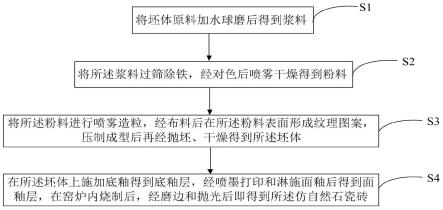
1.本技术涉及瓷砖技术领域,特别涉及一种仿自然石瓷砖及其制备工艺。
背景技术:2.天然石材由于具有独特的装饰效果,其作为装饰材料一直受到人们的追捧,随着开采技术的提升,天然石材广泛的走进了人们的生活。但天然石材在使用过程中会释放放射性氡元素,部分是镭、钍等放射性元素的衰变产物,氡元素继续衰变后生成氡子体,氡及其子体会对人体造成危害,且不同品种的石材放射性物质也不同;并且天然石材由于成型时间较久,出于资源的保护其开采也受到了较多的限制。因此,市场上的部分厂家开始研究仿石材的陶瓷砖,用以替代天然的石材,由于陶瓷砖具有吸水率低、机械强度和光泽度高的特点,且成产成本较低,因此将其用于替代石材作为装饰材料较为普遍。
3.而传统的仿石材陶瓷砖坯体在制备过程中,经过球磨、喷雾造粒、均化等工艺处理后得到粉料,再经过布料机一次布料或二次布料后直接半干压成型,现有的仿石材瓷砖表面分布有各类石纹用于仿真,但目前的仿石材瓷砖坯体对于色料的发色效果较差,导致最终的瓷砖产品其石材仿真效果较差;并且由于仿石材瓷砖需要将瓷砖的厚度调大,以获得较好的仿石效果,但随着厚度的增大,瓷砖在烧制时将会存在各类的缺陷,如瓷砖内部出现“黑心”情况等,导致仿石材瓷砖的质量较差。
技术实现要素:4.本技术的主要目的是提供一种仿自然石瓷砖及其制备工艺,旨在解决现有的仿石材瓷砖的仿石材效果较差,且仿石材瓷砖产品存在烧结缺陷的技术问题。
5.为实现上述目的,本技术提出的一种仿自然石瓷砖,包括以下步骤:
6.s1.将坯体原料加水球磨后得到浆料;
7.s2.将所述浆料过筛除铁,经对色后喷雾干燥得到粉料;
8.s3.将所述粉料进行喷雾造粒,经布料后在所述粉料表面形成纹理图案,压制成型后再经抛坯、干燥得到所述坯体;
9.s4.在所述坯体上施加底釉得到底釉层,经喷墨打印和淋施面釉后得到面釉层,在窑炉内烧制后,经磨边和抛光后即得到所述仿自然石瓷砖。
10.可选地,所述步骤s4中,窑炉内包括第一烧制区和第二烧制区,所述第一烧制区的温度为1190-1210℃,所述第一烧制区的烧制时间为40-55min;所述第二烧制区的温度为1215-1235℃,所述第二烧制区的烧制时间为90-110min。
11.可选地,所述步骤s4中,先采用硬质磨块抛光,再采用软质磨块进行抛光。
12.可选地,所述粉料中粒度为40目以上的占比为30-42%;粒度为40目-60目的占比为35%-43%;粒度为60目-100目的占比为11%-18%;粒度为100目以下的占比为6-9%。
13.除此之外,本发明还提出一种由上述任一项所述的仿自然石瓷砖的制备工艺制备得到的仿自然石瓷砖,包括坯体、底釉层和面釉层,所述底釉层位于所述坯体和所述面釉层
之间;
14.按质量百分比,所述坯体由包括如下组分的原料压制得到:第一瓷砂6-10%,第二瓷砂3-7%,第三瓷砂4-8%,第四瓷砂8-12%,石粉38-46%,泥6-10%,第一黏土5-9%,第二黏土9-13%,助熔剂2.5-3.5%。
15.可选地,按质量百分比,所述第一瓷砂的化学组成如下:sio265-72%、al2o317-19%、tio20.2-0.5%、lio20.2-0.3%、cao 0.1-0.2%、mgo 0.1-0.2%、k2o 3-4%、na2o 1-2%、l.o.i 4-5%;
16.所述第二瓷砂的化学组成如下:sio270-75%、al2o315-18%、tio20.3-0.5%、cao 0.3-0.5%、zno 0.1-0.2%、mgo 0.1-0.2%、k2o 2-3%、na2o0.5-1%、l.o.i 2-3%;
