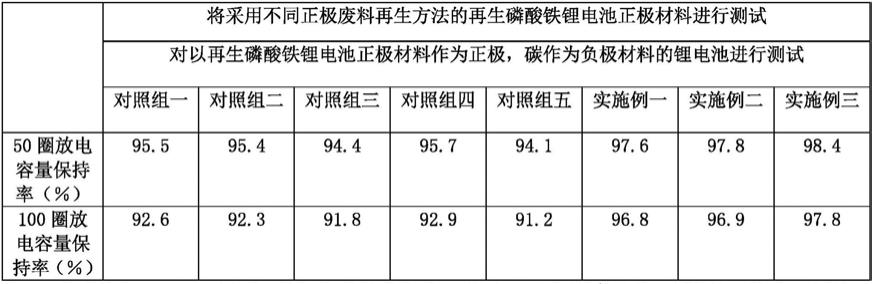
1.本发明涉及锂电池正极再生工艺技术领域,更具体地说,本发明涉及一种报废磷酸铁锂电池的正极废料再生方法。
背景技术:2.磷酸铁锂电池,是一种使用磷酸铁锂(lifepo4)作为正极材料,碳作为负极材料的锂离子电池。lifepo4具有较高的容量,低廉的价格,高的安全性以及环境友好等优点,是最有应用前景的锂离子电池正极材料。lifepo4电池具有高能量密度,安全性能好,无记忆效应,寿命长等优点,因此使用量在不断增加,然而,巨大的锂离子电池生产消费带来了数目惊人的报废电池。电池经过长期使用后,充放电容量会降低,最终不能满足使用的要求。其中原因之一是lifepo4会发生部分分解,产生fepo4和p2o5等杂质。因此,为了使正极废料能被重新利用,许多学者进行了这方面的研究。
3.现有的报废磷酸铁锂电池的正极废料再生方法,在热处理过程中由于li2o的挥发,并不能使修复效果达到最佳。
技术实现要素:4.为了克服现有技术的上述缺陷,本发明的实施例提供一种报废磷酸铁锂电池的正极废料再生方法。
5.一种报废磷酸铁锂电池的正极废料再生方法,具体再生步骤如下:
6.步骤一:将拆解下来的正极片进行粉碎处理,得到正极粉碎料;
7.步骤二:将步骤一中制得的正极粉碎料加入到在ph=9~11的稀naoh溶液中进行搅拌、离心,得到从铝箔上脱落的正极废料;
8.步骤三:将步骤二中制得的正极废料在65~75℃下真空干燥8~12h,420~480r/min球磨2~5h,过筛后得到待补锂再生的正极废料;
9.步骤四:将步骤三中制得的待补锂再生的正极废料添加补锂改性剂,进行微波辅助水热处理10~15分钟,然后进行真空干燥、球磨、过300~400目筛,得到补锂的正极废料;
10.步骤五:将步骤四中制得的补锂再生的正极废料进行压片,放入管式炉中煅烧,得到煅烧补锂正极废料;
11.步骤六:将步骤五中制得的煅烧补锂正极废料使用去离子水进行洗涤、抽滤,干燥后即可得到再生后的正极材料。
12.进一步的,在步骤四中,微波辅助水热法中,微波功率为300~400w,温度为175~215℃;在步骤五中,煅烧在h2/ar气氛下进行,升温速度为1~3℃/min,煅烧温度分别为600~800℃,煅烧时间为1~3h,h2/ar气氛中h2含量为3~5%。
13.进一步的,在步骤四中,待补锂再生的正极废料与补锂改性剂的重量比为:1∶1~2。
14.进一步的,在步骤二中的所述补锂改性剂按照重量百分比计算包括:51.40~
52.20%的碳酸锂、3.80~4.60%的淀粉、5.20~5.60%的硝酸银、5.40~6.20%的硫酸钛、0.35~0.55%的硅烷偶联剂、5.20~5.80%的碳纳米管,其余为去离子水;
15.所述补锂改性剂的制备工艺,具体制备步骤如下:
16.s1:称取上述重量份的碳酸锂、淀粉、硝酸银、硫酸钛、硅烷偶联剂、碳纳米管和去离子水;
17.s2:将步骤s1中的淀粉、硝酸银和三分之一重量份的去离子水中进行混合,进行水浴双频超声处理30~40min,得到混合料a;
18.s3:将氯化十六烷基吡啶加入到步骤s1中三分之一重量份的去离子水中,搅拌混合5~10min后加入环糊精,继续搅拌5~10min后加入步骤s1中的硫酸钛,超声处理5~10min,得到混合料b;
19.s4:将步骤s3中制得的混合料b、步骤s2中制得的混合料a和步骤s1中的碳酸锂、硅烷偶联剂、碳纳米管和去离子水进行混合,得到补锂改性剂。
20.进一步的,所述补锂改性剂按照重量百分比计算包括:51.40%的碳酸锂、3.80%的淀粉、5.20%的硝酸银、5.40%的硫酸钛、0.35%的硅烷偶联剂、5.20%的碳纳米管、28.65%的去离子水。
