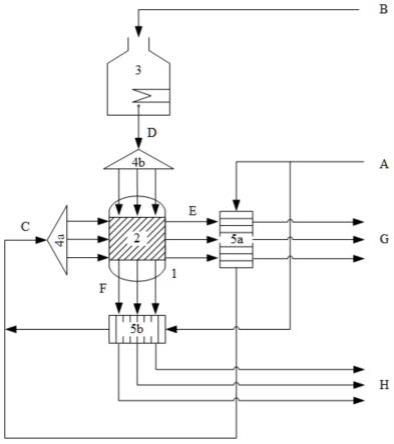
1.本发明涉及一种烃类重整制氢反应系统及甲烷水蒸气重整制氢的方法,以及甲烷水蒸气重整制氢的方法。
背景技术:2.氢气在现代化学工业中发挥着极其重要的作用。合成氨工业、甲醇工业、炼油工业都需要氢气作为原料。尤其在原油品质不断降低,而对成品油要求不断提高的趋势下,炼厂加氢任务增重,氢气需求量增大。另一方面,随着环境污染的加剧和能源危机的到来,氢能源以其燃烧热值高、清洁环保等优点受到极大关注。然而氢气沸点低、不易压缩和液化、易燃易爆,从而难于大量储存和运输。因此,为解决上述问题需要发展以化学方法现场制取氢气的方法。
3.烃类水蒸气重整制氢一直是几十年来工业广泛采用的氢气制备方法。然而,蒸汽重整条件苛刻,传统的天然气水蒸气重整制氢反应器体积庞大、效率低、能源消耗大,不能满足分布式制氢的技术要求。近年来,微尺度反应器作为一项新兴的技术得到越来越多的认可,dupont、basf、bayer、degussa等公司一直致力于推动和促进微尺度反应器。微尺度反应器是指反应器内流体流动通道在三维空间的其中一维方向上的尺寸在几十微米~几毫米尺度的反应器。微通道反应器体积小、传热效率高、响应时间短、温度分布均匀,且可通过增加反应通道数目实现灵活的数量放大以适应不同的生产规模,特别适用于高效、分散式生产氢气。
4.尽管各国研究者已对微通道反应器进行了大量研究,但由于蒸气重整通常在900℃,1-20atm的苛刻条件下进行,催化剂需定期更换再生,因此微通道反应器技术运用于蒸汽重整制氢仍然存在许多障碍。通常的微通道反应器使用黏附于反应器壁面的催化剂薄层,在蒸汽重整所要求的长时间高温操作和启停过程的升温降温中,微通道反应器的催化剂薄层易出现侵蚀和脱落。而且,通常的微通道反应器通过焊接、烧结等方式将多个相同的反应通道组合成为反应器核心实现生产放大,往往结构复杂,加工难度大,且催化剂难以更换再生。
技术实现要素:5.本发明的主要目的在于提供一种烃类重整制氢反应系统及其应用,以克服现有技术中烃类重整制氢反应器结构复杂,加工难度大,且催化剂难以更换再生的缺陷。
6.为了达到上述目的,本发明提供了一种烃类重整制氢反应系统,包括:
7.重整装置,该重整装置内设置有多个反应通道,多个催化剂板分别可装卸的设置于多个该反应通道内;该重整装置内设置有多个热流体通道,多个该热流体通道与多个该反应通道交错层叠设置;
8.热流体供应装置,连接于该重整装置的多个该热流体通道。
9.本发明所述的烃类重整制氢反应系统,其中,多个该反应通道沿第一方向贯穿该
重整装置,多个该热流体通道沿第二方向贯穿该重整装置,该第一方向与该第二方向交叉。
10.本发明所述的烃类重整制氢反应系统,其中,所述反应通道沿第三方向具有一最小尺寸,该最小尺寸小于6mm;该第三方向与该第一方向和该第二方向垂直;该第一方向与该第二方向垂直,所述反应通道在该第二方向具有两侧壁,该两侧壁上分别设置有定位槽,用于定位该催化剂板;所述催化剂板在该第二方向上具有一宽度,该宽度大于两该侧壁之间的距离、小于两该定位槽之间的距离。
11.本发明所述的烃类重整制氢反应系统,其中,所述热流体通道沿该第三方向具有一最小尺寸,该最小尺寸不大于2.5mm;所述反应通道和所述热流体通道的间距为小于或等于5mm。
12.本发明所述的烃类重整制氢反应系统,其中,该定位槽沿该第一方向的末端设置有阻挡结构,以定位该催化剂板。
13.本发明所述的烃类重整制氢反应系统,其中,所述热流体通道包括中心腔室和位于该中心腔室两侧的侧腔室,所述中心腔室与两侧腔室通过狭缝连通。
14.本发明所述的烃类重整制氢反应系统,其中,所述两侧腔室与该反应通道相邻,所述狭缝沿该第一方向设置。
