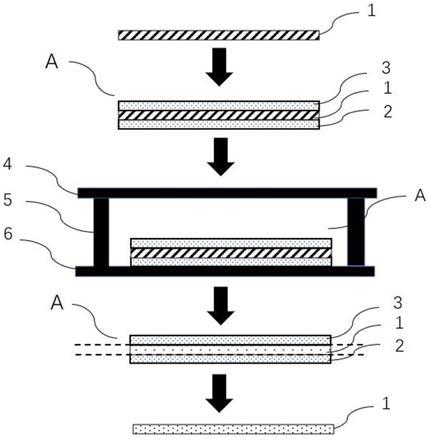
1.本发明涉及半导体材料技术领域,具体涉及一种提高氮化铝晶片紫外透过率的方法。
背景技术:2.氮化铝(aln)晶体直接禁带隙宽6.2ev,为第三代宽禁带半导体的典型材料,具有高击穿场强、宽带系、高的表面声速、高热导率等物理性能,在高温、高功率、紫外发光器件等方面具有相当大的应用前景。同时,随着algan(铝镓氮)基器件在高精密加工、医疗等方面的应用不断扩展,aln单晶因与其较小的失配晶格常数,外延生长algan(铝镓氮)具有低位错密度、表面平整、应力较小等的优点也受到广泛关注。
3.单晶aln是制造紫外发光器件的理想衬底,生长高质量aln单晶一般采用物理气相传输法(pvt)。然而,高紫外光透过率的aln衬底难以制备。因为来自原料或生长室内的杂质在生长过程中会进入晶体,容易诱导产生点缺陷。非故意掺杂的杂质,如si、o和c,缺陷复合体(v
al
‑
o
n
)
‑
或(v
al
‑
o
n
)2‑
,以及本征点缺陷如al空位,都会产生uv吸收带,严重影响晶片的光学、电学等性能,从而降低uvc
‑
led的紫外光发光效率。目前,难以通过pvt本身长晶工艺解决非故意掺杂的问题,主要是因为pvt长晶无法实现超高真空,环境杂质含量较高,以及晶体及习性面生长会引起掺杂浓度不均匀等问题。另外,还有方案通过其他金属元素如镁、铍通过扩散方式取代al空位从而提高uv透过率。
4.综合而言,现有的对aln单晶进行处理的方案包括:1)aln衬底市场上售价昂贵,在满足aln衬底高温热处理>1500℃条件时,单晶片在高温下的升华量大、质量及尺寸耗损大,经济上耗损非常大。直接将晶片放置在异质部件上,高温状态下易与部件粘结导致热处理的晶片取出后表面容易破损。同时由于晶片接触异质衬底,由于热膨胀系数不匹配甚至可能产生裂纹等,影响晶片的性能。
5.2)在氮化铝晶体生长室生长完成后进行原位热处理,可以释放应力解决氮化铝晶体由于应力集中导致晶体开裂等问题。但这种方法工艺步骤复杂难控制,原料或生长室内的杂质仍然存在,对于改善aln晶片紫外(uv)透过率方面效果不明显。
6.3)在热处理室内对晶片进行高温高压热处理,晶片的升华量少,质量及尺寸耗损少。但该环境下晶片内部非故意掺杂的杂质较低压环境扩散效果差,提高晶片的紫外透过率效果不明显。
技术实现要素:7.基于上述背景,本发明提供了一种提高氮化铝晶片紫外透过率的方法,采用高温低压热处理的方式提升aln晶片的紫外光透过率,改善非故意掺杂引起的晶片颜色及光学性能的均匀性。
8.为实现上述目的,本发明采用了如下技术方案:一种提高氮化铝晶片紫外透过率的方法,包括如下步骤:
s1、在待处理氮化铝晶片的上下表面覆盖至少一层保护材料,形成夹层组合结构;s2、将所述夹层组合结构装配至容器中,并将所述容器置于高温炉中;s3、将所述高温炉抽真空,升温后充入保护气体,达到预设保温温度和低压环境后保温预设时间;s4、降温至室温,从高温炉中取出容器,去除所述夹层组合结构中的保护材料并取出氮化铝晶片。
9.可选的,步骤s1中,所述保护层材料为铝、硅、钨、钽、钼、铌、钒、铬、钛、锆、石墨单质或上述材料的硼化物、碳化物、氮化物、硅化物、磷化物或硫化物所形成的体块晶体或金属或陶瓷或薄膜。
10.优选的,步骤s1中,所述保护材料全覆盖所述氮化铝晶片。
11.优选的,步骤s1中,覆盖于待处理氮化铝晶片上下表面上的保护材料为两层以上。
12.可选的,步骤s2中,所述容器由铝、硅、钨、钽、钼、铌、钒、铬、钛、锆、石墨单质或上述材料的硼化物、碳化物、氮化物、硅化物、磷化物或硫化物所形成的体块晶体或陶瓷或金属制成。
13.优选的,所述容器于底部设有用于支撑所述夹层组合结构的多个支撑柱,或者于底部设有表面呈多个波浪形凸起的粗糙体块。
14.可选的,步骤s3中,所述保护气体为氮气、氢气、氩气、氨气中的一种或几种组合气体,所述低压环境气压为10
‑2~50kpa。
15.可选的,步骤s3中,所述预设保温温度为1500~2300℃,保温时间大于0.1h。
16.优选的,步骤s3中,所述保护气体为氮气,所述预设保温温度为1700~2000℃,采用氮气保护,所述低压环境气压为5~30kpa,保温时间为1~20h。