21.进一步的,所述补锂改性剂按照重量百分比计算包括:52.20%的碳酸锂、4.60%的淀粉、5.60%的硝酸银、6.20%的硫酸钛、0.55%的硅烷偶联剂、5.80%的碳纳米管、25.05%的去离子水。
22.进一步的,所述补锂改性剂按照重量百分比计算包括:51.80%的碳酸锂、4.20%的淀粉、5.40%的硝酸银、5.80%的硫酸钛、0.45%的硅烷偶联剂、5.50%的碳纳米管、26.85%的去离子水。
23.进一步的,在步骤s2中,双频超声的频率为26~30khz+1.3~1.5mhz,水浴温度为60~80℃;在步骤s3中,所述氯化十六烷基吡啶的浓度为0.025~0.075mol/l,所述环糊精与所述氯化十六烷基吡啶的摩尔比为1∶1.3~1.5,超声的频率为1.6~1.8mhz。
24.进一步的,在步骤s2中,双频超声的频率为26khz+1.3mhz,水浴温度为60℃;在步骤s3中,所述氯化十六烷基吡啶的浓度为0.025mol/l,所述环糊精与所述氯化十六烷基吡啶的摩尔比为1∶1.3,超声的频率为1.6mhz。
25.进一步的,在步骤s2中,双频超声的频率为28khz+1.4mhz,水浴温度为70℃;在步骤s3中,所述氯化十六烷基吡啶的浓度为0.050mol/l,所述环糊精与所述氯化十六烷基吡啶的摩尔比为1∶1.4,超声的频率为1.7mhz。
26.本发明的技术效果和优点:
27.1、采用本发明的正极废料再生方法制备的再生磷酸铁锂电池正极材料,在步骤一中,对正极片进行粉碎,便于后续正极废料和铝箔的分离;在步骤二中,可有效将铝箔和正极废料进行分离;在步骤三中,制得待补锂再生的正极废料;在步骤四中,添加补锂改性剂,同时进行微波辅助水热处理,可有效加速补锂改性剂和正极废料进行反应,加速补锂再生和废料的浸出效果,使得正极废料再生后具有良好的物理、化学和电化学性能,符合再利用的要求;在步骤五中,对补锂后的正极废料进行压片煅烧处理,保证补锂正极废料结构的稳定性;在步骤六中,对煅烧补锂正极废料进行洗涤、抽滤处理,得到再生后的正极材料;淀粉对硝酸银进行还原反应,再进行水洗真空干燥保证纳米银颗粒负载到再生正极材料上,纳
米银颗粒可有效加强再生正极材料的结构稳定性、导电性能和抗菌性能;在补锂过程中进行微波辅助水热处理,可有效在再生正极材料上形成多层二氧化钛介孔薄膜,同时纳米银离子和碳纳米管可插接到多层二氧化钛介孔薄膜内部,可有效保证再生正极材料的高比容量性能,同时可有效提高再生正极材料的耐老化性能和抗菌性能,同时碳纳米管可有效复合到再生正极材料上,碳纳米管起到导电网络的作用,使得再生正极材料表面电阻更小,可有效提高再生正极材料的放电比容量和长循环稳定性;
28.2、本发明在制备补锂改性剂的过程中,在步骤s2中,对淀粉、硝酸银和去离子水进行混合,70℃水浴28khz+1.4mhz双频超声处理,可有效保证淀粉对硝酸银进行还原反应,制成纳米银颗粒的前驱体,便于后续在补锂过程中快速合成纳米银颗粒;在步骤s3中,使用氯化十六烷基吡啶和环糊精和硫酸钛进行共混1.7mhz超声处理,可有效保证上述原料的接触混合效果,形成多层二氧化钛介孔薄膜前驱体,保证在补锂过程中,形成多层二氧化钛介孔薄膜;在步骤s4中,对混合料a、混合料b、碳酸锂、硅烷偶联剂、碳纳米管和去离子水进行混合制成补锂改性剂。
具体实施方式
29.下面将结合本发明实施例中的技术方案进行清楚、完整地描述,显然,所描述的实施例仅仅是本发明一部分实施例,而不是全部的实施例。基于本发明中的实施例,本领域普通技术人员在没有做出创造性劳动前提下所获得的所有其他实施例,都属于本发明保护的范围。
30.实施例1:
31.本发明提供了一种报废磷酸铁锂电池的正极废料再生方法,具体再生步骤如下:
32.步骤一:将拆解下来的正极片进行粉碎处理,得到正极粉碎料;
33.步骤二:将步骤一中制得的正极粉碎料加入到在ph=9的稀naoh溶液中进行搅拌、离心,得到从铝箔上脱落的正极废料;
