsa),在较低的温度下进行吸附,在较高的温度下进行吸附剂再生,循环操作,其中,被吸附饱和的吸附剂,在再生操作时,采用较高温度的水蒸气或惰性氮气为再生载气解吸吸附质而流出吸附塔,再经过冷却或冷凝等得到硅烷与c
2+
溶液输出。吸附法仅进行净化处理,适合尾气中sih4、乙烯及c
2+
含量较低的工况,大量的h2几乎完全浪费,并且还有温室气体排放,或吸附废气中轻烃类c
2+
组分超标而需要进一步催化燃烧才能达标,从而又增加了尾气处理的成本。
7.第二,燃烧法是直接进行空气氧化处理尾气,由于尾气中的h2、sih4、ch4、c2h4及c
2+
等都是极易燃烧的组分,经过燃烧后形成无害的h2o、sio2、co2等组分,再经过适当处理后直接排放。燃烧法因其经济性而在业界比较普遍采用,多为小型化现场处理装置,但需要通入几倍于尾气流量的空气,保证极易爆炸的氢气、硅烷等在空气中的浓度处于爆炸极限范围之外,因而消耗较高且存在着一定的安全隐患,同时,燃烧产生大量的热量以及微小颗粒在燃烧过程中极易爆炸,需要大量的水进行及时喷淋,造成二次污染排放或进行额外的处理。此外,大量有价值的h2、sih4、c2h4、ch4等资源不但未能有效利用,而且排放还带来温室效应。此外,业界也有将吸附法作为燃烧法的辅助方法,当燃烧法点火失败或发生安全隐患而停机时,sic
‑
cvd制程尾气便自动切换到吸附法装置中进行处理。
8.第三,直接冷凝法是对尾气直接冷却到
‑
60~
‑
30℃以下,使得硅烷、c2h4等组分先液化成液体,不凝气体中的主要成分是h2与ch4,携带有少量的sih4、c2h4等组分,再对不凝气体进行干法吸附或燃烧后排放或回收h2,冷凝液再进行处理。但是,由于基于乙烯与硅烷反应的sic
‑
cvd无氯外延尾气中的不凝气体组分,如h2、ch4含量较高,大量的冷量被浪费,能耗很高,进而处理的成本也非常高,工业上一般不采用。
技术实现要素:9.本发明的目的在于:提供乙烯与硅烷反应的sic
‑
cvd无氯外延制程尾气ftrpsa回收与循环再利用方法,以解决现有的基于乙烯与硅烷反应的sic
‑
cvd无氯外延制程尾气进行处理的方法耗能高,成本高,不安全,大量有效组分未能有效利用,排放还带来温室效应的问题。
10.本发明采用的技术方案如下:
11.乙烯与硅烷反应的sic
‑
cvd无氯外延制程尾气ftrpsa回收与循环再利用方法,包括如下步骤:
12.步骤1、原料气预处理,先后脱除尘埃、颗粒、油雾及部分高烃杂质;
13.步骤2、中温变压吸附浓缩,将来自预处理工序的原料气,直接或加压至小于1.0mpa,并经冷热交换后,进入至少由4塔组成的多塔变压吸附浓缩工序,至少一个吸附塔处于吸附步骤,其余吸附塔处于解吸再生步骤,所形成的非吸附相气体为中间混合气体;
14.步骤3、浅冷变压吸附浓缩,来自中温变压吸附浓缩工序的中间混合气体,经过精密过滤、压缩且冷热交换后进入由4个及以上的吸附塔组成的浅冷变压吸附浓缩工序,进行吸附浓缩,吸附塔顶流出富氢的甲烷氢气体,进入下一个工序——吸附净化,吸附塔底部流出的富硅烷解吸气,经冷热交换及增压后返回至后续工序——浅冷油吸收;
15.步骤4、吸附净化,甲烷氢气体进入由2个或3个吸附塔组成的吸附净化工序,形成净化甲烷氢气体,进入下一工序,即变压吸附提氢工序;
16.步骤5、变压吸附提氢,净化甲烷氢,直接或经冷热交换至常温后,进入至少由4塔组成的多塔变压吸附提纯氢气工序,所形成的非吸附相气体为超高纯氢气,其纯度为大于等于99.999~99.9999%,其中,co与co2含量小于0.1~1.0ppm、碳氢化合物,以甲烷计,含量小于10ppm、硅烷小于0.1~1.0ppm,进入下一工序——氢气纯化;
17.步骤6、氢气纯化,超高纯氢气,在操作温度为50~500℃、操作压力为常压或sic
‑
cvd制程中使用氢气所需的压力条件下进行纯化,脱除痕量杂质,得到最终的电子级氢气产
品,经过热交换降温或降压,或送入电子级氢气产品罐储存,或经过氢气产品缓冲罐,直接返回到sic
‑