17.所述第三瓷砂的化学组成如下:sio268-73%、al2o317-19%、tio20.3-0.5%、bao 0.2-0.3%、cao 0.1-0.2%、mgo 0.1-0.2%、k2o 2-5%、na2o 1-2%、l.o.i 4-5%;
18.所述第四瓷砂的化学组成如下:sio260-65%、al2o320-25%、tio20.4-0.5%、zro20.15-0.35%、sno20.1-0.2%、cao 0.35-0.5%、mgo 0.1-0.2%、k2o 1-2%、na2o 1-2%、l.o.i 5-6%。
19.可选地,所述第一黏土的化学组成如下:sio265-70%、al2o318-23%、tio20.3-0.5%、cao 0.4-0.5%、mgo 0.3-0.5%、k2o 1-2%、na2o 1-2%、l.o.i5-8%;
20.所述第二黏土的化学组成如下:sio272-78%、al2o313-20%、tio20.1-0.35%、cao 0.3-0.4%、mgo 0.3-0.5%、k2o 2-3%、na2o 1-2%、l.o.i 4-7%。
21.可选地,所述石粉的化学组成如下:sio275-78%、al2o312-15%、tio2《0.1%、cao《0.5%、mgo《0.2%、k2o 3-4%、na2o 2-3%、l.o.i 1-2%。
22.可选地,所述助熔剂由b2o3和baf2复配而成,b2o3和baf2的质量比为(2-4.5):1。
23.可选地,所述坯体的原料中还包括增强剂,所述增强剂为三聚磷酸钠、五水偏硅酸钠、碳酸钠、水玻璃、甲基纤维素或羧甲基纤维素中的至少一种。
24.本技术的技术方案通过在窑炉中设置2个烧成区对瓷砖进行烧制,使得陶瓷砖的机械强度有所提升。通过坯体组分中四组瓷砂的配合使用,使得仿自然石瓷砖具有较好的白度和发色效果,同时还可以避免制备厚度较大的瓷砖在烧结时产生的缺陷,瓷砖产品的质量较优;除此之外,本方案还添加有由b2o3和baf2复配而成的特殊助熔剂,进一步提升瓷砖的机械强度和发色效果,从而使制备得到的瓷砖产品从图案纹理、视觉效果和质感上达到了较好的仿石材效果。
附图说明
25.为了更清楚地说明本技术实施例或现有技术中的技术方案,下面将对实施例或现有技术描述中所需要使用的附图作简单地介绍,显而易见地,下面描述中的附图仅仅为本技术的一些实施例,对于本领域普通技术人员来讲,在不付出创造性劳动的前提下,还可以根据这些附图获得其他相关的附图。
26.图1为本技术提供的一种仿自然石瓷砖的制备工艺一实施例的流程示意图。
27.本技术目的的实现、功能特点及优点将结合实施例,参照附图做进一步说明。
具体实施方式
28.为使本技术实施例的目的、技术方案和优点更加清楚,下面将对本技术实施例中的技术方案进行清楚、完整地描述。实施例中未注明具体条件者,按照常规条件或制造商建议的条件进行。所用试剂或仪器未注明生产厂商者,均为可以通过市售购买获得的常规产品。
29.本技术提出一种仿自然石瓷砖。参照图1,图1为本技术提供的一种仿自然石瓷砖的一实施例的流程示意图。
30.在本技术实施例中,一种仿自然石瓷砖,包括以下步骤:
31.s1.将坯体原料加水球磨后得到浆料;
32.s2.将所述浆料过筛除铁,经对色后喷雾干燥得到粉料;
33.s3.将所述粉料进行喷雾造粒,经布料后在所述粉料表面形成纹理图案,压制成型后再经抛坯、干燥得到所述坯体;
34.s4.在所述坯体上施加底釉得到底釉层,经喷墨打印和淋施面釉后得到面釉层,在窑炉内烧制后,经磨边和抛光后即得到所述仿自然石瓷砖。