34.步骤三:将步骤二中制得的正极废料在65℃下真空干燥8h,420r/min球磨2h,过筛后得到待补锂再生的正极废料;
35.步骤四:将步骤三中制得的待补锂再生的正极废料添加补锂改性剂,进行微波辅助水热处理10分钟,然后进行真空干燥、球磨、过300目筛,得到补锂的正极废料;
36.步骤五:将步骤四中制得的补锂再生的正极废料进行压片,放入管式炉中煅烧,得到煅烧补锂正极废料;
37.步骤六:将步骤五中制得的煅烧补锂正极废料使用去离子水进行洗涤、抽滤,干燥后即可得到再生后的正极材料。
38.在步骤四中,微波辅助水热法中,微波功率为300w,温度为175℃;在步骤五中,煅烧在h2/ar气氛下进行,升温速度为1℃/min,煅烧温度分别为600℃,煅烧时间为1h,h2/ar气氛中h2含量为3%。
39.在步骤四中,待补锂再生的正极废料与补锂改性剂的重量比为:1∶1。
40.所述补锂改性剂按照重量百分比计算包括:51.40%的碳酸锂、3.80%的淀粉、5.20%的硝酸银、5.40%的硫酸钛、0.35%的硅烷偶联剂、5.20%的碳纳米管、28.65%的去离子水;
41.所述补锂改性剂的制备工艺,具体制备步骤如下:
42.s1:称取上述重量份的碳酸锂、淀粉、硝酸银、硫酸钛、硅烷偶联剂、碳纳米管和去离子水;
43.s2:将步骤s1中的淀粉、硝酸银和三分之一重量份的去离子水中进行混合,进行水浴双频超声处理30min,得到混合料a;
44.s3:将氯化十六烷基吡啶加入到步骤s1中三分之一重量份的去离子水中,搅拌混合5min后加入环糊精,继续搅拌5min后加入步骤s1中的硫酸钛,超声处理5min,得到混合料b;
45.s4:将步骤s3中制得的混合料b、步骤s2中制得的混合料a和步骤s1中的碳酸锂、硅烷偶联剂、碳纳米管和去离子水进行混合,得到补锂改性剂。
46.在步骤s2中,双频超声的频率为26khz+1.3mhz,水浴温度为60℃;在步骤s3中,所述氯化十六烷基吡啶的浓度为0.025mol/l,所述环糊精与所述氯化十六烷基吡啶的摩尔比为1∶1.3,超声的频率为1.6mhz。
47.实施例2:
48.与实施例1不同的是,所述补锂改性剂按照重量百分比计算包括:52.20%的碳酸锂、4.60%的淀粉、5.60%的硝酸银、6.20%的硫酸钛、0.55%的硅烷偶联剂、5.80%的碳纳米管、25.05%的去离子水。
49.实施例3:
50.与实施例1
‑
2均不同的是,所述补锂改性剂按照重量百分比计算包括:51.80%的碳酸锂、4.20%的淀粉、5.40%的硝酸银、5.80%的硫酸钛、0.45%的硅烷偶联剂、5.50%的碳纳米管、26.85%的去离子水。
51.分别取上述实施例1
‑
3中的正极废料再生方法与对照组一的正极废料再生方法、对照组二的正极废料再生方法、对照组三的正极废料再生方法、对照组四的正极废料再生方法和对照组五的正极废料再生方法,对照组一的正极废料再生方法与实施例相比水性uv油墨中没有淀粉;对照组二的正极废料再生方法与实施例相比水性uv油墨中没有硝酸银;对照组三的正极废料再生方法与实施例相比水性uv油墨中没有硫酸钛;对照组四的正极废料再生方法与实施例相比水性uv油墨中没有硅烷偶联剂;对照组五的正极废料再生方法与实施例相比水性uv油墨中没有碳纳米管;分八组分别测试三个实施例中再生方法制备的再生磷酸铁锂电池正极材料以及五个对照组的正极废料再生方法制备的再生磷酸铁锂电池正极材料,每30个再生磷酸铁锂电池正极材料实验数据为一组,进行测试,测试结果如表一所示:
52.表一:
[0053][0054]
锂电池在0.05c下先运行五圈,锂电池稳定后,再运行50圈后计算和第6圈相比,得到50圈放电容量保持率,再运行100圈后计算和第51圈相比,得到100圈放电容量保持率;
