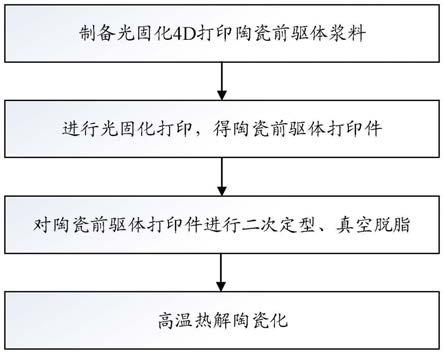
一种光固化4d打印陶瓷基前驱体浆料、陶瓷件及制备方法
技术领域
1.本发明涉及陶瓷增材技术领域,尤其涉及一种光固化4d打印陶瓷基前驱体浆料、陶瓷件及制备方法。
背景技术:2.4d打印的概念为3d打印与时间的结合,是指3d打印出来的构件的特征、结构和功能的变化跟时间相联系,是将刺激响应材料与3d打印技术相结合,借助外部激励和交互机制,利用3d模型设计形成的一种技术。将刺激反应原材料与3d打印技术相结合的4d打印就能够生产出形状、性质以及功能可调的构件。设计出来的三维模型在3d打印下只能打印出三维静态的结构,4d打印等效于通过将刺激性响应的原材料与3d打印技术相结合而创建的新技术。4d打印技术及产品可广泛应用于军事、航空航天、生物及日常生活等领域中。
3.在众多增材制造技术中,光固化成型技术可以一次成形一个面,而且具备成形精度高、效率高、表面质量好等优点。
4.传统的陶瓷材料具有良好的热稳定性、抗腐蚀性、电绝缘性以及特殊的光学特性等优点,但因为其强度和硬度很高,陶瓷粉末经过光固化3d打印成型后的陶瓷构件不能再次成型来满足不同的需求,即不能实现3d+1d。
5.陶瓷前驱体的增材制造是用于构建复杂陶瓷结构的最先进的技术,得益于陶瓷前驱体的流变形态和结构性质,其中部分陶瓷前驱体含有可光固化的活性基团,并且在交联固化后还具有柔性特性,因此可以借助光固化3d打印出具备柔软的构件,这就为4d打印提供了再次成型的可能。
技术实现要素:6.本发明所要解决的技术问题是克服现有技术的不足,提供一种光固化4d打印陶瓷基前驱体浆料、光固化4d打印陶瓷件及制备方法,将陶瓷基前驱体与光固化3d打印技术相结合,制造出够柔软可控,能弯曲变形的结构素坯,再利用其柔性可弯的特性进行二次定型,最后通过脱脂烧结工艺将二次定型的前驱体素坯转化为陶瓷样件。
7.为了解决上述问题,本发明提出以下技术方案:
8.第一方面,本发明提供光固化4d打印陶瓷基前驱体浆料,由光敏树脂、光引发剂、染料、陶瓷前驱体溶液及消泡剂制备而成;其中,光敏树脂、光引发剂、陶瓷前驱体溶液、染料及消泡剂的质量百分数分别为10%~85%、1%~3%、10%~85%、0.02%~0.1%及1%~5%。
9.其进一步地技术方案为,所述陶瓷前驱体溶液选自含有甲基或乙烯基基团的聚硅氮烷,含有甲基或乙烯基基团的聚硅氧烷的一种或多种。
10.其进一步地技术方案为,所述染料选自具有紫外光吸收作用且不与体系发生反应的颜色染料。
11.需要说明的是,在对样品成型精度要求较高的情况下,染料如苏丹红ⅲ、苏丹橙等
能起到合适的光吸收作用,加入染料后可对精度进行调整,进而可以限制发出光的穿透深度及避免过曝现象;在其他实施例中也可使用其他能对打印机发射的紫外光波长范围起一定吸收作用且不与浆料体系反应的颜色染料。
12.其进一步地技术方案为,所述光敏树脂选自聚乙二醇二丙烯酸酯、乙氧化季戊四醇四丙烯酸酯及聚氨酯丙烯酸酯的一种或多种。
13.其进一步地技术方案为,所述光引发剂选自2,4,6
‑
三甲基苯甲酰基
‑
二苯基氧化膦、irgacure 819、irgacure369或安息香二甲醚;消泡剂为kyc
‑
766、kyc
‑
713或kyc
‑
750。
14.本发明还提供所述的光固化4d打印陶瓷基前驱体浆料的制备方法,包括以下步骤:
15.按比例,将光敏树脂、光引发剂、染料、陶瓷前驱体溶液及消泡剂混合,搅拌均匀;将混合均匀的浆料进行真空脱泡,得到光固化4d打印陶瓷基前驱体浆料。
16.第二方面,本发明提供一种光固化4d打印陶瓷件的制备方法,包括以下步骤:
17.s1,将权利要求6制备得到的光固化4d打印陶瓷基前驱体浆料倒入陶瓷光固化打印机浆料槽中,利用刮刀进行刮平;
18.s2:在设置选项中对打印平台进行调平操作,按照预设打印模型切片并选择曝光参数进行打印,得陶瓷前驱体打印件;
19.s3:对清洗后的陶瓷前驱体打印件用高熔点金属丝进行预设形状的二次定型,再进行真空脱脂,得陶瓷前驱体脱脂坯体;
20.s4:将陶瓷前驱体脱脂坯体放入到氮气气氛炉中进行高温热解,得到光固化4d打印陶瓷件。
21.需要说明的是,步骤s3中,二次定型是指对打印件进行弯曲或扭转变形折叠成特定结构。金属丝的作用是固定保持变形后的形状,由于还需保持形状进行高温脱脂工艺才能得到陶瓷制品,因此,金属丝的熔点需高于脱脂烧结工艺的温度。合适的金属丝例如铜丝。
22.其进一步地技术方案为步骤s2中,打印参数为:单层厚度为10~100um,曝光强度为5~30mw/cm2,单层固化时长为2~20s。
23.其进一步地技术方案为,步骤s3中,真空脱脂的脱脂制度为以0.3
‑
0.8℃/min升温至600℃,其中分别在300℃、600℃时保温0.5
‑
1.5h,再以1℃/min降温至300℃再随炉冷却至室温;
24.步骤s4中,高温热解时,以0.3
‑
0.8℃/min升温至1200℃,其中分别在300℃、600℃、1200℃分别保温0.5
‑
1.5h,再以3℃/min进行降温。
25.需要说明的是,在进行真空脱脂工序中,初期阶段,低熔点的小分子有机物在高温下会由于无法及时排出体外而在坯体内挥发产生较高的压力,导致坯体发生开裂、变形、坍塌等缺陷,因此脱脂的升温速率要十分缓慢,以0.3
‑
0.8℃/min升温速率为宜,0.5℃/min升温速率较佳;设置保温时长可以使有机组分完全挥发,通常保温时长为0.5
‑
1.5h,以1h为较佳。严格控制脱脂工艺的升温程序,使有机物的挥发、热解具有一致性;在脱脂后期,由于气孔通道已经贯通在一起,所以坯体内部有机物的气相产物可迅速到达孔道中排除,因此可以使用较快的升温速率来排除残余的有机物。
26.本发明提供的所述的光固化4d打印陶瓷件的制备方法得到的陶瓷件,烧结后的致
密度为90%~99%;热解后的线性收缩率为30%~45%。
27.与现有技术相比,本发明所能达到的技术效果包括:
28.本发明提供的4d打印陶瓷基前驱体将陶瓷前驱体与光固化dlp打印技术相结合,得到的光固化4d打印陶瓷基前驱体浆料具备较好的稳定性、分散性以及光敏性。
29.由本发明提供的4d打印陶瓷基前驱体浆料用光固化打印技术能实现打印后成型良好、柔软且能弯曲变形进行二次定型的坯体,再经过真空脱脂及高温反应热解得到致密度为90%~99%、线性收缩率为30%~45%的陶瓷制品。
附图说明
30.图1为本发明光固化4d打印陶瓷件的制备方法流程图;
31.图2为本发明实施例2dlp打印成型后的试样图,(a)为五叶花瓣坯体展示图,(b)为六叶花瓣坯体展示图,(c)为“田”字坯体展示图;
32.图3为本发明实施例2dlp打印后的试样经铜丝固定二次成型图,(a)、(b)为经铜丝二次弯曲变形固定后的五叶花瓣展示图,(c)为经铜丝二次弯曲变形固定后的长条(30mm