35.本技术的技术方案包括:将坯体原料加水,经球磨后细碎成细度为250目筛筛余量为0.8%-1.2%的浆料,浆料中含有35%-36%的水分,球磨时间为11-12小时;经除铁过筛、对色对版、喷雾干燥制成粉料,粉料中7%-7.8%的水分,经造粒、数码布料、液压成型、抛坯后进入干燥窑中干燥得到坯体,干燥温度为300℃以下,优选265-285℃,干燥时间为170-180min。将底釉和面釉原料分别加水,经球磨细碎成细度为325目筛筛余量为0.3%-0.5%的底釉釉浆和面釉釉浆,底釉釉浆和面釉釉浆中均含有28%-32%的水分,经除铁过筛后分别得到底釉和面釉,在坯体上施加底釉,再经喷墨打图、淋施面釉、烧制、磨边和抛光得到仿自然石瓷砖。其中,在施底釉前干坯表面的温度为70-75℃,在干坯表面喷水后再进行施釉。制备得到的瓷砖产品从图案纹理、视觉效果和质感上达到了较好的仿石材效果。
36.在本技术一实施例中,所述步骤s4中,窑炉内包括第一烧制区和第二烧制区,所述第一烧制区的温度为1190-1210℃,所述第一烧制区的烧制时间为40-55min;所述第二烧制区的温度为1215-1235℃,所述第二烧制区的烧制时间为90-110min。
37.可以理解,普通陶瓷砖烧制时的温度较低,本方案中的返自然石瓷砖在窑炉中进行烧制时,窑炉设置有第一烧制区和第二烧制区,本方案将第一烧制区的烧制温度提高,具体为1190-1210℃,烧成时间为40-55min;之后瓷砖进入第二烧制区,具体的烧制温度为1215-1235℃,烧制周期为90-110min,第二烧制区的烧成周期相对较长,使瓷砖烧结完全,避免产生二次变形等缺陷。采用一次高温烧制工艺进行生产,其中第一烧制区和第二烧制区的烧成温度差不超过30℃,整个烧制步骤中兼顾到了坯体、底釉和干粒的烧制性能,在保证坯体具有合适的烧结强度的同时,避免由于坯体的图案花纹导致的坯体变形增大的问题,提升瓷砖的仿石材效果,同时采用上述烧制工艺,还可以避免由于坯体中有机物燃烧不充分,使坯体中的有机物等挥发性组分在进入窑炉第二烧制区前充分氧化挥发,避免砖坯产生黑心等缺陷。
38.在本技术一实施例中,所述步骤s4中,先采用硬质磨块抛光后,再采用软质磨块进行抛光。在本方案中,针对抛光工艺也进行了适应性的优化调整。为了使自然石的光感更加接近石材,消除瓷砖的水波纹和辊棒印等缺陷,抛光工序先采用硬质磨块对釉面进行深抛,
再采用软质磨块进行抛光。
39.在本技术一实施例中,所述粉料中粒度为40目以上的占比为30-42%;粒度为40目-60目的占比为35%-43%;粒度为60目-100目的占比为11%-18%;粒度为100目以下的占比为6-9%。粉料采用上述颗粒级配,可以保证仿自然石瓷砖在具有较好的石材仿真效果的同时还具有较好的机械性能和强度。
40.本技术还提供一种仿自然石瓷砖,所述仿自然石瓷砖由上述任一种仿自然石瓷砖制备工艺制备得到,包括坯体、底釉层和面釉层,所述底釉层位于所述坯体和所述面釉层之间;按质量百分比,所述坯体由包括如下组分的原料压制得到:第一瓷砂6-10%,第二瓷砂3-7%,第三瓷砂4-8%,第四瓷砂8-12%,石粉38-46%,泥6-10%,第一黏土5-9%,第二黏土9-13%,助熔剂2.5-3.5%。
41.仿自然石瓷砖由上述仿自然石瓷砖制备工艺制备得到,仿自然石瓷砖参照上述实施例,由于仿自然石瓷砖采用了上述所有实施例的全部技术方案,因此至少具有上述实施例的技术方案所带来的所有效果,在此不再一一赘述。
