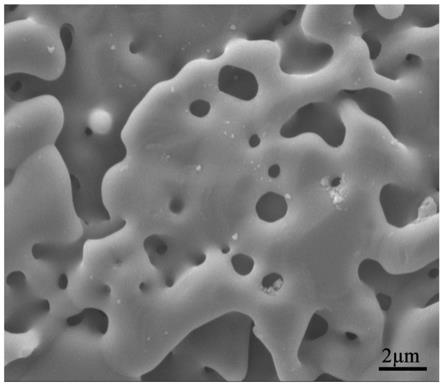
1.本发明涉及多孔材料技术领域,具体涉及一种氯磷灰石多孔材料及其制备方法。
背景技术:2.氯磷灰石对人体无害,在食品工业中具有很高的安全性。它对氟和绝大多数重金属离子具有很强的吸附作用,可作为净化水质的过滤芯。其比表面积大,生物安全性高,可用作药物雾化芯。氯磷灰石通过表面吸附、离子交换、溶解和沉淀等作用机理吸附水中的重金属,达到净化水质的作用。氯磷灰石的吸附性能主要受比表面积和表面活性的影响,比表面积的增加能够增强氯磷灰石的表面吸附,而表面活性越高,离子置换越显著。提高氯磷灰石的表面活性可以通过降低其结晶度、增加缺陷和空位、增加孔隙率来实现。增加孔隙率是提高比表面积最有效的方法,但高孔隙率氯磷灰石多孔材料难以实现高强度。
3.鉴于此,本发明的目的在于提供一种新的材料解决上述技术问题。
技术实现要素:4.本发明要解决的技术问题是提供一种氯磷灰石多孔材料,具有高孔隙率和高强度的特性,且表面活性高。
5.为了解决上述问题,本发明的技术方案如下:
6.一种氯磷灰石多孔材料,原材料包括氯磷灰石基体材料、增强剂sio2和zno2、及造孔剂,以粉末冶金方法成型、烧结制备得到;
7.其中氯磷灰石基体材料由含氯化钠的羟基磷灰石在高温下分解、反应得到,所述含氯化钠的羟基磷灰石由cacl2溶液、na3po4溶液、氨水共沉积法生成。
8.进一步地,所述氯磷灰石基体材料的制备方法,包括如下步骤:
9.步骤s1,配制cacl2溶液、na3po4溶液;
10.步骤s2,在搅拌条件下,将适量的氨水缓慢加入到步骤s1配制的na3po4溶液中,调节溶液ph至8
‑
10;
11.步骤s3,在搅拌条件下,将cacl2溶液缓慢逐滴加入到步骤s2所得的溶液中,得到羟基磷灰石反应沉淀物;
12.步骤s4,将步骤s3的反应沉淀物溶液陈放一定时间后,进行过滤、干燥,得到含氯化钠的羟基磷灰石粉末;
13.步骤s5,将步骤s4的含氯化钠的羟基磷灰石粉末进行焙烧,得到氯磷灰石基体材料。
14.进一步地,配制的cacl2溶液、na3po4溶液的浓度分别为0.2mol/l。
15.进一步地,步骤s5中,焙烧温度为650
‑
750℃,焙烧时间为1
‑
2h。
16.进一步地,造孔剂为硬脂酸。
17.进一步地,氯磷灰石多孔材料的制备工艺包括如下步骤:
18.将原材料均匀混合后,采用液压机将原材料成型得到压制坯;
19.对压制坯进行烧结,烧结工艺为:升温至270
‑
400℃进行脱脂,保温时间为1.5
‑
3h,然后升温至1100
‑
1250℃烧结1
‑
2h。
20.进一步地,sio2和zno2的加量分别为氯磷灰石基体材料质量的2
‑
3%。
21.本发明还提供一种氯磷灰石多孔材料的制备方法,包括如下步骤:
22.制备氯磷灰石基体材料,由cacl2溶液、na3po4溶液、氨水共沉积法制备得到含氯化钠的羟基磷灰石反应沉淀物,然后经过滤、干燥、焙烧得到氯磷灰石基体材料;
23.将氯磷灰石基体材料、增强剂sio2和zno2、及造孔剂按比例混合,以粉末冶金方法成型、烧结制备得到氯磷灰石多孔材料。
24.进一步地,制备氯磷灰石基体材料,具体包括如下步骤:
25.步骤s1,配制cacl2溶液、na3po4溶液;
26.步骤s2,在搅拌条件下,将适量的氨水缓慢加入到步骤s1配制的na3po4溶液中,调节溶液ph至8
‑
10;
27.步骤s3,在搅拌条件下,将cacl2溶液缓慢逐滴加入到步骤s2所得的溶液中,得到羟基磷灰石反应沉淀物;
28.步骤s4,将步骤s3的反应沉淀物溶液陈放一定时间后,进行过滤、干燥,得到含氯化钠的羟基磷灰石粉末;