15.本发明所述的烃类重整制氢反应系统,其中,该反应系统还包括重整原料分布装置和热流体分布装置,重整原料经过该重整原料分布装置后进入重整反应器的反应通道,热流体通过该热流体分布装置后进入重整反应器的热流体通道。
16.本发明所述的烃类重整制氢反应系统,其中,该反应系统还包括第一热交换装置及/或第二热交换装置,该第一热交换装置分别连接反应通道和重整原料分布装置,重整原料进入第一热交换装置与反应通道中流出的重整气体进行热交换后,进入该重整原料分布装置;及/或该第二热交换装置连接热流体通道和重整原料分布装置,重整原料进入第二热交换装置与热流体通道中流出的废热流体进行热交换后,进入该重整原料分布装置。
17.本发明所述的烃类重整制氢反应系统,其中,所述催化剂板是fecral合金基板,基板两侧喷涂形成有过渡层,在过渡层上涂覆有多孔载体,在多孔载体上沉积有催化活性物质;所述多孔载体为γ-氧化铝,sio2,zro2中的一种或几种;所述催化活性物质为ni,rh,pt中的一种或几种。
18.为了达到上述目的,本发明还提供了一种甲烷水蒸气重整制氢的方法,该方法使用上述的烃类重整制氢反应系统进行。
19.本发明的有益效果:
20.本发明烃类重整制氢反应系统,将结构化催化剂板作为可更换插件,通过定位槽与重整装置主体装配,可实现催化剂板容易地更换再生。另外,将热流体供应装置与重整装置作为独立的组件,可以利用成熟的燃烧器技术和电加热技术为重整装置供热,便于根据不同生产规模集成和放大烃类重整制氢反应系统;同时,避免了集成式燃烧器-重整器内燃烧和重整反应速率难以匹配的问题,使该烃类重整制氢反应系统便于更换不同类型的重整催化剂,具有更大的生产灵活性。
附图说明
21.图1是本发明第一实施方式中烃类重整制氢反应系统的示意性流程图;
22.图2是本发明第一实施方式中重整装置的立体图;
23.图3是本发明第一实施方式中反应通道的截面图;
24.图4是本发明第一实施方式中烃类重整制氢反应系统的部分装配示意图;
25.图5是本发明第二实施方式中重整装置的立体图;
26.图6是本发明第二实施方式中反应通道的截面图;
27.图7是本发明第三实施方式中热流体通道的截面图。
28.其中,附图标记:
29.1 重整装置
30.2 催化剂板
31.3 热流体供应装置
32.4a 重整原料分布装置
33.4b 热流体分布装置
34.5a 第一热交换装置
35.5b 第二热交换装置
36.11 反应通道
37.12 热流体通道
38.13a 法兰
39.13b 法兰
40.14 定位槽
41.15 阻挡结构
42.20 重整装置
43.201 反应通道
44.202 热流体通道
45.203a 法兰
46.203b 法兰
47.204 定位槽
48.205 阻挡结构
49.212 中心腔室
50.213a 第一侧腔室
51.213b 第二侧腔室
52.214a 第一狭缝
53.214b 第二狭缝
54.a 重整原料
55.b 冷流体
56.c 重整原料
57.d 热流体
58.e 重整气体
59.f 废热流体
60.g 重整气体
61.h 废热流体
62.l 中轴线
具体实施方式
63.以下对本发明技术方案进一步进行详细描述,未特别说明的结构皆为本领域常规结构。
64.图1是本发明第一实施方式中烃类重整制氢反应系统的示意性流程图;图2是本发明第一实施方式中重整装置的立体图;图3是本发明第一实施方式中反应通道的截面图;图4是本发明第一实施方式中烃类重整制氢反应系统的部分装配示意图。
65.请参照图1至图4,本发明烃类重整制氢反应系统,包括重整装置1、热流体供应装置3、热流体分布装置4b和重整原料分布装置4a。另外,本发明烃类重整制氢反应系统还可以包括第一热交换装置5a和第二热交换装置5b。
