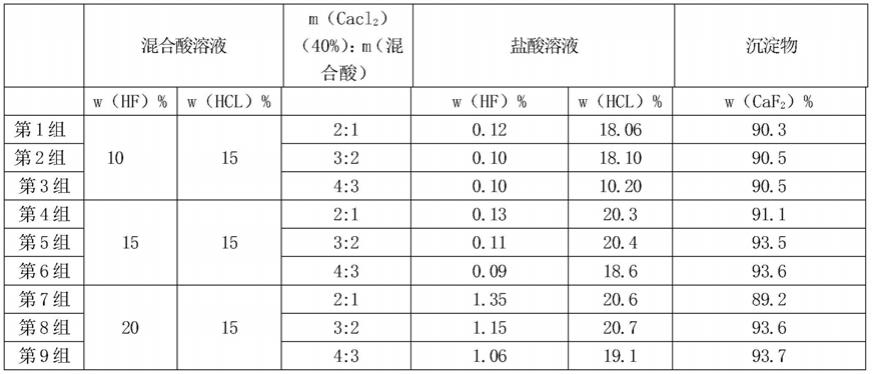
1.本发明属于废酸回收利用领域,具体涉及一种利用废酸生产高纯氟化钙及提浓废盐酸的方法。
背景技术:2.随着半导体、电子化学等行业的不断发展,酸性及碱性的刻蚀清洗液等废酸产量越来越多。在其生产过程中由于工艺需要,产生了大量的含氢氟酸和盐酸的混合酸。该混合酸的组成为氢氟酸、盐酸、水、还有少量的其他杂质(主要为硅化物)。在日常生活中,该混合酸无法直接销售,一般经过废水中和除氟后排放处理。废液如处理不好,会带来严重的环境污染。
技术实现要素:3.本发明的目的是提供一种利用废酸生产高纯氟化钙及提浓废盐酸的方法,以解决现有大量的含氢氟酸和盐酸的混合酸不能有效再利用的问题。
4.本发明采用以下技术方案:一种利用废酸生产高纯氟化钙及提浓废盐酸的方法,包括以下步骤:
5.步骤1:将含氢氟酸、盐酸的混合酸进行过滤,将过滤后的混合酸加热至恒温50
‑
60℃搅拌;
6.步骤2:向经步骤1处理得到的混合酸溶液中滴加氯化钙溶液,搅拌反应结束后得到混合溶液,对混合溶液进行真空抽滤处理,得到盐酸溶液和沉淀物;
7.步骤3:向沉淀物中加入氢氧化钠溶液,搅拌反应得到混合物,将混合物过滤分离出滤渣和碱性滤液,滤渣用去离子水冲洗后再烘干粉碎,得到高纯度氟化钙。
8.进一步的,在步骤2中,氯化钙溶液与混合酸的质量比为(4:3)~(2:1),氯化钙溶液的浓度为10~40%。
9.进一步的,在步骤2中,氯化钙溶液与混合酸的质量比为3:2。
10.进一步的,在步骤3中,加入浓度为10%~30%的naoh溶液,对过滤分离出的滤渣进行一次水洗后得到氟化钙。
11.进一步的,在步骤3中,搅拌反应时间为20
‑
30min,烘干温度为100℃
‑
120℃,烘干时间1
‑
2h。
12.本发明的有益效果是:本发明的方法先在含盐酸、氢氟酸的废酸中按一定速度滴加氯化钙溶液,使氯化钙与氢氟酸反应生成氟化钙析出沉淀,剩余水溶液为浓度提高了的盐酸;再将沉淀物用氢氧化钠水溶液碱溶除硅后干燥即可得到高纯度氟化钙固体。本发明得到的氟化钙纯度高,杂质少,可直接销售或使用;浓度提高了的盐酸溶液可以出售或者用于废水中和等方面;降低污水中和氟离子处理成本;混合废酸得到循环利用,达到环境保护、资源利用的目的,具有明显的社会效益和经济效益。
具体实施方式
13.下面结合具体实施方式对本发明进行详细说明。
14.本发明提供了一种利用废酸生产高纯氟化钙及提浓废盐酸的方法,包括以下步骤:
15.步骤1:将含氢氟酸、盐酸的混合酸进行过滤,将过滤后的混合酸加热至恒温50
‑
60℃搅拌;
16.步骤2:向经所述步骤1处理得到的混合酸溶液中滴加氯化钙溶液,搅拌反应结束后得到混合溶液,对混合溶液进行真空抽滤处理,得到盐酸溶液和沉淀物。氯化钙与混合酸中的氢氟酸反应生成盐酸,则相对于原始废酸来说,经步骤2处理得到的盐酸的浓度提高了,该浓度提高了的盐酸溶液可以出售或者用于废水中和。
17.步骤3:向所述沉淀物中加入氢氧化钠溶液,搅拌反应得到混合物,将混合物过滤分离出滤渣和碱性滤液,滤渣用去离子水冲洗后再烘干粉碎,得到高纯度氟化钙。
18.在一些实施例中,在所述步骤2中,氯化钙溶液与所述混合酸的质量比为(4:3)~(2:1),氯化钙溶液的浓度为10~40%。氯化钙的作用主要是与混酸中氢氟酸反应生成氟化钙和盐酸,一般来讲废弃混酸中氢氟酸浓度不会超过使用前浓度,电子级氢氟酸浓度为49%。故40%的氯化钙就可以满足与混酸中氢氟酸完全反应。氯化钙浓度超过40%多余氯化钙不参与反应,反而会带入新的污染。
19.在一些实施例中,在步骤2中,氯化钙溶液与所述混合酸的质量比为3:2。
20.在一些实施例中,在所述步骤3中,加入浓度为10%~30%的naoh溶液,对过滤分离出的所述滤渣进行一次水洗后得到氟化钙。氢氧化钠的作用为碱洗除硅,氟化钙中杂质硅不会超过30%,故氢氧化钠浓度10
