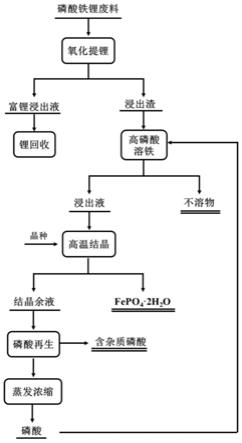
1.本发明属于电池废料资源回收技术领域,具体涉及一种磷酸铁锂电池废料制备高纯磷酸铁的方法。
背景技术:2.近年来,新能源产业发展迅猛,其中以锂离子电池的发展最引人注目。目前,锂离子电池在手机、电脑、新能源汽车、储能站等行业中应用较为广泛。磷酸铁锂锂离子电池由于安全性高,热稳定性好,价格低廉和污染小的优势倍受推崇,2019年我国磷酸铁锂仅用于电动客车动力电池的装机量就达到了13.8gwh。在磷酸铁锂被广泛应用的同时,大量的磷酸铁锂电池被报废淘汰,磷酸铁锂电池废料的数量飞速增长。
3.目前,磷酸铁锂电池废料的回收主要采用湿法回收工艺:一种是通过强酸浸出、除杂、中和沉淀等工序实现有价金属的综合回收;另一种是通过补充锂、铁、磷来实现磷酸铁锂电池的修复再生。中国发明专利申请cn 104362408a公开了一种磷酸铁锂电池废料综合回收再利用的方法,该方法首先高温处理磷酸铁锂电池废料的极片,然后分离磷酸铁锂和集流体铝箔,然后剥离下来的磷酸铁锂经过高温烘烤和筛分得到磷酸铁锂粉料,最后通过修复来再生磷酸铁锂正极材料。由于磷酸铁锂电池废料成分波动大,且再生材料纯度低、电学性能差,该方法并不能实现大宗磷酸铁锂电池废料的综合回收利用。中国发明专利申请cn 103280610a公开了一种磷酸铁锂电池正极片的回收方法,该方法首先采用碱溶处理磷酸铁锂正极片,得到含锂溶液和含磷酸铁的滤渣,含锂溶液可加入95℃饱和碳酸钠溶液,沉淀制备碳酸锂;滤渣先用混合酸溶解,使铁以磷酸铁沉淀形式存在并与炭黑等杂质分离。该方法酸碱消耗量大,且无法实现酸碱的再生循环利用,工艺成本高,还伴有大量废水及废渣产生,不利于磷酸铁锂电池废料的经济高效处理。
4.因此,开发一种简单、高效、绿色环保的磷酸铁锂电池废料的回收工艺,实现磷酸铁锂电池废料的资源化利用,具有重要的意义。
技术实现要素:5.针对现有技术磷酸铁锂电池废料的回收工艺中存在的工序繁杂、试剂消耗量大、试剂无法循环利用、成本高和回收得到的磷酸铁纯度低等问题,本发明提供了一种磷酸铁锂电池废料制备高纯磷酸铁的方法,该方法首先采用氧化提锂工艺分离富集磷酸铁锂电池废料中的有价金属锂,然后对浸出渣进行浓磷酸溶铁处理,反应结束后固液分离,得到不溶物和浸出液;浸出液稀释调ph,通过高温结晶制备高纯磷酸铁;结晶余液经过磷酸再生
‑
蒸发浓缩工艺实现初始磷酸的再生循环。该方法工艺流程短,无额外的中和剂、沉淀剂以及酸引入,成本低,对环境友好;制备得到高纯度的磷酸铁,可用于锂离子电池和陶瓷,催化剂等材料的制备,产品附加值高。
6.本发明的目的是通过以下技术方案实现的:
7.一种磷酸铁锂电池废料制备高纯磷酸铁的方法,包括以下步骤:
8.(1)氧化提锂:向待处理的磷酸铁锂电池废料中添加氧化剂和低浓度有机酸,反应结束后固液分离,得到富锂浸出液和主要物相为磷酸铁的浸出渣;
9.(2)浓磷酸溶铁:向前述浸出渣中加入高浓度磷酸,反应结束后,固液分离,得到不溶物和浸出液;
10.(3)高温结晶:向步骤(2)所述浸出液中加水进行稀释,后加入磷酸铁晶种和表面活性剂,在高温下完成磷酸铁的结晶,固液分离得到结晶余液和结晶产物,所述结晶产物干燥后得到磷酸铁;
11.(4)磷酸再生:采用膜分离工艺处理步骤(3)中所述结晶余液,控制进磷酸温度及压力和产磷酸流量,得到初步浓缩至质量分数为40
‑
60%的磷酸;
12.(5)蒸发浓缩:采用蒸发浓缩工艺进一步浓缩步骤(4)得到的磷酸,得到再生磷酸,返回步骤(2)循环利用。
