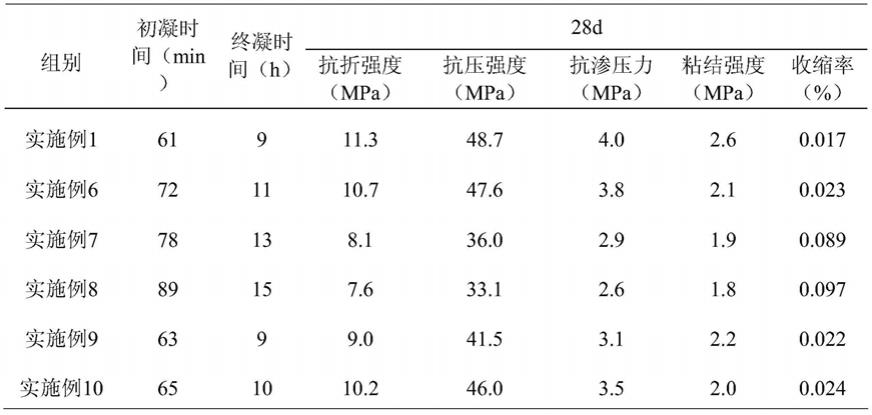
1.本发明属于建筑材料技术领域,具体涉及一种预拌砂浆及其制备方法。
背景技术:2.预拌砂浆是指用于建设工程中的各种砂浆拌合物,是我国近年发展起来的一种新型建筑材料。预拌砂浆具有如下优势:预拌砂浆能够节约现场拌料的时间,提高施工效率;预拌砂浆便于运输与存放,在施工现场,采用预拌砂浆可避免堆积大量的各种原材料,减少对周围环境的污染和影响;目前施工现场配置的砂浆存在质量不稳定,强度等级不均匀,易开裂,空鼓脱落等缺陷,已成为建筑行业普遍存在的问题,而预拌砂浆质量可控。20世纪五十年代初,欧洲国家就开始大量生产和使用预拌砂浆,至今已有50多年的发展历史。随着建筑业技术进步和文明施工要求的提高,预拌砂浆在我国也同样得到越来越大的推广使用,有很大的市场前景。
3.铝渣是一种矿渣废弃物,目前没有很好的回收处理方法,当前技术虽然也有研究使用于水泥中,然而因其自身的性质缺陷,比如含重金属、掺入后影响强度等,掺量通常很低,难以解决废物利用的问题。
4.随着中国经济的持续发展,近年来建筑业一直处于飞速发展状态,砂矿作为重要的建筑原料,需求量巨大。根据调查显示,近年来河道砂石资源逐步减少,导致规划采量逐渐减少,用砂供需矛盾日益突出,建筑用砂价格逐年攀升。河砂被称之为软黄金,但是随着建筑行业的发展,内陆河砂已近枯竭,导致供砂远不能满足市场建筑用砂的需求。我国沿海广阔,有着丰富海砂资源,如果能用海砂代替河砂用于预拌砂浆中,不仅能缓解河砂短缺的问题,而且可降低建筑成本。然而,因海砂具有腐蚀性,因此在建筑过程中难以得到推广使用。
技术实现要素:5.本发明的目的是为了解决现有技术存在的上述问题,提供一种预拌砂浆及其制备方法,本发明利用铝渣作为原料加入预拌砂浆中,再与稠化剂等原料混合使用,降低成本;制备预拌砂浆协同处置铝渣,可有效回收利用矿渣资源。
6.为了达到上述目的,本发明的技术方案如下:
7.一种预拌砂浆,由以下重量份的原料制成:水泥30
‑
50,细度模数为1.6
‑
2.2的海砂30
‑
40,铝渣20
‑
30,甲基纤维素0.03
‑
0.08,玄武岩纤维0.1
‑
1,稠化剂1.5
‑
2.0,聚羧酸减水剂0.1
‑
0.5;所述稠化剂由以下重量份的原料制成:膨润土50
‑
80、石脂10
‑
20、水铝英石5
‑
15、粉煤灰5
‑
10、三乙醇胺油酸皂0.1
‑
0.5、硬脂酸0.1
‑
0.5、醋酸乙烯0.3
‑
0.8。
8.进一步的,所述铝渣中,氧化钙的含量不小于30%,三氧化铝的含量不小于28%,二氧化硅的含量不小于10%。
9.进一步的,所述铝渣进行如下处理后再使用:将铝渣粉碎至0.25mm方孔筛筛余不大于10%,边搅拌边向粉碎后的铝渣中喷处理剂进行处理,处理过程的温度控制在40
‑
50
℃,搅拌速度50
‑
60r/min,处理时间为30
‑
40min,将处理得到的铝渣控干水分至含水量<1%即可;所述处理剂是由fecl2、泡花碱、k2sio3和海水混合制得,所述每kg处理剂中的各组分含量如下:fecl
2 3
‑
5g、泡花碱200
‑
300g、k2sio
3 3
‑
4g,余量为海水;所述处理剂的使用量为每吨铝渣中喷洒180