cvd外延制程需要氢气的工段中;
18.步骤7、浅冷油吸收,来自中温变压吸附浓缩工序的富硅烷解吸气,经冷热交换,压缩后从吸收塔底进入浅冷油吸收工序,采用5~15℃、2.5~3.5mpa的c4液体溶剂为吸收剂,至上而下喷淋吸收,从吸收塔顶流出含有sih4及甲烷氢的不凝气体1,进入下一工序——中浅冷精馏,吸收塔底流出富乙烯液,进入解吸塔,从塔顶流出粗乙烯气,进入后续工序——乙烯精制,从解吸塔底流出c4吸收剂,返回至吸收塔循环使用;
19.步骤8、中浅冷精馏,来自浅冷油吸收工序的不凝气体1,经过冷凝产生的被冷凝流体,进入中浅冷精馏塔,从精馏塔顶流出的富硅烷气,进入下一个工序——硅烷提纯,从精馏塔底流出的富乙烯与来自浅冷油吸收工序的粗乙烯气混合进入后续的乙烯精制工序,从经冷凝产生的不凝气体2,返回至浅冷变压吸附浓缩工序,或经冷热交换后返回至中温变压吸附浓缩工序,进一步回收有效组分;
20.步骤9、硅烷提纯,来自中浅冷精馏塔的富硅烷塔顶气,进入由至少2个及以上的吸附塔组成的变压吸附提纯硅烷系统,从吸附塔顶流出纯度大于等于99.99%硅烷产品气,直接或经过sih4金属吸气剂纯化器进一步纯化后作为sic
‑
cvd外延制程所需的原料气循环使用,而吸附塔经过抽真空解吸并从吸附塔底流出的解吸气,或直接作为燃料气,或经加压与冷热交换后返回至中浅冷精馏工序中的精馏塔进一步回收c2h4与sih4;
21.步骤10、乙烯精制,来自浅冷油吸收工序的粗乙烯气,经过脱碳处理后冷凝,与来自中浅冷精馏工序的富乙烯混合,进入乙烯精馏塔进行精制,从塔顶流出乙烯产品气,从塔底流出的包括乙烷在内的c
2+
组分,作为燃料气使用,或外输。
22.具体的:
23.步骤1、原料气预处理,原料气,以乙烯(c2h4)为主要的碳(c)源,以硅烷(sih4)为硅(si)源进行化学气相沉积(cvd)制备基于碳化硅(sic)外延生长无氯制程中的尾气,其主要组成为氢气(h2)、甲烷(ch4)、硅烷(sih4)、乙烯(c2h4),以及微量的一氧化碳(co)、二氧化碳(co2)、含乙烷及轻烃(c
2+
),以及二氧化硅(sio2)和碳(c)微细颗粒,压力为常压或低压,温度为常温;预处理,原料气经增压至0.2~0.3mpa送入由除尘器、除颗粒过滤器、除油雾捕集器组成的预处理单元,先后脱除尘埃、颗粒、油雾及部分高烃杂质,进入下一个工序——中温变压吸附浓缩;
24.步骤2、中温变压吸附浓缩,将来自预处理工序的原料气,直接或加压至小于1.0mpa,并经冷热交换至60~120℃后,进入至少由4塔组成的多塔变压吸附浓缩工序,吸附塔的操作压力为0.2~1.0mpa,操作温度为60~120℃,至少一个吸附塔处于吸附步骤,其余吸附塔处于解吸再生步骤,所形成的非吸附相气体为中间混合气体,主要组分为h2、ch4与sih4,进入下一工序——浅冷变压吸附浓缩,所形成的吸附相气体为富乙烯气体,经加压后进入后续工序——浅冷油吸收,其中,中温变压吸附浓缩工序的吸附剂采用活性氧化铝、硅胶、活性炭、分子筛,以及负载金属活性组分的活性炭或分子筛的一种或组合,解吸时采用抽真空再生;
25.步骤3、浅冷变压吸附浓缩,来自中温变压吸附浓缩工序的中间混合气体,经过精密过滤、压缩至1.0~3.0mpa且冷热交换至
‑
10~10℃后进入由4个及以上的吸附塔组成的浅冷变压吸附浓缩工序,在操作温度为
‑
10~10℃,操作压力为1.0~3.0mpa下进行吸附浓
缩,吸附塔顶流出富氢的甲烷氢气体,进入下一个工序——吸附净化,进一步净化脱除其中微量的硅烷(sih4)及乙烯(c2h4),吸附塔底部流出的富硅烷解吸气,经冷热交换及增压后返回至后续工序——浅冷油吸收,进一步回收sih4;
26.步骤4、吸附净化,来自浅冷变压吸附浓缩工序的甲烷氢气体,进入由2个或3个吸附塔组成的吸附净化工序,在操作温度为
‑
10~20℃,操作压力为1.0~3.0mpa下进行吸附,进一步净化脱除其中少量的sih4及c2h4,形成净化甲烷氢气体,进入下一工序,即变压吸附提氢工序;