66.请参照图2和图4,重整装置1可以为圆柱体、立方体等,本发明不作特别限定。重整装置1的材质可选为2520不锈钢,钛,镍等及其合金,蒙乃尔合金,英科耐尔合金等。重整装置1内设置有多个反应通道11,该多个反应通道11可以分组设置,本发明不特别限定反应通道11的数量,可以为4个,8个,12个等,本实施例中反应通道11的数量为5个。催化剂板2分别可装卸的设置于多个该反应通道11内,例如每个反应通道11内设置1个催化剂板2,但本发明不以此为限;该重整装置1内还设置有多个热流体通道12,该多个热流体通道12可以分组设置,本发明不特别限定热流体通道12的数量,可以为4个,8个,12个等,本实施例中热流体通道12的数量为5个。多个该热流体通道12与多个该反应通道11交错层叠设置,形成错流换热结构。
67.详细而言,多个反应通道11沿第一方向贯穿重整装置1,多个热流体通道12沿第二方向贯穿重整装置1,第一方向与第二方向交叉。例如第一方向和第二方向形成一角度θ,θ可以为锐角、钝角或直角。在本实施方式中,θ为直角,但本发明不以此为限。
68.本实施例中,反应通道11沿第三方向具有一最小尺寸,第三方向与该第一方向和该第二方向垂直。多个该热流体通道12与多个该反应通道11沿第三方向交替层叠排列。在一实施方式中,反应通道11和热流体通道12的间距为小于或等于5mm,在一实施方式中,该间距小于或等于2mm,该间距例如为反应通道11和热流体通道12在第三方向上的距离,更进一步地例如为反应通道11中轴线和热流体通道12中轴线之间的距离。
69.在一实施方式中,反应通道11截面形状可为圆形、长方形,优选为长方形,该截面指反应通道11沿第三方向上的截面;反应通道11沿第三方向的最小尺寸小于6mm,在一实施方式中,该最小尺寸小于3mm,在另一实施方式中,该最小尺寸不大于2.5mm。本发明不特别限定该截面的长和款,例如长度为2.4cm,宽度为2.8mm,该长度为该截面沿第二方向的尺寸,该宽度为该截面沿该第一方向的尺寸。
70.在一实施方式中,热流体通道12可位于两个反应通道11之间;本发明不特别限定热流体通道12的截面形状,可为长方形、正方形或圆形,该截面例如为热流体通道12沿第三方向的界面;热流体通道高度不大于2.5mm,优选不大于1mm;热流体通道长度不大于10cm。
71.请同时参照图3,在本实施方式中,第一方向与第二方向垂直,反应通道11在第二方向(即热流体流动方向)具有两侧壁,该两侧壁上分别设置有定位槽14,用于定位该催化
剂板2;定位槽14例如为两侧壁分别继续凹陷形成的槽状结构,定位槽沿第三方向上具有一高度,该高度略大于催化剂板2的厚度。催化剂板2在该第二方向上具有一宽度,该宽度大于两该侧壁之间的距离、小于两该定位槽之间的距离。催化剂板2插入反应通道11后,反应通道11被分为互为镜像的上下两部分,每部分高度(沿第三方向距离)小于1mm,用于进行蒸汽重整反应。
72.在本实施方式中,定位槽14沿第一方向的末端设置有阻挡结构15,以定位该催化剂板2,具体为在更换催化剂板2时,保证催化剂板顺利设置于重整装置1内。
73.本发明中,催化剂板可以是fecral合金基板,其两侧通过热喷涂或等离子体喷涂形成过渡层,在过渡层上涂覆有多孔载体,在多孔载体上沉积催化活性物质;催化剂板上也可设置有帮助流体均布的预制结构。
74.在一实施方式中,fecral合金基板上通过热喷涂或等离子体喷涂形成的过渡层可为α-氧化铝纳米颗粒或其他金属、非金属氧化物的纳米颗粒形成的薄层,过滤层厚度可以为0.05mm至0.5mm。多孔载体包括γ-氧化铝,sio2,zro2等,多孔载体可具有30%至99%的孔隙率;多孔载体上负载的催化活性物质可以是ni,rh,pt等一切具有水蒸气重整反应催化活性的催化剂及它们之间的组合。
75.本发明中,催化剂板还可以是薄层的泡沫状金属,纤维状金属毡或絮状金属压制而成的薄片,其上涂覆有多孔载体,在多孔载体上沉积催化活性物质。薄层的泡沫状金属,纤维状金属毡或絮状金属压制而成的薄片可具有60%至95%的孔隙率。
