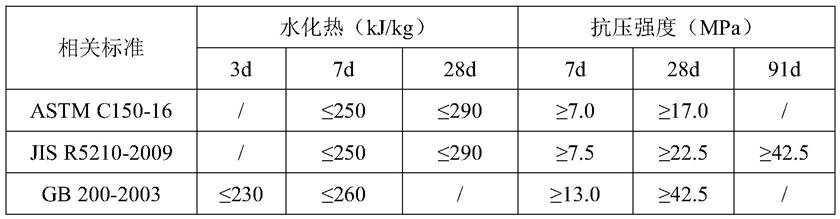
1.本发明属于固井技术领域,具体涉及一种固井用高强度低水化热低密度水泥浆体系及其制备方法和应用。
背景技术:2.随着石油勘探开发的进程,遇到低压地层、薄弱地层等易发生漏失地层的越来越多,而低密度水泥浆体系正是伴随着这些复杂情况的处理而逐渐发展和完善起来的,随着深井、超深井技术的不断发展和推广,使得在于深井、超深井的易漏地层往往会带来较为严重的井漏,从而严重影响了固井质量以及后续增产作业的实施。要改善该类复杂井况的固井质量就必须要完善低密度水泥浆体系。
3.如公开号cn106396509b的中国专利公开了一种适用范围广的低密度高强度水泥浆体系,由以下重量份的原料制备而成:低密度高强度水泥65
‑
75重量份,amps类聚合物降失水剂0.2
‑
2重量份,聚羧酸醚酯分散剂0.05
‑
0.2重量份,无机铝酸盐早强剂0.1
‑
2重量份,有机磷酸盐缓凝剂0.1
‑
0.55重量份,有机硅消泡剂0.1
‑
0.2重量份,蒸馏水25
‑
35重量份。但由于该水泥浆体系使用无机铝盐早强剂,激活低密度高强度水泥,激活剂为弱碱强酸盐,温度上升后转化为弱碱性,起到激活作用。该水泥浆体系的性能表现为:40
‑
55℃条件下,稠化时间偏长(260
‑
330min),给浅井固井的防窜带来风险,如要缩短时间需添加碱性添加剂,同时要追加一定量的激活剂,调整较杂;在65
‑
90℃条件下,稠化时间一般为160
‑
220min,用于高温深井需延长时间,追加酸性缓凝剂,会造成体系酸性增加,体系离析分层的风险。
技术实现要素:4.本发明的第一目的在于提供一种低水化热硅酸盐水泥,该低水化热硅酸盐水泥具有放热速率低、高后期强度和抗侵蚀性能好等特性,保证后期凝固强度满足行标要求。
5.本发明的第二目的在于提供一种包括上述低水化热硅酸盐水泥的固井用高强度低水化热低密度水泥浆体系,解决现有低密度水泥浆体系的缺陷,消除体系中使用缓凝剂与促凝激活剂之间的性能冲突,实现体系稠化时间的方便可调,提高油、气井固井质量及生产效益。
6.本发明的第三目的在于提供一种上述固井用高强度低水化热低密度水泥浆体系的制备方法。
7.本发明的第四目的在于提供一种上述固井用高强度低水化热低密度水泥浆体系在油、气井固井作业中的应用。
8.为了实现本发明的上述目的,本发明采用以下技术方案:
9.本发明提供了一种固井用高强度低水化热低密度水泥浆体系,按重量份数计,包括以下组份:低水化热硅酸盐水泥25
‑
35份、玻化微珠20~25份、矿渣粉25~30份、微硅粉8~10份、熟石膏3~5份、硫酸钠1~2份、生石灰1~2份、熟石灰2~3份、偏硅酸钠2~3份、碳酸钠0.5~1.5份、水65~75份。
10.作为进一步优选的技术方案,该固井用高强度低水化热低密度水泥浆体系还包括2.0~2.5重量份的降失水剂。
11.作为进一步优选的技术方案,该固井用高强度低水化热低密度水泥浆体系还包括0.1~0.25重量份的减阻剂。
12.作为进一步优选的技术方案,该固井用高强度低水化热低密度水泥浆体系还包括0~0.4重量份的缓凝剂。
13.作为进一步优选的技术方案,所述低水化热硅酸盐水泥包括如下质量百分比的矿物组份:硅酸三钙28%~33%;硅酸二钙42%~48%;铝酸三钙0~3%;铁铝酸四钙15%~17%;氧化钙3~4%;余量为混杂矿物成分。
14.具体地,所述混杂矿物成分的质量百分比含量<5%。