42.仿自然石瓷砖包括从上至下的面釉层、底釉层和坯体(层)。其中,坯体的组分包括四组瓷砂和两组黏土,同时复配有石粉、泥和助熔剂,采用上述组分配方,可以使制得的仿自然石瓷砖具有较好的白度和发色效果,从而瓷砖产品显现出的仿石材效果较好。
43.在本技术一实施例中,按质量百分比,所述第一瓷砂的化学组成如下:sio265-72%、al2o317-19%、tio20.2-0.5%、lio20.2-0.3%、cao 0.1-0.2%、mgo 0.1-0.2%、k2o 3-4%、na2o 1-2%、l.o.i 4-5%;所述第二瓷砂的化学组成如下:sio270-75%、al2o315-18%、tio20.3-0.5%、cao 0.3-0.5%、zno0.1-0.2%、mgo 0.1-0.2%、k2o 2-3%、na2o 0.5-1%、l.o.i 2-3%;所述第三瓷砂的化学组成如下:sio268-73%、al2o317-19%、tio20.3-0.5%、bao 0.2-0.3%、cao 0.1-0.2%、mgo 0.1-0.2%、k2o 2-5%、na2o 1-2%、l.o.i 4-5%;所述第四瓷砂的化学组成如下:sio260-65%、al2o320-25%、tio20.4-0.5%、zro20.15-0.35%、sno20.1-0.2%、cao 0.35-0.5%、mgo 0.1-0.2%、k2o 1-2%、na2o1-2%、l.o.i 5-6%。
44.由于仿自然石瓷砖的砖坯通常设置的较厚,以提高瓷砖的石材仿真效果,具体的产品厚度包括15.5mm、18mm、25mm或28mm等,目前市场上的仿石材瓷砖在厚度较大得情况下,烧制完成后容易产生黑心、烧结不完全而引起的二次变形等生产问题。本实施例采用上述四种瓷砂复配使用,当瓷砖的厚度较大时,上述烧结缺陷也不会发生,同时还可以改善仿自然石瓷砖整体的白度,在对色、烧制完成后,瓷砖整体的发色效果较好。
45.在本技术一实施例中,所述第一黏土的化学组成如下:sio265-70%、al2o318-23%、tio20.3-0.5%、cao 0.4-0.5%、mgo 0.3-0.5%、k2o 1-2%、na2o 1-2%、l.o.i 5-8%;所述第二黏土的化学组成如下:sio272-78%、al2o313-20%、tio20.1-0.35%、cao 0.3-0.4%、mgo 0.3-0.5%、k2o 2-3%、na2o 1-2%、l.o.i 4-7%。第一黏土和第二黏土组分的配合设置主要是为了改善陶瓷砖的机械性能,包括瓷砖的强度等。
46.在本技术一实施例中,所述石粉的化学组成如下:sio275-78%、al2o312-15%、tio2《0.1%、cao《0.5%、mgo《0.2%、k2o 3-4%、na2o 2-3%、l.o.i1-2%。其中,sio2的含量可以为75%、76%、77%以及78%之间的任意值;al2o3的含量可以为12%、13%、14%以及15%之间的任意值;k2o的含量可以为3%、3.5%、4%之间的任意值;na2o的含量可以为2%、
2.5%、3%之间的任意值。
47.在本技术一实施例中,所述助熔剂由b2o3和baf2复配而成,b2o3和baf2的质量比为(2-4.5):1。采用上述由b2o3和baf2复配得到的助熔剂,可以进一步改善瓷砖的发色效果,同时也可以避免烧结缺陷的产生,使制得的瓷砖具有较好的石材仿真效果,产品的质量较佳。
48.在本技术一实施例中,所述坯体的原料中还包括增强剂,所述增强剂为三聚磷酸钠、五水偏硅酸钠、碳酸钠、水玻璃、甲基纤维素或羧甲基纤维素中的至少一种。增强剂的添加量在1.5-2.5%的范围内,坯体组分加入上述增强剂后,分子链互相交连形成网络结构,坯体粉料进入网络结构而被粘结在一起,起到了骨架的作用,进一步提高了坯体的强度。