17.可选的,步骤s4中,去除所述夹层组合结构中的保护材料的方法包括直接去除、切割去除、研磨去除、抛光去除、化学腐蚀去除的一种或几种方法的组合。
18.本发明的有益效果如下:1)高温低压环境能够驱动晶片内部非故意掺杂的杂质(如si、o和c)扩散出晶片至环境中,从而能够大幅降低点缺陷(如复合体(v
al
‑
o
n
)
‑
或(v
al
‑
o
n
)2‑
,以及本征点缺陷如al空位密度)密度,有效提高晶片的紫外透过率,同时还能改善晶片中由点缺陷导致的整体颜色均匀性;2)在晶片两面采用保护夹层的方法,避免了高温低压环境下晶片出现大量升华和变形弯曲等现象,从而保证晶片厚度不发生变化、不破坏晶片,确保高产出,尤其适用于工业界量产环节。
附图说明
19.图1为本发明方法实施例的工艺流程示意图。
20.图2为本发明方法实施例中装配流程结构示意图。
21.图3为本发明方法实施例的工艺温度曲线图。
22.图4 为本发明方法实施例中多片装配结构示意图。
23.图5 为本发明方法实施例中多保护层装配结构示意图。
24.图6 为本发明方法实施例中容器内第一种支撑方式示意图。
25.图7 为本发明方法实施例中容器内第二种支撑方式示意图。
26.图8为经本发明方法处理前后氮化铝晶片的对比图。
27.图9为经本发明方法处理前后氮化铝晶片的紫外吸收系数对比图。
具体实施方式
28.为了进一步理解本发明,下面结合实施例对本发明优选实施方案进行描述,但是应当理解,这些描述只是为进一步说明本发明的特征和优点,而不是对本发明权利要求的限制。
29.本发明提供了一种提高氮化铝晶片紫外透过率的方法,其过程概述为:准备多片aln晶片及多片保护层覆盖片、高温热处理、去除保护层。
30.具体来讲,如图1和图2所示,在一种示出实施方案中,本发明的方法主要包括准备氮化铝晶片1及保护层晶片2、3组成夹层组合结构a的程序t1,改善氮化铝晶片紫外透过率的高温低压热处理程序t2;以及经过切抛磨得到高紫外透过率的氮化铝晶片的程序t3。
31.参考附图3,高温低压热处理程序t2中,首先炉内抽真空,在时间t0~t1h内由t0升温到t1℃,期间充入气体后保持气压稳定,在时间t1~t2h内保温,降温工艺是在时间t2~t3h降温到室温。在升降温区间内,气压是可变的。
32.下面结合具体实施例对本发明的方案作进一步详细说明。
33.实施例1:参考附图1
‑
3及图6,本示出实施例的实施步骤如下:步骤t11:准备一片aln单晶片1和两片aln多晶保护层2和3,aln单晶片1的取向为c向,及其厚度为0.6mm,两片aln多晶保护层2和3的厚度均为1mm。aln单晶片和两片aln多晶保护层均进行了双面研磨。aln单晶片的初始紫外吸收系数在265nm波长下为30
‑
45cm
‑1。
34.步骤t12:将aln单晶片和两片aln多晶保护层2和3组成夹层组合结构a,并将该夹层组合结构a放入由上下钨片4、6和圆筒钨物件5组成容器中,形成密闭环境。将装配好的容器放置于高温炉中。
35.步骤t21:高温炉内抽高真空至真空度达10
‑4pa。
36.步骤t22:启动加热并充入高纯氮气,达到低气压值10kpa并保压,升温速率为5
‑
20℃/min。
37.步骤t23:升温到预设温度2000
‑
2150℃,控温至上下红外检测温差为
±
10℃,持续保温5
‑
10h进行高温低压aln晶片热处理。
38.步骤t24:降温并冷却至室温,降温速率为5
‑
20℃/min。
39.步骤t31:取出容器,并从容器中取出aln单晶片1和两片aln多晶保护层2和3的夹层组合结构a。
40.步骤t32:评估经热处理后的两片aln多晶保护层2和3所剩厚度,首先通过金刚石单线切割,然后再进行研磨抛光将两片aln多晶保护层2和3从aln晶片上下表面完全去除。
41.参考附图8,经上述处理流程后,氮化铝晶片整体颜色发生明显变化,呈现均匀统一透白的成色,明显改观了晶片外观成色。参考附图9,对比处理前后的aln晶片紫外吸收图谱,表明aln晶片经本方法处理后吸收系数在紫外波段有明显下降,在紫外高效杀菌消毒265nm波长下的吸收系数低至15cm
‑1以下。并且,晶片厚度基本无损耗,有利于保证生产良率
