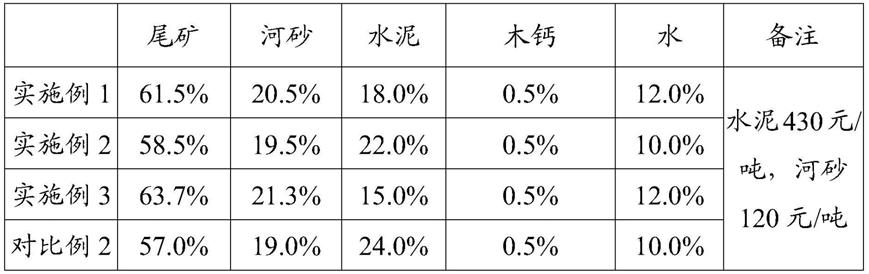
1.本发明涉及铁尾矿再利用技术领域,尤其涉及一种免蒸免烧尾矿砖及其制备方法。
背景技术:2.目前国内对铁矿尾矿的综合利用研究较多,发展较快,但由于工艺技术落后,尾矿综合利用率偏低,尚不具备大规模减少尾矿排放的条件,且多数矿山企业对铁矿尾矿的利用处理,只重视价值较高的有价金属的回收,往往又造成新的固体废弃物污染和环境生态问题,不能从根本上解决尾矿问题。资源利用率低、造成新的环境污染,是目前我国铁尾矿开发利用过程存在的突出问题。
3.矽卡岩式铁矿属接触交代-热液型矿床,按成分主要有两种类型,钙质矽卡岩型和镁质矽卡岩型。河北西部太行山区的铁尾矿属于镁质矽卡岩型,铁尾矿成分和性质较特殊,硅含量低(36~38%),且不含活性硅,镁含量高(30%以上),钙镁含量相差大,尾矿本身强度较低,加之尾矿自身的粒级较细,直接用作尾矿砖的骨料强度达不到国家标准要求。目前对低硅高镁型铁尾矿的研究较少,没有针对低硅高镁型铁尾矿产业化利用的途径。
技术实现要素:4.本发明的目的在于提供一种免蒸免烧尾矿砖及其制备方法,克服了低硅高镁型铁尾矿生产双免砖的难题,成本低廉、资源利用率高,并且对环境污染程度低,实现了低硅高镁型铁尾矿的资源化利用。
5.为了实现上述发明目的,本发明提供以下技术方案:
6.本发明提供了一种免蒸免烧尾矿砖,由固体原料、外加剂和水制备得到,所述固体原料的质量以100%计,所述固体原料包括低硅高镁型铁尾矿55~65%、水泥14~22%和余量的河砂;所述外加剂为木钙,所述木钙的质量为水泥质量的0.5%;所述水的质量为固体原料质量的10~12%;
7.所述低硅高镁型铁尾矿中硅的质量含量为37~39%,镁的质量含量在30%以上;所述低硅高镁型铁尾矿的粒径如表1所示;
8.表1所述低硅高镁型铁尾矿的粒径
9.粒级(mm)质量百分比(%)+0.903.76
‑
0.9+0.3027.84
‑
0.30+0.1541.32
‑
0.15+0.07516.20
‑
0.07510.88
10.。
11.优选的,所述固体原料包括低硅高镁型铁尾矿61.5%、水泥18.0%和余量的河砂。
12.优选的,所述低硅高镁型铁尾矿和河砂的质量比为3:1。
13.优选的,所述河砂的粒径小于3mm,sio2质量含量不低于85%。
14.优选的,所述水泥的标号为425#。
15.优选的,以质量百分含量计,所述低硅高镁型铁尾矿包括sio238.12%、mgo 31.76%、cao 8.43%、al2o32.17%、tfe 2.96%和zno 2.48%。
16.本发明提供了上述方案所述免蒸免烧尾矿砖的制备方法,包括以下步骤:将低硅高镁型铁尾矿、河砂和水泥混合,得到干混料;
17.将木钙分散到水中,将所得分散液和所述干混料混合,将所得混合料进行陈化,得到湿混料;
18.将所述湿混料置于模具中压制成型,脱模,得到砖坯;
19.将所述砖坯进行养护,得到免蒸免烧尾矿砖。
20.优选的,所述压制成型的压力为15mpa,保压时间为30s。
21.优选的,所述陈化的时间为30分钟。
22.优选的,所述养护包括:第1~7天为洒水养护,7天后自然养护至28天。
23.本发明提供了一种免蒸免烧尾矿砖,由固体原料、外加剂和水制备得到,所述固体原料的质量以100%计,所述固体原料包括低硅高镁型铁尾矿55~65%、水泥14~22%和余量的河砂;所述外加剂为木钙,所述木钙的质量为水泥质量的0.5%;所述水的质量为固体原料质量的10~12%;所述低硅高镁型铁尾矿中硅的质量含量为37~39%,镁的质量含量在30%以上;所述低硅高镁型铁尾矿的粒径如表1所示。
24.低硅高镁型铁尾矿本身强度低、颗粒细,本发明通过添加适量的河砂作为粗骨料,可以提高双免砖的强度,此外,河砂还作为增硅原料参与水泥的水化反应,通过水化反应增加双免砖的强度,所得双免砖的强度能达到mu10的水平,从而使低硅高镁型铁尾矿能够达到再利用。
25.本发明通过控制各原料的配比,在确保双免砖强度达到要求的前提下,最大程度的降低了河砂和水泥的用量,提高了铁尾矿的利用率,降低了双免砖的生产成本。