27.步骤5、变压吸附提氢,来自吸附净化工序的净化甲烷氢,直接或经冷热交换至常温后,进入至少由4塔组成的多塔变压吸附提纯氢气工序,吸附塔的操作压力为1.0~3.0mpa,操作温度为
‑
10~40℃,至少一个吸附塔处于吸附步骤,其余吸附塔处于解吸再生步骤,所形成的非吸附相气体为超高纯氢气,其纯度为大于等于99.999~99.9999%(v/v),其中,co与co2含量小于0.1~1.0ppm、碳氢化合物(以甲烷计)含量小于10ppm、硅烷小于0.1~1.0ppm,进入下一工序——氢气纯化,变压吸附提氢工序的吸附剂采用活性氧化铝、硅胶、活性炭、硅酸铝分子筛、碳分子筛的一种或多种组合,解吸时采用冲洗,或冲洗加抽真空方式,解吸气为富甲烷气体,可直接作为燃料气输出,或进入低温精馏回收甲烷,制得纯度大于等于99.99%的甲烷返回到sic
‑
cvd外延制程循环使用;
28.步骤6、氢气纯化,来自变压吸附提氢工序的超高纯氢气,或经过中间产品储罐后,或直接经过热交换,在50~500℃的温度下,直接或通过减压阀减压至sic
‑
cvd外延制程用氢所需的压力,进入由金属吸气剂,或钯膜,或钯膜
‑
金属吸气剂耦合的氢气纯化工序,在操作温度为50~500℃、操作压力为常压或sic
‑
cvd制程中使用氢气所需的压力条件下进行纯化,脱除痕量杂质,得到最终的电子级氢气产品,纯度达到国家及国际半导体协会(semi)所规定的电子级氢气的产品标准,氢气纯度大于等于7~8n级,经过热交换降温或降压,或送入电子级氢气产品罐储存,或经过氢气产品缓冲罐,直接返回到sic
‑
cvd外延制程需要氢气的工段中,其中,氢气纯化工序的操作温度,是由所采用的金属吸气剂或钯膜的工艺决定,金属吸气剂或钯膜的使用寿命至少大于2年,无需再生;由此得到的电子级氢气产品的收率大于75~85%;
29.步骤7、浅冷油吸收,来自中温变压吸附浓缩工序的富硅烷解吸气,经冷热交换至5~15℃、压缩至2.5~3.5mpa后从吸收塔底进入浅冷油吸收工序,采用5~15℃、2.5~3.5mpa的c4(正丁烷、异丁烷或混合丁烷)液体溶剂为吸收剂,至上而下喷淋吸收,从吸收塔顶流出含有sih4及甲烷氢的不凝气体1,进入下一工序——中浅冷精馏,进一步提取硅烷,吸收塔底流出富乙烯液,进入解吸塔,从塔顶流出粗乙烯气,进入后续工序——乙烯精制,从解吸塔底流出c4吸收剂,返回至吸收塔循环使用;
30.步骤8、中浅冷精馏,来自浅冷油吸收工序的不凝气体1,经过冷凝产生的被冷凝流体,进入操作温度为
‑
35~
‑
10℃、操作压力为2.0~2.5mpa的中浅冷精馏塔,从精馏塔顶流出的富硅烷气,进入下一个工序——硅烷提纯,从精馏塔底流出的富乙烯与来自浅冷油吸收工序的粗乙烯气混合进入后续的乙烯精制工序,从经冷凝产生的不凝气体2,返回至浅冷变压吸附浓缩工序,或经冷热交换后返回至中温变压吸附浓缩工序,进一步回收有效组分;
31.步骤9、硅烷提纯,来自中浅冷精馏塔的富硅烷塔顶气,经冷热交换至20~40℃并减压至小于1.0mpa后送入操作温度为20~40℃、操作压力为小于1.0mpa且由至少2个及以
上的吸附塔组成的变压吸附提纯硅烷系统,吸附塔中装填有硅藻土、硅胶、活性炭、分子筛的一种或多种组合的吸附剂,从吸附塔顶流出纯度大于等于99.99%硅烷(sih4)产品气,收率大于等于90~95%,直接或经过sih4金属吸气剂纯化器进一步纯化后(纯度大于等于99.999%)作为sic
‑
cvd外延制程所需的原料气循环使用,而吸附塔经过抽真空解吸并从吸附塔底流出的解吸气,或直接作为燃料气,或经加压与冷热交换后返回至中浅冷精馏工序中的精馏塔进一步回收c2h4与sih4,相应的收率分别达到95~98%以上;
32.步骤10、乙烯精制,来自浅冷油吸收工序的粗乙烯气,经过脱碳处理后冷凝,与来自中浅冷精馏工序的富乙烯混合,进入乙烯精馏塔进行精制,从塔顶流出乙烯产品气,纯度大于等于99.99%,收率大于等于90~95%,或返回cvd制程,从塔底流出的包括乙烷在内的c
2+
组分,作为燃料气使用,或外输。