×
4mm
×
1mm)展示图,(d)为经铜丝二次扭转变形180度固定后的长条(30mm
×
4mm
×
1mm)展示图;
33.图4为本发明实施例2在铜丝固定下脱脂烧结后的试样图;
34.图5为本发明实施例2试样在脱脂烧结前后(左边为打印坯体,右边为烧结后陶瓷件)的对比图。
具体实施方式
35.下面将结合本发明实施例中的附图,对实施例中的技术方案进行清楚、完整地描述。下述实施例中所述试验方法或测试方法,如无特殊说明,均为常规方法;所述试剂和材料,如无特殊说明,均从常规商业途径获得,或以常规方法制备。显然,以下将描述的实施例仅仅是本发明一部分实施例,而不是全部的实施例。基于本发明中的实施例,本领域普通技术人员在没有作出创造性劳动前提下所获得的所有其他实施例,都属于本发明保护的范围。
36.实施例1
37.本发明提供一种光固化4d打印陶瓷基前驱体浆料,由以下原料制备而成:光敏树脂、光引发剂、陶瓷前驱体溶液、染料及消泡剂的质量分数分别为10%~85%、1%~3%、10%~85%、0.02%~0.1%及1%~5%。
38.其中,光敏树脂、光引发剂、陶瓷前驱体溶液的质量比例为1:0.03:2。
39.本实施例中,陶瓷前驱体溶液为聚硅氮烷。
40.本实施例中,光敏树脂为乙氧化季戊四醇四丙烯酸酯(pptta)。
41.本实施例中,光引发剂为2,4,6
‑
三甲基苯甲酰基
‑
二苯基氧化膦(tpo)。
42.本实施例中,消泡剂为kyc
‑
713。
43.本实施例中,前驱体溶液为乙烯基聚硅氮烷。
44.本实施例中,光固化4d打印陶瓷基前驱体浆料制备方法,包括以下步骤:
45.s1:称取20g乙烯基聚硅氮烷,10g乙氧化季戊四醇四丙烯酸酯、0.3g光引发剂、
2.5g消泡剂及0.015g苏丹ⅲ加入到黑色罐中,使用磁力搅拌器进行搅拌8h,得光固化4d打印陶瓷前驱体浆料;
46.s2:待搅拌完成后,将混合均匀的浆料放入脱泡机里面真空
‑
0.1mpa除去气泡20min。
47.参见图1,本发明实施例提供的光固化4d打印陶瓷件的制备方法,包括以下步骤:
48.s1:将光固化4d打印陶瓷前驱体浆料倒入陶瓷光固化(dlp)打印机浆料槽中,然后利用刮刀进行刮平;
49.s2:在设置选项中对打印平台进行调平操作,按照预设打印模型30mm
×
4mm
×
1mm长条进行切片并选择曝光参数设置为打印单层厚度为20um,曝光强度为10mw/cm2,单层固化时长为4s。打印,得陶瓷前驱体打印件;
50.s3:将陶瓷前驱体打印件进行超声清洗,采用铜丝对其进行特殊形状的固定,即二次成型;
51.s4:放入到真空气氛中进行脱脂,以0.5℃/min升温至600℃,其中分别在300℃与600℃时保温1h,然后以1℃/min降温至300℃再随炉冷却至室温,得陶瓷前驱体脱脂坯体;
52.s5:将陶瓷前驱体脱脂坯体放入到氮气气氛炉中进行高温裂解反应陶瓷化,以0.5℃/min升温至1200℃,其中分别在300℃、600℃、1200℃分别保温1h,再以3℃/min进行降温,得到陶瓷制品。
53.实施例2
54.本实施例与实施例1的光固化4d打印陶瓷基前驱体浆料的区别如下:
55.本实施例中,光敏树脂、光引发剂、陶瓷前驱体溶液的质量比例为1:0.03:2。
