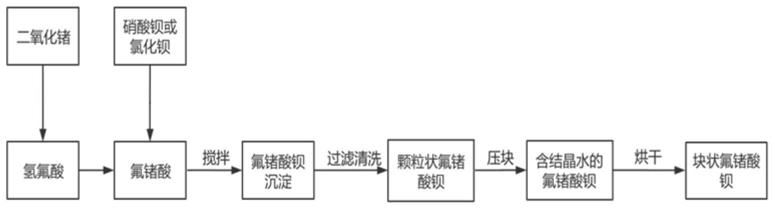
1.本发明属于四氟化锗制备技术领域,具体涉及一种利用氟锗酸钡热分解制备高纯四氟化锗的方法。
背景技术:2.高纯四氟化锗主要用于核工业领域锗同位素分离的中间体,在半导体工业中可用作掺杂剂和离子注入剂,其主要有一下几种制备方法:
3.(a)单质金属锗与氟气反应:
4.ge+2f2→
gef45.(b)二氧化锗与三氟化溴反应:
6.3geo2+4brf3→
3gef4+3o2+2br27.采用方法(a)申请号200980138501.3名称为四氟化锗的制造方法公开了一种四氟化锗的制造方法,采用稀释后的氟气与在料架上加热到一定温度的锗块进行反应,冷凝收集四氟化锗。该反应迅速并伴随大量放热,反应速率难以控制。其具体实施方法中,存在锗块反应热局部灼伤反应器的实例。其采用稀释氟气进行反应虽然可以有效控制反应速率,但不利于高效生产。且每次投料需要打开反应容器,增加了安全风险,对含有稀释气的氟气四氟化锗混合气进行冷凝也增加了资源浪费。
8.在实际生产中,方法(a)所述四氟化锗制造方法受限于氟气的纯度。我国对氟气执行的标准gb/t 26251
‑
2010最高纯度为99.0%,因氟气的性质活泼,皆采用氟氮混合气的方式进行充装,因此市面上较难获得能够生产高纯四氟化锗用的氟气。
9.虽然方法(b)可以定量生产,但其副产物会使四氟化锗引入过多杂质。
10.电子级四氟化锗作为一种离子注入剂在半导体工业中有很大的应用价值,但要求纯度要达到7n以上,故量化稳定生产高纯度四氟化锗变得十分迫切。
技术实现要素:11.本发明的主要目的是提供一种利用氟锗酸钡热分解制备高纯四氟化锗的方法,以解决四氟化锗制备的技术难题,得到高纯度的电子级四氟化锗。
12.为实现以上目的,本发明提供以下技术方案:
13.s1:将可溶性二氧化锗溶解于氢氟酸溶液,制成氟锗酸溶液,氢氟酸溶液和可溶性二氧化锗的摩尔比为6~6.25:1;
14.s2:在氟锗酸溶液中加入可溶性钡盐生成氟锗酸钡沉淀;
15.s3:将生成的氟锗酸钡沉淀使用无水乙醇清洗去除氟化氢残留,放入模具中压成块状,进行烘干。
16.其技术方案包括以下步骤:
17.(1)将可溶性二氧化锗溶解于氢氟酸溶液,制成氟锗酸溶液。
18.二氧化锗为白色粉末,可通过四氯化锗水解反应得到,二氧化锗有三种不同的形
态:无定型玻璃体、六方晶系、四方晶系,无定型玻璃体和六方晶系二氧化锗可溶于水与氢氟酸,四方晶系二氧化锗不溶于氢氟酸。四方晶系可通过加热至1086
±
5℃以上熔融后快速冷却获得无定型玻璃体二氧化锗。通过四氯化锗水解得到六方晶系二氧化锗可直接用于生产。
19.可溶性二氧化锗在氢氟酸溶液和可溶性二氧化锗的摩尔比为6:1溶液中可完全溶解,发生以下反应:
20.geo2+6hf=h2gef6+2h2o
21.geo2+h2o=h2geo322.geo2+2h2o=h4geo423.5geo2+h2o=h2ge5o
11
24.7geo2+2h2o=h4ge7o
16
25.其中h2geo3、h4geo4、h2ge5o
11
、h4ge7o
16
在氢氟酸过量时不存在。为提高锗的回收利用率,氢氟酸应过量。
26.(2)在氟锗酸溶液中加入可溶性钡盐(ba
2+
)生成氟锗酸钡沉淀。
27.在氟锗酸溶液中加入bacl2或ba(no3)2,会形成白色颗粒状bagef6沉淀,搅拌可以加快沉淀形成速度,发生以下反应:
28.ba
2+
+h2gef6=bagef6+2h
2+
29.为提高锗的回收利用率,降低废液处理难度,加入的钡盐(ba
2+
)应过量。
30.(3)将氟锗酸钡沉淀过滤、洗涤、压块、烘干得到无水氟锗酸钡
31.过滤后得到氟锗酸钡沉淀,使用无水乙醇清洗去除氟化氢残留。放入模具中压成块状,块状氟锗酸钡在热分解生产四氟化锗反应中,可减少固体杂质的引入,提高产品纯度。压块后烘干,设置烘干温度70℃,烘干时间10h,去除结晶水,使结块更牢固。若氟锗酸钡中的结晶水未去除干净,在热分解反应过程中可与四氟化锗发生反应产生hf对装置产生腐蚀。
