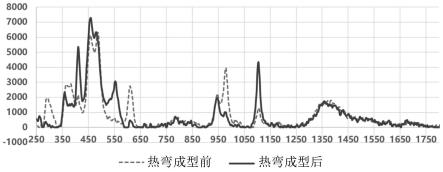
1.本技术涉及一种微晶玻璃盖板及其制备方法、微晶玻璃盖板的修复方法和微晶玻璃盖板抗指纹方法、以及应用该微晶玻璃盖板的电子设备。
背景技术:2.与金属材质和塑胶材质的后盖/壳体相比,透明玻璃作为手机等各类电子设备的后盖/壳体,具有更好的外观档次、更好的触感、可装饰性更强、科技感更高。此外与金属材料相比,玻璃材料对电磁波的屏蔽更小,随着5g时代的到来,这也成为玻璃材料的一个优势。但玻璃作为脆性材料,在电子设备中使用时,容易发生破裂。
技术实现要素:3.本技术实施例第一方面提供了一种微晶玻璃盖板,为微晶玻璃片材经化学离子交换的强化处理得到,所述强化处理使用的熔盐中包含lino3;
4.所述微晶玻璃盖板包括:
5.玻璃相,体积占比15%-70%;
6.石英晶体,体积占比10%-55%;
7.二硅酸锂,晶体体积占比为10%-40%;
8.透锂长石,晶体体积占比为10%-40%。
9.所述微晶玻璃盖板的强化过程包含两次离子交换,强化炉水配比中增加lino3成分,增强表面应力提升强度的同时也能保证表面状态的稳定进而得到强度高、抗跌性能优异,光学性能满足显示屏幕使用要求的微晶玻璃盖板。增加lino3的原因是:与常规玻璃相比,微晶玻璃中含有一定比例的晶体相,这一特性使得微晶玻璃在进行化学强化时,除了玻璃相进行离子交换,表层晶体相中的部分离子也会参与,从而破坏表层的晶体相,在表层形成疏松的空洞,交换出来的na离子和k离子富集在其中,在高温高湿环境下,这部分离子和水汽形成白色的na盐和k盐,附着在玻璃表面,影响材料的洁净度和显示效果。增加lino3一方面可以抑制强化过程对表面晶体的破坏;另一方面可以减少富集在表面的na离子和k离子,从而使得材料在高温高湿环境下可以保持表面性能的稳定。
10.本技术实施方式中,所述微晶玻璃盖板的配方为:
11.sio2重量比65%-85%,
12.al2o3重量比5%-12%,
13.na2o重量比0.5-6%,
14.li2o重量比4%-9%,
15.p2o5重量比0.05%-3%,
16.k2o重量比0.5%-3%,
17.mgo重量比0.5%-8%,
18.tio2重量比0.5%-3%,
19.zro2重量比0.1%-3%。
20.本技术实施方式中,所述微晶玻璃盖板为微晶玻璃片材经热弯成型和化学离子交换的强化处理得到。
21.所述3d热弯成型时,会促进二硅酸锂晶体和透锂长石晶体的形成,使微晶玻璃片材中的二硅酸锂晶体和透锂长石晶体增加,带来光学性能的优化和强度的提升。通过热弯前后的raman光谱测试结果可以看到,热弯过程中,伴随着si-o非桥氧键的断裂,硅氧与li、al等结合形成二硅酸锂晶体和透锂长石晶体。
22.本技术实施方式中,所述强化处理包括两次离子交换;第一次离子交换:熔盐成分为0mol%-50mol%的kno3、50mol%-100mol%的nano3及0mol%-5mol%的lino3,熔盐温度400℃-480℃;第二次离子交换:熔盐成分为kno3以及重量为kno3重量的0.05%-5%的lino3,熔盐温度350℃-420℃。
23.本技术实施方式中,经所述强化处理后,所述微晶玻璃片材的表层转化形成强化层,所述强化层的厚度大于等于90微米,所述强化层的表面压应力≥160mpa,距离外表面深度为50微米处的压应力≥65mpa。
24.本技术实施方式中,所述石英晶体、所述二硅酸锂晶体和所述透锂长石晶体的晶体尺寸均小于80nm,选优为小于50nm。
25.本技术实施方式中,所述微晶玻璃盖板对波长范围为450nm-1000nm内的光的平均透过率大于等于88%。