29.步骤s5,将步骤s4的含氯化钠的羟基磷灰石粉末进行焙烧,得到氯磷灰石基体材料。
30.进一步地,以粉末冶金方法成型、烧结制备氯磷灰石多孔材料,具体包括如下步骤:
31.将氯磷灰石基体材料、增强剂sio2和zno2、及造孔剂按比例混合,采用液压机将原材料成型得到压制坯;其中sio2和zno2的加量分别为氯磷灰石基体材料质量的2
‑
3%,造孔剂为硬脂酸;
32.对压制坯进行烧结,烧结工艺为:升温至250
‑
280℃进行脱脂,保温时间为1.5
‑
3h,然后升温至1100
‑
1250℃烧结1
‑
2h。
33.与现有技术相比,本发明提供的氯磷灰石多孔材料及其制备方法,有益效果在于:
34.本发明提供的氯磷灰石多孔材料,首先以cacl2溶液、na3po4、氨水作为原材料,利用溶液共沉积法制备含氯化钠的羟基磷灰石,含氯化钠的羟基磷灰石[ca
10
(po4)6(oh)2]在高温下分解、反应,高温下熔融状态的氯化钠产生大量的电负性更强的游离cl
—
占据羟基磷灰石中oh
—
的晶格位置,从而生成氯磷灰石基体材料[ca5(po4)3cl];在氯磷灰石基体材料中加入硬脂酸造孔剂,以及zno2、sio2增强剂,采用工艺简单的粉末冶金方法制备得到氯磷灰石多孔材料。本发明的氯磷灰石多孔材料强度高、孔隙率高、表面活性高,且制备工艺简单。
附图说明
[0035]
为了更清楚地说明本发明实施例中的技术方案,下面将对实施例描述中所需要使用的附图作简单地介绍,显而易见地,下面描述中的附图仅仅是本发明的一些实施例,对于本领域普通技术人员来讲,在不付出创造性劳动的前提下,还可以根据这些附图获得其他的附图。
[0036]
图1是本发明实施例1中含氯化钠的羟基磷灰石xrd衍射图;
[0037]
图2是本发明实施例1的氯磷灰石基体材料的xrd衍射图;
[0038]
图3是本发明实施例1的氯磷灰石多孔材料的sem图。
具体实施方式
[0039]
为了使本技术领域的人员更好地理解本发明实施例中的技术方案,并使本发明的上述目的、特征和优点能够更加明显易懂,下面对本发明的具体实施方式作进一步的说明。
[0040]
在本文中所披露的范围的端点和任何值都不限于该精确的范围或值,这些范围或值应当理解为包含接近这些范围或值的值。对于数值范围来说,各个范围的端点值之间、各个范围的端点值和单独的点值之间,以及单独的点值之间可以彼此组合而得到一个或多个新的数值范围,这些数值范围应该被视为在本文中具体公开。
[0041]
本发明的氯磷灰石多孔材料,制备方法包括如下步骤:
[0042]
步骤s1,制备氯磷灰石基体材料,由cacl2溶液、na3po4溶液、氨水共沉积法制备得到含氯化钠的羟基磷灰石反应沉淀物,然后经过滤、干燥、焙烧得到氯磷灰石基体材料;
[0043]
具体的,包括如下步骤:
[0044]
步骤s11,配制cacl2溶液、na3po4溶液;优选地,配制的cacl2溶液、na3po4溶液的浓度分别为0.2mol/l;
[0045]
步骤s12,在搅拌条件下,将适量的氨水缓慢加入到步骤s11配制的na3po4溶液中,调节溶液ph至8
‑
10;
[0046]
步骤s13,在搅拌条件下,将cacl2溶液缓慢逐滴加入到步骤s12所得的溶液中,得到羟基磷灰石反应沉淀物;
[0047]
反应式如下:
[0048]
6na3po4·
12h2o+10cacl2+2nh3·
h2o
→
ca
10
(po4)6(oh)2+18nacl+2nh4cl
[0049]
步骤s14,将步骤s3的反应沉淀物溶液陈放一定时间后,进行过滤、干燥,得到含氯化钠的羟基磷灰石粉末;优选地,陈放时间为24h;
