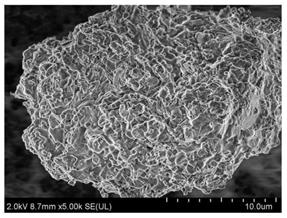
1.本发明涉及工业固废综合利用技术领域,尤其涉及一种以工业固废制备尾矿坝导渗材料的方法。
背景技术:2.目前,由于工业发展快速,会产生大量的工业固废,比如火电厂的高炉粉煤灰、钢铁企业的高铁铁渣、铅锌生产中的铅锌废渣和化工企业中产生的废盐渣等,这些固废具有粉尘颗粒多、颗粒细小,且会含有重金属离子,易形成粉尘污染、地下水污染和土壤污染等,大多数企业为了回收这些固废耗费了大量的成本,且回收率低下,回收效果不好,占用大量土地资源,造成有价资源的严重浪费,所以对这些工业固废进行综合利用并制备生产高值化产品已经是必由之路。
3.同时,目前大多数的工业尾矿坝使用的尾矿导水材料为立体有机网材料,其价格不低于150元/m2,由于全国尾矿坝使用量极大,不仅给矿场企业带来很高的成本,长期大量使用后对土地环境会造成严重的污染。
4.因此,目前急需一种稳定性好、环境友好且价格低廉的无机导渗材料。而上述的这些固废资源中含有氧、硅、铝、铁、钠、锌、钙和氯等的固废粉尘具有颗粒度小,烧结成型后结构稳定、强度高,耐酸碱腐蚀性好等特点,可以通过球磨、筛分、造粒和烧结等技术加工成一定粒度的导渗材料并用于尾矿坝的尾矿导水材料中。
技术实现要素:5.本发明的目的在于提供一种以工业固废制备尾矿坝导渗材料的方法,所述方法制备得到的尾矿坝导渗材料的抗压强度高、耐酸碱性好,使用损失率低,可反复循环使用以及环境友好。
6.为了实现上述发明目的,本发明提供以下技术方案:
7.本发明提供了一种以工业固废制备尾矿坝导渗材料的方法,包括以下步骤:
8.将工业固废、粘结剂和水混合后,依次进行压球造粒、脱水处理、预热、烧结和退火,得到尾矿坝导渗材料;
9.所述工业固废包括高炉粉煤灰、工业铁渣、煤矸石、工业废盐和铅锌渣中的至少两种。
10.优选的,所述工业固废的粒度≤150μm。
11.优选的,所述高炉粉煤灰、工业铁渣、煤矸石、工业废盐和铅锌渣的质量比为(0~50):(0~30):(0~40):(0~30):(0~40);
12.且所述高炉粉煤灰、工业铁渣、煤矸石、工业废盐和铅锌渣中的至少两种的用量不同时为0。
13.优选的,所述工业固废中工业废盐的用量不为0。
14.优选的,所述粘结剂、水与工业固废的质量比为(20~50):(5~15):100;
15.所述粘结剂的粒度≤150μm。
16.优选的,所述脱水处理的温度≥100℃,时间≥2h;
17.所述脱水处理后得到的物料的含水量为2~8%。
18.优选的,所述预热的温度为200~600℃,时间为1~4h。
19.优选的,所述烧结的温度为900~1100℃,时间为2~5h。
20.优选的,所述退火的温度为500~800℃,时间为1~4h。
21.优选的,所述高炉粉煤灰中al的质量百分含量≥15%;
22.所述工业铁渣中fe的质量百分含量≤20%;
23.所述煤矸石中al的质量百分含量≤20%;
24.所述工业废盐中的有机物含量≤6%;
25.所述铅锌渣包括si和al;
26.所述si和al的总量在铅锌渣中的质量百分比≥75%;
27.所述si和al的质量比为1.2:1;所述铅锌渣中的si和al的含量分别以si和al的氧化物的含量计。
28.本发明提供了一种以工业固废制备尾矿坝导渗材料的方法,包括以下步骤:将工业固废、粘结剂和水混合后,依次进行压球造粒、脱水处理、预热、烧结和退火,得到尾矿坝导渗材料;所述工业固废包括高炉粉煤灰、工业铁渣、煤矸石、工业废盐和铅锌渣中的至少两种。本发明采用各种工业固废依次经过预热、烧结和退火处理制备得到的尾矿坝导渗材料与目前尾矿坝使用的多层有机导渗材料相比,其导渗材料抗压强度高,耐酸碱性好,使用损失率低,可反复循环使用,价格低廉,环境友好,同时减轻了企业对工业固废的处理压力,并以此实现所述工业固废的耦合高值化的综合利用。根据实施例的记载,本发明制备得到的尾矿坝导渗材料的抗压强度≥15mpa,具有较好的耐酸碱性(弱酸弱碱的溶损率≤0.21%,重金属的浸出率≤0.0006mg/l),使用损失率≤0.5%,成本低(成本大约是同等有机导渗材料的1/10)。