26.本技术实施方式中,所述微晶玻璃盖板的雾度≤0.2%,优选为雾度≤0.15%。
27.本技术实施方式中,所述微晶玻璃盖板的色差b值满足|b|≤1.2,优选为|b|≤0.8。
28.本技术实施方式中,所述微晶玻璃盖板的四杆弯折强度b10大于550mpa,平均值大于800mpa。
29.本技术实施方式中,所述微晶玻璃盖板能承受的单体落球能量大于0.2j。
30.本技术实施方式中,所述微晶玻璃盖板装配在包括所述微晶玻璃盖板重量为180g的整机上,具有1.5m以上高度的整机砂纸跌落和大理石跌落强度。
31.本技术实施例第二方面提供了一种电子设备,包括透明的屏幕显示盖板以及壳体,所述屏幕显示盖板和所述壳体中的至少一个本技术第一方面所述的微晶玻璃盖板。
32.由于上述的微晶玻璃盖板的强度高,抗跌性能优异,可有效提升所述电子设备的使用寿命。
33.本技术实施例第三方面提供了一种微晶玻璃盖板的制备方法,包括:
34.采用以下原料在1300到1700℃温度条件下熔炼制得玻璃原液:
35.sio2重量比65%-85%,
36.al2o3重量比5%-12%,
37.na2o重量比0.5-6%,
38.li2o重量比4%-9%,
39.p2o5重量比0.05%-3%,
40.k2o重量比0.5%-3%,
41.mgo重量比0.5%-8%,
42.tio2重量比0.5%-3%,
43.zro2重量比0.1%-3%。
44.将所述玻璃原液形成玻璃体;
45.将所述玻璃体在500℃-650℃温度下热处理0.5h-10h进行成核,成核后在650℃-800℃下热处理0.5h-10h进行晶化,得到微晶玻璃;
46.对所述微晶玻璃进行切割和研磨,得到微晶玻璃的片材;
47.对所述微晶玻璃的片材进行化学离子交换的强化处理。
48.本技术实施方式中,所述强化处理包括两次离子交换;第一次离子交换:熔盐成分为0mol%-50mol%的kno3,50mol%-100mol%的nano3,0mol%-5mol%的lino3,熔盐温度400℃-480℃;第二次离子交换:熔盐成分为kno3以及重量为kno3重量的0%-5%的lino3,熔盐温度350℃-420℃。
49.本技术实施方式中,所述制备方法还包括在进行所述强化处理之前,对所述微晶玻璃的片材进行热弯成型处理,在650-800℃温度下进行,成型压力0.3mpa-0.8mpa。
50.本技术实施例第四方面提供了一种本技术第一方面所述的微晶玻璃盖板划伤的修复方法,包括:
51.对所述微晶玻璃盖板的相对两个表面进行抛光;
52.将抛光后的微晶玻璃盖板进行离子交换处理,所述离子交换处理的工艺和参数为:
53.熔盐成分为kno3以及重量为kno3的0%-5%的lino3,熔盐温度350℃-420℃,离子交换时间0.5h-2h;或者,
54.熔盐成分为0mol%-50mol%的kno3,50mol%-100mol%的nano3,0mol%-3mol%的lino3,熔盐温度400℃-480℃,离子交换时间0.5h-2h。
55.该修复方法通过返磨后再离子交换的强化的方案,显著提高该微晶玻璃盖板的加工良率。
56.本技术实施方式中,所述玻璃盖板的相对两个表面分别为凹面和凸面,采用海绵材质的抛光盘,所述凹面的抛光时间为900s-2500s,所述凸面的抛光时间为500s-1500s。
57.本技术实施例第五方面提供了一种提升本技术第一方面所述的微晶玻璃盖板的抗指纹方法,包括:
58.采用碱性溶液对微晶玻璃盖板进行清洗,所述碱性溶液的ph值<12,清洗后,所述微晶玻璃盖板的表面粗糙度ra<1.5nm;
