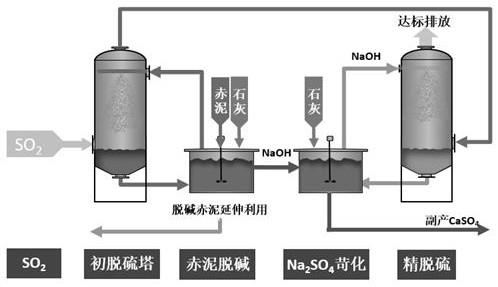
1.本发明涉及一种赤泥深度脱硫并全量化利用的方法,属于大宗固废与含硫废气同步资源化的环境保护领域。
背景技术:2.赤泥是制铝工业提取氧化铝时排出的强碱性工业固体废物,其ph值约为10
‑
12,一般平均每生产1吨氧化铝附带产生1.0
‑
2.0吨赤泥。我国作为氧化铝生产大国,每年排放的赤泥高达数百万吨。产生的赤泥除少部分应用于建筑材料等用途外,大多数赤泥采用湿法露天贮坝堆存。高碱性、高盐度的赤泥废液造成周边土壤盐碱化,恶化生态环境。同时,so2是我国目前主要的大气污染物之一,是环境酸化的主要前驱物,每年仅由于so2排放造成的酸雨等重大环境问题的损失多大数千亿元,对人类的生存环境带来了极大危害,因此实现so2的低成本、低碳环保污染治理迫在眉睫。
3.现有的赤泥用于脱硫的工艺或装置,可以满足达标排放的基本要求,但是脱硫后钠盐存在于脱硫渣中,无法后续大规模利用,无法根据上解决赤泥脱碱的要求。因此,如何利用赤泥脱硫耦合脱碱是目前存在的技术难点。本发明创造性地将烟气脱硫与赤泥脱碱进行技术耦合,解决了气
‑
固两类污染问题,并达到赤泥后续大规模利用和脱硫石膏的利用问题。
技术实现要素:4.本发明的目的是针对目前仅用赤泥矿浆脱硫工艺的不足和石灰脱硫的高成本问题,提供一种石灰苛化赤泥深度脱硫并全量利用的新方法,赤泥中含有大量的有效固硫成分,如cao、mgo和na2o等,利用赤泥和石灰耦合脱硫,不但脱硫效果好,还可以使赤泥本身脱碱,并副产高纯度石膏,实现了含so2烟气和大宗固废赤泥的同步治理和资源化,符合国家减污降碳的环境目标,具体内容如下:
5.(1)在第一循环曹内将各类氧化铝工艺生成的固废赤泥浆液配浆,并投配石灰得到浆液a,其中浆液a的液固体积比为7~15:1,浆液a进入一级脱硫塔与so2烟气逆向接触循环脱硫,根据赤泥的化学成分,浆液a中石灰投加量占赤泥+石灰总质量的 10~30%,实现同步脱硫与赤泥脱碱度,使得硫酸钠充分苛化产生naoh,实现赤泥初步脱硫耦合赤泥脱碱。
6.(2)苛化产生naoh后的浆液进入第二循环槽,并投配石灰得到浆液b,浆液b 中石灰投加量与naoh摩尔比控制大于等于1,浆液b中液固体积比为20
‑
30:1,浆液 b进入二级脱硫塔,在二级脱硫塔与一级脱硫塔处理后的so2烟气逆向接触脱硫,实现深度脱硫耦合产生高纯度脱硫石膏。
7.优选的,本发明步骤(1)中浆液温度为40
‑
75℃,循环浆液ph值保持在7
‑
10。
8.优选的,本发明步骤(1)脱硫塔液气比10
‑
20:1l/m3。
9.优选的,本发明步骤(2)中浆液温度为40
‑
60℃,循环浆液ph值保持在4
‑
6.