‑
200公斤处理剂。
10.进一步的,所述稠化剂的制备方法包括如下步骤:将膨润土、石脂、水铝英石、粉煤灰烘干至水分小于1%;将三乙醇胺油酸皂、硬脂酸加入膨润土中混合,然后加入磨机中混磨,物料磨至0.25mm方孔筛筛余不大于10%,得到混合物i;在混合物i中加入石脂、水铝英石,温度控制在40
‑
45℃,继续在磨机中混磨,物料磨至0.25mm方孔筛筛余不大于10%,得到混合物ii;边搅拌边在粉煤灰中加入醋酸乙烯,混合均匀后得到混合物iii;在混合物ii中加入混合物iii,于30
‑
40℃温度下在磨机中混合研磨10
‑
20min,静置5
‑
10min,再研磨5
‑
10min,制得稠化剂。
11.本发明还提供所述的预拌砂浆的制备方法,包括如下步骤:按原料的配方比例称取水泥、海砂、铝渣和玄武岩纤维,加入混合机中搅拌混合,搅拌速度为300
‑
400r/min,搅拌10
‑
20min,再加入甲基纤维素、稠化剂和聚羧酸减水剂,以转速200
‑
300r/min混合20
‑
30min,制得预拌砂浆。
12.进一步的,所述水泥、铝渣、玄武岩纤维的细度控制在0.25mm方孔筛筛余不大于10%,水分含量不大于1%。
13.本发明具有以下有益效果:
14.本发明通过将铝渣进行处理后,作为原料加入预拌砂浆中,再与稠化剂等原料混合使用,不仅可回收利用铝渣,降低生产成本,而且可提高预拌砂浆的强度。
15.本发明通过由fecl2、泡花碱、k2sio3和海水混合制得的处理剂对铝渣进行处理,在处理过程中,通过fecl2将重金属还原的同时通过泡花碱、k2sio3对其进行固化,海水起到辅助促进作用,能够有效固化铝渣中的重金属,从而使重金属稳定,在预拌砂浆成品的使用过程中不会发生迁移。
16.本发明研究发现,海砂虽然本身具有腐蚀性,但是与本发明的铝渣、稠化剂等原料混合使用制成预拌砂浆后,经试验发现,添加了海砂的预拌砂浆与添加了河砂的预拌砂浆在使用性能方面并无太大差异,因此通过本发明的配方及制备方法可以将海砂代替河砂使用于预拌砂浆中。
具体实施方式
17.下面结合具体的实施例对本发明作进一步说明。
18.实施例1
19.一种预拌砂浆,由以下重量份的原料制成:水泥5,细度模数为1.6
‑
2.2的海砂33,铝渣22,甲基纤维素0.04,玄武岩纤维0.3,稠化剂1.6,聚羧酸减水剂0.2;所述稠化剂由以下重量份的原料制成:膨润土55、石脂12、水铝英石8、粉煤灰6、三乙醇胺油酸皂0.2、硬脂酸0.2、醋酸乙烯0.4。
20.所述铝渣中,氧化钙的含量为31.1%,三氧化铝的含量为29.3%,二氧化硅的含量为10.4%。所述铝渣进行如下处理后再使用:将铝渣粉碎至0.25mm方孔筛筛余不大于10%,边搅拌边向粉碎后的铝渣中喷处理剂进行处理,处理过程的温度控制在45℃,搅拌速度
55r/min,处理时间为35min,将处理得到的铝渣控干水分至含水量<1%即可;所述处理剂是由fecl2、泡花碱、k2sio3和海水混合制得,所述每kg处理剂中的各组分含量如下:fecl
2 4g、泡花碱250g、k2sio
3 3.5g,余量为海水;所述处理剂的使用量为每吨铝渣中喷洒190公斤处理剂。
21.经本实施例处理的铝渣按照hjt299