59.采用真空镀膜的方式在所述微晶玻璃盖板上镀抗指纹膜。
60.通过控制加工过程中清洗工艺,可满足抗指纹镀膜后耐橡皮摩擦2500次后水滴角大于105
°
,耐钢丝绒摩擦2500次后水滴角大于102
°
。一般来说,微晶玻璃采用常规镀膜工艺难以达到该水平。
61.本技术实施方式中,所述清洗后,所述微晶玻璃盖板的清洗前后b值变化值<0.3。
附图说明
62.图1是热弯成型前后的微晶玻璃片材的拉曼光谱图。
63.图2是微晶玻璃片材和微晶玻璃盖板的光透过率图。
64.图3是微晶玻璃盖板的雾度分布图。
65.图4是微晶玻璃盖板的b值分布图。
66.图5是微晶玻璃盖板的单体落球破裂能力值分布图。
67.图6是微晶玻璃盖板的四杆弯折强度b10概率分布图。
68.图7是微晶玻璃盖板装配180g手机跌落碎裂高度分布图。
69.图8是微晶玻璃盖板装配180g手机跌落碎裂高度b20概率分布图。
70.图9是微晶玻璃盖板的原子力显微镜图。
71.图10是本技术实施例的微晶玻璃盖板的制备方法的流程示意图。
72.图11是本技术实施例的电子设备的示意图。
73.主要元件符号说明
74.电子设备
ꢀꢀꢀꢀꢀꢀꢀꢀꢀꢀꢀꢀꢀꢀꢀꢀꢀꢀꢀꢀꢀꢀꢀꢀꢀꢀ
100
75.屏幕显示盖板
ꢀꢀꢀꢀꢀꢀꢀꢀꢀꢀꢀꢀꢀꢀꢀꢀꢀꢀꢀꢀꢀꢀ
10
76.壳体
ꢀꢀꢀꢀꢀꢀꢀꢀꢀꢀꢀꢀꢀꢀꢀꢀꢀꢀꢀꢀꢀꢀꢀꢀꢀꢀꢀꢀꢀꢀ
30
具体实施方式
77.下面结合本技术实施例中的附图对本技术实施例进行描述。
78.本技术中记载的数据范围值如无特别说明均应包括端值。
79.透明玻璃材质的盖板作为手机等各类电子设备的后盖/壳体,具有更好的外观档次、更好的触感、可装饰性更强、科技感更高。然而,玻璃是脆性材料,在作为电子设备的后盖/壳体使用时,容易发生破裂等问题。
80.本技术实施例的微晶玻璃盖板,可作为手机等各类电子设备的后盖/壳体或者透明的屏幕盖板。所述微晶玻璃盖板强度高,具备优异的抗跌性能,整机跌落在砂纸和大理石上的跌落高度≥1.5m,同时透明度和光学性能满足手机等电子设备的屏幕使用要求。
81.本技术实施例的所述微晶玻璃盖板的配方为:
82.sio2重量比65%-85%,
83.al2o3重量比5%-12%,
84.na2o重量比0.5-6%,
85.li2o重量比4%-9%,
86.p2o5重量比0.05%-3%,
87.k2o重量比0.5%-3%,
88.mgo重量比0.5%-8%,
89.tio2重量比0.5%-3%,
90.zro2重量比0.1%-3%。
91.所述微晶玻璃盖板采用上述配比的原料制得。
92.所述微晶玻璃盖板为采用上述配比的原料制得的微晶玻璃片材经化学离子交换的强化处理得到。相较于常规的玻璃强化处理,本技术所述强化处理使用的熔盐中增加了lino3,使得强化处理增强所述微晶玻璃盖板的表面应力,提升强度的同时,也能保证表面状态的稳定。经所述强化处理后,微晶玻璃片材一定厚度(深度)的表层转化形成强化层,所述强化层的厚度大于等于90微米,所述强化层的表面压应力≥160mpa,距离外表面深度为
50微米处的压应力≥65mpa。
93.增加lino3的原因是:微晶玻璃与常规玻璃的区别是,微晶玻璃中含有一定比例的晶体相,这一特性使得微晶玻璃在进行化学强化时,除了玻璃相进行离子交换,表层晶体相中的部分离子也会参与,从而破坏表层的晶体相,在表层形成疏松的空洞,交换出来的na离子和k离子富集在其中,在高温高湿环境下,这部分离子和水汽形成白色的na盐和k盐,附着在玻璃表面,影响材料的洁净度和显示效果。增加lino3一方面可以抑制强化过程对表面晶体的破坏;另一方面可以减少富集在表面的na离子和k离子,从而使得材料在高温高湿环境下可以保持表面性能的稳定。所述微晶玻璃盖板包括玻璃相、石英(sio2)晶体、二硅酸锂(li2si2o5)晶体和透锂长石(li[alsi4o