‑
30%之间就可满足除硅要求。氧化钠碱洗除硅后还要经过水洗,氢氧化钠含量超过30%,水洗时氢氧化钠与水会有大量放热现象发生,不利于人员操作。
21.在一些实施例中,在所述步骤3中,搅拌反应时间为20
‑
30min,烘干温度为100℃
‑
120℃,烘干时间1
‑
2h。
22.在一些实施例中,将所述步骤3中分离出的碱性滤液排入酸性废水进行中和利用。
23.实施例1
24.步骤1:将含10%质量比的氢氟酸、15%质量比盐酸的混合酸进行过滤除杂,将过滤后的混合酸加热至恒温50℃搅拌。
25.步骤2:向经所述步骤1处理得到的混合酸溶液中滴加浓度为10%的氯化钙溶液,搅拌反应10分钟得到混合溶液,反应结束后,对所述混合溶液进行真空抽滤处理,得到浓度为18.06%的盐酸溶液和沉淀物。其中,氯化钙溶液与混合酸溶液的质量比分别为2:1。
26.步骤3:在沉淀物中加入浓度为10%的氢氧化钠溶液搅拌反应20min得到混合物,将混合物过滤分离出滤渣和碱性滤液,滤渣用去离子水冲洗后再烘干粉碎烘干温度为105℃,烘干时间1.6h,得到质量比为90.3%的氟化钙。
27.实施例2
28.步骤1:将含15%质量比的氢氟酸、15%质量比的盐酸的混合酸进行过滤除杂,将过滤后的混合酸加热至恒温55℃搅拌。
29.步骤2:向经所述步骤1处理得到的混合酸溶液中滴加浓度为40%的氯化钙溶液,
搅拌反应10分钟得到混合溶液,反应结束后,对所述混合溶液进行真空抽滤处理,得到浓度为20.4%的盐酸溶液和沉淀物。其中,氯化钙溶液与混合酸溶液的质量比分别为3:2。
30.步骤3:在沉淀物中加入浓度为20%的氢氧化钠溶液搅拌反应25min得到混合物,将混合物过滤分离出滤渣和碱性滤液,滤渣用去离子水冲洗后再烘干粉碎,烘干温度为120℃,烘干时间2h,得到质量比为93.5%的氟化钙。
31.实施例3
32.步骤1:将含20%质量比的氢氟酸、15%质量比的盐酸的混合酸进行过滤除杂,将过滤后的混合酸加热至恒温60℃搅拌。
33.步骤2:向经所述步骤1处理得到的混合酸溶液中滴加浓度为20%的氯化钙溶液,搅拌反应10分钟得到混合溶液,反应结束后,对所述混合溶液进行真空抽滤处理,得到浓度为20.7%的盐酸溶液和沉淀物。其中,氯化钙溶液与混合酸溶液的质量比分别为3:2。
34.步骤3:在沉淀物中加入浓度为30%的氢氧化钠溶液搅拌反应30min得到混合物,将混合物过滤分离出滤渣和碱性滤液,滤渣用去离子水冲洗后再烘干粉碎,烘干温度为110℃,烘干时间1.5h,得到质量比为93.6%的氟化钙。
35.实施例4
36.步骤1:将含30%质量比的氢氟酸、15%质量比的盐酸的混合酸进行过滤除杂,将过滤后的混合酸加热至恒温52℃搅拌。
37.步骤2:向经所述步骤1处理得到的混合酸溶液中滴加40%质量比的氯化钙溶液,搅拌反应10分钟得到混合溶液,反应结束后,对所述混合溶液进行真空抽滤处理,得到浓度为12.6%的盐酸溶液和沉淀物。其中,氯化钙溶液与混合酸溶液的质量比分别为4:3。
38.步骤3:在沉淀物中加入浓度为26%的氢氧化钠溶液搅拌反应22min得到混合物,将混合物过滤分离出滤渣和碱性滤液,滤渣用去离子水冲洗后再烘干粉碎,烘干温度为100℃,烘干时间1h,得到质量比为93.7%的氟化钙。
39.表1
[0040][0041][0042]
以上表1中提供了12组实验数据,该12组实验的方法步骤与本发明一种利用废酸生产高纯氟化钙及提浓废盐酸的方法的步骤相同,区别仅在于所使用的混合酸溶液中氢氟
酸和盐酸的含量不同,以及加入的氟化钙溶液与混合酸溶液的质量比不同,通过不同的用量得到不同的实验结果,以分析不同的氯化钙添加量对氟化钙产品质量及盐酸质量的影响。
[0043]