具体实施方式
26.本发明提供了一种免蒸免烧尾矿砖,由固体原料、外加剂和水制备得到,所述固体原料的质量以100%计,所述固体原料包括低硅高镁型铁尾矿55~65%、水泥14~22%和余量的河砂;所述外加剂为木钙,所述木钙的质量为水泥质量的0.5%;所述水的质量为固体原料质量的10~12%;
27.所述低硅高镁型铁尾矿中硅的质量含量为37~39%,镁的质量含量在30%以上;所述低硅高镁型铁尾矿的粒径如表1所示;
28.表1所述低硅高镁型铁尾矿的粒径
29.粒级(mm)质量百分比(%)+0.903.76
‑
0.9+0.3027.84
‑
0.30+0.1541.32
‑
0.15+0.07516.20
‑
0.07510.88
30.。
31.本发明提供的免蒸免烧尾矿砖,由固体原料、外加剂和水制备得到。
32.在本发明中,所述固体原料的质量以100%计,所述固体原料包括低硅高镁型铁尾矿55~65%,优选为57~63%,更优选为59~61.5%。在本发明中,所述低硅高镁型铁尾矿中硅的质量含量为37~39%,优选为37.5~38.5%,更优选为38.12%;镁的质量含量在30%以上,优选为30~40%,更优选为31.76%。在本发明中,以质量百分含量计,所述低硅高镁型铁尾矿优选包括sio238.12%、mgo 31.76%、cao 8.43%、al2o32.17%、tfe 2.96%和zno2.48%。余下未列出的部分为烧失量和少量的k2o、na2o、cuo、pbo、mno和s。在本发明中,所述tfe指的是全铁含量。
33.在本发明中,所述低硅高镁型铁尾矿主要是起骨料作用,是构成材料的主体构架与承担外部荷载的主要依托,在很大程度上决定着材料的力学性质、耐久性和经济性。
34.表1中所述
‑
0.15+0.075指的是粒径<0.15mm且≥0.075mm,其他粒级代表的含义以此类推,这里不再赘述。
35.在本发明中,所述固体原料的质量以100%计,所述固体原料包括水泥14~22%,优选为16~20%,更优选为18%。在本发明中,所述水泥的标号优选为425#,该标号的水泥后期强度增长较快,对硫酸盐类浸蚀的抵抗能力及抗水性较好。在本发明中,所述水泥作为胶凝材料,砖坯成型后短期内水泥通过水化反应生成水化硅酸钙、水化铝酸钙增加双免砖早期强度,此外水泥水化反应分解物与二氧化硅和活性氧化铝在水的参与下进行缓慢的化学反应,继续生成水化硅酸钙和水化铝酸钙,从而增加双免砖后期强度。
36.在本发明中,所述固体原料的质量以100%计,所述固体原料还包括余量的河砂。在本发明中,所述低硅高镁型铁尾矿和河砂的质量比优选为3:1。在本发明中,所述河砂的粒径优选小于3mm,更优选为大于0.075mm小于3mm;sio2质量含量优选不低于85%。在本发明中,所述河砂作为粗粒骨架组分,使双免砖的颗粒组成更加合理,同时作为双免砖的增硅原料,参与水泥的水化反应,增加双免砖的强度。
37.在本发明中,所述外加剂为木钙,所述木钙的质量为水泥质量的0.5%。本发明对所述木钙的来源没有特殊要求,采用本领域熟知的市售商品即可。在本发明中,所述木钙作为水泥的减水剂,对水泥颗粒有分散作用,减少用水量。本发明选择木钙作为减水剂,较其他减水剂不但可以减少水的用量,而且得到的双免砖的强度更高。
38.在本发明中,所述水的质量为固体原料质量的10~12%,优选为10.5~11.5%,更优选为10.8~11.2%。
39.本发明提供了上述方案所述免蒸免烧尾矿砖的制备方法,包括以下步骤:将低硅高镁型铁尾矿、河砂和水泥混合,得到干混料;
40.将木钙分散到水中,将所得分散液和所述干混料混合,将所得混合料进行陈化,得到湿混料;
41.将所述湿混料置于模具中压制成型,脱模,得到砖坯;
42.将所述砖坯进行养护,得到免蒸免烧尾矿砖。
43.本发明将低硅高镁型铁尾矿、河砂和水泥混合,得到干混料,本发明对所述混合的方式没有特殊要求,任意能够将三者混合均匀的方式均可。
44.得到干混料后,本发明将木钙分散到水中,将所得分散液和所述干混料混合,将所得混合料进行陈化,得到湿混料。