10
])晶体。玻璃相是指高温烧结时各组成物质和杂质产生一系列物理、化学反应后形成的一种非晶态物质,其主要作用是将分散的晶相黏合在一起。所述微晶玻璃盖板中,玻璃相体积占比15%-70%,石英晶体体积占比10%-55%,二硅酸锂晶体体积占比为10%-40%,透锂长石晶体体积占比为10%-40%。所述石英晶体、所述二硅酸锂晶体、和所述透锂长石晶体的晶体尺寸小于80nm,选优为小于50nm。
[0094]
一些实施例中,所述微晶玻璃盖板为微晶玻璃片材经过热弯成型和化学离子交换的强化处理得到。即,热弯成型可选择性进行或不进行。所述微晶玻璃片材在热弯处理时,会促进二硅酸锂晶体和透锂长石晶体的形成,使二硅酸锂晶体和透锂长石晶体增加,带来光学性能的优化和强度的提升。主要形成机理是热弯过程中,伴随着si-o非桥氧键的断裂,与li、al等结合形成二硅酸锂晶体和透锂长石晶体。
[0095]
所述微晶玻璃盖板的外形包括不限于二维平板结构(2d)、带有一定的弧度的二维平板结构(2.5d)和具有弯折的三维结构(3d)。所述热弯成型可为选择性进行的,对于2d\2.5d的微晶玻璃盖板,可不进行热弯成型处理。
[0096]
请参阅图1,微晶玻璃片材和经750℃温度下热弯成型后的微晶玻璃片材的拉曼光谱图;其中横坐标950-1050cm-1
对应si-o非桥氧键;横坐标400-700cm-1
表示桥氧。如图1可知:热弯成型后的微晶玻璃片材对应的横坐标950-1050cm-1
处的峰值强度明显下降,说明si-o非桥氧键发生了断裂而减少。
[0097]
结合参阅图2,所述微晶玻璃片材对波长范围为450nm-1000nm内的光的平均透过率≥85%;经热弯成型和强化处理所述微晶玻璃片材得到的所述微晶玻璃盖板,对波长范围为450nm-1000nm内的光的平均透过率≥88%。这说明,热弯成型和强化处理可显著提升玻璃的光透过率。
[0098]
所述微晶玻璃片材的雾度为1.0%-1.35%,色差值b值1.5≤|b|≤2.8。所述微晶玻璃盖板的雾度≤0.2%,优选为雾度≤0.15%。经热弯成型(可选择性进行)和强化处理所述微晶玻璃片材得到的所述微晶玻璃盖板的雾度≤0.2%,如图3所示,其中图3的每一个点代表一个测试的数据,纵坐标代表雾度的值。所述微晶玻璃盖板的色差b值满足|b|≤1.2,优选为|b|≤0.8。如图4所示,色差值b值|b|≤1.2,其中图4中每一个点代表一个测试的数据,纵坐标代表色差值b值。
[0099]
如图5所示,所述微晶玻璃盖板的单体落球能量大于0.2j。单体落球能量的测试为将测试样品放在试验台面上,将规定重量的钢球从规定跌落高度上自由跌落在样品上,对样品进行冲击,直至样品被砸裂,通过跌落高度和钢球重量计算冲击的能量值。
[0100]
如图6所示,所述微晶玻璃盖板的四杆弯折强度(韦泊分布b10)大于550mpa,平均
值大于800mpa。四杆弯折强度为手机领域的常规测试,具体的测试方法为:下面两个支撑杆支撑样品的相对的两端部,上面两个圆柱形压杆从所述样品的中间位置从上往下压,测试样品断裂时的一些受力值和位移量进行换算得到弯折强度。
[0101]
将所述微晶玻璃盖板装配在整机上,整机包括所述微晶玻璃盖板的重量为180g,跌落在砂纸和大理石上均具有1.5m以上的跌落高度,如图7所示。如图8所示,跌落高度(韦泊分布b20)大于1.65m。
[0102]