15.具体地,所述混杂矿物成分为mgo或so3中的一种或其混合物。
16.进一步地,所述低热硅酸盐水泥的粒径为2.0~150μm,放热速率3d水化热小于195kj/kg。
17.作为进一步优选的技术方案,所述降失水剂为聚乙烯醇1788。
18.作为进一步优选的技术方案,所述缓凝剂为羟基乙叉二膦酸四钠。
19.作为进一步优选的技术方案,所述减阻剂为聚羧酸类减阻剂。
20.本发明还提供了一种固井用高强度低水化热低密度水泥浆体系的制备方法,包括以下步骤:
21.s1.按照下述重量份数称取原料:低水化热硅酸盐水泥25
‑
35份、玻化微珠20~25份、矿渣粉25~30份、微硅粉8~10份、熟石膏3~5份、硫酸钠1~2份、生石灰1~2份、熟石灰2~3份、偏硅酸钠2~3份、碳酸钠0.5~1.5份、降失水剂2~3份、减阻剂0.1~0.25份;缓凝剂0~0.5份;
22.s2.在常温条件下,将s1所称取的原料混拌均匀,得混合干灰;
23.s3.将65~75份的水到入恒速搅拌器的搅拌浆杯中,开启恒速搅拌器,在4000转/分的转速下将s2所得混合干灰在0~15秒时间内均匀倒入转动浆杯中,继续搅拌35秒,即得高强度低水化热低密度水泥浆体系。
24.本发明还进一步提供了一种固井用高强度低水化热低密度水泥浆体系的应用,所述高强度低水化热低密度水泥浆体系的密度为1.20~1.30g/cm3,48小时强度达到10mpa以上;适用50~90℃范围内的油、气井固井作业。
25.采用上述技术方案,本发明的优点如下:
26.1.本发明所述的“高强度低水化热低密度水泥浆体系”,能在50
‑
90℃的温度范围内使用,该体系对比目前g级硅酸盐水泥配制的低密高强体系,具有更好的前期低水化热缓凝及后期更高强度的特性;不用或少用缓凝剂,为返至井筒中、上部的快速凝固及防窜减轻缓凝剂的干扰;解决了低密度前期靠缓凝剂延缓稠化时间,后期靠促凝剂提高凝固质量的冲突点,为提升填充段封固质量从材料上获得了基础性提高。
27.2.本发明采用低水化热硅酸盐水泥替代高抗硫g级水泥所配制的低热高强低密度体系,比原体系性能具有综合性的提高,克服原体系耐温性差,外加剂用量大,调配困难等问题;同时具有更好的流动度,降低了施工顶替摩阻;为更好的封固重点井及高难度井,提高了水泥浆技术水。
28.3.本发明开发的高性能低热硅酸盐水泥主要突破了传统硅酸盐水泥(pc)熟料以硅酸三钙(c3s≥50%)为主导矿物的组成设计,在制备技术上解决了c2s活化和常温稳定两大难题,并在国内外首次采用不同的水泥回转窑直接制备高活性的低热硅酸盐水泥,实现了低热硅酸盐水泥的规模化生产。
29.上述说明仅是本发明技术方案的概述,为了能够更清楚的了解本发明的技术手段,以下结合具体实施例,对本发明作进一步的详细说明。
具体实施方式
30.下面将结合实施例对本发明的实施方案进行详细描述,但是本领域技术人员将会理解,下列实施例仅用于说明本发明,而不应视为限制本发明的范围。
31.需要说明的是:实施例中未注明具体条件者,按照常规条件或制造商建议的条件进行。下述实施例中提及的所有原料如无特别说明均从公开的商业途径获得。
32.本发明中,如果没有特别的说明,百分数(%)或者份指的是相对于组合物的质量百分数或重量份。
33.针对目前低密高强体系的缺点,为提高油气井固井质量,本发明采用了如下的技术手段:
34.1、选择合适组分的低热硅酸盐水泥:
35.基于国内外标准对低热硅酸盐水泥组成及性能指标要求(分别见表1和表2),通过对不同组分配比硅酸盐水泥,在低密度体系中的反复实验筛选,优选出低水化热硅酸盐水泥组分为:c3s含量为28%~33%;c2s含量为42%~48%;c3a含量不大于3%;c4af含量为15%~17%;cao含量为3~4%;余量为混杂矿物成分。
36.具体地,所述混杂矿物成分为mgo或so3中的一种或其混合物;且混杂矿物成分的质量百分比含量<5%。
37.所选用的低水化热硅酸盐水泥组分中c2s的含量在42%以上,c3s的含量在33%以下,c3a含量不大于3%,熟料矿物体系中硅酸盐矿物的含量为75~80%,所述低热硅酸盐水泥的粒径为2.0
‑
150μm。本发明通过增加放热速率慢、凝结强度高的c2s含量,达到前期水化热降低、稠化时间延长,后期强度增加的目的。
38.表1各国标准对低热硅酸盐水泥或熟料化学成分和矿物组成要求
39.相关标准mgoso3c3sc2sc3aastmc150
‑
16≤6.0%≤2.3%≤35%≥40%≤7%jisr5210
‑
2009≤5.0%≤3.5%/≥40%≤6%gb200
‑
2003≤6.0%≤3.5%/≥40%≤6%
40.表2各国标准对低热水泥抗压强度及水化热性能指标要求
41.42.表3选用的低热硅酸盐水泥与其它水泥水化热对比
43.水泥品种3d水化热/kj/kg7d水化热/kj/kg28d水化热/kj/kg低热硅酸盐水泥192222263g级油井水泥233276315普通硅酸盐水泥253296348
44.通过表3可知,所选用的低热硅酸盐水泥放热速率(3d水化热小于195/kj/kg)比g级油井水泥(3d水化热小于233/kj/kg)低。
45.除此之外,该低水化热硅酸盐水泥的28d强度与通用硅酸盐水泥相当、90d后龄期强度高出传统硅酸盐水泥10mpa以上。因此,该低水化热硅酸盐水泥具有水化反应慢、水化热低、高后期强度和抗侵蚀性能好等特性,保证后期凝固强度满足行标要求。
46.2.在以上研究结果的基础上,本发明运用上述选定的低水化热硅酸盐水泥,为现场固井施工调配出性能平衡可靠的高强度低水化热低密度水泥浆体系,按重量份数计,包括以下组份:低水化热硅酸盐水泥25
‑
35份、玻化微珠20~25份、矿渣粉25~30份、微硅粉8~10份、熟石膏3~5份、硫酸钠1~2份、生石灰1~2份、熟石灰2~3份、偏硅酸钠2~3份、碳酸钠0.5~1.5份、水65~75份。
47.本发明所提供的高强度低水化热低密度水泥浆体系使用时,可需根据井温和井型的不同,选择加入不同量的缓凝剂、降失水剂和减阻剂等外加剂,以调整体系固化的稠化时间长短,。其中,缓凝剂的添加量优选2.0~2.5重量份;减阻剂的添加量优选0.1~0.25重量份;缓凝剂的添加量优选0~0.4重量份。
48.需要进一步说明的是,在油、气井施工中,要求低密度浆体既要有长的稠化时间,又有较高的胶结强度等特性,因此,要确保全井固井质量可根据实际需要添加上述缓凝剂、降失水剂、减阻剂中的任意一种或两种及两种以上。具体地实施方案举例说明如下:
49.作为进一步优选的技术方案,所述固井用高强度低水化热低密度水泥浆体系,按重量份数计,包括以下组份:低水化热硅酸盐水泥25
‑
35份、玻化微珠20~25份、矿渣粉25~30份、微硅粉8~10份、熟石膏3~5份、硫酸钠1~2份、生石灰1~2份、熟石灰2~3份、偏硅酸钠2~3份、碳酸钠0.5~1.5份、降失水剂2.0~2.5份、减阻剂0.1~0.25份、水65~75份。