从表1看出,每组所使用的均为浓度为40%的氯化钙溶液,第1~3组的混合酸溶液中,氢氟酸和盐酸的质量分数分别为10%和15%,氟化钙溶液的用量与混合酸溶液的质量比分别为2:1、3:2和4:3;第4~6组的混合酸溶液中,氢氟酸和盐酸的质量分数分别为15%和15%,氟化钙溶液的用量与混合酸溶液的质量比分别为2:1、3:2和4:3;第7~9组的混合酸溶液中,氢氟酸和盐酸的质量分数分别为20%和15%,氟化钙溶液的用量与混合酸溶液的质量比分别为2:1、3:2和4:3;第10~12组的混合酸溶液中,氢氟酸和盐酸的质量分数分别为30%和15%,氟化钙溶液的用量与混合酸溶液的质量比分别为2:1、3:2和4:3。
[0044]
以上的12组实验中,将氯化钙配置为浓度为40%的水溶液,由表1可以看出,当m(cacl2):m(混合酸)为4:1时,虽然可以提升caf2浓度,但因cacl2过量投加,会导致溶液中hcl浓度下降。当m(cacl2):m(混合酸)质量比在2:1时,可看出沉淀物b中caf2含量偏低。当m(cacl2):m(混合酸)质量比在3:2时,氟化钙含量与盐酸含量为最优方案。
[0045]
表2
[0046][0047][0048]
以上表2中提供了6组实验数据,该6组实验的方法均采用了本发明一种利用废酸生产高纯氟化钙及提浓废盐酸的方法中的各个步骤,区别仅在于步骤3中的处理过程不同,通过不同的数据,以分析出氢氧化钠浓度对氟化钙质量的影响。
[0049]
当沉淀物b中氟化钙含量不足97.5%,不能直接使用或者销售。需要碱洗除硅、水洗除杂。为了保证氟化钙产品质量,对碱洗及水洗进行实验选择确定洗涤除杂方式。从表2中看出,未洗涤时产品回收率为最高,但产品含量较低,二氧化硅含量较高,不能满足产品质量要求。单纯水洗时不能对二氧化硅杂质进行除去。氟化钙在水中有少量的溶解度,洗涤次数2次后产品回收率较低。加入浓度10%的naoh并结合一次水洗时,得到的氟化钙产品的二氧化硅杂质超标,(氟化钙国标对二氧化硅含量要求不能大于0.4%),加入浓度30%的naoh并结合一次水洗时,得到的氟化钙产品烘干所得率太低。故采用浓度20%的naoh并结合一次水洗时,可保证产品质量及产品回收率,同时二氧化硅也可达到要求。
[0050]
对比例分析
[0051]
取某光伏企业的废混酸15kg(该废酸中含20%质量比的氢氟酸和15%质量比的盐酸),均分为3桶(5kg/桶)。对比例1向桶中加入浓度为40%的ca(oh)2,对比例2向桶中加入
浓度为40%的caco3,实施例3向桶中加入浓度为40%的cacl2,各自搅拌10min后进行固液分离,分离的液体分别测定hcl含量;将三组固体(caf2)分别投入浓度为20%的naoh搅拌反应20min得到混合物,将三种混合物过滤分离出滤渣和碱性滤液,滤渣用去离子水冲洗后再烘干粉碎,分别测定固体中caf2的含量和sio2含量,见表3。
[0052]
表3
[0053][0054]
由表3可看出,采用本实施例3方法所得到的溶液a盐酸浓度较高,达到市售标准。而ca(oh)2结合水洗或caco3结合的水洗方法,除了与混酸中hf反应生成caf2,也会与混酸hcl反应生产其他物质,降低了混酸中hcl浓度。实施例3中碱洗加水洗的方法可以进一步提高caf2纯度,除去掉caf2里面杂质。
[0055]
本发明的方法先在含盐酸、氢氟酸的废酸中按一定速度滴加氯化钙溶液,使氯化钙与氢氟酸反应生成氟化钙析出沉淀,剩余水溶液为浓度提高了的盐酸;再将沉淀物用氢氧化钠水溶液碱溶除硅后干燥即可得到高纯度氟化钙固体。本发明得到的氟化钙纯度高,杂质少,可直接销售或使用;浓度提高了的盐酸溶液可以出售或者用于废水中和等方面;降低污水中和氟离子处理成本;本发明从循环经济的角度考虑,将混合酸回收利用,用混合酸中的氢氟酸生产其他氟化工产品,从而与盐酸分开,使氟化工产品与由盐酸形成的相关产品各自销售。这样既可减少大量的含氟工业废物,改善环境,又可实现最大资源利用率,降低生产成本,具有明显的社会效益和经济效益。