33.本申请的技术方案中,依据基于乙烯与硅烷反应的sic
‑
cvd无氯外延制程中产生的cvd尾气所含多种主要组分h2、sih4、c2h4/ch4的物理化学特性、相对分离系数、相对应的分离净化方法以及对应的操作条件(温度与压力),将各种常规的分离方法,包括吸附、精馏、吸收等相耦合,实现sic
‑
cvd无氯制程尾气全温程变压吸附(ftrpsa)回收h2、sih4、c2h4及ch4,并返回到sic
‑
cvd外延常规制程中循环使用,既实现尾气的全组分回收再利用,又减少了尾气排放,弥补了sic外延制程尾气处理技术的空白;采用中温与浅冷psa浓缩工序组合,既能有效解决sih4极性随温度变化所导致的吸附能力的变化,又可防止深度吸附导致解吸困难的问题;同时,在解吸过程中采用置换方式严格控制吸附塔内的h2/sih4/ch4的浓度,避免这些易燃易爆的组分发生爆炸的危险产生;利用各工序的操作温度的差异性,通过安排合理的冷热量交换系统,使得整个操作系统的冷热量得到充分的利用;在变压吸附提氢工序中充分利用变压方式,对含氢的进料气进行深度净化脱除各种微量乃至痕量的杂质组分,既保证了氢气纯化工序的原料气进料要求,又可延长了变压吸附提纯工序的吸附剂使用寿命;通过浅冷油吸收、中浅冷精馏的不凝气体与中温及浅冷变压吸附浓缩、吸附净化及变压吸附提氢工序的耦合,使得所回收的有效组分的收率都要超过70~80%,其中,硅烷、乙烯回收率超过90%。
34.优选的,所述的原料气,包括以其它烯烃为碳源的其余半导体制程中产生的含氢气、硅烷、甲烷及轻烯烃主要组分的废气或尾气。
35.优选的,所述的预处理,在原料气为含有较高浓度的包括酸性及挥发性有机物(vocs)在内的其它杂质的废气或尾气工况,除了除尘器、除颗粒过滤器、除油雾捕集器外,可增置碱洗、中和塔、干燥器及其它,脱除对变压吸附浓缩工序操作有较大影响的酸性、挥发性有机物(vocs)杂质组分。
36.优选的,所述的中温变压吸附浓缩,吸附塔解吸步骤中,在吸附塔吸附步骤结束后与均压降或顺放步骤开始前,采用来自浅冷油吸收工序中解吸塔顶的粗乙烯气,或来自中浅冷精馏工序中精馏塔底的富乙烯气,或来自乙烯精制的乙烯产品气进行置换,提升乙烯在本工序中的浓度与收率。
37.优选的,将来自预处理的原料气经升温增压后从作为中温变压吸附浓缩的第一psa吸附塔(1段psa)塔底进入,从1段psa塔顶流出的非吸附相的中间混合气经冷热交换后从作为浅冷变压吸附的第二psa吸附塔(2段psa)底进入,从2段吸附塔顶流出的非吸附相的富氢甲烷氢气体,进入下一个工序——吸附净化;从1段psa及2段psa的解吸气,经过冷热交
换与加压后进入浅冷油吸收工序,其中,一部分的1段或2段的非吸附相的中间混合气体或富氢甲烷氢气体,分别可以作为各自工序的进料气进行互补,调节各段吸附塔内乙烯或硅烷的浓度,以便提升乙烯或硅烷的收率。
38.优选的,所述的作为浅冷变压吸附浓缩的第二psa吸附塔(2段psa)在吸附步骤结束后与均压降或顺放步骤开始前,增加一个置换步骤,采用来自中浅冷精馏工序中的精馏塔富集sih4的塔顶气或来自硅烷提纯工序的sih4产品气进行置换,进一步提升sih4在本工序中的浓度与收率。
39.优选的,所述的吸附净化工序的来自浅冷变压吸附浓缩工序的甲烷氢气体进料气中,硅烷含量超过1%时,采用以乙醇或乙醚或低碳混合醇醚为吸收剂进行吸收净化,替代吸附净化,其中,来自浅冷变压吸附浓缩工序的甲烷氢气体,经精细过滤后加压至2.0~3.0mpa并经冷热交换至
‑
10~10℃进入吸收塔,从吸收塔顶流出硅烷含量小于10ppm的净化后的甲烷氢气体,直接进入变压吸附提氢工序,从吸收塔底流出的吸收液进入解吸塔进行解吸,解吸的操作条件为常温及常压,经过解吸出来的富硅烷气体,经过冷热交换及加压后,与从浅冷油吸收工序的吸收塔顶流出的不凝气体进行混合,再进入操作温度为
‑
35~
‑
10℃、操作压力为1.0~2.5mpa的中浅冷精馏工序,进一步回收sih4。