[0055]
由表一可知,实施例3为本发明的较佳实施方式;在步骤一中,对正极片进行粉碎,可有效加强正极片的粉碎程度,便于后续正极废料和铝箔的分离;在步骤二中,使用稀naoh溶液对正极粉碎料进行搅拌离心处理,可有效将铝箔和正极废料进行分离;在步骤三中,对正极废料进行真空干燥球磨处理,得到待补锂再生的正极废料(内部包含lifepo4、fepo4、p2o5和导电剂的混合物),便于后续补锂再生处理;在步骤四中,添加补锂改性剂,同时进行微波辅助水热处理,可有效加速补锂改性剂和正极废料进行反应,加速补锂再生和废料的浸出效果,同时加强再生之后正极材料的结构稳定性和安全性,使得正极废料再生后具有良好的物理、化学和电化学性能,符合再利用的要求;在步骤五中,对补锂后的正极废料进行压片煅烧处理,可对补锂正极废料进行锁定处理,保证补锂正极废料结构的稳定性,保证其良好的物理、化学和电化学性能;在步骤六中,对煅烧补锂正极废料进行洗涤、抽滤处理,洗掉多余的补锂改性剂和其他废料,干燥后得到再生后的正极材料;补锂改性剂中的碳酸锂对正极废料进行补锂操作,淀粉和硝酸银混共超声处理,淀粉对硝酸银进行还原反应,并在补锂过程中微波水热合成纳米银颗粒,再进行水洗真空干燥保证纳米银颗粒负载到再生正极材料上,纳米银颗粒可有效加强再生正极材料的结构稳定性、导电性能和抗菌性能;硫酸钛在经过氯化十六烷基吡啶和环糊精溶融搅拌混合处理之后,得到二氧化钛介孔薄膜的前驱体,然后在补锂过程中进行微波辅助水热处理,可有效在再生正极材料上形成多层二氧化钛介孔薄膜,同时纳米银离子和碳纳米管可插接到多层二氧化钛介孔薄膜内部,可有效保证再生正极材料的高比容量性能,同时可有效提高再生正极材料的耐老化性能和抗菌性能,同时碳纳米管可有效复合到再生正极材料上,碳纳米管起到导电网络的作用,使得再生正极材料表面电阻更小,可有效提高再生正极材料的放电比容量和长循环稳定性。
[0056]
实施例4:
[0057]
本发明提供了一种报废磷酸铁锂电池的正极废料再生方法,具体再生步骤如下:
[0058]
步骤一:将拆解下来的正极片进行粉碎处理,得到正极粉碎料;
[0059]
步骤二:将步骤一中制得的正极粉碎料加入到在ph=10的稀naoh溶液中进行搅拌、离心,得到从铝箔上脱落的正极废料;
[0060]
步骤三:将步骤二中制得的正极废料在70℃下真空干燥10h,450r/min球磨3.5h,过筛后得到待补锂再生的正极废料;
[0061]
步骤四:将步骤三中制得的待补锂再生的正极废料添加补锂改性剂,进行微波辅助水热处理13分钟,然后进行真空干燥、球磨、过350目筛,得到补锂的正极废料;
[0062]
步骤五:将步骤四中制得的补锂再生的正极废料进行压片,放入管式炉中煅烧,得到煅烧补锂正极废料;
[0063]
步骤六:将步骤五中制得的煅烧补锂正极废料使用去离子水进行洗涤、抽滤,干燥后即可得到再生后的正极材料。
[0064]
在步骤四中,微波辅助水热法中,微波功率为350w,温度为195℃;在步骤五中,煅烧在h2/ar气氛下进行,升温速度为2℃/min,煅烧温度分别为700℃,煅烧时间为2h,h2/ar气氛中h2含量为4%。
[0065]
在步骤四中,待补锂再生的正极废料与补锂改性剂的重量比为:1∶1.5。
[0066]
所述补锂改性剂按照重量百分比计算包括:51.80%的碳酸锂、4.20%的淀粉、5.40%的硝酸银、5.80%的硫酸钛、0.45%的硅烷偶联剂、5.50%的碳纳米管、26.85%的去离子水;
[0067]
所述补锂改性剂的制备工艺,具体制备步骤如下:
[0068]
s1:称取上述重量份的碳酸锂、淀粉、硝酸银、硫酸钛、硅烷偶联剂、碳纳米管和去离子水;
[0069]
s2:将步骤s1中的淀粉、硝酸银和三分之一重量份的去离子水中进行混合,进行水浴双频超声处理35min,得到混合料a;