56.本实施例中,陶瓷前驱体溶液由聚硅氮烷和聚硅氧烷组成,且聚硅氮烷和聚硅氧烷比例为7:3。
57.本实施例中,前驱体溶液为乙烯基聚硅氮烷及甲基聚硅氧烷混合的陶瓷前驱体溶液。
58.本实施例的光固化4d打印陶瓷基前驱体浆料制备方法,包括以下步骤:
59.s1:称取14g乙烯基聚硅氮烷和6g甲基聚硅氧烷加入到黑色罐中,在磁力搅拌器作用下对混合的陶瓷前驱体进行搅拌4h;
60.s2:向步骤s1得到的溶液中加入10g乙氧化季戊四醇四丙烯酸酯、0.3g光引发剂、2.5g消泡剂及0.015g苏丹ⅲ,然后继续使用磁力搅拌器进行搅拌4h,得光固化4d打印陶瓷前驱体浆料;
61.s3:待搅拌完成后,将混合均匀的浆料放入脱泡机里面真空
‑
0.1mpa除去气泡20min。
62.本发明实施例提供的光固化4d打印陶瓷件的制备方法,包括以下步骤:
63.s1:将光固化4d打印陶瓷前驱体浆料倒入陶瓷光固化(dlp)打印机浆料槽中,然后利用刮刀进行刮平;
64.s2:在设置选项中对打印平台进行调平操作,按照预设打印模型30mm
×
4mm
×
1mm长条进行切片并选择曝光参数设置为打印单层厚度为20um,曝光强度为10mw/cm2,单层固化时长为4s。打印,得陶瓷前驱体打印件,如图2所示;
65.s3:将陶瓷前驱体打印件进行超声清洗,采用铜丝对其进行特殊形状的固定,即二
次成型,如图3所示;
66.s4:放入到真空气氛中进行脱脂,以0.5℃/min升温至600℃,其中分别在300℃与600℃时保温1h,然后以1℃/min降温至300℃再随炉冷却至室温,得陶瓷前驱体脱脂坯体;
67.s5:将陶瓷前驱体脱脂坯体放入到氮气气氛炉中进行高温裂解反应陶瓷化,以0.5℃/min升温至1200℃,其中分别在300℃、600℃、1200℃分别保温1h,再以3℃/min进行降温,得到的陶瓷制品如图4所示、裂解前后对比图如图5所示。
68.实施例3
69.本实施例与实施例1的光固化4d打印陶瓷基前驱体浆料的区别如下:
70.本实施例中,光敏树脂、光引发剂、陶瓷前驱体溶液的质量比例为1:0.03:2。
71.本实施例中,陶瓷前驱体溶液由聚硅氮烷和聚硅氧烷组成,且聚硅氮烷和聚硅氧烷比例为5:5。
72.本实施例中,具体的:前驱体溶液为乙烯基聚硅氮烷及甲基聚硅氧烷混合的陶瓷前驱体溶液。
73.本实施例的光固化4d打印陶瓷基前驱体浆料制备方法,包括以下步骤:
74.s1:称取10g乙烯基聚硅氮烷和10g甲基聚硅氧烷加入到黑色罐中,在磁力搅拌器作用下对混合的陶瓷前驱体进行搅拌4h;
75.s2:向步骤s1得到的溶液中加入10g乙氧化季戊四醇四丙烯酸酯、0.3g光引发剂、2.5g消泡剂及0.015g苏丹ⅲ,然后继续使用磁力搅拌器进行搅拌4h,得光固化4d打印陶瓷前驱体浆料;
76.s3:待搅拌完成后,将混合均匀的浆料放入脱泡机里面真空
‑
0.1mpa除去气泡20min。
77.本发明实施例提供的光固化4d打印陶瓷件的制备方法,包括以下步骤:
78.s1:将光固化4d打印陶瓷前驱体浆料倒入陶瓷光固化(dlp)打印机浆料槽中,然后利用刮刀进行刮平;
79.s2:在设置选项中对打印平台进行调平操作,按照预设打印模型30mm
×
4mm
×
1mm长条进行切片并选择曝光参数设置为打印单层厚度为20um,曝光强度为10mw/cm2,单层固化时长为4s。进行打印,得陶瓷前驱体打印件;