40.优选的,所述的中浅冷精馏工序由两个精馏塔组成,来自浅冷油吸收工序的不凝气体1,经冷凝产生的被冷凝流体,进入操作温度为
‑
35~
‑
10℃、操作压力为2.0~2.5mpa的中浅冷精馏塔
‑
1,从塔顶流出轻组分的不凝气体3,主要为h2、ch4组分及微量的sih4,或经冷热交换器至温度为20~40℃与来自吸附净化工序的净化甲烷氢混合再进入变压吸附提氢工序进一步回收h2或/及ch4,或经冷热交换器至温度为5~20℃及减压至小于1mpa后与经预处理净化后的原料气混合再进入浅冷变压吸附浓缩工序进一步回收h2或/及ch4,h2或/ch4产品气的收率进一步提升,从精馏塔
‑
1塔底流出的重组份流体,再进入操作温度为
‑
35~
‑
10℃、操作压力为1.0~2.5mpa的中浅冷精馏塔
‑
2,从其塔底流出富乙烯的重组分,进入乙烯精制工序,从其塔顶流出含富集的硅烷(sih4)的塔顶气,或进入硅烷提纯工序,或直接作为硅烷产品气(纯度超过99.9%),或直接进入硅烷金属吸气剂进行纯化制得纯度大于等于99.999%的sih4产品气,返回sic
‑
cvd外延制程循环使用,从经冷凝产生的不凝气体2返回至中温变压吸附浓缩工序。
41.优选的,所述的硅烷提纯工序中所获得的纯度大于等于99.99%的硅烷产品气,或经过sih4金属吸气剂纯化器进一步纯化后(纯度大于等于99.999%)作为sic
‑
cvd外延制程所需的原料气循环使用,其中的金属吸气剂,是采用氢化的金属镐(zr)
‑
钒(v)
‑
铁(fe)合金制成,在25~100℃下进行纯化,得到的硅烷产品气纯度大于等于99.999%,其中,包括氧气(o2)、水(h2o)、一氧化碳(co)、二氧化碳(co2)、总的碳氢化合物、硫化物(h2s计)以及硅氧烷的主要杂质含量均小于0.01~0.1ppm,且金属吸气剂使用寿命大于1~2年。
42.优选的,所述的硅烷提纯工序中来自中浅冷精馏工序的精馏塔塔顶气,其中,除了含有少量的c2h4、co/co2、o2、h2o外,还含有微量的磷烷(ph3)、砷烷(ash3)、乙硼烷(b2h6)及硅氧烷的工况下,硅烷提纯工序的吸附塔除了装填有硅藻土、硅胶、活性炭、分子筛的一种或多种组合的吸附剂外,还需装填负载金属铜(cu)/锌(zn)或氧化铜(cuo)/氧化锌(zno)活性组分的分子筛或活性三氧化二铝(al2o3)的吸附剂,除杂深度可达到小于50~100ppb水平。
43.优选的,所述的中温变压吸附浓缩、浅冷变压吸附浓缩、变压吸附提氢与吸附净化
工序,在吸附压力大于等于0.6mpa的操作条件下,吸附与解吸循环操作过程中的压力变化,通过各吸附塔之间连接的管道上程序控制阀与调节阀,实现缓均控制,防止系统压力变化过大所导致的气流冲刷吸附塔床层及吸附剂粉化产生,使得本工序系统操作稳定与安全。
44.全温程变压吸附(英文全称:full temperature range
‑
pressure swing adsorption,简称:ftrpsa)是一种以变压吸附(psa)为基础并可与各种分离技术相耦合的方法,利用不同物料组分本身在不同压力与温度下的吸附分离系数及物理化学性质的差异性,采取中温与浅冷变压吸附过程中吸附与解吸易于匹配和平衡的循环操作来分离和提纯所需的主要有效组分(h2(纯度大于等于99.9995%(v/v))与sih4(大于等于99.99%),同时可副产乙烯(大于等于99.9%)或甲烷(大于等于99%)。
45.综上所述,由于采用了上述技术方案,本发明的有益效果是:
46.1、本发明中,可以从基于乙烯与硅烷反应的sic
‑
cvd无氯外延制程尾气全组分回收h2、sih4、c2h4及ch4,并返回到sic
‑
cvd外延常规制程中循环使用,既实现尾气的全组分回收再利用,又减少了尾气排放,弥补了sic外延制程尾气处理技术的空白;
47.2、利用尾气组分在中温与浅冷的温度(
‑
