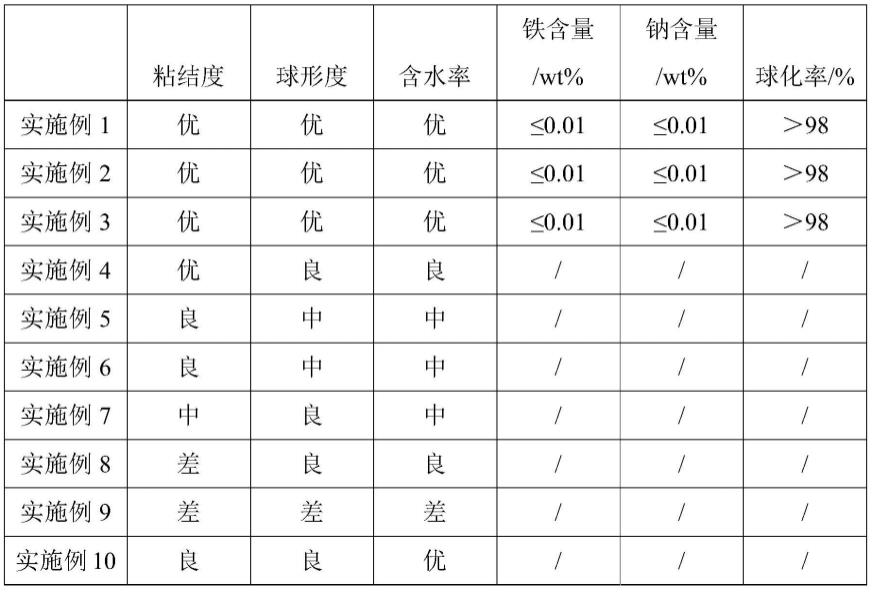
1.本发明涉及一种球形氧化铝,其主要应用于无机材料填充领域,主要应用于陶瓷材料和玻璃纤维中。
背景技术:2.随着现代芯片技术,电力和5g通讯网络科技的迅速发展,电子产品向小,微,轻,薄化的方向发展,而所需负载的功能却越来越多,原件的组装密度和集成度越来越高,单位面积内产生的热量越来越多,这势必会影响电子元器件的使用寿命和可靠性,因此延伸开发出了球形导热,绝缘材料,球形可以提高填充率,增大胶黏剂的流动性,并且球形材料的加入提高了材料的散热性和低介电性;球形材料对混炼机,成型机以及模具等设备的磨损大大降低,可以延长设备的使用寿命。
3.但是目前的制备球形氧化铝的工艺以氧化铝为原材料,原料氧化铝中含有较多的铁,钠等杂质,如果杂质不除去会影响其在后续电子产品中的使用寿命,大量钠,铁杂质的存在可能会使得电子产品的耐电压性能大幅度下降,严重时甚至会导致电路板击穿。因此开发一种纯度高,成球率高的球形氧化铝的制备方法至关重要。
技术实现要素:4.为了提高球形氧化铝的成球率和纯度,本发明的第一个方面提供了一种球形氧化铝的制备方法,包括一次除磁和火焰喷射,一次除磁包括以下步骤:
5.(1)将氧化铝加入铵盐中进行研磨,得到粒径为0.5-30μm的氧化铝;
6.(2)将氧化铝和水加入铺设磁棒的搅拌釜中,搅拌30~50min,搅拌的温度为85~95℃,然后过滤,加入洗涤剂洗涤,干燥,得到一次除磁氧化铝;
7.火焰喷射包括以下步骤:将一次除磁氧化铝通过火焰喷射,火焰喷射的温度为2300~2800℃,得到球形氧化铝。
8.作为一种优选的实施方式,所述一次除磁过程中氧化铝与水的比例为(0.4-0.6g):1ml。
9.作为一种优选的实施方式,所述铵盐选自有机铵盐和或无机铵盐。
10.作为一种优选的实施方式,所述无机铵盐选自氯化铵、硫酸铵、碳酸铵、碳酸氢铵、甲酸铵、乙酸铵、硝酸铵、硫酸氢铵、碘化铵、溴化铵中的一种或几种的组合。
11.作为一种优选的实施方式,所述铵盐占氧化铝的重量分数为0.2-2wt%。
12.作为一种优选的实施方式,所述洗涤剂为碳氢化合物,选自烷烃、环烷烃、芳香烃中的一种。
13.作为一种优选的实施方式,所述一次除磁过程中干燥的温度为350~400℃,干燥的时间为1~6h。
14.作为一种优选的实施方式,所述球形氧化铝的制备方法,还包括二次除磁,其包括以下步骤:
15.(1)将火焰喷射得到的球形氧化铝和水加入铺设磁棒的搅拌釜中,搅拌30~50min;
16.(2)过滤,干燥,得到二次除磁球形氧化铝。
17.作为一种优选的实施方式,所述二次除磁过程中球形氧化铝和水的比例为(0.1-0.3g):1ml。
18.本发明的第二个方面提供了一种球形氧化铝,其由所述球形氧化铝的制备方法制备得到。
19.本发明与现有技术相比具有以下有益效果:
20.(1)本发明所述的球形氧化铝及其制备方法,成球形率高,制备得到的球形氧化铝中α相氧化铝的占比高。
21.(2)本发明所述的球形氧化铝,用作橡胶、塑料、陶瓷等高分子材料的添加剂时,具有较高的填充率,还可以增大基体材料的流动性,并且还有利于材料的散热,降低介电常数。
22.(3)本发明所述的球形氧化铝及其制备方法,制备得到的球形氧化铝,钠,铁杂质含量更低,并且还具有较低的含水率。
23.(4)本发明所述的球形氧化铝及其制备方法,球形氧化铝的粘结率低,流动性好。
24.(5)本发明所述的球形氧化铝及其制备方法,采用火焰高温熔融法,在富氧的高温火焰中将不规则的粉体变为具有较好球形度的粉体。
具体实施方式