请参阅图9,所述微晶玻璃盖板的原子力显微镜图,从图9可知:所述微晶玻璃盖板的粒径约为50nm,表面粗糙度约为1.5nm。
[0103]
结合参阅图10,所述微晶玻璃盖板的制备方法,包括如下步骤:
[0104]
(1)采用以下原料配方在1300℃-1700℃温度条件下熔炼制得玻璃原液:
[0105]
sio2重量比65%-85%,
[0106]
al2o3重量比5%-12%,
[0107]
na2o重量比0.5-6%,
[0108]
li2o重量比4%-9%,
[0109]
p2o5重量比0.05%-3%,
[0110]
k2o重量比0.5%-3%,
[0111]
mgo重量比0.5%-8%,
[0112]
tio2重量比0.5%-3%,
[0113]
zro2重量比0.1%-3%。
[0114]
(2)将所述玻璃原液成型为透明的玻璃体;
[0115]
(3)将所述玻璃体在500℃-600℃温度下热处理0.5h-10h进行成核,成核后在650℃-800℃的温度下热处理0.5h-10h进行晶化,得到微晶玻璃片材;
[0116]
(4)对所述微晶玻璃片材进行热弯成型处理;
[0117]
(5)通过化学离子交换工艺对热弯成型后的微晶玻璃片材进行强化处理。
[0118]
将所述玻璃原液形成玻璃体的步骤(2)具体为:通过压延法、熔融浇注法、浮法、溢流法、烧结法中的一种形成玻璃体,然后使所述玻璃体以均匀的速度降温至室温,降温的过程称之为粗退火。形成所述玻璃体之前,还包括去除所述玻璃原液中的气泡的步骤。
[0119]
如图10所示,所述制备方法还包括:在对所述微晶玻璃片材进行热弯成型处理的步骤(4)之前,对所述微晶玻璃片材进行切割、抛光、以及计算机数字化控制加工(computerized numerical control,cnc)外形。切割可采用数控机床进行冷加工,例如假设最终要制得厚度为d的微晶玻璃产品,则切割得到的微晶玻璃片材的厚度要比厚度d大0.1-0.25mm。因为切割后还需对玻璃进行抛光等处理,可能厚度会降低。通常手机的玻璃盖板的厚度一般为0.3mm-1.2mm。切割后得到的微晶玻璃片材的薄片需进行抛光,以使表面平整光滑,可采用抛光革、毛刷、海绵抛光盘等配合抛光粉进行粗磨和精磨。
[0120]
可以理解的,热弯成型处理的步骤(4)也可省略去除。对所述微晶玻璃片材进行热弯成型处理为选择性进行,对所述微晶玻璃片材进行热弯成型处理的步骤(4)具体为:在650℃-800℃的温度下进行热弯成型,成型压力0.3mpa-0.8mpa。热弯成型的目的使为了得到所需3d形状的玻璃盖板。对微晶玻璃片材进行强化处理的步骤(5)包括两次离子交换强化。强化处理在强化炉中进行,强化炉中设置有熔融状态的碱金属盐(熔盐,也称为强化炉
水),将微晶玻璃浸入到熔盐中进行离子交换,然后进行冷却。第一次离子交换:熔盐成分为0mol%-50mol%的kno3,50mol%-100mol%的nano3,0mol%-5mol%的lino3,熔盐温度400℃-480℃,离子交换时间6h-15h。第二次离子交换:熔盐成分为kno3以及重量为kno3重量的0.05%-5%的lino3,熔盐温度350℃-420℃,离子交换时间0.5h-2h。化学离子交换的原理是,通过强化炉水中半径比较大碱金属离子(k离子,na离子)和半径比较小的碱金属离子(na离子,li离子)进行离子交换而在玻璃表面形成压应力强化层,第一次离子交换主要进行熔盐中的钠离子替换微晶玻璃片材中的锂离子,第二次离子交换主要进行熔盐中的钾离子替换微晶玻璃片材中的钠离子。经过上述两次化学离子交换的强化后在微晶玻璃表面形成的应力强化层,可以有效提升微晶玻璃的抗跌落强度。
[0121]
