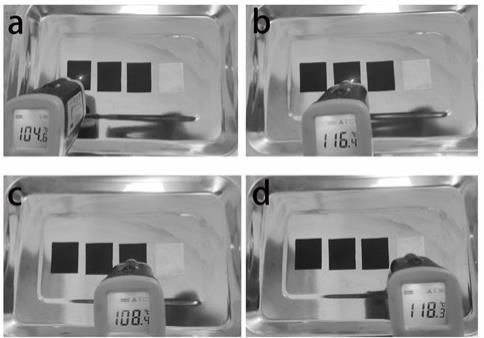
1.本发明涉及石墨烯制备领域,公开了一种复合熔盐研磨剥离制备石墨烯的方法。
背景技术:2.石墨烯是由碳原子构成的具有单原子层厚度的二维晶体,碳原子之间以sp2 杂化方式互相键合形成蜂窝状晶格网络,其基本结构单元是苯六元环,可看作是一层被剥离的单层石墨片,其厚度仅为0.35 nm。同其他云母、二硫化钼、滑石粉、蒙脱土、硼化物等二维材料一样,石墨的层间由很高键能的氢键连接。因此,为了将石墨剥离为单层或多层的石墨烯,关键的问题是克服石墨层间氢键能。
3.目前传统的化学氧化法制备石墨烯,其本质是利用强氧化剂(浓硫酸)破坏石墨层间的氢键,从而使得石墨被轻易的剥离为石墨烯,适合规模化制备。然而由于使用大量的强氧化剂,极易造成环境污染、成本高。另外,由于使用强氧化剂使得石墨烯的晶格受到损伤,石墨烯的增强性、电性能大幅下降。目前市面上大部分为氧化石墨烯,其应用具有很大的限制。
4.从理论上分析,只要有效地破坏石墨层间的氢键,制备石墨烯变为可能。为此,采用以机械力为代表的物理法,通过机械力能、电能、磁能、光能、声能等克服石墨层间氢键剥离制备石墨烯成为无污染、规模化、低成本化制备高品质石墨烯的最佳选择。特别是,通过机械力剥离制备石墨烯由于设备简单,产量规模大,生产环保,逐步成为生产石墨烯的主流技术。根据目前已公开的相关技术,已有采用球磨机、砂磨机、三辊磨、螺杆挤出机等研磨剪切设备剥离制备石墨烯的技术。
5.在生产实践中,石墨被逐步细化剥离,随着粒径的减小,剪切对石墨产生的剪切力越来越小,造成剥离效率低,而且得到的石墨烯是石墨、石墨烯微片、多层石墨烯、单层石墨烯的复合物,石墨烯质量较低。随着机械剥离石墨烯在锂电池、散热涂料、印刷导电浆料等高端产品的应用需求,对机械剥离石墨烯的质量要求越来越高,因此,需要进一步提升机械剥离制备石墨烯的质量和生产效率。
6.中国发明专利申请号201010179119.1公开了高效率低成本机械剥离制备石墨烯或氧化石墨烯的方法,利用固体颗粒和液体工作介质(或气体工作介质)采用机械剥离碳素材料后分离;获得石墨烯或氧化石墨烯;碳素材料为石墨粉、膨胀石墨、可膨胀石墨或氧化石墨粉。
7.中国发明专利申请号201910254520.8公开了一种通过机械剥离制备石墨烯的方法及其制备的石墨烯,该石墨烯的原料按质量百分比计包含:石墨粉4~25%,溶剂70~95%,表面活性剂0.1~5%。该发明还提供了该通过机械剥离制备石墨烯的方法,其包含:步骤(1),按比例称取各原料;步骤(2),对石墨粉进行膨化处理;步骤(3),将膨化石墨与溶剂、分散剂混合,进行分散处理;步骤(4),将分散液进行机械剥离;步骤(5),将处理液进行均匀化处理;步骤6,将处理液通过喷雾干燥,得到石墨烯粉体。
8.在生产实践中,石墨被逐步细化剥离,随着粒径的减小,剪切对石墨产生的剪切力
越来越小,造成剥离效率低,而且得到的石墨烯是石墨、石墨烯微片、多层石墨烯、单层石墨烯的复合物,石墨烯质量较低。随着机械剥离石墨烯在锂电池、散热涂料、印刷导电浆料等高端产品的应用需求,对机械剥离石墨烯的质量要求越来越高,因此,需要进一步提升机械剥离制备石墨烯的质量和生产效率。
技术实现要素:9.通过上述可见,目前采用机械剥离制备石墨烯的方法具有剥离效率低、石墨烯质量较差的缺陷。