10.优选的,本发明步骤(2)中脱硫塔液气比8
‑
15:1l/m3。
11.优选的,本发明步骤(2)中投加的石灰量与循环液中naoh摩尔比为1
‑
1.5:1,提高脱硫效果与副产石膏的纯度。
12.初步脱硫塔和第二级脱硫塔均采用空塔设计,第一级脱硫塔产生固废可满足土壤化和烧结砖对原料的要求,第二级脱硫塔产生精制石膏满足建材对原料的要求。
13.本发明的原理:
14.本发明采用二级脱硫设计,第一级实现赤泥初步脱硫耦合赤泥脱碱,产生的固废符合烧结砖和赤泥土壤化对钠碱度的要求;第二级实现深度脱硫耦合产生高纯度脱硫石膏;在进口烟气so2浓度3000mg/m3以下的工况下,二级脱硫工艺满足so2超低排放的要求(so2低于50mg/m3)。
15.本发明脱硫过程采用各类氧化铝生成工艺产生的大宗固废赤泥和一般矿山产生的石灰,石灰纯度要求在85%以上即可,一级脱硫发生的化学反应式:
16.na2o
·
al2o3·
1.7sio2·
nh2o+cao
→
3cao
·
al2o3·
xsio2·
(6
‑
2x)h2o+naoh
17.2naoh+so2→
na2so3+h2o
18.2al2o3+9h2so3→
2al2(so4)3+3s+9h2o
19.cao+2so2+h2o
→
2caso3·
12h2o
20.2cao
·
sio2+2h2so3→
2caso3+sio2+2h2o
21.cao+h2o
→
ca(oh)222.ca(oh)2+so2→
caso3+h2o
23.2caso3+o2→
2caso424.2na2so3+o2→
2na2so425.2fe2o3+4h2so3+o2→
4feso4+4h2o
26.ca(oh)2+feso4→
fe(oh)2+caso427.4fe(oh)2+2h2o+o2→
4fe(oh)328.ca(oh)2+na2so4→
caso4+2naoh
29.二级脱硫发生的化学反应式:
30.2naoh+so2→
na2so3+h2o
31.2na2so3+o2→
2na2so432.cao+h2o
→
ca(oh)233.ca(oh)2+na2so4→
caso4+2naoh
34.通过赤泥与石灰的耦合设计的二级深度脱硫新工艺,可实现含so2烟气超低排放,脱硫后赤泥钠碱低于0.1%,满足烧结砖和土壤化的要求,且副产高纯度石膏(纯度大于95%),满足石膏建材对原料的要求;与其它脱硫技术相比,本发明采用两级脱硫工艺,可以实现赤泥脱钠碱与高纯度石膏的回收,避免赤泥后续资源化利用过程白霜(钠盐溶出)现象;一级脱硫塔内脱硫效率85
‑
95%,二级脱硫塔内脱硫效率90%以上。
35.本发明的有益效果:
36.(1)本发明将赤泥碱性物质与石灰石苛化硫酸盐的能力结合,充分发挥赤泥碱性脱硫的潜力,大大降低脱硫石灰的用量。充分利用赤泥中的活性钠碱、固体碱实现烟气的初步脱硫,符合固废资源化利用和碳减排的国家需求;本发明根据赤泥脱硫过程中碱度的变换,巧妙地引入石灰中间介质,解决了赤泥活性碱的存在制约赤泥大规模利用的瓶颈。
37.(2)本发明利用两级脱硫系统,第一级实现高浓度高负荷脱硫,第二级实现深度脱硫,通过两级脱硫设计实现脱硫石膏的高纯度回收,更符合国家低碳发展的要求。采用二级逆流脱硫的新工艺,第一级以混合矿浆高固液比初步脱硫、第二级低固液比深度脱硫,两级脱硫解决了赤泥脱碱、石膏纯度的两项资源化利用对工艺操作的要求,真正实现了赤泥全量化利用,有利于推动2060年碳中和目标的实现。
38.(3)本发明两个循环槽内固液分离的产物不同,避免了混合物料给后续利用带来的环境问题,实现了脱硫产物的高值化利用。
附图说明
39.图1为本发明的工艺流程图。
具体实施方式
40.下面结合具体实施实例对本发明作进一步详细说明,但保护范围并不限于以下所述内容。
41.实施例1
42.一种石灰苛化赤泥深度脱硫并全量利用的新方法,实现铝业烟气深度脱硫并资源化利用,具体步骤如下:
43.(1)将拜耳法赤泥与石灰混合制备第一循环槽浆液,用于氧化铝企业锅炉烟气脱硫,其中,浆液a中石灰投加量占赤泥+石灰总质量的15%;将赤泥和投加的石灰与水按8:1的液固体积比在第一循环曹内混合均匀得赤泥浆液a,浆液a进入一级脱硫塔与so2烟气逆向接触循环脱硫,产生的硫酸钠充分苛化产生naoh,确保脱硫与赤泥脱碱度同步实现;其中,赤泥固体的主要组分质量百分比为20%al2o3,8%sio2, 25%fe2o3,20%cao,7%na2o,3%tio2。苛化产生naoh后的浆液b进入第二循环槽,投配石灰与循环液naoh摩尔比1:1,浆液b进入二级脱硫塔,与一级脱硫塔处理后的so2烟气逆向接触脱硫,实现深度脱硫耦合产生高纯度脱硫石膏。