25.为了提高球形氧化铝的成球率和纯度,本发明的第一个方面提供了一种球形氧化铝的制备方法,包括一次除磁和火焰喷射,一次除磁包括以下步骤:
26.(1)将氧化铝加入铵盐中进行研磨,得到粒径为0.5-30μm的氧化铝;
27.(2)将氧化铝和水加入铺设磁棒的搅拌釜中,搅拌30~50min,搅拌的温度为85~95℃,然后过滤,加入洗涤剂洗涤,干燥,得到一次除磁氧化铝;
28.火焰喷射包括以下步骤:将一次除磁氧化铝通过火焰喷射,火焰喷射的温度为2300~2800℃,得到球形氧化铝。
29.作为一种优选的实施方式,所述一次除磁过程中氧化铝与水的比例为(0.4-0.6g):1ml。
30.作为一种优选的实施方式,所述铵盐选自有机铵盐和或无机铵盐。
31.氧化铝原料中一般有铁、钠的氧化物、碳酸盐、硫酸盐、硝酸盐等杂质,会影响后续在集成电路、5g通讯等方面的应用,故需要进行除铁和钠,本发明依据铁的杂质的磁性,和钠杂质的水溶性,在磁化条件下加水混合,搅拌,可有效去除原料中铁、钠等杂质,但发明人也发现,加水的方式也造成了后续干燥过程中水难易除去,使得在火焰喷射过程中,水分迅速气化,使得球形氧化铝的孔隙增加,使得球形度下降,且孔隙增加也使得吸附在内部的水分、铁、钠等杂质增加,影响最终成品的纯度。
32.发明人意外发现,通过采用铵盐和氧化铝一起研磨,得到一定粒径的研磨氧化铝后,加入水中,进行磁化搅拌,在促进铁、钠等杂质去除的同时,也促进了干燥后含水量下降,这可能是因为一方面氧化铝吸附的铵盐加入水中,在一定温度下搅拌时,迅速溶于水中
的同时,也带动了里面的钠等可溶性杂质的析出,且在干燥过程中,残留的铵盐分解的过程中也促进了游离水和晶格水的快速挥发,促进氧化铝中水分的下降,得到高球形度的产品。
33.作为一种优选的实施方式,所述铵盐为无机铵盐。
34.作为一种优选的实施方式,所述无机铵盐选自氯化铵、硫酸铵、碳酸铵、碳酸氢铵、甲酸铵、乙酸铵、硝酸铵、硫酸氢铵、碘化铵、溴化铵中的一种或几种的组合。
35.进一步优选,所述无机铵盐为碳酸氢铵和氯化铵的复配使用。
36.进一步优选,碳酸氢铵和氯化铵的重量比为1:(0.5~1)。
37.作为一种优选的实施方式,所述铵盐占氧化铝的重量分数为0.2-2wt%。
38.发明人发现,氧化铝中的水,比如说结晶水需要长时间高温去除,约6h左右,而发明人发现,通过添加不同种类的铵盐,如硫酸铵、碳酸铵等,和乙酸铵、甲酸铵等共同作用,可促进铁、钠去除的同时,在较短干燥时间,如2~3h时也具有高的水的去除率,实现高的球形度和球化率。
39.这可能是因为通过使用高的无机铵盐,如碳酸氢铵和硫酸铵,在干燥过程中,残留的碳酸氢铵和氯化铵等发生分解,其中氯化铵分解产生的酸可进一步促进碳酸氢铵的分解,从而带动水的快速去除,且发明人发现,当使用一种铵盐,或者碳酸氢铵和硫酸铵等作用时,难以实现快速干燥,从而影响后续球形度和球化率。
40.作为一种优选的实施方式,所述洗涤剂为碳氢化合物,选自烷烃、环烷烃、芳香烃中的一种。
41.作为一种优选的实施方式,所述洗涤剂选自煤油、汽油、正庚烷、正己烷、正戊烷、正辛烷中的一种。
42.进一步优选,洗涤剂为煤油。
43.发明人发现,在干燥过程中,尤其是使用铵盐共同研磨、除磁后的氧化铝,容易发生粘结甚至结块的现象,影响后续火焰喷射后的球形度,且会导致干燥过程中水分等杂质难以完全去除,发明人意外发现,在干燥前洗涤,尤其是使用碳氢化合物,如煤油等洗涤,可进一步除水的同时,避免干燥过程中的粘结,提高后续的球形度。