‑
2007《固体废物浸出毒性浸出方法
‑
硫酸硝酸法》进行浸出试验,结果如下:
22.处理前:ni含量3.92mg/l,cr含量34.10mg/l;
23.处理后:ni含量0.05mg/l,cr含量0.73mg/l。
24.所述稠化剂的制备方法包括如下步骤:将膨润土、石脂、水铝英石、粉煤灰烘干至水分小于1%;将三乙醇胺油酸皂、硬脂酸加入膨润土中混合,然后加入磨机中混磨,物料磨至0.25mm方孔筛筛余不大于10%,得到混合物i;在混合物i中加入石脂、水铝英石,温度控制在40℃,继续在磨机中混磨,物料磨至0.25mm方孔筛筛余不大于10%,得到混合物ii;边搅拌边在粉煤灰中加入醋酸乙烯,混合均匀后得到混合物iii;在混合物ii中加入混合物iii,于35℃温度下在磨机中混合研磨15min,静置8min,再研磨8min,制得稠化剂。
25.所述的预拌砂浆的制备方法,包括如下步骤:按原料的配方比例称取水泥、海砂、铝渣和玄武岩纤维,所述水泥、铝渣、玄武岩纤维的细度控制在0.25mm方孔筛筛余不大于10%,加入混合机中搅拌混合,搅拌速度为350r/min,搅拌15min,再加入甲基纤维素、稠化剂和聚羧酸减水剂,以转速250r/min混合25min,制得预拌砂浆。
26.将实施例1制备得到的预拌砂浆调浆后浇筑入圆钢管,设为试验组;同时使用河砂代替海砂并用实施例1的方法制备预拌砂浆,将预拌砂浆调浆后浇筑入与试验组相同型号的圆钢管,设为对照组;将试验组和对照组的试件进行轴压试验,静置240天后再次进行轴压试验,轴压试验参考gb50936
‑
2014;最终轴压承载力下降率:试验组5.3%,对照组5.0%。可见,本发明使用海砂代替河砂使用于预拌砂浆中,在腐蚀性方面差别不大,本发明使用海水代替河砂使用是可行的。
27.实施例2
28.一种预拌砂浆,由以下重量份的原料制成:水泥45,细度模数为1.6
‑
2.2的海砂38,铝渣27,甲基纤维素0.06,玄武岩纤维0.8,稠化剂1.9,聚羧酸减水剂0.4;所述稠化剂由以下重量份的原料制成:膨润土70、石脂18、水铝英石13、粉煤灰8、三乙醇胺油酸皂0.4、硬脂酸0.4、醋酸乙烯0.6。
29.所述铝渣中,氧化钙的含量为31.1%,三氧化铝的含量为29.3%,二氧化硅的含量为10.4%。所述铝渣进行如下处理后再使用:将铝渣粉碎至0.25mm方孔筛筛余不大于10%,边搅拌边向粉碎后的铝渣中喷处理剂进行处理,处理过程的温度控制在40℃,搅拌速度60r/min,处理时间为30min,将处理得到的铝渣控干水分至含水量<1%即可;所述处理剂是由fecl2、泡花碱、k2sio3和海水混合制得,所述每kg处理剂中的各组分含量如下:fecl
2 3.5g、泡花碱220g、k2sio
3 3.2g,余量为海水;所述处理剂的使用量为每吨铝渣中喷洒180公斤处理剂。
30.所述稠化剂的制备方法包括如下步骤:将膨润土、石脂、水铝英石、粉煤灰烘干至水分小于1%;将三乙醇胺油酸皂、硬脂酸加入膨润土中混合,然后加入磨机中混磨,物料磨至0.25mm方孔筛筛余不大于10%,得到混合物i;在混合物i中加入石脂、水铝英石,温度控
5g、泡花碱300g、k2sio33g,余量为海水;所述处理剂的使用量为每吨铝渣中喷洒180公斤处理剂。