50.作为进一步优选的技术方案,所述固井用高强度低水化热低密度水泥浆体系,按重量份数计,包括以下组份:低水化热硅酸盐水泥25
‑
35份、玻化微珠20~25份、矿渣粉25~30份、微硅粉8~10份、熟石膏3~5份、硫酸钠1~2份、生石灰1~2份、熟石灰2~3份、偏硅酸钠2~3份、碳酸钠0.5~1.5份、缓凝剂0~0.4份、水65~75份。
51.作为进一步优选的技术方案,所述固井用高强度低水化热低密度水泥浆体系,按重量份数计,包括以下组份:低水化热硅酸盐水泥25
‑
35份;60目闭口玻化珍珠岩20~25份;s105矿渣粉25~30份;微硅粉(工业级)8~10份;熟石膏(工业级)3~5份;硫酸钠(工业级)1~2份;生石灰(工业级)1~2份;熟石灰(工业级)2~3份;偏硅酸钠(模数2.8
‑
3.0)2~3份;碳酸钠(工业级)0.5~1.5份;降失水剂(聚乙烯醇1788)2.0~2.5份;减阻剂(聚羧酸类)0.1~0.25份;缓凝剂(羟基乙叉二膦酸四钠)0.15~0.4份水65~75份。
52.本发明依靠s105级矿渣粉的活性,产生相当于同质量水泥105份的强度效果,加上与体系中的低水化热硅酸盐水泥、减轻材料玻化微珠、微硅粉,形成颗粒紧密级配,从而实现强度较高的效果。
53.作为进一步优选的技术方案,所述降失水剂为聚乙烯醇1788。
54.作为进一步优选的技术方案,所述缓凝剂为羟基乙叉二膦酸四钠。
55.作为进一步优选的技术方案,所述减阻剂为聚羧酸类减阻剂。
56.3.在以上研究结果的基础上,本发明进一步提供了一种固井用高强度低水化热低密度水泥浆体系的制备方法,包括以下步骤:
57.s1.按照下述重量份数称取原料:低水化热硅酸盐水泥25
‑
35份、玻化微珠20~25份、矿渣粉25~30份、微硅粉8~10份、熟石膏3~5份、硫酸钠1~2份、生石灰1~2份、熟石灰2~3份、偏硅酸钠2~3份、碳酸钠0.5~1.5份、降失水剂2~3份、减阻剂0.1~0.25份;缓凝剂0~0.4份;
58.s2.在常温条件下,将s1所称取的原料混拌均匀,得混合干灰;
59.s3.将65~75份的水到入恒速搅拌器的搅拌浆杯中,开启恒速搅拌器,在4000转/分的转速下将s2所得混合干灰在0~15秒时间内均匀倒入转动浆杯中,继续搅拌35秒,即得高强度低水化热低密度水泥浆体系。
60.作为进一步优选的技术方案,
61.4.在以上研究结果的基础上,本发明进一步提供了一种固井用高强度低水化热低密度水泥浆体系的应用,该高强度低水化热低密度水泥浆体系的密度为1.20~1.30g/cm3,48小时强度达到10mpa以上;适用50~90℃范围内的油、气井固井作业。
62.下面结合实施例和对比例对本发明做进一步详细的说明。
63.实施例1:
64.本实施例提供了一种固井用高强度低水化热低密度水泥浆体系,其配方为:25份低水化热水泥+30份60目闭口玻化珍珠岩(玻化微珠)+25份s105矿渣粉+10份微硅粉+3.5份熟石膏+3.0份偏硅酸钠+0.75份碳酸钠+1.5份硫酸钠+1.0份生石灰+1.0份熟石灰+2.2份降失水剂+0.15份减阻剂+75份自来水。
65.本实施例所述固井用高强度低水化热低密度水泥浆体系的制备方法,包括以下步骤:
66.s1.在常温条件下,将25份低水化热水泥、30份60目闭口玻化珍珠岩、25份s105矿渣粉、10份微硅粉、3.5份熟石膏、3.0份偏硅酸钠、0.75份碳酸钠、1.5份硫酸钠、1.0份生石灰、1.0份熟石灰、2.2份降失水剂、0.15份减阻剂混拌均匀,得混合干灰;