76.本发明中,催化剂板厚度(即沿第三方向上催化剂板的尺寸)不大于5mm,优选不大于2mm,宽度不大于10cm,长度(即催化剂板贯穿重整装置的方向)可为1
–
25cm。
77.本实施例中,烃类重整制氢反应系统还包括热流体供应装置3,用于提供温度为750℃至1200℃的热流体。热流体供应装置3可以是但不限于催化燃烧器,非催化燃烧器,电加热器以及它们的组合,热流体供应装置3的热流体出口数目为一个或数个;催化燃烧器和非催化燃烧器所使用的燃料可为任何现场易获得的燃料,氧化剂可为空气或氧气。
78.热流体供应装置3与热流体分布装置4b连接,热流体分布装置4b与重整装置1连通,具体与重整装置1的多个热流体通道12连通。在一实施方式中,重整装置1通过法兰13b与热流体分布装置4b连接。冷流体b经过热流体供应装置3加热后形成热流体d,通入热流体分布装置4a中,以使热流体d分布均匀地输送至重整装置1中的所有反应通道11内。热流体分布装置4b的结构可以为一种渐扩式的接头,或者为单层或多层的多孔筛状流体分布板,或者为其他有效的流体分布结构。
79.本实施方式中,烃类重整制氢反应系统还包括重整原料分布装置4a,与重整装置1连接,具体与重整装置1的多个反应通道11连通。在一实施方式中,重整装置1通过法兰13a与重整原料分布装置4a连接。重整原料c首先输入重整原料分布装置4a中,以使重整原料c均匀分布,然后再输入重整装置1的多个反应通道11内,在反应通道11内的催化剂板2上的催化剂催化作用下,在热流体d的加热作用下,重整原料进行反应,得到重整气体e。热流体分布装置4a的结构可以为一种渐扩式的接头,或者为单层或多层的多孔筛状流体分布板,或者为其他有效的流体分布结构。
80.本发明安装于重整装置1上的重整原料分布装置4a和热流体分布装置4b的数目视热流体和重整原料待分布面积大小,为一个或数个。
81.重整装置1的反应通道11还可以与第一热交换装置5a连通,第一热交换装置5a与重整原料分布装置4a连通,重整原料a和重整气体e分别通入第一热交换装置5a中进行换热,即得到预热后的重整原料c和被冷却的重整气体g。
82.重整装置1的热流体通道12还可以与第二热交换装置5b连通,第二热交换装置5b与重整原料分布装置4a连通,重整原料a和热流体通道12流出的废热流体f分别通入第二热交换装置5b中进行热交换,即得到预热后的重整原料c和被冷却的废热流体h。
83.本发明并不特别限定第一热交换装置5a和第二热交换装置5b的具体类型,可以为任何已有的板式、螺旋片式或管式换热器。
84.图5是本发明第二实施方式中重整装置的立体图;图6是本发明第二实施方式中反应通道的截面图。本发明第二实施方式与第一实施方式的差异在于:本发明第二实施方式中,重整装置20设置有4组反应通道201,每组反应通道201的数量为5个,重整装置1通过法兰203a与重整原料分布装置42连接;重整装置20设置有2组热流体通道202,每组热流体通道202的数量为6个,每组热流体通道202与每2组反应通道201交错层叠设置,形成错流换热结构。反应通道201设置有定位槽204和阻挡结构205,定位槽204和阻挡结构205的设置方式与第一实施方式相同,于此不再赘述。
85.图7是本发明第三实施方式中热流体通道的截面图。本发明第三实施方式与第一实施方式的差异在于:本发明第三实施方式中,热流体通道202具有分层结构,例如热流体通道202包括中心腔室212和位于该中心腔室212两侧的第一侧腔室213a和第二侧腔室213b,中心腔室212沿第三方向的两侧壁面上沿热流体流动方向分布若干第一开口214a和若干第二开口214b,该开口可以为圆形或狭长的长方形,中心腔室212与第一侧腔室213a和第二侧腔室213b分别通过该第一开口214a和第二开口214b与第一侧腔室213a和第二侧腔室213b连通,第一侧腔室213a和第二侧腔室213b分别与反应通道11毗邻。