附图说明
29.图1为实施例2制备得到的尾矿坝导渗材料的xrd图;
30.图2为实施例5制备得到的尾矿坝导渗材料的sem图。
具体实施方式
31.本发明提供了一种以工业固废制备尾矿坝导渗材料的方法,包括以下步骤:
32.将工业固废、粘结剂和水混合后,依次进行压球造粒、脱水处理、预热、烧结和退火,得到尾矿坝导渗材料;
33.所述工业固废包括高炉粉煤灰、工业铁渣、煤矸石、工业废盐和铅锌渣中的至少两种。
34.在本发明中,所述工业固废的粒度优选≤150μm,更优选为50~150μm。
35.在本发明中,所述工业固废包括高炉粉煤灰、工业铁渣、煤矸石、工业废盐和铅锌渣中的至少两种。在本发明中,所述高炉粉煤灰、工业铁渣、煤矸石、工业废盐和铅锌渣的质量比优选为(0~50):(0~30):(0~40):(0~30):(0~40),且所述高炉粉煤灰、工业铁渣、
煤矸石、工业废盐和铅锌渣中的至少两种的用量不同时为0,更优选为所述工业固废中工业废盐的用量不为0。当所述工业固废中工业废盐的用量不为0时,制备得到的尾矿坝导渗材料包括钠长石相,所述钠长石相结构稳定,可以进一步提升抗压强度。在本发明中,所述高炉粉煤灰、工业铁渣、煤矸石、工业废盐和铅锌渣的质量比更优选为(10~40):(5~25):(10~30):(5~25):(10~30),最优选为(15~30):(10~20):(15~23):(8~16):(16~22)。
36.本发明对所述高炉粉煤灰、工业铁渣、煤矸石、工业废盐和铅锌渣的具体成分没有任何特殊的限定,采用本领域技术人员熟知来源的高炉粉煤灰、工业铁渣、煤矸石、工业废盐和铅锌渣即可。在本发明中,所述高炉粉煤灰中al的质量百分含量优选≥15%;所述工业铁渣中fe的质量百分含量优选≤20%;所述煤矸石中al的质量百分含量优选≤20%;所述工业废盐中的有机物含量优选≤6%;所述铅锌渣优选包括si和al;所述si和al的总量在铅锌渣中的质量百分比优选≥75%;所述si和al的质量比优选为1.2:1;所述铅锌渣中的si和al的含量分别优选以si和al的氧化物的含量计。
37.在本发明中,所述粘结剂优选为粘土;所述粘结剂的粒度优选≤150μm,更优选为50~150μm。
38.在本发明中,将所述工业固废和粘结剂控制在上述粒度范围内可以避免材料的团聚,更利于原料之间的高温固相化学反应。
39.在本发明中,所述粘结剂、水与工业固废的质量比优选为(20~50):(5~15):100,更优选为(28~45):(8~14):100,最优选为(30~40):(10~12):100。
40.在本发明中,所述混合优选为先将工业固废和粘结剂混合后,再与水进行混合。当所述工业固废和粘结剂的粒度不满上述粒度条件时,本发明优选将所述工业固废和粘结剂进行混合后依次进行研磨和过筛;在本发明中,所述研磨的方式优选为球磨;本发明对所述球磨和过筛的过程没有任何特殊的限定,采用本领域技术人员熟知的过程进行即可。
41.本发明对所述压球造粒没有任何特殊的限定,采用本领域技术人员熟知的过程并使球的粒径在2.5~3cm的范围内即可。
42.在本发明中,所述脱水处理的温度优选为≥100℃,更优选为100~120℃;时间优选为≥2h,更优选为2.5~3h;所述脱水处理后得到的物料的含水量优选为2~8%,更优选为3~4%。
43.在本发明中,所述预热的温度优选为200~600℃,更优选为300~500℃,最优选为350~450℃;时间优选为1~4h,更优选为1.5~3.5h,最优选为2~3h;所述预热的升温速率优选为3~5℃/min,更优选为4℃/min。
44.所述预热处理后,优选由预热的温度以≤10℃/min的升温速率,升温至烧结温度。
45.在本发明中,所述烧结的温度优选为900~1100℃,更优选为950~1050℃,最优选为980~1020℃;时间优选为2~5h,更优选为2.5~4.5h,最优选为3~4h;所述烧结完成后,优选以≤8℃/min的降温速率降温至后续退火的温度。