的高水准。以上结果表明本实施例中的方法完全达到了本发明预期的技术效果。
42.实施例2:参考附图1、3、4
‑
5及图7,本示出实施例的实施步骤如下:步骤一:准备多片aln单晶片1和多片aln多晶保护层2、3、4、5,aln单晶片的取向为c或m或带有偏角的r向,及其厚度在0.3
‑
2mm之间,aln多晶保护层2、3、4、5的厚度在0.5
‑
4mm之间。每一片aln单晶片由两片aln多晶保护层进行全覆盖。
43.步骤二:参考附图4,将每片aln单晶片1与其对应的两片aln多晶保护层2、3、4、5组成多个夹层组合结构,并将多个夹层组合结构放入多层容器中,形成密闭环境。将装配好的容器放置于高温炉中。
44.步骤三:炉内抽高真空至真空度达10
‑4pa。
45.步骤四:启动加热并充入高纯氩气,达到低气压值15kpa并保压,升温速率为5
‑
20℃/min。
46.步骤五:升温到预设温度1800
‑
2000℃,控温至上下红外检测温差为
±
10℃,持续保温10
‑
30h进行高温低压aln晶片热处理。
47.步骤六:降温并冷却至室温,降温速率为5
‑
20℃/min。
48.步骤七:取出多层容器,然后从每个容器中取出夹层组合结构a。
49.步骤八:评估经热处理后多个夹层组合结构a的两片aln多晶保护层2和3所剩厚度,首先在380℃的koh/naoh共晶溶液中浸泡30min,然后再进行研磨抛光将aln多晶保护层2和3从aln晶片上下表面完全去除。
50.实施例3:参考附图1
‑
3及图6,本示出实施例的实施步骤如下:步骤t11:准备一片aln单晶片1和钽片保护层2和3,aln单晶片1的取向为m向,双面研磨及其厚度2.2mm,钽片保护层2和3的厚度均为1.8mm。aln单晶片进行了。aln单晶片的初始紫外吸收系数在265nm波长下为45
‑
55cm
‑1。
51.步骤t12:将aln单晶片和钽片保护层2和3组成夹层组合结构a,并将该夹层组合结构a放入由上下钽片4、6和圆筒钨物件5组成容器中,形成密闭环境。将装配好的容器放置于高温炉中。
52.步骤t21:高温炉内抽高真空至真空度达10
‑5pa。
53.步骤t22:启动加热并充入高纯氮气,达到低气压值5kpa并保压,升温速率为5
‑
20℃/min。
54.步骤t23:升温到预设温度2000
‑
2200℃,控温至上下红外检测温差为
±
8℃,持续保温12
‑
18h进行高温低压aln晶片热处理。
55.步骤t24:降温并冷却至室温,降温速率为5
‑
20℃/min。
56.步骤t31:取出容器,并从容器中取出aln单晶片1和两片钽片保护层2和3的夹层组合结构a。
57.步骤t32:评估经热处理后的两片aln多晶保护层2和3所剩厚度,通过等离子激光切割将钽片保护层2和3从aln晶片上下表面去除。
58.需要说明的是,上述实施例仅为本发明方法的三种具体实施方案,并不构成对本发明技术方案的限制。本发明的其它实施例中,密闭的系统中可放置一层或多层的晶片,高
温(>1900℃)、低压(10
‑2‑
50kpa)热处理环境有利于晶片内部的原子进入平衡的位置,减少点缺陷等,应力得到释放,内部的杂质原子扩散,从而改善aln晶片紫外(uv)透过率。在降温过程中为了进一步释放晶片内应力,也可以选择多段式降温在低温(1400
‑
1800℃)保温2
‑
15h。高质量aln晶片放置在中间,上下两层由保护层覆盖。上层晶片通过自身的升华减少高质量aln晶片的升华量,下层晶片一方面减少高质量aln晶片升华,另一方面通过控制下层晶片厚度即使与搭载部件接触粘结或产生裂纹也不会影响到中间高质量aln晶片,最终达到降低中间高质量aln晶片升华量,减少其质量及尺寸耗损。完成热处理后,切抛研磨方式去除上下表面的保护晶片层,得到优化的紫外(uv)透过率aln晶片,在深紫外波段的紫外吸收系数为小于或等于18cm
‑1。该装置及方法为制造高紫外(uv)透过率的aln衬底可行性提供了有效技术手段。
59.以上实施例的说明只是用于帮助理解本发明的方法及其核心思想。应当指出,对于本技术领域的普通技术人员来说,在不脱离本发明原理的前提下,还可以对本发明进行若干改进和修饰,这些改进和修饰也落入本发明权利要求的保护范围内。