[0050]
步骤s15,将步骤s4的含氯化钠的羟基磷灰石粉末进行焙烧,得到氯磷灰石基体材料;
[0051]
具体的烧结工艺为:
[0052]
焙烧温度为650
‑
750℃,焙烧时间为1
‑
2h;
[0053]
反应式如下:
[0054]
ca
10
(po4)6(oh)2+18nacl
→
2ca5(po4)3cl+h2o+na2o
[0055]
得到的ca5(po4)3cl即为氯磷灰石基体材料;
[0056]
步骤s2,将氯磷灰石基体材料、增强剂sio2和zno2、及造孔剂按比例混合,以粉末冶金方法成型、烧结制备得到氯磷灰石多孔材料;
[0057]
本发明中,增强剂sio2和zno2的添加量分别为氯磷灰石基体材料质量的2
‑
3%,可以是2%、2.5%、3%等;造孔剂为硬脂酸,其添加量为氯磷灰石基体材料质量的15
‑
70%,可以是15%、40%、65%、70%等,造孔剂的加入,可控制氯磷灰石多孔材料的孔隙率在10
‑
75%范围内。
[0058]
具体的,制备工艺如下:
[0059]
步骤s21,将原材料均匀混合后,采用液压机将原材料成型得到压制坯;压力为2t,
保压时间为10s;
[0060]
步骤s22,对压制坯进行烧结,烧结工艺为:升温至270
‑
400℃进行脱脂,保温时间为1.5
‑
3h,然后升温至1100
‑
1250℃烧结1
‑
2h。
[0061]
以下通过具体的实施例对本发明的氯磷灰石多孔材料进行详细阐述。
[0062]
实施例1
[0063]
本实施例的氯磷灰石多孔材料的制备方法,具体步骤如下:
[0064]
称量45.6g的na3po4·
12h2o试剂溶于0.6l蒸馏水中并充分搅拌,配制成浓度为0.2mol/l的磷酸钠溶液;然后称量22.2g的无水cacl2试剂溶于1l蒸馏水中并充分搅拌,配置成浓度为0.2mol/l的氯化钙溶液;
[0065]
将3ml氨水倒入na3po4溶液中,利用电动搅拌器持续搅拌;
[0066]
在电动搅拌器持续搅拌下,利用漏斗控制配好的cacl2溶液缓慢滴加到含氨水的na3po4溶液中,待cacl2溶液滴加完后再经过1h,停止搅拌,并将反应沉淀物陈放24h;
[0067]
利用漏斗将沉淀物过滤,然后放置于干燥箱中将其烘干;
[0068]
将烘干后的羟基磷灰石在700℃条件下焙烧1h;
[0069]
利用球磨机将羟基磷灰石和硬脂酸进行球磨,球磨后过300目标准筛。按氯磷灰石基材、硬脂酸、zno、sio2粉末按分别为10g、6.5g、0.2g、0.2g进行配料,并均匀混合;
[0070]
利用液压机混好的配粉进行压制成形,压力为2t,保压时间为10s;
[0071]
利用马弗炉将压坯进行烧结,脱脂工艺温度为360℃,保温时间2h,烧结工艺温度为1200℃,烧结时间1h。
[0072]
请结合参阅图1、图2和图3,其中图1是本发明实施例1中含氯化钠的羟基磷灰石xrd衍射图;图2是本发明实施例1的氯磷灰石基体材料的xrd衍射图;图3是本发明实施例1的氯磷灰石多孔材料的sem图。
[0073]
测得实施例1的氯磷灰石多孔材料的孔隙率为55%。
[0074]
实施例2
[0075]
本实施例的氯磷灰石多孔材料的制备方法,具体步骤如下:
[0076]
称量45.6g的na3po4·
12h2o试剂溶于0.6l蒸馏水中并充分搅拌,配制成浓度为0.2mol/l的磷酸钠溶液;然后称量22.2g的无水cacl2试剂溶于1l蒸馏水中并充分搅拌,配置成浓度为0.2mol/l的氯化钙溶液;
[0077]
将3ml氨水倒入na3po4溶液中,利用电动搅拌器持续搅拌;
[0078]