10.本发明通过以下技术方案解决上述问题:一种复合熔盐研磨剥离制备石墨烯的方法,制备的具体过程为:(1)先将氯化钠与氯化钙盐混合均匀,加热熔融形成复合熔盐,然后将膨胀石墨加入复合熔盐中,搅拌分散均匀,使熔盐与膨胀石墨的表面、层间嵌入形成整体,再冷却、粉碎,得到石墨与盐镶嵌的大颗粒;(2)将步骤(1)得到的石墨与盐镶嵌的大颗粒、分散剂、乙醇、研磨介质在球磨机中研磨3~5h,在大颗粒被不断研磨的同时,镶嵌的石墨被剥离形成石墨烯;(3)先将步骤(2)研磨的物料用粗网过滤,除去研磨介质,然后细网过滤,除去乙醇,进一步通过反复水洗除脱盐,干燥,得到石墨烯粉。
11.公知的,通过机械研磨,破坏石墨烯层间的氢键,可将石墨层层剥离得到石墨烯。然而,在机械研磨过程中,随着颗粒料的逐步细化,研磨越来越困难,效率越来越低。尤其是对于纳米级别的颗粒,研磨介质球之间的间隙较大,难以形成良好的研磨剪切力。为了在纳米级别实现良好的剪切研磨,需要研磨介质的粒径足够小。目前在砂磨机中使用的研磨介质最小达到了0.1mm,但足够小粒径的研磨介质难以分离,同时研磨剪切有限。本发明通过使盐类加热熔融形成熔盐,将熔盐镶嵌于膨胀石墨的表面及层间,熔盐相当于支撑体,使石墨处在一个较大的颗粒,从而与研磨介质接触充分,剪切力强,克服了单纯石墨逐步研磨细化影响研磨剥离效率的问题,提高了石墨烯的质量。
12.氯化钠与氯化钙都是易溶于水的盐类,采用氯化钠与氯化钙形成复合盐,可使熔融温度降低,有利于完全熔融及均匀混合。
13.作为本发明的优选,步骤(1)所述加热熔融的温度为810℃。
14.膨胀石墨是一种新型功能性碳素材料,是由天然石墨鳞片经插层、水洗、干燥、高温膨化得到的一种疏松多孔的蠕虫状物质。 膨胀石墨除了具备天然石墨本身的耐冷热、耐腐蚀、自润滑等优良性能以外,还具有天然石墨所没有的柔软、压缩回弹性、吸附性、生态环境协调性、生物相容性、耐辐射性等特性。膨胀石墨是在石墨层间c轴方向膨胀的石墨,与天然石墨相比,通过膨胀使石墨粒子的层间结合力减弱,因而更容易被剥离形成石墨烯。
15.作为本发明的优选,步骤(1)所述膨胀石墨的粒径为50~100μm。
16.进一步的,本发明在机械研磨体系中加入了乙醇,复合熔盐中的氯化钙溶于乙醇,使得石墨与盐镶嵌的大颗粒的强度降低,有利于被研磨细化,而氯化钠不溶于乙醇,可作为石墨的支撑骨架,保持较大的颗粒状态,实现稳定的良好剪切。
17.作为本发明的优选,步骤(1)所述各原料配比为,按重量份计,氯化钠5重量份、氯化钙1重量份、膨胀石墨2重量份。
18.优选的,步骤(2)所述分散剂为聚乙烯吡咯烷酮。进一步优选的,所述聚乙烯吡咯烷酮的数均分子量为30万。
19.优选的,步骤(2)所述乙醇的纯度为99%。
20.研磨介质是研磨时的载能体,通过研磨介质的相互摩擦、剪切及碰撞,实现物料颗粒的分散或破碎。氧化锆陶瓷球在常温下具有高强度及高韧性、耐磨性好、耐高温耐腐蚀、刚度高、不导磁、电绝缘性好,在作为研磨介质时,由于其圆整度好,表面光滑,对设备磨损小,并且由于其韧性好,在高速研磨时不开裂不剥离,是非常理想的研磨介质。
21.作为本发明的优选,步骤(2)所述研磨介质为氧化锆陶瓷球。作为本发明的进一步优选,所述氧化锆陶瓷球的粒径为0.3mm。
22.进一步优选的,步骤(2)所述各原料配比为,按重量份计,石墨与盐镶嵌的大颗粒10~20重量份、分散剂0.5~0.8重量份、乙醇70~80重量份、研磨介质60~100重量份。
23.本发明提供了一种复合熔盐研磨剥离制备石墨烯的方法,将氯化钠与氯化钙盐混合均匀,加热熔融形成复合熔盐,然后将膨胀石墨加入复合熔盐中,搅拌分散均匀,使熔盐与膨胀石墨的表面、层间嵌入形成整体,再冷却、粉碎,得到石墨与盐镶嵌的大颗粒;将石墨与盐镶嵌的大颗粒、分散剂、乙醇、研磨介质在球磨机中研磨3~5h,在大颗粒被不断研磨的同时,镶嵌的石墨被剥离形成石墨烯;将研磨物料用粗网过滤,除去研磨介质,然后细网过滤,除去乙醇,进一步通过反复水洗除脱盐,干燥,即可。