32.(4)将无水氟锗酸钡热分解得到四氟化锗
33.将干燥后的氟锗酸钡放入石英管中,石英管一端封闭,另一端连接冷却收集器。在干燥的氮气保护气氛下加热至600℃~800℃,反应时间1h~2h,温度越高,反应速率越快。
34.bagef6→
baf2+gef435.(5)将生成的四氟化锗冷却收集得到四氟化锗
36.由于四氟化锗的蒸汽压很高,在石英管中生成的四氟化锗很快会溢出至冷却收集器。冷却收集装置温度为
‑
80℃~
‑
50℃,四氟化锗在常压下于
‑
36.5℃凝华,降低冷却温度可提高收集速率。反应结束后对含有四氟化锗结晶的冷却收集器抽真空至
‑
0.1~
‑
0.09mpa。
37.(6)四氟化锗提纯制备高纯四氟化锗
38.将收集得到的四氟化锗再多次冷却收集后再抽真空,去除轻杂质即可获得高纯四氟化锗。然后提高收集器的温度使四氟化锗挥发,打开收集钢瓶阀门,控制钢瓶温度
‑
30℃~0℃充装至钢瓶压力发生明显变化时,停止充装,获得成品高纯四氟化锗。
39.本发明使用氟锗酸钡在600℃~700℃可快速分解生成四氟化锗,锗的收率高,其固体副产物氟化钡具有非常广泛的应用领域和科学应用研究价值。其反应不需要氟气参
与,对反应装置的要求低,配置简单,容易控制,其热分解生产的四氟化锗纯度高,杂质少。
附图说明
40.图1为本发明氟锗酸钡制备方法的流程图;
41.图2为本发明利用氟锗酸钡热分解制备高纯四氟化锗方法的流程图;
42.其中:
43.1、块状氟锗酸钡;2、烘箱;3、石英管;4、干燥氮气;5、一级冷却收集器;6、二级冷却收集器;7、三级冷却收集器;8、收集气瓶;9、尾气出口。
具体实施方式
44.以下参照附图和实施例对本发明利用氟锗酸钡热分解制备高纯四氟化锗的方法进行详细说明,本发明所使用的化学试剂无特别说明均为优级纯,均可以从市场进行购买。
45.实施例1
46.在25℃条件下,采用100g可溶性二氧化锗投入250ml的25mol/l hf氢氟酸溶液中,搅拌10min,可见所制得氟锗酸和氢氟酸混合液澄清透明。加入205g bacl2粉末,搅拌10min,使其充分沉淀,可见溶液内出现白色颗粒状沉淀。过滤后用纯水洗涤一次结晶,用无水乙醇洗涤三次。压制成10*10*10mm的块体,放入烘箱,设置烘干温度70℃,烘干时间10h,获得产品311.7g。二氧化锗与氢氟酸反应完全,氢氟酸溶液和可溶性二氧化锗的摩尔比为6.53:1,大于6~6.25:1,二氧化锗反应完全后溶液内剩余大量的氟化氢,投入钡盐后氯化钡与氢氟酸反应,生成微溶于水的氟化钡混杂在氟锗酸钡中,影响后续热分解收率。
47.实施例2
48.在25℃环境下,采用100g可溶性二氧化锗投入235ml的25mol/l hf氢氟酸溶液中,搅拌10min,可见所制得氟锗酸和氢氟酸混合液澄清透明。加入205g bacl2粉末,搅拌10min,使其充分沉淀。可见溶液内出现白色颗粒状沉淀。过滤后用纯水洗涤一次结晶,用无水乙醇洗涤三次。压制成10*10*10mm的块体,放入烘箱,设置烘干温度70℃,烘干时间10h,获得产品307.9g,经热重法检测,其氟锗酸钡含量为99.6%,锗的综合回收率为99.0%。
49.在石英管内通入干燥氮气4,对体系进行气体置换,取制得100.0g块状氟锗酸钡放入石英管3中,石英管内压强为常压。设置石英管温度为700℃,一级冷却收集器5温度为
‑
70℃,观察石英管压力变化判断反应进行程度。加热后40min左右,其压力不发生明显变化。为使氟锗酸钡充分分解,保持加热温度至1h。一级冷却收集收集时间与反应时间一致。反应完成后关闭石英管与一级冷却收集器间的连接阀,打开尾气出口9,在石英管内内通干燥氮气,吹扫出四氟化锗。尾气处理液为水,处理完成后打开石英管,取出管内氟化钡结晶于干燥处存储。
50.关闭一、二、三级冷却收集器6、7间阀门,对三个冷却收集器抽真空至
‑
0.1mpa。打开一级、二级冷却收集器连接阀,涉及二级冷却收集器温度
‑