49.以下结合具体实施例对本技术的技术方案作进一步详细说明,应当理解,以下实施例仅仅用以解释本技术,并不用于限定本技术。
50.实施例1
51.一种仿自然石瓷砖的制备工艺,包括如下步骤:
52.s1.将坯体原料加水球磨后得到浆料;
53.s2.将所述浆料过筛除铁,经对色后喷雾干燥得到粉料,粉料中粒度为40目以上的占比为42%;粒度为40目-60目的占比为35%;粒度为60目-100目的占比为16%;粒度为100目以下的占比为7%;
54.s3.将所述粉料进行喷雾造粒,经布料后在所述粉料表面形成纹理图案,压制成型后再经抛坯、干燥得到所述坯体;
55.s4.在所述坯体上施加底釉得到底釉层,经喷墨打印和淋施面釉后得到面釉层,在窑炉内烧制后,窑炉内包括第一烧制区和第二烧制区,所述第一烧制区的温度为1200℃,所述第一烧制区的烧制时间为48min;所述第二烧制区的温度为1215℃,所述第二烧制区的烧制时间为100min,经磨边和抛光后即得到所述仿自然石瓷砖,抛光时先采用硬质磨块抛光,再采用软质磨块进行抛光。
56.本实施例中选用的坯体原料、底釉原料和面釉原料均采用本领域中的常规原料,制得的仿自然石瓷砖规格为750
×
1500mm,厚度为25mm。
57.实施例2
58.一种仿自然石瓷砖的制备工艺,包括如下步骤:
59.s1.将坯体原料加水球磨后得到浆料;
60.s2.将所述浆料过筛除铁,经对色后喷雾干燥得到粉料,粉料中粒度为40目以上的占比为40%;粒度为40目-60目的占比为41%;粒度为60目-100目的占比为11%;粒度为100目以下的占比为8%;
61.s3.将所述粉料进行喷雾造粒,经布料后在所述粉料表面形成纹理图案,压制成型后再经抛坯、干燥得到所述坯体;
62.s4.在所述坯体上施加底釉得到底釉层,经喷墨打印和淋施面釉后得到面釉层,在窑炉内烧制后,窑炉内包括第一烧制区和第二烧制区,所述第一烧制区的温度为1210℃,所述第一烧制区的烧制时间为50min;所述第二烧制区的温度为1235℃,所述第二烧制区的烧制时间为105min,经磨边和抛光后即得到所述仿自然石瓷砖,抛光时先采用硬质磨块抛光,再采用软质磨块进行抛光。
63.本实施例中选用的坯体原料、底釉原料和面釉原料均采用本领域中的常规原料,
制得的仿自然石瓷砖规格为750
×
1500mm,厚度为25mm。
64.实施例3
65.一种仿自然石瓷砖的制备工艺,包括如下步骤:
66.s1.将坯体原料加水球磨后得到浆料;
67.s2.将所述浆料过筛除铁,经对色后喷雾干燥得到粉料,粉料中粒度为40目以上的占比为34%;粒度为40目-60目的占比为41%;粒度为60目-100目的占比为17%;粒度为100目以下的占比为8%;
68.s3.将所述粉料进行喷雾造粒,经布料后在所述粉料表面形成纹理图案,压制成型后再经抛坯、干燥得到所述坯体;
69.s4.在所述坯体上施加底釉得到底釉层,经喷墨打印和淋施面釉后得到面釉层,在窑炉内烧制后,窑炉内包括第一烧制区和第二烧制区,所述第一烧制区的温度为1200℃,所述第一烧制区的烧制时间为50min;所述第二烧制区的温度为1230℃,所述第二烧制区的烧制时间为105min,经磨边和抛光后即得到所述仿自然石瓷砖,抛光时先采用硬质磨块抛光,再采用软质磨块进行抛光。
70.本实施例中选用的坯体原料、底釉原料和面釉原料均采用本领域中的常规原料,制得的仿自然石瓷砖规格为750
×
1500mm,厚度为25mm。
71.将实施例1-3进行性能检测,具体的性能检测参数如下表1所示:
72.表1
[0073][0074]
从表1的测试结果可以看出,本技术制备得到的仿自然石瓷砖具有较好的机械性能和光泽度,保证了瓷砖产品在具有石材光感的同时其质量较佳。
[0075]
实施例4
[0076]
本对比例中各项条件与实施例3相同,不同之处在于:粉料中粒度为40目以上的占比为48%;粒度为40目-60目的占比为48%;粒度为60目-100目的占比为2%;粒度为100目以下的占比为2%。
[0077]
实施例5
[0078]
本对比例中各项条件与实施例3相同,不同之处在于:窑炉内的烧制温度为1235℃,烧制时间为155min。
[0079]
实施例6
[0080]
本对比例中各项条件与实施例3相同,不同之处在于:所述第一烧制区的温度为1180℃,所述第二烧制区的温度为1230℃。
[0081]
将实施例4-6进行性能检测,具体的性能检测参数如下表2所示:
[0082]
表2
[0083][0084]
从表2的测试结果可以看出,在制备仿自然石瓷砖的粉料中,如果改变粉料的颗粒级配,对瓷砖的机械强度具有较大的影响,机械强度明显降低;同样的,在烧制过程中保持温度前后不变时,以及将第一烧制区和第二烧制区的温度差值设置为超过30℃时,也会降低瓷砖产品的机械强度,从而降低瓷砖产品的质量。
[0085]
实施例7
[0086]
本对比例中各项条件与实施例3相同,不同之处在于,所述坯体由包括如下组分的原料压制得到:第一瓷砂12%,第二瓷砂7%,第三瓷砂11%,石粉42%,泥8%,第一黏土7%,第二黏土10%,碳酸钡助熔剂3%;
[0087]
所述第一瓷砂的化学组成如下:sio267%、al2o318%、tio20.5%、lio20.3%、cao 0.1%、fe2o30.5%、mgo 0.5%、k2o 4%、na2o 2.6%、l.o.i 6.5%;所述第二瓷砂的化学组成如下:sio271%、al2o318%、tio20.3%、cao 0.5%、zro20.3%、sno20.1%、fe2o30.6%、mgo 0.2%、k2o 2%、na2o 3%、l.o.i 4%;所述第三瓷砂的化学组成如下:sio273%、al2o315%、tio20.65%、bao 0.3%、cao 0.1%、fe2o30.5%、mgo 0.45%、k2o 4%、na2o 3%、l.o.i 3%。
[0088]
对比例1
[0089]
本对比例中各项条件与实施例3相同,不同之处在于:按质量百分比,所述坯体由包括如下组分的原料压制得到:第一瓷砂17%,第二瓷砂13%,石粉42%,泥8%,第一黏土7%,第二黏土10%,碳酸钡助熔剂3%;
[0090]
所述第一瓷砂的化学组成如下:sio267%、al2o318%、tio20.5%、lio20.3%、cao 0.1%、fe2o30.5%、mgo 0.5%、k2o 4%、na2o 2.6%、l.o.i 6.5%;所述第二瓷砂的化学组成如下:sio271%、al2o318%、tio20.3%、cao 0.5%、zro20.3%、sno20.1%、fe2o30.6%、mgo 0.2%、k2o 2%、na2o 3%、l.o.i 4%。
[0091]
对比例2
[0092]
本对比例中各项条件与实施例3相同,不同之处在于:所述坯体由包括如下组分的原料压制得到:第二瓷砂13%,第三瓷砂17%,石粉42%,泥8%,第一黏土7%,第二黏土10%,碳酸钡助熔剂3%;
[0093]