如图10所示,强化处理得到的微晶玻璃还可进行表面装饰处理,例如通过丝印、移印、镀膜或膜片贴合工艺对微晶玻璃进行表面装饰处理,从而获得最终效果的微晶玻璃盖板。
[0122]
微晶玻璃片材经过热弯成型和化学离子交换的强化处理,该强化过程包含两次离子交换,强化炉水中增加lino3成分,增强表面应力提升强度的同时也能保证表面状态的稳定。
[0123]
所述微晶玻璃盖板在高温3d热弯成型时,微晶玻璃片材中的二硅酸锂晶体和透锂长石晶体增加,带来光学性能的优化和强度的提升,进而得到强度高、抗跌性能优异,光学性能满足显示屏幕使用要求的微晶玻璃盖板。所述微晶玻璃片材主要包括石英晶体,还包括二硅酸锂晶体和透锂长石晶体;所述微晶玻璃片材在热弯处理时,会促进二硅酸锂晶体和透锂长石晶体的形成。通过热弯前后的raman光谱测试结果可以看到,热弯过程中,伴随着si-o非桥氧键的断裂,硅氧与li、al等结合形成二硅酸锂晶体和透锂长石晶体。所述微晶玻璃盖板中玻璃相体积占比15%-70%,石英晶体体积占比10%-55%,二硅酸锂晶体体积占比为10%-40%,透锂长石晶体体积占比为10%-40%。
[0124]
所述微晶玻璃片材对波长范围为450nm-1000nm内的光的平均透过率≥85%;经热弯成型(选择性进行)和强化处理得到的所述微晶玻璃盖板,对波长范围为450nm-1000nm内的光的平均透过率≥88%。
[0125]
所述微晶玻璃片材的雾度为1.0%-1.35%,色差值b值1.5≤|b|≤2.8;经热弯成型(选择性进行)和强化处理得到的所述微晶玻璃盖板的雾度≤0.2%,色差值b值满足|b|≤1.2。
[0126]
请参阅图11,本技术还提供一种电子设备100,包括透明的屏幕显示盖板10以及壳体30,所述屏幕显示盖板10和所述壳体30配合容纳所述电子设备100的功能模组(图未示),例如显示触控面板、电池、电路板、芯片等。所述屏幕显示盖板10和所述壳体30中的至少一个为上述的微晶玻璃盖板。本实施例中,所述电子设备100为手机,但不限于手机,还可为其他的电子设备,例如平板电脑等。
[0127]
由于上述的微晶玻璃盖板的强度高,抗跌性能优异,同时透明度和光学性能满足手机等电子设备的屏幕使用要求,因此,可有效提升所述电子设备100的使用寿命。
[0128]
本技术还提供一种修复上述微晶玻璃盖板的表面划伤等外观不良的方法。该方法可有效提升微晶玻璃盖板的加工良率。
[0129]
所述方法包括:(1)对微晶玻璃盖板的相对两个表面进行抛光;(2)将抛光后的微
晶玻璃盖板放入强化炉中进行离子交换处理。
[0130]
所述玻璃盖板的相对两个表面分布为凹面和凸面,采用海绵材质的抛光盘,所述凹面的抛光时间为900s-2500s,所述凸面的抛光时间为500s-1500s。
[0131]
抛光后的微晶玻璃盖板在强化炉中进行离子交换,熔盐成分为kno3以及重量为kno3的0%-5%的lino3,熔盐温度350℃-420℃,离子交换时间0.5h-2h。
[0132]
或者,离子交换的熔盐成分为0mol%-50mol%的kno3,50mol%-100mol%的nano3,0mol%-3mol%的lino3,熔盐温度400℃-480℃,离子交换时间0.5h-2h。
[0133]
经离子交换的强化处理,所述微晶玻璃盖板的距离外表面深度为50微米的压应力(cs_50)≥65mpa,强化深度(dol)≥90μm,表面应力(ct)≥160mpa。所述微晶玻璃盖板的单体强度四杆弯折强度b10大于550mpa,单体落球能量大于0.2j。
[0134]