44.(2)一级脱硫塔工况:脱硫塔内浆液a的液固体积比为8:1,实测进口烟气浓度在1500
‑
2200mg/m3之间,浆液温度控制在55
‑
70℃之间,循环液ph值保持在8.5,脱硫塔液气比10:1l/m3,一级脱硫塔循环浆液与so2烟气逆向接触脱硫,脱硫效率90%。
45.(3)二级脱硫塔工况:脱硫塔内液固体积比控制在20:1,实测进口烟气浓度在 300
‑
350mg/m3之间,浆液温度为50
‑
55℃之间,循环液ph值保持在5.5,脱硫塔液气比8:1l/m3,二级脱硫塔循环浆液与so2烟气逆向接触脱硫,脱硫效率93%以上。
46.本实施例中赤泥与石灰耦合的二级深度脱硫新工艺,实现含so2烟气排放浓度低于35mg/m3的超低排放效果,脱硫后赤泥钠碱低于0.1%,副产高石膏纯度大于95%。
47.实施例2
48.一种石灰苛化赤泥深度脱硫并全量利用的新方法,实现铜业烟气深度脱硫并资源化利用,具体步骤如下:
49.(1)将拜耳法赤泥研磨至200目与石灰混合配置成循环液a,用于铜冶炼烟气深度脱硫,其中,浆液a中石灰投加量占赤泥+石灰总质量的15%;浆液a进入一级脱硫塔与so2烟气逆向接触循环脱硫,使得硫酸钠充分苛化产生naoh,实现赤泥初步脱硫耦合赤泥脱碱;其
中,赤泥固体的主要组分质量百分比为15%al2o3,14%sio2, 30%fe2o3,25%cao,5%na2o,3%tio2。苛化产生naoh后的浆液b进入第二循环槽,投配石灰与循环液naoh摩尔比1.3:1,浆液b进入二级脱硫塔,与一级脱硫塔处理后的so2烟气逆向接触脱硫,实现深度脱硫耦合产生高纯度脱硫石膏。
50.(2)一级脱硫塔工况:脱硫塔内浆液a的液固体积比为10:1,实测进口烟气浓度在2800
‑
3000mg/m3之间,浆液温度在50
‑
65℃之间,循环液ph值保持在8.0
‑
9.0之间,脱硫塔液气比15:1l/m3,一级脱硫塔循环浆液与so2烟气逆向接触脱硫,脱硫效率 92%。
51.(3)二级脱硫塔工况:脱硫塔内液固体积比为25:1,进口烟气浓度在400
‑
480mg/m3之间,浆液温度在55
‑
60℃之间,循环液ph值保持在5.0
‑
6.0之间,脱硫塔液气比15:1 l/m3,二级脱硫塔循环浆液与so2烟气逆向接触脱硫,脱硫效率95%以上。
52.本实施例中赤泥与石灰耦合的二级深度脱硫新工艺,实现铜冶炼烟气so2浓度低于50mg/m3超低排放,脱硫后赤泥钠碱低于0.05%,副产高石膏纯度大于97%。
53.实施例3
54.一种石灰苛化赤泥深度脱硫并全量利用的新方法,实现工业硅烟气深度脱硫并资源化利用,具体步骤如下:
55.(1)将拜耳法赤泥研磨至300目与石灰混合配置成循环液a,用于煅烧石油焦烟气脱硫,其中,浆液a中石灰投加量占赤泥+石灰总质量的30%。浆液a进入一级脱硫塔与so2烟气逆向接触循环脱硫,使得硫酸钠充分苛化产生naoh,实现赤泥初步脱硫耦合赤泥脱碱;其中,赤泥固体的主要组分质量百分比为13%al2o3,22%sio2, 23%fe2o3,27%cao,8%na2o,2%tio2。苛化产生naoh后的浆液b进入第二循环槽,投配石灰与循环液naoh摩尔比1.5:1,浆液b进入二级脱硫塔,与一级脱硫塔处理后的so2烟气逆向接触脱硫,实现深度脱硫耦合产生高纯度脱硫石膏。
56.(2)一级脱硫塔工况:脱硫塔内浆液a的液固体积比为15:1,实测进口烟气浓度在2500
‑
2800mg/m3之间,浆液温度在60
‑
65℃之间,循环液ph值保持在8.5
‑
10.0之间,脱硫塔液气比15:1l/m3,一级脱硫塔循环浆液与so2烟气逆向接触脱硫,脱硫效率 90%。
57.(3)二级脱硫塔工况:脱硫塔内液固体积比控制在30:1,实测进口烟气浓度在 380
‑
450mg/m3之间,浆液温度在50
‑
55℃之间,循环液ph值保持在5.0
‑
5.5之间,脱硫塔液气比10:1l/m3,二级脱硫塔循环浆液与so2烟气逆向接触脱硫,脱硫效率97%以上。
58.本实施例中赤泥与石灰耦合的二级深度脱硫新工艺,实现工业硅冶炼烟气so2浓度低于35mg/m3超低排放,脱硫后赤泥钠碱低于0.1%,副产高石膏纯度大于95%。