44.这可能是因为,一方面使用和水完全不相容的碳氢化合物,如煤油等,有利于进一步减少氧化铝表面的水含量,且在干燥过程中,因为表面的非极性碳氢化合物形成的气膜,进一步避免了氧化铝之间的粘连和结块,此外,在火焰喷射过程中,一般使用碳氢化合物如天然气作为燃气,并通过氧气作为载体喷射高温火焰,当氧化铝粉体接触高温火焰时,变成熔融状态,此时可能残留的碳氢化合物燃烧放热过程中,可减少水分挥发的空隙,从而使得氧化铝在表面张力状态下,得到高球形度和球化率的球形氧化铝。
45.作为一种优选的实施方式,所述一次除磁过程中干燥的温度为350~400℃,干燥的时间为1~6h。
46.作为一种优选的实施方式,所述火焰喷射的载气为氧气,燃料为天然气。
47.作为一种优选的实施方式,所述球形氧化铝的制备方法,还包括二次除磁,其包括以下步骤:
48.(1)将火焰喷射得到的球形氧化铝和水加入铺设磁棒的搅拌釜中,搅拌30~50min;
49.(2)过滤,干燥,得到二次除磁球形氧化铝。
50.作为一种优选的实施方式,所述二次除磁过程中球形氧化铝和水的比例为(0.1-0.3g):1ml。
51.作为一种优选的实施方式,所述二次除磁中,干燥的时间为3~6h,温度为150~200℃。
52.在火焰喷射过程中,残留的的铁可能会吸附在球形氧化铝表面,且氧化铝内部的钠等也可能会析出,故在火焰喷射后,可以通过二次除磁进一步去除铁和钠,使得最终的球形氧化铝的铁和钠含量在0.02wt%以下。使得球形氧化铝可用于集成电路、5g通讯等方面,作为粘结剂添加材料等。
53.本发明的第二个方面提供了一种球形氧化铝,其由所述球形氧化铝的制备方法制备得到。
54.下面通过实施例对本发明进行具体描述。有必要在此指出的是,以下实施例只用于对本发明作进一步说明,不能理解为对本发明保护范围的限制,该领域的专业技术人员根据上述本发明的内容做出的一些非本质的改进和调整,仍属于本发明的保护范围。
55.另外,如果没有其它说明,所用原料都是市售得到的。
56.实施例1
57.一种球形氧化铝的制备方法,包括一次除磁和二次除磁,其包括以下步骤:
58.(1)将氧化铝加入铵盐中进行研磨,得到粒径为20μm的研磨氧化铝,所述铵盐为碳酸氢铵和氯化铵,重量比为1:0.75,所述铵盐占氧化铝的1wt%。;
59.(2)将研磨氧化铝和水加入铺设磁棒的搅拌釜中,所述研磨氧化铝和水的比例为0.5g:1ml,搅拌40min,搅拌的温度为90℃,然后过滤,加入煤油洗涤,干燥,干燥温度为375℃,干燥的时间为2.5h得到一次除磁氧化铝;
60.(3)将一次除磁氧化铝通过火焰喷射,火焰喷射的温度为2500℃,得到球形氧化铝;
61.(4)将球形氧化铝和水加入铺设磁棒的搅拌釜中,球形氧化铝和水的比例为0.2g:1ml,搅拌40min;
62.(5)过滤,干燥,干燥的时间为4h,干燥的温度为175℃,得到二次除磁球形氧化铝。
63.所述氧化铝购自阿拉丁,粒径为80-150μm,型号为a100277。
64.所述煤油购自麦克林,型号为k812242。
65.本实施例还提供如所述制备方法制备得到的球形氧化铝。
66.实施例2
67.一种球形氧化铝的制备方法,包括一次除磁和二次除磁,其包括以下步骤:
68.(1)将氧化铝加入铵盐中进行研磨,得到粒径为0.5μm的研磨氧化铝,所述铵盐为碳酸氢铵和氯化铵,重量比为1:0.5,所述铵盐占氧化铝的0.2wt%;
69.(2)将研磨氧化铝和水加入铺设磁棒的搅拌釜中,所述研磨氧化铝和水的比例为0.4g:1ml,搅拌30min,搅拌的温度为85℃,然后过滤,加入正庚烷洗涤,干燥,干燥的时间为2h,温度为400℃得到一次除磁氧化铝;
70.(3)将一次除磁氧化铝通过火焰喷射,火焰喷射的温度为2300℃,得到球形氧化铝;
71.(4)将球形氧化铝和水加入铺设磁棒的搅拌釜中,球形氧化铝和水的比例为0.1g:
1ml,搅拌30min;
72.(5)过滤,干燥,干燥的时间为3h,干燥的温度为200℃,得到二次除磁球形氧化铝。
73.所述氧化铝购自阿拉丁,粒径为80-150μm,型号为a100277。
74.所述正庚烷购自麦克林,型号为h811064。
75.本实施例还提供如所述制备方法制备得到的球形氧化铝。
76.实施例3
77.一种球形氧化铝的制备方法,包括一次除磁和二次除磁,其包括以下步骤:
78.(1)将氧化铝加入铵盐中进行研磨,得到粒径为30μm的研磨氧化铝,所述铵盐为碳酸氢铵和氯化铵,重量比为1:1,所述铵盐占氧化铝的2wt%;
79.(2)将研磨氧化铝和水加入铺设磁棒的搅拌釜中,所述研磨氧化铝和水的比例为0.6g:1ml搅拌50min,搅拌的温度为95℃,然后过滤,加入正己烷洗涤,干燥,干燥的时间为3h,干燥温度为350℃,得到一次除磁氧化铝;
80.(3)将一次除磁氧化铝通过火焰喷射,火焰喷射的温度为2800℃,得到球形氧化铝;
81.(4)将球形氧化铝和水加入铺设磁棒的搅拌釜中,球形氧化铝和水的比例为0.3g:1ml,搅拌50min;
82.(5)过滤,干燥,干燥的时间为5h,干燥的温度为150℃,得到二次除磁球形氧化铝。
83.所述氧化铝购自阿拉丁,粒径为80-150μm,型号为a100277。
84.所述正己烷购自麦克林,型号为h811141。
85.本实施例还提供如所述制备方法制备得到的球形氧化铝。
86.实施例4
87.一种球形氧化铝的制备方法及其制得的球形氧化铝,具体步骤同实施例1,不同点在于所述铵盐为碳酸氢铵和硫酸铵,重量比为1:0.75。
88.实施例5
89.一种球形氧化铝的制备方法及其制得的球形氧化铝,具体步骤同实施例1,不同点在于所述铵盐为碳酸氢铵。
90.实施例6
91.一种球形氧化铝的制备方法及其制得的球形氧化铝,具体步骤同实施例1,不同点在于所述铵盐为氯化铵。
92.实施例7
93.一种球形氧化铝的制备方法及其制得的球形氧化铝,具体步骤同实施例1,不同点在于所述步骤2中的干燥温度为450℃,干燥时间为1h。
94.实施例8
95.一种球形氧化铝的制备方法及其制得的球形氧化铝,具体步骤同实施例1,不同点在于所述步骤2中无洗涤步骤。
96.实施例9
97.一种球形氧化铝的制备方法及其制得的球形氧化铝,具体步骤同实施例1,不同点在于研磨氧化铝和水的比例为1g:1ml。
98.实施例10
99.一种球形氧化铝的制备方法及其制得的球形氧化铝,具体步骤同实施例1,不同点在于所述铵盐为碳酸氢铵和氯化铵,重量比为1:1.5。
100.性能测试:
101.1.粘结度:观察一次除磁后是否有粘结和结块等现象,优:无粘结和较大结块;良:略有粘结;无较大结块;差:有较大结块,粘连明显。
102.2.球形度:火焰喷射后球形度:球形度=4πa/b2,a为单个氧化铝颗粒投影的面积,b为单个氧化铝颗粒投影的周边长度。优:》0.97;良:0.97≥球形度》0.95;中:0.95≥球形度》0.93;差:≤0.93。
103.3.含水率:火焰喷射后含水率:依据卡尔水分测定方法测试得到。优:《0.02wt%;良:0.02wt%≤含水率《0.04wt%;中:0.04wt%≤含水率《0.06wt%;差:≥0.06wt%。
104.4.铁杂质含量:二次除磁后,依据icd-aes方法进行测试。
105.5.钠杂质含量:二次除磁后,依据icd-aes方法进行测试。
106.6.球化率:火焰喷射后成球率:成球率=颗粒成球数量/颗粒总数量*100%。
107.将实施例依据上述标准进行测试,结果见于表1。
108.表1
109.