86.本实施例中,中心腔室212设置有热流体进口,该热流体进口与热流体分布装置4a连通;第一侧腔室213a和第二侧腔室213b分别设置有热流体出口,该热流体出口与第二热交换装置5b连通。如此,热流体经中心腔室212的热流体进口进入,通过第一开口214a和第二开口214b进入两侧第一侧腔室213a和第二侧腔室213b,为反应通道11内进行的蒸汽重整反应均匀供热,废热流体经两侧第一侧腔室213a和第二侧腔室213b的热流体出口流出。
87.本发明烃类重整制氢反应系统的操作方法例如为:冷流体b进入热流体供应装置3进行加热得到热流体d,热流体d经热流体分布装置4b均匀分布后进入重整装置1的热流体通道12。预热后的重整原料c通过重整原料分布装置4a均匀分布后,进入重整装置1的反应通道11,在催化剂板2的催化作用下以及热流体的加热作用下进行重整反应,得到重整气体e从反应通道11流出,废热流体从热流体通道12流出。从重整装置1流出的重整气体e可以通入第一热交换装置5a中对重整原料a进行预热,从重整装置1流出的废热流体f可以通入第二热交换装置5b中对重整原料a进行预热。
88.本发明烃类重整制氢反应系统可以用于甲烷蒸汽重整制氢。重整原料气体为甲烷和水蒸汽的混合物,体积比例1:1~1:3,重整气体在反应通道11内的停留时间为1ms至500ms,反应温度750~900℃,反应压力1~20atm,甲烷转化率95%~99%,氢气选择性75%~82%。
89.由此,本发明提供一种烃类重整制氢反应系统,利用组件的模块化组合,提升烃类
重整制氢的灵活性和适应性,催化剂稳定、易更换再生,降低设备加工制造难度,从而克服了传统微通道反应器的固有缺点,特别适合于各种分布式制氢场合。
90.下面以甲烷水蒸气重整反应为例,结合本发明烃类重整制氢反应系统,对重整制氢方法进一步进行说明。
91.实施例1:
92.将水蒸气和甲烷以压力1atm,体积比3的比例混合后形成重整原料a,进入第一热交换装置5a与第二热交换装置5b,与重整气体e及废热流体f换热;换热后的重整原料c温度为450℃~850℃,经过带有渐扩型接口的重整原料分布装置4a,均匀分布后流入重整装置1的反应通道11,与插入反应通道11内的可更换结构化催化剂板2接触,发生甲烷水蒸气重整反应,在通道内的停留时间为20ms~40ms,ch4转化率为90%~95%,h2选择性为75%~80%。重整装置1的反应通道11流出重整气体e温度为850℃~900℃,组成包括h2、co、co2以及未反应的ch4、h2o;甲烷水蒸气重整反应所需的反应热由热流体提供,热流体供应装置(例如电热器)3提供的热流体d为热空气,其温度为1000℃~1050℃;热流体d经过带有渐扩型接口的热流体分布装置4b,均匀分布后流入重整装置1的热流体通道12,为重整反应供热,排出的废热流体f温度为900℃~950℃。其中重整气体e、废热流体f进入第一热交换装置5a、第二热交换装置5b与冷重整原料a换热,完成热量回收。回收热量后的重整气体g的温度为500℃~650℃,废热流体h温度为500℃~900℃,可进一步为公用工程供能。
93.该重整反应中,ch4转化率为95%~99%,h2选择性为78%~82%,重整装置1的反应通道11重整气体e温度为700℃~750℃,热流体通道12废热流体f温度为750℃~800℃;回收热量后的重整气体g的温度为450℃~600℃,废热流体h温度为450℃~750℃。
94.当然,本发明还可有其它多种实施例,在不背离本发明精神及其实质的情况下,熟悉本领域的技术人员可根据本发明作出各种相应的改变和变形,但这些相应的改变和变形都应属于本发明权利要求的保护范围。