80.s3:将陶瓷前驱体打印件进行超声清洗,采用铜丝对其进行特殊形状的固定,即二次成型;
81.s4:放入到真空气氛中进行脱脂,以0.5℃/min升温至600℃,其中分别在300℃与600℃时保温1h,然后以1℃/min降温至300℃再随炉冷却至室温,得陶瓷前驱体脱脂坯体;
82.s5:将陶瓷前驱体脱脂坯体放入到氮气气氛炉中进行高温裂解反应陶瓷化,以0.5℃/min升温至1200℃,其中分别在300℃、600℃、1200℃分别保温1h,再以3℃/min进行降温,得到陶瓷制品。
83.实施例4
84.本实施例与实施例1的光固化4d打印陶瓷基前驱体浆料的区别如下:
85.本实施例中,光敏树脂、光引发剂、陶瓷前驱体溶液的质量比例为1:0.03:2。
86.本实施例中,陶瓷前驱体溶液由聚硅氮烷和聚硅氧烷组成,且聚硅氮烷和聚硅氧烷比例为3:7。
87.本实施例中,前驱体溶液为乙烯基聚硅氮烷及甲基聚硅氧烷混合的陶瓷前驱体溶液。
88.本实施例的光固化4d打印陶瓷基前驱体浆料制备方法,包括以下步骤:
89.s1:称取6g乙烯基聚硅氮烷和14g甲基聚硅氧烷加入到黑色罐中,在磁力搅拌器作用下对混合的陶瓷前驱体进行搅拌4h;
90.s2:向步骤s1得到的溶液中加入10g乙氧化季戊四醇四丙烯酸酯、0.3g光引发剂、2.5g消泡剂及0.015g苏丹ⅲ,然后继续使用磁力搅拌器进行搅拌4h,得光固化4d打印陶瓷前驱体浆料;
91.s3:待搅拌完成后,将混合均匀的浆料放入脱泡机里面真空
‑
0.1mpa去气泡20min。
92.本发明实施例提供的光固化4d打印陶瓷件的制备方法,包括以下步骤:
93.s1:将光固化4d打印陶瓷前驱体浆料倒入陶瓷光固化(dlp)打印机浆料槽中,然后利用刮刀进行刮平;
94.s2:在设置选项中对打印平台进行调平操作,按照预设打印模型30mm
×
4mm
×
1mm长条进行切片并选择曝光参数设置为打印单层厚度为20um,曝光强度为10mw/cm2,单层固化时长为4s。进行打印,得陶瓷前驱体打印件;
95.s3:将陶瓷前驱体打印件进行超声清洗,采用铜丝对其进行特殊形状的固定,即二次成型;
96.s4:放入到真空气氛中进行脱脂,以0.5℃/min升温至600℃,其中分别在300℃与600℃时保温1h,然后以1℃/min降温至300℃再随炉冷却至室温,得陶瓷前驱体脱脂坯体;
97.s5:将陶瓷前驱体脱脂坯体放入到氮气气氛炉中进行高温裂解反应陶瓷化,以0.5℃/min升温至1200℃,其中分别在300℃、600℃、1200℃分别保温1h,再以3℃/min进行降温,得到陶瓷制品。
98.实施例5
99.本实施例与实施例1的光固化4d打印陶瓷基前驱体浆料的区别如下:
100.本实施例中,光敏树脂、光引发剂、陶瓷前驱体溶液的质量比例为1:0.03:2。
101.本实施例中,陶瓷前驱体溶液由聚硅氧烷组成。
102.本实施例中,陶瓷前驱体溶液为甲基聚硅氧烷。
103.本实施例的光固化4d打印陶瓷基前驱体浆料制备方法,包括以下步骤:
104.s1:称取20g甲基聚硅氧烷、10g乙氧化季戊四醇四丙烯酸酯、0.3g光引发剂、2.5g消泡剂及0.015g苏丹ⅲ加入到黑色罐中,然后使用磁力搅拌器进行搅拌8h,得光固化4d打印陶瓷前驱体浆料;
105.s2:待搅拌完成后,将混合均匀的浆料放入脱泡机里面真空
‑
0.1mpa去气泡20min。