67.s2.将75份的自来水到入恒速搅拌器的搅拌浆杯中,开启恒速搅拌器,在4000转/分的转速下将s1所得混合干灰在0~15秒时间内均匀倒入转动浆杯中,继续搅拌35秒,即得高强度低水化热低密度水泥浆体系。
68.实施例2:
69.本实施例提供了一种固井用高强度低水化热低密度水泥浆体系,其配方为:25份低水化热水泥+30份60目闭口玻化珍珠岩+25份s105矿渣粉+10份微硅粉+3.5份熟石膏+2.5份偏硅酸钠+0.5份碳酸钠+1.5份硫酸钠+1.0份生石灰+1.0份熟石灰+2.2份降失水剂+0.15份减阻剂+65份自来水。
70.本实施例所述固井用高强度低水化热低密度水泥浆体系的制备方法,包括以下步骤:
71.s1.在常温条件下,将25份低水化热水泥、30份60目闭口玻化珍珠岩、25份s105矿
渣粉、10份微硅粉、3.5份熟石膏、2.5份偏硅酸钠、0.5份碳酸钠、1.5份硫酸钠、1.0份生石灰、1.0份熟石灰、2.2份降失水剂、0.15份减阻剂混拌均匀,得混合干灰;
72.s2.将65份的自来水到入恒速搅拌器的搅拌浆杯中,开启恒速搅拌器,在4000转/分的转速下将s1所得混合干灰在0~15秒时间内均匀倒入转动浆杯中,继续搅拌35秒,即得高强度低水化热低密度水泥浆体系。
73.实施例3:
74.本实施例提供了一种固井用高强度低水化热低密度水泥浆体系,其配方为:25份低水化热水泥+25份60目闭口玻化珍珠岩+30份s105矿渣粉+10份微硅粉+3.0份熟石膏+2.5份偏硅酸钠+0.5份碳酸钠+1.5份硫酸钠+1.5份生石灰+1.0份熟石灰+2.2份降失水剂+0.15份减阻剂+70份自来水。
75.本实施例所述固井用高强度低水化热低密度水泥浆体系的制备方法,包括以下步骤:
76.s1.在常温条件下,将25份低水化热水泥、25份60目闭口玻化珍珠岩、30份s105矿渣粉、10份微硅粉、3.0份熟石膏、2.5份偏硅酸钠、0.5份碳酸钠、1.5份硫酸钠、1.5份生石灰、1.0份熟石灰、2.2份降失水剂、0.15份减阻剂混拌均匀,得混合干灰;
77.s2.将70份的自来水到入恒速搅拌器的搅拌浆杯中,开启恒速搅拌器,在4000转/分的转速下将s1所得混合干灰在0~15秒时间内均匀倒入转动浆杯中,继续搅拌35秒,即得高强度低水化热低密度水泥浆体系。
78.测试实施例1
‑
3所得不同密度的固井用高强度低水化热低密度水泥浆体系在不同温度下的性能,测试结果如下表4、表5、表6、表7、表8所示。
79.表4不同密度固井用高强度低水化热低密度水泥浆体系在50℃条件下的实验结果
[0080][0081]
表5不同密度固井用高强度低水化热低密度水泥浆体系在60℃条件下的实验结果
[0082][0083]
表6不同密度固井用高强度低水化热低密度水泥浆体系在70℃条件下的实验结果
[0084][0085]
表7不同密度固井用高强度低水化热低密度水泥浆体系在80℃条件下的实验结果
[0086][0087]
表8不同密度固井用高强度低水化热低密度水泥浆体系在90℃条件下的实验结果
[0088][0089]
通过上述系列实验数据表明,不同密度的低热高强低密度体系(即高强度低水化热低密度水泥浆体系),可以通过少量的缓凝剂加量调整,使得在50
‑
90℃范围内都具有较长的稠化时间,同时强度发展受到的干扰控制在可接受的范围之内,其中对两天以后的强度影响几乎不存在;实现了即节约了外加剂又提高了工作效率的目的。