[0070]
s3:将氯化十六烷基吡啶加入到步骤s1中三分之一重量份的去离子水中,搅拌混合8min后加入环糊精,继续搅拌8min后加入步骤s1中的硫酸钛,超声处理8min,得到混合料b;
[0071]
s4:将步骤s3中制得的混合料b、步骤s2中制得的混合料a和步骤s1中的碳酸锂、硅烷偶联剂、碳纳米管和去离子水进行混合,得到补锂改性剂。
[0072]
在步骤s2中,双频超声的频率为26khz+1.3mhz,水浴温度为60℃;在步骤s3中,所述氯化十六烷基吡啶的浓度为0.025mol/l,所述环糊精与所述氯化十六烷基吡啶的摩尔比为1∶1.3,超声的频率为1.6mhz。
[0073]
实施例5:
[0074]
与实施例4不同的是,在步骤s2中,双频超声的频率为30khz+1.5mhz,水浴温度为80℃;在步骤s3中,所述氯化十六烷基吡啶的浓度为0.075mol/l,所述环糊精与所述氯化十六烷基吡啶的摩尔比为1∶1.5,超声的频率为1.8mhz。
[0075]
实施例6:
[0076]
与实施例4
‑
5均不同的是,在步骤s2中,双频超声的频率为28khz+1.4mhz,水浴温度为70℃;在步骤s3中,所述氯化十六烷基吡啶的浓度为0.050mol/l,所述环糊精与所述氯化十六烷基吡啶的摩尔比为1∶1.4,超声的频率为1.7mhz。
[0077]
分别取上述实施例4
‑
6所制得的正极废料再生方法与对照组六的正极废料再生方法、对照组七的正极废料再生方法和对照组八的正极废料再生方法,对照组六的正极废料再生方法与实施例相比没有步骤s2中的操作,对照组七的正极废料再生方法与实施例相比没有步骤s3的操作,对照组八的正极废料再生方法与实施例相比没有步骤s4的操作,分六组分别测试三个实施例中制备的再生磷酸铁锂电池正极材料以及三个对照组的正极废料再生方法制备的再生磷酸铁锂电池正极材料,每30个再生磷酸铁锂电池正极材料实验数据为一组,进行测试,测试结果如表二所示:
[0078]
表二:
[0079][0080][0081]
锂电池在0.05c下先运行五圈,锂电池稳定后,再运行50圈后计算和第6圈相比,得到50圈放电容量保持率,再运行100圈后计算和第51圈相比,得到100圈放电容量保持率;
[0082]
由表二可知,实施例6为本发明的较佳实施方式;在步骤s2中,对淀粉、硝酸银和去离子水进行混合,70℃水浴28khz+1.4mhz双频超声处理,可有效保证淀粉对硝酸银进行还原反应,制成纳米银颗粒的前驱体,便于后续在补锂过程中快速合成纳米银颗粒;在步骤s3中,使用氯化十六烷基吡啶和环糊精和硫酸钛进行共混1.7mhz超声处理,可有效保证上述原料的接触混合效果,形成多层二氧化钛介孔薄膜前驱体,保证在补锂过程中,形成多层二氧化钛介孔薄膜;在步骤s4中,对混合料a、混合料b、碳酸锂、硅烷偶联剂、碳纳米管和去离子水进行混合制成补锂改性剂。
[0083]
需要说明的是,在本文中,诸如第一和第二等之类的关系术语仅仅用来将一个实体或者操作与另一个实体或操作区分开来,而不一定要求或者暗示这些实体或操作之间存在任何这种实际的关系或者顺序。而且,术语“包括”、“包含”或者其任何其他变体意在涵盖非排他性的包含,从而使得包括一系列要素的过程、方法、物品或者设备不仅包括那些要素,而且还包括没有明确列出的其他要素,或者是还包括为这种过程、方法、物品或者设备所固有的要素。
[0084]
最后应说明的是:以上所述仅为本发明的优选实施例而已,并不用于限制本发明,尽管参照前述实施例对本发明进行了详细的说明,对于本领域的技术人员来说,其依然可以对前述各实施例所记载的技术方案进行修改,或者对其中部分技术特征进行等同替换。凡在本发明的精神和原则之内,所作的任何修改、等同替换、改进等,均应包含在本发明的保护范围之内。