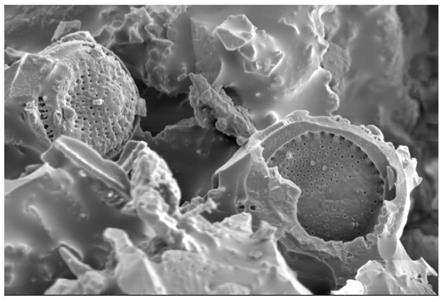
1.本发明涉及雾化技术领域,尤其涉及一种微孔陶瓷雾化芯及其制备方法。
背景技术:2.陶瓷雾化芯作为电子烟等雾化领域的核心部件,随着该领域的发展,人们对陶瓷雾化芯的要求就不仅仅是雾化,其雾化效果也成为了评判雾化芯的一个重要指标。
3.目前的陶瓷雾化芯存在着雾化颗粒大、使用或运输过程中漏液、高温烧结使雾化芯收缩变形等主要问题,极大程度上限制了陶瓷雾化芯的发展。
技术实现要素:4.本发明要解决的技术问题在于,提供一种孔隙率高、提高雾化效果的微孔陶瓷雾化芯及其制备方法。
5.本发明解决其技术问题所采用的技术方案是:提供一种微孔陶瓷雾化芯,包括原料及其质量份数如下:主体材料10
‑
50份、陶瓷粉体0
‑
40份、助烧剂10
‑
50份、造孔剂0
‑
20份、石蜡20
‑
50份以及表面活性剂0.1
‑
2.0份;
6.所述主体材料包括硅藻土、二氧化硅气凝胶粉末以及多孔氮化硼中的至少一种;所述主体材料的粒度为200目
‑
1500目。
7.优选地,所述陶瓷粉体包括石英砂、氮化硅、硅粉和刚玉中的至少一种,粒度为100目
‑
1500目。
8.优选地,所述助烧剂为金属氧化物或玻璃粉,粒度为200目
‑
2000目,始熔温度为300℃
‑
600℃。
9.优选地,所述金属氧化物为氧化镁、二氧化钛、氧化铌中至少一种。
10.优选地,所述玻璃粉为非铅系低温熔融玻璃粉、稀有元素系低温熔融玻璃粉或硼系低熔点玻璃粉。
11.优选地,所述造孔剂包括小麦粉、ps微球和谷壳粉中至少一种,粒度为200目
‑
1000目。
12.优选地,所述石蜡为半炼或精炼石蜡,熔点为40℃
‑
100℃。
13.优选地,所述表面活性剂包括失水山梨醇脂肪酸酯、聚山梨酯和油酸中至少一种。
14.本发明还提供一种微孔陶瓷雾化芯的制备方法,包括以下步骤:
15.s1、按质量份数将各原料混合,压制形成坯体;
16.s2、将所述坯体置于烧结炉中,在500℃
‑
800℃下进行烧结。
17.本发明的有益效果:通过自带微孔、具有高比表面的主体材料的加入,提高雾化芯的孔隙率及锁液能力,确保雾化液的充分雾化,增强雾化芯的使用体验感。
18.在制备时,以低温(500℃
‑
800℃)烧结成型,制备条件简单易实施。
附图说明
19.下面将结合附图及实施例对本发明作进一步说明,附图中:
20.图1是本发明中硅藻土的sem图;
21.图2是本发明的微孔陶瓷雾化芯的sem图。
具体实施方式
22.为了对本发明的技术特征、目的和效果有更加清楚的理解,现对照附图详细说明本发明的具体实施方式。
23.本发明的微孔陶瓷雾化芯,包括原料及其质量份数如下:主体材料10
‑
50份、陶瓷粉体0
‑
40份、助烧剂10
‑
50份、造孔剂10
‑
20份、石蜡20
‑
50份以及表面活性剂0.1
‑
2.0份。
24.其中,主体材料选择自带微孔、具有高比表面的材料,在雾化芯中能提高锁液效果并使雾化颗粒细腻。该主体材料包括硅藻土、二氧化硅气凝胶粉末以及多孔氮化硼中的至少一种。主体材料的粒度为200目
‑
1500目。
25.主体材料中,硅藻土主要成分是硅酸质,表面有无数细孔,具有吸附性能强、容重轻、细度均匀、ph值中性无毒及混合均匀性好等优点。硅藻土的sem图如图1所示,从图中示出的硅藻土粉体颗粒的显微形貌表征可知,硅藻土分布着均匀的微孔,比表面较大。
26.二氧化硅气凝胶粉末是利用常压干燥方法制备的低密度、低导热系数、高比表面、高吸附性的气凝胶材料;多孔氮化硼是一种新型非氧化物多孔材料,内部由相互贯通或封闭的孔洞构成,具有高比表面积和丰富的孔道结构,孔径尺寸可根据实际应用进行调控。
27.陶瓷粉体作为微孔陶瓷雾化芯的骨架材料,可包括石英砂、氮化硅、硅粉和刚玉中的至少一种。陶瓷粉体优选粒度为100目
‑
1500目。
28.助烧剂为金属氧化物或玻璃粉,粒度为200目
‑
2000目,始熔温度为300℃
‑
600℃。金属氧化物可为氧化镁、二氧化钛、氧化铌等中至少一种。玻璃粉可为非铅系低温熔融玻璃粉、稀有元素系低温熔融玻璃粉或硼系低熔点玻璃粉。
29.造孔剂为小麦粉、ps微球及谷壳粉中至少一种,粒度为200目
‑
1000目。