10~120℃)和中低压(0.2~3.0mpa)范围内的物理化学与相对分离系数特性,选择性的同时分离回收非吸附相的h2/ch4或/sih4及吸附相的c2h4或/sih4,避免了吸附循环操作中的sih4组分在中温范围内作为非吸附质组分而在浅冷范围内为吸附质的特性转变所带来的困难,以及sih4、c2h4为吸附质组分的深度吸附而再生困难传统变温或变压吸附难于直接处理sih4易燃易爆的技术难题,使得本发明基于各种吸附与精馏/吸收分离技术耦合为基础的中浅冷温度范围(
‑
35~20℃)的全温程变压吸附(ftrpsa)系统的吸附与再生循环操作得以实现,并最终得到电子级氢气、硅烷或乙烯产品,解决了传统吸附分离工艺难以同时回收h2、sih4、c2h4再利用的技术瓶颈;
48.3、在实现全组分(h2、sih4/c2h4为主)回收再利用的同时,未给系统带入sic
‑
cvd无氯外延制程及其敏感的含氧化合物,尤其是o2、h2o、co等,使得回收再利用整个过程平稳,对sic外延质量的影响减小到零的程度;
49.4、对于常压或低压废气进行提纯回收再利用,可根据碳化硅外延制程(电子级)氢气、硅烷、c2h4使用条件,采用加压或不加压的两种处理方式,得到可返回到外延制程中使用的电子级的氢气、硅烷及乙烯产品;
50.5、采用中温与浅冷psa浓缩工序组合,既能有效解决sih4极性随温度变化所导致的吸附能力的变化,又可防止深度吸附导致解吸困难的问题;同时,在解吸过程中采用置换方式严格控制吸附塔内的h2/sih4/ch4的浓度,避免这些易燃易爆的组分发生爆炸的危险产生;
51.6、利用各工序的操作温度的差异性,通过安排合理的冷热量交换系统,使得整个操作系统的冷热量得到充分的利用;
52.7、在变压吸附提氢工序中充分利用变压方式,对含氢的进料气进行深度净化脱除各种微量乃至痕量的杂质组分,避免因吸附杂质组分因分压过低而无法深度脱除,同时,避免因采用传统的变温吸附(tsa)脱除微量或痕量杂质组分而导致对氢气纯化工序可能引入热氮再生或热载体所形成的新杂质组分的问题,以及吸附与再生难以匹配所形成的循环操作问题,既保证了氢气纯化工序的原料气进料要求,又可延长了变压吸附提纯工序的吸附剂使用寿命;
53.8、通过浅冷油吸收、中浅冷精馏的不凝气体与中温及浅冷变压吸附浓缩、吸附净化及变压吸附提氢工序的耦合,使得所回收的有效组分的收率都要超过70~80%,其中,硅烷、乙烯回收率超过90%。
附图说明
54.图1为本发明实施例1流程示意图;
55.图2为本发明实施例2流程示意图;
56.图3为本发明实施例3流程示意图;
57.图4为本发明实施例4流程示意图;
58.图5为本发明实施例5流程示意图。
具体实施方式
59.为了使本发明的目的、技术方案及优点更加清楚明白,以下结合附图及实施例,对本发明进行进一步详细说明。应当理解,此处所描述的具体实施例仅用以解释本发明,并不用于限定本发明。
60.实施例1
61.如图1所示,乙烯与硅烷反应的sic
‑
cvd无氯外延制程尾气ftrpsa回收与循环再利用方法,包括如下步骤:
62.步骤1、原料气预处理,原料气,以乙烯(c2h4)为主要的碳(c)源,以硅烷(sih4)为硅(si)源进行化学气相沉积(cvd)制备基于碳化硅(sic)外延生长无氯制程中的尾气,其主要组成为氢气(h2)、甲烷(ch4)、硅烷(sih4)、乙烯(c2h4),以及微量的一氧化碳(co)、二氧化碳(co2)、含乙烷及轻烃(c
2+
),以及二氧化硅(sio2)和碳(c)微细颗粒,压力为常压或低压,温度为常温;预处理,原料气经增压至0.2~0.3mpa送入由除尘器、除颗粒过滤器、除油雾捕集器组成的预处理单元,先后脱除尘埃、颗粒、油雾及部分高烃杂质,进入下一个工序——中温变压吸附浓缩;
63.步骤2、中温变压吸附浓缩,来自预处理工序的原料气加压至0.6~0.8mpa,并经冷热交换至60~120℃后,进入由5塔组成的多塔变压吸附浓缩工序,吸附塔的操作压力为0.6~0.8mpa,操作温度为60~120℃,其中一个吸附塔处于吸附步骤,其余吸附塔处于解吸再生步骤,所形成的非吸附相气体为中间混合气体,主要组分为h2、ch4与sih4,进入浅冷变压吸附浓缩工序,所形成的吸附相气体为富乙烯气体,经加压后进入浅冷油吸收工序,其中,中温变压吸附浓缩工序的吸附剂采用活性氧化铝、硅胶、活性炭、分子筛,以及负载金属活性组分的活性炭或分子筛的多种组合,解吸时采用抽真空再生;