13.进一步的,步骤(1)中所述磷酸铁锂电池废料包括废旧磷酸铁锂电池、废极片、磷酸铁锂废料中的一种或多种。
14.进一步的,步骤(1)中所述氧化剂包括过氧化氢或氧气。
15.进一步的,步骤(1)中所述有机酸包括柠檬酸、酒石酸、苹果酸中的一种或多种。
16.进一步的,步骤(2)中所述磷酸的浓度为3
‑
6mol/l。
17.进一步的,步骤(2)中所述浓磷酸溶铁的固液比为1:4
‑
1:10g/ml,反应温度控制在70
‑
95℃,搅拌转速设定为300
‑
500rpm,反应时间为0.5
‑
5h。
18.进一步的,步骤(3)中水的添加量为所述浸出液体积的1
‑
4倍,ph控制范围为1.2
‑
2.6。
19.进一步的,步骤(3)中所述磷酸铁晶种的添加量为步骤(2)所述浸出液中铁含量质量分数的10
‑
50%。
20.进一步的,步骤(3)中所述表面活性剂的种类包括ctab、sds、sdbs中的一种,添加量为步骤(2)所述浸出液中铁含量质量分数的0.1
‑
0.5%。
21.进一步的,步骤(3)中所述结晶的温度为85
‑
95℃,时间为1
‑
12h,搅拌转速为150
‑
400rpm。
22.进一步的,步骤(3)中所述结晶产物在60℃烘箱中干燥8h后得到磷酸铁。
23.进一步的,步骤(4)中所述膜分离工艺包括微滤、超滤、纳滤、双极膜、反渗析、电渗析中的一种或多种联合工艺。
24.进一步的,步骤(4)中所述进磷酸温度为25
‑
75℃,进磷酸压力为1.2
‑
4.0mpa,产磷酸流量控制为40
‑
150l/h。
25.进一步的,步骤(5)中所述蒸发浓缩工艺采用mvr蒸发器或多效蒸发器,磷酸浓缩后质量分数为65
‑
85%。
26.本发明技术方案的实现原理如下:
27.本发明所述方法的步骤(2)中,浓磷酸溶铁通过高浓度磷酸与氧化提锂浸出渣中磷酸铁反应生成铁磷酸式盐,实现铁的溶出与其他杂质高效分离,发生的主要反应为:
[0028][0029]
2fepo4+h3po4→
fe2hpo
44+
+2hpo
42
‑
ꢀꢀꢀꢀꢀꢀꢀꢀꢀꢀꢀꢀꢀꢀꢀꢀꢀꢀꢀꢀꢀ
(2)
[0030]
fepo4+h3po4→
fehpo
4+
+h2po4‑
ꢀꢀꢀꢀꢀꢀꢀꢀꢀꢀꢀꢀꢀꢀꢀꢀꢀꢀꢀꢀꢀꢀꢀꢀ
(3)
[0031][0032]
步骤(3)中在1.2≤ph≤2.6范围中结晶,利用磷酸铁在高温中溶解度低,容易析出的特性实现高纯磷酸铁的制备。制备得到磷酸铁中铁含量的质量分数范围为29.2
‑
30%,磷含量的质量分数为16.5
‑
17%。其中发生的主要反应为:
[0033][0034]
步骤(4)在磷酸再生时,采用膜分离技术利用不同膜的分离性能脱除杂质元素,可用于提锂操作,进一步提高了本发明的综合经济效益。
[0035]
由上述技术方案可以看出:本发明所提供的利用磷酸铁锂电池废料制备高纯磷酸铁的方案,高效分离富集了有价金属锂,利用了磷酸铁可溶于高浓度磷酸的特性和磷酸铁在温度升高时溶解度降低的性质,实现磷酸铁锂电池废料中铁的溶出和高纯磷酸铁的制备。结晶余液还可通过磷酸再生
‑
蒸发浓缩实现浸出剂磷酸的再生循环利用。该方法灵活运用磷酸铁溶解特性,全流程仅需少量补充磷酸,无其他试剂引入,实现磷酸铁锂电池废料的高效经济回收利用,工艺流程简单,资源利用率高,对环境影响小。本发明灵活运用磷酸铁锂在高浓度磷酸中的溶解特性和磷酸铁溶解度随温度升高降低的性质,解决了磷酸铁锂电池废料造成的环境污染和资源浪费问题,为磷酸铁锂电池废料的高效经济回收利用提供了新思路。
[0036]
与现有技术相比,本发明技术方案具有如下技术优势或积极效果:
[0037]