46.在本发明中,所述退火的温度优选为500~800℃,更优选为550~750℃,最优选为580~720℃;时间优选为1~4h,更优选为1.5~3.5h,最优选为2~3h。
47.在本发明中,所述预热为初步烧结过程,可以使各原料在达到烧结温度之前进行充分的热量传递,形成一个化学反应的均热场所,为下一步烧结反应的完全提供前期反应基础;所述烧结的作用是使各原料在一定的高温下充分进行固相化学反应,形成复合氧化
物的矿物形态,从而形成致密、高强度的尾矿坝导渗材料,所述退火的作用是使经过高温烧结后的材料继续保持其反应后形成的致密性和高强度,杜绝材料由于急速降温使材料内部形成内应力而破坏材料的结构。
48.所述退火完成后,本发明还优选包括冷却的过程,在本发明中,所述冷却优选为自然冷却至室温。
49.下面结合实施例对本发明提供的以工业固废制备尾矿坝导渗材料的方法进行详细的说明,但是不能把它们理解为对本发明保护范围的限定。
50.注:实施例1~7中的高炉粉煤灰的来源为青海桥头铝电有限公司,工业铁渣的来源为青海华信环保科技有限公司,煤矸石的来源为青海海西州,工业废盐的来源为浙江某制药厂,铅锌渣的来源为青海华信环保科技有限公司;
51.其中,实施例1~7中原料的配比可以理解为,实施例1~7的技术方案可以应用于不同重量级的实施案例中,即用量单位可以为“g”、“kg”或“t”等;
52.实施例1
53.按照高炉粉煤灰(al的质量百分含量为15~20%)、工业铁渣(fe的质量百分含量为≤20%)、铅锌渣(si、al质量比约为1.2:1,si和al的总量≥75%)和粘土的质量比为1.5:1:1:1的配比进行混合后,经过球磨和筛分,得到粒度≤150μm的混合料,按照高炉粉煤灰、工业铁渣、粘土和铅锌渣的总质量与水的质量比为100:10的配比,将所述混合料与水混合后,经压球造粒,得到粒度为3cm的料球;
54.将所述料球在100℃下脱水3h,使脱水后的料球的含水量为3%,然后在350℃下进行预热2h后,以10℃/min的升温速率升至950℃并在950℃下烧结3h,以8℃/min的降温速率降温至650℃,在650℃下退火1.5h后,自然冷却,得到所述尾矿坝导渗材料。
55.实施例2
56.按照高炉粉煤灰(al的质量百分含量为15~20%)、工业废盐(有机物的质量百分含量为≤6%)、铅锌渣(si、al质量比约为1.2:1,si和al的总量≥75%)和粘土的质量比为1:1:1:1.5的配比进行混合后,经过球磨和筛分,得到粒度≤150μm的混合料,按照高炉粉煤灰、工业废盐、铅锌渣和粘土的总质量与水的质量比为100:12的配比,将所述混合料与水混合后,经压球造粒,得到粒度为2.5cm的料球;
57.将所述料球在100℃下脱水2.5h,使脱水后的料球的含水量为4%,然后在300℃下进行预热3h后,以10℃/min的升温速率升至1000℃并在1000℃下烧结2h,以8℃/min的降温速率降温至700℃,在700℃下退火1h后,自然冷却,得到所述尾矿坝导渗材料。
58.实施例3
59.按照高炉粉煤灰(al的质量百分含量为15~20%)、工业废盐(有机物的质量百分含量为≤6%)、工业铁渣(fe的质量百分含量为≤20%)和粘土的质量比为1:1:1:1.5的配比进行混合后,经过球磨和筛分,得到粒度≤150μm的混合料,按照高炉粉煤灰、工业铁渣、粘土和工业废盐的总质量与水的质量比为100:10的配比,将所述混合料与水混合后,经压球造粒,得到粒度为2.5cm的料球;
60.将所述料球在120℃下脱水2h,使脱水后的料球的含水量为3%,然后在400℃下进行预热2h后,以10℃/min的升温速率升至1050℃并在1050℃下烧结2h,以8℃/min的降温速率降温至800℃,在800℃下退火1h后,自然冷却,得到所述尾矿坝导渗材料。
61.实施例4
62.按照高炉粉煤灰(al的质量百分含量为15~20%)、工业废盐(有机物的质量百分含量为≤6%)、铅锌渣(si、al质量比约为1.2:1,si和al的总量≥75%)和粘土的质量比为1:1:1:1的配比进行混合后,经过球磨和筛分,得到粒度≤150μm的混合料,按照高炉粉煤灰、粘土、工业废盐和铅锌渣的总质量与水的质量比为100:14的配比,将所述混合料与水混合后,经压球造粒,得到粒度为2.5cm的料球;