24.本发明提供了一种复合熔盐研磨剥离制备石墨烯的方法,与现有技术相比,其突出的特点和优异的效果在于:1、提出了采用复合熔盐对膨胀石墨进行镶嵌,再球磨剥离制备石墨烯的方法。
25.2、通过复合熔盐的镶嵌,熔盐相当于支撑体,使石墨处在一个较大的颗粒,从而与研磨介质接触充分,剪切力强,克服了单纯石墨逐步研磨细化影响研磨剥离效率的问题。
26.3、由于研磨后的复合盐易溶于水,通过简单的水洗即可除去,过程简单,成本低。
27.4、通过选用氯化钠和氯化钙组成的复合盐,氯化钙溶于乙醇,使大颗粒强度降低利于被研磨细化,氯化钠不溶于乙醇,可作为石墨的支撑骨架保持石墨在较大的颗粒条件下与研磨介质剪切剥离,由此,不但提高了研磨的效率,而且得到的石墨烯质量高。
附图说明
28.图1为对测试铝板表面温度变化测试的现场图,其中,a为实施例6石墨烯配制的散热涂料涂层表面20min时的温度测试,b为对比例1石墨烯配制的散热涂料涂层表面20min时的温度测试,c为对比例2石墨烯配制的散热涂料涂层表面20min时的温度测试,d为空白样涂层表面20min时的温度测试。
29.具体实施方式
30.以下通过具体实施方式对本发明作进一步的详细说明,但不应将此理解为本发明的范围仅限于以下的实例。在不脱离本发明上述方法思想的情况下,根据本领域普通技术知识和惯用手段做出的各种替换或变更,均应包含在本发明的范围内。
31.实施例1
(1)先将氯化钠与氯化钙盐混合均匀,加热熔融形成复合熔盐,然后将膨胀石墨加入复合熔盐中,搅拌分散均匀,使熔盐与膨胀石墨的表面、层间嵌入形成整体,再冷却、粉碎,得到石墨与盐镶嵌的大颗粒;加热熔融的温度为810℃;膨胀石墨的粒径为50μm;分散体系中,按重量份计,氯化钠5重量份、氯化钙1重量份、膨胀石墨2重量份;(2)将步骤(1)得到的石墨与盐镶嵌的大颗粒、分散剂、乙醇、研磨介质在球磨机中研磨4h,在大颗粒被不断研磨的同时,镶嵌的石墨被剥离形成石墨烯;分散剂为数均分子量30万的聚乙烯吡咯烷酮;乙醇的纯度为99%;研磨介质为粒径0.3mm的氧化锆陶瓷球;研磨体系中,按重量份计,石墨与盐镶嵌的大颗粒15重量份、分散剂0.6重量份、乙醇75重量份、研磨介质70重量份;(3)先将步骤(2)研磨的物料用粗网过滤,除去研磨介质,然后细网过滤,除去乙醇,进一步通过反复水洗除脱盐,干燥,得到石墨烯粉。
32.实施例2(1)先将氯化钠与氯化钙盐混合均匀,加热熔融形成复合熔盐,然后将膨胀石墨加入复合熔盐中,搅拌分散均匀,使熔盐与膨胀石墨的表面、层间嵌入形成整体,再冷却、粉碎,得到石墨与盐镶嵌的大颗粒;加热熔融的温度为810℃;膨胀石墨的粒径为50μm;分散体系中,按重量份计,氯化钠5重量份、氯化钙1重量份、膨胀石墨2重量份;(2)将步骤(1)得到的石墨与盐镶嵌的大颗粒、分散剂、乙醇、研磨介质在球磨机中研磨4.5h,在大颗粒被不断研磨的同时,镶嵌的石墨被剥离形成石墨烯;分散剂为数均分子量30万的聚乙烯吡咯烷酮;乙醇的纯度为99%;研磨介质为粒径0.3mm的氧化锆陶瓷球;研磨体系中,按重量份计,石墨与盐镶嵌的大颗粒15重量份、分散剂0.8重量份、乙醇75重量份、研磨介质80重量份;(3)先将步骤(2)研磨的物料用粗网过滤,除去研磨介质,然后细网过滤,除去乙醇,进一步通过反复水洗除脱盐,干燥,得到石墨烯粉。