40.所述稠化剂的制备方法包括如下步骤:将膨润土、石脂、水铝英石、粉煤灰烘干至水分小于1%;将三乙醇胺油酸皂、硬脂酸加入膨润土中混合,然后加入磨机中混磨,物料磨至0.25mm方孔筛筛余不大于10%,得到混合物i;在混合物i中加入石脂、水铝英石,温度控制在40℃,继续在磨机中混磨,物料磨至0.25mm方孔筛筛余不大于10%,得到混合物ii;边搅拌边在粉煤灰中加入醋酸乙烯,混合均匀后得到混合物iii;在混合物ii中加入混合物iii,于30℃温度下在磨机中混合研磨20min,静置5min,再研磨10min,制得稠化剂。
41.所述的预拌砂浆的制备方法,包括如下步骤:按原料的配方比例称取水泥、海砂、铝渣和玄武岩纤维,所述水泥、铝渣、玄武岩纤维的细度控制在0.25mm方孔筛筛余不大于10%,加入混合机中搅拌混合,搅拌速度为300r/min,搅拌20min,再加入甲基纤维素、稠化剂和聚羧酸减水剂,以转速300r/min混合20min,制得预拌砂浆。
42.实施例5
43.一种预拌砂浆,由以下重量份的原料制成:水泥50,细度模数为1.6
‑
2.2的海砂40,铝渣30,甲基纤维素0.08,玄武岩纤维1,稠化剂2.0,聚羧酸减水剂0.5;所述稠化剂由以下重量份的原料制成:膨润土80、石脂20、水铝英石15、粉煤灰10、三乙醇胺油酸皂0.5、硬脂酸0.5、醋酸乙烯0.8。
44.所述铝渣中,氧化钙的含量为32.01%,三氧化铝的含量为29.3%,二氧化硅的含量为10.8%。所述铝渣进行如下处理后再使用:将铝渣粉碎至0.25mm方孔筛筛余不大于10%,边搅拌边向粉碎后的铝渣中喷处理剂进行处理,处理过程的温度控制在50℃,搅拌速度50r/min,处理时间为40min,将处理得到的铝渣控干水分至含水量<1%即可;所述处理剂是由fecl2、泡花碱、k2sio3和海水混合制得,所述每kg处理剂中的各组分含量如下:fecl23g、泡花碱200g、k2sio34g,余量为海水;所述处理剂的使用量为每吨铝渣中喷洒200公斤处理剂。
45.所述稠化剂的制备方法包括如下步骤:将膨润土、石脂、水铝英石、粉煤灰烘干至水分小于1%;将三乙醇胺油酸皂、硬脂酸加入膨润土中混合,然后加入磨机中混磨,物料磨至0.25mm方孔筛筛余不大于10%,得到混合物i;在混合物i中加入石脂、水铝英石,温度控制在45℃,继续在磨机中混磨,物料磨至0.25mm方孔筛筛余不大于10%,得到混合物ii;边搅拌边在粉煤灰中加入醋酸乙烯,混合均匀后得到混合物iii;在混合物ii中加入混合物iii,于40℃温度下在磨机中混合研磨10min,静置10min,再研磨10min,制得稠化剂。
46.所述的预拌砂浆的制备方法,包括如下步骤:按原料的配方比例称取水泥、海砂、铝渣和玄武岩纤维,所述水泥、铝渣、玄武岩纤维的细度控制在0.25mm方孔筛筛余不大于10%,加入混合机中搅拌混合,搅拌速度为400r/min,搅拌10min,再加入甲基纤维素、稠化剂和聚羧酸减水剂,以转速200r/min混合30min,制得预拌砂浆。
47.实施例6
48.一种预拌砂浆,由以下重量份的原料制成:水泥5,细度模数为1.6
‑