64.步骤3、浅冷变压吸附浓缩,来自变压吸附浓缩工序的中间混合气体,经过精密过滤、压缩至2.0~3.0mpa且冷热交换至5~10℃后进入由5个吸附塔组成的浅冷变压吸附浓缩工序,在操作温度为5~10℃,操作压力为2.0~3.0mpa下进行吸附浓缩,吸附塔顶流出富氢的甲烷氢气体,进入吸附净化工序,进一步净化脱除其中微量的硅烷(sih4)及乙烯(c2h4),吸附塔底部流出的富硅烷解吸气,经冷热交换及增压后返回至浅冷油吸收工序,进一步回收sih4;
65.步骤4、吸附净化,来自浅冷变压吸附浓缩工序的甲烷氢气体,进入由2个吸附塔组
成的吸附净化工序,在操作温度为5~10℃,操作压力为2.0~3.0mpa下进行吸附,进一步净化脱除其中少量的sih4及c2h4,形成净化甲烷氢气体,进入变压吸附提氢工序;
66.步骤5、变压吸附提氢,来自吸附净化工序的净化甲烷氢,经冷热交换至常温后,进入由5塔组成的多塔变压吸附提纯氢气工序,吸附塔的操作压力为2.0~3.0mpa,操作温度为20~40℃,其中一个吸附塔处于吸附步骤,其余吸附塔处于解吸再生步骤,所形成的非吸附相气体为超高纯氢气,其纯度为大于等于99.999~99.9999%(v/v),其中,co与co2含量小于0.1~1.0ppm、碳氢化合物(以甲烷计)含量小于10ppm、硅烷小于0.1~1.0ppm,进入氢气纯化工序,变压吸附提氢工序的吸附剂采用活性氧化铝、硅胶、活性炭、硅酸铝分子筛、碳分子筛的多种组合,解吸时采用冲洗加抽真空方式,解吸气为富甲烷气体,可直接作为燃料气输出;
67.步骤6、氢气纯化,来自变压吸附提氢工序的超高纯氢气,经过热交换至400~450℃后进入由金属吸气剂组成的氢气纯化工序,在操作温度为400~450℃、操作压力为2.0~3.0mpa条件下进行纯化,脱除痕量杂质,得到最终的电子级氢气产品,纯度达到国家及国际半导体协会(semi)所规定的电子级氢气的产品标准,氢气纯度大于等于7~8n级,经过热交换降温及氢气产品缓冲罐,直接返回到sic
‑
cvd外延制程需要氢气的工段中,其中,金属吸气剂的使用寿命至少大于2年,无需再生,由此得到的电子级氢气产品的收率大于75~85%;
68.步骤7、浅冷油吸收,来自中温变压吸附浓缩工序的富硅烷解吸气,经冷热交换至5~15℃、压缩至2.5~3.5mpa后从吸收塔底进入浅冷油吸收工序,采用5~15℃、2.5~3.5mpa的c4(正丁烷、异丁烷或混合丁烷)液体溶剂为吸收剂,至上而下喷淋吸收,从吸收塔顶流出含有sih4及甲烷氢的不凝气体1,进入中浅冷精馏工序,进一步提取硅烷,吸收塔底流出富乙烯液,进入解吸塔,从塔顶流出粗乙烯气,进入后乙烯精制工序,从解吸塔底流出c4吸收剂,返回至吸收塔循环使用;
69.步骤8、中浅冷精馏,来自浅冷油吸收工序的不凝气体1,经过冷凝产生的被冷凝流体,进入操作温度为
‑
35~
‑
20℃、操作压力为2.0~2.5mpa的中浅冷精馏塔,从精馏塔顶流出的富硅烷气,进入硅烷提纯工序,从精馏塔底流出的富乙烯与来自浅冷油吸收工序的粗乙烯气混合进入乙烯精制工序,从经冷凝产生的不凝气体2,返回至浅冷变压吸附浓缩工序,进一步回收有效组分;
70.步骤9、硅烷提纯,来自中浅冷精馏塔的富硅烷塔顶气,经冷热交换至20~40℃并减压至小于1.0mpa后送入操作温度为20~40℃、操作压力为小于1.0mpa且由3个及以上的吸附塔组成的变压吸附提纯硅烷系统,吸附塔中装填有硅藻土、硅胶、活性炭、分子筛的多种组合的吸附剂,从吸附塔顶流出纯度大于等于99.99%硅烷(sih4)产品气,收率大于等于90~95%,再经过sih4金属吸气剂纯化器进一步纯化后(纯度大于等于99.999%)作为sic
‑