106.本发明实施例提供的光固化4d打印陶瓷件的制备方法,包括以下步骤:
107.s1:将光固化4d打印陶瓷前驱体浆料倒入陶瓷光固化(dlp)打印机浆料槽中,然后利用刮刀进行刮平;
108.s2:在设置选项中对打印平台进行调平操作,按照预设打印模型30mm
×
4mm
×
1mm长条进行切片并选择曝光参数设置为打印单层厚度为20um,曝光强度为10mw/cm2,单层固化时长为4s。进行打印,得陶瓷前驱体打印件;
109.s3:将陶瓷前驱体打印件进行超声清洗,采用铜丝对其进行特殊形状的固定,即二
次成型;
110.s4:放入到真空气氛中进行脱脂,以0.5℃/min升温至600℃,其中分别在300℃与600℃时保温1h,然后以1℃/min降温至300℃再随炉冷却至室温,得陶瓷前驱体脱脂坯体;
111.s5:将陶瓷前驱体脱脂坯体放入到氮气气氛炉中进行高温裂解反应陶瓷化,以0.5℃/min升温至1200℃,其中分别在300℃、600℃、1200℃分别保温1h,再以3℃/min进行降温,得到陶瓷制品。
112.实施例6
113.本实施例与实施例1的光固化4d打印陶瓷基前驱体浆料的区别如下:
114.本实施例中,光敏树脂、光引发剂、陶瓷前驱体溶液的质量比例为1:0.02:1。
115.本实施例中,陶瓷前驱体溶液由聚硅氮烷和聚硅氧烷组成,且聚硅氮烷和聚硅氧烷比例为7:3。
116.本实施例中,前驱体溶液为乙烯基聚硅氮烷及甲基聚硅氧烷混合的陶瓷前驱体溶液。
117.本实施例的光固化4d打印陶瓷基前驱体浆料制备方法,包括以下步骤:
118.s1:称取7g乙烯基聚硅氮烷和3g甲基聚硅氧烷加入到黑色罐中,在磁力搅拌器作用下对混合的陶瓷前驱体进行搅拌4h;
119.s2:向步骤s1得到的溶液中加入10g乙氧化季戊四醇四丙烯酸酯、0.2g光引发剂、1.5g消泡剂及0.01g苏丹ⅲ,然后继续使用磁力搅拌器进行搅拌4h,得光固化4d打印陶瓷前驱体浆料;
120.s3:待搅拌完成后,将混合均匀的浆料放入脱泡机里面真空
‑
0.1mpa去气泡20min。
121.本发明实施例提供的光固化4d打印陶瓷件的制备方法,包括以下步骤:
122.s1:将光固化4d打印陶瓷前驱体浆料倒入陶瓷光固化(dlp)打印机浆料槽中,然后利用刮刀进行刮平;
123.s2:在设置选项中对打印平台进行调平操作,按照预设打印模型30mm
×
4mm
×
1mm长条进行切片并选择曝光参数设置为打印单层厚度为20um,曝光强度为10mw/cm2,单层固化时长为4s。进行打印,得陶瓷前驱体打印件;
124.s3:将陶瓷前驱体打印件进行超声清洗,采用铜丝对其进行特殊形状的固定,即二次成型;
125.s4:放入到真空气氛中进行脱脂,以0.5℃/min升温至600℃,其中分别在300℃与600℃时保温1h,然后以1℃/min降温至300℃再随炉冷却至室温,得陶瓷前驱体脱脂坯体;
126.s5:将陶瓷前驱体脱脂坯体放入到氮气气氛炉中进行高温裂解反应陶瓷化,以0.5℃/min升温至1200℃,其中分别在300℃、600℃、1200℃分别保温1h,再以3℃/min进行降温,得到陶瓷制品。
127.实施例1
‑
6得到的陶瓷前驱体打印件、陶瓷制品的性能参数见表1。
128.表1:
[0129] 光固化质量柔软性致密度/%线收缩率/%实施例1好差99.140.4实施例2好较好98.538.7实施例3较好较好97.036.5