30.石蜡为半炼或精炼石蜡,熔点为40℃
‑
100℃。
31.表面活性剂为失水山梨醇脂肪酸酯(司盘)、聚山梨酯(吐温)和油酸中至少一种。
32.本发明的微孔陶瓷雾化芯的制备方法,包括以下步骤:
33.s1、按质量份数将各原料混合,压制形成坯体。
34.对于压制成型,可以采用热压铸成型,也可以干压成型。
35.s2、将坯体置于烧结炉中,在500℃
‑
800℃下进行烧结,以一次烧结方式得到微孔雾化芯。
36.可以理解地,本发明的微孔陶瓷雾化芯的制备方法不限于上述热压铸或干压,其他成型制备雾化芯的方法均可采用。
37.本发明的微孔陶瓷雾化芯的sem图如图2所示,从图可看出,雾化芯除了由颗粒堆积及造孔剂形成的孔外,主体材料的加入使微孔大幅增加,在确保进液的同时,极大的改善了微孔雾化芯的毛细作用,储液锁液能力大大提升,使雾化器工作时保证充分供油,并且使雾化颗粒细腻。
38.以下通过具体实施例对本发明作进一步说明。
39.实施例1:
40.各原料份数如下:硅藻土80份,玻璃粉50份,石蜡50份,油酸0.5份;将上述原料混合后进行热压铸成型,于500℃
‑
800℃下一次烧结,形成微孔雾化芯。
41.实施例2:
42.硅藻土改为二氧化硅气凝胶粉末,其余与实施例1相同。
43.实施例3:
44.硅藻土改为多孔氮化硼,其余与实施例1相同。
45.实施例4:
46.原料在实施例1基础上增加小麦粉10份,其余与实施例1相同。
47.实施例5:
48.原料在实施例1基础上增加小麦粉20份,其余与实施例1相同。
49.实施例6:
50.各原料份数如下:硅藻土40份,硅粉10份,玻璃粉50份,小麦粉20份,石蜡40份,油酸0.5份;将上述原料混合后进行热压铸成型,于500℃
‑
800℃下一次烧结,形成微孔雾化芯。
51.实施例7:
52.各原料份数如下:硅藻土40份,硅粉20份,玻璃粉40份,小麦粉20份,石蜡40份,油酸0.5份;将上述原料混合后进行热压铸成型,于500℃
‑
800℃下一次烧结,形成微孔雾化芯。
53.实施例8:
54.各原料份数如下:硅藻土40份,石英砂20份,玻璃粉40份,小麦粉20份,石蜡40份,油酸0.5份;将上述原料混合后进行热压铸成型,于500℃
‑
800℃下一次烧结,形成微孔雾化芯。
55.实施例9:
56.各原料份数如下:硅藻土40份,刚玉20份,玻璃粉40份,小麦粉20份,石蜡40份,油酸0.5份;将上述原料混合后进行热压铸成型,于500℃
‑
800℃下一次烧结,形成微孔雾化芯。
57.实施例10:
58.各原料份数如下:二氧化硅气凝胶粉末40份,硅粉20份,玻璃粉40份,小麦粉20份,石蜡40份,油酸0.5份;将上述原料混合后进行热压铸成型,于500℃
‑
800℃下一次烧结,形成微孔雾化芯。
59.实施例11:
60.各原料份数如下:多孔氮化硼40份,硅粉20份,玻璃粉40份,小麦粉20份,石蜡40份,油酸0.5份;将上述原料混合后进行热压铸成型,于500℃
‑
800℃下一次烧结,形成微孔雾化芯。
61.比较例1:
62.各原料份数如下:刚玉粉70份,玻璃粉30份,小麦粉20份,石蜡30份,油酸0.5份;将上述原料混合后进行热压铸成型,于500℃
‑
800℃下一次烧结,形成微孔雾化芯。
63.比较例2:
64.各原料份数如下:石英砂70份,玻璃粉30份,小麦粉20份,石蜡30份,油酸0.5份;将上述原料混合后进行热压铸成型,于500℃
‑
800℃下一次烧结,形成微孔雾化芯。
65.对实施例1
‑
11及比较例1
‑
2得到的微孔雾化芯的孔隙率(阿基米德排水法)及吸水率进行测试,测试结果如下表1。
66.表1
[0067][0068][0069]
由表1结果可知,相比于比较例的雾化芯的孔隙率偏小、孔径偏大、雾化芯储液能力低及易产生漏油等问题,本发明中通过硅藻土等主体材料的加入,使得微孔雾化芯的孔隙率明显升高,且平均孔径能保持在一个相对平稳偏小的水平,确保了雾化芯有较佳的锁液能力。
[0070]
以上所述仅为本发明的实施例,并非因此限制本发明的专利范围,凡是利用本发明说明书及附图内容所作的等效结构或等效流程变换,或直接或间接运用在其他相关的技术领域,均同理包括在本发明的专利保护范围内。