(1)本发明所述方法原料适应性强,废旧磷酸铁锂电池、废极片、磷酸铁锂废料等均可作为本发明技术方案中的原料;
[0038]
(2)本发明所述方法试剂消耗量少,无需额外的中和剂和沉淀剂,同时可实现高效分离富集有价金属锂;
[0039]
(3)本发明充分利用磷酸铁锂废料中的铁、磷资源生产高纯磷酸铁,全流程磷酸可再生循环利用,磷酸补充量极少,工艺成本低,环境友好度高;
[0040]
(4)本发明工艺流程简单,磷酸铁产品附加值高,适合大宗磷酸铁锂电池废料的回收处理。
附图说明
[0041]
为了更清楚地说明本发明实施例的技术方案,下面将对实施例描述中所需要使用的附图作简单地介绍,显而易见地,下面描述中的附图仅仅是本发明的一些实施例,对于本领域的普通技术人员来讲,在不付出创造性劳动的前提下,还可以根据这些附图获得其他附图。
[0042]
图1为本发明所述的磷酸铁锂电池废料制备高纯磷酸铁的工艺流程图。
[0043]
图2为本发明实施例1所制备的磷酸铁微观形貌图。
具体实施方式
[0044]
为使本发明的目的、技术方案和优点更加清楚,下面将对本发明实施方式作进一步地详细描述。
[0045]
实施例1
[0046]
如图1所示,一种磷酸铁锂电池废料制备高纯磷酸铁的方法,包括:向磷酸铁锂电池废料中添加过氧化氢和少量酒石酸,完成氧化提锂,得到富锂浸出液和浸出渣;然后向浸出渣中添加4mol/l的磷酸,固液比为:1:4g/ml,反应温度控制为85℃,时间为2h,搅拌转速设定为500rpm;固液分离,得到不溶物和浸出液。向浸出液中添加1倍体积的水进行稀释,体系ph维持在1.2,并添加10%的磷酸铁作为晶种和铁含量为0.1%的ctab作为表面活性剂,结晶温度为95℃,时间为6h,搅拌转速为150rpm;结晶结束后,固液分离,结晶产物在60℃烘箱中干燥8h后得到二水磷酸铁,制备得到的磷酸铁微观形貌见图2。结晶余液采用超滤
‑
双极膜
‑
电渗析联合工艺实现磷酸再生,再生条件为:进磷酸温度为75℃,进磷酸压力为4.0mpa,产磷酸流量为150l/h,磷酸浓度为45%。通过超滤实现大粒径杂质离子的脱除,然后利用电渗析与双极膜结合工艺实现锂离子的高效分离和磷酸的初步浓缩。膜分离制备得到的磷酸采用多效蒸发器进行蒸发浓缩,得到浓度为65%的磷酸,可继续循环利用。
[0047]
实施例2
[0048]
如图1所示,一种磷酸铁锂电池废料制备高纯磷酸铁的方法,包括:向磷酸铁锂电池废料中添加少量柠檬酸并通入氧气,完成氧化提锂,得到富锂浸出液和浸出渣;然后向浸出渣中添加5mol/l的磷酸,固液比为:1:6g/ml,反应温度控制为90℃,时间为4h,搅拌转速设定为500rpm;固液分离,得到不溶物和浸出液。向浸出液中添加1倍体积的水进行稀释,体系ph维持在1.8,并添加20%的磷酸铁作为晶种和铁含量为0.5%的sdbs作为表面活性剂,结晶温度为95℃,时间为12h,搅拌转速为150rpm;结晶结束后,固液分离,结晶产物在60℃烘箱中干燥8h后得到二水磷酸铁,磷酸铁中铁含量为29.6%,磷含量为16.5%。结晶余液采用超滤
‑
纳滤结合联合工艺实现磷酸再生,再生条件为:进磷酸温度为30℃,进磷酸压力为1.8mpa,产磷酸流量为120l/h,磷酸浓度为40%。采用超滤实现大粒径杂质离子的脱除,然后利用纳滤工艺达到磷酸净化浓缩的目的。膜分离制备得到的磷酸采用mvr蒸发器进行蒸发浓缩,得到浓度为85%的磷酸,可继续循环利用。
[0049]
实施例3
[0050]