本技术还提供一种在上述微晶玻璃盖板的抗指纹方法。该方法包括:(1)采用碱性溶液对微晶玻璃盖板进行清洗;(2)采用真空镀膜的方式在所述微晶玻璃盖板上镀抗指纹膜。
[0135]
采用碱性溶液对微晶玻璃盖板进行清洗,所述碱性溶液的ph值<12,清洗后,所述微晶玻璃盖板的表面粗糙度ra<1.5nm,清洗前后对比,所述微晶玻璃盖板的b值变化值<0.3。
[0136]
采用真空镀膜的方式在所述微晶玻璃盖板上镀抗指纹膜。通常镀抗指纹膜前,会在所述微晶玻璃盖板上预先形成打底层,打底层可为3nm-15nm厚度的sio2层,可以通过真空溅射或者蒸发镀膜的方式得到。然后再在打底层上形成10nm-50nm厚度的低表面能的抗指纹膜,成分可为全氟聚醚等链状物质,主要通过蒸发镀膜的方式得到。镀膜时机台真空度最好在5*10-5
torr以上。一些实施例中,所述真空镀膜分为3个操作步骤:等离子处理玻璃表面、镀sio2打底层、镀有机材质的抗指纹膜层。等离子处理时间50-300s;镀sio2打底层的转速0.5-2rpm,时间200-600s,电压2-5v,电流150ma-300ma;镀抗指纹膜层的转速1.0-2rpm,时间300-700s,电压2-5v,电流150ma-300ma。
[0137]
镀有所述抗指纹膜层的微晶玻璃盖板耐橡皮摩擦3500次后水滴角大于105
°
。如下表一所示,镀有所述抗指纹膜层的微晶玻璃盖板耐橡皮摩擦3500次后水滴角大于109
°
。
[0138]
表一
[0139][0140]
镀有所述抗指纹膜层的微晶玻璃盖板的耐钢丝绒摩擦2500次后水滴角大于102
°
。如下表二所示,水滴角大于103
°
。
[0141]
表二
[0142][0143]
下面通过具体实施例对本技术实施例进行进一步的说明。
[0144]
实施例一
[0145]
将质量配比70%sio2,11%al2o3,1%na2o,8%li2o,3%p2o5,1%k2o,3%mgo,2%tio2,1%zro2的原材料在1650℃下熔炼并成型成块料。通过切割工艺,将块料切割成厚度为0.7-0.9mm的片材,然后对片材进行晶化处理,在550℃温度下热处理6h,之后以30℃/h升温到720℃,保温5h,最后炉冷降到室温,得到透明微晶玻璃。
[0146]
通过外形cnc加工和抛光,将晶化后的片材抛光到0.55-0.75mm的透明薄片。然后在730℃,0.65mpa的热弯成型条件下,将平片微晶玻璃成型成3d曲面的微晶玻璃。
[0147]
将成型好的3d微晶玻璃进行离子交换强化,强化条件为:第一次离子交换,熔盐成分为7.8mol%kno3,92mol%nano3,0.2mol%lino3,熔盐温度450℃,离子交换时间11h;第二次离子交换,熔盐成分为99.8wt%kno3,0.2wt%lino3,熔盐温度390℃,离子交换时间1h。
[0148]
最后通过移印油墨和抗指纹镀膜对加工好的3d微晶玻璃进行外观装饰处理,得到3d曲面的微晶玻璃盖板。
[0149]
制备的曲面微晶玻璃盖板在450nm-1000nm波长范围内,平均透光率≥88%,优选≥91.5%,|b值|≤1.2,优选|b值|≤0.8,雾度≤0.2%,优选雾度≤0.15%。
[0150]
制备的微晶玻璃盖板装配到180g的手机上,能通过1.5m的大理石跌落和180目砂纸地面跌落。
[0151]
实施例二
[0152]
将质量配比68%sio2,10%al2o3,3%na2o,7%li2o,5%p2o5,1%k2o,3%mgo,2%tio2,1%zro2的原材料在1650℃下熔炼并成型成块料。通过切割工艺,将块料切割成厚度为0.7-0.9mm的片材,然后对片材进行晶化处理,在550℃温度下热处理7.5h,之后以40℃/h升温到720℃,保温6h,最后炉冷降到室温,得到透明微晶玻璃。