[0090]
实施例4:
[0091]
本实施例提供了一种固井用高强度低水化热低密度水泥浆体系,其配方为:25份低水化热水泥+30份60目闭口玻化珍珠岩+25份s105矿渣粉+10份微硅粉+3.5份熟石膏+2.5份偏硅酸钠+0.5份碳酸钠+1.5份硫酸钠+1.0份生石灰+1.0份熟石灰+2.2份降失水剂+0.15份减阻剂+65份自来水。
[0092]
本实施例所述固井用高强度低水化热低密度水泥浆体系的制备方法,包括以下步骤:
[0093]
s1.在常温条件下,将25份低水化热水泥+30份60目闭口玻化珍珠岩+25份s105矿渣粉+10份微硅粉+3.5份熟石膏+2.5份偏硅酸钠+0.5份碳酸钠+1.5份硫酸钠+1.0份生石灰+1.0份熟石灰+2.2份降失水剂+0.15份减阻剂混拌均匀,得混合干灰;
[0094]
s2.将65份的自来水到入恒速搅拌器的搅拌浆杯中,开启恒速搅拌器,在4000转/分的转速下将s1所得混合干灰在0~15秒时间内均匀倒入转动浆杯中,继续搅拌35秒,即得高强度低水化热低密度水泥浆体系。
[0095]
对比实施例:
[0096]
本实施例提供了一种固井用高强度低水化热低密度水泥浆体系,其配方为:25份高抗g级水泥+30份60目闭口玻化珍珠岩+25份s105矿渣粉+10份微硅粉+3.5份熟石膏+2.5份偏硅酸钠+0.5份碳酸钠+1.5份硫酸钠+1.0份生石灰+1.0份熟石灰+2.2份降失水剂+0.15份减阻剂+65份自来水。
[0097]
本实施例所述固井用高强度低水化热低密度水泥浆体系的制备方法,包括以下步骤:
[0098]
s1.在常温条件下,将25份高抗g级水泥+30份60目闭口玻化珍珠岩+25份s105矿渣粉+10份微硅粉+3.5份熟石膏+2.5份偏硅酸钠+0.5份碳酸钠+1.5份硫酸钠+1.0份生石灰+1.0份熟石灰+2.2份降失水剂+0.15份减阻剂混拌均匀,得混合干灰;
[0099]
s2.将65份的自来水到入恒速搅拌器的搅拌浆杯中,开启恒速搅拌器,在4000转/分的转速下将s1所得混合干灰在0~15秒时间内均匀倒入转动浆杯中,继续搅拌35秒,即得
高强度低水化热低密度水泥浆体系。
[0100]
测试本实施例所得固井用高强度低水化热低密度水泥浆体系与高抗g级水泥体系的流变性能,测试结果如下表9、表10所示。
[0101]
表9固井用高强度低水化热低密度水泥浆体系流变性能(65度/20min/常压)
[0102]
转速36100200300600上行1114436587133下行914416486132平均11144264.586.5132.5
[0103]
其中,表观粘度=66.5厘泊、塑性粘度=46厘泊、n=0.5596、k=13.64。
[0104]
表10高抗g级水泥体系流变性能(65度/20min/常压)
[0105]
转速36100200300600上行1216375580139下行1216385078137平均121637.549.579138
[0106]
其中,表观粘度=69厘泊、塑性粘度=59厘泊、n=0.4917、k=18.44。
[0107]
对照上述两组数据,可以明显的看出:低密高强体系为了获得较高的体系强度,采用了较低的水灰比(水与总干灰之比0.65
‑
0.75),单位体积内的固相含量高,造成浆体的初始稠度普遍较高(20bc以上),同条件下,固井用高强度低水化热低密度水泥浆体系前期水化程度低,流动度和流性指数明显好于高抗g级水泥体系,流动度好、粘度低利于降低流动阻力,流性指数平稳表明体系随着温度上升粘度上升更接近线形,而不是呈指数态加速上升。