如图1所示,一种磷酸铁锂电池废料制备高纯磷酸铁的方法,包括:向磷酸铁锂电池废料中添加过氧化氢和少量柠檬酸,完成氧化提锂,得到富锂浸出液和浸出渣;然后向浸出渣中添加6mol/l的磷酸,固液比为:1:8g/ml,反应温度控制为70℃,时间为5h,搅拌转速设定为400rpm;固液分离,得到不溶物和浸出液。向浸出液中添加4倍体积的水进行稀释,体系ph维持在2.6,并添加50%的磷酸铁作为晶种和铁含量为0.2%的sdbs作为表面活性剂,结晶温度为90℃,时间为1h,搅拌转速为300rpm;结晶结束后,固液分离,结晶产物在60℃烘箱中干燥8h后得到二水磷酸铁。结晶余液采用纳滤工艺脱除杂质元素实现磷酸再生,再生条件为:进磷酸温度为25℃,进磷酸压力为2.5mpa,产磷酸流量为80l/h,磷酸浓度为60%。膜分离制备得到的磷酸采用mvr蒸发器进行蒸发浓缩,得到浓度为85%的磷酸,可继续循环利用。
[0051]
实施例4
[0052]
如图1所示,一种磷酸铁锂电池废料制备高纯磷酸铁的方法,包括:向磷酸铁锂电池废料中添加过氧化氢和少量苹果酸,完成氧化提锂,得到富锂浸出液和浸出渣;然后向浸出渣中添加3mol/l的磷酸,固液比为:1:10g/ml,反应温度控制为95℃,时间为0.5h,搅拌转速设定为350rpm;固液分离,得到不溶物和浸出液。向浸出液中添加3倍体积的水进行稀释,
体系ph维持在1.5,并添加40%的磷酸铁作为晶种和铁含量为0.4%的sds作为表面活性剂,结晶温度为90℃,时间为6h,搅拌转速为400rpm;结晶结束后,固液分离,结晶产物在60℃烘箱中干燥8h后得到二水磷酸铁。结晶余液采用双极膜
‑
电渗析联合工艺实现磷酸再生,再生条件为:进磷酸温度为60℃,进磷酸压力为1.2mpa,产磷酸流量为40l/h,磷酸浓度为60%。在电场作用下,锂离子和磷酸根实现高效分离。膜分离制备得到的磷酸采用多效蒸发器进行蒸发浓缩,得到浓度为85%的磷酸,可继续循环利用。
[0053]
实施例5
[0054]
如图1所示,一种磷酸铁锂电池废料制备高纯磷酸铁的方法,包括:向磷酸铁锂电池废料中添加少量酒石酸并通入氧气,完成氧化提锂,得到富锂浸出液和浸出渣;然后向浸出渣中添加6mol/l的磷酸,固液比为:1:10g/ml,反应温度控制为90℃,时间为1h,搅拌转速设定为300rpm;固液分离,得到不溶物和浸出液。向浸出液中添加2倍体积的水进行稀释,体系ph维持在2.2,并添加40%的磷酸铁作为晶种和铁含量为0.5%的ctab作为表面活性剂,结晶温度为85℃,时间为6h,搅拌转速为200rpm;结晶结束后,固液分离,结晶产物在60℃烘箱中干燥8h后得到二水磷酸铁,磷酸铁中铁含量为29.8%,磷含量为16.6%。结晶余液采用反渗析
‑
超滤联合工艺实现磷酸再生,再生条件为:进磷酸温度为30℃,进磷酸压力为3.0mpa,产磷酸流量为130l/h,磷酸浓度为54%。膜分离制备得到的磷酸采用mvr蒸发器进行蒸发浓缩,得到浓度为85%的磷酸,可继续循环利用。
[0055]
综上可见,本发明实施例使用高浓度磷酸处理磷酸铁锂电池废料,实现磷酸铁锂电池废料中铁的溶出,浸出液高温结晶制备高纯磷酸铁,结晶余液通过磷酸再生
‑
蒸发浓缩工艺实现磷酸的再生循环利用,全流程无中和剂、沉淀剂的引入,同时高效分离富集了有价金属锂,为磷酸铁锂电池废料的高效利用和工业应用提供了新思路。
[0056]
以上所述,仅为本发明较佳的具体实施方式,但本发明的保护范围并不局限于此,任何熟悉本技术领域的技术人员在本发明揭露的技术范围内,可轻易想到的变化或替换,都应涵盖在本发明的保护范围之内。因此,本发明的保护范围应该以权利要求书的保护范围为准。