2.2的海砂33,铝渣22,甲基纤维素0.04,玄武岩纤维0.3,稠化剂1.6,聚羧酸减水剂0.2;所述稠化剂由以下重量份的原料制成:膨润土55、石脂12、水铝英石8、粉煤灰6、三乙醇胺油酸皂0.2、硬脂酸0.2、醋酸乙烯0.4。
49.所述铝渣中,氧化钙的含量为31.1%,三氧化铝的含量为29.3%,二氧化硅的含量为10.4%。
50.所述稠化剂的制备方法包括如下步骤:将膨润土、石脂、水铝英石、粉煤灰烘干至水分小于1%;将三乙醇胺油酸皂、硬脂酸加入膨润土中混合,然后加入磨机中混磨,物料磨至0.25mm方孔筛筛余不大于10%,得到混合物i;在混合物i中加入石脂、水铝英石,温度控制在40℃,继续在磨机中混磨,物料磨至0.25mm方孔筛筛余不大于10%,得到混合物ii;边搅拌边在粉煤灰中加入醋酸乙烯,混合均匀后得到混合物iii;在混合物ii中加入混合物iii,于35℃温度下在磨机中混合研磨15min,静置8min,再研磨8min,制得稠化剂。
51.所述的预拌砂浆的制备方法,包括如下步骤:按原料的配方比例称取水泥、海砂、铝渣和玄武岩纤维,所述水泥、铝渣、玄武岩纤维的细度控制在0.25mm方孔筛筛余不大于10%,加入混合机中搅拌混合,搅拌速度为350r/min,搅拌15min,再加入甲基纤维素、稠化剂和聚羧酸减水剂,以转速250r/min混合25min,制得预拌砂浆。
52.实施例7
53.一种预拌砂浆,由以下重量份的原料制成:水泥5,细度模数为1.6
‑
2.2的海砂33,铝渣22,甲基纤维素0.04,玄武岩纤维0.3,稠化剂1.6,聚羧酸减水剂0.2;所述稠化剂由以下重量份的原料制成:膨润土55、石脂12、水铝英石8、粉煤灰6、三乙醇胺油酸皂0.2、硬脂酸0.2、醋酸乙烯0.4。
54.所述铝渣中,氧化钙的含量为31.1%,三氧化铝的含量为29.3%,二氧化硅的含量为10.4%。所述铝渣进行如下处理后再使用:将铝渣粉碎至0.25mm方孔筛筛余不大于10%,边搅拌边向粉碎后的铝渣中喷处理剂进行处理,处理过程的温度控制在45℃,搅拌速度55r/min,处理时间为35min,将处理得到的铝渣控干水分至含水量<1%即可;所述处理剂是由fecl2、泡花碱、k2sio3和海水混合制得,所述每kg处理剂中的各组分含量如下:fecl24g、泡花碱250g、k2sio33.5g,余量为海水;所述处理剂的使用量为每吨铝渣中喷洒190公斤处理剂。
55.所述稠化剂的制备方法包括如下步骤:将膨润土、石脂、水铝英石、粉煤灰烘干至水分小于1%,磨至0.25mm方孔筛筛余不大于10%,然后将各原料组分混合后于35℃温度下在磨机中混合研磨15min,静置8min,再研磨8min,制得稠化剂。
56.所述的预拌砂浆的制备方法,包括如下步骤:按原料的配方比例称取水泥、海砂、铝渣和玄武岩纤维,所述水泥、铝渣、玄武岩纤维的细度控制在0.25mm方孔筛筛余不大于10%,加入混合机中搅拌混合,搅拌速度为350r/min,搅拌15min,再加入甲基纤维素、稠化剂和聚羧酸减水剂,以转速250r/min混合25min,制得预拌砂浆。
57.实施例8
58.一种预拌砂浆,由以下重量份的原料制成:水泥5,细度模数为1.6
‑