[0108]
通过上述系列实验数据表明:本发明所述固井用高强度低水化热低密度水泥浆体系与g级高抗水泥所形成的低密度体系相比,综合性的提高,克服原体系耐温性差,外加剂用量大,调配困难等问题;同时具有更好的流动度,降低了施工顶替摩阻;为更好的封固重点井及高难度井,提高了水泥浆技术水平。
[0109]
综上所述,本发明所述固井用高强度低水化热低密度水泥浆体系的性能可达到以下指标:
[0110]
(1)适用范围:
[0111]
①
体系密度:1.20
‑
1.30g/cm3[0112]
②
适用温度:50~90℃
[0113]
③
水泥石强度要求:常压/45℃/24h/48h>7mpa/10mpa(符合:sy/t6544
‑
2017油井水泥浆性能要求)。
[0114]
所述固井用高强度低水化热低密度水泥浆体系解决以下缺陷:
[0115]
①
耐温性差:70℃以上时,原体系稠化时间明显缩短(缩短60
‑
100min以上);
[0116]
②
外加剂用量大:同温度、同密度、相同稠化时间,原体系加入的缓凝剂、增强剂超过新体系50%以上;
[0117]
③
调配困难等问题:由于调整稠化时间的缓凝剂加量大,影响体系24
‑
48h的强度发展,需多次调整缓凝和增强之间的配比关系。
[0118]
(2)性能的提升:
[0119]
①
具有更好的流动度:由于所选材料的前期水化度低,降低了体系前期粘度,保持了良好的流动度,减少施工顶替摩阻。
[0120]
②
更好的中后期强度:由于c2s具有比c3s更高的凝结强度,加上缓凝剂的用量低,使得体系具有更高的凝结强度(提高15份以上)。
[0121]
③
在相同配比条件下,形成的水泥浆体系密度、稠度、稳定性等基础物理指标数据,不发生明显的改变(各项数据波动小于3份),方便后续开展配方微调工作。
[0122]
④
在相同的稠化实验条件下,高强度低水化热低密度水泥浆体系稠化时间具有明显的延长(不同温度条件下,延长40
‑
80min以上);
[0123]
⑤
在相同的强度养护实验条件下,高强度低水化热低密度水泥浆体系后期强度发展具有明显的增长(48
‑
72h不同温度条件下,增长1
‑
3mpa以上)。
[0124]
因此,本发明所述固井用高强度低水化热低密度水泥浆体系,解决现有“固井用g级油井水泥高强度低密度体系”的缺陷,尤其适用于长庆区域的重点井和复杂井固井(该类井普遍施工灰量大、施工时间长,要求低密度浆体既要有长的稠化时间,又有较高的胶结强度),该固井用高强度低水化热低密度水泥浆体系的密度使用范围为:1.20
‑
1.30g/cm3,强度性能为:>7/10mpa(常压45℃/24h/48h),该水泥浆体系的密度低,确保一次上返全封固井筒环空;强度高,能更好的支撑套管;温度适用范围(50~90℃)广,消除了现有水泥浆体系中使用缓凝剂与促凝激活剂之间的性能冲突,该固井用高强度低水化热低密度水泥浆体系不仅实现了稠化时间在不影响强度性能指标下的可调性;而且为重点井固井防止漏失、提高封固率、压稳产层段,确保全井固井质量,提供了可靠的技术保障。
[0125]
以上对本发明的较佳实施方式进行了具体说明,但本发明创造并不限于所述实施例,熟悉本领域的技术人员在不违背本发明精神的前提下还可作出种种的等同变型或替换,这些等同的变型或替换均包含在本申请权利要求所限定的范围内。