63.将所述料球在120℃下脱水2h,使脱水后的料球的含水量为4%,然后在400℃下进行预热2.5h后,以10℃/min的升温速率升至1000℃并在1000℃下烧结2h,以8℃/min的降温速率降温至700℃,在700℃下退火1h后,自然冷却,得到所述尾矿坝导渗材料。
64.实施例5
65.按照高炉粉煤灰(al的质量百分含量为15~20%)、工业废盐(有机物的质量百分含量为≤6%)、煤矸石(al的质量百分含量为≤30%)和粘土的质量比为1:1:1:1的配比进行混合后,经过球磨和筛分,得到粒度≤150μm的混合料,按照高炉粉煤灰、粘土、工业废盐和煤矸石的总质量与水的质量比为100:12的配比,将所述混合料与水混合后,经压球造粒,得到粒度为2.5cm的料球;
66.将所述料球在120℃下脱水2h,使脱水后的料球的含水量为3%,然后在400℃下进行预热2.5h后,以10℃/min的升温速率升至1050℃并在1050℃下烧结2h,以8℃/min的降温速率降温至700℃,在700℃下退火1.5h后,自然冷却,得到所述尾矿坝导渗材料。
67.实施例6
68.按照高炉粉煤灰(al的质量百分含量为15~20%)、工业废盐(有机物的质量百分含量为≤6%)和粘土的质量比为1:1.5:1的配比进行混合后,经过球磨和筛分,得到粒度≤150μm的混合料,按照高炉粉煤灰、工业废盐和粘土的总质量与水的质量比为100:10的配比,将所述混合料与水混合后,经压球造粒,得到粒度为2.5cm的料球;
69.将所述料球在120℃下脱水2h,使脱水后的料球的含水量为3%,然后在350℃下进行预热3h后,以10℃/min的升温速率升至950℃并在950℃下烧结2.5h,以8℃/min的降温速率降温至600℃,在600℃下退火1h后,自然冷却,得到所述尾矿坝导渗材料。
70.实施例7
71.按照高炉粉煤灰(al的质量百分含量为15~20%)、铅锌渣(si、al质量比约为1.2:1,si和al的总量≥75%)、工业废盐(有机物的质量百分含量为≤6%)和粘土的质量比为1:1:1.5:1的配比进行混合后,经过球磨和筛分,得到粒度≤150μm的混合料,按照高炉粉煤灰、铅锌渣、工业废盐和粘土的总质量与水的质量比为100:10的配比,将所述混合料与水混合后,经压球造粒,得到粒度为2.5cm的料球;
72.将所述料球在120℃下脱水2h,使脱水后的料球的含水量为3%,然后在350℃下进行预热3h后,以10℃/min的升温速率升至950℃并在950℃下烧结2.5h,以8℃/min的降温速率降温至600℃,在600℃下退火3h后,自然冷却,得到所述尾矿坝导渗材料。
73.测试例
74.将实施例2制备得到的尾矿坝导渗材料进行xrd测试,测试结果如图1所示,由图1可知,各原料之间进行了充分的化学反应,形成了多种复合氧化物矿物结构,物相中类长石相结构al6c
l2
na8o
24
si6,有效的化学固化了废盐渣中的氯化钠,使得形成稳定的矿物结构,
从而在长期的水环境中使用不会轻易溶出导致材料强度下降;
75.将实施例5制备得到的尾矿坝导渗材料进行sem测试,测试结果如图2所示,由图2可知,形成的高强度导渗材料在微观结构上比较均匀,各物相分布均匀,从而在宏观表现为材料强度高,致密性好;
76.按照工业陶粒材料gb/t 4383和gb/t 603标准,将实施例1~7制备得到的尾矿坝导渗材料进行抗压强度、耐酸碱性和使用损失率的测试,测试结果如表1所示:
77.表1实施例1~7制备得到的尾矿坝导渗材料的性能数据
[0078][0079][0080]
由表1可知,利用本发明所述的方法制备得到的尾矿坝导渗材料抗压强度高、耐酸碱性好,使用损失率低,可反复循环使用以及环境友好。
[0081]
以上所述仅是本发明的优选实施方式,应当指出,对于本技术领域的普通技术人员来说,在不脱离本发明原理的前提下,还可以做出若干改进和润饰,这些改进和润饰也应视为本发明的保护范围。