45.本发明对所述木钙的分散方式没有特殊要求,任意能够将木钙分散均匀的方式均可。本发明对所述分散液和干混料混合的方式没有特殊要求,能够将二者混合均匀即可。在本发明中,所述陈化的时间优选为30分钟。本发明通过陈化使各种物料充分渗透混合,使混合料水分均匀一致,减少成型时层裂的发生。
46.得到湿混料后,本发明将所述湿混料置于模具中压制成型,脱模,得到砖坯。在本发明中,所述压制成型的压力优选为15mpa,保压时间优选为30s。本发明通过控制成型压力能使物料之间结合紧密,提高砖坯的强度。在本发明中,所述压制成型优选在yes
‑
300压力机中进行,压制速率优选<0.5kn/s。得到砖坯后,本发明将所述砖坯进行养护,得到免蒸免烧尾矿砖。
47.在本发明中,所述养护优选包括:第1~7天为洒水养护,7天后自然养护至28天。在本发明中,所述洒水养护的条件优选为:养护温度为20
±
2℃,湿度>95%。
48.本发明在养护过程中,短期内水泥通过水化反应生成水化硅酸钙、水化铝酸钙增加双免砖早期强度,此外水泥水化反应分解物与二氧化硅和活性氧化铝(二氧化硅和活性氧化铝来源于铁尾矿和河砂)在水的参与下进行缓慢的化学反应,继续生成水化硅酸钙和水化铝酸钙,从而增加双免砖后期强度。
49.下面结合实施例对本发明提供的免蒸免烧尾矿砖及其制备方法进行详细的说明,但是不能把它们理解为对本发明保护范围的限定。
50.以下实施例和对比例所用低硅高镁型铁尾矿采自易县当地的于城铁矿尾矿库,以质量百分含量计,主要化学组成为:sio238.12%、mgo 31.76%、cao 8.43%、al2o32.17%、tfe 2.96%和zno 2.48%;粒径如表1所示;
51.河砂取自易县拒马河,经过筛分的河砂粒径大于0.075mm且小于3mm,sio2含量不低于85%;
52.水泥使用河北省满城县水泥厂生产的425#普通硅酸盐水泥。
53.实施例1~3
54.分别称取低硅高镁型铁尾矿、河砂、水泥、木钙和水,不同配方的具体含量见表2。
55.将低硅高镁型铁尾矿、河砂和水泥混合均匀,得到干料;
56.将称取好的木钙置于水中分散均匀,一并加入干料中,仔细搅拌至均匀,将获得的混合料陈化30分钟,得到湿混料;
57.将所述湿混料置于模具中,在压力机上压制成型,成型压力为15mpa,压制速率<0.5kn/s,保压30s,脱模后得到砖坯;
58.将所述砖坯在第1~7天进行洒水养护(养护温度为20
±
2℃,湿度>95%),7天后自然养护至28天,即得双免砖。
59.表2实施例1~3及对比例2的原料组成
[0060][0061]
表2中,尾矿、河砂和水泥作为固体原料,其中,尾矿、河砂和水泥的质量百分比指的是占固体原料的质量百分比,木钙的质量百分比指的是占水泥的质量百分比,水的质量百分比指的是占固体原料质量的百分比。
[0062]
对比例1
[0063]
与实施例1的不同之处仅在于将木钙替换为减水剂fdn。
[0064]
对比例2
[0065]
与实施例1的不同之处在于制备原料的配比。具体的配比见表2。
[0066]
性能测试
[0067]
依据gb/t 2542
‑
2012,对实施例1~3和对比例1~2制备的双免砖进行性能测试,结果见表3。
[0068]
表3实施例1~3及对比例1~2制备的双免砖的性能
[0069][0070]
由表2和表3的结果可知,本发明制得的双免砖符合mu10标准。由实施例1和对比例1的结果可知,本发明采用木钙作为减水剂,相比其他减水剂制得的双免砖具有更高的强度。由对比例2的结果可知,提高水泥用量,虽然能够提高双免砖的强度,但导致铁尾矿利用率降低、水泥用量增加,成产成本增加。
[0071]
由以上实施例和对比例可知,本发明通过控制双免砖各原料的种类及用量,克服了低硅高镁型铁尾矿生产双免砖的难题,成本低廉、资源利用率高,实现了低硅高镁型铁尾矿的资源化利用。
[0072]
以上所述仅是本发明的优选实施方式,应当指出,对于本技术领域的普通技术人员来说,在不脱离本发明原理的前提下,还可以做出若干改进和润饰,这些改进和润饰也应视为本发明的保护范围。