33.实施例3(1)先将氯化钠与氯化钙盐混合均匀,加热熔融形成复合熔盐,然后将膨胀石墨加入复合熔盐中,搅拌分散均匀,使熔盐与膨胀石墨的表面、层间嵌入形成整体,再冷却、粉碎,得到石墨与盐镶嵌的大颗粒;加热熔融的温度为810℃;膨胀石墨的粒径为50μm;分散体系中,按重量份计,氯化钠5重量份、氯化钙1重量份、膨胀石墨2重量份;(2)将步骤(1)得到的石墨与盐镶嵌的大颗粒、分散剂、乙醇、研磨介质在球磨机中研磨3.5h,在大颗粒被不断研磨的同时,镶嵌的石墨被剥离形成石墨烯;分散剂为数均分子量30万的聚乙烯吡咯烷酮;乙醇的纯度为99%;研磨介质为粒径0.3mm的氧化锆陶瓷球;研磨体系中,按重量份计,石墨与盐镶嵌的大颗粒13重量份、分散剂0.7重量份、乙醇72重量份、研磨介质70重量份;(3)先将步骤(2)研磨的物料用粗网过滤,除去研磨介质,然后细网过滤,除去乙醇,进一步通过反复水洗除脱盐,干燥,得到石墨烯粉。
34.实施例4(1)先将氯化钠与氯化钙盐混合均匀,加热熔融形成复合熔盐,然后将膨胀石墨加入复合熔盐中,搅拌分散均匀,使熔盐与膨胀石墨的表面、层间嵌入形成整体,再冷却、粉碎,得到石墨与盐镶嵌的大颗粒;加热熔融的温度为810℃;膨胀石墨的粒径为50μm;
分散体系中,按重量份计,氯化钠5重量份、氯化钙1重量份、膨胀石墨2重量份;(2)将步骤(1)得到的石墨与盐镶嵌的大颗粒、分散剂、乙醇、研磨介质在球磨机中研磨4h,在大颗粒被不断研磨的同时,镶嵌的石墨被剥离形成石墨烯;分散剂为数均分子量30万的聚乙烯吡咯烷酮;乙醇的纯度为99%;研磨介质为粒径0.3mm的氧化锆陶瓷球;研磨体系中,按重量份计,石墨与盐镶嵌的大颗粒12重量份、分散剂0.7重量份、乙醇77重量份、研磨介质80重量份;(3)先将步骤(2)研磨的物料用粗网过滤,除去研磨介质,然后细网过滤,除去乙醇,进一步通过反复水洗除脱盐,干燥,得到石墨烯粉。
35.实施例5(1)先将氯化钠与氯化钙盐混合均匀,加热熔融形成复合熔盐,然后将膨胀石墨加入复合熔盐中,搅拌分散均匀,使熔盐与膨胀石墨的表面、层间嵌入形成整体,再冷却、粉碎,得到石墨与盐镶嵌的大颗粒;加热熔融的温度为810℃;膨胀石墨的粒径为50μm;分散体系中,按重量份计,氯化钠5重量份、氯化钙1重量份、膨胀石墨2重量份;(2)将步骤(1)得到的石墨与盐镶嵌的大颗粒、分散剂、乙醇、研磨介质在球磨机中研磨3h,在大颗粒被不断研磨的同时,镶嵌的石墨被剥离形成石墨烯;分散剂为数均分子量30万的聚乙烯吡咯烷酮;乙醇的纯度为99%;研磨介质为粒径0.3mm的氧化锆陶瓷球;研磨体系中,按重量份计,石墨与盐镶嵌的大颗粒20重量份、分散剂0.8重量份、乙醇70重量份、研磨介质100重量份;(3)先将步骤(2)研磨的物料用粗网过滤,除去研磨介质,然后细网过滤,除去乙醇,进一步通过反复水洗除脱盐,干燥,得到石墨烯粉。
36.实施例6(1)先将氯化钠与氯化钙盐混合均匀,加热熔融形成复合熔盐,然后将膨胀石墨加入复合熔盐中,搅拌分散均匀,使熔盐与膨胀石墨的表面、层间嵌入形成整体,再冷却、粉碎,得到石墨与盐镶嵌的大颗粒;加热熔融的温度为810℃;膨胀石墨的粒径为50μm;分散体系中,按重量份计,氯化钠5重量份、氯化钙1重量份、膨胀石墨2重量份;(2)将步骤(1)得到的石墨与盐镶嵌的大颗粒、分散剂、乙醇、研磨介质在球磨机中研磨5h,在大颗粒被不断研磨的同时,镶嵌的石墨被剥离形成石墨烯;分散剂为数均分子量30万的聚乙烯吡咯烷酮;乙醇的纯度为99%;研磨介质为粒径0.3mm的氧化锆陶瓷球;研磨体系中,按重量份计,石墨与盐镶嵌的大颗粒20重量份、分散剂0.5重量份、乙醇80重量份、研磨介质60重量份;(3)先将步骤(2)研磨的物料用粗网过滤,除去研磨介质,然后细网过滤,除去乙醇,进一步通过反复水洗除脱盐,干燥,得到石墨烯粉。