所述第二瓷砂的化学组成如下:sio271%、al2o318%、tio20.3%、cao0.5%、zro20.3%、sno20.1%、fe2o30.6%、mgo 0.2%、k2o 2%、na2o 3%、l.o.i 4%;所述第三瓷砂的化学组成如下:sio273%、al2o315%、tio20.65%、bao 0.3%、cao 0.1%、fe2o30.5%、mgo 0.45%、k2o 4%、na2o 3%、l.o.i 3%。
[0094]
对比例3
[0095]
本对比例中各项条件与实施例3相同,不同之处在于:所述坯体由包括如下组分的原料压制得到:第一瓷砂9%,第二瓷砂6%,第三瓷砂7%,第四瓷砂8%,石粉42%,泥8%,第一黏土7%,第二黏土10%,碳酸钡助熔剂3%;
[0096]
所述第一瓷砂的化学组成如下:sio267%、al2o318%、tio20.5%、lio20.3%、cao 0.1%、fe2o30.5%、mgo 0.5%、k2o 4%、na2o 2.6%、l.o.i 6.5%;所述第二瓷砂的化学组成如下:sio271%、al2o318%、tio20.3%、cao 0.5%、zro20.3%、sno20.1%、fe2o30.6%、mgo 0.2%、k2o 2%、na2o 3%、l.o.i 4%;所述第三瓷砂的化学组成如下:sio273%、al2o315%、tio20.65%、bao 0.3%、cao 0.1%、fe2o30.5%、mgo 0.45%、k2o 4%、na2o 3%、l.o.i 3%;所述第四瓷砂的化学组成如下:sio265%、al2o324.2%、tio20.4%、cao 0.4%、mgo0.15%、k2o 1.95%、na2o 1.9%、l.o.i 6%。
[0097]
将实施例7和对比例1-3进行性能检测,具体的性能检测参数如下表3所示:
[0098]
表3
[0099][0100][0101]
测定自然石纹中的各个颜色后将其作为标准值,再测定仿自然石瓷砖中实施例7和对比例1-3的仿石纹颜色,计算得到检测值和标准值之间的差值,评价发色效果为a级时,即表示各个颜色的差值均≤0.3,b级为各个颜色的差值均≤0.6,c级为各个颜色的差值均≤1,最终得到仿自然石瓷砖的发色效果。上述烧结缺陷是具体包括成品仿自然石瓷砖是否存在“黑心”和变形的缺陷。
[0102]
从表3的测试结果可以看出,仿自然石瓷砖在采用了3种复合形成的瓷砂组分后,对于瓷砖的发色效果、白度和机械强度均有一定程度的改善,而当瓷砂的组分调整为两种或四种复配时,均不能达到对仿自然石瓷砖的发色效果、白度和机械强度同时起到改善效果。
[0103]
实施例8
[0104]
本实施例中各项条件与实施例7相同,不同之处在于:所述助熔剂由b2o3和baf2复配而成,b2o3和baf2的质量比为4:1。
[0105]
实施例9
[0106]
本实施例中各项条件与实施例7相同,不同之处在于:仿自然石瓷砖的厚度为
28mm。
[0107]
实施例10
[0108]
本实施例中各项条件与实施例8相同,不同之处在于:仿自然石瓷砖的厚度为28mm。
[0109]
将实施例8-10进行性能检测,具体的性能检测参数如下表4所示:
[0110]
表4:
[0111][0112][0113]
根据上述检测结果可知,仿自然石瓷砖在采用了由b2o3和baf2复配而成的助熔剂后,在瓷砖厚度增大的情况下,仍可以保持较好的发色效果,并且不存在烧结缺陷;而使用常规的助熔剂时,在厚度增大的情况下,瓷砖的烧结缺陷越来越明显。
[0114]
以上所述仅为本技术的优选实施例,并非因此限制本技术的专利范围,凡是在本技术的发明构思下,利用本技术说明书及附图内容所作的等效结构变换,或直接/间接运用在其他相关的技术领域均包括在本技术的专利保护范围内。