70℃,一级冷却收集器温度缓慢升至10℃。观察压力表,压力值升高后降低,当压力不在降低时,二级冷却收集完成,关闭一级、二级冷却收集器连接阀,对二级冷却收集器抽真空至
‑
0.1mpa。循环操作至三级冷却收集完成,设置充装钢瓶温度
‑
30℃,进行产品充装。检测称重获得99.9%以上四氟化锗45.0g,综合锗收率为97.6%。
51.实施例3
52.25℃环境下,采用500g可溶性二氧化锗投入1.15l的25mol/l hf氢氟酸溶液中,搅拌20min,可见所制得氟锗酸和氢氟酸混合液澄清透明。加入990.0g bacl2粉末,搅拌30min,使其充分沉淀。可见溶液内出现白色颗粒状沉淀。过滤后用纯水洗涤一次结晶,用无水乙醇洗涤三次。压制成10*10*10mm的块体,放入烘箱,设置烘干温度70℃,烘干时间10h,获得产品1546.7g,经热重法检测,其氟锗酸钡含量为99.7%,锗的综合回收率为99.6%。
53.在石英管内通入干燥氮气4,对体系进行气体置换,取制得1000.0g块状氟锗酸钡放入石英管3中,石英管内压强为常压。设置石英管温度为650℃,一级冷却收集器5温度为
‑
70℃,观察石英管压力变化判断反应进行程度。加热后60min左右,其压力不发生明显变化。为使氟锗酸钡充分分解,保持加热至1.5h。一级冷却收集收集时间与反应时间一致。反应完成后关闭石英管与一级冷却收集器间的连接阀,打开尾气出口9,在石英管内内通干燥氮气,吹扫出四氟化锗。尾气处理液为水,处理完成后打开石英管,取出管内氟化钡结晶于干燥处存储。
54.关闭一、二、三级冷却收集器6、7间阀门,对三个冷却收集器抽真空至
‑
0.1mpa。打开一级、二级冷却收集器连接阀,涉及二级冷却收集器温度
‑
70℃,一级冷却收集器温度缓慢升至10℃。观察压力表,压力值升高后降低,当压力不在降低时,二级冷却收集完成,关闭一级、二级冷却收集器连接阀,对二级冷却收集器抽真空至
‑
0.1mpa。循环操作至三级冷却收集完成,设置充装钢瓶温度
‑
30℃,进行产品充装。检测称重获得99.9%以上四氟化锗433.5g,综合锗收率为96.0%。
55.控制氢氟酸过量可提高二氧化锗的反应程度,过量太多会使产物中混杂氟化钡。
56.实施例4
57.在25℃环境下,采用100g可溶性二氧化锗投入235ml的25mol/l hf氢氟酸溶液中,搅拌10min,可见所制得氟锗酸和氢氟酸混合液澄清透明。加入260.0g ba(no3)2粉末,搅拌10min,使其充分沉淀。可见溶液内出现白色颗粒状沉淀。过滤后用纯水洗涤一次结晶,用无水乙醇洗涤三次。压制成10*10*10mm的块体,放入烘箱,设置烘干温度70℃,烘干时间10h,获得产品305.6g,经热重法检测,其氟锗酸钡含量为99.3%,锗的综合回收率为98.0%。
58.在石英管内通入干燥氮气4,对体系进行气体置换,取制得100.0g块状氟锗酸钡放入石英管3中,石英管内压强为常压。设置石英管温度为700℃,一级冷却收集器5温度为
‑
70℃,观察石英管压力变化判断反应进行程度。加热后40min左右,其压力不发生明显变化。为使氟锗酸钡充分分解,保持加热温度至1h。一级冷却收集收集时间与反应时间一致。反应完成后关闭石英管与一级冷却收集器间的连接阀,打开尾气出口9,在石英管内内通干燥氮气,吹扫出四氟化锗。尾气处理液为水,处理完成后打开石英管,取出管内氟化钡结晶于干燥处存储。
59.关闭一、二、三级冷却收集器6、7间阀门,对三个冷却收集器抽真空至
‑
0.1mpa。打开一级、二级冷却收集器连接阀,涉及二级冷却收集器温度
‑
70℃,一级冷却收集器温度缓慢升至10℃。观察压力表,压力值升高后降低,当压力不在降低时,二级冷却收集完成,关闭一级、二级冷却收集器连接阀,对二级冷却收集器抽真空至
‑
0.1mpa。循环操作至三级冷却收集完成,设置充装钢瓶温度
‑
30℃,进行产品充装。检测称重获得99.9%以上四氟化锗44.1g,综合锗收率为96.7%。
60.基于以上实施例对本发明做出说明,但本发明不受以上实施例的限定。
61.本发明操作简单,反应易于控制,四氟化锗产物纯度高,设备要求简单。