实施例4一般好96.234.3实施例5差好
‑‑
实施例6好一般96.545.0
[0130]
注:由于没有关于该实验材料成型的光固化质量及柔软性的国家标准,故采用本实验室的经验判断标准来进行比较说明:
[0131]
光固化质量的判断标准为:利用高精度螺旋测微器测量坯体成型尺寸与目标尺寸的误差。本专利实施例中打印坯体(30mm
×
4mm
×
1mm)成型精度误差δ:好:δ≤0.5%;较好:0.5%<δ≤1%;一般:1%<δ≤1.5%;差:δ>1.5%。
[0132]
陶瓷前驱体打印件柔软性的判断标准为:根据坯体成型后将其弯曲折叠成一定角度且无破环其结构。本专利实施例中打印坯体(30mm
×
4mm
×
1mm)弯曲折叠的角度θ:好:θ>180
°
;较好:90
°
<θ≤180
°
;一般:30
°
<θ≤90
°
;差:θ≤30
°
。
[0133]
从上表1可以看出,以乙烯基聚硅氮烷与甲基聚硅氧烷作为前驱体溶液、pptta作为光敏树脂为例,本发明打印坯体和制品的的性能会受到聚硅氮烷和聚硅氧烷的不同基团与比例影响:由实施例1、实施例2、实施例3、实施例4间的对比可以看出,在确定的前驱体溶液:光敏树脂=2:1比例前提下,随着乙烯基聚硅氮烷比例的减少,甲基聚硅氧烷的比例增加,光固化质量逐渐变差、柔软性逐渐变好、致密度逐渐减小、收缩率逐渐变小,这是由于:乙烯基聚硅氮烷含不饱和双键能进行自由基聚合,同时具备的低粘度特性能调节浆料体系粘度,从而更适合打印;甲基聚硅氧烷固化是具有一定柔软性及韧性的弹性体,它的加入能调节打印坯体的柔软性能;
[0134]
同时,由于实施例1没有甲基聚硅氧烷,虽然光固化的质量好,但是导致了固化后坯体的柔软性变差,达不到实验目标要求;实施例5因为没有乙烯基聚硅氮烷的存在,光固化的质量变差,影响了打印成型及打印坯体的质量,达不到实验目标要求,故该组实例不再进行后续工艺探索及数据对比;
[0135]
实施例2与实施例6对比可以看出,虽然光敏树脂是选取具备一定柔韧性的pptta,能在一定程度上增加交联度、提升粘接性,但随着体系光敏树脂的相对比例增加,甲基聚硅氧烷的相对减少引起光固化性能变好的同时也导致了打印坯体柔软性能相对下降,同时也会导致陶瓷产率较低,高温陶瓷化过程中会有较多小分子逸出,造成裂纹孔隙出现,从而降低最终陶瓷样品的性能;
[0136]
综上,本发明提供的陶瓷前驱体浆料的固化性、稳定性良好,且制备简单;通过光固化3d打印技术可以打印出具有柔软特性的陶瓷前驱体素坯结构,再将3d打印的柔性物体经二次变形如弯曲或扭转变形折叠成特定结构以实现3d+1d的打印物体成型,最后将4d成型的柔性物体经脱脂烧结裂解,即得到4d打印的陶瓷物体。本发明通过提供的前驱体与光固化3d打印技术结合,可以在保证坯体及制品各方面性能兼顾的情况下,经过金属丝二次辅助定型,实现了结构的3d+1d成型,获得收缩均匀的陶瓷制品。
[0137]
在上述实施例中,对各个实施例的描述都各有侧重,某个实施例中没有详细描述的部分,可以参见其他实施例的相关描述。
[0138]
以上所述,为本发明的具体实施方式,但本发明的保护范围并不局限于此,任何熟悉本技术领域的技术人员在本发明揭露的技术范围内,可轻易想到各种等效的修改或替换,这些修改或替换都应涵盖在本发明的保护范围之内。因此,本发明的保护范围应以权利
要求的保护范围为准。