[0153]
通过外形cnc加工和抛光,将晶化后的片材抛光到0.55-0.75mm的透明薄片。然后在720℃,0.75mpa的热弯成型条件下,将平片微晶玻璃成型成3d曲面微晶玻璃。
[0154]
将成型好的3d微晶玻璃进行离子交换强化,强化条件为:第一次离子交换,熔盐成分为9.8mol%kno3,90mol%nano3,0.2mol%lino3,熔盐温度450℃,离子交换时间10h;第二次离子交换,熔盐成分为99.8wt%kno3,0.2wt%lino3,熔盐温度380℃,离子交换时间1.5h。
[0155]
最后通过移印油墨和抗指纹镀膜对加工好的曲面微晶玻璃进行外观装饰处理,得到3d曲面的微晶玻璃盖板。
[0156]
加工过程中应避免长时间强碱处理,采用平板和超声槽式清洗时,清洗液ph<12,温度<65℃,单次清洗时间<60min。
[0157]
抗指纹镀膜前,通过控制过程中的清洗,保证清洗前后的b值变化值<0.3,表面粗糙度ra<1.5nm。
[0158]
制备的曲面微晶玻璃盖板在可达成2500次橡皮摩擦后水滴角大于105
°
,耐钢丝绒
摩擦2500次后水滴角大于100
°
。
[0159]
制备的微晶玻璃盖板装配到180g的手机上,能通过1.5m的大理石跌落和180目砂纸地面跌落。
[0160]
实施例三
[0161]
将质量配比69%sio2,10%al2o3,2%na2o,7%li2o,3%p2o5,1%k2o,5%mgo,2%tio2,1%zro2的原材料在1650℃下熔炼并成型成块料。通过切割工艺,将块料切割成厚度为0.7-0.9mm的片材,然后对片材进行晶化处理,在580℃温度下热处理6h,之后以30℃/h升温到720℃,保温6h,最后炉冷降到室温,得到透明微晶玻璃。
[0162]
通过外形cnc加工和抛光,将晶化后的片材抛光到0.55-0.75mm的透明薄片。然后在730℃,0.65mpa的热弯成型条件下,将平片微晶玻璃成型成3d曲面的微晶玻璃。
[0163]
将成型好的3d玻璃陶瓷盖板进行离子交换强化,强化条件为:第一次离子交换,熔盐成21.8mol%kno3,78mol%nano3,0.2mol%lino3,熔盐温度450℃,离子交换时间11h;第二次离子交换,熔盐成分为99.5wt%kno3,0.5wt%lino3,熔盐温度390℃,离子交换时间45min。
[0164]
最后通过移印油墨和抗指纹镀膜对加工好的曲面微晶玻璃进行外观装饰处理,得到3d曲面的微晶玻璃盖板。
[0165]
强化后的玻璃盖板出现表面划伤,或者移印油墨过程中出现不良,可对不良样品进行返工处理,返工制程为:将不良品进行返磨,时间为凹面扫磨1200s,凸面扫磨700s。扫磨后样品在强化炉中进行强化,熔盐成分为99.8wt%kno3,0.2wt%lino3,熔盐温度390℃,离子交换时间1h。
[0166]
制备的微晶玻璃盖板在强化返工后可修复划伤不良和油墨不良,返工后微晶玻璃样品cs_50≥80mpa,dol≥100μm,ct≤125mpa。
[0167]
制备的微晶玻璃盖板装配到180g的手机上,能通过1.5m的大理石跌落和180目砂纸地面跌落。
[0168]
需要说明的是,以上仅为本技术的具体实施方式,但本技术的保护范围并不局限于此,任何熟悉本技术领域的技术人员在本技术揭露的技术范围内,可轻易想到变化或替换,都应涵盖在本技术的保护范围之内;在不冲突的情况下,本技术的实施方式及实施方式中的特征可以相互组合。因此,本技术的保护范围应以权利要求的保护范围为准。