37.对比例1(1)将膨胀石墨、分散剂、乙醇、研磨介质在球磨机中研磨5h;分散剂为数均分子量30万的聚乙烯吡咯烷酮;乙醇的纯度为99%;研磨介质为粒径0.3mm的氧化锆陶瓷球;膨胀石墨的粒径为50μm;研磨体系中,按重量份计,膨胀石墨5重量份、分散剂0.5重量份、乙醇80重量份、研磨介质60重量份;(2)先将步骤(1)研磨的物料用粗网过滤,除去研磨介质,然后细网过滤,除去乙
醇,干燥,得到石墨烯粉。
38.对比例1没有将膨胀石墨与熔盐镶嵌复合,而是直接以膨胀石墨与分散剂、乙醇、研磨介质在球磨机中研磨,其他制备条件与实施例6相同。
39.对比例2(1)先将氯化钠加热熔融形成熔盐,然后将膨胀石墨加入熔盐中,搅拌分散均匀,使熔盐与膨胀石墨的表面、层间嵌入形成整体,再冷却、粉碎,得到石墨与盐镶嵌的大颗粒;膨胀石墨的粒径为50μm;分散体系中,按重量份计,氯化钠5重量份、膨胀石墨2重量份;(2)将步骤(1)得到的石墨与盐镶嵌的大颗粒、分散剂、乙醇、研磨介质在球磨机中研磨5h,在大颗粒被不断研磨的同时,镶嵌的石墨被剥离形成石墨烯;分散剂为数均分子量30万的聚乙烯吡咯烷酮;乙醇的纯度为99%;研磨介质为粒径0.3mm的氧化锆陶瓷球;研磨体系中,按重量份计,石墨与盐镶嵌的大颗粒20重量份、分散剂0.5重量份、乙醇80重量份、研磨介质60重量份;(3)先将步骤(2)研磨的物料用粗网过滤,除去研磨介质,然后细网过滤,除去乙醇,进一步通过反复水洗除脱盐,干燥,得到石墨烯粉。
40.对比例2没有加入氯化钙,其他制备条件与实施例6相同。
41.石墨烯性能验证:由于石墨烯很难直观的判定质量,本次通过将石墨烯制备成散热涂料,通过散热性间接衡量石墨烯的质量。将实施例1~6、对比例1~2得到的石墨烯50g加入300ml水性氟碳乳液分散成散热涂料,然后在厚度为1mm的铝板上自流平自然干燥48h,未涂涂料的铝板为空白参比样,然后放置在120℃的恒温板上,涂层向上,测试涂层表面温度的变化。
42.由表1可知:本发明得到的石墨烯具有良好的热辐射性,从而及时将热辐射散出,使涂层温度保持在相对较低的水平;对比例1直接以膨胀石墨进行研磨,在相同的研磨时间内,研磨制得的石墨烯的纯度、质量不高,热辐射相对较弱,散热效果较差;对比例2由于没有加入氯化钙,导致氯化钠单独熔融镶嵌的颗粒不易被磨碎,研磨能耗高,且在相同的研磨时间内,研磨制得的石墨烯的纯度、质量不高,热辐射相对较弱,散热效果稍差。
43.图1为对测试铝板表面温度变化测试的现场图,其中,a为实施例6石墨烯配制的散热涂料涂层表面20min时的温度测试,b为对比例1石墨烯配制的散热涂料涂层表面20min时的温度测试,c为对比例2石墨烯配制的散热涂料涂层表面20min时的温度测试,d为空白样涂层表面20min时的温度测试。
44.表1:
性能指标实施例1实施例2实施例3实施例4实施例5实施例6对比例1对比例2空白样5min温度(℃)82.782.182.582.882.481.999.588.5113.710min温度(℃)97.697.197.497.797.396.8112.1103.5115.515min温度(℃)103.2102.6102.9103.4102.7102.4114.7106.2116.220min温度(℃)104.2104.1104.3104.7103.9104.6116.4108.4118.3