在电动搅拌器持续搅拌下,利用漏斗控制配好的cacl2溶液缓慢滴加到含氨水的na3po4溶液中,待cacl2溶液滴加完后再经过1h,停止搅拌,并将反应沉淀物陈放24h;
[0079]
利用漏斗将沉淀物过滤,然后放置于干燥箱中将其烘干;
[0080]
将烘干后的羟基磷灰石在650℃条件下焙烧2h;
[0081]
利用球磨机将羟基磷灰石和硬脂酸进行球磨,球磨后过300目标准筛。按氯磷灰石基材、硬脂酸、zno、sio2粉末按分别为10g、4g、0.3g、0.3g进行配料,并均匀混合;
[0082]
利用液压机混好的配粉进行压制成形,压力为2t,保压时间为10s;
[0083]
利用马弗炉将压坯进行烧结,脱脂工艺温度为270℃,保温时间3h,烧结工艺温度为1100℃,烧结时间1h。
[0084]
实施例3
[0085]
本实施例的氯磷灰石多孔材料的制备方法,具体步骤如下:
[0086]
称量45.6g的na3po4·
12h2o试剂溶于0.6l蒸馏水中并充分搅拌,配制成浓度为0.2mol/l的磷酸钠溶液;然后称量22.2g的无水cacl2试剂溶于1l蒸馏水中并充分搅拌,配置成浓度为0.2mol/l的氯化钙溶液;
[0087]
将3ml氨水倒入na3po4溶液中,利用电动搅拌器持续搅拌;
[0088]
在电动搅拌器持续搅拌下,利用漏斗控制配好的cacl2溶液缓慢滴加到含氨水的na3po4溶液中,待cacl2溶液滴加完后再经过1h,停止搅拌,并将反应沉淀物陈放24h;
[0089]
利用漏斗将沉淀物过滤,然后放置于干燥箱中将其烘干;
[0090]
将烘干后的羟基磷灰石在750℃条件下焙烧1h;
[0091]
利用球磨机将羟基磷灰石和硬脂酸进行球磨,球磨后过300目标准筛。按氯磷灰石基材、硬脂酸、zno、sio2粉末按分别为10g、7g、0.3g、0.3g进行配料,并均匀混合;
[0092]
利用液压机混好的配粉进行压制成形,压力为2t,保压时间为10s;
[0093]
利用马弗炉将压坯进行烧结,脱脂工艺温度为400℃,保温时间1.5h,烧结工艺温度为1250℃,烧结时间1h。
[0094]
实施例4
‑5[0095]
以实施例1的制备方法为基础,通过调整硬脂酸的含量,使氯磷灰石多孔材料的孔隙率控制为35%和72%,其他工艺条件不变,形成实施例4
‑
5。
[0096]
将实施例1、实施例4
‑
5的氯磷灰石多孔材料进行力学性能测试,测试结果如表1:
[0097]
表1:不同孔隙率对应的力学性能测试结果
[0098] 孔隙率(%)压缩强度(mpa)实施例15530实施例43542实施例57216
[0099]
由表1可以看出,当孔隙率为55%时,压缩性能高达30mpa以上,具有良好的力学性能。
[0100]
本发明提供的氯磷灰石多孔材料的制备方法,以溶液共沉积法制备含氯化钠的羟基磷灰石具有烧结活性高,成形性能好等性能特点。反应产物不会对环境造成污染,工艺简单,制备成本低。
[0101]
本发明提供的氯磷灰石多孔材料的制备方法,以硬脂酸为造孔剂,zno2、sio2粉末作为增强剂,制备的氯磷灰石材料兼具高孔隙率、高强度、表面活性高。试样表面光滑平整,不掉粉,孔隙率可控制在10%~75%,55%孔隙率时压缩性能高达30mpa以上。
[0102]
本发明的氯磷灰石多孔材料,吸附能力强,可应用于吸附重金属、污水过滤、药物雾化等领域。
[0103]
以上对本发明的实施方式作出详细说明,但本发明不局限于所描述的实施方式。对本领域的技术人员而言,在不脱离本发明的原理和精神的情况下对这些实施例进行的多种变化、修改、替换和变型均仍落入在本发明的保护范围之内。