cvd外延制程所需的原料气循环使用,而吸附塔经过抽真空解吸并从吸附塔底流出的解吸气,经加压与冷热交换后返回至中浅冷精馏工序中的精馏塔进一步回收c2h4与sih4,相应的收率分别达到95~98%以上;
71.步骤10、乙烯精制,来自浅冷油吸收工序的粗乙烯气,经过脱碳处理后冷凝,与来自中浅冷精馏工序的富乙烯混合,进入乙烯精馏塔进行精制,从塔顶流出乙烯产品气,纯度大于等于99.99%,收率大于等于90~95%,从塔底流出的包括乙烷在内的c
2+
组分,作为燃
料气使用。
72.实施例2
73.如图2所示,在实施例1基础上,中温变压吸附浓缩工序的吸附塔解吸步骤中,在吸附塔吸附步骤结束后与均压降或顺放步骤开始前,采用来自中浅冷精馏工序中精馏塔底的富乙烯气,提升乙烯在本工序中的浓度与收率。
74.实施例3
75.如图3所示,在实施例1基础上,中温变压吸附浓缩与浅冷变压吸附浓缩工序合并成一个由二段psa组成的工序,将来自预处理的原料气经升温增压后从作为中温变压吸附浓缩的第一psa吸附塔(1段psa)塔底进入,从1段psa塔顶流出的非吸附相的中间混合气经冷热交换后从作为浅冷变压吸附的第二psa吸附塔(2段psa)底进入,从2段吸附塔顶流出的非吸附相的富氢甲烷氢气体,进入吸附净化;从1段psa及2段psa的解吸气,经过冷热交换与加压后进入浅冷油吸收工序,其中,一部分的1段或2段的非吸附相的中间混合气体或富氢甲烷氢气体,分别可以作为各自工序的进料气进行互补,调节各段吸附塔内乙烯或硅烷的浓度,以便提升乙烯或硅烷的收率。
76.实施例4
77.如图4所示,在实施例1基础上,吸附净化工序的来自浅冷变压吸附浓缩工序的甲烷氢气体进料气中,硅烷含量超过1%时,采用以乙醇为吸收剂进行吸收净化,替代吸附净化,其中,来自浅冷变压吸附浓缩工序的甲烷氢气体,经精细过滤后加压至2.0~3.0mpa并经冷热交换至5~10℃进入吸收塔,从吸收塔顶流出硅烷含量小于10ppm的净化后的甲烷氢气体,直接进入变压吸附提氢工序,从吸收塔底流出的吸收液进入解吸塔进行解吸,解吸的操作条件为常温及常压,(经解析出来的乙醇吸收剂返回吸收塔再次利用)经过解吸出来的富硅烷气体,经过冷热交换及加压后,与从浅冷油吸收工序的吸收塔顶流出的不凝气体进行混合,再进入中浅冷精馏工序,进一步回收sih4。
78.实施例5
79.如图5所示,在实施例1基础上,中浅冷精馏工序由两个精馏塔组成,来自浅冷油吸收工序的不凝气体1,经冷凝产生的被冷凝流体,进入操作温度为
‑
35~
‑
25℃、操作压力为2.0~2.5mpa的中浅冷精馏塔
‑
1,从塔顶流出轻组分的不凝气体3,主要为h2、ch4组分及微量的sih4,经冷热交换器至温度为5~20℃及减压至小于1mpa后与经预处理净化后的原料气混合再进入浅冷变压吸附浓缩工序进一步回收h2或/及ch4,h2或/ch4产品气的收率进一步提升,从精馏塔
‑
1塔底流出的重组份流体,再进入操作温度为
‑
20~
‑
15℃、操作压力为1.5~2.5mpa的中浅冷精馏塔
‑
2,从其塔底流出富乙烯的重组分,进入乙烯精制工序,从其塔顶流出含富集的硅烷(sih4)的塔顶气进入硅烷提纯工序的硅烷金属吸气剂进行纯化制得纯度大于等于99.999%的sih4产品气,返回sic
‑
cvd外延制程循环使用,从经冷凝产生的不凝气体2返回至中温变压吸附浓缩工序。
80.实施例6
81.在实施例1基础上,硅烷提纯工序中来自中浅冷精馏工序的精馏塔塔顶气,其中,除了含有少量的c2h4、co/co2、o2、h2o外,还含有微量的磷烷(ph3)、砷烷(ash3)、乙硼烷(b2h6)及硅氧烷的工况下,硅烷提纯工序的吸附塔除了装填有硅藻土、硅胶、活性炭、分子筛的多种组合的吸附剂外,还需装填负载金属铜(cu)/锌(zn)或氧化铜(cuo)/氧化锌(zno)
活性组分的分子筛或活性三氧化二铝(al2o3)的吸附剂,除杂深度可达到小于50~100ppb水平。
82.以上所述仅为本发明的较佳实施例而已,并不用以限制本发明,凡在本发明的精神和原则之内所作的任何修改、等同替换和改进等,均应包含在本发明的保护范围之内。