2.2的海砂33,铝渣22,甲基纤维素0.04,玄武岩纤维0.3,稠化剂1.6,聚羧酸减水剂0.2;所述稠化剂由以下重量份的原料制成:膨润土55、高岭土12、蒙脱石8、粉煤灰6、三乙醇胺油酸皂0.2、硬脂酸0.2、醋酸乙烯0.4。
59.所述铝渣中,氧化钙的含量为31.1%,三氧化铝的含量为29.3%,二氧化硅的含量为10.4%。所述铝渣进行如下处理后再使用:将铝渣粉碎至0.25mm方孔筛筛余不大于10%,边搅拌边向粉碎后的铝渣中喷处理剂进行处理,处理过程的温度控制在45℃,搅拌速度
55r/min,处理时间为35min,将处理得到的铝渣控干水分至含水量<1%即可;所述处理剂是由fecl2、泡花碱、k2sio3和海水混合制得,所述每kg处理剂中的各组分含量如下:fecl24g、泡花碱250g、k2sio33.5g,余量为海水;所述处理剂的使用量为每吨铝渣中喷洒190公斤处理剂。
60.所述稠化剂的制备方法包括如下步骤:将膨润土、高岭土、蒙脱石、粉煤灰烘干至水分小于1%,磨至0.25mm方孔筛筛余不大于10%,然后将各原料组分混合后于35℃温度下在磨机中混合研磨15min,静置8min,再研磨8min,制得稠化剂。
61.所述的预拌砂浆的制备方法,包括如下步骤:按原料的配方比例称取水泥、海砂、铝渣和玄武岩纤维,所述水泥、铝渣、玄武岩纤维的细度控制在0.25mm方孔筛筛余不大于10%,加入混合机中搅拌混合,搅拌速度为350r/min,搅拌15min,再加入甲基纤维素、稠化剂和聚羧酸减水剂,以转速250r/min混合25min,制得预拌砂浆。
62.实施例9
63.使用实施例1的配方及制备方法制备预拌砂浆,并选择不同氧化钙含量、三氧化铝含量、二氧化硅含量的铝渣;所选择的铝渣中,氧化钙的含量为28.1%,三氧化铝的含量为26.3%,二氧化硅的含量为9.4%。
64.实施例10
65.使用实施例1的配方及制备方法制备预拌砂浆,在铝渣的处理过程中,所使用的处理剂是由fecl2、泡花碱、k2sio3和淡水混合制得,所述每kg处理剂中的各组分含量如下:fecl24g、泡花碱250g、k2sio33.5g,余量为自来水。
66.经本实施例处理的铝渣按照hjt299
‑
2007《固体废物浸出毒性浸出方法
‑
硫酸硝酸法》进行浸出试验,结果如下:
67.处理前:ni含量3.92mg/l,cr含量34.10mg/l;
68.处理后:ni含量0.97mg/l,cr含量2.35mg/l。
69.按照jgj/t70
‑
2009检测各实施例的预拌砂浆标准试块的各项性能指标,具体见表1。
70.表1
[0071][0072]
由表1的数据可知,实施例1的预拌砂浆的各项性能指标达到了很好的技术效果;实施例6的铝渣不经处理即添加使用,最终预拌砂浆的各项指标效果均有下降;实施例7改
变了稠化剂的制备方法、实施例8改变了稠化剂的组分配方,对预拌砂浆成品的各项性能均有一定影响;实施例9选择了不同含量成分的铝渣,对预拌砂浆的抗折强度、抗压强度也有影响;由实施例10的数据可以看出,处理剂配方中的海水对铝渣的处理效果有一定作用。
[0073]
虽然本发明已以较佳实施例揭示如上,然其并非用以限制本发明,任何本领域技术人员,在不脱离本发明的精神和范围内,当可做些许的修改和完善,因此本发明的保护范围当以权利要求书所界定的为准。